МЕЖГОСУДАРСТВЕННЫЙ СОВЕТ ПО СТАНДАРТИЗАЦИИ, МЕТРОЛОГИИ И СЕРТИФИКАЦИИ (МГС)
INTERSTATE COUNCIL FOR STANDARDIZATION, METROLOGY AND CERTIFICATION (ISC)
ГОСТ 9.909— 2023
МЕЖГОСУДАРСТВЕННЫЙ СТАНДАРТ
Единая система защиты от коррозии и старения
ПОКРЫТИЯ МЕТАЛЛИЧЕСКИЕ И НЕМЕТАЛЛИЧЕСКИЕ НЕОРГАНИЧЕСКИЕ, МЕТАЛЛЫ И СПЛАВЫ
Методы испытаний на климатических испытательных станциях
Издание официальное
Москва Российский институт стандартизации 2023
Предисловие
Цели, основные принципы и общие правила проведения работ по межгосударственной стандартизации установлены ГОСТ 1.0 «Межгосударственная система стандартизации. Основные положения» и ГОСТ 1.2 «Межгосударственная система стандартизации. Стандарты межгосударственные, правила и рекомендации по межгосударственной стандартизации. Правила разработки, принятия, обновления и отмены»
Сведения о стандарте
1 РАЗРАБОТАН Федеральным государственным унитарным предприятием «Всероссийский научно-исследовательский институт авиационных материалов» (ФГУП «ВИАМ»)
2 ВНЕСЕН Межгосударственным техническим комитетом по стандартизации МТК 543 «Защита изделий и материалов от коррозии, старения и биоповреждений»
3 ПРИНЯТ Межгосударственный советом по стандартизации, метрологии и сертификации (протокол от 28 июля 2023 г. № 163-П)
За принятие проголосовали:
Краткое наименование страны по МК (ИСО 3166) 004—97 | Код страны по МК (ИСО 3166) 004—97 | Сокращенное наименование национального органа по стандартизации |
Армения | АМ | ЗАО «Национальный орган по стандартизации и метрологии» Республики Армения |
Беларусь | BY | Госстандарт Республики Беларусь |
Киргизия | KG | Кыргызстандарт |
Россия | RU | Росстандарт |
Узбекистан | UZ | Узстандарт |
4 Приказом Федерального агентства по техническому регулированию и метрологии от 5 сентября 2023 г. № 801-ст межгосударственный стандарт ГОСТ 9.909—2023 введен в действие в качестве национального стандарта Российской Федерации с 1 апреля 2024 г.
5 ВЗАМЕН ГОСТ 9.909—86
Информация о введении в действие (прекращении действия) настоящего стандарта и изменений к нему на территории указанных выше государств публикуется в указателях национальных стандартов, издаваемых в этих государствах, а также в сети Интернет на сайтах соответствующих национальных органов по стандартизации.
В случае пересмотра, изменения или отмены настоящего стандарта соответствующая информация будет опубликована на официальном интернет-сайте Межгосударственного совета по стандартизации, метрологии и сертификации в каталоге «Межгосударственные стандарты»
© Оформление. ФГБУ «Институт стандартизации», 2023

В Российской Федерации настоящий стандарт не может быть полностью или частично воспроизведен, тиражирован и распространен в качестве официального издания без разрешения Федерального агентства по техническому регулированию и метрологии
Содержание
1 Область применения
2 Нормативные ссылки
3 Термины и определения
4 Обозначения и сокращения
5 Метод испытаний на атмосферную коррозию
6 Методы испытаний на склонность к коррозионному растрескиванию под напряжением в атмосферных условиях
7 Метод испытаний на контактную коррозию в атмосфере
8 Метод испытаний на щелевую коррозию в атмосфере
9 Метод испытаний в морской воде
10 Метод испытаний на контактную коррозию в морской воде
11 Метод испытаний на щелевую коррозию в морской воде
12 Метод натурно-ускоренных испытаний
Приложение А (рекомендуемое) Опись варианта образцов
Приложение Б (рекомендуемое) Результаты предварительного осмотра образцов
Приложение В (рекомендуемое) Результаты взвешивания образцов
Приложение Г (рекомендуемое) Приспособления и образцы для испытаний на коррозию под напряжением
Приложение Д (рекомендуемое) Пакеты для испытаний на контактную коррозию
Приложение Е (рекомендуемое) Пакеты для испытаний на щелевую коррозию
Приложение Ж (рекомендуемое) Требования к проведению климатических испытаний и оценке свойств
МЕЖГОСУДАРСТВЕННЫЙ СТАНДАРТ
Единая система защиты от коррозии и старения ПОКРЫТИЯ МЕТАЛЛИЧЕСКИЕ И НЕМЕТАЛЛИЧЕСКИЕ НЕОРГАНИЧЕСКИЕ, МЕТАЛЛЫ И СПЛАВЫ
Методы испытаний на климатических испытательных станциях
Unified system of corrosion and ageing protection. Metal and non-metal inorganic coatings, metals and alloys. Test methods at climatic test stations
Дата введения — 2024—04—01
1 Область применения
Настоящий стандарт распространяется на металлы, сплавы, металлические и неметаллические неорганические покрытия и устанавливает методы их испытаний на климатических испытательных станциях (далее — станции).
2 Нормативные ссылки
В настоящем стандарте использованы нормативные ссылки на следующие межгосударственные стандарты:
ГОСТ 9.106 Единая система защиты от коррозии и старения. Коррозия металлов. Термины и определения
ГОСТ 9.905 Единая система защиты от коррозии и старения. Методы коррозионных испытаний. Общие требования1)
ГОСТ 9.906 Единая система защиты от коррозии и старения. Станции климатические испытательные. Общие требования
ГОСТ 9.908 Единая система защиты от коррозии и старения. Металлы и сплавы. Методы определения показателей коррозии и коррозионной стойкости
ГОСТ 25.502 Расчеты и испытания на прочность в машиностроении. Методы механических испытаний металлов. Методы испытаний на усталость
ГОСТ 1497 (ИСО 6892—84) Металлы. Методы испытаний на растяжение
ГОСТ 4233 Реактивы. Натрий хлористый. Технические условия
ГОСТ 6996 (ИСО 4136—89, ИСО 5173—81, ИСО 5177—81) Сварные соединения. Методы определения механических свойств
Примечание — При пользовании настоящим стандартом целесообразно проверить действие ссылочных стандартов и классификаторов на официальном интернет-сайте Межгосударственного совета по стандартизации, метрологии и сертификации (www.easc.by) или по указателям национальных стандартов, издаваемым в государствах, указанных в предисловии, или на официальных сайтах соответствующих национальных органов по стандартизации. Если на документ дана недатированная ссылка, то следует использовать документ, действующий на текущий момент, с учетом всех внесенных в него изменений. Если заменен ссылочный документ, на который дана датированная ссылка, то следует использовать указанную версию этого документа. Если после принятия настоящего стандарта в ссылочный документ, на который дана датированная ссылка, внесено изменение, затрагивающее положение, на которое дана ссылка, то это положение применяется без учета данного изменения. Если ссылочный документ отменен без замены, то положение, в котором дана ссылка на него, применяется в части, не затрагивающей эту ссылку.
1) В Российской Федерации действует ГОСТ Р 9.905—2007 (ИСО 7384:2001, ИСО 11845:1995).
Издание официальное
3 Термины и определения
В настоящем стандарте применены термины по ГОСТ 9.106, а также следующие термины с соответствующими определениями:
3.1 натурно-ускоренные испытания: Испытания для определения коррозионной стойкости металла (материала) и/или защитных покрытий, проводимые в естественной окружающей среде, но дающие результат в более короткий срок.
3.2 образцы сравнения: Образец из материала с известными характеристиками коррозионной стойкости, контролируемыми при испытании, экспонируемый одновременно с испытуемым образцом в тех же климатических условиях, предназначенный для сравнения результатов его экспонирования с результатами экспонирования испытуемого образца.
3.3 контрольные образцы: Образец, идентичный испытуемому образцу, хранящийся в течение периода испытания в определенных условиях, предназначенный для сравнения его характеристик с характеристиками испытуемого образца.
3.4 коррозионная стойкость: Способность металла сопротивляться коррозионному воздействию среды.
3.5 стрела прогиба: Максимальное смещение продольной оси центральной части поверхности конструкции (образца) от первоначального положения.
4 Обозначения и сокращения
4.1 Обозначения
В настоящем стандарте применены следующие обозначения:
о' — напряжение при нагрузке, МПа;
Е — модуль упругости, МПа;
а0 2 — предел текучести материала при растяжении, МПа;
ов — предел прочности до испытаний, МПа;
овк — предел прочности после испытаний, МПа;
8 — относительное удлинение, %;
V — относительное сужение, %;
t — продолжительность испытаний, год;
h — толщина образца, мм.
4.2 Сокращения
В настоящем стандарте применены следующие сокращения:
НД — нормативный документ;
ОКП — общероссийский классификатор продукции;
КР — коррозионное растрескивание;
МКК — межкристаллитная коррозия;
РСК — расслаивающая коррозия;
ЛКП — лакокрасочное покрытие;
ИПП — ингибированные полимерные покрытия;
МРСА — микрорентгеноспектральный анализ.
5 Метод испытаний на атмосферную коррозию
5.1 Сущность метода заключается в оценке коррозионной стойкости испытуемых образцов в атмосферных условиях.
5.2 Отбор образцов
5.2.1 Требования к форме, размерам и количеству образцов — по ГОСТ 9.905.
Основными типами образцов являются пластины площадью (150 х 100) мм2, толщиной (0,5—3,0) мм.
Допускается применять образцы в виде стержней, проволоки, узлов изделий и т. п.
Образцы для испытаний сварных и паяных соединений изготовляют по ГОСТ 6996.
5.2.2 На поверхности образцов не должно быть смазки, различных загрязнений, очагов коррозии, окалины, неоднородностей проката, расслоений, трещин, пор, раковин, механических повреждений.
Состояние поверхности образца должно быть оговорено программой испытаний.
5.2.3 Продолжительность испытаний образцов металлов и сплавов устанавливают в программе испытаний, которую разрабатывают с учетом требований к проведению климатических испытаний и оценке свойств, требований НД на материал (продукцию).
В технически обоснованных случаях в программе испытаний устанавливают более короткий срок испытаний.
Если программой испытаний не установлено иное, периодические осмотры внешнего вида образцов металлических материалов проводятся первые 10 дней ежедневно, один раз в неделю — в течение месяца, далее ежемесячно в течение одного года и один раз в квартал при испытаниях свыше одного года.
5.2.4 В установленный срок от каждого варианта снимают с испытаний пять образцов. При испытаниях крупногабаритных изделий, образцов, изготовленных из дефицитных и дорогостоящих материалов, снимают три образца.
За вариант принимают совокупность образцов, изготовленных из одного металла или сплава и имеющих одинаковое покрытие, нанесенное по одному технологическому процессу.
5.2.5 От каждого варианта в течение всего срока экспонирования необходимо хранить контрольные образцы в количестве, установленном программой испытаний.
5.2.6 Контрольные образцы хранят одним из следующих способов:
- в закрытом помещении с неагрессивной атмосферой при температуре от 15 до 30 °C и относительной влажности воздуха до 65 %;
- в полиэтиленовом мешке, закрытом перегибом;
- в заваренном полиэтиленовом мешке;
- в закрытом полиэтиленовом мешке с применением некоррозионно-агрессивного влагопоглотителя (далее — влагопоглотитель);
- в эксикаторе с относительной влажностью до 50 %, которая обеспечивается влагопоглотителем, например силикагелем.
Способ хранения выбирают в зависимости от стойкости образцов к воздействию атмосферы.
Для хранения образцов свыше 1 мес применяют способы хранения в закрытом полиэтиленовом мешке или в эксикаторе.
5.2.7 При испытаниях металлов, подверженных естественному старению, сохраняют контрольные образцы для оценки изменения механических свойств.
5.2.8 Образцы сравнения экспонируют вместе с испытуемыми образцами.
5.2.9 Маркировку наносят на лицевую сторону каждого образца. В левом верхнем углу плоских образцов проставляют порядковый номер варианта по описи и в правом верхнем углу — порядковый номер образца. Образцы одного и того же варианта должны иметь порядковые номера начиная с первого. Форма описи приведена в приложении А.
Также возможны другие варианты маркировки, не влияющие на результаты испытаний.
5.2.10 Маркировка должна быть четкой и не стираться в процессе проведения испытаний.
5.2.11 Комплектацию образцов для станции проводят следующим образом: каждый образец закладывают в конверт, на котором указывают название станции, полную маркировку образца, даты начала и конца испытаний.
Все образцы одного варианта укладывают в общий полиэтиленовый чехол, помещают в него влагопоглотитель и заваривают.
К каждому варианту образцов прикладывают опись и программу испытаний.
5.2.12 Количество образцов — в соответствии с программой испытаний.
5.3 Аппаратура
Станции — по ГОСТ 9.906.
5.4 Подготовка к испытаниям
5.4.1 Образцы перед испытаниями обезжиривают органическими растворителями. Применение хлорсодержащих растворителей не допускается.
После обезжиривания допускается брать образцы только за торцы руками в хлопчатобумажных перчатках.
5.4.2 Перед установкой на испытания образцы осматривают.
5.4.3 Осмотр образцов, коррозионную стойкость которых оценивают по изменению внешнего вида, проводят на соответствие требованиям п. 5.2.2, при этом отмечают цвет, блеск поверхности, наличие и местоположение допустимых дефектов.
Для определения местоположения дефектов на образец накладывают проволочную сетку или прозрачный материал с нанесенной на него сеткой, которая делит поверхность образца на квадраты со стороной 5 мм.
Квадраты сетки должны быть пронумерованы.
5.4.4 Результаты осмотра записывают отдельно для лицевой и оборотной стороны каждого образца. Форма записи результатов испытаний приведена в приложении Б.
5.4.5 Испытуемые образцы и образцы сравнения, коррозионное поведение которых оценивают по потере массы, после обезжиривания выдерживают в эксикаторе с влагопоглотителем, например силикагелем, не менее 24 ч и взвешивают образцы массой до 200 г с ценой деления не более 0,0001 г, а свыше 200 г — с ценой деления не более 0,01 г.
Результаты взвешивания записывают в таблицу, рекомендуемая форма которой приведена в приложении В.
5.4.6 У образцов, коррозионную стойкость которых оценивают по изменению электрических свойств, измеряют исходное сечение с погрешностью не более 0,1 мм.
5.4.7 Подготовленные к испытанию образцы хранят не более 1 мес, затем применяют способы хранения в закрытом полиэтиленовом мешке или в эксикаторе в соответствии с требованиями п. 5.2.6.
5.5 Проведение испытаний
5.5.1 Испытания образцов на станциях проводят в соответствии с программой испытаний, отражающей специфику требований, предъявляемых к испытуемому материалу.
5.5.2 Условия проведения испытаний должны имитировать превалирующие факторы, действующие в условиях фактического использования материалов, или должны быть сравнимы с предполагаемыми условиями эксплуатации. Допускается параллельное выставление материалов в различных условиях. Условия экспозиции выбирают из перечня:
- открытая площадка;
- навес;
- жалюзийное хранилище;
- наземные отапливаемые/неотапливаемые хранилища.
5.5.3 Испытуемые образцы и образцы сравнения на открытом воздухе (в жалюзийном хранилище или под навесом) устанавливают под углом 45° к горизонту, допускаются углы наклона 30° и 90°.
Маркированные лицевые стороны образцов должны быть обращены вверх, в направлении к югу в северном полушарии и в направлении к северу — в южном полушарии. Короткая сторона образцов параллельна основанию стенда.
На станциях берегового типа допускается выставление образцов с маркированной лицевой стороной, обращенной в направлении источников максимального выноса хлоридов.
5.5.4 Испытуемые образцы и образцы сравнения крепят на рамах и стендах на изоляторах, например фарфоровых. Допускается подвешивать образцы на рейках.
5.5.5 На каждой станции составляют план расположения образцов.
В плане указывают номера стендов или стеллажей, рам на стендах и номер места каждого образца данного варианта на раме.
5.5.6 Образцы располагают таким образом, чтобы испытуемая поверхность была доступна воздействию атмосферы, если не испытывают материалы или защитные покрытия в недоступных или закрытых частях изделий.
5.5.7 Образцы не соприкасаются с материалом, который мог бы повлиять на ход их разрушения, если целью испытаний не является проверка этого влияния.
5.5.8 Расстояние между образцами на стендах по горизонтали — не менее 20 мм, по вертикали — не менее 10 мм.
Образцы на стендах должны быть расположены на расстоянии не менее 500 мм от поверхности земли.
Расстояние между испытуемыми поверхностями соседних образцов на стенде — не менее 50 мм.
Образцы располагают на расстоянии не менее 500 мм от крыши навеса, если программой испытаний не установлено иное.
В жалюзийном хранилище расстояние образцов от стен, пола и крыши должно быть не менее 500 мм.
5.6 Обработка результатов испытаний
После съема образцов металлических материалов при необходимости проводят сушку образцов для предотвращения дальнейшего развития коррозионных процессов, после чего укладывают в герметичную упаковку или эксикатор.
Стойкость к атмосферной коррозии материалов оценивают по основным показателям коррозии, а также оценивают изменение физико-механических свойств материала (изделия) в сравнении с исходными значениями (приложение Ж, НД на материал) после проведения натурных испытаний. Программой испытаний могут быть предусмотрены определения дополнительных показателей оценки изменения свойств материала (изделия).
Обработка результатов испытаний — по ГОСТ 9.908.
Определение свойств материалов и обработку результатов испытаний проводят в соответствии с регламентирующими нормативными документами на методы испытаний.
6 Методы испытаний на склонность к коррозионному растрескиванию под напряжением в атмосферных условиях
6.1 Сущность методов заключается в определении склонности образцов к коррозионному растрескиванию при атмосферных условиях путем экспонирования образцов в условиях, сочетающих воздействие климатических факторов и внешних заданных деформаций посредством приложения нагрузки.
6.2 Метод испытаний при заданной деформации
6.2.1 Отбор образцов — по 5.2.1—5.2.11.
Для испытаний применяют плоские и кольцевые образцы. Допускается применять образцы в виде петель.
6.2.2 Аппаратура — по 5.3.
Скоба для создания заданной деформации в плоских образцах — толщиной не более 10 мм путем их изгиба. При изготовлении скобы из металла между образцом и опорами скобы и вкладыша помещают электроизоляционные прокладки. Конструкция скобы 1 приведена в приложении Г (рис. Г.1).
Шпилька стяжная, проходящая через диаметрально противоположные отверстия в кольцевых образцах, — для создания заданной деформации путем их сжатия. Конструкция шпильки 1 приведена в приложении Г (рис. Г.2).
6.2.3 Подготовка к испытаниям — по 5.4.
Для плоских образцов стрелу прогиба f, мм, вычисляют по формуле
f = ТТТГ18'’2 +3'2'(4'1 + '2,!’ О)
где о' —напряжение для заданной деформации, МПа;
Е— модуль упругости, МПа;
h — толщина образца, мм;
/1 и /2 — расстояния между опорами скобы и вкладыша, мм.
Для кольцевых образцов величину деформации мм, вычисляют по формуле
c'-D2-7T
(2)
(3)
4-h-E '
где D —исходный внешний диаметр кольца, мм;
h — толщина кольца, мм.
Значение о' в формулах (1) и (2) в МПа вычисляют по формуле
ст' = 1.а-Г1-1-д2\
2 I 3 J
где А=----; а = а02-К;
14 ст+ 0,0025 °’2
°0 2 — предел текучести испытуемого материала при растяжении, МПа;
К — коэффициент, показывающий отношение задаваемых напряжений к пределу текучести материала.
6.2.4 Проведение испытаний — по п. 5.5.
При этом образцы размещают на стендах таким образом, чтобы поверхность, находящаяся под воздействием напряжений, была обращена вверх.
Напряжение в образцах задают в долях, равных 0,9 от предела текучести испытуемого металла.
При высокой скорости разрушения образцов испытания повторяют на нескольких уровнях напряжения, достаточных для построения характеристической кривой (время до разрушения — напряжение). При испытании сварных образцов построение характеристических кривых обязательно.
При испытании сварных образцов напряжение выбирают в зависимости от предела текучести основного металла, а при сваривании разнородных металлов — от предела текучести менее прочного металла. Если предел прочности сварного соединения меньше предела текучести свариваемых металлов, напряжение выбирают исходя из прочности сварного соединения. Плоские сварные образцы испытывают без снятия и (или) со снятием усилия как с лицевой, так и с оборотной стороны.
При испытаниях образцы периодически перенагружают (образец полностью разгружают и вновь нагружают в соответствии с первоначальным расчетом стрелы прогиба). Перенагружение образцов проводят через 3, 6, 12 мес и в дальнейшем — один раз в год.
При испытаниях на коррозию под напряжением осмотр образцов проводится ежедневно.
6.2.5 Обработка результатов испытаний
Оценкой стойкости к коррозионному растрескиванию под напряжением служит среднее арифметическое значение времени до появления трещин или до разрушения образцов.
Если более половины из испытуемых параллельно образцов не подверглись растрескиванию или разрушению, испытания повторяют и за оценку принимают среднее арифметическое значение времени, вычисленное из всех значений времени для треснувших или разрушившихся образцов. При этом указывают, что время до появления трещин или разрушения испытуемого металла или сплава больше вычисленного среднего арифметического значения для всех треснувших или разрушившихся образцов.
При отсутствии разрушения образцов для установления влияния механической нагрузки на скорость коррозии определяют в процентах изменение предела прочности Q по ГОСТ 1497 испытуемого металла по сравнению с исходным по формуле
Q = ctb-ctbk.100;
ав
где ств — предел прочности до испытаний, МПа;
ствк — предел прочности после испытаний, МПа.
6.2.6 Кроме указанной оценки коррозионную стойкость образцов определяют по ГОСТ 9.908.
6.3 Метод испытаний при постоянной осевой растягивающей нагрузке
6.3.1 Отбор образцов — по 5.2.2—5.2.11.
При этом применяют образцы прямоугольного или круглого сечения. Форма и размеры образцов приведены в рекомендуемом приложении Г.
6.3.2 Аппаратура — по 5.3.
Используют специальные установки пружинной или рычажной конструкции для нагружения образцов.
6.3.3 Подготовка к испытаниям — по 6.2.3.
6.3.4 Проведение испытаний — по 6.2.4.
Напряжение в образцах задают, равном 0,75 от предела текучести испытуемого металла. Обработка результатов испытаний — по 6.2.5.
7 Метод испытаний на контактную коррозию в атмосфере
7.1 Сущность метода заключается в определении степени влияния контакта разнородных материалов на скорость атмосферной коррозии образцов.
7.2 Отбор образцов
7.2.1 Испытуемые образцы представляют собой пакеты плоских пластин (приложение Д), в которых одна пластина из металла (металла с покрытием) может вести себя как анод, а две пластины из другого металла (металла с покрытием) — как катод, создавая тем самым электрохимический элемент в присутствии электролита.
7.2.2 Для определения влияния контакта разнородного материала совместно с образцами на контактную коррозию (пакетами) экспонируются образцы сравнения, которые представляют собой анодные пластины по 7.2.1. Также в качестве образцов сравнения могут быть использованы пакеты по 7.2.1, в которых вместо катодной пластины применены пластины из инертного, не влияющего на контактную коррозию, материала.
7.2.3 Контрольные образцы представляют собой анодные пластины, которые хранятся по 5.2.6.
7.2.4 Толщина анодных пластин должна быть не более 6 мм, а длина — такой же, как при испытании на растяжение по ГОСТ 1497.
Толщина катодных пластин — от 1 до 6 мм. При испытании драгоценных металлов катодная пластина может быть выполнена нанесением фольги драгоценного металла на пластину инертного материала, например пластмассы. Толщина пластины должна быть не менее 1 мм.
При неизвестной полярности металлов, составляющих испытуемый образец, каждый металл (металл с покрытием) следует испытывать в одном комплекте образцов в качестве анода, в другом комплекте — в качестве катода.
Зазоры и щели между анодной и катодной пластинами должны быть не более 0,02 мм. При сборке испытуемого образца момент силы при завинчивании гаек у болтов должен быть более 5,0 Н • м.
7.2.5 Материал, размеры, направление вырезки, способ обработки поверхности и другие параметры анодных пластин испытуемых образцов, образцов сравнения и контрольных образцов должны быть одинаковыми.
При испытаниях контакта «металл — металл с покрытием» допускается нарушение или отсутствие покрытия на торцах только анодных пластин.
7.2.6 Стойкость к контактной коррозии по всем показателям коррозии, кроме потери массы, оценивают на образцах, размеры которых приведены в приложении Д (черт. 1).
Стойкость к контактной коррозии по всем показателям коррозии, кроме изменения механических свойств, оценивают на образцах, размеры которых приведены в приложении Д (черт. 2).
7.2.7 Маркировка и комплектация образцов — по 5.2.10—5.2.12.
7.2.8 Прокладки и втулки должны обеспечивать изоляцию болтов от металлических пластин и плотное прижатие металлических пластин в течение всего времени испытаний. Рекомендуется использовать в качестве прокладок для болтов керамические или другие изолирующие материалы, которые не подвержены разрушению в течение всего времени испытаний, для втулок — полиэтилен и полипропилен.
Металлические болты и шайбы должны изготовляться из нержавеющей стали марки 12Х18Н9Т (типа 18-8) или из стали с более высоким содержанием хрома.
7.2.9 Количество испытуемых образцов, образцов сравнения и контрольных образцов — по 5.2.12.
7.3 Аппаратура — по 5.3.
7.4 Подготовка к испытаниям — по 5.4.
7.5 Проведение испытаний
7.5.1 Испытуемые образцы и образцы сравнения устанавливают по п. 5.5.3 и крепят по п. 5.5.4.
7.5.2 Продолжительность испытаний — по 5.2.3.
7.6 Обработка результатов испытаний — по 5.6.
7.6.1 Скорость коррозии испытуемых образцов Kv г/(м2тод), вычисляют по формуле
_ дт1
1 (5)
где Дл?1 — потеря массы анодной пластины испытуемого образца, г;
S1 —общая площадь поверхности анодной пластины, м2;
S2— площадь поверхности контакта анодной пластины с катодным материалом, м2; t—продолжительность испытаний, год.
7.6.2 Скорость коррозии образцов сравнения К2, г/(м2-год), вычисляют по формуле где Дт2 — потеря массы образца сравнения, г;
S3 — общая площадь поверхности образца сравнения, м2.
7.6.3 Потерю массы анодной пластины или образца сравнения Дт, г, вычисляют по формуле
Am = т0 - т,
(7)
где т0 —масса образца до испытаний, г;
т — масса образца после испытаний и удаления продуктов коррозии, г.
7.6.4 Стойкость к контактной коррозии определяют по показателю ускорения, равному отношению скоростей коррозии испытуемого образца и образца сравнения.
8 Метод испытаний на щелевую коррозию в атмосфере
8.1 Сущность метода заключается в определении увеличения скорости атмосферной коррозии за счет наличия щелей и/или зазоров.
8.2 Отбор образцов — по 5.2.1.
8.2.1 Испытуемые образцы представляют собой пакеты из плоских пластин, конструкции которых приведены в приложении Е.
Допускается применять другие конструкции пакетов в зависимости от специфики требований, предъявляемых к изделиям.
Для каждого испытуемого материала готовят по три образца одного или более типов (в зависимости от предполагаемых условий практического применения материала) с одинаковым зазором в щели с целью проведения параллельных испытаний.
Для образцов типов 1 и 2 зазор в щели может составлять от 0,01 до 1,0 мм. Для образцов типа 3 максимальная величина зазора в щели — 5 мм.
8.2.2 Образцы, собираемые в пакет, следует удовлетворять требованиям п. 5.2.2.
8.2.3 Образцы сравнения — пакеты — по 8.2.1 из малоуглеродистой стали, контрольные образцы — по 5.2.5.
8.3 Аппаратура — по 5.3.
8.4 Подготовка к испытаниям — по 5.4.
8.5 Проведение испытаний — по 5.5. При этом продолжительность испытаний — по 5.2.3.
8.6 Обработка результатов испытаний
8.6.1 Снятые с испытаний пакеты осматривают, фиксируют наличие или отсутствие в щелях или зазорах продуктов коррозии, очагов коррозии и устанавливают преимущественный вид коррозионного разрушения. По окончании осмотра пакеты разбирают, образцы хранят в эксикаторе до взвешивания.
8.6.2 Результаты испытаний образцов из пакетов типов 1 и 3 оценивают по изменению массы. Причем на образцах из пакетов типа 3 определяют длину зоны щелевой коррозии и величину зазора в щели, соответствующую максимальной глубине коррозионных повреждений.
8.6.3 Результаты испытаний образцов из пакетов типа 2 оценивают по изменению разрушающей нагрузки при испытании на растяжение.
8.6.4 Далее обработку результатов испытаний проводят по 5.6.
9 Метод испытаний в морской воде
9.1 Сущность метода заключается определение показателей коррозии образцов после натурных испытаний в морской воде.
9.2 Условия и параметры проведения испытаний должны имитировать превалирующие факторы условий фактического использования материалов или сравнимы с ожидаемыми условиями эксплуатации. Допускается параллельное выставление материалов в различных условиях. Условия экспозиции выбирают из перечня:
- в зоне полного погружения;
- в зоне переменного смачивания;
- в зоне забрызгивания (капельного попадания влаги на поверхность образцов без образования сплошной пленки).
Испытания образцов металлических материалов на стойкость к коррозии в натурных морских условиях проводят на испытательных стационарных и плавучих (требования к исполнению стенда устанавливают в программе испытаний) стендах и гидротехнических сооружениях, а также на исследовательских судах.
Требования настоящего стандарта могут быть использованы при проведении испытаний материалов в резервуарах с морской водой при условии периодического (не реже одного раза в неделю) обновления их свежей морской водой.
9.3 Отбор образцов — по 5.2.1, контрольные образцы — по 5.2.5, образцы сравнения — по 5.2.8.
9.3.1 Толщину испытуемых образцов: выбирают в зависимости от вида материала, продолжительности испытаний и ожидаемых коррозионных повреждений.
Рекомендуемые толщины образцов: из цинка — 6,5 мм; низкоуглеродистой нелегированной стали — 3,0 мм; легированной стали — 2,0 мм; меди, латуни и алюминия — 1,5 мм. Геометрические размеры образцов измеряют с погрешностью не более 0,1 мм.
9.4 Аппаратура
9.4.1 Для испытаний применяют испытательные стенды, изготовленные из устойчивых к воздействию морской воды материалов, которые не будут оказывать влияния на изменение скорости протекания коррозионных процессов.
9.4.1.1 Для установки образцов допускается использование стационарно установленных испытательных стендов и гидротехнических сооружений (пирсов, мостов), а также плавучих объектов. При этом расстояние между сооружением и расположенным на стенде образцом должно быть не менее 10 см.
9.4.2 Если предусмотрены периодические съемы, рекомендуется использовать отдельные стойки (рамы) для крепления образцов для каждого периода испытаний.
9.4.3 При продолжительной экспозиции используют крепежные элементы из материалов, стойких к деструкции, коррозии и биоповреждению в морской воде и при воздействии ультрафиолета, например полимерные неэлектропроводные материалы или изолированную проволоку и пр. Запрещено применение металлической проволоки без изоляции. При использовании для крепления неметаллических материалов необходимо учесть возможность их растяжения со временем для исключения касания экспонируемых образцов с дном или друг с другом.
9.5 Подготовка к испытаниям — по 5.4.
9.6 Проведение испытаний
9.6.1 Программа испытаний содержит данные о начале и конце испытаний, глубине погружения, метеорологические данные для района станции, а, при необходимости, о содержании аммиака, сероводорода, углекислого газа в атмосфере и морской воде.
9.6.2 Если программой испытаний не установлено иное, то устанавливают сроки экспозиции 0,5; 1; 2; 5; 10 и 20 лет.
Контроль параметров климатических факторов — по ГОСТ 9.906.
9.6.3 Образцы закрепляют на рамах по 5.5.4—5.5.8.
9.6.3.1 Схему крепления образцов выбирают таким образом, чтобы обеспечить их надежное крепление в течение всего периода экспозиции с учетом волновой и ветровой нагрузки.
9.6.3.2 Если испытаниям необходимо подвергнуть материалы нестандартной формы (болты, гайки, трубы и т. д.), для их крепления в испытательных стендах может быть применена сетка из неметаллических материалов. При этом важно, чтобы образцы были электрически изолированы от крепежа и друг от друга для предотвращения гальванической коррозии.
9.6.3.3 При испытаниях образцов металлов и сплавов, а также при испытаниях образцов с металлическими покрытиями не допустим прямой контакт образцов с металлическими элементами стенда или элементами крепления без применения инертных неметаллических изолирующих материалов (например, тефлоновых шайб или лент).
9.6.3.4 При проведении испытаний в зоне полного погружения для обеспечения свободного протока воды расстояние между соседними образцами на стенде должно быть не менее 50 мм.
Расстояние от образцов до поверхности воды должно быть не менее 500 мм.
Расстояние от образцов до дна должно быть не менее 200 мм во избежание заиливания образцов.
9.6.3.5 При проведении испытаний в зоне переменного смачивания образцы располагают с учетом приливно-отливного режима. Образцы на стенде необходимо располагать таким образом, чтобы во время прилива поверхность образца была полностью погружена в морскую воду, а во время отлива находилась полностью на воздухе.
9.6.3.6 При проведении испытаний в зоне забрызгивания образцы располагают выше максимального уровня воды во время прилива таким образом, чтобы образцы во время испытаний подвергались воздействию капельной воды.
9.6.3.7 При выставлении на экспозицию образцы располагают вертикально, наименьшей стороной параллельно дну.
9.6.3.8 Стационарные испытательные стенды следует располагать таким образом, чтобы они были в наибольшей степени подвержены воздействию течений.
9.6.3.9 Периодические осмотры внешнего вида образцов и их крепления к стенду проводят ежеквартально. Для зон установки образцов, характеризующихся повышенной скоростью коррозии и обрастания в морской воде, сроки проведения периодических осмотров могут быть сокращены до 2—4 недель.
9.6.3.10 Для станций, где образцы подвергаются обледенению в зимний период, на период от становления до схода льда допускается перенос образцов с морского стенда в резервуары (см. 9.2) с обновляемой морской водой при поддержании минимальной температуры.
9.7 Обработка результатов испытаний
9.7.1 Образцы периодически снимают для осмотра и оценки согласно программе испытаний. Для каждого образца ведут отчетную карту в соответствии с приложениями А—В.
9.7.2 Со снятых образцов удаляют морские обрастания с помощью деревянных или пластмассовых приспособлений (скребков и др.) так, чтобы на образцах не осталось царапин. При необходимости сохранения морских обрастаний способы их снятия и сохранения должны быть указаны в программе испытаний.
9.7.3 Результаты испытаний обрабатывают по 5.6.
9.7.4 После окончания испытаний образцы снимают с экспозиции, проводят оценку внешнего вида, фотографирование и идентификацию биообрастателей.
Образцы, снятые с экспозиции в натурных условиях, до начала проведения оценки свойств материала должны храниться в герметичной упаковке или эксикаторе с силикагелем.
10 Метод испытаний на контактную коррозию в морской воде
10.1 Сущность метода заключается в определении степени влияния контакта разнородных материалов на скорость коррозии образцов.
10.2 Отбор образцов — по 7.2.
При этом необходимо соблюдать соотношение площади катода к площади анода 1:10, 1:1, 10:1.
10.3 Аппаратура — по 5.3.
10.4 Подготовка к испытаниям — по 5.4.
10.5 Проведение испытаний — по 7.5.
При этом испытания образцов с соотношением площади катода к площади анода по 10.2 проводят параллельно.
10.6 Обработка результатов испытаний — по 7.6.
11 Метод испытаний на щелевую коррозию в морской воде
11.1 Сущность метода заключается в определении увеличения скорости коррозии в морской воде за счет наличия щелей и/или зазоров.
11.2 Отбор образцов — по 8.2.
При этом зазор в щели устанавливают от 0,01 до 3,0 мм.
11.3 Аппаратура — по 5.3.
11.4 Подготовка к испытаниям — по 5.4.
11.5 Проведение испытаний — по 8.5.
11.6 Обработка результатов испытаний — по 8.6.
12 Метод натурно-ускоренных испытаний
12.1 Сущность метода заключается в экспонировании образцов в условиях распыления аэрозолей морской воды, способствующих значительной интенсификации коррозионных процессов. Метод предназначен для более быстрой оценки коррозионной стойкости металлических материалов в условиях повышенной коррозионной агрессивности по сравнению с испытаниями без дополнительного воздействия коррозионно-активными факторами. Облив морской водой может быть осуществлен вручную либо с использованием специального стенда, предусматривающего проведение автоматического об-лива коррозионно-активными растворами.
12.2 Отбор образцов — по 5.2.
12.3 Аппаратура
12.3.1 Для испытаний применяют испытательный стенд, представляющий собой каркас (горизонтально расположенная рама, установленная на ножки) с системой автоматического облива.
12.3.2 Каркас стенда изготавливают из устойчивых к воздействию солевых растворов материалов. Все детали распылителя: емкость, шланги, кронштейны, крепежные элементы и форсунки также выполняют из материалов, инертных к воздействию коррозионно-активных факторов открытой атмосферы и морской воды.
12.3.3 В качестве системы автоматического облива применяют кронштейны с форсунками, расположение которых обеспечивает равномерное распыление раствора по всей рабочей площади стенда.
12.3.4 Высота расположения форсунок над поверхностью рамы стенда не менее 30 см для обеспечения возможности проведения испытаний образцов в напряженном состоянии (при испытаниях на коррозионное растрескивание) либо конструктивно-подобных образцов.
12.3.5 Управление распылителем стенда следует осуществлять автоматически по заданному оператором режиму с целью нормирования количества наносимого раствора и обеспечения воспроизведения операций облива в строго определенное время согласно заданному режиму.
12.3.6 Устройству распылителя стенда следует обеспечивать стабильный режим работы при температуре окружающей среды 0 °C—40 °C и заданной силе ветра. Стенд должен обладать автономной системой остановки орошения с фиксацией времени отключения при понижении температуры ниже 0 °C. При этом устройство распылителя должно исключать образование застойных зон с раствором для избегания их перемерзания и выхода из строя при понижении температуры ниже 0 °C.
Схема испытательного стенда приведена в ГОСТ 9.906.
12.3.7 Допускается применение стендов с автоматическим обливом другой компоновочной схемы, если это обусловлено требованиями программы испытаний.
12.4 Подготовка к испытаниям — по 5.4.
12.5 Проведение испытаний
12.5.1 Для испытаний применяется фильтрованная (пропущенная не менее чем через три слоя марлевой ткани) морская вода, либо раствор морской соли, концентрация которого устанавливается программой испытаний.
12.5.1.1 Для приготовления раствора используют морскую соль, полученную из морской воды методом выпаривания.
12.5.1.2 Забор морской воды из акватории осуществляется при силе ветра не более 5 м/с во избежание попадания морского ила.
12.5.1.3 Для получения морской соли проводят:
- фильтрование морской воды с помощью фильтров типа «белая лента»;
- упаривание до состояния плотной солевой массы;
- выпаривание в выпаривательной чашке на водяной бане до рыхлого состояния;
- подсушивание в термошкафу при 60 °C до постоянной массы.
12.5.1.4 Морскую соль хранят в банке с притертой крышкой.
12.5.1.5 Для испытаний применяют раствор морской соли, приготовленный на дистиллированной воде.
12.5.1.6 Допускается также приготовление солевого раствора с применением соли NaCI (х.ч.) по ГОСТ 4233.
12.5.2 Для увеличения продолжительности увлажнения поверхности образцов при натурно-ускоренных испытаниях стенд с автоматическим обливом размещают под проветриваемым навесом на климатической станции, требования к которому установлены в ГОСТ 9.906.
Допускается расположение стенда на открытой площадке, если это предусмотрено программой испытаний.
12.5.3 Крепление образов на стенде осуществляют в рейках таким образом, чтобы лицевая сторона образца была обращена вверх (перпендикулярно распылению солевого раствора). При размещении криволинейных образцов или образцов для испытаний на коррозионное растрескивание образцы размещают таким образом, чтобы обливу была подвержена как можно большая часть рабочей поверхности образца.
12.5.4 Для крепления плоских образов используют инертные материалы, не оказывающие влияние на скорость протекания коррозионных процессов, при этом площадь образца, занимаемая под крепление, должна быть минимальной.
12.5.5 Режим испытаний (количество и периодичность операций облива в течение суток, концентрацию наносимого солевого раствора) определяют программой испытаний.
12.5.6 Количество и дисперсность распыляемого раствора следует отрегулировать таким образом, чтобы на поверхности образцов образовывалась тонкая пленка электролита, при этом образование крупных стекающих капель следует исключать.
12.5.7 В качестве стандартного используют следующий режим испытаний:
- ежедневный однократный облив в 16.00 3,0 % раствором NaCI (pH раствора должно находиться в пределах 6,0—7,0).
12.5.8 Если программой испытаний не установлено иное, то устанавливают сроки экспозиции 3, 6 мес, 1,2,3г.
12.6 Обработка результатов испытаний — по 5.6.
Приложение А (рекомендуемое)
Опись варианта образцов
ПРИМЕР
Организация — изготовитель образцов:
Климатическая станция:
Условия размещения:
Продолжительность испытаний, лет:
Календарные сроки испытаний, с.....г. по...г.:
ООО «Прогресс»
Береговая
Открытая площадка
5
с 01.09.2022 г. по 01.09.2027 г.
Таблица А.1—Описание образцов
Номер варианта | Количество образцов, шт. | Маркировка образцов | Марка материала по ОКП | Размер образцов, мм | Состояние поверхности | Вид покрытия, средняя толщина |
1 | 2 | 3 | 4 | 5 | 6 | 7 |
Приложение Б (рекомендуемое)
Результаты предварительного осмотра образцов
Таблица Б.1 — Предварительный осмотр образцов
Маркировка образца | Внешний вид стороны образца | |
лицевой | оборотной | |
1 | 2 | 3 |
Приложение В (рекомендуемое)
Результаты взвешивания образцов
Таблица В.1 — Результаты взвешивания образцов
Маркировка образцов | Продолжительность испытаний t, год | Размеры образца, мм | Площадь поверхности образца S, м2 | Масса образца до испытаний т0, г | Масса образца с продуктами коррозии г | Масса образца после удаления продуктов коррозии т, г | Потеря массы ДП7, г |
1 | 2 | 3 | 4 | 5 | 6 | 7 | 8 |
Приложение Г (рекомендуемое)
Приспособления и образцы для испытаний на коррозию под напряжением
Г.1 Испытания при заданной деформации проводят на образцах плоской и кольцевой формы.
Г.2 Приспособления, предназначенные для испытаний при заданной деформации, отображены на рисунках 1 и 2 для плоских и кольцевых образцов соответственно.
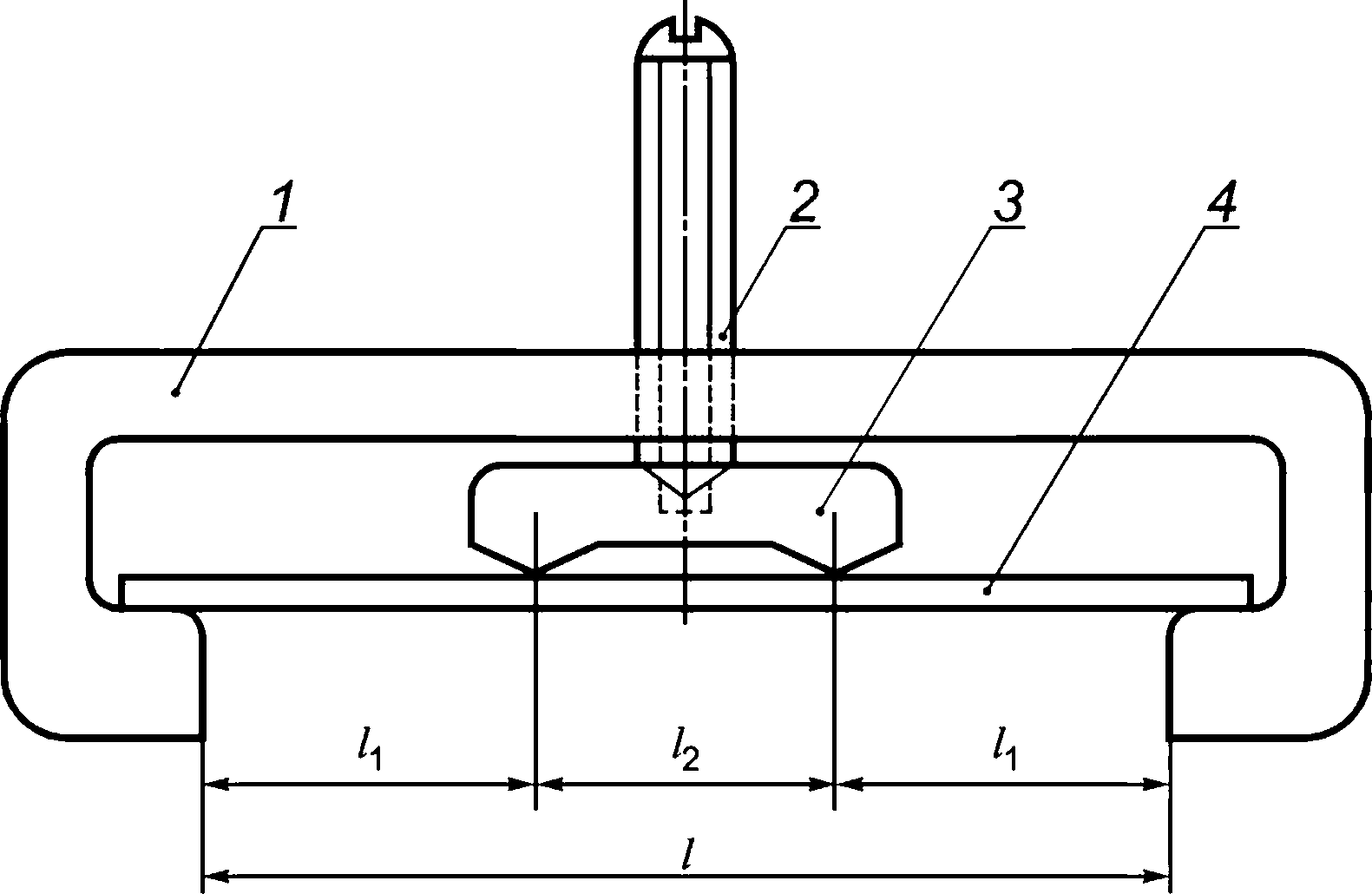
1 — скоба; 2 — шпилька; 3 — вкладыш; 4 — образец
Рисунок Г.1 — Приспособление для испытаний плоских образцов при заданной деформации (скоба)
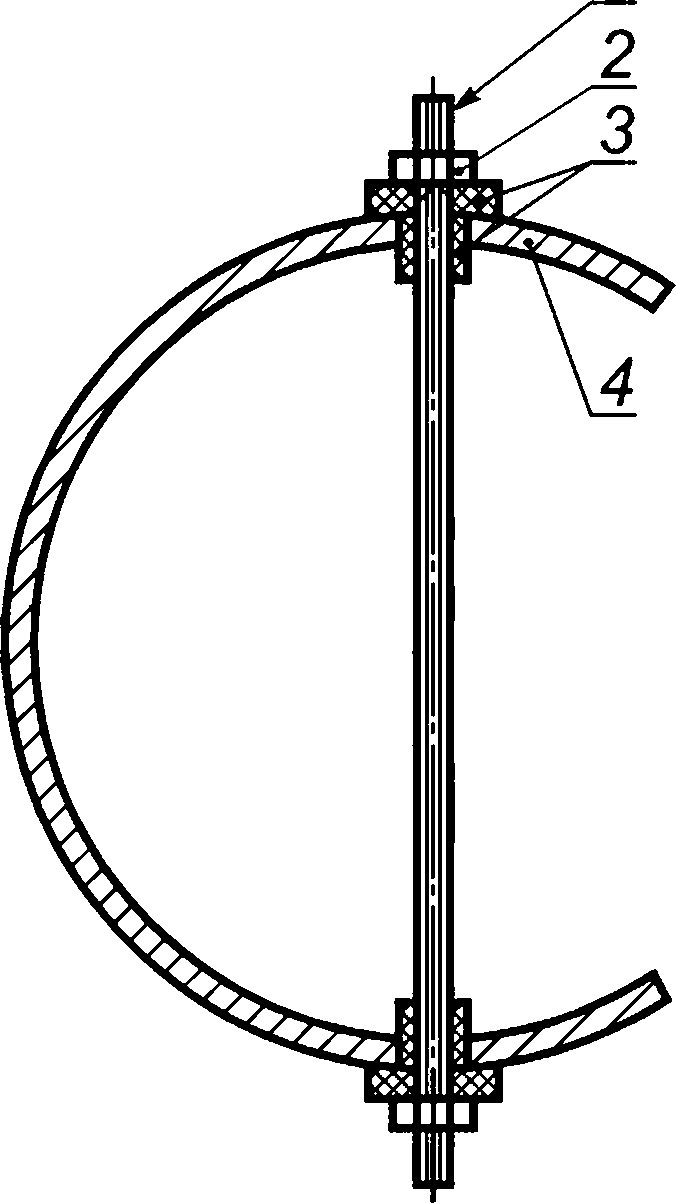
1 — шпилька; 2 — гайка; 3 — прокладка; 4 — образец
Рисунок Г.2 — Приспособление для испытаний кольцевых образцов при заданной деформации (шпилька)
Г.З Испытания при постоянной осевой нагрузке проводят на образцах круглого и прямоугольного сечения, отображенных на рисунке Г.З.
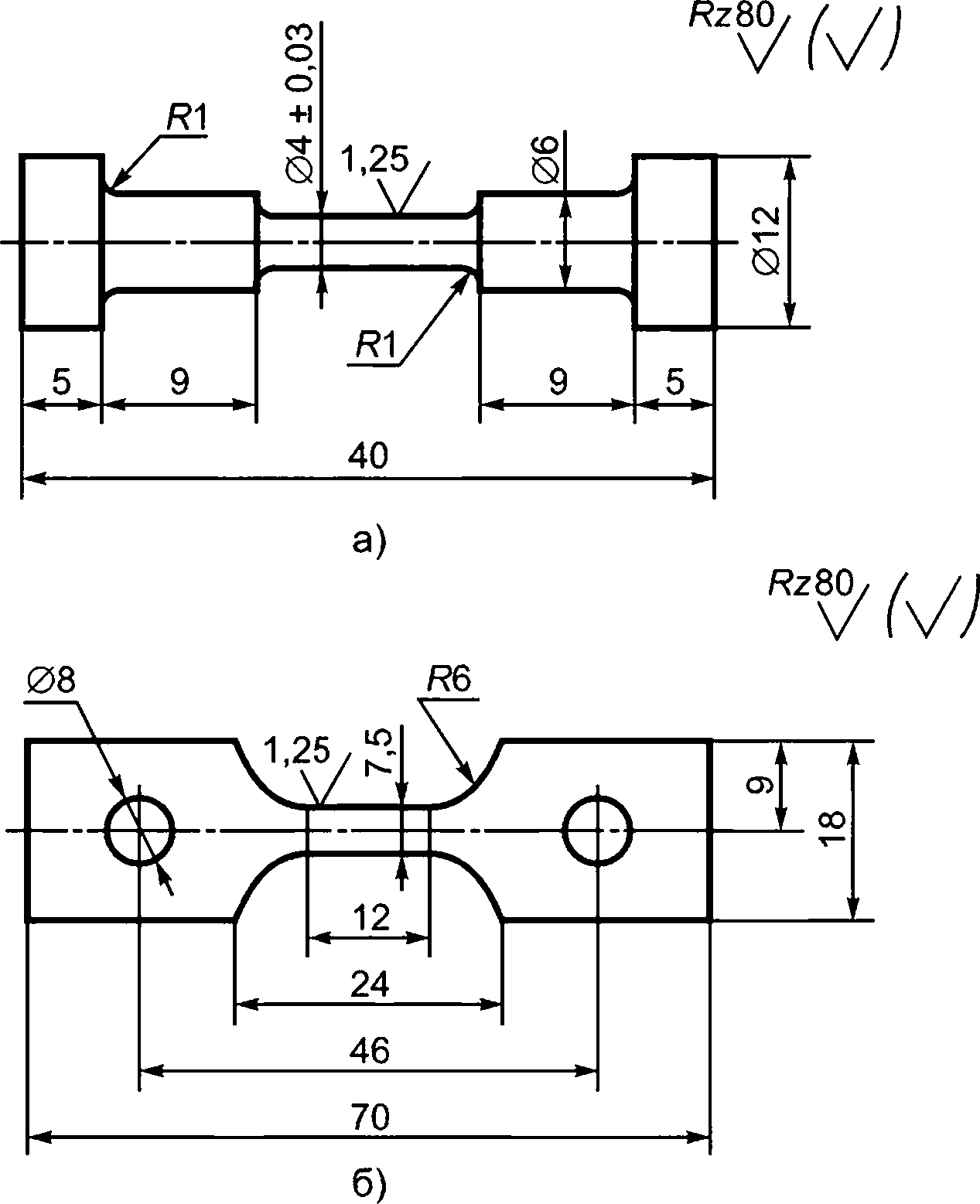
а — образцы круглого сечения; б — образцы прямоугольного сечения Рисунок Г.З — Образцы для испытаний при постоянной осевой нагрузке
Приложение Д (рекомендуемое)
Пакеты для испытаний на контактную коррозию
Используют два вида пакетов для испытаний на контактную коррозию — с возможностью получения данных по изменению механических свойств материала анода (тип 1) и без нее (тип 2), отображенные на рисунках Д.1 и Д.2 соответственно.
А-А
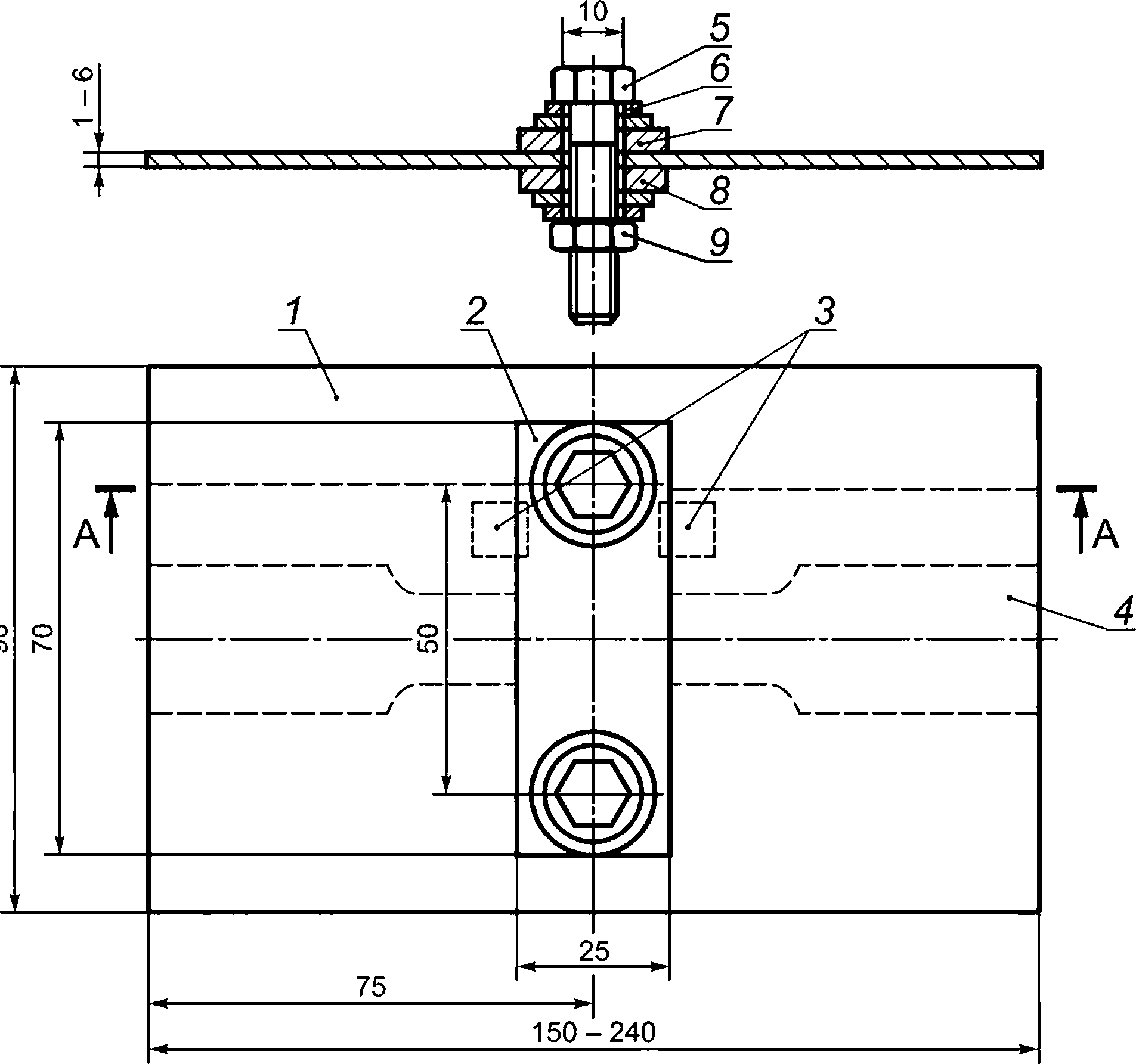
1 — анодная пластина; 2 — катодная пластина; 3 — шлиф; 4 — образец, испытуемый на растяжение; 5 — болт 8><40 мм; 6 — шайба толщиной 1 мм, диаметром 16 мм; 7 — изолирующая шайба толщиной 1 — Змм, диаметром 18—20 мм; 8 — изолирующая втулка; 9 — гайка
Рисунок Д.1 — Пакет для испытаний на контактную коррозию — тип 1
А-А

1 — анодная пластина; 2 — катодная пластина; 3 —болт 8><40 мм; 4 — шайба толщиной 1мм, диаметром 16 мм; 5 — изолирующая шайба толщиной 1—3 мм, диаметром 18—20 мм; б — изолирующая втулка; 7 — гайка; 8 — шлиф
Рисунок Д.2 — Пакет для испытаний на контактную коррозию — тип 2
Приложение Е (рекомендуемое)
Пакеты для испытаний на щелевую коррозию
Используют три типа пакетов для испытаний на щелевую коррозию. Тип 1 предназначен для испытаний на коррозию в щелях и зазорах между металлом и неметаллом (рисунок Е.1). Пакеты по типам 2 и 3 предназначены для испытаний на коррозию в щелях и зазорах между металлами (рисунки Е.2 и Е.З).
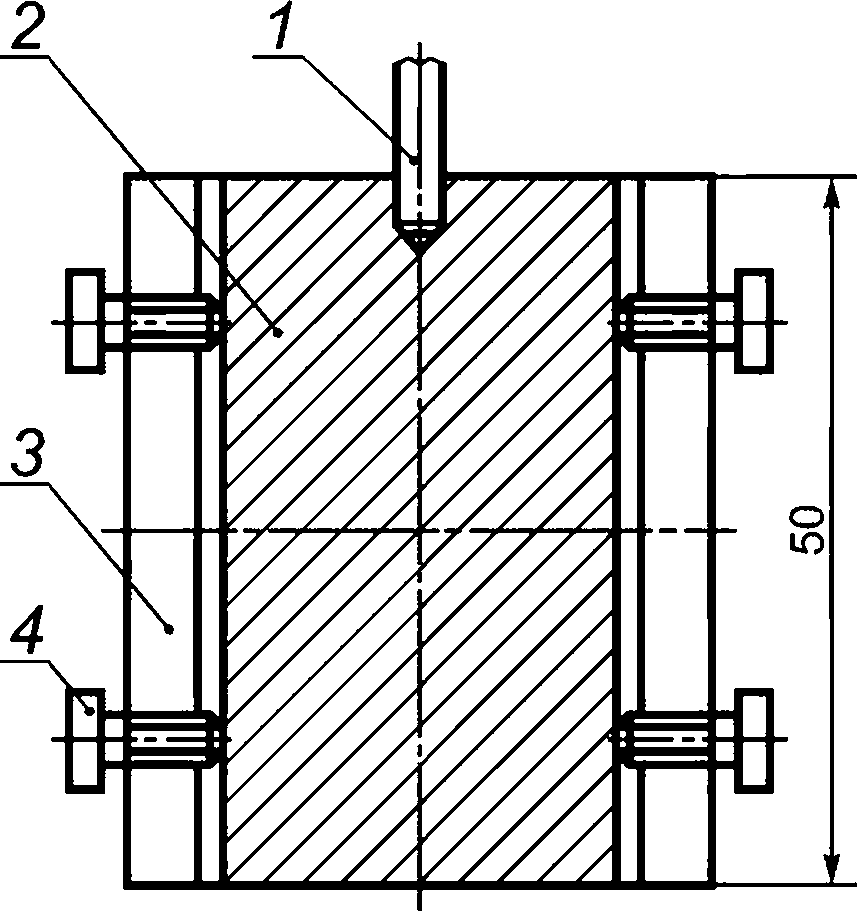
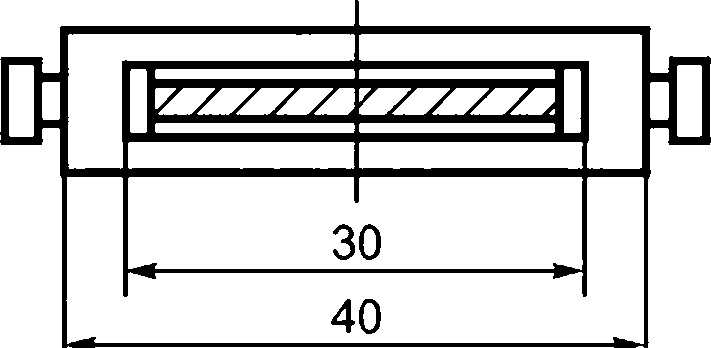
1 — стержень; 2 — образец; 3 — накладка из органического стекла; 4 — винт из органического стекла Рисунок Е.1 — Пакет для испытаний на щелевую коррозию — тип 1
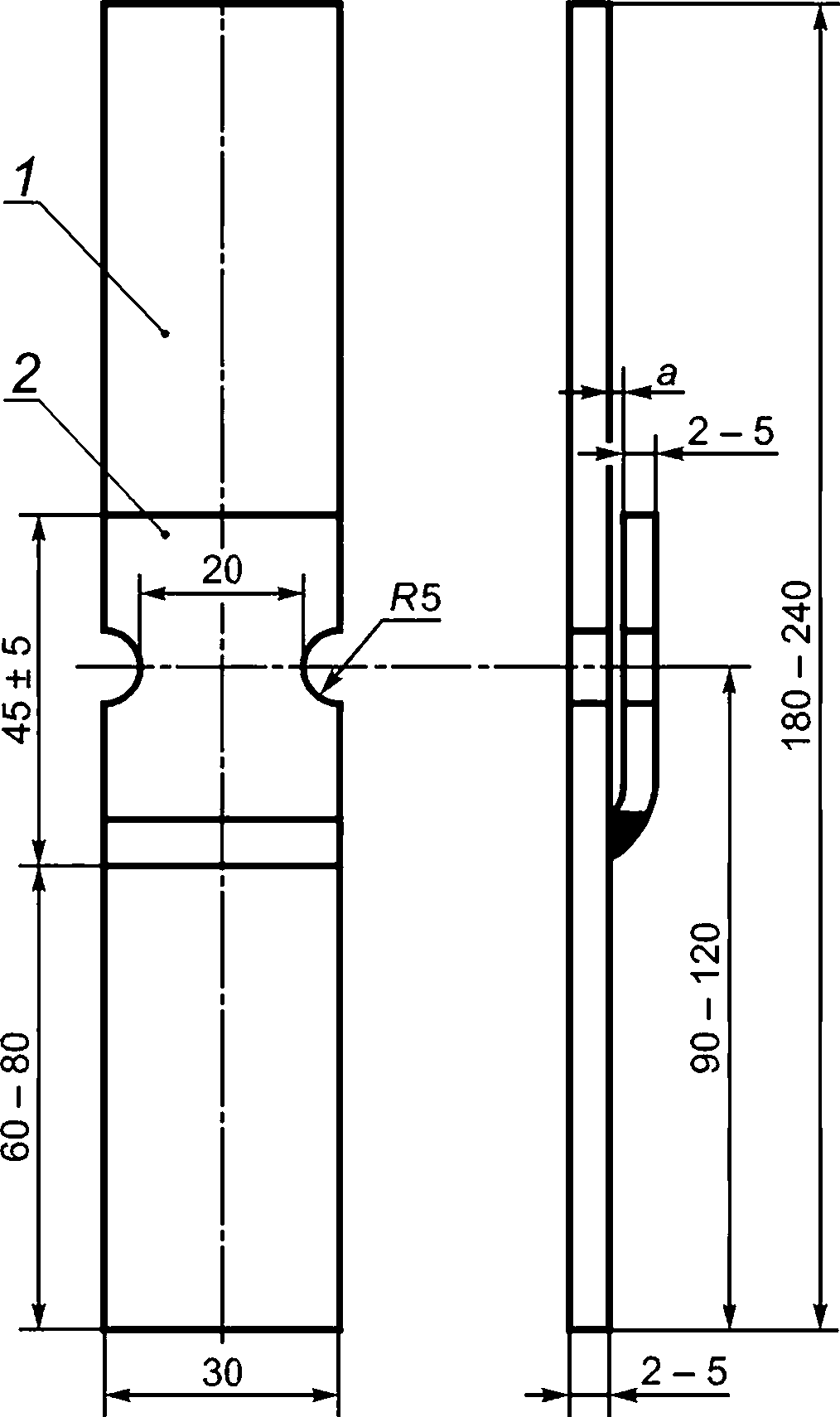
1 — металлический образец; 2 — металлическая накладка
Рисунок Е.2 — Пакет для испытаний на щелевую коррозию — тип 2
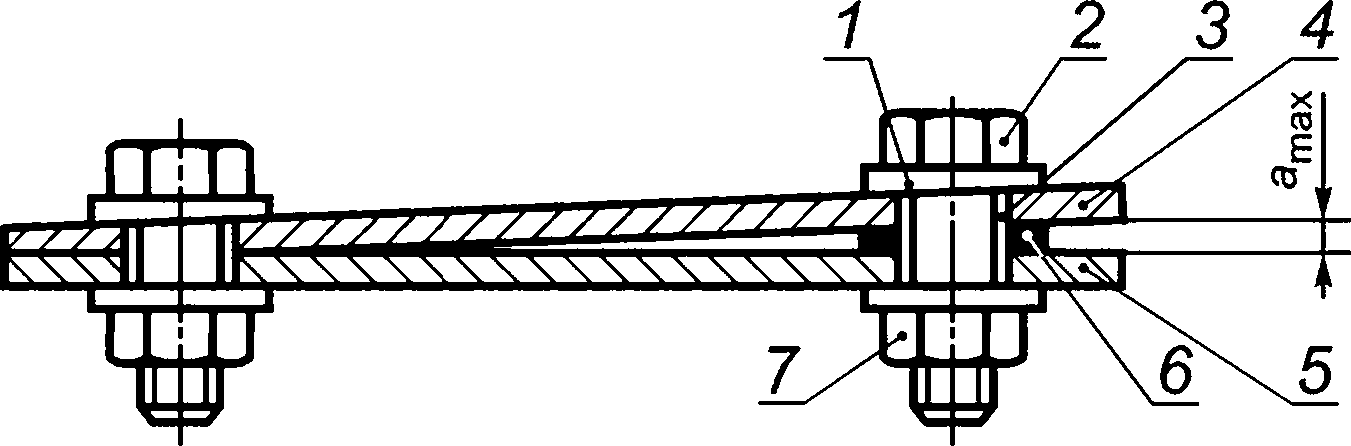
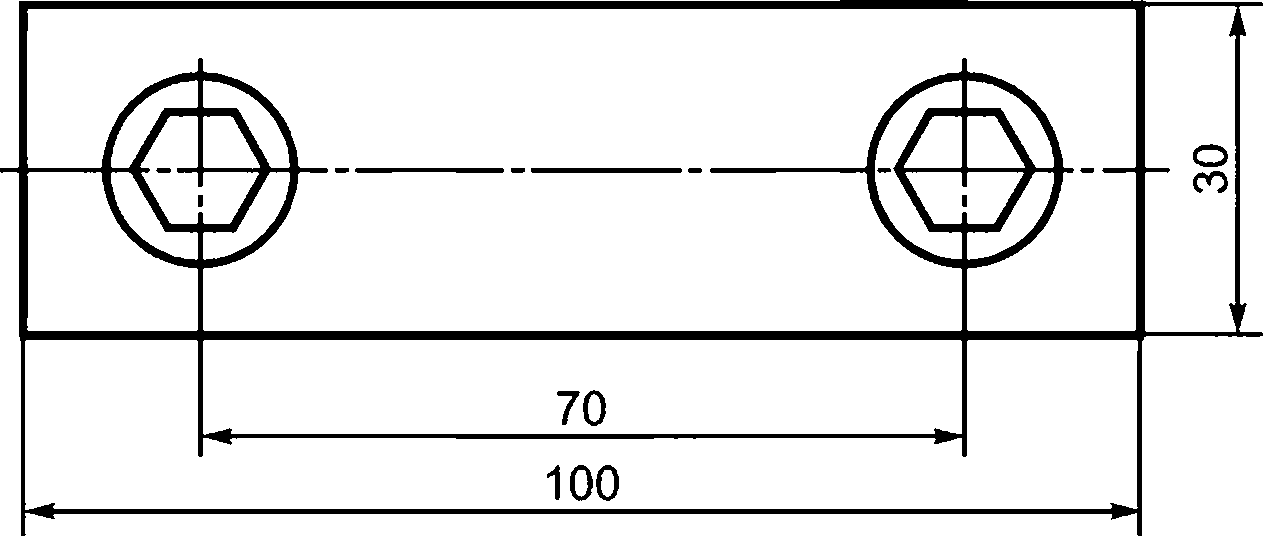
1 — шайба из органического стекла; 2 — болт; 3 — втулка из органического стекла; 4 и 5 — металлические образцы; 6 — прокладка из органического стекла; 7 — гайка
Рисунок Е.З — Пакет для испытаний на щелевую коррозию — тип 3
Приложение Ж (рекомендуемое)
ГОСТ 9.909—2023
Требования к проведению климатических испытаний и оценке свойств
Класс материалов | Условия экспозиции | Вид испытаний | Срок испытаний | Показатели коррозии | Изменение механических свойств | |
качественные | количественные | |||||
Алюминиевые сплавы | Открытая площадка/ навес/ежедневный облив 3 % р-м NaCI/ морской водой/рас-твором морской соли | Испытания на общую коррозионную стойкость | 6 мес, 1, 2, 3, 5, 10, 15 лет При испытаниях с обливом: 3, 6 мес, 1,2, 3 г. | Внешний вид; определение состава продуктов коррозии | Время до появления первых очагов коррозии | Статические по ГОСТ 1497; усталостные по ГОСТ 25.502 |
Скорость коррозии | ||||||
Глубина и характер МКК | ||||||
Оценка параметров питтинговой коррозии: площади, диаметра коррозионных очагов, глубины питтинга | ||||||
Склонность к РСК | ||||||
Определение количества осажденных на поверхности хлоридов | ||||||
Испытания на КР | До разрушения, но не более 2 лет | Внешний вид, характер коррозионных трещин определяется микроскопическим исследованием микрошлифов или фрактографическими исследованиями | Время до разрушения при заданной нагрузке | — |
Класс материалов | Условия экспозиции | Вид испытаний | Срок испытаний | Показатели коррозии | Изменение механических свойств | |
качественные | количественные | |||||
Алюминиевые сплавы | Открытая площадка/ навес/ежедневный облив 3 % р-м NaCI/ морской водой/рас-твором морской соли | Испытания на щелевую коррозию | До разрушения, но не более 2 лет | Внешний вид; наличие в щелях или зазорах продуктов коррозии, очагов коррозии и определение преимущественного вида коррозионного разрушения | Время до разрушения | — |
Металло-полимерные композиционные материалы | Открытая площадка/ навес | Испытания на общую коррозионную стойкость | 6 мес, 1,2, 3, 5, 10, 15 лет | Внешний вид | Статические по ГОСТ 1497; усталостные по ГОСТ 25.502 | |
Стали коррозионностойкие (основной металл, сварные образцы,образцы с покрытиями (ЛКП, гальванические, ИПП и др.), без покрытий) | Открытая площадка/ навес/жалюзийная будка/склад | Испытания на общую коррозионную стойкость | 6 мес, 1,2, 3, 5, 10, 15 лет | Внешний вид (ежемесячно) в течение 1-го года испытаний, далее через 3—6 месяцев; оценка вида коррозионных поражений; определение состава продуктов коррозии | Время до образования первых очагов коррозии (ежедневно до образования первых продуктов коррозии) | Статические по ГОСТ 1497; усталостные по ГОСТ 25.502 |
Скорость коррозии | ||||||
Глубина коррозионных поражений (питтингов, язв и т. п.) | ||||||
Количество поражений на единицу площади | ||||||
Площадь, покрытая продуктами коррозии |
ГОСТ 9.909—2023
Класс материалов | Условия экспозиции | Вид испытаний | Срок испытаний | Показатели коррозии | Изменение механических свойств | |
качественные | количественные | |||||
Стали коррозионностойкие (основной металл, сварные образцы,образцы с покрытиями (ЛКП, гальванические, ИПП и др.), без покрытий) | Открытая площадка/ навес/жалюзийная будка/склад | Испытания на склонность к КР | До появления трещин или разрушения образца, но не более 10 лет | Время до разрушения; внешний вид (ежедневно); металлографические и фрактографические исследования поверхности образцов и изломов с помощью оптической и электронной микроскопии (при необходимости — МРСА) | Влияние приложенных напряжений на время до образования трещин | — |
Определение критического (условно критического) напряжения на выбранной временной базе испытаний | ||||||
Влияние нагревов на сопротивление КР | ||||||
Испытания на щелевую коррозию | 6 мес, 1,2, 3, 5, 10, 15 ле т | Внешний вид (ежемесячно) в течение 1-го года испытаний, далее через 3—6 месяцев; оценка вида коррозионных поражений | Время до образования первых очагов коррозии (ежедневно до образования первых продуктов коррозии) | — | ||
Скорость коррозии | ||||||
Глубина коррозионных поражений (питтингов, язв и т. п.) | ||||||
Количество поражений на единицу площади | ||||||
Площадь, покрытая продуктами коррозии |
ГОСТ 9.909—2023
ю СП
Класс материалов | Условия экспозиции | Вид испытаний | Срок испытаний | Показатели коррозии | Изменение механических свойств | |
качественные | количественные | |||||
Сплавы на никелевой и кобальтовой основе (основной металл, сварные образцы,образцы с покрытиями и без покрытий) | Открытая площадка/ навес/жалюзийная будка/склад | Испытания на общую коррозионную стойкость | 6 мес, 1,2, 3, 5, 10, 15 лет | Внешний вид (ежемесячно) в течение 1-го года испытаний, далее через 3—6 месяцев; оценка вида коррозионных поражений; определение состава продуктов коррозии | Время до образования первых очагов коррозии (ежедневно до образования первых продуктов коррозии) | Статические по ГОСТ 1497; усталостные по ГОСТ 25.502 |
Скорость коррозии | ||||||
Глубина коррозионных поражений (питтингов, язв и т.п.) | ||||||
Количество поражений на единицу площади | ||||||
Площадь, покрытая продуктами коррозии | ||||||
Магниевые сплавы | Открытая площадка/ навес | Испытания на общую коррозионную стойкость | 6 мес, 1, 2, 3, 5, 10, 15 лет | Внешний вид; определение состава продуктов коррозии | Время до появления первых очагов коррозии | — |
Оценка площади и вида коррозионных поражений |
ГОСТ 9.909—2023
ю CD
Класс материалов | Условия экспозиции | Вид испытаний | Срок испытаний | Показатели коррозии | Изменение механических свойств | |
качественные | количественные | |||||
Магниевые сплавы | Открытая площадка/ навес | Испытания на склонность к КР | До появления трещин или разрушения образца, но не более 10 лет | Внешний вид (ежедневно); металлографические и фрактографические исследования поверхности образцов и изломов с помощью оптической и электронной микроскопии | Время до разрушения | |
Влияние приложенных напряжений на время до образования трещин | — | |||||
Определение критического (условно критического) напряжения на выбранной временной базе испытаний Влияние нагревов на сопротивление КР | ||||||
Титановые сплавы | Открытая площадка | Испытания на общую коррозионную стойкость | 6 мес, 1,2, 3, 5, 10, 15 лет | Внешний вид; определение состава продуктов коррозии | Время до появления первых очагов коррозии | Статические по ГОСТ 1497; усталостные по ГОСТ 25.502 |
ГОСТ 9.909—2023
УДК 669.018.9:006.354
МКС 49.025.99
Ключевые слова: климатические центры, станции, площадки, внешние факторы
Редактор Е.Ю. Митрофанова Технический редактор И.Е. Черепкова Корректор Р.А. Ментова Компьютерная верстка А.Н. Золотаревой
Сдано в набор 06.09.2023. Подписано в печать 13.09.2023. Формат 60x8478. Гарнитура Ариал. Усл. печ. л. 3,72. Уч.-изд. л. 2,98.
Подготовлено на основе электронной версии, предоставленной разработчиком стандарта
Создано в единичном исполнении в ФГБУ «Институт стандартизации» , 117418 Москва, Нахимовский пр-т, д. 31, к. 2.