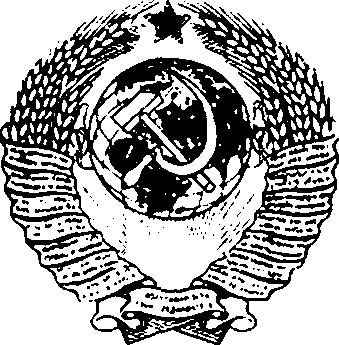
ГОСУДАРСТВЕННЫЙ СТАНДАРТ СОЮЗА ССР
ПОРОШКИ МЕТАЛЛИЧЕСКИЕ
МЕТОД ОПРЕДЕЛЕНИЯ ПОТЕРИ МАССЫ ПРИ ПРОКАЛИВАНИИ В ВОДОРОДЕ
ГОСТ 18897—73
(СТ СЭВ 1561—79J
Издание официальное
Цена 3 кол.
ГОСУДАРСТВЕННЫЙ КОМИТЕТ СССР ПО СТАНДАРТАМ
Москва
УДК 669*492.2 : 001.4 :006.354 Группа 859
ГОСУДАРСТВЕННЫЙ СТАНДАРТ СОЮЗА ССР
ПОРОШКИ МЕТАЛЛИЧЕСКИЕ | ГОСТ |
Метод определения потери массы при прокаливании в водороде | 18897-73* |
Metal powders. Method for determination of metal powders losses while heating it in hydrogen | (СТ СЭВ 1561—79) |
ОКСТУ 1709
Постановлением Государственного комитета стандартов Совета Министров СССР от 14 июня 1973 г, М2 1465 срок введения установлен
с 01.01.75 Проверен в 1984 г. Постановлением Госстандарта от 13.12.84 № 4259 срок действия продлен до 01,07.90
Несоблюдение стандарта преследуется по закону
Настоящий стандарт устанавливает метод определения потери массы при прокаливании в водороде металлических порошков железа, никеля, кобальта, меди, бронзы, молибдена, вольфрама, легированной стали, олова, свинца. Метод позволяет приближенно определять содержание кислорода в металлических порошках.
Метод заключается в уменьшении массы порошка после его прокаливания.
Стандарт полностью соответствует СТ СЭВ 1561—79.
1. ОТБОР ПРОБ
Отбор и подготовку проб для анализа проводят по ГОСТ 23148—78.
2. АППАРАТУРА, МАТЕРИАЛЫ И РЕАКТИВЫ
Установка для определения потери массы при прокаливании в водороде (см. чертеж).
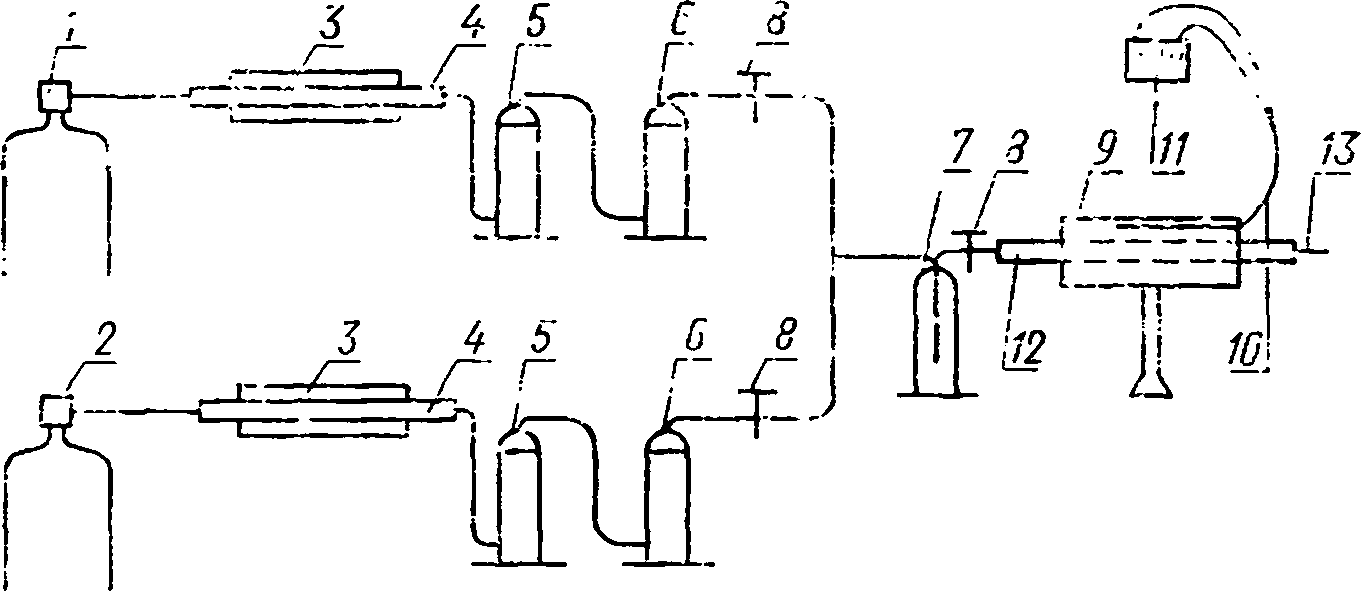
Установка состоит из следующих элементов: водородного баллона с редуктором /; азотного баллона с редуктором 2; электрических трубчатых печей 3 (зона нагрева не менее 150 мм) со средствами контроля и управления температурой; кварцевых труб 4 диаметром 18—22 мм и длиной около 400 мм, наполненных медной стружкой, предназначенных для очистки водорода и азота от кислорода; склянок Тищенко: с аскаритом 5, с фосфорным ангидридом, смешанным с прокаленным асбестом 6\ склянки Дрекселя 7 с концентрированной серной кислотой; кранов стеклянных 8 по ГОСТ 7995—80, соединяющих систему очистки с печью; электрической трубчатой печи 9 с сопротивлением, разрешающим поддерживать температуру до 1200°С; термопары платина-пла-тинородиевой 10\ гальванометра //; кварцевой или керамической газонепроницаемой трубы 12 диаметром 22 мм и длиной 750— 1000 мм; резиновой пробки с кварцевой трубкой 13.
Реактивы для поглощения влаги (аскарит, фосфорный ангидрид и серная кислота) заменяются через 1,5—2 месяца.
Для очистки водорода от кислорода применяют также поглотительную склянку с палладированным асбестом. Для поглощения влаги — склянку с силикагелем.
Лодочки фарфоровые по ГОСТ 9147—80, кварцевые, корундовые, из окиси циркония, молибденовой жести, никелевые длиной 50—90 мм.
Эксикатор по ГОСТ 25336—82.
Крючок из легированной стали для загрузки и выгрузки лодочки из печи.
Весы лабораторные с погрешностью взвешивания не более 0,0002 г.
Аскарит.
Фосфорный ангидрид.
Кислота серная по ГОСТ 4204—77.
Водород технический марки А по ГОСТ 3022—80.
Азот по ГОСТ 9293—74.
(Измененная редакция, Изм. № 1, 2).
3. ПОДГОТОВКА К АНАЛИЗУ
3.1. Сборка установки и проверка герметичности.
Собирают установку, как указано на чертеже. Газ, использованный для продувки, должен удаляться через вытяжную вентиляцию.
Для проверки герметичности системы вынимают из конца трубы резиновую пробку с кварцевой трубкой и заменяют ее резиновой пробкой. Включают ток водорода и открывают кран, соединяющий печь с водородом (доступ азота должен быть перекрыт). Если в дрекселе с серной кислотой в течение 5 мин не замечено выделения пузырьков газа, система герметична. Затем перекрывают доступ водорода, открывают ток азота и проверяют герметичность азотной линии.
3.2. Подготовка лодочек для анализа
Перед проведением испытания лодочки должны быть прокалены в токе водорода до постоянной массы и должны храниться в эксикаторе. Включают печи 3, предназначенные для очистки газов от кислорода. На протяжении всего процесса работы на установке в них поддерживается температура 450°С.
Трубку помещают в печь 9 так, чтобы один конец ее на дветре,-ти выступал из печи в сторону подачи газа.
Печь 9 со вставленной в нее трубой нагревают до температуры 1000°С. Включают ток азота и пропускают его через систему в течение 5 мин. Затем открывают трубу и в ее короткую часть, в середину печи, помещают лодочки. Закрывают трубу и снова пропускают ток азота в течение 1 мин. Прекращают подачу азота и одновременно включают ток водорода со скоростью 3—5 пузырьков в секунду. На выходе из печи зажигают факел водорода. Через 1 ч трубу с лодочками выдвигают по ходу тока водорода так, чтобы лодочка находилась на расстоянии 150—200 мм от горячей зоны печи.
Лодочки охлаждают в токе водорода в течение 20—30 мин. Прекращают подачу водорода и одновременно включают ток азота, который пропускают в- течение 1 мин.
(Измененная редакция, Изм. № 1).
4. ПРОВЕДЕНИЕ АНАЛИЗА
4.1. В прокаленную и взвешенную лодочку помещают 1—10 г исследуемого порошка, взвешенного с погрешностью не более 0,0002 г. Навеску порошка равномерно распределяют в лодочке так, чтобы толщина его слоя не превышала 3 мм.
Печь 9 со вставленной в нее трубой нагревают до температуры, указанной в табл. 1.
Включают ток азота и пропускают его в течение 5 мин. Линейная скорость протекания азота в холодной части трубы должна быть не менее 2,5 см/с. Линейную скорость газа (V), см/с, вычисляют по формуле
V=JL__
л Д2 ’
где К — расход газа, см3/с;
Д— внутренний диаметр трубы, см.
Открывают трубу и помещают лодочку с навеской порошка в ее короткую часть, в середину печи.
Закрывают трубу и снова пропускают ток азота в течение 1 мин.
Прекращают подачу азота и одновременно включают ток водорода. Линейная скорость протекания водорода в холодной части трубы должна быть не менее 2,5 см/с.
Таблица 1
Порошок | Температура прокаливания, °C | Время прокаливания, мин | Наименование лодочки |
Медный | 875±15 | 30 | Фарфоровые, кварцевые, |
Бронзы оловянной | 775dzl5 | 30 | корундовые, из окиси циркония, молибденовой жес- |
Бронзы свинцовой | 66010 | 10 | ти, никелевые |
Железный | 115Q±20 | 60 | Фарфоровые, корундовые, |
Стали легированной | 1150+20 | 60 | из окиси циркония, молибденовой жести, никелевые То же |
Кобальтовый | 1050±20 | 60 | Фарфоровые, корундовые, из окиси циркония, молиб- |
Вольфрамовый | 115Д±20 | 60 | деновой жести, никелевые То же |
Молибденовый | 1 Ю0±20 | 60 | Фарфоровые, корундовые, из окиси циркония, нике- |
Никелевый | 1050±20 | 60 | левые Фарфоровые, кварцевые, |
Оловянный | 550± 10 | 30 | корундовые, из окиси циркония, молибденовой жести Фарфоровые, кварцевые, |
Свинцовый | 550±10 | 30 | корундовые То же |
По истечении времени, необходимого для восстановления порошка, трубу с лодочкой выдвигают из горячей зоны печи. Лодочку с навеской охлаждают в токе водорода в течение 20 — 30 мин. Затем прекращают подачу водорода и одновременно включают ток азота, который пропускают через систему в течение 5 мин.
Открывают трубу, вынимают лодочку с навеской, помещают ее в эксикатор, охлаждают до комнатной температуры и взвешивают с погрешностью не более 0,0002 г.
(Измененная редакция, Изм. № 1, 2).
4.2. Допускается определять потери массы при прокаливании в водороде без применения азота.
Определение производят следующим образом: лодочку с навеской порошка помещают в холодную печь и пропускают через систему водород в течение 10—15 мин. Зажигают факел водорода.
Затем включают печь 9, нагревают ее до температуры, указанной в табл. 1.
По истечении времени, необходимого для восстановления порошка, печь выключают.
Трубу с лодочкой выдвигают из горячей зоны печи, снижают температуру печи до 500°С, не прекращая подачи водорода. Затем вынимают лодочку, помещают ее в эксикатор, охлаждают до комнатной температуры и взвешивают.
5. ПОДСЧЕТ РЕЗУЛЬТАТОВ АНАЛИЗА
5.1. Потери массы при прокаливании в водороде (X) в процентах вычисляют с погрешностью не более 0,01% по формуле
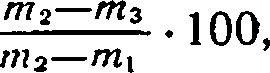
где гп\— масса лодочки, прокаленной до постоянной массы, г; ги2— масса лодочки с порошком перед испытанием, г; /Из — масса лодочки с порошком после испытания, г.
(Измененная редакция, Изм. № Г, 2).
5.2. Среднее арифметическое результатов двух параллельных определений принимают за окончательный результат.
Абсолютные допускаемые расхождения результатов параллельных определений не должны превышать значений, указанных в табл. 2.
Таблица 2
Потерн массы при прокаливании, % | Абсолютные допускаемые |
расхождения, % | |
От 0,1 ДО 0,3 | 0,02 |
Св. 0,3 » 0,5 | 0,04 |
» 0,8 | 0,05 |
(Измененная редакция, Изм. № 1).
ПРИЛОЖЕНИЕ Рекомендуемое
Определяемая потеря массы при прокаливании в водороде является более низкой, чем содержание кислорода, если порошок загрязнен окислами, которые не восстанавливаются в условиях, оговоренных настоящим стандартом (например SiO2, Al2O3, CaO, MgO, TiO2), и может быть выше, чем содержание кислорода, если в порошке присутствуют влага, углеводороды и их смеси, а также адсорбированные или абсорбированные металлическим порошком газы, которые удаляются во время нагревания (количество их незначительно).
Потеря массы при прокаливании в водороде может быть выше, если в порошке присутствуют элементы, которые в условиях проведения испытания частично или полностью улетучиваются (S, N, С, Р и некоторые летучие металлы, например, свинец, кадмий, цинк), а также, если порошок содержит углерод и окислы, которые могут в условиях проведения испытания восстанавливаться углеродом (Сг2Оь МпО).
Порошки, содержащие марганец, хром и другие элементы, обладающие высоким сродством к кислороду, могут быть окислены во время испытания под влиянием атмосферы или в результате восстановления менее жаростойких окислов. В некоторых случаях это может привести к отрицательной величине потери массы при прокаливании в водороде.
(Введено дополнительно, Изм. № 2).
Редактор Л. Д. Курочкина
Технический редактор Э. В. Митяй Корректор Л. В. Сницарчук
Сдано в наб. 08.05.86 Подп. в печ. 01.08.86 0.5 усл. п. л. 0.5 усл. кр.-отт. 0,41 уч.-изд. л. Тираж 6000 Цена 3 коп.
Изменение № 3 ГОСТ 18897—73 Порошки металлические. Метод определения потери массы при прокаливании в водороде
Утверждено и введено в действие Постановлением Государственного комитета СССР по управлению качеством продукции и стандартам от 18.12.89 № 3790
Дата введения 01,07.90
Вводная часть. Первый абзац дополнить словами: «(при массовой доле кислорода от 0,1 до 2,0 %). Для порошков с массовой долей кислорода менее
(Продолжение см. с. 88)
87
(Продолжение изменения к ГОСТ 18897—73) 0,1 % и наличием металлоидов определение кислорода проводят по ГОСТ 27417—87»;
дополнить абзацем (после второго): «Рекомендации по выбору метода определения кислорода в металлических порошках в соответствии с ГОСТ 27417—87». Раздел 2. Чертеж заменить новым:
(Продолжение см. с. 89)
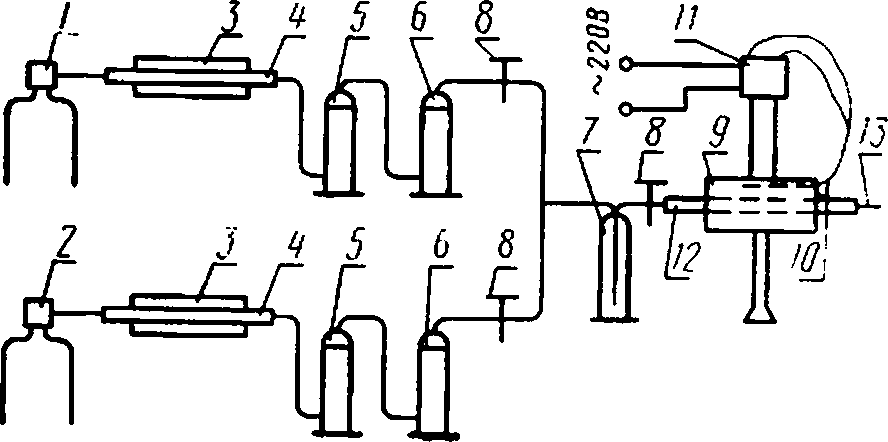
второй абзац. Заменить слова: «электрической трубчатой печи 9 с сопротивлением, разрешающим поддерживать температуру до 1200 °C; термопары плати-ка-платинародиевой 10\ гальванометра //> на «электрической печи 9, позволяющей получать температуру до 1200 °C; системы регулирования с платина-платина-родиевой термопарой, обеспечивающей поддержание температур в печи с погреш-■остью не более указанной в табл. 1»;
восьмой абзац изложить в новой редакции: «Весы лабораторные общего назначения по ГОСТ 24104—88, не ниже 2-го класса точности с наибольшим пределом взвешивания до 200 г или другие весы, отвечающие указанным метрологическим характеристикам».
Пункт 4.1. Первый, второй абзацы изложить в новой редакции: «Массовую долю потери массы порошка при прокаливании определяют для двух параллельных навесок массой 1—10 г каждая. Навеску порошка, взвешенную с погрешностью не более 0,0001, г, помещают в прокаленную и взвешенную лодочку. Порошок равномерно распределяют в лодочке до получения слоя толщиной не
(Продолжение см. с. 90)
(Продолжение изменения к ГОСТ 18897—73) более 3 мм. Допускается вместо навески порошка испытывать его прессовку толщиной не более 2 мм пористостью не менее 30 %, изготовленную без применения связки, смазки, увлажнителя и других добавок.
Навески порошка или его прессовки прокаливают в печи одновременно или каждую в отдельности. Для этого печь 9 со вставленной в нее трубой нагревают до температуры, указанной в табл. 1»;
последний абзац. Заменить значение: 0,0002 г на 0,0001 г.
Пункт 5.1. Первый абзац. Исключить слова: «с погрешностью не более 0,01 %>;
дополнить абзацем: «Результаты вычислений округляют до второго десятичного знака».
Пункт 5.2. Второй абзац изложить в новой редакции: «Абсолютные допускаемые расхождения двух параллельных определений при доверительной вероятности 0,95 и абсолютная погрешность записи их среднего арифметического результата указаны в табл. 2»;
таблицу 2 изложить в новой редакции:
Таблица 2
Потер н массы при прока' ливании, % | Абсолютные допускаемые расхождения | Абсолютная погрешность записи среднего арифметического |
для двух параллельных | определенно, %, не более | |
До 0,8 | 0,04 | 0,02 |
Св. 0,8 | 5 от их среднего арифметического | 0,05 |
(ИУС № 3 1990 г.)