ФЕДЕРАЛЬНОЕ АГЕНТСТВО
ПО ТЕХНИЧЕСКОМУ РЕГУЛИРОВАНИЮ И МЕТРОЛОГИИ
ГОСТР 50.05.02— 2022
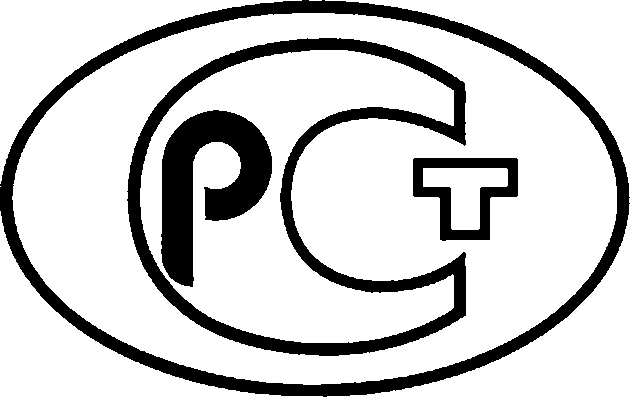
НАЦИОНАЛЬНЫЙ СТАНДАРТ РОССИЙСКОЙ ФЕДЕРАЦИИ
Система оценки соответствия в области использования атомной энергии
ОЦЕНКА СООТВЕТСТВИЯ В ФОРМЕ КОНТРОЛЯ
Унифицированные методики. Ультразвуковой контроль сварных соединений и наплавленных поверхностей
Издание официальное
Москва Российский институт стандартизации 2023
Предисловие
1 РАЗРАБОТАН Акционерным обществом «Российский концерн по производству электрической и тепловой энергии на атомных станциях» (АО «Концерн Росэнергоатом»)
2 ВНЕСЕН Техническим комитетом по стандартизации ТК 322 «Атомная техника»
3 УТВЕРЖДЕН И ВВЕДЕН В ДЕЙСТВИЕ Приказом Федерального агентства по техническому регулированию и метрологии от 19 декабря 2022 г. № 1527-ст
4 ВЗАМЕН ГОСТ Р 50.05.02—2018
Правила применения настоящего стандарта установлены в статье 26 Федерального закона от 29 июня 2015 г. № 162-ФЗ «О стандартизации в Российской Федерации». Информация об изменениях к настоящему стандарту публикуется в ежегодном (по состоянию на 1 января текущего года) информационном указателе «Национальные стандарты», а официальный текст изменений и поправок — в ежемесячном информационном указателе «Национальные стандарты». В случае пересмотра (замены) или отмены настоящего стандарта соответствующее уведомление будет опубликовано в ближайшем выпуске ежемесячного информационного указателя «Национальные стандарты». Соответствующая информация, уведомление и тексты размещаются также в информационной системе общего пользования — на официальном сайте Федерального агентства по техническому регулированию и метрологии в сети Интернет (www.rst.gov.ru)
© Оформление. ФГБУ «Институт стандартизации», 2023
Настоящий стандарт не может быть полностью или частично воспроизведен, тиражирован и распространен в качестве официального издания без разрешения Федерального агентства по техническому регулированию и метрологии
Содержание
1 Область применения
2 Нормативные ссылки
3 Термины и определения
4 Сокращения
5 Общие положения
5.1 Общие требования
5.2 Организация работ по ультразвуковому контролю
5.3 Общие требования при подготовке к ультразвуковому контролю
6 Требования к проведению ультразвукового контроля
6.1 Методики и операции ультразвукового контроля
6.2 Ультразвуковой контроль стыковых сварных соединений
6.3 Ультразвуковой контроль стыковых сварных соединений с антикоррозионной наплавленной поверхностью
6.4 Ультразвуковой контроль угловых и тавровых сварных соединений
6.5 Ультразвуковой контроль сварных соединений на поперечные несплошности
6.6 Выбор параметров ультразвукового контроля наплавленных поверхностей на деталях и на кромках деталей
6.7 Выбор параметров ультразвукового контроля зоны сплавления антикоррозионной наплавленной поверхности из сталей аустенитного класса с основным металлом
6.8 Требования к объектам контроля
6.9 Требования к средствам ультразвукового контроля и образцам
6.10 Требования к персоналу, выполняющему ультразвуковой контроль
7 Проведение ультразвукового контроля
7.1 Подготовка к ультразвуковому контролю
7.2 Разметка объекта контроля при подготовке к проведению ультразвукового контроля
7.3 Последовательность операций ультразвукового контроля сварных соединений
7.4 Настройка аппаратуры
7.5 Проведение ультразвукового контроля
7.6 Анализ результатов ультразвукового контроля
8 Учетная и отчетная документация
9 Требования к метрологическому обеспечению
10 Требования безопасности
Приложение А (справочное) Методика распознавания типа несплошностей по коэффициенту формы
Приложение Б (справочное) Методика определения конфигурации и ориентации несплошностей при изменении угла наблюдения
Приложение В (справочное) Составы контактных сред
Приложение Г (обязательное) Требования к содержанию технологической карты и технологической инструкции ультразвукового контроля
Приложение Д (обязательное) Ультразвуковой контроль по схеме «тандем»
Приложение Е (обязательное) Методика ультразвукового контроля подповерхностной части сварных соединений головными волнами
Приложение Ж (обязательное) Методика ультразвукового контроля стыковых продольных сварных соединений цилиндрических конструкций
Приложение И (обязательное) Методика ультразвукового контроля методом «корневой тандем» сварных соединений биметаллических сосудов и трубопроводов
Приложение К (справочное) Реализуемая чувствительность
Приложение Л (обязательное) Ультразвуковой контроль по схеме «стредл»
Приложение М (обязательное) Методика ультразвукового контроля металла наплавленной поверхности головными волнами
Приложение Н (обязательное) Методика настройки чувствительности дефектоскопа
Приложение П (обязательное) Методика ультразвукового контроля сварных соединений сферических корпусов задвижек трубопроводов
Приложение Р (справочное) Особенности ультразвукового контроля сварных соединений различных конструкций
Приложение С (обязательное) Методика классификации несплошностей по условной протяженности
Приложение Т (обязательное) Сокращенная форма описания несплошностей
Библиография
ГОСТ Р 50.05.02—2022
НАЦИОНАЛЬНЫЙ СТАНДАРТ РОССИЙСКОЙ ФЕДЕРАЦИИ
Система оценки соответствия в области использования атомной энергии
ОЦЕНКА СООТВЕТСТВИЯ В ФОРМЕ КОНТРОЛЯ
Унифицированные методики. Ультразвуковой контроль сварных соединений и наплавленных поверхностей
Conformity assessment system for the use of nuclear energy. Conformity assessment in the form of testing. Unified procedures. Ultrasonic testing of welded joints and cladded surfaces
Дата введения — 2023—03—01
1 Область применения
1.1 Настоящий стандарт распространяется на оценку соответствия сварных соединений, наплавленных поверхностей и зоны сплавления наплавленных поверхностей (далее — объекты контроля)1) продукции2) в форме контроля (ультразвукового) при ее изготовлении, монтаже и эксплуатации.
1.2 Настоящий стандарт содержит унифицированные методики оценки соответствия в форме контроля (ультразвукового) объектов контроля продукции, изготовленной в соответствии с [3]—[9]. Нормы оценки качества объектов контроля продукции указаны в [2], [4], [10], документах по стандартизации, а также конструкторской документации, технологической документации, устанавливающих требования к оценке соответствия металла продукции.
2 Нормативные ссылки
В настоящем стандарте использованы нормативные ссылки на следующие стандарты:
ГОСТ 2789 Шероховатость поверхности. Параметры и характеристики
ГОСТ 8433 Вещества вспомогательные ОП-7 и ОП-Ю. Технические условия
ГОСТ 23829 Контроль неразрушающий акустический. Термины и определения
ГОСТ Р 50.04.03—2018 Система оценки соответствия в области использования атомной энергии. Оценка соответствия в форме испытаний. Аттестационные испытания технологий сварки (наплавки)
ГОСТ Р 50.04.07 Система оценки соответствия в области использования атомной энергии. Оценка соответствия в форме испытаний. Аттестационные испытания систем неразрушающего контроля
ГОСТ Р 50.05.05—2018 Система оценки соответствия в области использования атомной энергии. Оценка соответствия в форме контроля. Унифицированные методики. Ультразвуковой контроль основных материалов (полуфабрикатов)
ГОСТ Р 50.05.11 Система оценки соответствия в области использования атомной энергии. Персонал, выполняющий неразрушающий и разрушающий контроль металла. Требования и порядок подтверждения компетентности
ГОСТ Р 50.05.14 Система оценки соответствия в области использования атомной энергии. Средства ультразвукового контроля основных материалов, сварных соединений и наплавленных поверхностей оборудования и трубопроводов атомных энергетических установок. Общие требования
1) Качество и свойства материалов должны удовлетворять требованиям документов по стандартизации, включенных в Сводный перечень документов по стандартизации, предусмотренный [1].
2) В настоящем стандарте под продукцией понимается оборудование, трубопроводы и другие элементы атомных станций (определены в [2]), на которые распространяются требования [2]—[10].
Издание официальное
ГОСТ Р 50.05.15 Система оценки соответствия в области использования атомной энергии. Оценка соответствия в форме контроля. Неразрушающий контроль. Термины и определения
ГОСТ Р 50.05.16 Система оценки соответствия в области использования атомной энергии. Оценка соответствия в форме контроля. Неразрушающий контроль. Метрологическое обеспечение
ГОСТ Р 55724—2013 Контроль неразрушающий. Соединения сварные. Методы ультразвуковые
ГОСТ Р 55725 Контроль неразрушающий. Преобразователи ультразвуковые пьезоэлектрические. Общие технические требования
ГОСТ Р 58904/ISO/TR 25901-1:2016 Сварка и родственные процессы. Словарь. Часть 1. Общие термины
ГОСТ Р ИСО 5577 Контроль неразрушающий. Ультразвуковой контроль. Словарь
Примечание — При пользовании настоящим стандартом целесообразно проверить действие ссылочных стандартов в информационной системе общего пользования — на официальном сайте Федерального агентства по техническому регулированию и метрологии в сети Интернет или по ежегодному информационному указателю «Национальные стандарты», который опубликован по состоянию на 1 января текущего года, и по выпускам ежемесячного информационного указателя «Национальные стандарты» за текущий год. Если заменен ссылочный стандарт, на который дана недатированная ссылка, то рекомендуется использовать действующую версию этого стандарта с учетом всех внесенных в данную версию изменений. Если заменен ссылочный стандарт, на который дана датированная ссылка, то рекомендуется использовать версию этого стандарта с указанным выше годом утверждения (принятия). Если после утверждения настоящего стандарта в ссылочный стандарт, на который дана датированная ссылка, внесено изменение, затрагивающее положение, на которое дана ссылка, то это положение рекомендуется применять без учета данного изменения. Если ссылочный стандарт отменен без замены, то положение, в котором дана ссылка на него, рекомендуется применять в части, не затрагивающей эту ссылку.
3 Термины и определения
В настоящем стандарте применены термины по ГОСТ 23829, ГОСТ Р 50.05.15, ГОСТ Р 58904, ГОСТ Р 55725, ГОСТ Р ИСО 5577, а также следующие термины с соответствующими определениями:
3.1
браковочный уровень чувствительности: Уровень чувствительности, при превышении которого выявленная несплошность относится к дефекту.
[[6], приложение № 2]
3.2 второй критический угол: Наименьший угол падения продольной волны, при котором поперечная преломленная волна распространяется вдоль поверхности и превращается в поверхностную волну (волну Рэлея).
3.3 волнистость поверхности сканирования: Отношение максимальной стрелы прогиба (максимального отклонения от плоскостности) к периоду волнистости.
3.4 головная волна: Комплекс волн, возбуждаемых на границе раздела и в приграничных (соприкасающихся) средах при падении продольной волны под первым критическим углом, фронты которых распространяются со скоростью продольной волны в нижней среде.
3.5
контрольный уровень чувствительности (уровень фиксации): Уровень чувствительности, при котором производят регистрацию несплошностей и оценку их допустимости по условным размерам и количеству.
[[6], приложение № 2]
3.6 методика контроля: Документ, содержащий совокупность процедур, условий проведения и требований к средствам контроля, реализующих один или несколько способов контроля, выполнение которых обеспечивает получение информации об объекте контроля или результатах контроля.
3.7 наплавленная поверхность: Слой металла или сплава, нанесенный на поверхность объекта контроля посредством сварки плавлением.
3.8 первый критический угол: Наименьший угол падения продольной волны, при котором преломленная продольная волна распространяется вдоль поверхности.
3.9
поисковый уровень чувствительности: Уровень чувствительности, устанавливаемый при поиске несплошностей.
[ГОСТ Р 55724—2013, пункт 3.1.26]
3.10 схема прозвучивания: Документально оформленный порядок сканирования объекта контроля выбранным(и) в соответствии с требованиями методик контроля пьезоэлектрическим(и) преобразователем(ями) с целью полного прозвучивания наплавленного металла сварного соединения (металла наплавленной поверхности), с учетом расположения возможных несплошностей и условий доступности контроля.
Примечание — Сварное соединение включает три характерные зоны, образующиеся во время сварки: зону сварного шва, зону сплавления и зону термического влияния (околошовную зону).
3.11 технологическая инструкция по неразрушающему контролю: Документ, регламентирующий объемы и технологию контроля качества металла (основного и наплавленных поверхностей) на каждом конкретном объекте контроля, в соответствии с унифицированной методикой контроля, а также содержащий нормы оценки качества.
3.12 технологическая карта контроля: Производственная контрольная документация или ее часть, регламентирующая средства, параметры, последовательность и содержание операций, в соответствии с которыми проводится неразрушающий контроль и оценка качества.
3.13 угловой отражатель: Искусственный отражатель в настроечном образце типа зарубки, прямоугольного паза, сегмента и т. п., предназначенный для настройки чувствительности.
3.14 шкала амплитуда-расстояние-диаметр; АРД-шкала: АРД-диаграмма, на которой зависимости между амплитудой, расстоянием и диаметром представлены в виде горизонтальных линий (строк).
3.15
эквивалентная площадь несплошности: Площадь плоскодонного искусственного отражателя, ориентированного перпендикулярно акустической оси преобразователя и расположенного на том же расстоянии от поверхности ввода, что и несплошность, при которой значения сигнала акустического прибора от несплошности и отражателя равны.
[ГОСТ Р 50.05.05—2018, пункт 3.18]
4 Сокращения
В настоящем стандарте использованы следующие сокращения:
АРК — кривая амплитуда — расстояние;
АСД — автоматический сигнализатор дефекта;
ВРЧ — временная регулировка чувствительности;
ГЦТ — главный циркуляционный трубопровод;
КД — конструкторская документация;
КО — калибровочный образец;
НП — наклонный преобразователь;
НО — настроечный образец;
ОК — объект контроля;
ПГВ — преобразователь головных волн;
ПС — прямой совмещенный;
ПРС — прямой раздельно-совмещенный;
ПЭ — пьезоэлемент;
ПЭП — пьезоэлектрический преобразователь;
PC — раздельно-совмещенный;
СС — сварное соединение;
ТД — техническая документация;
ТИ — технологическая инструкция;
ТКК — технологическая карта контроля;
УЗ — ультразвук (ультразвуковой);
УЗК — ультразвуковой контроль.
5 Общие положения
5.1 Общие требования
5.1.1 Оценке соответствия в форме контроля (ультразвукового) подлежат:
- стыковые, угловые и тавровые СС деталей из сталей перлитного класса и высокохромистых сталей, выполненных дуговой и электрошлаковой сваркой низколегированными сварочными материалами с полным проплавлением, с толщиной свариваемых деталей от 5,5 до 400,0 мм;
- металл наплавленных поверхностей [в том числе предварительных (переходных)] толщиной от 4 до 40 мм, выполненных сварочными материалами перлитного класса и высокохромистыми материалами на кромках деталей из сталей перлитного класса, и зоны сплавления основного металла с металлом наплавленных поверхностей из сталей аустенитного класса, выполненных на поверхности и кромках свариваемых деталей с толщиной основного металла не менее 10 мм;
- зоны сплавления основного металла с металлом антикоррозионных наплавленных поверхностей из сталей аустенитного класса толщиной 4 мм и более на деталях (ОК) из сталей перлитного класса.
Примечание — СС (наплавленные поверхности) при проведении УЗК считаются однотипными при соблюдении требований к классификации групп однотипных сварных соединений (наплавленных поверхностей) в соответствии с ГОСТ Р 50.04.03—2018 (подраздел 6.4), а также при отнесении к одному диапазону (в пределах 1 мм) следующих величин:
- толщин в соответствии с таблицами 1—5;
- номинальных значений диаметров.
5.1.2 Радиус кривизны околошовной наружной поверхности должен быть не менее 150,0 мм для продольных швов, 100,0 мм для наплавленных поверхностей, 12,5 мм для кольцевых швов. Внутренний радиус кривизны свариваемой детали при УЗК угловых и тавровых швов должен быть не менее 50,0 мм.
5.1.3 УЗК по методикам, представленным в настоящем стандарте, предназначен для выявления и измерения контактным способом несплошностей, эквивалентной площадью не менее величин, указанных в [2], [4], [10], документах по стандартизации, а также КД, ТД, устанавливающих требования к оценке соответствия объектов контроля оборудования и трубопроводов атомных энергетических установок и других элементов атомных станций. Характер и действительные размеры несплошности не определяют. При оценке формы, ориентации и конфигурации несплошностей используют методики, приведенные в приложениях А и Б.
5.1.4 УЗК по настоящему стандарту не предназначен для выявления несплошностей на фоне мешающих отражателей в виде неровностей усиления и корневой части шва, конструктивных особенностей свариваемых деталей и структурных неоднородностей, если не предусмотрены специальные способы их обнаружения и идентификации. УЗК по настоящему стандарту не обеспечивает выявление несплошностей в пределах «мертвой» зоны ПЭП, а также непосредственно под усилением шва и в придонной области.
Минимизировать «мертвую» зону следует путем применения ПЭП с большим углом ввода и/или большей номинальной частотой, а также следует выбирать схему контроля, обеспечивающую прозву-чивание слоя металла, находящегося в «мертвой зоне» однократно отраженным лучом, и/или применять методику контроля головными волнами.
Проверку «мертвой» зоны следует осуществлять после настройки чувствительности по образцу СО-2 согласно ГОСТ Р 50.05.14.
5.1.5 В СС УЗК подлежит зона контроля — металл шва, зоны сплавления и термического влияния. При этом ширина контролируемой зоны основного металла определена КД, устанавливающей требования к оценке соответствия металла СС и наплавленных поверхностей.
5.1.6 В СС деталей различной номинальной толщины ширину указанной зоны определяют отдельно для каждой из свариваемых деталей.
5.1.7 Ширину контролируемых участков основного металла определяют от границы сварного шва, включая наплавленные поверхности на кромках (при их наличии).
5.1.8 Приемочный контроль должен выполняться после окончательной термообработки СС и восстановления наплавленных поверхностей (если они предусмотрены технологическим процессом), при этом следует учитывать, что результаты операционного и приемочного контроля могут не совпадать. 4
5.1.9 Требования по созданию необходимых условий (5.2, 5.3.1) для выполнения работ по УЗК являются обязательными для организации, предоставляющей ОК.
5.10 Проведение ручного УЗК средствами контроля без автоматической записи процесса сканирования с 00:00 до 06:00 местного времени не допускается.
5.2 Организация работ по ультразвуковому контролю
5.2.1 Для проведения УЗК, осуществления технологической подготовки к УЗК, проведения подготовительных, проверочных работ, а также для хранения аппаратуры, ПЭП, образцов, вспомогательных приспособлений и другого инвентаря организуют подразделения (лаборатории, участки, группы) УЗК. Подразделения УЗК должны соответствовать требованиям [2] (раздел VI), располагать соответствующими площадями и помещениями.
5.2.2 Подразделение УЗК должно быть оснащено:
- средствами измерений и контроля (УЗ-дефектоскопами с комплектом ПЭП и соединительными кабелями; металлическими измерительными линейками, штангенциркулями, металлическими рулетками и другими необходимыми СИ);
- комплектами КО, НО;
- вспомогательными устройствами (например, шаблонами, шкалами);
- розетками сети переменного тока напряжением 110 и/или 220 В, частотой 50 Гц, с заземлением; стабилизатором питающего напряжения (при необходимости);
Также подразделение УЗК оснащают:
- подводкой горячей и холодной воды;
- емкостями с контактной средой;
- лабораторными и канцелярскими столами;
- стеллажами, шкафами для хранения аппаратуры, образцов, запасных частей, документации;
- шкафами для одежды и обуви.
Подразделение УЗК может быть дооснащено:
- электроизмерительной и радиотехнической аппаратурой для проведения проверочных и ремонтных работ (при наличии подразделения по ремонту);
- электротельфером;
- слесарным инструментом;
- тележками для установки и транспортирования дефектоскопов;
- оборудованием и материалами, необходимыми для проведения УЗК в конкретных условиях.
5.2.3 Участки УЗК в цехе, на монтажной площадке также оснащают роликоопорами, кантователями, розетками сети переменного тока напряжением 110 и/или 220 В, частотой 50 Гц, имеющими заземление.
5.2.4 При проведении УЗК должна обеспечиваться освещенность на поверхности в зоне контроля не менее 500 лк.
5.2.5 При проведении УЗК крупногабаритных ОК, а также в условиях монтажа и ремонта должны быть обеспечены следующие условия:
- леса и подмостки должны обеспечивать безопасное и удобное расположение специалиста по УЗК и аппаратуры относительно зоны контроля ОК;
- не допускается проведение работ, вызывающих вибрацию и загрязнение абразивной пылью ОК в зоне контроля, на расстоянии менее чем 10 м;
- яркие источники света (например, посты электросварки, резки), расположенные на расстоянии менее 15 м от места проведения УЗК, должны быть экранированы;
- при ярком дневном свете или сильном искусственном освещении, затрудняющем наблюдение изображения на экране дефектоскопа, должны быть приняты меры по затемнению экрана дефектоскопа или рабочего места.
5.2.6 Колебания напряжения в электрической сети, к которой подключают дефектоскопы, не должны превышать значений, указанных в техническом описании дефектоскопа.
При больших колебаниях напряжения дефектоскопы следует подключать через стабилизаторы.
5.2.7 УЗК проводят при температуре окружающего воздуха и металла ОК в зоне контроля от 5 °C до 40 °C.
Допускается проведение контроля в более широком температурном диапазоне при условии наличия средств контроля, технические характеристики которых позволяют проводить контроль при тем-5
пературах, превышающих установленный диапазон. При этом персонал, проводящий контроль, должен быть обеспечен средствами индивидуальной защиты от воздействия высоких или низких температур соответственно.
5.2.8 Для ОК, допускающих кантование, проведение УЗК в потолочном положении не допускается.
5.2.9 УЗК проводят группой, состоящей из двух (или более) специалистов по УЗК. При этом как минимум один из них должен иметь право выдачи заключения по результатам УЗК.
5.2.10 Контактная среда должна обладать достаточными смачиваемостью, вязкостью и однородностью для обеспечения стабильного акустического контакта. Также она должна быть прозрачной для УЗ в рабочем диапазоне частот и безвредной для специалиста по УЗК. Контактная среда должна удовлетворять требованиям пожарной безопасности организации, проводящей УЗК, легко удаляться с поверхности и не вызывать коррозии ОК. При большой кривизне поверхности ОК в зоне контроля, а также при проведении УЗК в вертикальном и/или потолочном положениях, следует использовать контактную среду более густой консистенции.
5.2.11 Вещества, входящие в состав контактной среды, и сама контактная среда не являются дефектоскопическими материалами и входному контролю не подлежат.
5.2.12 Состав некоторых применяемых контактных сред приведен в приложении В.
5.3 Общие требования при подготовке к ультразвуковому контролю
5.3.1 Подготовку поверхности СС или наплавленной поверхности в зоне контроля для проведения УЗК и ее очистку после его проведения (в т. ч. удаление контактной среды) осуществляют соответствующие подразделения организации — владельца или изготовителя ОК. Выполнение данных операций в обязанности специалиста по УЗК не входит.
5.3.2 До проведения УЗК на все подлежащие контролю СС и наплавленные поверхности (в соответствии с 5.1.1) или группы однотипных СС и наплавленных поверхностей составляют ТИ и/или ТКК. УЗК проводится в соответствии с ТИ и/или ТКК (приложение Г).
ТИ и/или ТКК разрабатывает специалист, квалификация которого подтверждена в соответствии с требованиями ГОСТ Р 50.05.11, имеющий уровень компетентности специалиста с правом выдачи заключения по результатам УЗК или уровень компетентности специалиста с правом проведения оценки компетентности персонала.
5.3.3 Выбор схем прозвучивания, параметров УЗК проводят в соответствии с требованиями раздела 6.
6 Требования к проведению ультразвукового контроля
6.1 Методики и операции ультразвукового контроля
6.1.1 Схемы прозвучивания, характеристики ПЭП при УЗК стыковых, угловых и тавровых СС трубопроводов, сосудов и плоских конструкций выбирают исходя из необходимости обеспечения прозвучивания центральным лучом всего сечения СС с учетом его толщины и конструкции.
При УЗК СС и металла наплавленных поверхностей применяют следующие операции прозвучивания:
а) продольными волнами с углом ввода 0’ (ПС и ПРС ПЭП) (примеры схем реализации приведены на рисунке 1а);
б) поперечными волнами (пример схемы реализации приведен на рисунке 16) с углом ввода более 33,5°;
в) головными волнами (пример схемы реализации приведен на рисунке 1в);
г) поперечными волнами по схемам «тандем» или «корневой тандем» (пример схемы реализации приведен на рисунке 1г);
д) прозвучивание по стредл-схеме (пример схемы реализации приведен на рисунке 1ж).
а — прозвучивание продольными волнами с углом ввода 0° (ПС и ПРС ПЭП); б — прозвучивание поперечными волнами одним УЗ-пучком с углом ввода более 33,5°; в — прозвучивание головными волнами; г — прозвучивание поперечными волнами по схемам «тандем» или «корневой тандем»; д — прозвучивание по стредл-схеме
Рисунок 1 — Операции прозвучивания
6.2 Ультразвуковой контроль стыковых сварных соединений
6.2.1 Общие требования по УЗК стыковых СС плоских конструкций6.2.1.1 Стыковые СС плоских конструкций с толщиной свариваемых деталей от 5,5 до 400,0 мм включительно при наличии доступа контролируют НП прямым лучом с двух поверхностей с обеих сторон шва по схемам, приведенным на рисунках 2а (при отсутствии усиления шва), 2е (при наличии усиления шва).
Стыковые СС плоских конструкций с толщиной свариваемых деталей от 5,5 до 60,0 мм включительно допускается контролировать НП с одной поверхности прямым и однократно отраженным лучами с обеих сторон шва (рисунок 2в, 2и).
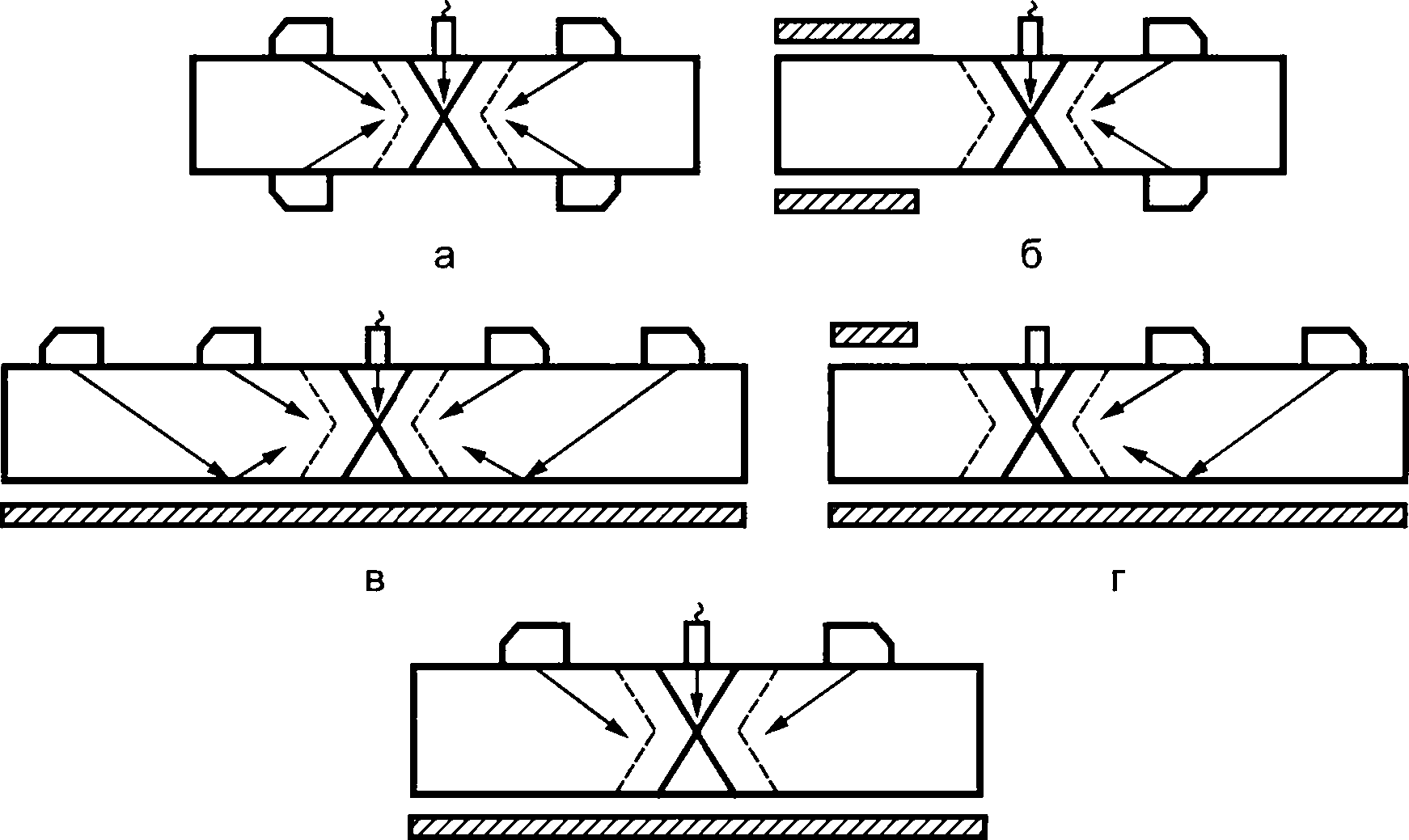
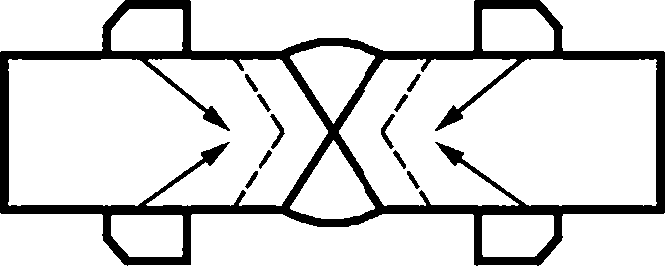
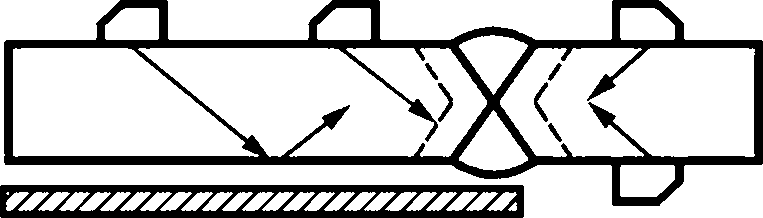
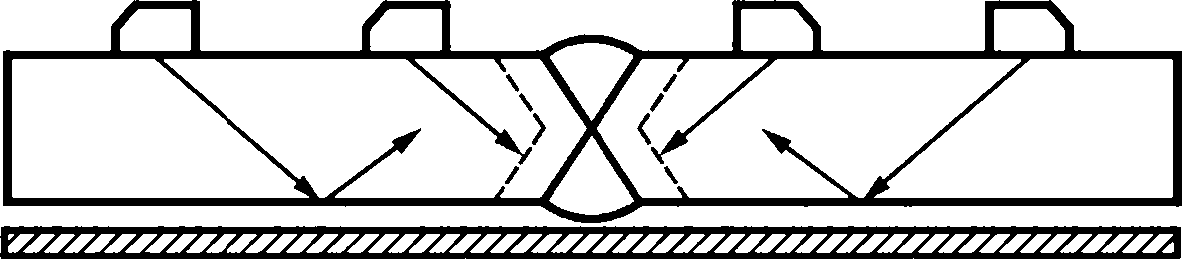

а — УЗК ПС (ПРС) и НП СС без усиления шва прямым лучом с четырех сторон; б —УЗК ПС (ПРС) и НП СС без усиления шва прямым лучом с двух поверхностей с одной стороны; в — УЗК ПС (ПРС) и НП СС без усиления шва прямым и однократно отраженным УЗ-лучами с двух сторон с одной поверхности; г — УЗК ПС (ПРС) и НП СС без усиления шва прямым и однократно отраженным УЗ-лучами с одной стороны с одной поверхности; д — УЗК ПС (ПРС) и НП СС без усиления шва прямым лучом с двух сторон с одной поверхности; е — УЗК НП СС прямым лучом при наличии усиления шва с четырех сторон СС; ж — УЗК НП СС прямым и однократно отраженным УЗ-лучами при наличии усиления шва с трех сторон СС; и — УЗК НП СС прямым и однократно отраженным лучами при наличии усиления шва при отсутствии доступа с одной поверхности; к — УЗК НП СС прямым лучом при наличии усиления шва и отсутствии доступа с одной стороны с двух поверхностей; л — УЗК НП СС прямым и однократно отраженным лучами при наличии усиления шва и отсутствии доступа с трех сторон СС
Рисунок 2 — Схемы УЗК стыковых СС НП и ПС ПЭП
6.2.1.2 При отсутствии доступа с одной или нескольких сторон (поверхностей) УЗК стыковых СС плоских конструкций с толщиной свариваемых деталей от 5,5 до 60,0 мм включительно выполняют прямым или прямым и однократно отраженным лучами с одной или обеих сторон шва (в зависимости от наличия доступа) по схемам, приведенным на рисунке 26 — г, ж, и, л.
При отсутствии доступа с одной или нескольких сторон (поверхностей) УЗК стыковых СС плоских конструкций с толщиной свариваемых деталей свыше 60,0 мм выполняют прямым лучом с одной или обеих сторон шва (в зависимости от наличия доступа и усиления шва) по схемам, приведенным на рисунке 26, д, к.
6.2.1.3 УЗК СС проводят с использованием ПЭП с параметрами в соответствии с таблицей 1.
Таблица 1 — Параметры НП (номинальные значения) для УЗК СС в зависимости от номинальной толщины свариваемых деталей
Номинальная толщина свариваемых деталей, мм | Частота, МГц | Угол ввода при УЗК, град | |
прямым лучом | однократно отраженным лучом | ||
От 5,5 до 9,0 включ. | От 4,0 до 6,0 | 70, 72 | 65, 70 |
Св. 9,0 до 12,0 включ. | От 4,0 до 6,0 | 65, 70 | 65, 70 |
Св. 12,0 до 20,0 включ. | От 2,5 до 5,0 | 65, 70 | 65, 70 |
Св. 20 до 40 включ. | От 2,5 до 4,0 | 65, 70 | 45, 50 |
Св. 40 до 60 включ. | От 1,8 до 4,0 | 65, 70 | 45, 50 |
Св. 60 до 100 включ. | От 1,8 до 2,5 | 45, 50, 60, 65 | Не допускается |
Св. 100 до 400 включ. | От 1,0 до 2,0 | 45, 50, 60, 65 | Не допускается |
Примечания
|
6.2.1.4 Стыковые СС с удаленным усилением шва контролируют дополнительно ПС или ПРС ПЭП, выбираемым по таблице 2, схемы прозвучивания 2а—д.
6.2.1.5 Проведение УЗК с одной стороны поверхности прямым и однократно отраженным лучами допускается в тех случаях, когда конструкция СС или основной металл одной из деталей не позволяют проводить УЗК с обеих сторон (поверхностей) соединения (рисунок 2л), например, СС детали из проката с литыми деталями или наличие несплошностей в основном металле.
Таблица 2 — Параметры ПЭП для УЗК СС в зависимости от номинальной толщины свариваемых деталей
Номинальная толщина свариваемых деталей, мм | Частота, МГц | Тип ПЭП |
Св. 5,5 до 20,0 включ. | От 4,0 до 6,0 | ПРС |
Св. 20,0 до 40,0 включ. | От 2,5 до 4,0 | |
Св. 40,0 до 60,0 включ. | От 1,8 до 4,0 | ПС+ПРС |
Св. 60,0 до 400,0 включ. | От 1,25 до 2,50 | ПС+ПРС |
Примечания
|
6.2.1.6 При УЗК СС, сваренных в узкую разделку до 10°, а также СС с щелевой и К-образной разделкой схему контроля (рисунок 2) следует выбирать, исходя из обеспечения максмального прозвучивания всего объема СС. Для выявления вертикально ориентированных плоскостных несплошностей (типа трещин) и несплавлений по кромкам в СС рекомендуется дополнительно проводить УЗК по схеме «тандем» с использованием ПЭП с углом ввода 45° или 50° на частоте от 1,8 до 2,5 МГц (приложение Д).
6.2.1.7 Стыковые СС с толщиной свариваемых деталей 34 мм и более дополнительно контролируют на отсутствие поперечных несплошностей в соответствии с 6.5.
6.2.1.8 На отсутствие вертикально ориентированных несплошностей (при наличии соответствующих указаний в КД) УЗК проводят по методике с применением головных волн (приложение Е).
6.2.2 Требования по УЗК продольных стыковых СС
Продольные стыковые СС трубопроводов и цилиндрических конструкций контролируют в соответствии с приложением Ж.
6.2.3 Требования по УЗК стыковых СС секторных отводов
СС секторных отводов контролируют так же, как и кольцевые стыковые СС.
6.2.4 Требования по УЗК кольцевых стыковых СС
6.2.4.1 Стыковые СС с толщиной свариваемых деталей менее 60 мм, представляющие собой кольцевые швы трубопроводов и сосудов, контролируют:
- с одной поверхности прямым и однократно отраженным лучами (рисунок 2в, и), если внутренний диаметр менее 800 мм;
- так же, как стыковые СС плоских конструкций, если внутренний диаметр не менее 800 мм.
6.2.4.2 В остальных случаях при УЗК кольцевых СС схему контроля (рисунок 2) следует выбирать, исходя из обеспечения максимального прозвучивания всего объема СС.
6.2.4.3 При УЗК кольцевых стыковых СС трубопроводов и цилиндрических конструкций диаметром D не более 15g, где q — ширина контактной поверхности ПЭП, используют ПЭП, у которых контур рабочей поверхности соответствует радиусу кривизны поверхности ОК в зоне контроля.
6.2.4.4 При снятом усилении шва для реализации возможности проведения УЗК по схемам, приведенным на рисунке 2а—д, следует использовать ПРС, у которых контур рабочей поверхности соответствует радиусу кривизны внешней или внутренней поверхности ОК в зоне контроля (следует учитывать, что в процессе сканирования ПРС положение разделительного экрана должно быть перпендикулярно к оси трубопровода и цилиндрических конструкций) и ПС при условии соблюдения требований по величине зазора между поверхностью металла СС в зоне контроля и ПЭП — он не должен превышать 0,2 мм.
6.2.4.5 При УЗК кольцевых стыковых СС трубопроводов и цилиндрических конструкций настройку чувствительности выполняют на НО, соответствующих по радиусу кривизны и глубине залегания искусственных отражателей в соответствии с толщиной свариваемых деталей ОК в зоне контроля, изготовленным в соответствии с требованиями 6.9.6 и ГОСТ Р 50.05.14. В случае использования ПРС допускается применение НО с соответствующим ОК в зоне контроля радиусом кривизны при наличии плоскодонных отражателей на необходимой для корректной настройки глубине.
6.3 Ультразвуковой контроль стыковых сварных соединений с антикоррозионной наплавленной поверхностью
6.3.1 УЗК СС проводят в целях оценки сплошности металла СС из сталей перлитного класса и зоны сплавления металла антикоррозионной наплавленной поверхности с металлом шва и околошов-ной зоны до и после выполнения (восстановления) антикоррозионной наплавленной поверхности.
6.3.2 УЗК проводят со стороны поверхности металла перлитного класса (на стороне, противоположной той, на которой выполнена антикоррозионная наплавленная поверхность), НП только прямым лучом с параметрами в соответствии с таблицей 1.
Допускается выполнять УЗК со стороны наплавленной поверхности ПС или ПРС (подход, аналогичный 7.4.2.13), выбор параметров ПЭП в соответствии с таблицей 2.
6.3.3 Для СС с наплавленной поверхностью из сталей аустенитного класса толщиной свариваемых деталей от 20 до 60 мм дополнительно применяют НП с углом ввода 45° или 50°.
6.3.4 Корневую зону СС биметаллических сосудов и трубопроводов, имеющих антикоррозионную наплавленную поверхность, контролируют головными волнами со стороны антикоррозионной наплавленной поверхности в соответствии с приложением Е, а при отсутствии доступа со стороны антикоррозионной наплавленной поверхности при толщине свариваемых деталей от 36 до 100 мм включительно — со стороны основного металла по схеме «корневой тандем» в соответствии с приложением И.
6.3.5 Зону сплавления антикоррозионной наплавленной поверхности со СС контролируют согласно методическим указаниям 6.7.
6.4 Ультразвуковой контроль угловых и тавровых сварных соединений
6.4.1 УЗК угловых и тавровых СС проводят по схемам, приведенным на рисунке 3. Параметры ПЭП (частоту, угол ввода) выбирают в соответствии с таблицами 3, 4 в зависимости от номинальной толщины той части СС (основной или привариваемой), с которой осуществляется ввод УЗ-луча. Углы, указанные в скобках в таблице 4, следует использовать при проведении УЗК угловых и тавровых СС НП со стороны основной детали.
Таблица 3 — Параметры прямых ПЭП для УЗК угловых и тавровых СС в зависимости от номинальной толщины детали, с которой осуществляется ввод УЗ-луча
Номинальная толщина детали, с которой осуществляется ввод УЗ-луча, мм | Частота, МГц | Тип ПЭП |
Св. 5,5 до 20,0 включ. | От 2,5 до 6,0 | ПРС |
Св. 20,0 до 40,0 включ. | От 2,0 до 4,0 | |
Св. 40,0 до 60,0 включ. | От 1,8 до 2,5 | ПС |
Св. 60,0 до 400,0 включ. | От 1,0 до 2,5 |
6.4.2 Угловые и тавровые СС плоских конструкций с толщиной привариваемой детали от 5,5 до 16,0 мм включительно контролируют НП прямым и/или однократно отраженным лучами с обеих поверхностей привариваемой детали (рисунок Зг, д), а при отсутствии доступа прямым и однократно отраженным лучами с одной поверхности (рисунок 36, д).
Таблица 4 — Параметры НП (номинальные значения) при УЗК угловых и тавровых СС в зависимости от номинальной толщины детали, с которой осуществляется ввод УЗ-луча
Номинальная толщина детали, с которой осуществляется ввод УЗ-луча, мм | Частота, МГц | Угол ввода при УЗК, град | |
прямым лучом | однократно отраженным лучом | ||
От 5,5 до 20,0 включ. | От 2,5 до 6,0 | 65, 70, 72 (40, 45, 50) | 65 или 70 |
Св. 20,0 до 40,0 включ. | От 2,0 до 4,0 | 65, 70 (40, 45, 50) | 65 или 70 |
Св. 40,0 до 60,0 включ. | От 1,8 до 2,5 | 50, 60, 65 (40, 45, 50) | 45 или 50 |
Св. 60,0 до 100,0 включ. | От 1,8 до 2,5 | 50, 60, 65 (40, 45, 50) | Не допускается |
Св. 100,0 до 400,0 включ. | От 1,0 до 2,5 | 45, 50 (40, 45, 50) | Не допускается |
Примечания
|
6.4.3 Угловые и тавровые СС плоских конструкций с толщиной привариваемой детали более 16 мм, а также швы приварки штуцеров сосудов с толщиной более 60 мм при отношении толщин основной и привариваемой детали, обеспечивающие заданную чувствительность, контролируют ПС или ПРС ПЭП со стороны основной детали и НП прямым лучом с обеих поверхностей привариваемой детали
(рисунок За, в) или прямым и однократно отраженным лучами с одной поверхности привариваемой детали (рисунок 36, г). Реализуемая чувствительность ПС ПЭП определяется согласно приложению К.
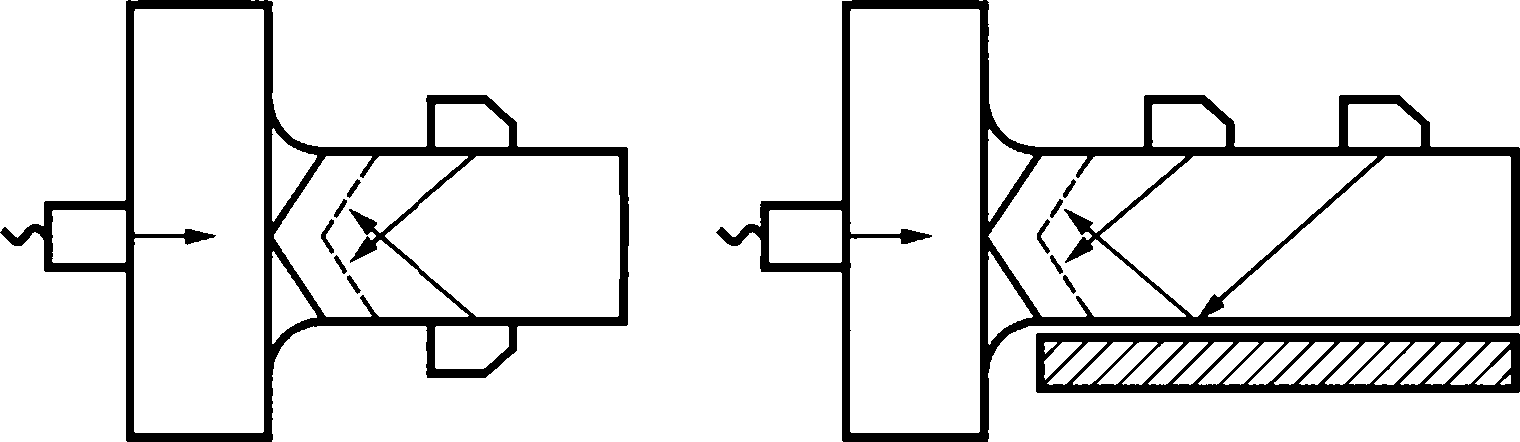
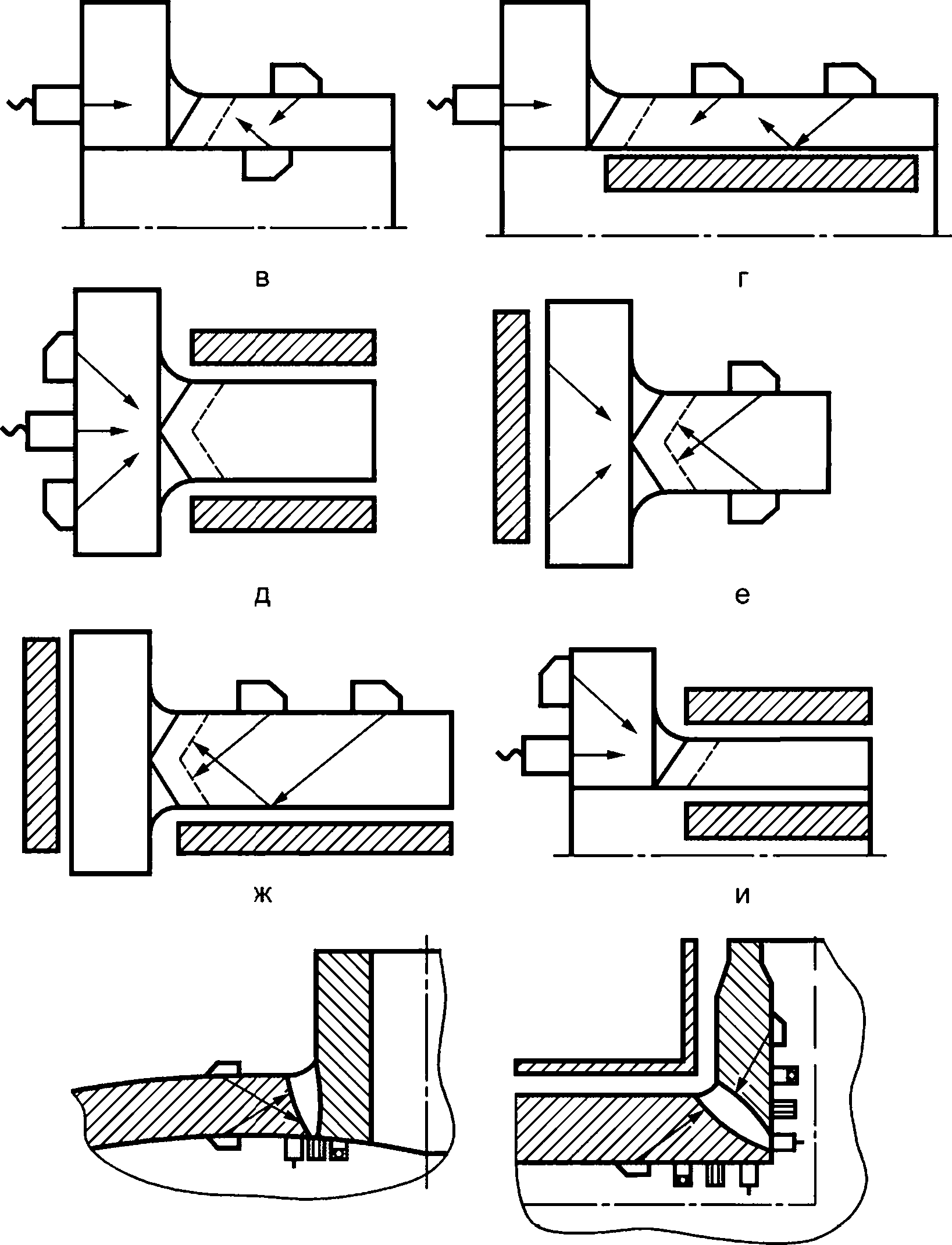
а — УЗК ПС (ПРС) и НП прямым лучом; б — УЗК ПС (ПРС) и НП прямым и однократно отраженным лучами; в — УЗК ПС (ПРС) и НП прямым лучом при радиусе кривизны внутренней поверхности не менее 400 мм; г — УЗК ПС (ПРС) и НП прямым и однократно отраженным лучами; д — УЗК ПС и НП прямым лучом со стороны основной детали; е — УЗК НП прямым лучом при отсутствии доступа со стороны основной детали; ж — УЗК НП прямым и однократно отраженным лучами при отсутствии доступа со стороны основной детали; и — УЗК ПС (ПРС) и НП прямым лучом со стороны основной детали; к — УЗК ПС (ПРС) и НП прямым лучом;
л — УЗК ПС (ПРС) и НП прямым лучом
Рисунок 3 — Схемы УЗК угловых и тавровых СС
6.4.4 Угловые и тавровые СС плоских конструкций с толщиной привариваемой детали от 16 до 60 мм включительно, сосудов, при отсутствии доступа с одной стороны привариваемой детали или ра-12
диусе кривизны внутренней поверхности привариваемой детали менее 400 мм контролируют НП прямым и отраженным лучами со стороны привариваемой детали и ПС ПЭП со стороны основной детали (рисунок 36, г).
6.4.5 Угловые и тавровые СС плоских конструкций с толщиной привариваемой детали от 16 до 60 мм включительно, сосудов, при отсутствии доступа со стороны основной детали контролируют НП прямым лучом с обеих поверхностей привариваемой детали (рисунок Зе), или прямым и однократно отраженным лучами с одной поверхности привариваемой детали (рисунок Зж).
6.4.6 Угловые СС сосудов со штуцерами (патрубками) при отсутствии доступа с внутренней стороны привариваемой детали, тавровые СС с толщиной стенки 10 мм и более контролируют с наружной поверхности патрубка по схемам, приведенным на рисунке Зд, и.
6.4.7 Угловые и тавровые СС плоских конструкций с толщиной привариваемой детали более 16 мм, сосудов, швы приварки штуцеров при наличии разделки со стороны основной детали, а также основной и привариваемой детали, контролируют ПС (ПРС) ПЭП и НП прямым и/или однократно отраженным лучами с обеих поверхностей детали, в которой выполнена разделка (рисунок Зк), а при отсутствии доступа прямым лучом с одной поверхности (рисунок Зл).
6.5 Ультразвуковой контроль сварных соединений на поперечные несплошности
6.5.1 УЗК на поперечные несплошности подлежат типы СС, указанные в таблице 5.
Таблица 5 — Указания по УЗК на поперечные несплошности
Тип СС | Поверхность сканирования | Диаметр основной детали, мм | Толщина основной детали, мм | Схема УЗК |
Стыковое без усиления | Поверхность шва и околошовной зоны | От 300 | От 34 | Рисунок 4а или 46 |
Стыковое с усилением | Основной металл околошовной зоны | От 800 | От 34 до 60 | Рисунок 4в* или 4г |
Угловое и тавровое с усилением | УЗК со стороны основной детали (зона проекции шва и околошовной зоны плюс 10 мм) | От 800 | Рисунок 4а | |
УЗК со стороны привариваемой детали (патрубка) | От 800 | Св. 60 | Рисунок 4в |
* Для швов с Х-образной разделкой предпочтительна схема, приведенная на рисунке 4г.
6.5.2 При УЗК угловых и тавровых СС при отсутствии доступа со стороны основной детали УЗК проводят со стороны привариваемой детали при ее диаметре от 800 мм.
6.5.3 УЗК проводят только прямым лучом. Угол ввода НП выбирают в соответствии с таблицей 4 (за исключением УЗК по схеме «тандем» и «стредл»). Фиксацию и поиск несплошностей осуществляют на уровне чувствительности, превышающем заданный контрольный (уровень фиксации) на 6 дБ.
6.5.4 УЗК стыковых СС со снятым усилением и швов угловых и тавровых соединений (со стороны основной детали) проводят ПЭП, ориентированным вдоль шва в двух встречных направлениях на всю ширину контролируемой зоны. В процессе УЗК ПЭП поворачивают в секторе от 0° до 10° в обе стороны от продольной оси шва. При этом шаг сканирования во всех направлениях не должен превышать половины диаметра (ширины) ПЭ ПЭП. Техника УЗК по схеме «тандем» приведена в приложении Д.
6.5.5 УЗК стыковых СС, выполненных с усилением шва, а также угловых и тавровых СС (со стороны привариваемой детали), проводят сплошным сканированием НП в секторе от 10° до 40° относительно продольной оси шва в околошовной поверхности основного металла в двух встречных направлениях (рисунок 4в).
При этом шаг сканирования вдоль шва не должен превышать половины диаметра (ширины) ПЭ ПЭП.
6.5.6 УЗК стыковых СС, выполненных с усилением шва, допускается контролировать по схеме «стредл» (рисунок 4г) в соответствии с приложением Л.
а — УЗК НП; б — УЗК по схеме «тандем»; в — УЗК НП; г — УЗК по стредл-схеме
Рисунок 4 — Схемы УЗК на поперечные несплошности СС с удаленным усилением (а, б) и с усилением (в, г)
6.6 Выбор параметров ультразвукового контроля наплавленных поверхностей на деталях и на кромках деталей
6.6.1 Контроль наплавленных поверхностей из сталей перлитного класса на деталях и кромках деталей
6.6.1.1 При УЗК наплавленных поверхностей из сталей перлитного класса проверяют сплошность наплавленных поверхностей, включая прилегающий слой основного металла толщиной 2 мм.
6.6.1.2 Наплавленную поверхность из сталей перлитного класса контролируют на частотах от 2 до 5 МГц включительно:
- ПРС со стороны наплавленной поверхности (рисунок 5а) и НП с углами ввода от 65° до 70° включительно со стороны основного металла толщиной менее 20 мм (рисунок 56);
- ПРС и НП с углом ввода от 65° до 70° включительно со стороны наплавленной поверхности при толщине основного металла 20 мм и более (рисунок 5а).
в г
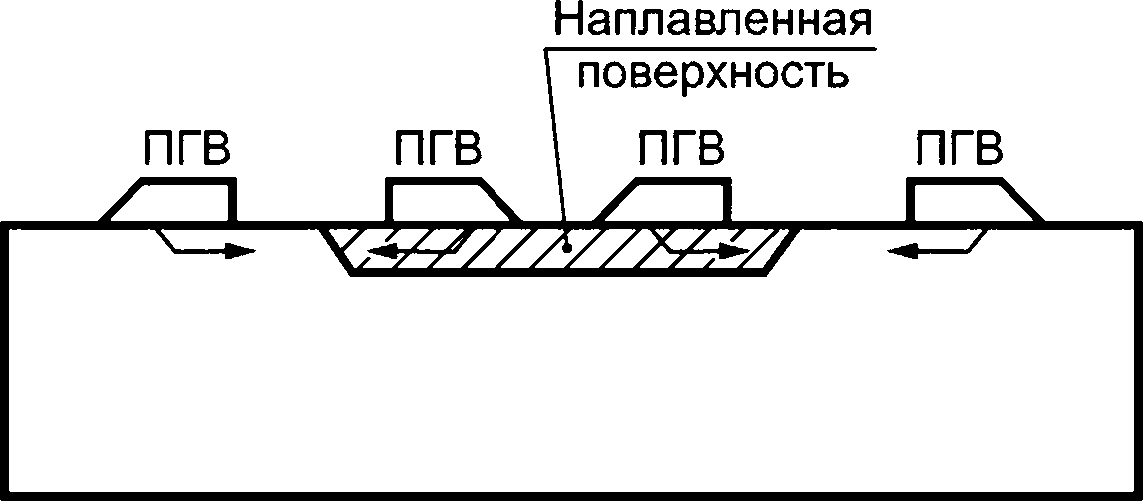
Д
а — УЗК ПРС ПЭП со стороны наплавленных поверхностей; б — УЗК НП;
в — УЗК ПРС ПЭП со стороны основного металла; г — УЗК ПС ПЭП; д — УЗК боковых участков наплавленных поверхностей ПГВ Рисунок 5 — Схемы УЗК металла наплавленных поверхностей
6.6.1.3 Допускается совмещать УЗК наплавленных поверхностей из сталей перлитного класса и готовых СС.
6.6.2 Контроль наплавленных поверхностей из сталей аустенитного класса на деталях и кромках деталей
6.6.2.1 При УЗК наплавленных поверхностей из сталей аустенитного класса оценивают сплошность зоны сплавления наплавленной поверхности с основным металлом.
6.6.2.2 Зону сплавления наплавленной поверхности из сталей аустенитного класса контролируют на частоте от 2 до 5 МГц включительно со стороны основного металла ПС (или ПРС — в зависимости от толщины основного металла) или НП с углами ввода, обеспечивающими близкое к нормальному (90° ± 2,5°) падение УЗ-волны на линию сплавления (рисунок 5а, б). Если такой контроль невозможен, наплавленную поверхность контролируют со стороны наплавленной поверхности (рисунок 5а).
6.6.3 При проведении УЗК с целью выявления поднаплавочных трещин, перпендикулярных к зоне сплавления (рисунок 5д), при толщине наплавленной поверхности не более 13 мм дополнительно к 6.6.1,6.6.2 проводят УЗК в соответствии с приложением Е.
6.7 Выбор параметров ультразвукового контроля зоны сплавления антикоррозионной наплавленной поверхности из сталей аустенитного класса с основным металлом
6.7.1 Зону сплавления металла антикоррозионной наплавленной поверхности из сталей аустенитного класса с основным металлом контролируют на частотах от 2 до 5 МГц включительно при толщине основного металла:
- менее 40 мм ПРС ПЭП со стороны основного металла (рисунок 5в), а в случае невозможности проведения УЗК со стороны основного металла — со стороны наплавленной поверхности (рисунок 5а);
- 40 мм и более — ПС ПЭП со стороны основного металла (рисунок 5г), а в случае отсутствия доступа — ПРС ПЭП со стороны наплавленной поверхности (рисунок 5а).
6.7.2 Если суммарная площадь участков, доступных для проведения УЗК со стороны основного металла, менее одной трети общей площади наплавленной поверхности, то УЗК указанных участков допускается проводить со стороны наплавленной поверхности.
6.7.3 Если непараллельность поверхности основного металла в зоне сплавления превышает <р (по 6.8.3.3):
- УЗК проводят со стороны наплавленной поверхности;
- допускается применение специализированных ПЭП, обеспечивающих нормальное падение УЗ-волны на линию зоны сплавления.
6.7.4 Для обеспечения УЗК боковых участков наплавленной поверхности, выходящих на поверхность ОК, УЗК проводят головными волнами (рисунок 5д/
6.7.5 При проведении УЗК с целью выявления поднаплавочных трещин используют методику УЗК головными волнами в соответствии с приложением М или методику УЗК способом «корневой тандем» в соответствии с приложением И.
6.8 Требования к объектам контроля
6.8.1 Объем УЗК определяется федеральными нормами и правилами в области использования атомной энергии, документами по стандартизации, КД, ТД, устанавливающих требования к оценке соответствия металла СС и наплавленных поверхностей, как протяженность для СС или площадь для наплавленных поверхностей. При наличии неконтролируемых из-за недоступности участков СС, наплавленной поверхности, УЗК считают выполненным в неполном объеме, а недоступные участки отмечают в отчетной документации (в соответствии с разделом 8).
6.8.2 Степень контроледоступности определяется представителем подразделения неразрушающего контроля в зависимости от ограничений, налагаемых конструкцией ОК в зоне контроля, на возможность установки и пределы перемещения ПЭП (геометрические размеры и разделка шва, наличие доступа, форма и размеры околошовных зон).
При определении степени контроледоступности не учитывается непрозвучиваемость усиления стыкового СС, катетов угловых и тавровых СС.
6.8.3 Для СС, контролируемых по настоящему стандарту, устанавливают следующие степени контроледоступности в порядке ее снижения (по уменьшению объема прозвучивания и направлений прозвучиваний):
а) 1С — центральный луч УЗ-пучка пересекает каждую точку металла контролируемого сечения СС в трех или более направлениях. Примеры типовых схем УЗК приведены на рисунках 2а—г;
б) 2С — центральный луч УЗ-пучка пересекает каждую точку металла контролируемого сечения СС в двух и более направлениях. Примеры типовых схем УЗК приведены на рисунках 2д—ж, и, Зд;
в) ЗС — центральный луч УЗ-пучка пересекает каждую точку металла контролируемого сечения СС в одном и более направлениях. Примеры типовых схем УЗК приведены на рисунках 2к, л, За—г;
г) 4С — часть контролируемого сечения СС не может быть прозвучена центральным лучом УЗ-пучка ни по одному из направлений, предусмотренных для степени 1С. Примеры типовых схем УЗК приведены на рисунках Зе, ж, и;
д) СС считают неконтроледоступным, если все сечение СС не может быть прозвучено центральным лучом УЗ-пучка ни по одному из направлений, предусмотренных для степени 1С;
е) проведение УЗК с целью выявления поперечных несплошностей не изменяет степень контроледоступности СС, определенную по перечислениям а)—г);
ж) направления считаются разными, если угол между центральными лучами УЗ-пучков отличаются не менее чем на 35°.
При выборе оптимальной схемы УЗК с использованием основных операций прозвучивания [6.1.1, перечисления а), б)] необходимо учитывать обязательность прозвучивания центральным лучом УЗ-пучка центральной зоны шва (рисунок 6) в состав которой входит корень шва.
На рисунке 6а секторами обозначены зоны шва (в данном случае стыкового СС с V-образной разделкой кромок) в его поперечном сечении. Сектору А-А' соответствует центральная зона шва, корень шва расположен в секторе А'.
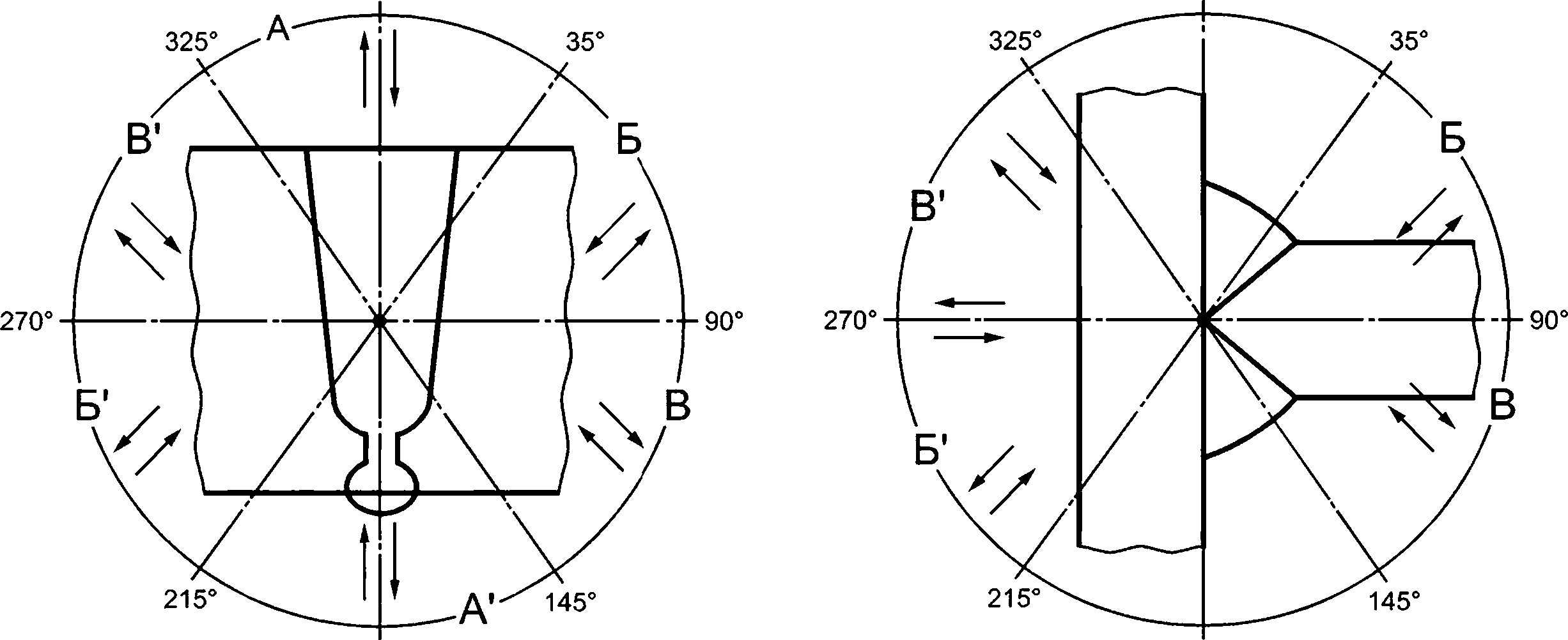
О — контролируемая часть СС; <--направления прозвучивания (цифрами обозначены углы ввода УЗ, буквами — секторы
обзора)
а — схема для стыкового СС; б — схема для углового и таврового СС
Рисунок 6 — Схемы определения степени контроледоступности СС
6. 8.3.1 При проектировании (конструировании) ОК должна обеспечиваться максимально возможная контроледоступность СС по всей его протяженности, наплавленной поверхности по всей ее площади (например, путем удаления или уменьшения ширины усиления, изменением конструкции контролируемого узла).
Для увеличения контроледоступности следует дополнительно применять иные углы ввода (в соответствии с ГОСТ Р 55725), исходя из угла(ов) разделки свариваемых деталей и обеспечения максимального прозвучивания всего объема СС. и дополнительные схемы прозвучивания, что должно быть отражено в ТКК. Соответствующие изменения степени контроледоступности вносят в КД (если в них содержались данные сведения).
6. 8.3.2 УЗК мест пересечений швов с усилением стыковых соединений и стыковых соединений с тавровыми технически невыполним. УЗК мест пересечения стыковых швов возможен при снятом и зачищенном усилении шва в пределах зон перемещения ПЭП.
6. 8.3.3 Для антикоррозионных наплавленных поверхностей установлены следующие степени контроледоступности в порядке ее снижения:
а) 1Н — непараллельность поверхности основного металла границе «основной металл — металл наплавленной поверхности» в зоне сплавления не превышает ср, вычисляемую по формуле
, . 0,61 С
о = ±arcsin—----,
af (1)
где С — скорость УЗ-волны, мм/с;
а — радиус (половина ширины) ПЭ, мм;
f — частота, МГц;
б) 2НА — непараллельность поверхности основного металла границе «основной металл — металл наплавленной поверхности» превышает <р, но УЗК со стороны основного металла проводят специальными ПЭП, обеспечивающими нормальное падение (90°) УЗ-волны на поверхность зоны сплавления, отличными от приведенных в 6.3, или по схеме приема зеркально отраженного от металла наплавленной поверхности луча;
в) 2НБ — УЗК со стороны основного металла невозможен, его проводят со стороны наплавленной поверхности. Непараллельность наплавленной поверхности границе «основной металл — металл наплавленной поверхности» не превышает значений ср;
г) наплавленную поверхность считают неконтроледоступной, если не выполнены условия по перечислениям а)—в).
Для металла наплавленной поверхности определяют объем УЗК как процентное отношение площади контроледоступной части зоны сплавления основного металла с металлом наплавленной поверхности к площади всей зоны сплавления контролируемой наплавленной поверхности. Объем УЗК фиксируют в КД.
Для переходных наплавленных поверхностей, выполненных из сталей аустенитного и перлитного классов, степень контроледоступности не устанавливается.
6.8.4 СС и наплавленные поверхности или их участки, признанные неконтроледоступными, УЗК не подлежат, что должно быть отражено в КД.
6.8.5 При УЗК кромки (края) СС, наплавленной поверхности (со стороны основного металла) существует зона, в которой не гарантируется выявление дефектов. Ширина этой зоны / определена большей из величин
/ = Ji,5H — , (2)
V f
где Н — толщина СС или основного металла при УЗК наплавленной поверхности, мм;
С — скорость УЗ-волны, м/с;
f— частота, МГц;
/=а, (3)
где а — радиус (половина ширины) ПЭ, мм.
При УЗК металла наплавленных поверхностей данную зону проверяют со стороны наплавленной поверхности. В этом случае зона, в которой не гарантируется выявление дефектов, равна а. Наличие такой зоны не учитывают при оценке контроледоступности.
6.8.6 УЗК СС труб с внутренней расточкой однократно отраженным лучом возможен, если длина /р цилиндрической части расточки не менее величины, определенной формулой
/р =/7tga+ —+ Д + 5, (4)
где Н — номинальная толщина трубы, мм;
a — угол ввода, град;
b — ширина усиления шва, мм;
А — ширина прилегающих к СС участков основного металла (околошовная зона), мм.
При меньших размерах расточки УЗК проводят только прямым лучом при удаленном усилении, что должно быть отражено в ТИ и/или ТКК.
6.8.7 Поверхности СС в зоне перемещения ПЭП с обеих сторон сварного шва очищают от пыли, грязи, окалины. С них удаляют забоины и неровности по всей длине контролируемого участка.
6.8.8 Ширина подготовленной под УЗК зоны с каждой стороны шва должна быть не менее:
- при УЗК С ПЭП прямым лучом
Н tga + А + В - п + 10, (5)
где Н — толщина СС, мм;
a — угол ввода, град;
А — ширина прилегающих к СС участков основного металла (околошовная зона), мм;
В — длина контактной поверхности ПЭП, мм;
п — величина стрелы ПЭП, мм;
- при УЗК однократно отраженным лучом и по схеме «тандем»
2/7 tga + Д + В - л + 10. (6)
6.8.9 При подготовке зоны УЗК с помощью механической обработки шероховатость поверхности должна быть не более Ra 6,3 мкм (Rz 40). Шероховатость механически обработанной донной поверхности при УЗК отраженным лучом и по схеме «тандем» должна быть не более Ra 20 мкм (Rz 80). Зазор между поверхностью металла СС и/или наплавленной поверхности в зоне контроля и ПЭП, образующийся из-за волнистости, не должен превышать 0,2 мм.
6.8.10 Усиление шва должно быть удалено и выровнено с поверхностью основного металла в следующих случаях:
- при УЗК стыковых СС категории 1 толщиной 40 мм и более (рисунок 2а). В стыковых СС с различной номинальной толщиной деталей усиление шва допускается не удалять (рисунок 7а);
- при наличии антикоррозионной наплавленной поверхности на донной поверхности (рисунок 76);
- при УЗК СС сосудов, если одна из сторон соединения недоступна для проведения УЗК (рисунок 26, г) и УЗК отраженным лучом невозможен (рисунок 2в);
- при УЗК стыковых СС, если ширина усиления не позволяет проконтролировать корень шва прямым центральным лучом или все сечение центральным лучом (рисунок 7в).
Рисунок 7 — Примеры СС с усилением и с удаленным усилением
6.9 Требования к средствам ультразвукового контроля и образцам
6.9.1 При проведении УЗК используют:
- импульсные УЗ-дефектоскопы общего назначения (или имеющего функции дефектоскопа общего назначения) с параметрами, соответствующими требованиям ГОСТ Р 50.05.14;
- ПЭП, с параметрами (угол, частота), соответствующими ГОСТ Р 55725, с соединительными кабелями;
- КО и НО по ГОСТ Р 50.05.14;
- АРД-диаграммы (AVG-диаграммы, АРД-шкалы);
- вспомогательные устройства, приспособления и материалы.
6.9.2 Работоспособность дефектоскопа, соединительного кабеля и ПЭП определяется при их взаимном подключении и включении прибора.
6.9.2.1 При определении работоспособности дефектоскопа с ПС ПЭП необходимо определять «мертвую» зону [после настройки поисковой чувствительности, в соответствии с ГОСТ Р 50.05.05—2018 (пункт 7.1.9)].
Примечание — Дополнительно рекомендуется определять отклонение акустической оси от нормали к рабочей поверхности [в соответствии с ГОСТ Р 50.05.05—2018 (пункт 7.1.10)].
6.9.2.2 При определении работоспособности дефектоскопа с ПРС ПЭП необходимо определять «мертвую» зону [после настройки поисковой чувствительности, см. ГОСТ Р 50.05.05—2018 (пункт 7.1.9)].
Примечание — Если планируется проведение настройки чувствительности с помощью АРД- и AVG-диа-грамм или АРД-шкал, дополнительно рекомендуется определять глубину фокуса [см. ГОСТ Р 50.05.05—2018 (пункт 7.1.11)].
6.9.2.3 При определении работоспособности дефектоскопа с НП необходимо определять:
- точку выхода ПЭП [см. ГОСТ Р 50.05.05—2018 (пункт 7.1.12)];
- угол ввода ПЭП [см. ГОСТ Р 50.05.05—2018 (пункт 7.1.13)];
- мертвую зону [см. ГОСТ Р 50.05.05—2018 (пункт 7.1.9)].
Дополнительно определяют отклонение акустической оси от плоскости падения [см. ГОСТ Р 50.05.05—2018 (пункт 7.1.14)].
Проверку вышеуказанных параметров ПЭП, у которых контур рабочей поверхности соответствует радиусу кривизны поверхности ОК в зоне контроля, допускается не проводить. При этом следует руководствоваться данными, указанными в паспорте (свидетельстве о поверке/сертификате о калибровке), на такой ПЭП.
6.9.2.4 Проверка правильности настройки параметров УЗК должна осуществляться периодически— до начала, после окончания, через каждые два часа работы. В случае обнаружения несоответствия в параметрах настройки должен быть выполнен повторный УЗК всех СС и/или наплавленных поверхностях, проконтролированных после предыдущей проверки настройки.
6.9.3 Требования к параметрам НП и ПС ПЭП отражены в таблицах 1—5.
ПЭП, используемые совместно с дефектоскопами для УЗК, должны обеспечивать отклонение угла ввода УЗ-луча от номинального значения — не более ± 2°.
6.9.4 НО следует изготавливать из того же материала и по той же технологии, что и контролируемое СС или наплавленная поверхность. Допускается изготавливать НО из материала того же структурного класса и подвергнутого той же термообработке, что и контролируемое СС или наплавленная поверхность. На акустические свойства НО устанавливают допуски в соответствии с ГОСТ Р 50.05.14.
6.9.5 НО с плоской поверхностью применяют при УЗК СС, изготовленных сваркой плоских деталей, и СС (продольных и кольцевых) при сварке деталей цилиндрической формы для ПРС ПЭП и НП, если их наружный диаметр DH не менее 150 мм или внутренний Овн не менее 300 мм, а также для ПС ПЭП при наружном диаметре DH более 500 мм или внутреннем Овн не менее 500 мм.
6.9.6 При УЗК по цилиндрической поверхности настройку проводят по НО, имеющих отклонение от номинальных значений наружного и внутреннего диаметров Он и Овк — в соответствии с допусками на изготовление, но не более ±10 %.
6.9.7 При проведении УЗК СС трубопроводов и цилиндрических конструкций радиус кривизны поверхности НП должен соответствовать радиусу кривизны поверхности ОК в зоне контроля (с учетом формы). При этом, в зависимости от поверхности ввода УЗ-волны и от ориентации выявляемых несплошностей профиль поверхности НП должен:
- удовлетворять требованиям 6.2.4.3 при УЗК с выпуклой поверхности с целью выявления продольных несплошностей;
- повторять профиль поверхности в зоне контроля (с учетом 6.9.5) — при УЗК с вогнутой поверхности вне зависимости от ориентации несплошностей и при УЗК с выпуклой поверхности с целью выявления поперечных несплошностей.
Одновременно с этим необходимо учитывать, что подготовка ПЭП в соответствии с 6.9.6 должна быть выполнена по большему из двух диаметров ОК в зоне контроля или НО (Оок или Оно) при УЗК по выпуклой поверхности и по меньшему из двух диаметров Оок или £>н0 при УЗК по вогнутой поверхности.
6.9.8 На линейные размеры и ориентацию отражателей в образцах устанавливают допуски в соответствии с ГОСТ Р 50.05.14.
6.9.9 Паспортизацию и проверку пригодности НО к использованию проводят в соответствии с ГОСТ Р 50.05.14, ГОСТ Р 50.05.16.
6.10 Требования к персоналу, выполняющему ультразвуковой контроль
К проведению УЗК по настоящему стандарту допускаются специалисты, обладающие теоретическими знаниями и практическими навыками контроля, прошедшие процедуру подтверждения компетентности в соответствии с требованиями ГОСТ Р 50.05.11.
7 Проведение ультразвукового контроля
7.1 Подготовка к ультразвуковому контролю
7.1.1 Перед началом проведения работ специалист по УЗК получает задание (заявку) на контроль с указанием типа и номера СС, наплавленной поверхности и его/ее расположения на ОК (узле, трубопроводе), объема УЗК, толщины, диаметра СС, марки основного и сварочного материала, типа сварки (наплавления поверхности), номеров чертежа и перечня конструктивных отклонений, влияющих 20
на контроледоступность СС. В случае многослойной наплавленной поверхности ее толщина может быть указана на эскизе.
7.1.2 После получения заявки специалист по УЗК должен ознакомиться с ТИ и/или ТКК, конструкцией и особенностями технологии выполнения СС, наплавленной поверхности, а также с документацией, в которой указаны допущенные отклонения от установленной технологии и результаты предшествующего контроля.
7.1.3 Перед проведением работ специалист по УЗК должен удостовериться, что подготовленная под УЗК поверхность соответствует требованиям 6.8.7, ширина подготовленной под УЗК зоны соответствует требованиям 6.8.8.
7.2 Разметка объекта контроля при подготовке к проведению ультразвукового контроля
7.2.1 Контролируемое СС должно быть размечено.
7.2.2 Разметка включает отметку границ шва и наплавленной поверхности, разбиение на участки длиной не более 500 мм и их маркировку. Разметка должна соответствовать разметке для радиографического контроля, если он предусмотрен ТД.
7.2.3 Кольцевые СС трубопроводов разбивают на участки по аналогии с часовым циферблатом.
7.2.4 Антикоррозионную наплавленную поверхность следует разметить на участки площадью не более 0,25 м2 и большей стороной не более 1 м.
7.2.5 Разметка должна быть предусмотрена технологическим процессом изготовления или условиями проведения УЗК ОК, должно быть обеспечено ее воспроизведение на всех стадиях проведения УЗК данного СС и/или наплавленной поверхности. Начало и направление отсчета участков должны быть замаркированы постоянным клеймом. Допускается вместо клеймения применять иной способ разметки, соответствующий требованиям [4].
7.2.6 Разметка в обязанности специалиста по УЗК не входит.
7.3 Последовательность операций ультразвукового контроля сварных соединений
УЗК СС и металла наплавленных поверхностей проводят в следующей последовательности:
- на дефектоскопе настраивают диапазон развертки, рабочую зону и глубиномер;
- последовательно устанавливают браковочный, контрольный (фиксации) и поисковый уровни чувствительности (в соответствии с 7.4.2);
- в соответствии со схемой прозвучивания проводят прозвучивание СС (металла наплавленной поверхности) сканированием ПЭП по поверхности зоны контроля;
- при обнаружении эхо-сигнала от несплошности определяют его максимум;
- если высота эхо-сигнала ниже контрольного уровня, то продолжают сканирование;
- если высота эхо-сигнала равна или превышает контрольный уровень, то определяют и записывают характеристики несплошностей в учетной документации (в соответствии с разделом 8);
- оценивают допустимость несплошностей и качество СС путем сравнения полученных значений характеристик (эквивалентная площадь/амплитуда сигнала, условная протяженность, количество несплошностей на единицу длины/площади) с нормативными значениями;
- фиксируют результаты УЗК и оценку годности в отчетной документации (в соответствии с разделом 8).
7.4 Настройка аппаратуры
7.4.1 Настройка диапазона развертки и глубиномера7.4.1.1 Настройку диапазона развертки следует проводить таким образом, чтобы сигналы от несплошностей в любом участке СС находились в пределах экрана дефектоскопа.
7.4.1.2 Настройку диапазона развертки при УЗК СС толщиной свариваемых деталей менее 12 мм допускается проводить по угловому отражателю в НО согласно схеме настройки развертки по угловым отражателям (рисунок 8).
1 — максимальный эхо-сигнал от нижнего углового отражателя; 2 — максимальный эхо-сигнал от верхнего углового отражателя Рисунок 8 — Схема настройки развертки по угловым отражателям
7.4.1.3 При контроле сварных соединений толщиной от 5,5 до 12,0 мм включительно допускается настройку глубиномера не проводить, а глубину залегания несплошности определять по месту расположения эхо-сигнала на развертке дефектоскопа.
Для СС с толщиной свариваемых деталей 12,0 мм и более диапазон развертки устанавливают:
- по эхо-сигналам от двугранных углов или вогнутой поверхности КО или по НО с отражателями на различной глубине;
- глубиномеру дефектоскопа. При этом границы рабочей зоны экрана (контроля) устанавливают по значениям минимально и максимально возможной глубины залегания несплошностей.
При УЗК прямым лучом глубину залегания несплошности определяют как расстояние от наружной поверхности, а при УЗК однократно отраженным лучом — как разность толщины свариваемых деталей и расстояния от внутренней поверхности соединения до несплошности.
7.4.1.4 Настройку диапазона развертки ПС и ПРС проводят:
- по донным эхо-сигналам;
- по НО, содержащем плоскодонные отражатели на различных глубинах, при толщине свариваемых деталей не более 100 мм;
- устанавливают по глубиномеру дефектоскопа, при толщине свариваемых деталей 20 мм и более. При этом границы рабочей зоны экрана (контроля) устанавливают по значениям минимально и максимально возможной глубины залегания несплошностей.
7.4.1.5 Настройку глубиномера проводят в соответствии с инструкцией по эксплуатации дефектоскопа по донным эхо-сигналам, эхо-сигналам от двугранных углов или вогнутой поверхности КО или по НО с отражателями на различной глубине.
7.4.1.6 Допускается настраивать глубиномер и диапазон развертки по эхо-сигналу от двугранного угла шлифованного прямоугольного бруска («плавающий» отражатель — концевая мера длины (плитки Иогансона), удерживаемый магнитом и акустически связанный со шлифованным торцом СО-2 или НО через слой контактной среды).
7.4.1.7 Диапазон развертки при УЗК металла наплавленной поверхности настраивают по плоскодонным отражателям в НО согласно схемам, приведенным на рисунках 9—11, или по донному сигналу.
а
Нн — толщина металла наплавленной поверхности; d — диаметр плоскодонного отражателя; S — площадь дна плоскодонного отражателя (d и S — маркировать)
Рисунок 9 — НО для УЗК ПРС металла наплавленной поверхности кромок из сталей перлитного класса (а); НО для УЗК ПРС металла наплавленной поверхности кромок из сталей аустенитного класса (б); схема настройки дефектоскопа (в)
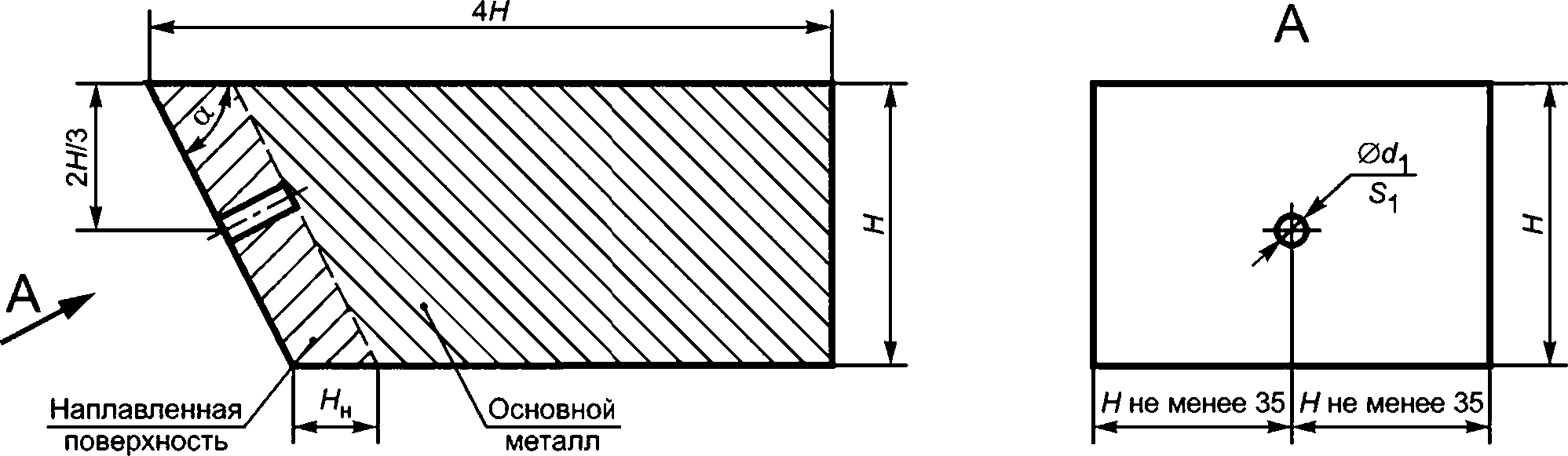
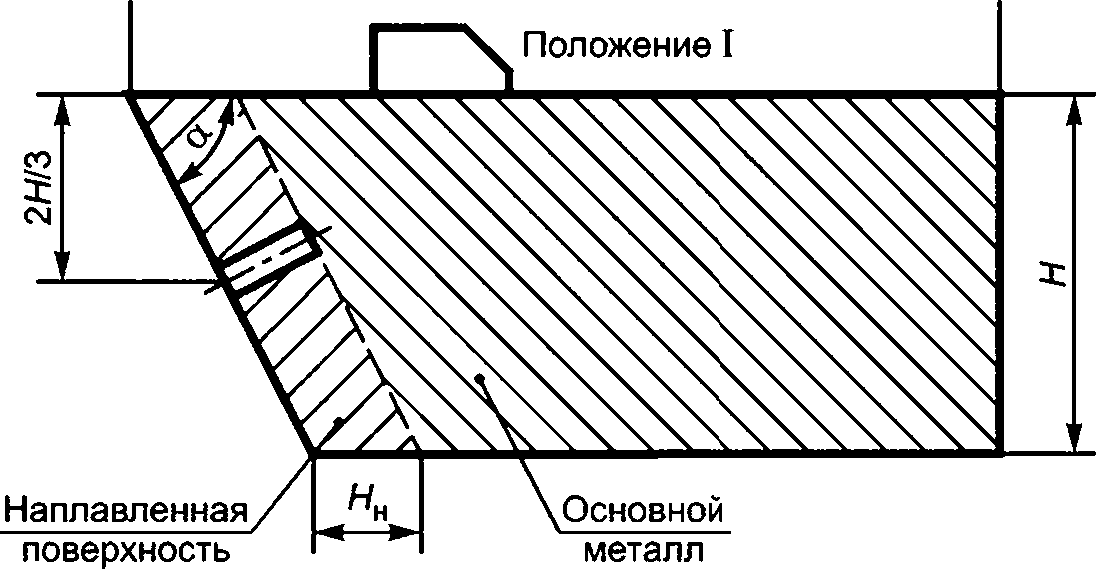
Зондирующий
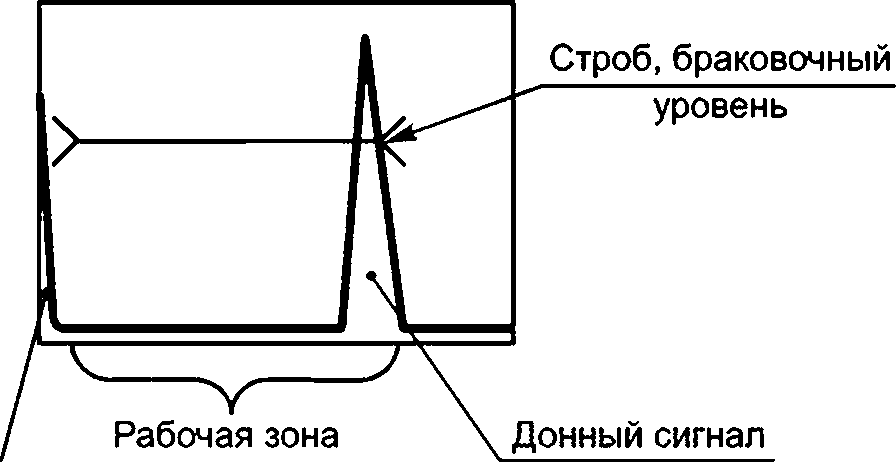
сигнал
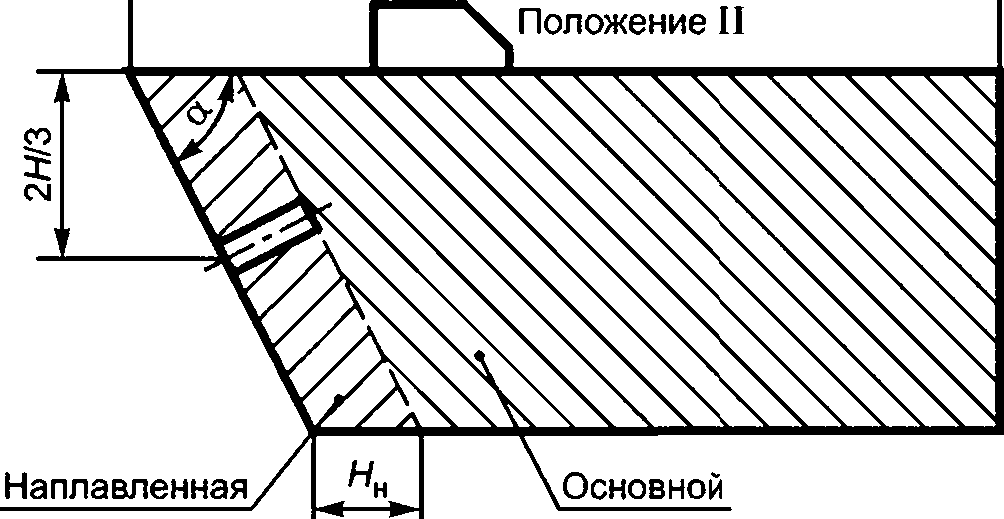
поверхность
металл
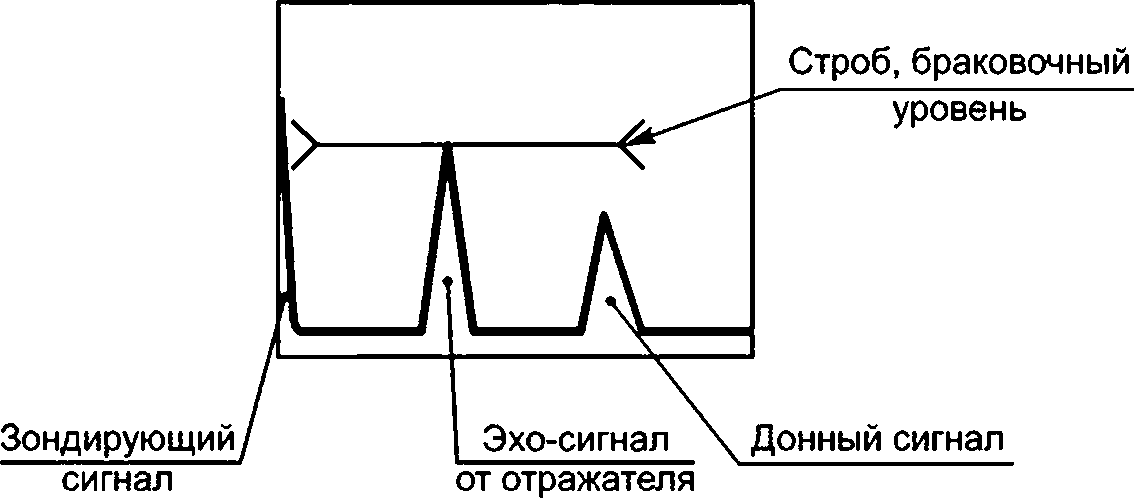
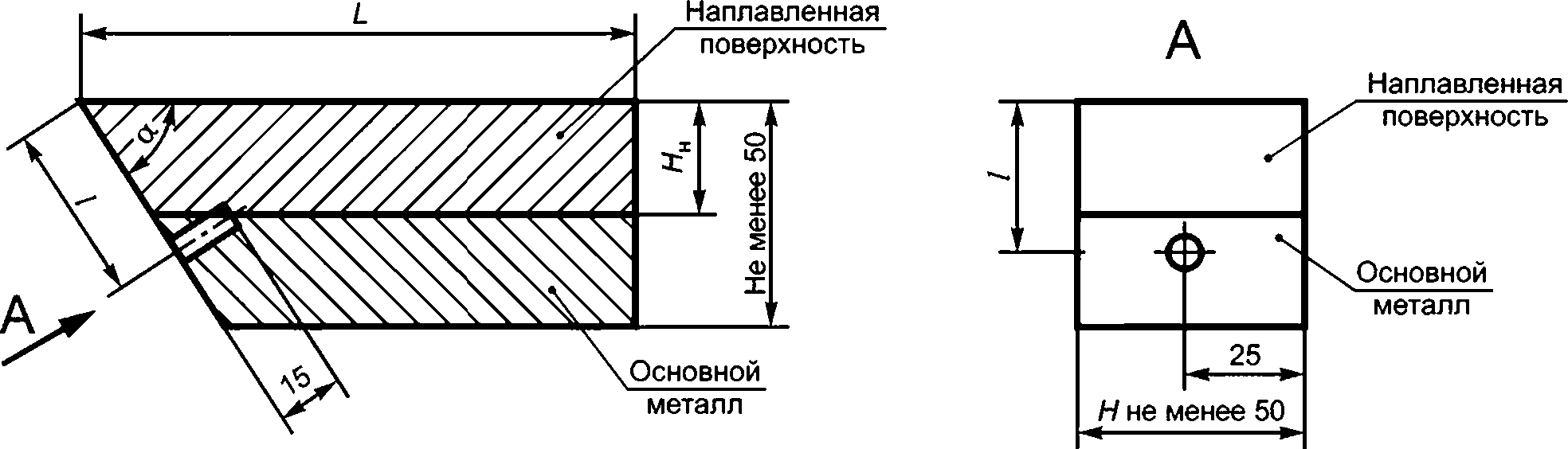
S — площадь плоскодонного отражателя; Н — толщина образца; Нн — глубина плоскодонного отражателя, равная толщине металла наплавленной поверхности; L — длина образца
Рисунок 10 — НО для УЗК НП металла наплавленной поверхности из сталей перлитного класса и аустенитного класса (а); схема настройки дефектоскопа (б); НО для УЗК металла наплавленной поверхности на кромках под сварку из сталей перлитного класса НП (в)
7.4.1.8 Для ПЭП с углом ввода от 60° до 72° настройку дефектоскопа и определение фактического угла ввода и времени задержки в призме НП следует проводить при температуре, равной той, при которой проводят УЗК. При различии этих температур учитывают изменение угла ввода и времени задержки в призме. Температурные поправки угла ввода для ПЭП с призмой из органического стекла определяют по графику, приведенному на рисунке 12.
а — схема настройки дефектоскопа; б — УЗК со стороны основного металла; в — УЗК со стороны наплавленной поверхности; г — УЗК через наплавленную поверхность; d — диаметр плоскодонного отражателя; S — площадь плоскодонного отражателя; Н — толщина основного металла; Нн — толщина металла наплавленной поверхности
Рисунок 11 — НО для УЗК металла антикоррозионной наплавленной поверхности
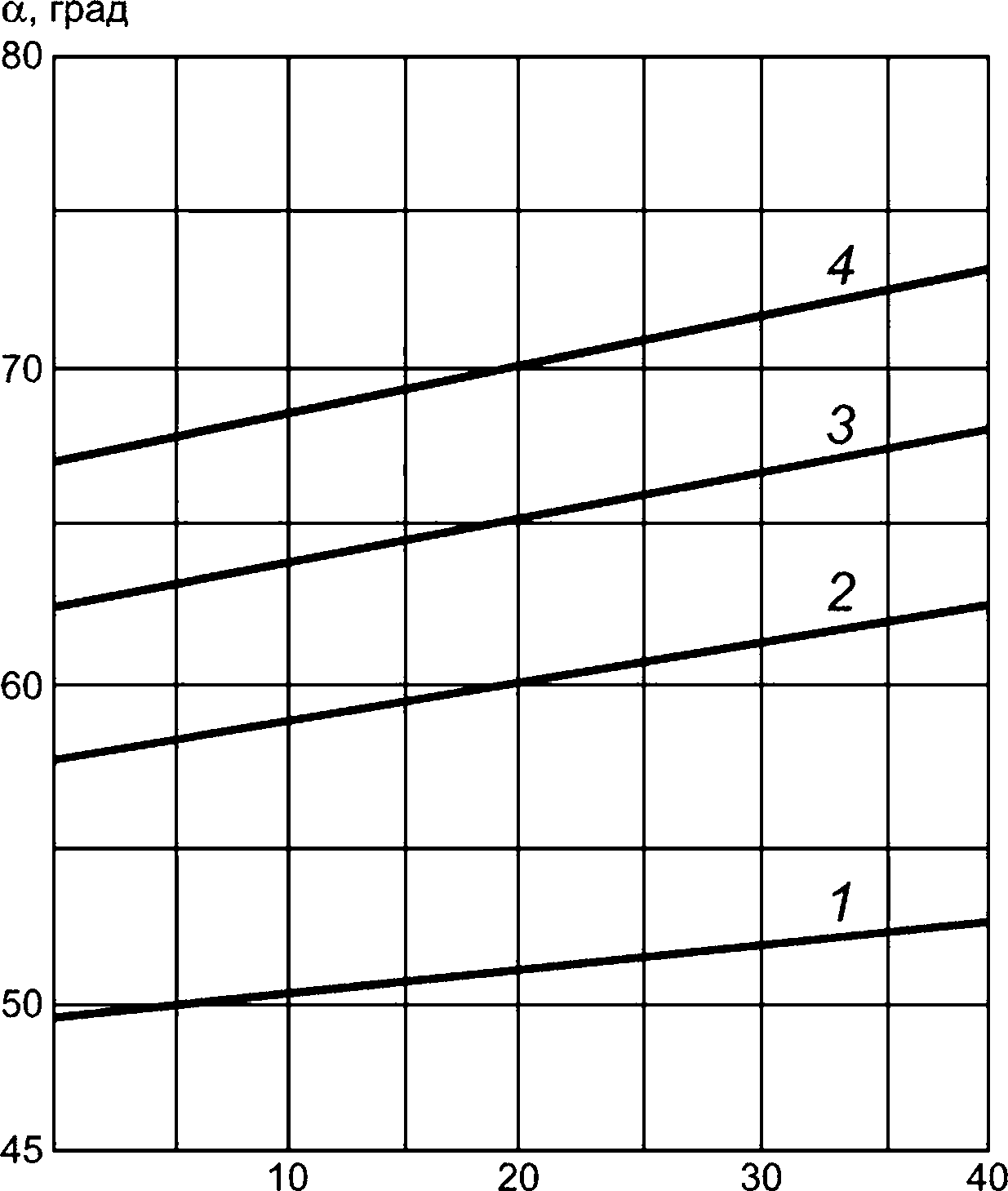
Температура, °C
а = 51° (Р = 40°) (7); 60°(2); 65° (р = 50°) (3) и 70° (р = 54°) (4)
Рисунок 12 — Зависимость угла ввода а от температуры для ПЭП с призмой из органического стекла с номинальными углами ввода
7.4.2 Настройка чувствительности
7.4.2.1 Настройку чувствительности проводят в целях обеспечения выявления несплошностей, подлежащих фиксации в данном СС и контролируемой околошовной зоне (металле наплавленной поверхности, зоне сплавления металла наплавленной поверхности с основным металлом).
Для настройки чувствительности допускается использовать следующие сигналы и/или отражатели:
- донный сигнал от параллельной (или эквидистантной) или наклонной поверхности (перпендикулярной к направлению падения луча);
- плоскодонный отражатель;
- прямой двугранный угол контактной или донной поверхности и вертикальной плоскости;
- двугранный угол донной или контактной поверхности и углового отражателя [вертикального паза в виде прямоугольника (зарубки), или сегмента круга, или боковой поверхности паза, в том числе переменной высоты].
7.4.2.2 При настройке устанавливают следующие уровни чувствительности:
а) браковочный, при котором проводят оценку допустимости обнаруженной несплошности по амплитуде эхо-сигнала.
Браковочный уровень устанавливают в соответствии с федеральными нормами и правилами в области использования атомной энергии, документами по стандартизации, КД, ТД, устанавливающими требования к оценке соответствия металла СС и наплавленных поверхностей;
б) контрольный (уровень фиксации), при котором проводят фиксацию обнаруженных несплошностей, определение их характеристик и оценку их допустимости по предельным значениям характеристик (например, условной протяженности, высоте).
Контрольный уровень устанавливают путем повышения чувствительности на 6 дБ от браковочного уровня;
в) поисковый, при котором проводят поиск несплошностей.
Поисковый уровень устанавливают путем повышения чувствительности на 6 дБ от контрольного уровня.
7.4.2.3 Браковочный и контрольный уровни устанавливают отдельно для каждой обнаруженной несплошности в зависимости от глубины ее залегания.
Допускается устанавливать одно значение поискового уровня для контролируемого СС по максимально возможной глубине залегания несплошности.
7.4.2.4 Настройку чувствительности при УЗК СС с толщиной свариваемых деталей менее 12 мм проводят по угловым отражателям (рисунок 13а) в соответствии с приложением Н.
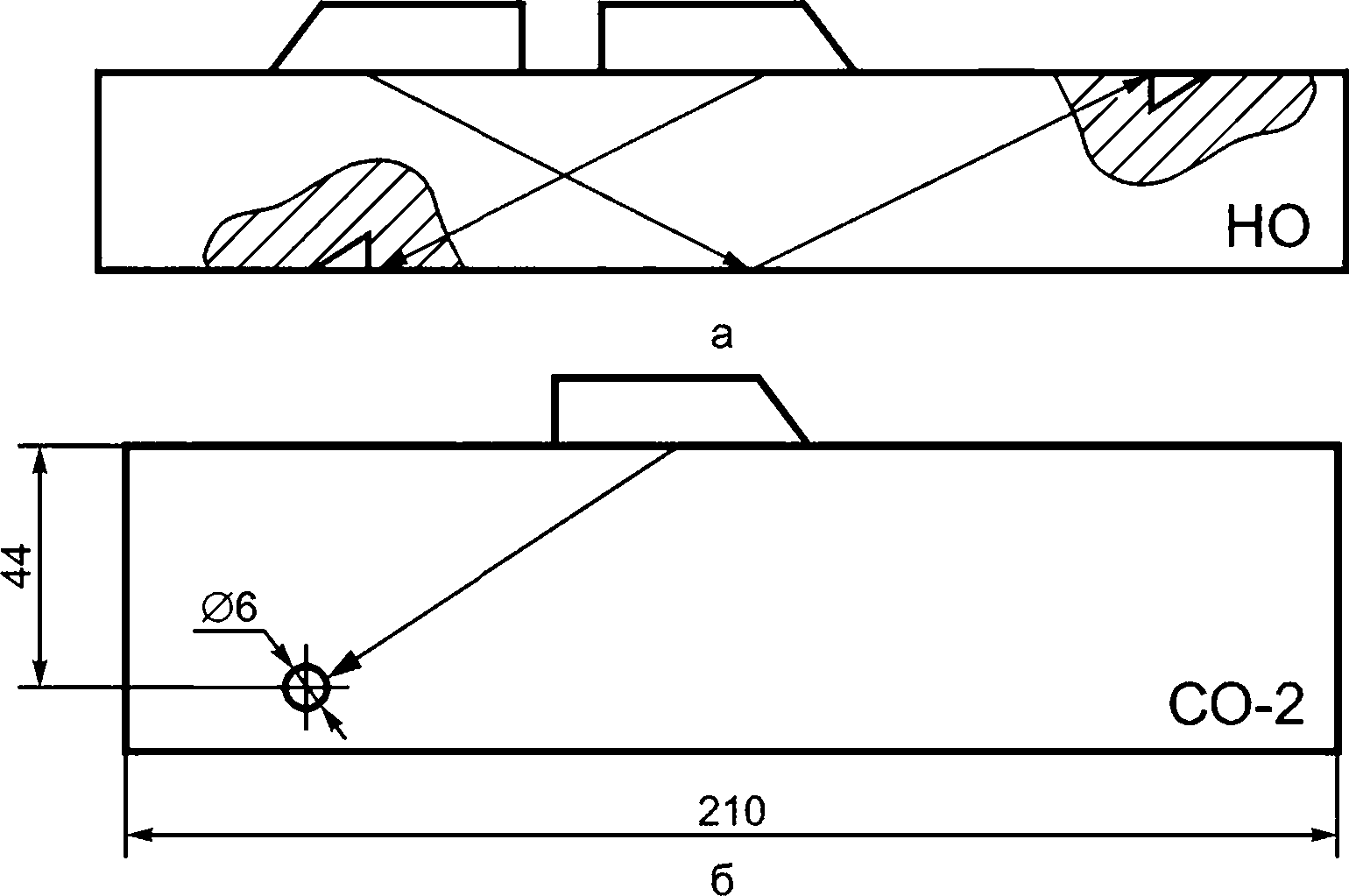
а — при УЗК СС с толщиной свариваемых деталей менее 12 мм;
б — при УЗК СС с толщиной свариваемых деталей 12 мм и более
Рисунок 13 — Схемы получения сигналов, в том числе опорных, при настройке чувствительности
Допускается настраивать чувствительность по цилиндрическому отражателю, сегменту при условии воспроизведения браковочного или контрольного (суммарно) уровня чувствительности контроля с погрешностью ±1 дБ.
Допускается проводить настройку чувствительности и определение эквивалентной площади (диаметра) обнаруженных несплошностей по НО с плоскодонными отражателями при УЗК СС с толщиной свариваемых деталей более 5,5 мм.
7.4.2.5 При пересчете эквивалентной площади плоскодонного отражателя из площади углового отражателя необходимо использовать формулу
Sn = N-Syrn, (7)
где Sn — эквивалентная площадь плоскодонного отражателя, мм2;
Л/ — коэффициент, зависящий от угла прозвучивания;
Syrn — площадь углового отражателя (зарубки), мм2.
Значения коэффициента Л/для некоторых углов приведены в таблице 6.
Таблица 6 — Зависимость коэффициента N от угла ввода НП
Угол ввода ПЭП, град | 40 | 45 | 50 | 55 | 60 | 65 | 70 | 72 |
Коэффициент N | 2,4 | 1,75 | 1,25 | 0,85 | 0,6 | 0,5 | 0,7 | 0,8 |
При пересчете эквивалентной площади плоскодонного отражателя из площади цилиндрического отражателя необходимо использовать формулу
Sn=LjR~b, (8)
где Sn — эквивалентная площадь плоскодонного отражателя, мм2;
X — длина УЗ-волны, мм;
R — расстояние до цилиндрического отражателя, мм;
b — радиус цилиндрического отражателя, мм.
7.4.2.6 Настройку чувствительности при УЗК СС с толщиной свариваемых деталей 12 мм и более проводят с помощью искусственных отражателей в НО и/или КО (рисунок 136) и/или АРД-диаграмм. Примеры настройки представлены в приложении Н.
7.4.2.7 Допускается использование НО с плоскодонными отражателями (зарубками), площади которых отличаются от регламентируемых федеральными нормами и правилами в области использования атомной энергии, документами по стандартизации, КД, ТД, устанавливающими требования к оценке соответствия металла СС и наплавленных поверхностей, значений, при условии корректировки чувствительности на величину АД, определенную формулой где SHopM — площадь плоскодонного отражателя (зарубки) по нормам федеральных норм и правил в области использования атомной энергии, документов по стандартизации, КД, ТД, устанавливающих требования к оценке соответствия металла СС и наплавленных 2 поверхностей, мм ,
AA = 20lg
°норм $обр
(9)
So6p — площадь фактически выполненного отражателя (зарубки) в образце, мм2.
Допускается определять величину корректировки по АРД-диаграммам по приложению Н. При этом величина ДА не должна превышать 12 дБ.
7.4.2.8 Для СС с толщиной свариваемых деталей не более 20 мм допускается проводить настройку чувствительности по угловым отражателям в соответствии с 7.4.2.4 и приложением Н.
7.4.2.9 Для получения опорных сигналов допускается использовать отражатели в виде поверхностей, прямых углов НО или ОК. При этом разница между опорным сигналом и настраиваемым уровнем чувствительности должна быть указана в ТИ и/или ТКК.
7.4.2.10 При настройке чувствительности по двугранному углу образца вместо плоскости, перпендикулярной к УЗ-лучу, следует учитывать, что при работе ПЭП с углами ввода от 37° до 52° эхо-сигналы от угла и плоскости отличаются не более чем на ±0,5 дБ, а при работе ПЭП с углом ввода от 57° до 65’ эхо-сигнал от угла менее эхо-сигнала от плоскости на (10 ± 1) дБ. Для углов ввода поперечных волн от 32° до 36° и от 57° до 65° этот способ настройки допускается использовать только в исключительных случаях (при отсутствии возможности выполнить настройку по НО с требуемыми отражателями).
7.4.2.11 Сглаживание вершины угла путем снятия фаски (под углом 45°) допускается в пределах, регламентируемых согласно данным, приведенным в таблице 7. При этом искажение эхо-сигнала не должно превышать ±1 дБ.
Таблица 7 — Максимально допустимая ширина фаски Вф в вершине двугранного угла образца
Частота, МГц | (Вф ± 1,0) мм при толщине образца | |
От 70 до 120 мм | Св. 120 мм | |
2,0 ±0,5 4,0 ± 1,0 | 1,5 1,0 | 3,0 2,0 |
При УЗК на продольные несплошности кольцевых СС трубопроводов и цилиндрических конструкций отраженным лучом с настройкой по плоскопараллельным образцам или по опорным сигналам, полученным прямым лучом, следует учитывать потери энергии на внутренней цилиндрической поверхности околошовной зоны контролируемого СС. Для этого вводят поправки ДА, определяемые экспериментально или в соответствии с графиком на рисунке 14. Значение поправки округляют до ближайшего целого значения.
7.4.2.12 При УЗК металла наплавленной поверхности на кромках СС чувствительность настраивают по плоскодонным отражателям в НО или АРД-диаграммам (при проведении УЗК со стороны 28
основного металла). Примеры НО для УЗК металла наплавленной поверхности на кромках показаны на рисунках 9а, б и 10а, в (НО для УЗК металла наплавленной поверхности на кромках под сварку из сталей перлитного класса НП со стороны наплавленной поверхности); схема настройки диапазона развертки и браковочного уровня чувствительности — на рисунках 9в и 106, где S и d— нормативные значения эквивалентных площади и диаметра.
7.4.2.13 При УЗК зоны сплавления металла антикоррозионной наплавленной поверхности из сталей аустенитного класса с основным металлом чувствительность настраивают по НО, представленным на рисунке 11, или АРД-диаграммам (при проведении УЗК со стороны основного металла).
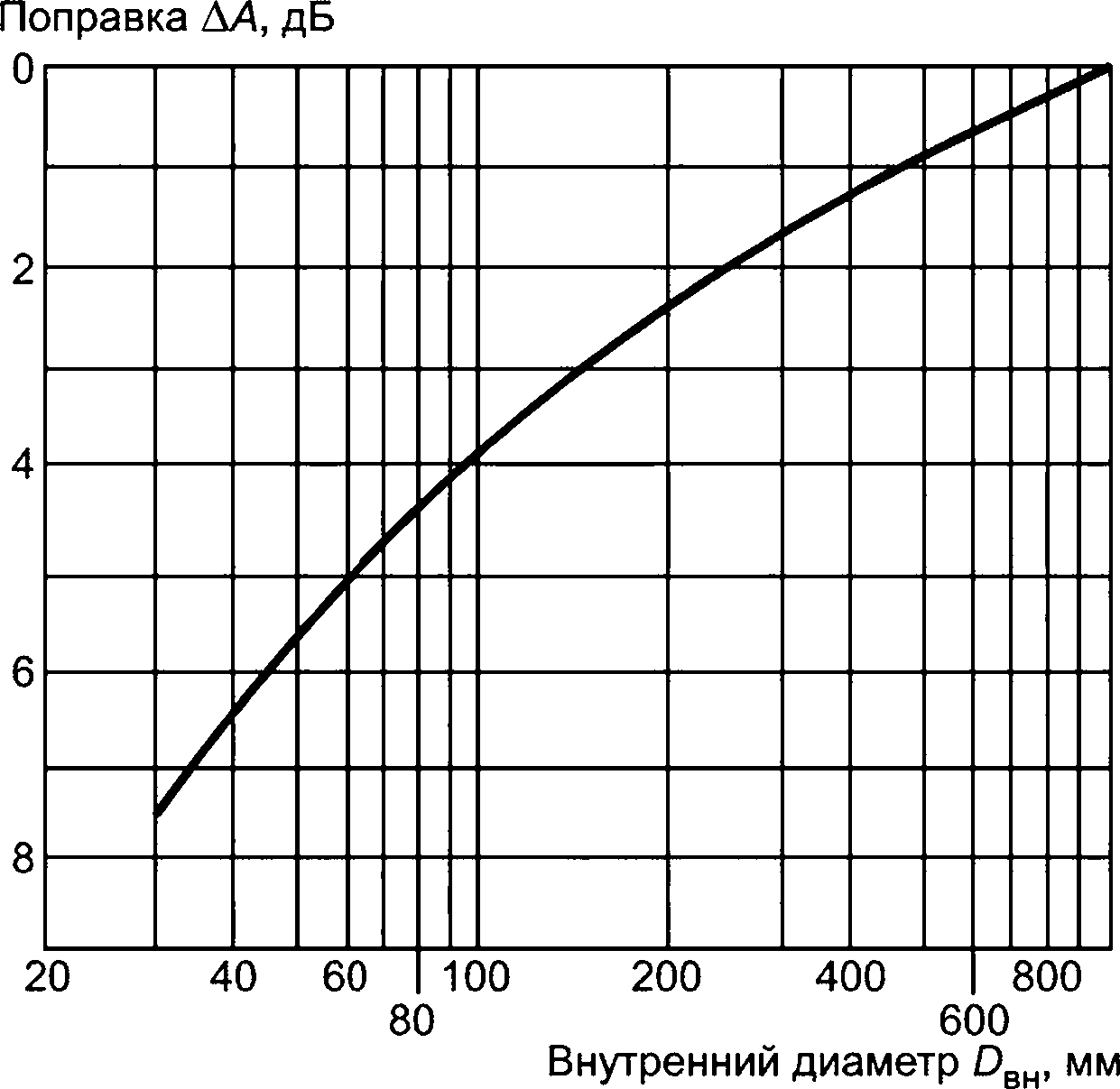
Рисунок 14 — Поправка на потери чувствительности при отражении от донной поверхности кольцевых СС трубопроводов и цилиндрических конструкций для НП на частотах от 1,25 до 5,00 МГц включительно с углами ввода от 40° до 50°
При настройке и проведении УЗК ПС ПЭП на частотах от 1,8 до 2,5 МГц включительно по АРД-диа-граммам и использовании в качестве опорного сигнала эхо-сигнала от донной поверхности необходимо учитывать дополнительное ослабление сигнала в металле наплавленной поверхности, равное 0,35 дБ/мм (рисунок 15). Учитывать затухание необходимо для каждого конкретного ПЭП.
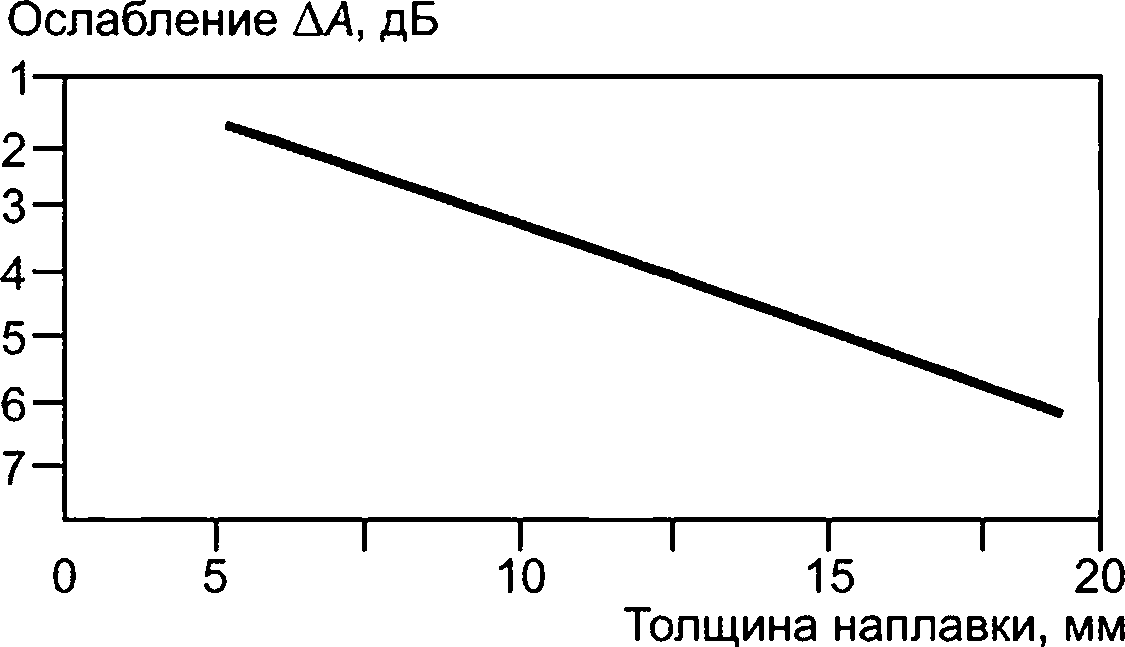
f = 1,80 - 2,50 МГц (для f = 2 МГц, затухание равно 0,35 дБ/мм)
Рисунок 15 — Ослабление ДА донного сигнала за счет затухания в металле наплавленной поверхности из сталей аустенитного класса различной толщины при УЗК продольной волной ПС ПЭП
7.4.2.14 Глубина залегания дна отражателя в НО по рисунку 116 не должна отличаться от номинальной толщины металла наплавленной поверхности более чем на 1 мм при толщине металла наплавленной поверхности не более 12 мм и более чем на 2 мм при большей толщине. Толщина металла наплавленной поверхности и глубина отражателя в образце, представленном на рисунке 116, г должны быть равными минимальной толщине металла наплавленной поверхности ±1 мм в зоне контроля. Толщина основного металла НО и глубина отражателя в образце, представленном на рисунке 11 в, должны быть равными толщине основного металла ±1 мм в зоне контроля, но не менее 15 мм.
Для исключения перебраковки отражающая поверхность плоскодонного отражателя во всех случаях должна располагаться в основном металле.
НО изготавливают из тех же материалов и по той же технологии, что и контролируемое СС и/или наплавленная поверхность. При отсутствии такой возможности необходимо руководствоваться 6.9.4. НО, представленный на рисунке 116, допускается изготавливать из основного металла толщиной (Н + Нн) без наплавленной поверхности. НО могут быть изготовлены в виде фрагментов НО, приведенных на рисунке 9.
7.4.2.15 Настройку чувствительности по НО следует проводить в случаях УЗК:
- в ближней зоне ПЭП;
- ПРС ОК толщиной от 3 до 10 мм включительно;
- ПЭП, кривизна контактной поверхности которых соответствует кривизне поверхности в зоне контроля.
7.4.2.16 Для проведения УЗК настройку чувствительности выполняют таким образом, чтобы на максимально возможной глубине залегания несплошности в СС и/или наплавленной поверхности был реализован уровень чувствительности, установленный федеральными нормами и правилами в области использования атомной энергии, документами по стандартизации, КД, ТД, устанавливающими требования к оценке соответствия металла СС и наплавленных поверхностей.
Для толщин свариваемых деталей свыше 40 мм рекомендуется использовать ВРЧ (АРК). Настройку ВРЧ (АРК) проводят в соответствии с инструкцией по эксплуатации дефектоскопа.
7.4.2.17 При УЗК СС по схеме «тандем» установку браковочного уровня по 7.4.2.2 а) и оценку эквивалентного диаметра (площади) обнаруженной несплошности проводят с помощью АРД-диаграммы по схеме «тандем» (рисунок 16) относительно опорного донного сигнала Аоо, получаемого непосредственно на ОК развернутыми навстречу друг другу ПЭП (рисунок 16). Рабочую зону развертки устанавливают путем стробирования опорного сигнала.
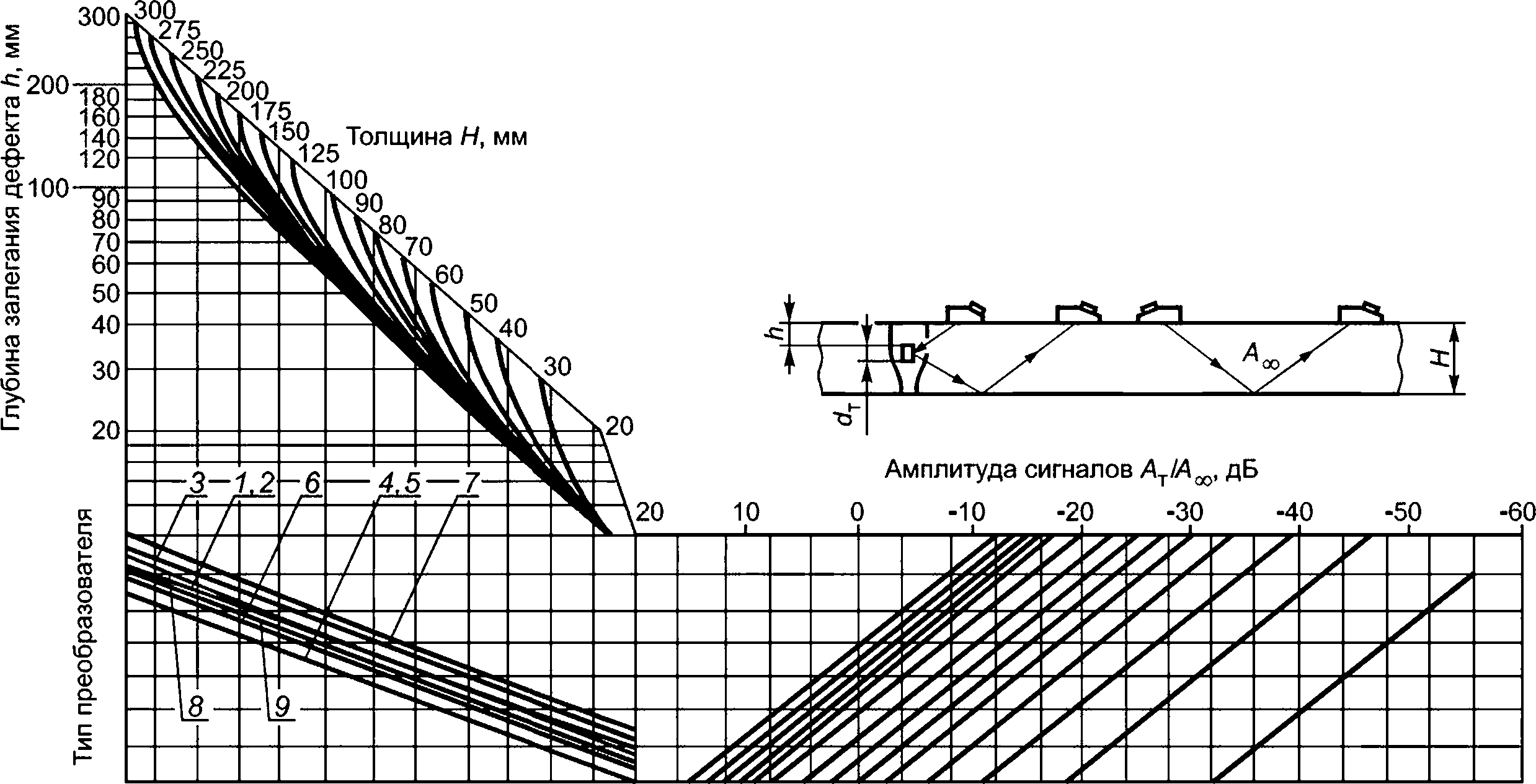
14 12 10 8 6 4 3 2 1 ф
Эквивалентный диаметр, мм
1 — П121-1,8-30°° (ПЭ 0 18 мм); 2— П121-1,8-40° (ПЭ 0 18 мм); 3 — П121-1,8-50° (ПЭ 12 *16 мм); 4 — П121-2.5-ЗО0 (ПЭ 0 12 мм);
5 — П121-2,5-40° (ПЭ 0 12 мм); 6 — П121-2.5—50° (ПЭ 12 х 16 мм); 7 — ИЦ 1,8-50° (ПНЦ); 8 — ИЦ 1,8-30°, 1,8-40° (ПНЦ), WB 35-N2, MWB 35-N2; 9 — ИЦ 2,5-30°, 40°, 50° (ПНЦ), WB 45 — N2, MWB 45 — N2
Рисунок 16 — АРД-диаграмма при проведении УЗК по схеме «тандем»
7.4.2.18 Настройку аппаратуры и оценку несплошностей при УЗК СС сферических корпусов задвижек трубопроводов проводят в соответствии с приложением П.
7.5 Проведение ультразвукового контроля
7.5.1 УЗК проводят контактным способом, перемещая ПЭП по поверхности ОК в зоне контроля.
7.5.2 В процессе сканирования обеспечивают постоянный акустический контакт ПЭП с наплавленной поверхностью и поверхностью свариваемых деталей.
7.5.3 В процессе перемещения ПЭП проводят его повороты относительно собственной вертикальной оси в точке выхода от 0° до 15° (за исключением ПЭП, у которых контур рабочей поверхности соответствует радиусу кривизны поверхности ОК в зоне контроля).
7.5.4 Величина шага сканирования не должна превышать половины максимально допустимой условной протяженности одиночной несплошности, расположенной на половине толщины СС.
Для СС с толщиной свариваемых деталей более 100 мм допускается устанавливать шаг сканирования равным половине диаметра/ширины ПЭ.
7.5.5 При УЗК по размеченным участкам перекрытие у границ участков должно быть не менее шага сканирования ПЭП.
7.5.6 Для стабилизации положения ОК цилиндрической формы при УЗК применяют насадки для ПЭП.
7.5.7 Скорость сканирования не должна превышать 150 мм/с.
7.5.8 Проведение УЗК металла антикоррозионной наплавленной поверхности
7.5.8.1 УЗК металла наплавленной поверхности (в том числе антикоррозионной) проводят путем построчного сканирования перпендикулярно к наплавленным валикам с шагом не более половины диаметра (ширины) ПЭП при УЗК со стороны основного металла и не более половины условной протяженности предельно допустимого отражателя при УЗК со стороны наплавленной поверхности.
7.5.8.2 При сканировании ПРС ПЭП рекомендуется, чтобы направления электроакустического экрана и наложения валика наплавленной поверхности совпадали.
7.5.8.3 При УЗК зоны сплавления металла антикоррозионных наплавленных поверхностей и металла наплавленных поверхностей из сталей аустенитного класса на кромках со стороны наплавленной поверхности ПРС ПЭП сканирование в прикромочных областях осуществляют при ориентации электроакустического экрана ПЭП перпендикулярно к краю кромки. Необходимо следить за положением ПЭП, не допуская нависания ПЭ над краем кромки более чем на 2 мм.
7.5.9 Проведение УЗК СС
7.5.9.1 УЗК СС при поперечно-продольном сканировании НП проводят путем перемещения ПЭП по поверхности сварных деталей параллельно оси сварного шва с одновременным возвратно-поступательным перемещением перпендикулярно к оси (рисунок 17).
X, мм Начало отсчета
Контрольный уровень
Рисунок 17 — Схема определения координат несплошности (а) и амплитуды эхо-сигнала (б)
7.5.9.2 УЗК ПС и ПРС ПЭП проводят путем его перемещения по поверхности СС вдоль или поперек шва.
7.5.10 Ширину зоны сканирования (см. Хтах на рисунке 18) определяют с учетом толщины свариваемых деталей геометрическим построением или расчетом в соответствии с формулой (10) при УЗК прямым лучом или формулой (11) при УЗК однократно отраженным лучом и указывают в ТИ и/или ТКК.
Хтах = ^ ' tga + е/2 + А,
(Ю)
где Хтах — ширина зоны сканирования, мм;
Н — толщина свариваемой детали, мм;
а — угол ввода УЗ, град;
е — ширина сварного шва (усиление), мм;
А — ширина прилегающих к СС участков основного металла, подлежащих УЗК, мм;
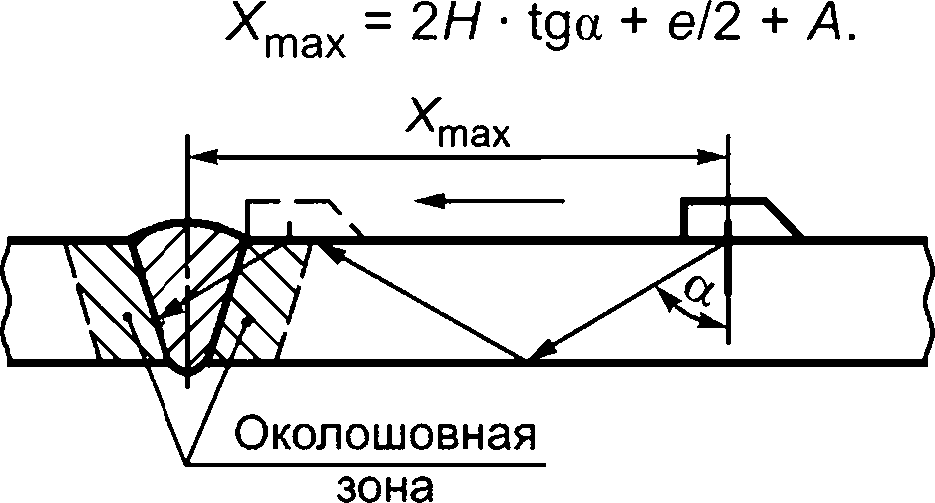
(11)
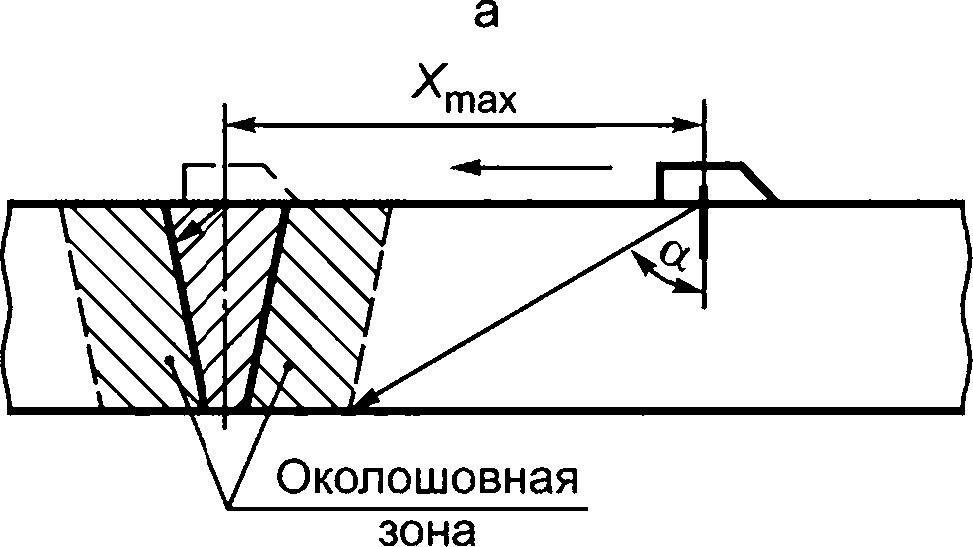
б
у ''max
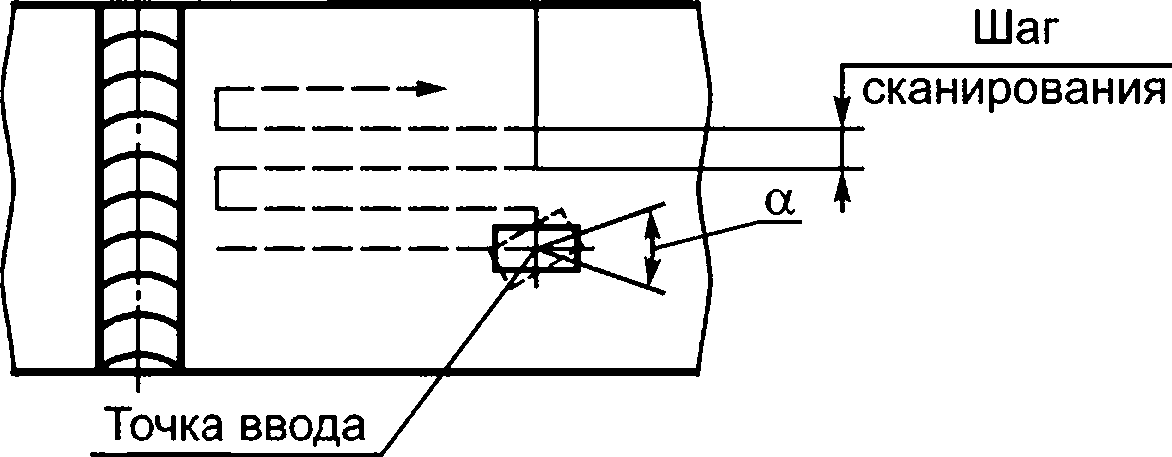
а — при УЗК СС с толщиной свариваемых деталей менее 60 мм; б — при УЗК СС с толщиной свариваемых деталей 60 мм и более; в — траектория сканирования; Хтах — максимальное удаление ПЭП от шва
Рисунок 18 — Схемы сканирования СС
7.6 Анализ результатов ультразвукового контроля
7.6.1 Определение характеристик несплошностей7.6.1.1 При обнаружении несплошностей с амплитудой эхо-сигнала, равной или большей контрольного уровня, определяют:
- максимальную амплитуду эхо-сигнала (максимальную эквивалентную площадь);
- координаты несплошности (в положении, соответствующем максимальной амплитуде эхо-сигнала);
- условную протяженность или класс идентификации по протяженности (протяженный — непротяженный).
В случаях, предусмотренных федеральными нормами и правилами в области использования атомной энергии, документами по стандартизации, КД, ТД, устанавливающими требования к оценке соответствия металла СС и наплавленных поверхностей или в целях получения дополнительной информации о несплошности определяют:
- условную высоту несплошности;
- характеристику формы и ориентации несплошности.
7.6.1.2 Условную высоту, характеристики формы и ориентации несплошностей определяют в случаях, предусмотренных федеральными нормами и правилами в области использования атомной энергии, документами по стандартизации, КД, ТД, устанавливающими требования к оценке соответствия металла СС и наплавленных поверхностей, или в целях получения дополнительной информации о несплошности.
7.6.1.3 Координаты h, х и L (рисунок 18) определяют при появлении в рабочей зоне экрана дефектоскопа эхо-сигнала следующим образом:
- координату h, мм (глубина залегания несплошности) определяют в соответствии с инструкцией по эксплуатации УЗ-дефектоскопа общего назначения, или по шкале развертки (путем сопоставления с положением сигналов от отражателей в НО), или расчетом;
- координату х мм, определяют как кратчайшее расстояние от продольной оси СС до местоположения несплошности (в горизонтальной плоскости). При этом, местоположение несплошности определяют по известному значению угла ввода расчетом или по индикатору дефектоскопа, или отсчетом по градуированной шкале развертки, или по координатным линейкам;
- координату L, мм (расстояние от точки, соответствующем началу отсчета до местоположения несплошности — вдоль оси СС) — как место расположения несплошности вдоль продольной оси шва относительно начала отсчета.
Координаты измеряют при положении ПЭП, соответствующем максимальной амплитуде эхо-сигнала от несплошности. Значение максимальной амплитуды считывают при доведении сигнала до определенного уровня (обычно уровня, равного половине высоты экрана дефектоскопа).
Если настройка глубиномера проводилась по СО-2, то при глубине залегания несплошностей более 150 мм оцененная с применением УЗ-дефектоскопа глубина несплошности может отличаться от реальной из-за квазиискривления акустического луча, связанного с затуханием УЗ в металле. При этом необходимо руководствоваться требованиями 7.4.1.8.
7.6.1.4 Амплитуду эхо-сигнала измеряют по показаниям усилителя (аттенюатора) при заданной высоте на экране дефектоскопа. Измерение максимальной эквивалентной площади несплошности проводят по максимальному сигналу независимо от направления прозвучивания, при котором он получен.
7.6.1.5 Условную протяженность (рисунок 19) измеряют как расстояние между крайними положениями ПЭП при его перемещении вдоль несплошности. При этом крайними положениями ПЭП считают те, при которых амплитуда эхо-сигнала уменьшается до контрольного уровня чувствительности.
AL — условная протяженность
Рисунок 19 — Схема определения условной протяженности AL несплошности
При УЗК кольцевых СС трубопроводов и цилиндрических конструкций условную протяженность AL вычисляют по найденному значению А£изм условной протяженности по формуле
Ы-— AZ-изм^
(12)
где h, мм — глубина залегания несплошности;
D, мм — наружный диаметр трубопровода или цилиндрической конструкции.
7.6.1.6 Условную высоту (рисунок 20) определяют, как разность значений глубины залегания несплошности в крайних положениях ПЭП, при которых амплитуда эхо-сигнала уменьшается до контрольного уровня чувствительности.
Контрольный уровень
А/? = h2 - hi
а
б
Л/? — условная высота
Рисунок 20 — Схемы определения условной протяженности: схематичное изображение сигналов на экране дефектоскопа при перемещении ПЭП (а) и схема определения условной высоты (б) несплошности
7.6.1.7 Условную высоту протяженной несплошности определяют в том месте, где эхо-сигнал имеет наибольшую амплитуду. Условную высоту определяют только для несплошностей, отстоящих от внутренней или наружной поверхности СС более чем на 5 мм.
7.6.1.8 Несплошности в количестве двух или более учитывают раздельно, если эхо-сигналы от них, наблюдаемые на экране одновременно или последовательно при перемещении ПЭП по поверхности металла в зоне контроля, разделены интервалом (на линии развертки или вдоль линии сканирования), где амплитуда уменьшается на 6 дБ или более относительно меньшего эхо-сигнала. Если это условие не выполняется, то несплошности рассматриваются как одна несплошность.
7.6.1.9 Пределы погрешности измерения параметров несплошностей не должны превышать:
- амплитуд эхо-сигналов — ±2 дБ;
- эквивалентной площади — ±50 %;
- условной протяженности — ±5 мм для толщин не более 200 мм и ±10 мм для толщин более 200 мм;
- условной высоты — удвоенных пределов Д/?о погрешности глубиномера дефектоскопа.
При сличении результатов УЗК согласно [2] (пункт 89) расхождения результатов измерений считают приемлемыми, если они не превышают величины 1,41 А, где А — предел погрешности измерения соответствующего параметра несплошности, указанный выше.
Для получения воспроизводимости результатов УЗК в ТИ и/или ТКК следует однозначно указывать применяемые при УЗК типы ПЭП, или их параметры (например, размеры пьезопластины, частота, диаграмма направленности).
7.6.1.10 Число одиночных несплошностей или их суммарную эквивалентную площадь определяют по длине СС или площади антикоррозионной наплавленной поверхности соответственно.
При этом расстояние между двумя отдельными несплошностями определяют как расстояние между двумя ближайшими положениями ПЭП, при которых сигнал от одной несплошности уменьшается до контрольного уровня, а сигнал от другой достигает контрольного уровня.
7.6.1.11 При проведении оценки геометрических размеров, формы и ориентации несплошностей используют методики, приведенные в приложениях А и Б, иные методики УЗК, прошедшие оценку соответствия в форме аттестационных испытаний согласно ГОСТ Р 50.04.07.
7.6.1.12 При интерпретации результатов УЗК учитывают особенности УЗК СС различных конструкций в соответствии с приложением Р.
7.6.2 Оценка допустимости несплошностей
7.6.2.1 Допустимость зафиксированных несплошностей оценивают в соответствии с требованиями федеральными нормами и правилами в области использования атомной энергии, документами по стандартизации, КД, ТД, устанавливающими требования к оценке соответствия металла СС и наплавленных поверхностей.
7.6.2.2 При оценке допустимости несплошностей по протяженности их классифицируют на протяженные и непротяженные (точечные) по приложению С.
7.6.2.3 Несплошность считают поперечным дефектом типа «Т», если при прозвучивании в направлении продольной оси шва ее эквивалентная площадь (Snor), мм2) независимо от условной протяженности равна 50 % или более величины наименьшей фиксируемой эквивалентной площади, а при расположении ПЭП под углом (90 ± 15)° к продольной оси шва его эквивалентная площадь менее 50 % Sn 0 п. При проведении УЗК по схеме «тандем» поиск поперечных несплошностей типа «Т» осуществляется путем сканирования вдоль оси СС со снятым усилением.
7.6.2.4 Браковочный уровень при операционном контроле СС и металла наплавленных поверхностей, подвергаемых окончательной термообработке, рекомендуется снижать (повышать чувствительность) на 3 дБ, учитывая вероятность увеличения эхо-сигнала от несплошности после термообработки.
7.6.2.5 Рекламации по результатам УЗК должны быть основаны на данных контроля с учетом требований 7.6.1.9, выполненного в соответствии с настоящим стандартом и ТИ и/или ТКК.
7.6.2.6 Для получения дополнительной информации о характеристике формы и ориентации несплошности следует использовать указания 7.6.1.11.
7.6.2.7 Если обнаруженная несплошность залегает в пределах ближней зоны ПЭП, то ее окончательную оценку проводят другим ПЭП с длиной ближней зоны, меньшей расстояния до несплошности, или сравнением с контрольным отражателем максимально допустимой эквивалентной площади, выполненным на глубине залегания несплошности. Ближнюю зону ПЭП определяют в соответствии с ГОСТ Р 50.05.05—2018 (пункт 7.1.12) или оценивают по НО, содержащему БЦО 0 2 мм, расположенные на различном расстоянии относительно поверхности ввода УЗ.
8 Учетная и отчетная документация
8.1 Требования к учетной документации
8.1.1 Требования к учетной документации (журналам) по неразрушающему контролю изложены в [2], [10].
8.1.2 Журнал результатов УЗК должен иметь сквозную нумерацию страниц, быть сброшюрован и скреплен подписью руководителя подразделения неразрушающего контроля.
8.1.3 Все исправления и изменения в журнале должны быть заверены подписью руководителя подразделения неразрушающего контроля с указанием даты их внесения.
8.1.4 В журнал допускается вносить дополнительные данные.
8.1.5 Ведение журнала в электронном виде допускается при условии обеспечения восстановления результатов УЗК в случае утраты или порчи отчетной документации.
8.2 Требования к отчетной документации
8.2.1 На основании учетной документации должна быть оформлена отчетная документация в виде заключения (протокола).
8.2.2 Требования к отчетной документации, требования к форме и содержанию заключения (протокола) по неразрушающему контролю изложены в [2], [10].
8.2.3 В заключение (протокол) допускается вносить дополнительные данные.
8.2.4 Для сокращенной записи следует использовать буквенно-цифровую форму записи результатов УЗК в соответствии с приложением Т.
9 Требования к метрологическому обеспечению
9.1 Метрологическое обеспечение УЗК, включая метрологическое обеспечение аттестованных объектов и методик измерений, должно соответствовать требованиям [11], [12] с учетом ГОСТ Р 50.05.16.
9.2 Средства измерений (дефектоскопы, меры и другие средства измерений, входящие в сферу государственного регулирования), применяемые при УЗК, должны быть утвержденного типа и пройти своевременную поверку.
9.3 ПЭП, применяемые при УЗК, должны иметь заводской номер и маркировку.
9.4 НО для настройки (регулировки) УЗ-дефектоскопов, в случае отнесения к аттестованным объектам, в соответствии с [12], подлежат первичной и периодической аттестациям (подтверждение метрологических характеристик). Периодичность подтверждения метрологических характеристик устанавливают при первичной аттестации.
9.5 Проекты методик УЗК подлежат рассмотрению в соответствии с ГОСТ Р 50.04.07—2022 (пункт 6.15).
10 Требования безопасности
10.1 УЗ-дефектоскопы являются переносными электроприемниками, поэтому при их эксплуатации должны выполняться требования по электробезопасности в соответствии с [13].
10.2 Перед допуском к проведению УЗК все лица, участвующие в его выполнении, должны проходить соответствующий инструктаж по охране труда с регистрацией в журнале регистрации инструктажа на рабочем месте.
10.3 Инструктаж следует проводить периодически в сроки, установленные организационно-распорядительным документом организации.
10.4 При проведении УЗК на высоте, в стесненных условиях, а также внутри сосудов специалисты и обслуживающий персонал проходят дополнительный инструктаж по охране труда согласно положению, действующему в организации.
10.5 Специалисты, участвующие в проведении УЗК, должны знать и выполнять общие требования по охране труда, установленные для работников цехов и участков, в которых проводят УЗК.
10.6 Требования относительно защиты от вредного воздействия постоянных магнитных полей должны соответствовать требованиям [14]. Специалисты должны быть обеспечены специальной защитной одеждой, не стесняющей движение (костюмами, комбинезонами, халатами), средствами защиты ног и рук, средствами защиты головы, обтирочными материалами (обрезками ткани с хорошей смачиваемостью), кремом для рук, мылом, полотенцами, блокнотами и пишущими инструментами. Номенклатура и нормы расхода средств индивидуальной защиты и материалов устанавливаются организацией в зависимости от объемов и условий работы.
10.7 При проведении УЗК вблизи мест выполнения сварочных работ рабочее место специалиста должно быть ограждено светозащитными экранами.
10.8 При проведении работ в зоне ионизирующего излучения должны соблюдаться требования по обеспечению радиационной безопасности, установленные законодательством Российской Федерации в области использования атомной энергии [15].
10.9 Требования безопасности при проведении УЗК СС и металла наплавленных поверхностей должны соответствовать ГОСТ Р 55724—2013 (раздел 12).
Приложение А (справочное)
Методика распознавания типа несплошностей по коэффициенту формы
А.1 Общие требования
А.1.1 Настоящая методика определяет порядок и специальные нормы оценки типа (плоскостные или объемные) обнаруженных несплошностей. К плоскостным несплошностям относят трещины, несплавления по кромкам разделки, непровары. К объемным относят шлаковые и газовые включения, шлаковые трубки, поры и зоны пористости. Несплошности вблизи от поверхностей свариваемых деталей по настоящей методике не распознаются.
А. 1.2 Методика распространяется на стыковые СС деталей с эквидистантными поверхностями, удовлетворяющих условию по формуле (1), с толщиной свариваемых деталей от 60 до 300 мм включительно.
Методика не распространяется на СС литых деталей, деталей с антикоррозионной наплавленной поверхностью, а также деталей из биметалла.
А. 1.3 Распознавание плоскостных и объемных несплошностей проводят путем определения коэффициента формы несплошности Кф.
Кф определяют при прозвучивании несплошностей по схеме «тандем» (эхо-зеркальный метод УЗК) двумя НП, включенными по PC-схеме (рисунок А.1). Кф вычисляют в виде отношения амплитуды сигнала, отраженного от несплошности обратно к ПЭП б/д, к амплитуде сигнала, прошедшего от одного ПЭП к другому и испытавшего отражение от несплошностей и внутренней поверхности СС U3. Оценка типа несплошности по Кф обусловлена различием в направленности отраженного от объемных и плоскостных несплошностей УЗ-поля.
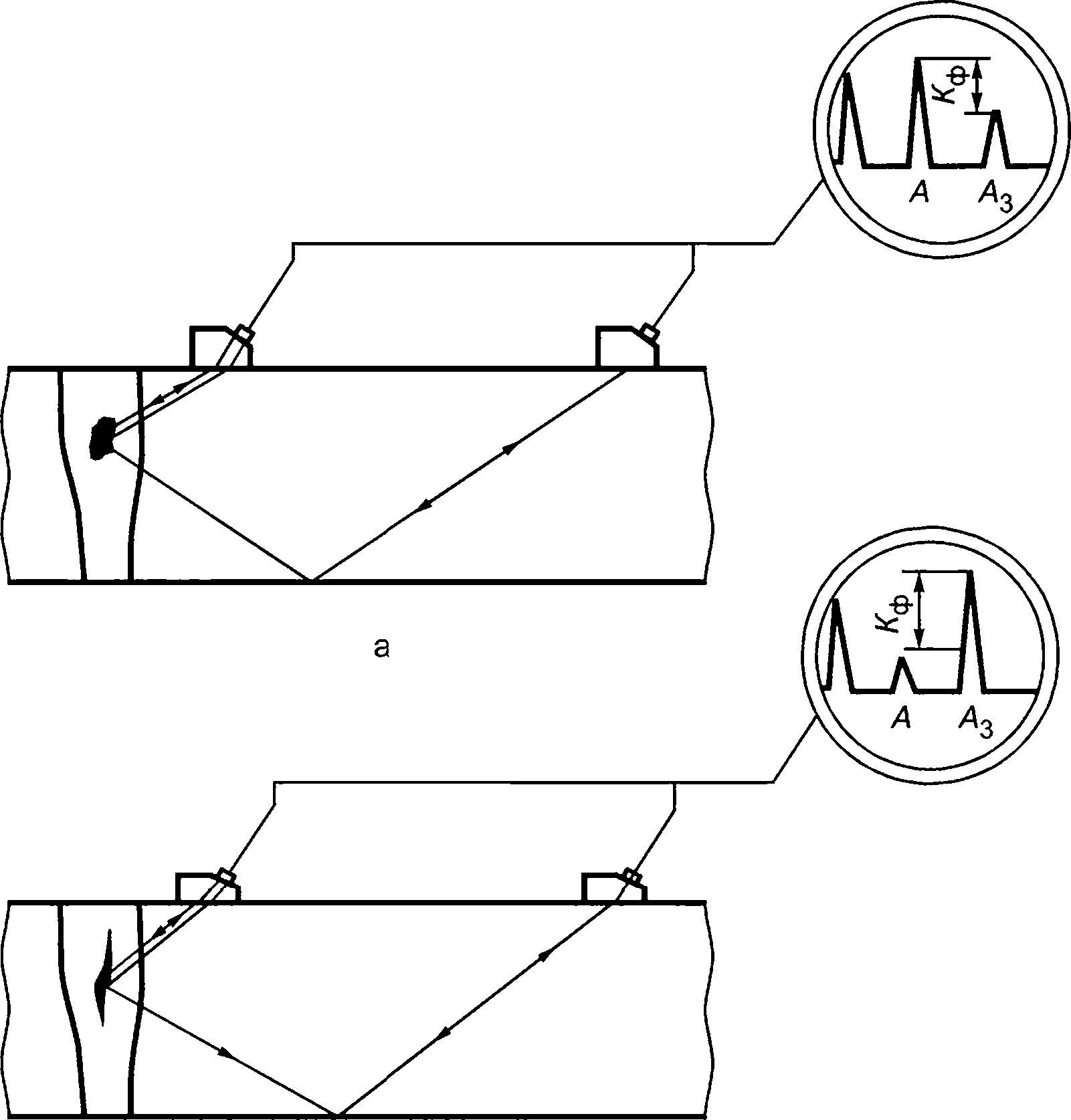
Рисунок А.1 — Коэффициент формы объемных (а) и плоскостных (б) несплошностей
А.1.4 УЗК проводят любым типом дефектоскопов.
А. 1.5 УЗК проводят двумя однотипными НП с углами ввода от 40° до 50° с частотами от 1,8 до 2,5 МГц включительно.
Примечание — Рекомендуется использовать тот тип ПЭП, которым проводился поиск несплошностей.
А.1.6 Абсолютная разница в величине углов наклона ПЭП не должна превышать 1°.
ПЭП должны иметь одинаковую чувствительность. ПЭП считают одинаковыми по чувствительности, если при прозвучивании каждым из них последовательно одного и того же отражателя в СО-2 по ГОСТ Р 55724 амплитуды эхо-сигналов отличаются не более чем на 1 дБ.
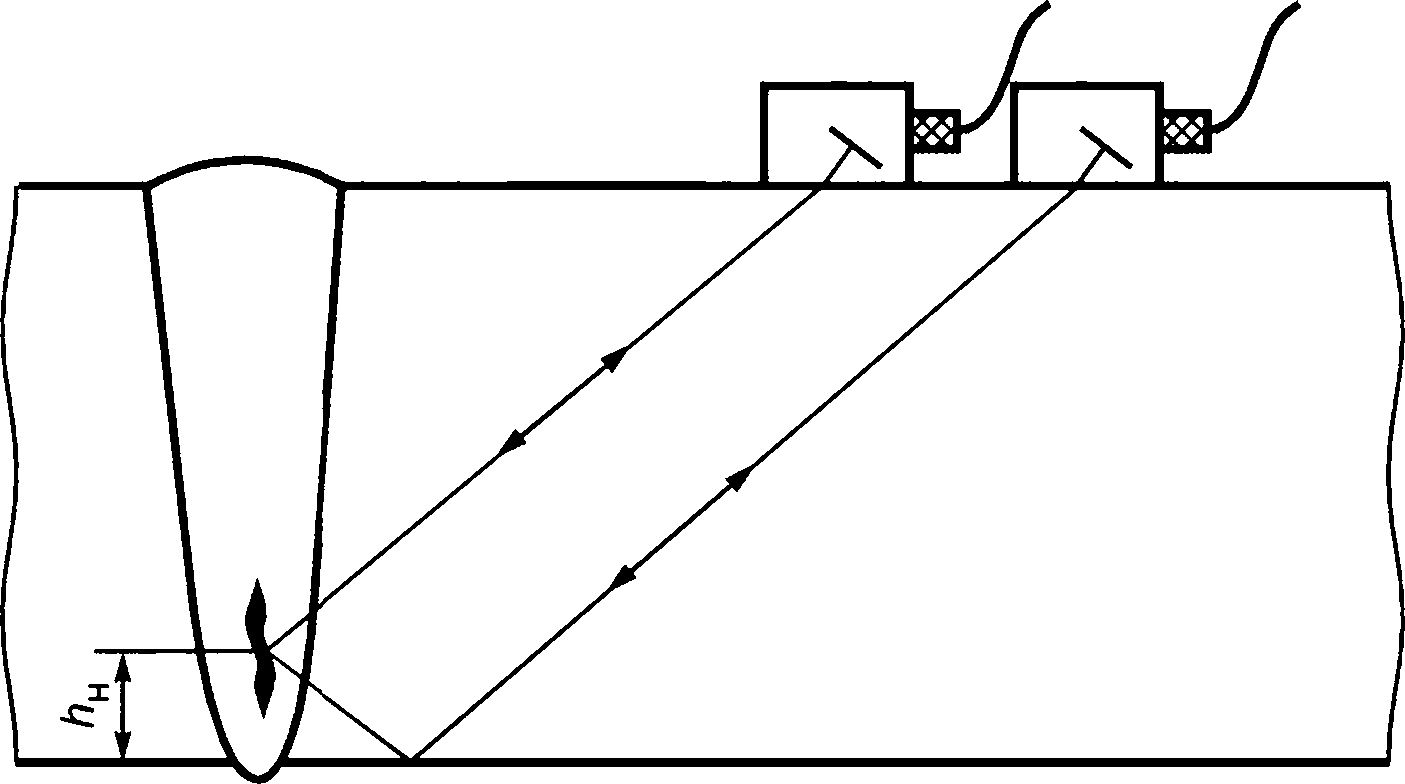
Рисунок А.2 — Зона непрозвучивания /?н при определении коэффициента формы несплошности
Если из ПЭП, имеющихся в распоряжении специалиста по УЗК, не удается подобрать два равных по чувствительности и однотипных, то для выравнивания чувствительности следует включить последовательно в цепь одного из ПЭП переменное сопротивление от 0,5 до 1,0 КОм.
При проведении УЗК следует учитывать наличие зоны «непрозвучивания» (рисунок А.2) — слоя металла, не-сплошность в котором не может быть достоверно оценена по Кф. Величина hH этой зоны может быть уменьшена за счет использования ПЭП меньших габаритных размеров (например, применение ПЭП с углом ввода 50° на частоту 2,5 МГц вместо ПЭП с углом ввода 50° на частоту 1,8 МГц уменьшает зону «непрозвучивания» на 8 мм) за счет изменения конструкций ПЭП (уменьшения стрелы заднего и габаритов разъема переднего ПЭП).
Если при УЗК обеспечен доступ к сварному шву с обеих поверхностей свариваемых деталей, ПЭП устанавливают на той поверхности, к которой несплошность ближе.
А.1.7 Если конструкция СС не обеспечивает возможности установки двух ПЭП, то Кф не определяют.
А.2 Технология УЗК
А.2.1 ПЭП подключают к дефектоскопу по PC-схеме [ГОСТ Р 55724—2013 (рисунок 3)].
А.2.2 Чувствительность дефектоскопа во время проведения УЗК должна обеспечивать возможность наблюдения на экране минимум одного из двух сигналов.
А.2.3 УЗК проводят при диапазоне развертки, настроенной для контроля СС, в соответствии с 7.4.
А.2.4 Оба ПЭП устанавливают друг за другом на поверхности свариваемой детали в одной вертикальной плоскости и перемещают их в этой плоскости в поисках максимума сигнала U3.
При УЗК ПЭП устанавливают таким образом, чтобы точка ввода переднего ПЭП соответствовала глубине залегания несплошности, а точка ввода заднего ПЭП находилась в положении выявления «тандем»-сигнала от несплошности.
Положение сигнала U3 на линии развертки не зависит от глубины залегания несплошности и соответствует положению эхо-сигнала от нижнего угла образца толщиной, равной толщине контролируемого СС, при прозвучивании одним ПЭП.
А.2.5 Коэффициент формы определяют при фиксированном положении ПЭП, соответствующем максимуму сигнала U3. При этом чувствительность дефектоскопа устанавливают таким образом, чтобы на экране дефектоскопа были видны вершины сигналов UR и U3 или минимум одного из этих сигналов.
А.2.6 Коэффициент формы считают:
- положительным, если высота сигнала UR на экране дефектоскопа более высоты сигнала U3;
- равным 0 дБ, если UR отличается от U3 не более чем на 1 дБ;
- отрицательным, если UR менее U3.
А.2.7 Несплошность считают:
- объемной, если коэффициент формы имеет положительное или равное 0 дБ значение;
- плоскостной, если коэффициент формы имеет отрицательное значение.
А.2.8 Каждую несплошность оценивают по Кф прозвучиванием с двух сторон шва. Оценку Кф несплошности с условной протяженностью более 30 мм проводят не менее чем в трех сечениях несплошности.
Оценку типа несплошности проводят по наименьшему из полученных значений Кф.
Приложение Б (справочное)
Методика определения конфигурации и ориентации несплошностей при изменении угла наблюдения
Б.1 Настоящая методика определяет порядок и критерии оценки конфигурации и ориентации обнаруженных несплошностей по результатам их озвучивания под разными углами.
Б.2 По конфигурации несплошности разделяют на плоскостные и объемные. К плоскостным относят трещины, несплавления, непровары, для них определена ориентация. К объемным относят шлаковые включения и поры, их цепочки и скопления.
Б.З УЗК проводят ПЭП с переменным углом ввода на частоте 1,8 МГц.
Б.3.1 Положение ПЭП на поверхности ОК в зоне контроля и угол ввода в любой момент сканирования должны обеспечивать прохождение центрального УЗ-луча через максимум отражения.
Б.3.2 Допускается использовать специальное устройство, обеспечивающее автоматическое выполнение условия по Б.3.1 при ручном УЗК.
Б.3.3 Допускается использование комплекта из отдельных ПЭП с углами ввода от 40° до 65° и шагом не более 5°.
Б.4 Порядок проведения УЗК
Б.4.1 Устанавливают угол ввода ПЭП равным углу, при котором в процессе штатного УЗК обнаружена оцениваемая несплошность. Находят максимум сигнала и определяют глубину залегания центра отражения.
Б.4.2 Настройку диапазона развертки проводят по боковому сверлению, расположенному на глубине залегания несплошности, при максимальном угле ввода.
5.4.3 Чувствительность дефектоскопа должна обеспечивать возможность обнаружения несплошности во всем диапазоне углов.
Б.4.4 Оценивают амплитуды эхо-сигналов от несплошности при различных углах ввода (см. рисунок Б. 1а);
Б.4.5 Оценивают амплитуду эхо-сигналов от бокового сверления, расположенного на глубине залегания несплошности (опорный сигнал) при тех же углах ввода (см. рисунок Б. 16).
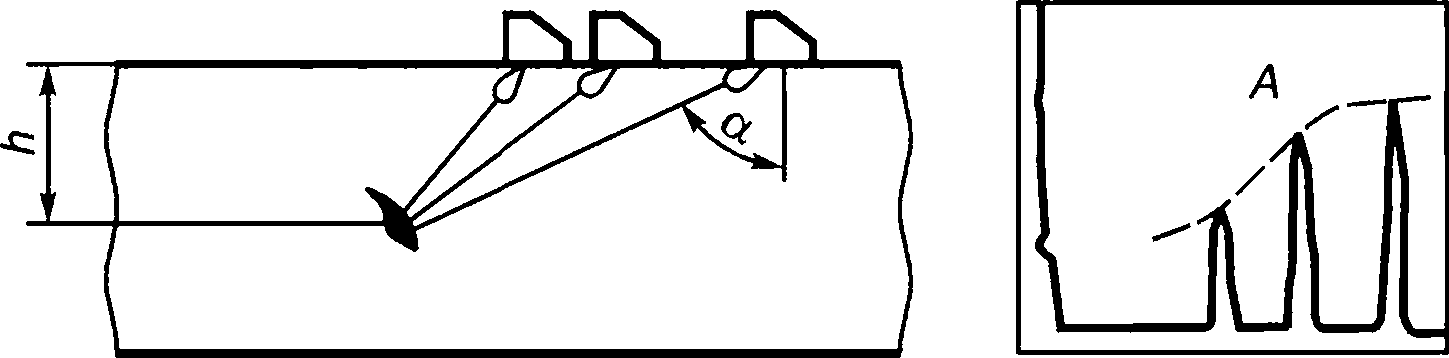

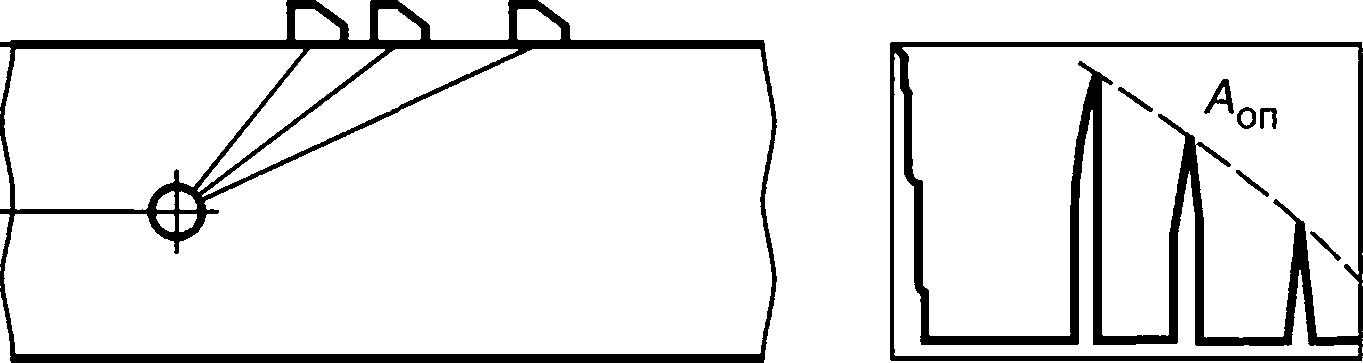
б
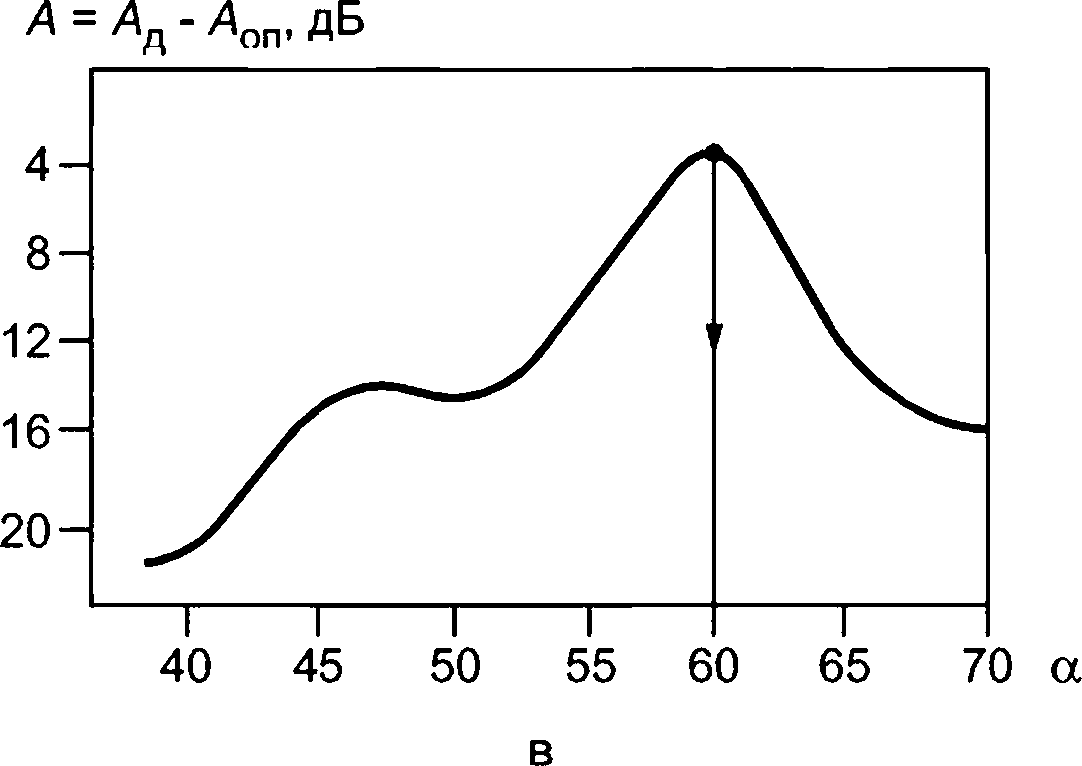
Рисунок Б.1 — Схемы определения ориентации несплошности
Б.4.6 По результатам УЗК строят нормированную по ненаправленному отражателю (боковому сверлению) огибающую эхо-сигналов от несплошности (рисунок Б.1в) в соответствии с формулой
(Б.1)
А Амт
где А — нормированная амплитуда эхо-сигнала от несплошности;
Дд — амплитуда эхо-сигнала от несплошности;
Доп — амплитуда эхо-сигнала от бокового сверления.
Б.4.7 При проведении УЗК отдельными ПЭП определяют эквивалентные площади несплошности для каждого угла ввода.
Б.5 По результатам УЗК оценивают несплошности.
Б.5.1 Каждую несплошность оценивают по результатам УЗК с двух сторон шва.
Б.5.2 Несплошность считают объемной, если нормированная амплитуда эхо-сигнала от нее изменяется во всем диапазоне углов не более чем на 12 дБ или ее эквивалентная площадь изменяется менее чем в четыре раза.
Б.5.3 Несплошность считают плоскостной, если изменение амплитуды больше 12 дБ или эквивалентная площадь изменяется более чем в четыре раза.
Б.5.4 Ориентация несплошности определена углом ввода, при котором амплитуда А максимальна (рисунок Б.1в).
Б.5.5 Если огибающая нормированной амплитуды сигнала А не имеет максимума, но возрастает при увеличении угла ввода в процессе УЗК с двух сторон шва, считают, что несплошность — плоскостная с вертикальной ориентацией. При этом для окончательной оценки ее оценивают по схеме «тандем».
Б.5.6 Если огибающая нормированной амплитуды сигнала от несплошности не имеет максимума, но увеличивается при уменьшении угла ввода, то для окончательной оценки рекомендуется проводить УЗК ПС или ПРС ПЭП при удаленном усилении.
Приложение В (справочное)
Составы контактных сред
В.1 Контактная среда на основе обойного клея
Строительный обойный клей растворяют в холодной или теплой воде в объемном соотношении 1:1—1:3 в зависимости от условий проведения УЗК.
В.2 Контактная среда на основе дикстрина
Состав контактной среды, %: дикстрин — 30—34; вспомогательное вещество ОП-7 по ГОСТ 8433 — 4; глицерин 9—10; сода — 1; вода — остальное. Дикстрин растворяют в нагретой до температуры от 40 °C до 50 °C воде, добавляют глицерин, вспомогательное вещество ОП-7, соду и размешивают до получения однородного раствора.
В.З Ингибиторная контактная среда ИКС-1
Состав контактной среды: на 1 л воды от 50 до 70 г глицерина, от 40 до 50 г натрий-карбоктиметилцеллюлозы (натрий-КМЦ), от 30 до 50 г тринатрийфосфата. В горячей воде при температуре от 60 °C до 80 °C растворяют КМЦ, а затем тринатрийфосфат. Доливают, непрерывно перемешивая, натрий-КМЦ. Раствор выдерживают в течение одних суток (до набухания). После этого добавляют глицерин.
Приложение Г (обязательное)
Требования к содержанию технологической карты и технологической инструкции ультразвукового контроля
Г.1 ТИ и/или ТКК должны содержать информацию о конструкции и категории СС или наплавленной поверхности в соответствии с КД, соответствовать требованиям [3]—[9], настоящего стандарта, иметь учетный номер и отражать рабочую технологию УЗК конкретного СС, металла наплавленной поверхности. Для серии однотипных СС, наплавленных поверхностей (в т. ч. и на заводах-изготовителях и на монтаже) допускается разрабатывать одну ТКК или одну ТИ.
Г.2 В ТИ и/или ТКК должна быть представлена информация в объеме, позволяющем воспроизвести технологию контроля и оценку качества для любого СС и/или наплавленной поверхности.
Г.З ТКК и ТИ должны содержать следующие сведения:
а) идентификацию СС и/или наплавленной поверхности [наименование, чертеж, материал (основной и сварочный), способ сварки; тип СС, класс, категория СС (наплавленной поверхности); объем контроля, степень контроледоступности; эскиз СС (наплавленной поверхности); стадия изготовления (операция в маршрутном технологическом процессе); сведения об организации — владельце ОК; сведения об организации, проводящей УЗК].
Сведения должны однозначно идентифицировать СС и/или наплавленную поверхность и давать исходную информацию для выбора схемы и расчета параметров УЗК;
б) документацию, регламентирующую проведение УЗК и устанавливающую исходные требования к технологии УЗК (федеральными нормами и правилами в области использования атомной энергии, документами по стандартизации, КД, ТД, устанавливающими требования к оценке соответствия металла СС и наплавленных поверхностей);
в) данные о типе и размерах СС и/или наплавленной поверхности, необходимые для разработки технологии УЗК — исходные данные для выбора параметров УЗК;
г) требования по оценке качества СС и/или наплавленной поверхности в соответствии с федеральными нормами и правилами в области использования атомной энергии, документами по стандартизации, КД, ТД, устанавливающими требования к оценке соответствия металла СС и наплавленных поверхностей, способ настройки чувствительности;
д) сведения о необходимой для проведения УЗК аппаратуре, средствах контроля.
Примечания
1 В сведениях о применяемом приборе (аппаратуре) необходимо указать марку УЗ-дефектоскопа. Допускается в соответствующей графе ТКК (пункте ТИ) или в примечании к ней (нему) дополнять указанный УЗ-дефектоскоп иными марками УЗ-дефектоскопов и/или модификациями приведенного в ТИ и/или ТКК. Также допускается указать возможность его замены на аналогичные приборы.
2 В сведениях о применяемом ПЭП необходимо указать его тип в соответствии с ГОСТ Р 55725 или рабочую частоту ПЭП, угол ввода (для НПЭП). Дополнительно следует указать максимально допустимую стрелу ПЭП (для НПЭП), сведения о форме и размере контактной поверхности ПЭП.
3 В сведениях о КО (мерах) указывается их тип в соответствии с ГОСТ Р 50.05.14.
4 В сведениях о НО необходимо указать номер НО, размер эталонных отражателей, глубину залегания эталонного отражателя (при необходимости). Допускается указывать иные сведения, необходимые для идентификации НО и/или проверки его применимости для проведения УЗК.
5 В случае указания в ТИ и/или ТКК вспомогательного оборудования указывается его тип;
е) схемы прозвучивания, схемы сканирования и параметры УЗК. На схемах указывают расположение зон контроля на СС и/или наплавленной поверхности;
ж) указания по подготовке к УЗК — требования к подготовке УЗК, в том числе требования по подготовке поверхности в зоне контроля в соответствии с требованиями федеральных норм и правил в области использования атомной энергии, документов по стандартизации, КД, ТД, устанавливающих требования к оценке соответствия металла СС и наплавленных поверхностей;
и) требования к оформлению отчетной документации в соответствии с КД, ТД и документации СМК, действующей в организации.
ТКК и ТИ могут включать другие дополнительные сведения. При необходимости, в них включают указания на условия и порядок проведения УЗК (сведения о месте проведения работ, допускаемом диапазоне рабочих температур), сведения о способе и схеме разметки СС и/или наплавленной поверхности на участки (зоны), состав звена специалистов по УЗК, проводящих контроль, краткое описание последовательности операций при проведении УЗК, 42
операции по обработке СС и/или наплавленной поверхности после проведения контроля, дополнительные материалы, используемые при проведении УЗК.
Г.4 В разделе «Оценка качества» ТКК и ТИ необходимо указывать сведения о допустимых или недопустимых в зависимости от категории СС или наплавленной поверхности эквивалентных площадях, условных размерах несплошностей (протяженности и/или площади), их количества, ориентации (например, дефекты типа «Т» отсутствуют), максимально допустимое или минимально необходимое расстояние между несплошностями, их местоположение. Допускается дополнять раздел иными требованиями в соответствии с федеральными нормами и правилами в области использования атомной энергии, документами по стандартизации, КД, ТД, устанавливающими требования к оценке соответствия металла СС и наплавленных поверхностей.
Г.5 ТКК и ТИ должны иметь идентификационное обозначение (учетный номер), которое присваивает организация-разработчик, содержать дату разработки ТИ и/или ТКК и быть подписанной (на каждом листе) разработчиком технологии УЗК с указанием номера его квалификационного удостоверения и даты его выдачи, а также проверяющим руководителем подразделения неразрушающего контроля.
Г.6 Рекомендуемая форма ТКК приведена на рисунке Г.1. Допускается иная форма ТКК, которая принята в организации, проводящей УЗК.
Наименование организации | ||||||||||
Наименование подразделения НК | Технологическая карта ультразвукового контроля № XXX | Лист 1 Листов 2 | ||||||||
1 Объект контроля | ||||||||||
1.1 Контролируемое оборудование | ||||||||||
1.2 Организация-изготовитель | ||||||||||
1.3 Тип сварного соединения | ||||||||||
1.4 Обозначение | ||||||||||
1.5 Способ сварки | ||||||||||
1.6 Основной металл | ||||||||||
1.7 Сварочные материалы | ||||||||||
1.8 Контроль (стадия) | ||||||||||
2 Документация по контролю | ||||||||||
2.1 Методическая | 2.2 Нормативная | |||||||||
3 Требования к объему контроля и оценке качества | ||||||||||
3.1 Категория сварного соединения | 3.2 Степень контроледоступности | |||||||||
3.3 Объем контроля | ||||||||||
4 Тип и размеры объекта контроля | ||||||||||
4.1 Тип объекта контроля | ||||||||||
4.2 Размеры, мм | ||||||||||
5 Требования к поверхности объекта контроля | ||||||||||
6 Условия проведения контроля | ||||||||||
Место проведения работ: Температура окружающего воздуха и контролируемой поверхности: Допустимое время контроля: | ||||||||||
7 Средства контроля | ||||||||||
7.1 Дефектоскоп | ||||||||||
7.2 Ультразвуковой преобразователь (ПЭП), тип | 7.3 Номинальная частота, МГц | 7.4 Угол ввода, град | 7.5 Стрела наклонного ПЭП, мм | 7.6 Размер и форма пьезоэлемента ПЭП, мм | ||||||
7.7 Калибровочные образцы (меры) | ||||||||||
7.8 Настроечные образцы (НО) |
7.7 Калибровочные образцы (меры)
7.8 Настроечные образцы (НО)
Карту разработал: | Карту проверил: | Согласовано: |
Должность ____________________/Ф.И.О. (подпись, дата) | Должность ______________________/Ф.И.О. (подпись, дата) | |
Удостоверение | Удостоверение |
Рисунок Г.1, лист 1 — Рекомендуемая форма ТКК
Наименование организации | |||||||||||
Наименование подразделения НК | Технологическая карта ультразвукового контроля № XXX | Лист 2 Листов 2 | |||||||||
8 Параметры контроля | |||||||||||
8.1 Направление | 8.2 Тип | 8.3 Зона | 8.4 Способ настройки чувствительности: | ||||||||
прозвучивания | ПЭП | контроля по глубине, мм | Браковочная, Sep, мм2 | Фиксации, Эк, мм2 | Поисковая, Sn, мм2 | ||||||
8.5 Схема прозвучивания | |||||||||||
8.5.1 Сканирование | |||||||||||
8.5.2 Шаг сканирования | | 8.5.3 Скорость сканирования | | ||||||||||
8.6 Параметры несплошностей, подлежащие определению | |||||||||||
9 Оценка качества | |||||||||||
9.1 Качество сварного соединения считается удовлетворительным, если: | |||||||||||
- характеристики требованиям: | и количество | несплошностей, оцениваемые по ____ | _________ удовлетворяют | ||||||||
Номинальная толщина сваренных деталей, мм | Эквивалентная площадь одиночных несплошностей, мм2 | Допускаемое число фиксируемых одиночных несплошностей на любые 100 мм протяженности сварного соединения | |||||||||
Минимально фиксируемая | Максимально допускаемая | ||||||||||
Карту разработал: | Карту проверил: | Согласовано: |
______________________/Ф.И.О. (подпись, дата) | _______________________/Ф.И.О. (подпись, дата) |
Рисунок Г.1, лист 2
Приложение Д (обязательное)
Ультразвуковой контроль по схеме «тандем»
Д.1 Схема «тандем» применяется для УЗК стыковых СС с углом разделки кромки 10° и менее (щелевой, К-образной разделкой и др.) с толщиной свариваемых деталей 30 мм и более следующих типов конструкций:
- плоских конструкций;
- стыковых кольцевых СС цилиндрических конструкций с наружным диаметром более 800 мм;
- стыковых продольных СС цилиндрических конструкций с наружным диаметром не менее 4 м.
Схема «тандем» может быть применена также для УЗК угловых и тавровых СС при толщине привариваемой детали 30 мм и более при отсутствии доступа со стороны основной детали (при этом ПЭП устанавливают на поверхность привариваемой детали).
Д.2 УЗК по схеме «тандем» проводят для выявления вертикально ориентированных плоскостных несплошностей (типа трещин) и несплавлений по кромкам в СС. УЗК по схеме «тандем» проводят для выявления:
- продольных несплошностей (рисунок Д. 1а, проходы 1—4);
- поперечных несплошностей (рисунок Д.16, проходы 5—8). При этом усиление СС удалено, УЗК проводят по зачищенным поверхностям СС.
Д.З УЗК по схеме «тандем» рекомендуется проводить ПЭП с углами ввода от 45° до 50° на частоте от 1,8 до 2,5 МГц при раздельном режиме работы дефектоскопа. Один из ПЭП работает в режиме излучения, другой — в режиме приема.
Д.4 Размер ПЭ для ПЭП, работающего на частоте 2,5 МГц, равен диаметру 12 мм или 12x12 мм, а сумма значений т и п должна быть не более 20 мм (рисунок Д.2), где т, мм — расстояние от точки выхода излучающего ПЭП до передней грани принимающего ПЭП; л, мм — стрела принимающего ПЭП.
Размер ПЭ для ПЭП, работающего на частоте 1,8 МГц или 1,25 МГц, равен диаметру 18 мм или 18x18 мм, а сумма значений л? и л должна быть не более 30 мм (рисунок Д.2).
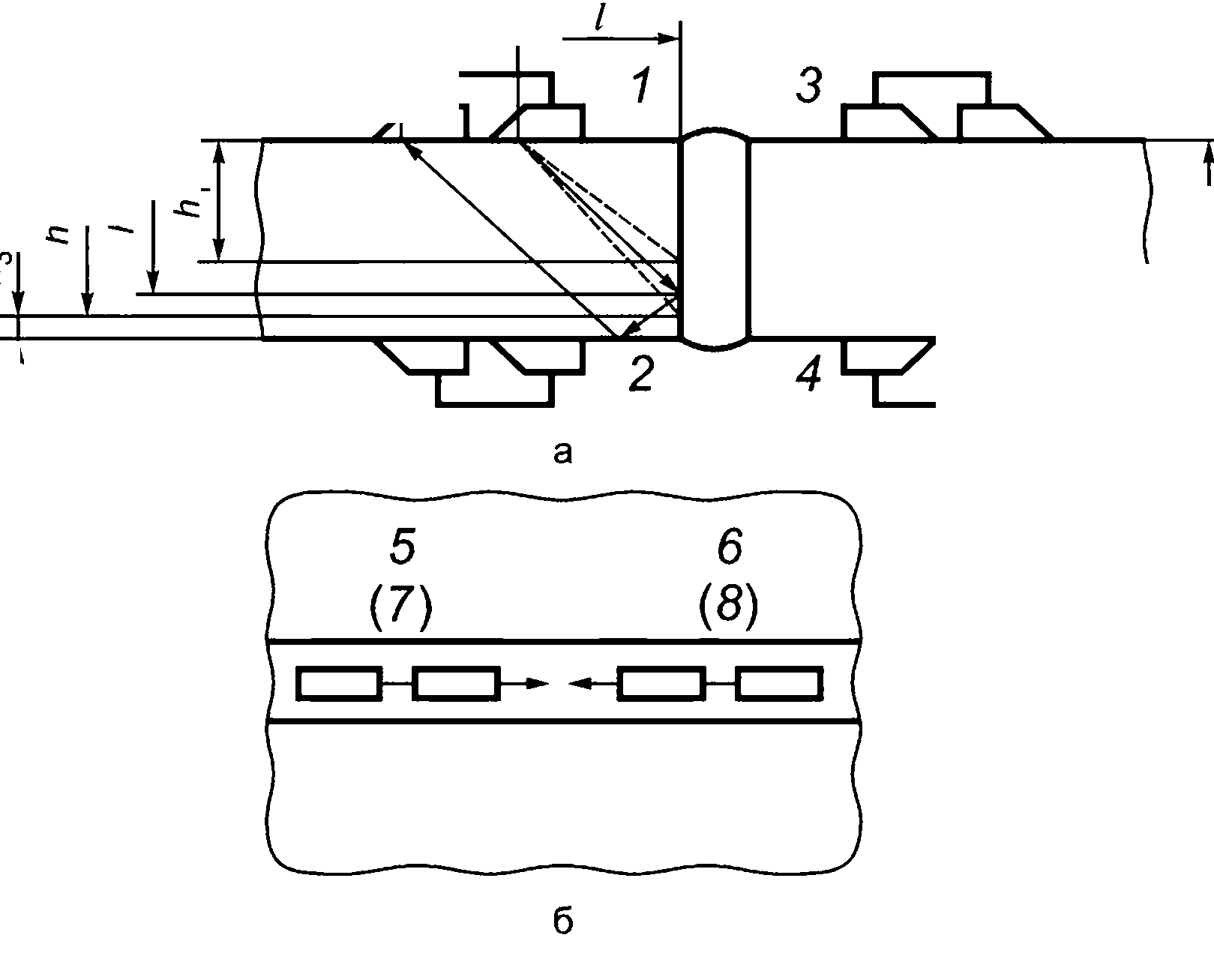
а — схема контроля при наличии усиления шва; б — схема контроля шва со снятым усилением Рисунок Д.1 — УЗК по схеме «тандем»

Рисунок Д.2 — Расположение ПЭП при прозвучивании изделия на наибольшей глубине
Д.5 При УЗК ПЭП должны быть жестко закреплены между собой с помощью специализированного устройства для обеспечения необходимого расстояния между ПЭП. Расстояние L между точками выхода ПЭП, а также расстояние /, на которое должна быть удалена точка выхода излучающего ПЭП (рисунок Д.1), определяют по таблице Д.1. По таблице Д.1 определяют также соответствующую каждой паре L и / глубину залегания точки пересечения акустических осей /?0 и точек пересечения боковых лучей с контролируемой поверхностью УЗ-пучка минус 4 дБ /?1 и /?2 (рисунок Д.1). При проведении УЗК каждым проходом должны выявляться несплошности, расположенные в областях глубин между /?1 и h2. Высота неконтролируемой области шва h3 (см. рисунок Д.1) также может быть определена по таблице Д.1.
Таблица Д.1 — Значения L, I, hQ, hv h2, h3
В миллиметрах
Номинальная толщина свариваемых деталей Н | Необходимые фокусировки | ин | 1/Н | h0IH | h^/H | h2/H | h2/H |
От 30 до 40 включ. | 1 | 1,20 | 0,60 | 0,5 | 0,4 | 0,6 | 0,2 |
2 | 0,70 | 0,85 | 0,7 | 0,6 | 0,8 | ||
Св. 40 до 120 включ. | 1 | 0,95 | 0,70 | 0,6 | 0,5 | 0,7 | 0,1 |
2 | 0,50 | 0,95 | 0,8 | 0,7 | 0,9 | ||
Св. 120 | 1 | 1,20 | 0,60 | 0,5 | 0,4 | 0,6 | — |
2 | 0,70 | 0,85 | 0,7 | 0,6 | 0,8 | ||
3 | 0,25 | 1,1 | 0,9 | 0,8 | 1,0 |
Д.6 Схемы прозвучивания показаны на рисунке Д.1. УЗК проводят только в том случае, если размеры СС позволяют реализовать значения Ln/, заданные таблицей Д.1. Прозвучивание с каждой стороны СС и по каждой схеме осуществляют всеми проходами, указанными в таблице Д.1 для данной толщины, характеризующимися значениями L и /.
Д.7 Настройка чувствительности в соответствии с 7.4.2.17 и приложением Н (Н.2.10).
Примечание — При использовании АРД-диаграмм при УЗК по схеме «тандем» учет затухания УЗ не требуется.
Д.8 Ширина подготовленной под УЗК зоны с каждой стороны шва должна быть в соответствии с 6.8.8. Подготовка поверхности в соответствии с 6.8.9.
Д.9 Сканирование и поиск несплошностей
Д.9.1 При проведении УЗК по схемам прозвучивания (рисунок Д.1а) ПЭП следует перемещать вдоль шва на расстоянии от контролируемой плоскости до точки выхода переднего ПЭП, равном I. При этом необходимо осуществлять поперечно-продольное перемещение ПЭП на расстояние от 5 до 10 мм в обе стороны от положения, характеризуемого значением /, и развороты ПЭП на угол от 10° до 15° в обе стороны от перпендикуляра к контролируемой плоскости.
Д.9.2 При схеме прозвучивания, показанной на рисунке Д.16, прозвучивание осуществляется путем перемещения ПЭП поперек СС с шагом не более 6 мм с одновременным разворотом на угол от 10° до 15° в обе стороны от продольной оси шва.
Д.10 Эхо-сигналы от несплошностей возникают на экране дефектоскопа на том же месте развертки, что и при оценке амплитуды опорного сигнала.
Глубина залегания несплошностей не определяется. В заключении по результатам УЗК указывается диапазон глубин, в котором расположена несплошность.
При схеме прозвучивания, показанной на рисунке Д.16, местоположение несплошности вдоль шва определяется исходя из значения /.
Эквивалентная площадь несплошности определяется по АРД-диаграммам по схеме «тандем» в зависимости от значения амплитуд полученных сигналов (опорного и эхо-сигнала) и их разности.
Приложение Е (обязательное)
Методика ультразвукового контроля подповерхностной части сварных соединений головными волнами
Е.1 Настоящая методика регламентирует порядок проведения УЗК СС деталей толщиной 30 мм и более с целью обнаружения несплошностей в подповерхностных слоях соединения от 0 до 15 мм включительно. Основные положения методики могут быть использованы при УЗК металла наплавленной поверхности на кромках и боковых участков металла наплавленной поверхности.
Е.2 УЗК проводят головными УЗ-волнами ПГВ в конструктивном отношении: «тандем» или «дуэт» [соответственно ПГЦ-91 или ПГЦ-70 (ИЦ-70)]. Допускается применение других ПЭП, реализующих способ проведения УЗК головными волнами и удовлетворяющих требованиям настоящего стандарта.
Е.З Способ УЗК головными волнами представлен на рисунке Е.1. Излучатель 1 ПЭП с углом призмы, равным первому критическому углу, возбуждает в СС продольно-поверхностную (головную) волну 2, которая распространяется в металле СС и при наличии несплошности 3 отражается от него и идет в обратном направлении — волна 4. Волна 4, распространяясь вдоль поверхности СС, образует в граничной среде так называемую боковую волну, которую и регистрирует приемник 5.
Рисунок Е.1 — Способ УЗК головными волнами
Е.4 УЗК проводят дефектоскопом с подключением ПГВ по раздельной схеме.
Е.5 Настройку диапазона развертки дефектоскопа производят по отражению головных волн от вертикальной грани прямого двугранного угла, образованного торцом и контактной поверхностью ОК или НО.
Е.6 НО изготавливают из металла, идентичного металлу свариваемых деталей в СС. Качество поверхности образца должно соответствовать поверхности СС в зоне контроля (в месте контакта ПГВ), но не должно быть более Ra 6,3 мкм. Размеры НО приведены на рисунке Е.2.
Е.7 Настройку диапазона развертки осуществляют в следующей последовательности:
- устанавливают ПГВ на НО таким образом, чтобы передняя грань ПЭП совпадала с плоскостью торца образца. Поднимают чувствительность дефектоскопа до появления на экране эхо-сигнала, соответствующего отражению от торца НО. При этом отраженный сигнал должен пальпироваться пальцем, смоченным контактной средой со стороны торца на глубине от 5 до 10 мм включительно;
- совмещают передний фронт строб-импульса с передним фронтом эхо-сигнала (рисунок Е.З);
- отодвигают ПГВ на расстояние, равное ширине шва и околошовной зоны, наблюдая за эхо-сигналом. Совмещают задний фронт строб-импульса с задним фронтом эхо-сигнала от торца (рисунок Е.З). Эхо-сигнал в процессе перемещения ПГВ следует постоянно пальпировать;
- устанавливают длительность строб-импульса такой, чтобы его задний фронт отстоял от 30 % до 60 % длины развертки от ее начала.
1 — зондирующий импульс; 2 — зона контроля (строб-импульс); 3 — импульсы, отраженные от плоскодонного отражателя в НО;
4 — уровень чувствительности УЗК
Рисунок Е.З — Схема настройки чувствительности и диапазона развертки
Е.8 Настройку чувствительности производят по эхо-сигналу от отражателя с плоским дном в НО согласно рисунку Е.2.
Е.9 Настройку чувствительности производят посредством установки:
- ПГВ на НО, получают эхо-сигнал от плоскодонного отражателя. Перемещают ПГВ и устанавливают эхо-сигнал от плоскодонного отражателя в конце строб-импульса;
- высоты эхо-сигнала, равной 50 % экрана — браковочный уровень;
- поискового уровня путем добавления чувствительности на 6 дБ.
Примечание — Если при одинаковой чувствительности на экране дефектоскопа наблюдаются вершины эхо-сигналов от плоскодонного отражателя в начале и конце строб-импульса, рекомендуется, перемещая ПЭП к отражателю, фиксировать изменение высоты эхо-сигнала на экране дефектоскопа по всей длине строб-импульса и огибающую линию (рисунок Е.З) на экране дефектоскопа.
Е.10 УЗК выполняют путем последовательного перемещения ПЭП по поверхности свариваемых деталей (или по наплавленной поверхности) по всей протяженности соединения с обеих сторон от шва.
При сканировании ПЭП перемещают параллельно к оси шва с одновременным возвратно-поступательным перемещением перпендикулярно оси. Величина продольного (вдоль шва) шага сканирования не должна превышать 8 мм. Величина поперечного шага сканирования — от 15 до 30 мм включительно (рисунок Е.4). При удален-
X + (15...30 мм)
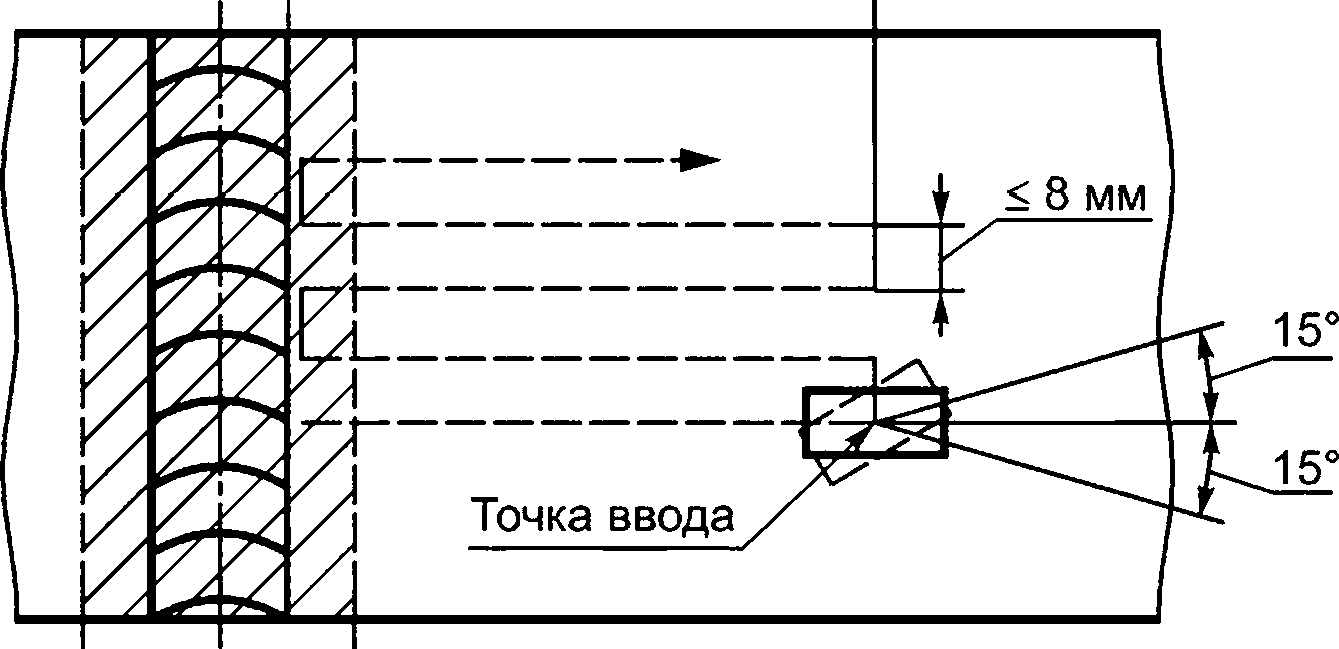
Зона контроля
X — околошовная зона;
продольный шаг сканирования — не более 8 мм; поперечный шаг сканирования — 15—30 мм
Рисунок Е.4 — Схема сканирования ПГВ при наличии усиления СС
ном усилении сканирование осуществляют по всей ширине СС, включая околошовную зону. При наличии усиления сканирование осуществляют непосредственно от границы сварного шва. В процессе перемещения ПЭП производят его повороты относительно собственной оси на 15° (за исключением ПЭП, у которых контур рабочей поверхности соответствует радиусу кривизны поверхности ОК в зоне контроля).
Е.11 В процессе УЗК необходимо обеспечивать постоянный акустический контакт ПЭП с поверхностью металла в зоне контроля.
Рекомендуется для наблюдения за акустическим контактом ПЭП следить за импульсом, расположенным между зондирующим импульсом и строб-импульсом. Этот импульс наблюдается при повышении чувствительности дефектоскопа в режиме поиска и соответствует обратной продольно-поверхностной волне, распространяющейся от излучателя к приемнику через СС.
Е.12 Признаком наличия несплошности является эхо-сигнал в пределах строб-импульса.
Е.13 Оценку несплошностей производят следующим образом:
- при обнаружении несплошности регуляторами чувствительности устанавливают высоту эхо-сигнала, равную 50 % экрана, и фиксируют ее местоположение на экране дефектоскопа;
- перемещают ПЭП по НО и, не изменяя положения регуляторов чувствительности, устанавливают эхо-сигнал от плоскодонного отражателя в зону развертки, где располагался сигнал от несплошности;
- сравнивают (визуально, с учетом показаний дефектоскопа) его амплитуду с амплитудой эхо-сигнала от несплошности;
- несплошность считают недопустимой (дефектом), если амплитуда эхо-сигнала от нее превышает амплитуду эхо-сигнала от плоскодонного отражателя в НО.
Приложение Ж (обязательное)
Методика ультразвукового контроля стыковых продольных сварных соединений цилиндрических конструкций
Ж.1 Настоящее приложение определяет особенности методики УЗК стыковых продольных СС цилиндрических конструкций.
Ж.2 Предварительный выбор ПЭП проводят согласно таблице 1 по фактической толщине Н цилиндрической конструкции.
Ж.З Для обеспечения УЗК стыковых продольных СС цилиндрических конструкций используют эквивалентную толщину с наружной поверхности Нэ н п, и с внутренней поверхности Нэ в п, мм, которую рассчитывают по формулам
^э.н.п = cos а • RH п • cos а - JrI п - п • (sin а)2
(Ж.1)
(Ж.2)
где а — угол ввода, град;
/?н п — РаДиУс наружной поверхности, мм;
RB п — радиус внутренней поверхности, мм;
I / 9 9 / \2 I
/-L и п = cos a- JRun - Rr п - sina - Rr п cos а . O.D.II у П.11 О. I I \ / D.ll I
Эквивалентная толщина плоского СС для ОК цилиндрической формы представлена на рисунке Ж.1.
Выбирают ПЭП по таблице 1, исходя из значений Нэ н п и Нэ в п-
Ж.4 В зависимости от отношения H/RM п и H/RB п по таблице Ж.1 устанавливают для каждого из выбранных ПЭП, к какой области (А, Б или В) значений отношения Н/R при УЗК с наружной и (или) внутренней стороны ОК принадлежат СС.
Проверку корректности выбранного угла ввода допускается проводить расчетно-графическим способом. Для увеличения степени контроледоступности изменяют значение угла ввода выбранного ПЭП на такое, при котором будет обеспечена максимально возможная контроледоступность СС. При этом отклонение уточненного угла ввода от угла, приведенного в таблице Ж.1, не должно превышать 3°.
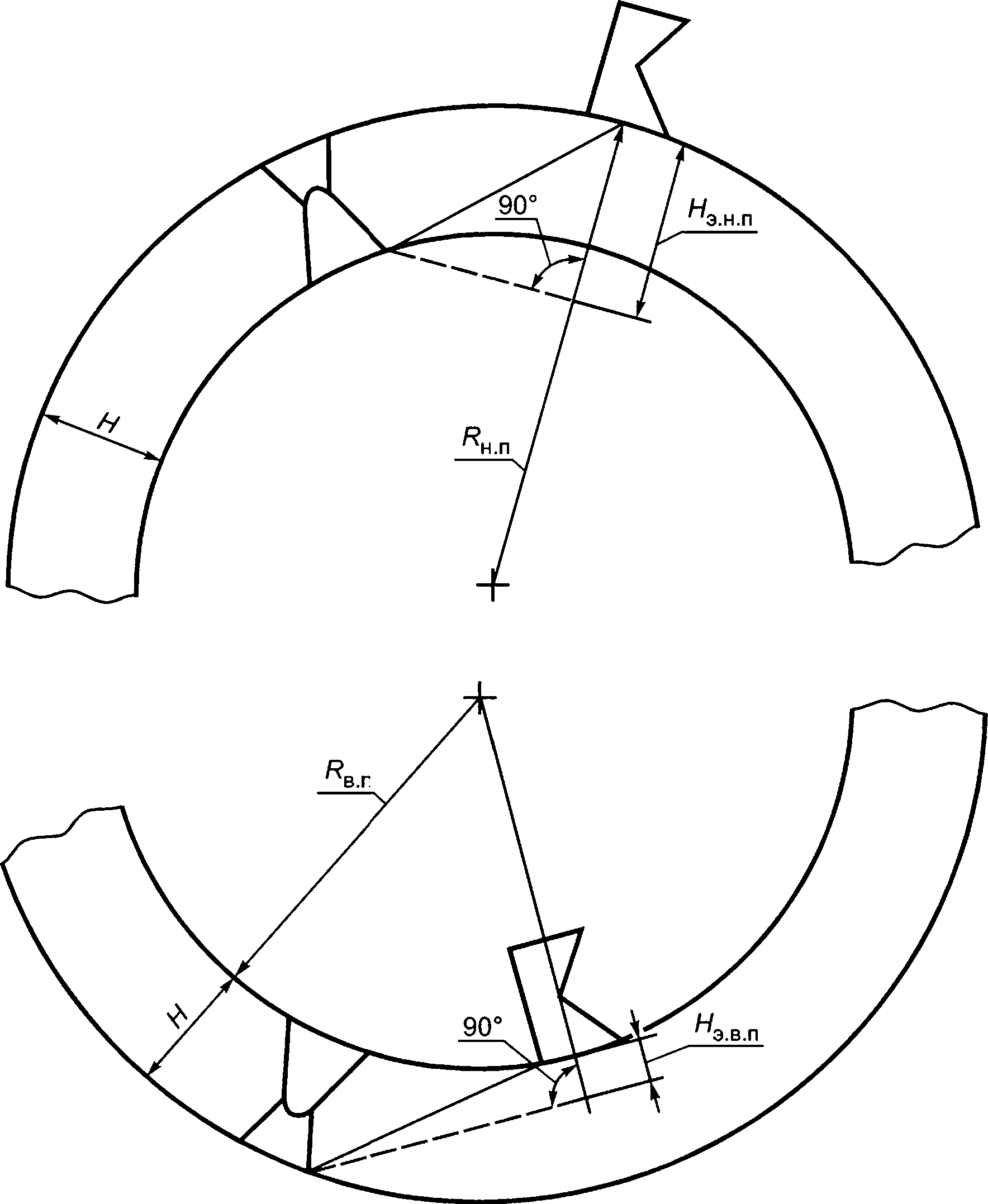
Рисунок Ж.1 — Эквивалентная толщина Нэнпи Нэвп плоского СС ОК цилиндрической формы
Таблица Ж.1 — Области значений H/R
Угол ввода УЗ, град | Область значений HIR | ||
А | Б | В | |
"/*н.п | "/*н.п | ^н.п | |
40 | Св. 0 до 0.188 включ. Св. 0 до 0,526 включ. | Св. 0.188 до 0,375 включ. Св. 0,526 до 1 включ. | Св. 0,375 |
45 | Св.О до 0,140 включ. Св. 0 до 0,322 включ. | Св. 0,140 до 0,293 включ. Св. 0,322 до 1 включ. | Св. 0,293 |
50 | Св. 0 до 0,104 включ. Св. 0 до 0,208 включ. | Св. 0,104 до 0,234 включ. Св. 0,208 до 1 включ. | Св. 0,234 |
60 | Св. 0 до 0,052 включ. Св. 0 до 0,089 включ. | Св. 0,052 до 0,134 включ. Св. 0,089 до 1 включ. | Св. 0,134 |
Окончание таблицы Ж. 1
Угол ввода УЗ, град | Область значений H/R | ||
А | Б | В | |
"/*н.п H/RB.n | "/*н.п Н//?вп | "/*н.п | |
65 | Св. 0 до 0,035 включ. Св. 0 до 0,057 включ. | Св. 0,036 до 0,094 включ. Св. 0,057 до 1 включ. | Св. 0,094 |
68 | Св. 0 до 0,026 включ. Св. 0 до 0,042 включ. | Св. 0,026 до 0,073 включ. Св. 0,042 до 1 включ. | Св. 0,073 |
70 | Св. 0 до 0,021 включ. Св. 0 до 0,034 включ. | Св. 0,021 до 0,060 включ. Св. 0,034 до 1 включ. | Св. 0,060 |
72 | Св. 0 до 0,017 включ. Св. 0 до 0,027 включ. | Св. 0,017 до 0,049 включ. Св. 0,027 до 1 включ. | Св. 0,049 |
Примечание — Н — номинальная толщина свариваемых деталей, мм; /?нп — радиус наружной поверхности, мм; RB п — радиус внутренней поверхности, мм.
Ж.5 Если отношение HIR находится в области А, то УЗК СС осуществляют аналогично УЗК плоских конструкций в соответствии с настоящим стандартом.
Ж.6 Если отношение Н/R находится в области Б, то возможность проведения УЗК всего сечения шва (при наличии усиления) и зоны перемещения ПЭП устанавливают расчетно-графическим способом.
Ж.7 При проведении УЗК с наружной стороны выбранным ПЭП чувствительность устанавливают, исходя из требований федеральных норм и правил в области использования атомной энергии, документов по стандартизации, КД, ТД, устанавливающих требования к оценке соответствия металла СС и наплавленных поверхностей, и эквивалентной толщины СС Нэнп (Ж.1). При этом:
- если Нэ н п СС входит в тот же диапазон толщин, что и истинная толщина Н, то УЗК следует проводить с чувствительностью, предусмотренной для толщины Н;
- если Нэ н п попадает в следующий диапазон толщин, то УЗК следует проводить с чувствительностью, предусмотренной для этого диапазона толщин, что должно быть отмечено в ТКК и результатах УЗК.
Ж.8 При проведении УЗК с внутренней стороны выбранным ПЭП чувствительность определяют исходя из истинной толщины соединений Н, но настраивают ее для глубины, соответствующей эквивалентной толщине свариваемых деталей Нэ в п.
Ж.9 Если отношение HIR находится в области В, то при определении контроледоступности следует учесть, что УЗК всего сечения шва с наружной стороны невозможен (степень контроледоступности не выше ЗС). В этом случае УЗК всего сечения шва может быть обеспечен при отсутствии усиления шва и его прозвучивания с наружной и внутренней сторон СС, что должно быть проверено расчетно-графическим способом. Если УЗК возможен, то при выборе его параметров следует учесть требованиями Ж.7.
Ж.10 Для определения координат несплошностей в сечении шва глубиномер дефектоскопа следует настраивать в расстояниях по лучу.
Ж.11 УЗК на отсутствие поперечных несплошностей проводят в соответствии с требованиями 6.2.1.6.
Ж. 12 При выполнении УЗК СС цилиндрических конструкций допускается использовать опору или проточку (сопряжение поверхностей) (рисунки Ж.2, Ж.З).
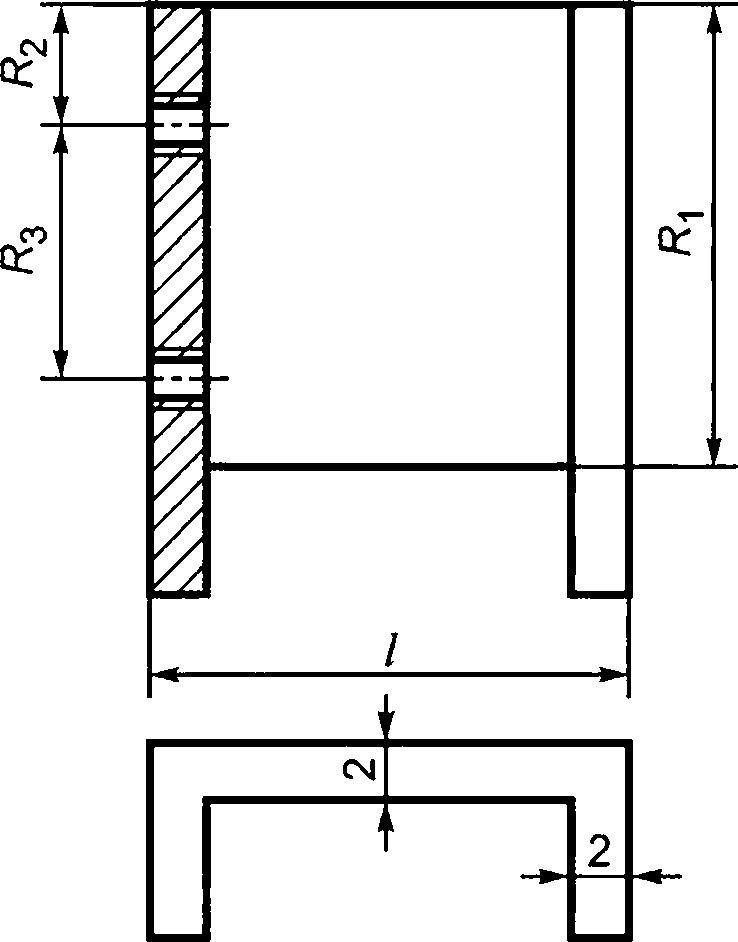
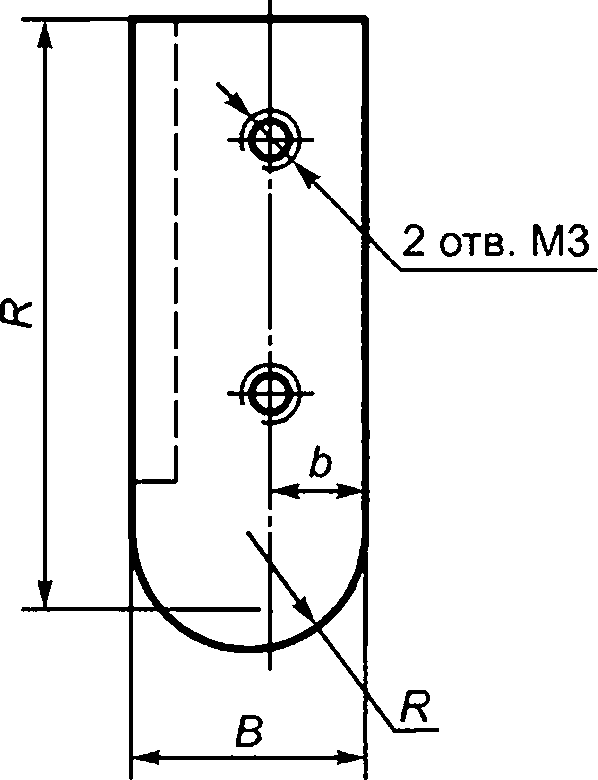
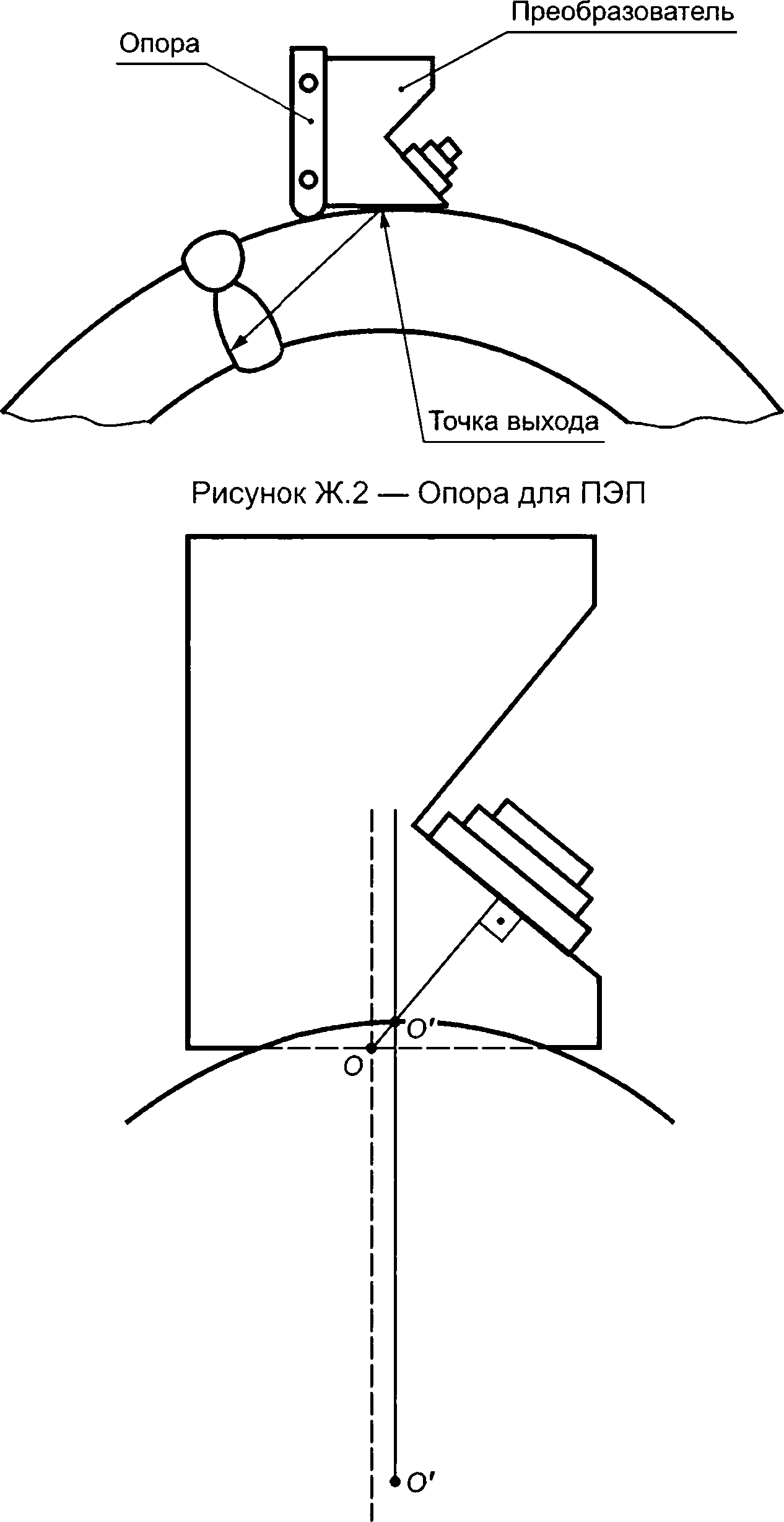
О и О' — точки выхода луча ПЭП с плоской контактной (до проточки) и обработанной поверхностями
Рисунок Ж.З — Схема проточки (сопряжения) контактной поверхности ПЭП
Приложение И (обязательное)
Методика ультразвукового контроля методом «корневой тандем» сварных соединений биметаллических сосудов и трубопроводов
И.1 Общие положения
И.1.1 Настоящая методика распространяется на УЗК СС биметаллических сосудов и трубопроводов, с толщиной свариваемых деталей от 36 до 100 мм включительно, имеющих антикоррозионную наплавленную поверхность.
Методика предназначена для обнаружения вертикально-ориентированных трещин (в том числе усталостных, возникающих в процессе эксплуатации) под наплавленной антикоррозионной поверхностью на СС (рисунок И.1).
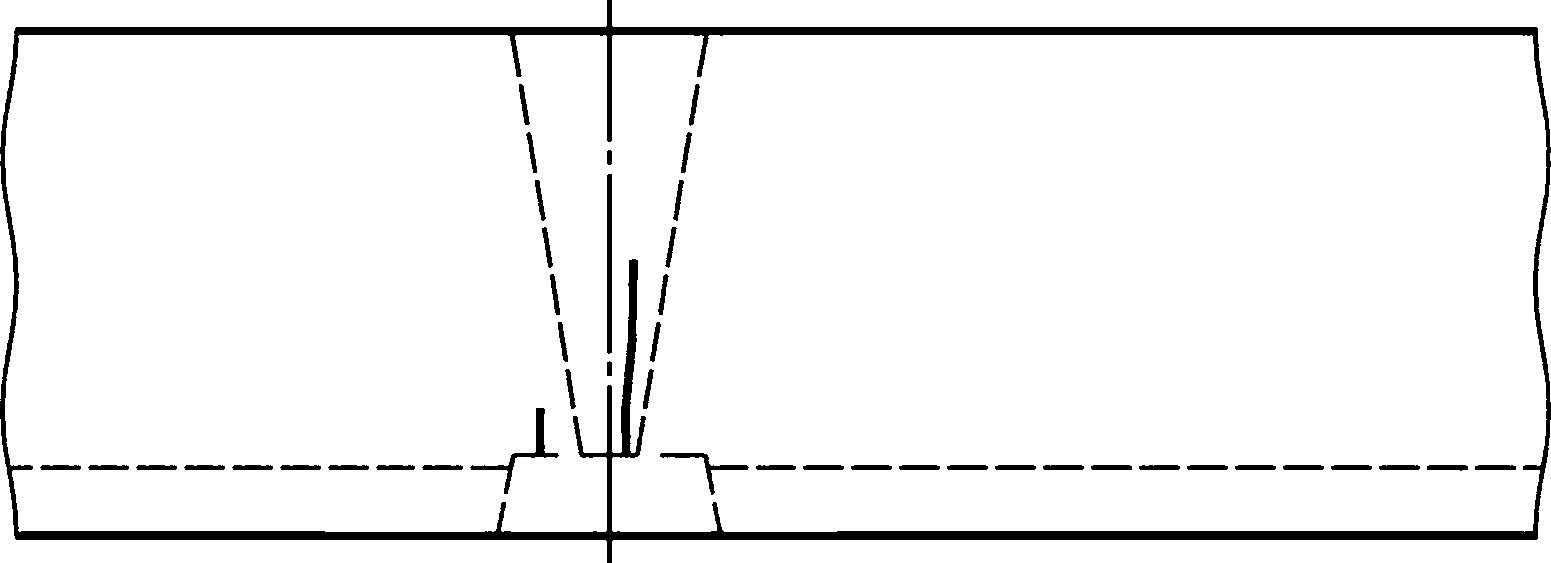
Рисунок И.1 —Трещины под наплавленной поверхностью из сталей аустенитного класса на СС
Настоящая методика основана на использовании метода «корневой тандем», который позволяет обнаруживать вертикальные трещины при сканировании ПЭП по наружной поверхности трубопровода (рисунок И.2).
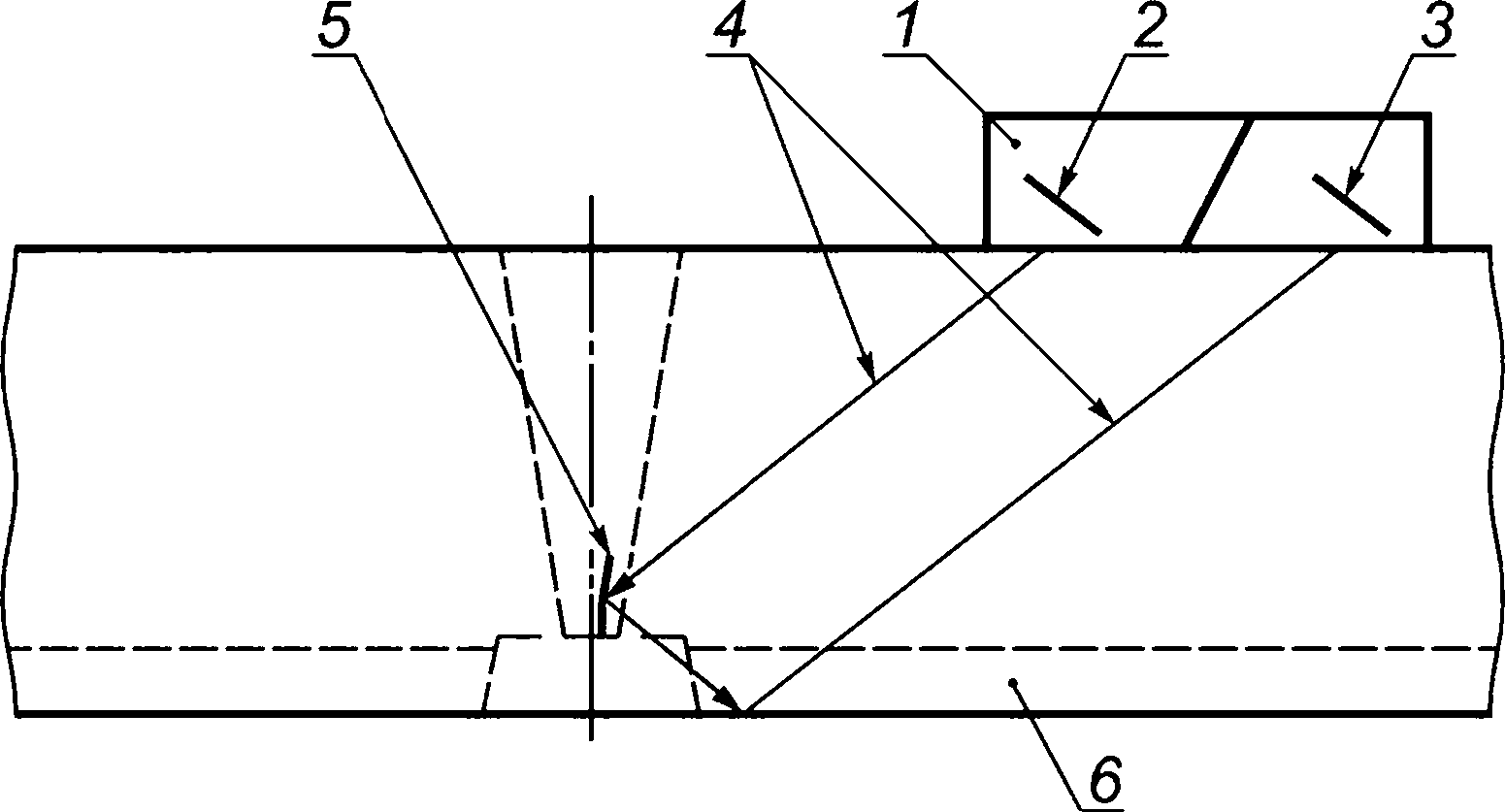
1 — ПЭП; 2,3—излучающий и приемный ПЭ; 4 — направление хода УЗ-колебаний; 5—трещина под наплавленной поверхностью;
6 — антикоррозионная поверхность
Рисунок И.2 — Способ УЗК методом «корневой тандем»
Настоящая методика УЗК осуществляется при ручном сканировании ПЭП контактным методом и может быть использована при автоматизированном УЗК.
И.2 Метод УЗК «корневой тандем»
И.2.1 Метод основан на использовании специализированных наклонных PC ПЭП «корневой тандем».
И.2.2 УЗ-волны распространяются в ОК, как показано на рисунке И.2. Конструкция специализированного ПЭП позволяет минимизировать мертвую зону УЗК методом «корневой тандем» и обеспечивает обнаружение вертикальных трещин высотой 3 мм и более. С помощью данной методики возможно обнаружение вертикальных трещин в зоне сплавления и над наплавленной поверхностью на расстоянии от 0 до 20 мм включительно от зоны сплавления.
И.З Средства УЗК и образцы
И.3.1 При проведении УЗК применяют переносные УЗ-дефектоскопы, позволяющие работать по раздельной схеме, и специализированные наклонные PC ПЭП «корневой тандем» (например, типа ПЦ-45-1,2 КТ). Угол ввода УЗ поперечных волн — 45°, частота УЗ — 1,2 МГц.
И.3.2 Для настройки параметров УЗК используют НО (рисунок И.З). Ширина образца — 30 мм (минимальная), длина образца — 140 мм (минимальная).
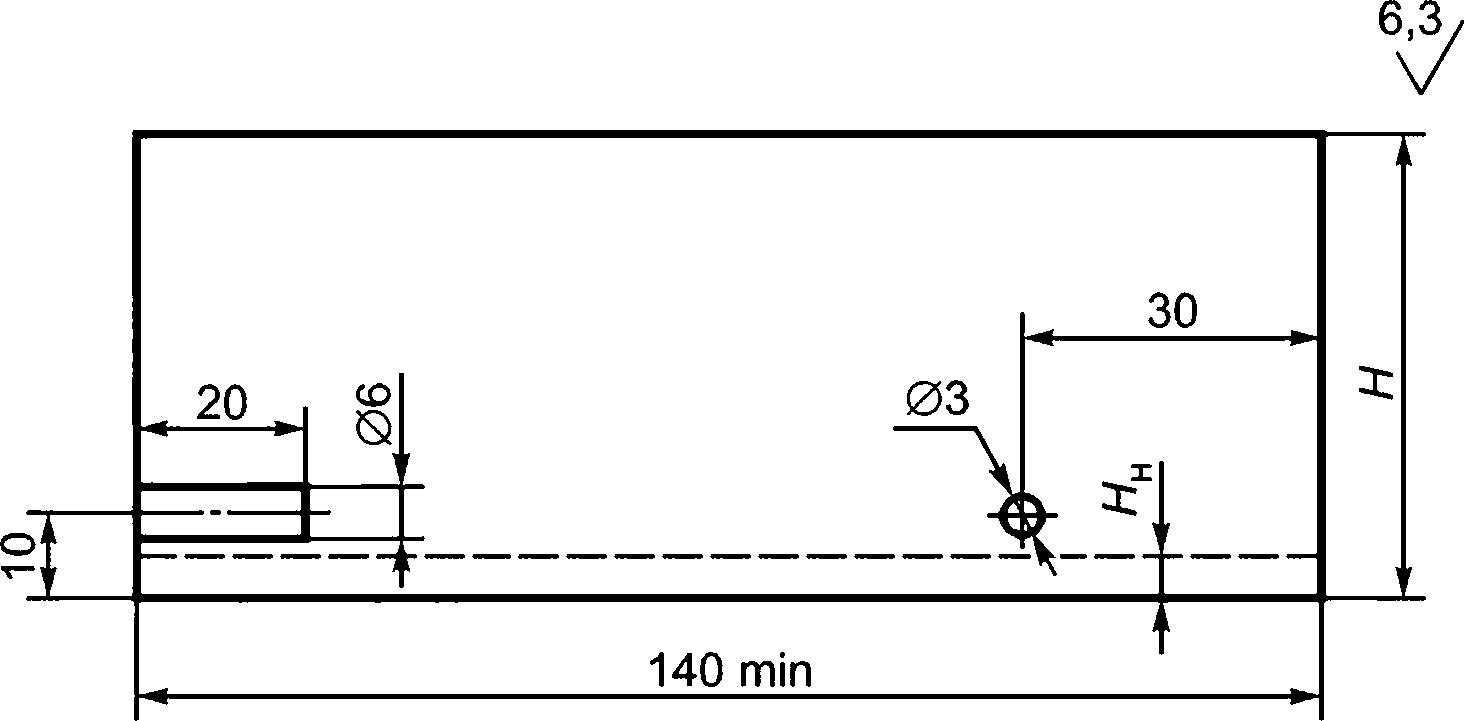
Н— номинальная толщина ОК; /7Н — номинальная толщина антикоррозионной поверхности Рисунок И.З — НО для настройки параметров УЗК
И.3.3 НО должен быть идентичен ОК по материалам, типоразмерам, методу изготовления и виду механической деформации. Допускается изготовление НО из участка ОК.
И.3.4 Контактная поверхность НО должна иметь шероховатость не более Ra 6,3 мкм.
И.3.5 Отражатель диаметром 6 мм должен иметь плоское дно. Клеймо с числовым значением диаметра располагают в непосредственной близости от отражателя. Отражатель диаметром 3 мм (цилиндрический) имитирует шлаковое включение в зоне сплавления восстановленной наплавленной поверхности на СС, служит для получения эхо-сигнала от несплошности (рисунок И.4) и правильной интерпретации сигналов от трещин и объемных включений.
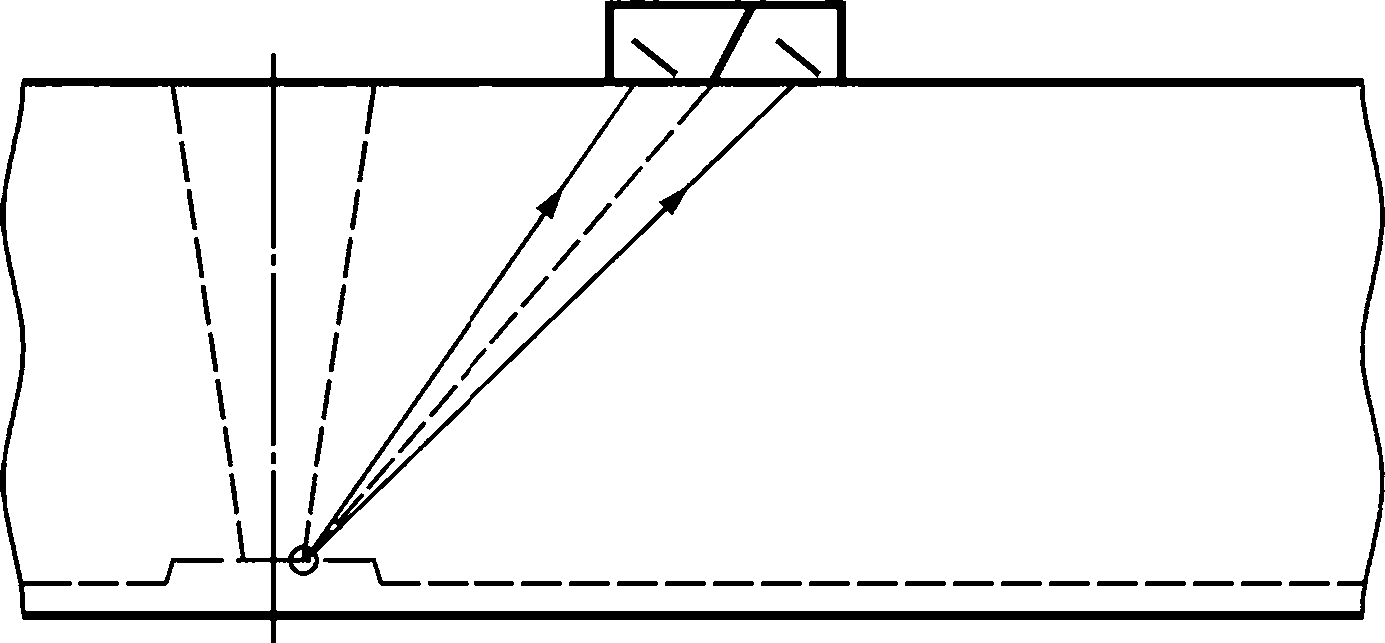
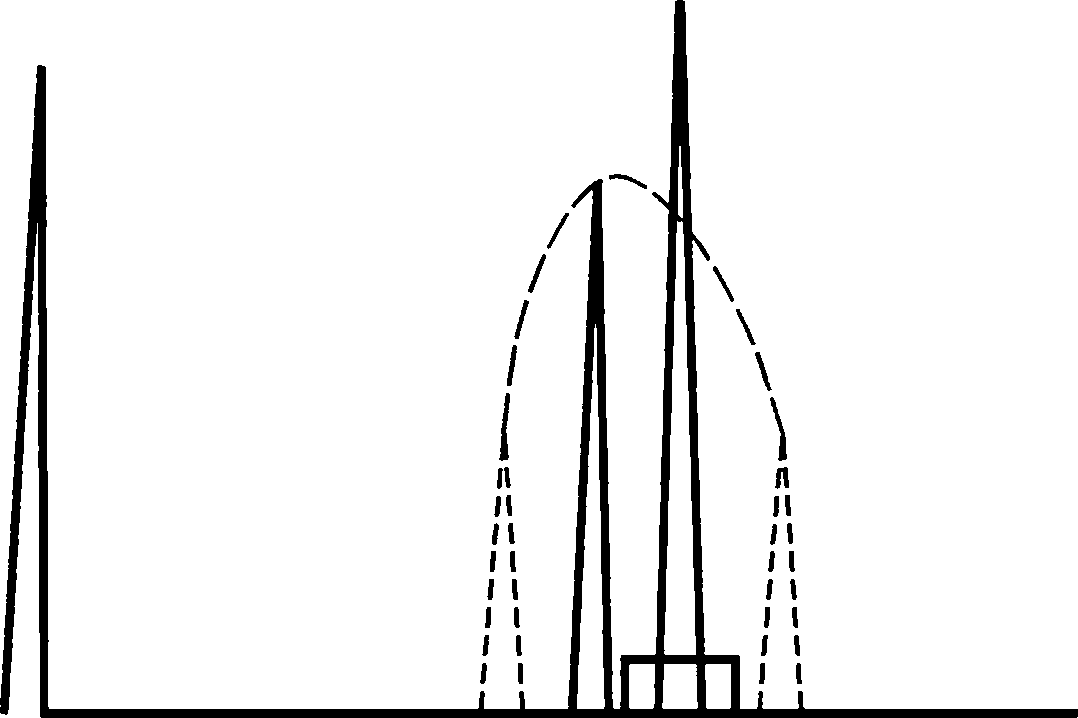
Рисунок И.4 — Схема обнаружения и интерпретации объемных несплошностей под наплавленной поверхностью
И.4 Общие положения по ультразвуковому контролю
И.4.1 Подключение ПЭП к дефектоскопу
И.4.1.1 Включают дефектоскоп для работы в раздельном режиме. Кабели ПЭП подключают к выходу генератора дефектоскопа и ко входу усилителя в соответствии с инструкцией по применению дефектоскопа.
И.4.1.2 При наличии в дефектоскопе переключателя диапазона частот УЗ устанавливают его в положение, соответствующее необходимой частоте или ближайший диапазон к данному значению.
И.4.1.3 Включают полное усиление дефектоскопа и рассматривают картину на экране дефектоскопа. При исправно работающей системе «ПЭП — кабель — дефектоскоп» после зондирующего импульса должен наблюдаться импульс, соответствующий прохождению УЗ от излучающего ПЭ к приемнику через щель под акустическим экраном ПЭП.
И.4.1.4 Этот импульс изменяет свою амплитуду при прощупывании пальцем участка под экраном.
И.4.2 Настройка развертки дефектоскопа
И.4.2.1 Настройку диапазона развертки проводят по отражению поперечной волны от прямого двугранного угла НО, т. е. по донному сигналу (рисунок И.5).
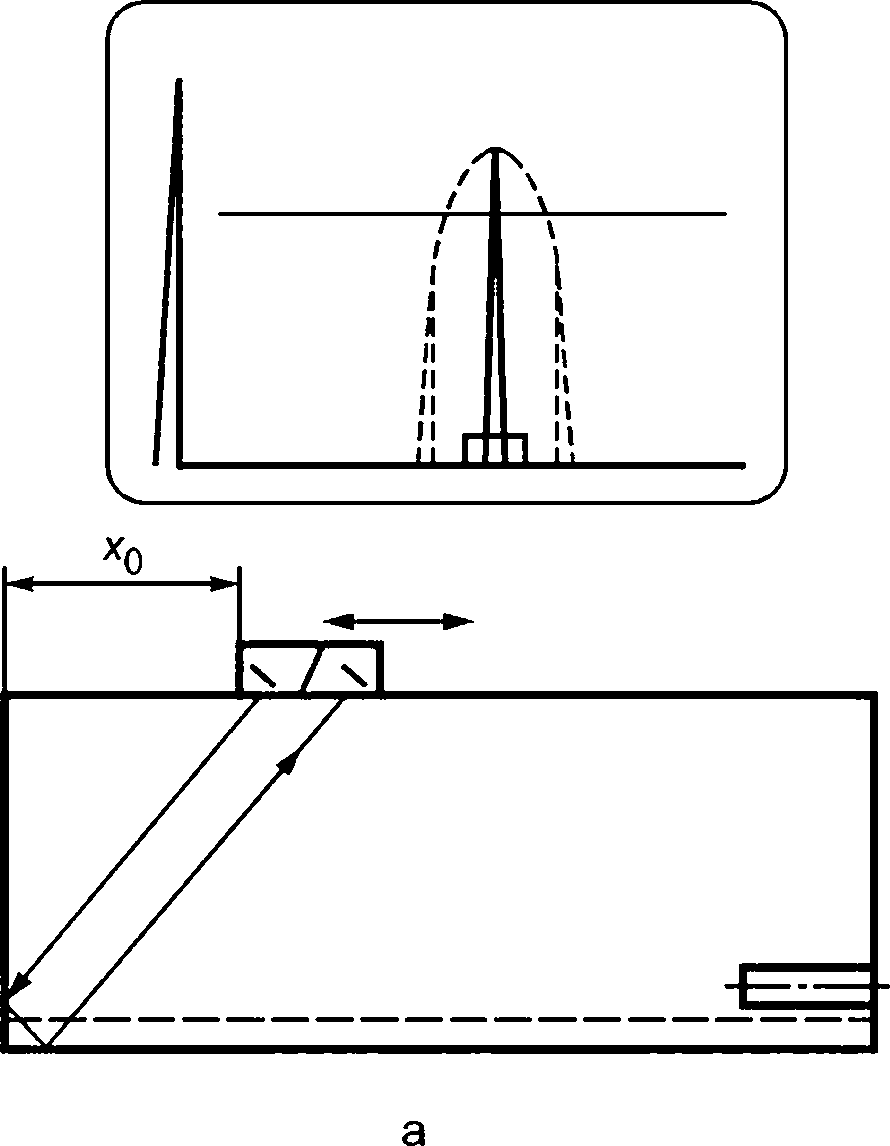
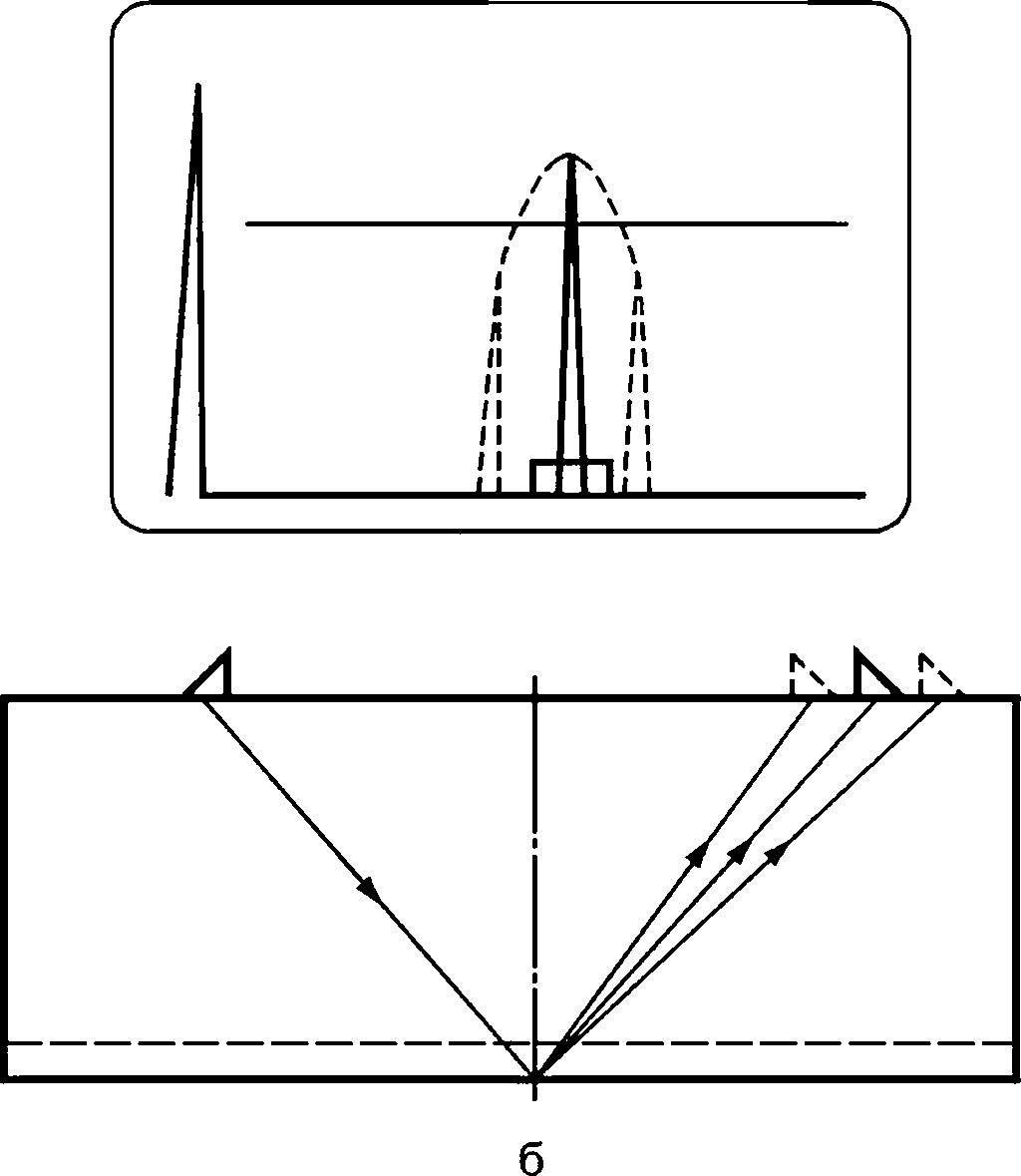
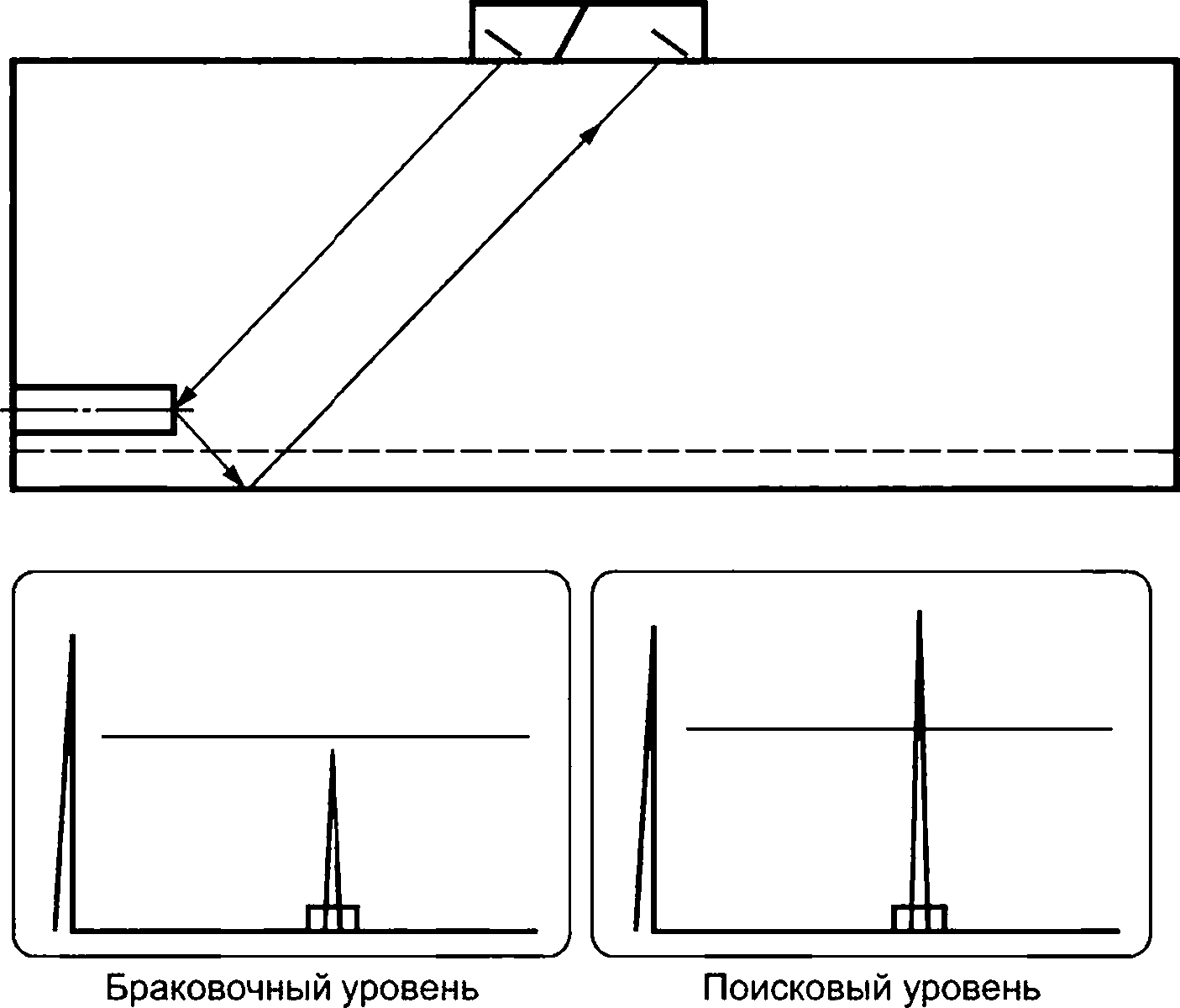
а — настройка развертки; б — проверка и корректировка диапазона развертки; в — настройка чувствительности Рисунок И.5 — Схемы настройки дефектоскопа
И.4.2.2 Устанавливают ПЭП перпендикулярно к грани образца и путем сканирования (ближе и дальше от грани) находят максимум донного сигнала (рисунок И.5а). Следует прощупать донный сигнал на торцевой поверхности в зоне сплавления образца и убедиться в его идентичности по экрану дефектоскопа. Амплитуда сигнала при прикосновении пальца к образцу уменьшается.
И.4.2.3 Необходимо переместить, регулируя диапазон развертки дефектоскопа, импульс донного сигнала «корневой тандем» на середину горизонтальной развертки, оставив положение зондирующего в крайнем левом положении развертки.
И.4.2.4 Определяют величину расстояния х0 (см. рисунок И.5а).
И.4.2.5 Устанавливают длину строб-импульса в соответствии с величиной контролируемой зоны и перемещают его на середину развертки. Импульс «корневой тандем» должен располагаться в середине строб-импульса.
И.4.2.6 Правильность расположения импульса «корневой тандем» может быть проверена на поверхности в зоне контроля или рядом с ней с помощью ПС ПЭП по положению донных импульсов или при включении двух ПЭП «корневой тандем» ПЦ-45-1,2 КТ навстречу друг другу по зеркально-теневой схеме (рисунок И.56).
И.4.3 Настройка чувствительности
И.4.3.1 Настройку чувствительности проводят по амплитуде эхо-сигнала от плоского дна отражателя в НО (см. рисунок И.З).
И.4.3.2 При настройке чувствительности устанавливают следующие уровни:
- браковочный уровень, при котором проводят оценку допустимости обнаруженной несплошности по амплитуде сигнала. Браковочный уровень чувствительности равен максимальной амплитуде сигнала «тандем» (корневой) от плоского дна отражателя в НО;
- поисковый уровень, при котором проводят поиск несплошностей. Поисковый уровень чувствительности на 6 дБ выше браковочного.
И.4.3.3 Настройку браковочного уровня чувствительности проводят следующим образом:
- устанавливают ПЭП на рабочей (контактной) поверхности НО перпендикулярно к оси отражателя и соосно с ним; сканированием ПЭП находят максимальное значение амплитуды импульса;
- устанавливают регулятором усиления высоту сигнала равной половине высоты экрана дефектоскопа — браковочный уровень чувствительности (рисунок И.5в).
И.4.3.4 Поисковый уровень чувствительности устанавливают добавлением 6 дБ к браковочному уровню (см. рисунок И.5в).
И.4.4 Сканирование
И.4.4.1 УЗК СС проводят с обеих сторон шва при сканировании ПЭП путем его перемещения по поверхности свариваемых деталей параллельно оси сварного шва с одновременным возвратно-поступательным перемещением перпендикулярно к его оси (рисунок И.6).
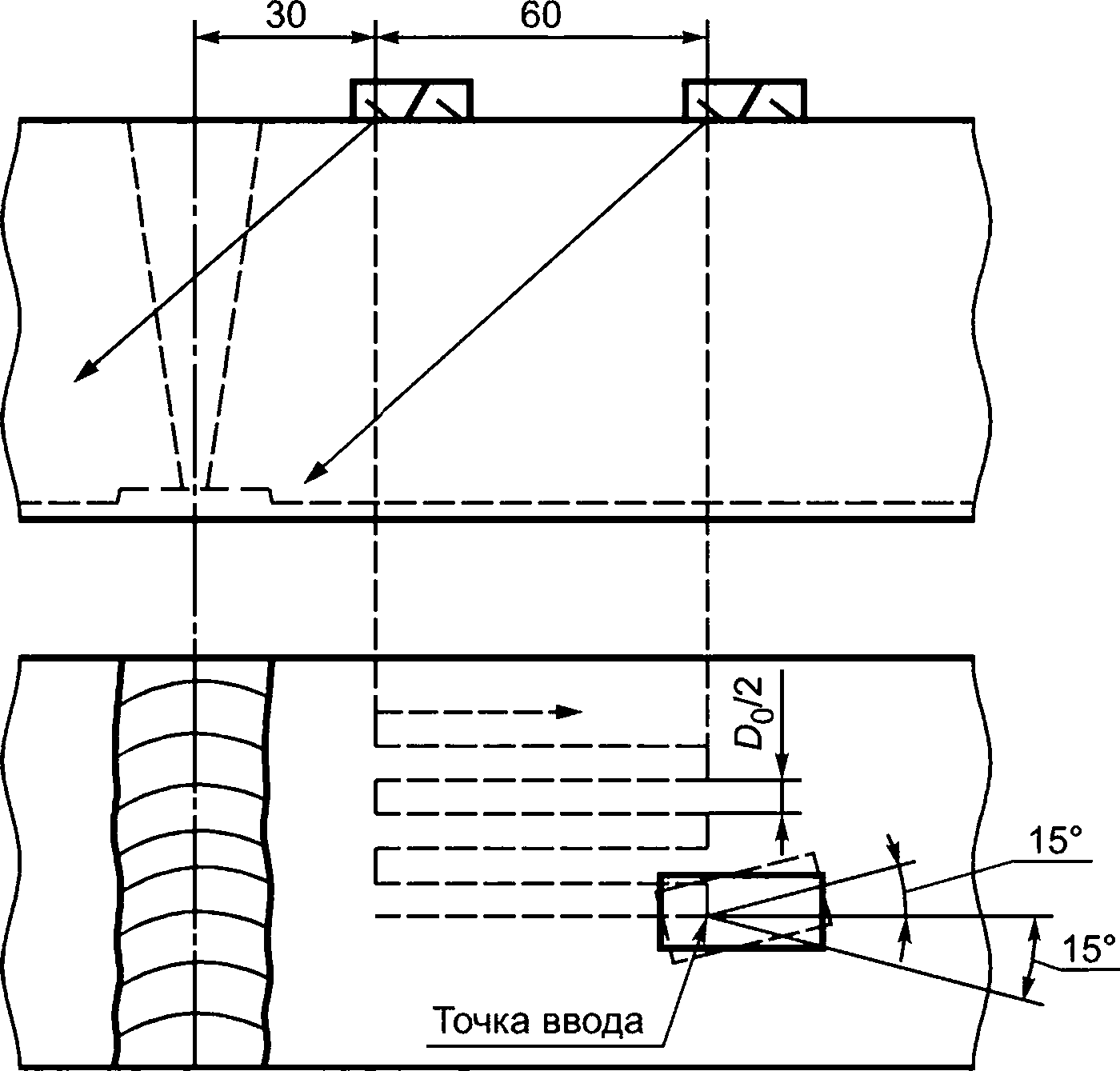
Рисунок И.6 — Схема сканирования
И.4.4.2 Размах и границы зоны сканирования должны обеспечить прозвучивание всей прикорневой и около-шовной зон СС в соответствии с требованиями КД, как показано на рисунке И.6.
И.4.4.3 В процессе сканирования необходимо обеспечивать постоянный акустический контакт ПЭП с поверхностью свариваемых деталей.
И.4.4.4 Скорость сканирования не должна превышать 150 мм/с, а шаг сканирования — 10 мм.
И.4.4.5 В процессе перемещения ПЭП проводят его повороты относительно собственной вертикальной оси в точке выхода от 0° до 15° (рисунок И.6).
И.4.5 Определение характеристик несплошностей
И.4.5.1 При обнаружении несплошностей с амплитудой сигнала, равной поисковому уровню или большей, определяют:
- координаты h, L;
- амплитуду сигнала (эквивалентную площадь);
- условную протяженность.
И .4.5.2 Координаты h и L определяют при появлении сигнала в рабочей зоне экрана дефектоскопа.
И .4.5.2.1 Глубину залегания отражателя h определяют по положению от него эхо-сигнала. Для получения эхо-сигнала необходимо отключить от дефектоскопа заднюю призму ПЭП и переключить дефектоскоп на работу в режим эхо-метода. Координату отражателя определяют по положению максимального эхо-сигнала от него, которое находят путем сканирования ПЭП по поверхности в зоне контроля.
И .4.5.2.2 Если эхо-сигнал не наблюдается, а такое возможно при обнаружении вертикальной трещины, то принимают глубину залегания отражателя равной (12 ± 3) мм от внутренней поверхности ОК, что соответствует глубине фокуса ПЭП.
И .4.5.2.3 Координату L определяют как место расположения несплошности вдоль продольной оси шва.
И .4.5.3 При определении координаты несплошности на поверхности относительно оси СС производят действия в следующей последовательности:
- фиксируют положение ПЭП в момент максимальной амплитуды сигнала;
- отмеряют расстояние, равное х0 (И.4.2.4), перед ПЭП — в конечной точке располагается зона несплошности с максимальной отражательной способностью;
- протравляют поверхность СС, устанавливают положение границ сплавления сварного шва и фиксируют относительное положение несплошности.
И.4.5.4 Амплитуду сигнала определяют в децибелах по отношению к амплитуде сигнала от плоскодонного отражателя диаметром 6 мм (браковочный уровень по И.4.3.2). Если амплитуда сигнала превосходит браковочный уровень на N дБ, то записывают Абр + N, если амплитуда сигнала менее браковочного уровня на М дБ, то записывают Абр — М.
И.4.6 Идентификация сигналов
И.4.6.1 Сигнал от вертикальной трещины в корне над наплавленной поверхностью на экране дефектоскопа располагается в строб-импульсе (рисунок И.5).
И.4.6.2 Возможно обнаружение объемных несплошностей (например, шлаковых включений, пор) в корне СС и под наплавленной поверхностью из сталей аустенитного класса на СС. Такие несплошности обнаруживаются как показано на рисунке И.4. Время распространения эхо-сигнала при этом менее, чем у сигнала по методу «корневой тандем», и он располагается левее строб-импульса. В некоторых случаях на экране вместе с эхо-сигналом наблюдается сигнал «корневой тандем» и его амплитуда может быть более эхо-сигнала.
И.4.7 Измерение условной протяженности
И.4.7.1 Условную протяженность измеряют как расстояние между точками, соответствующими крайним положениям ПЭП при перемещении его вдоль несплошности (рисунок И.7).
И.4.7.2 Крайними положениями ПЭП считают те, при которых амплитуда эхо-сигнала уменьшается до поискового уровня чувствительности.
И.4.7.3 Для облегчения обнаружения несплошностей допускается использовать систему АСД—дефектоскопа со звуковой и световой сигнализацией.
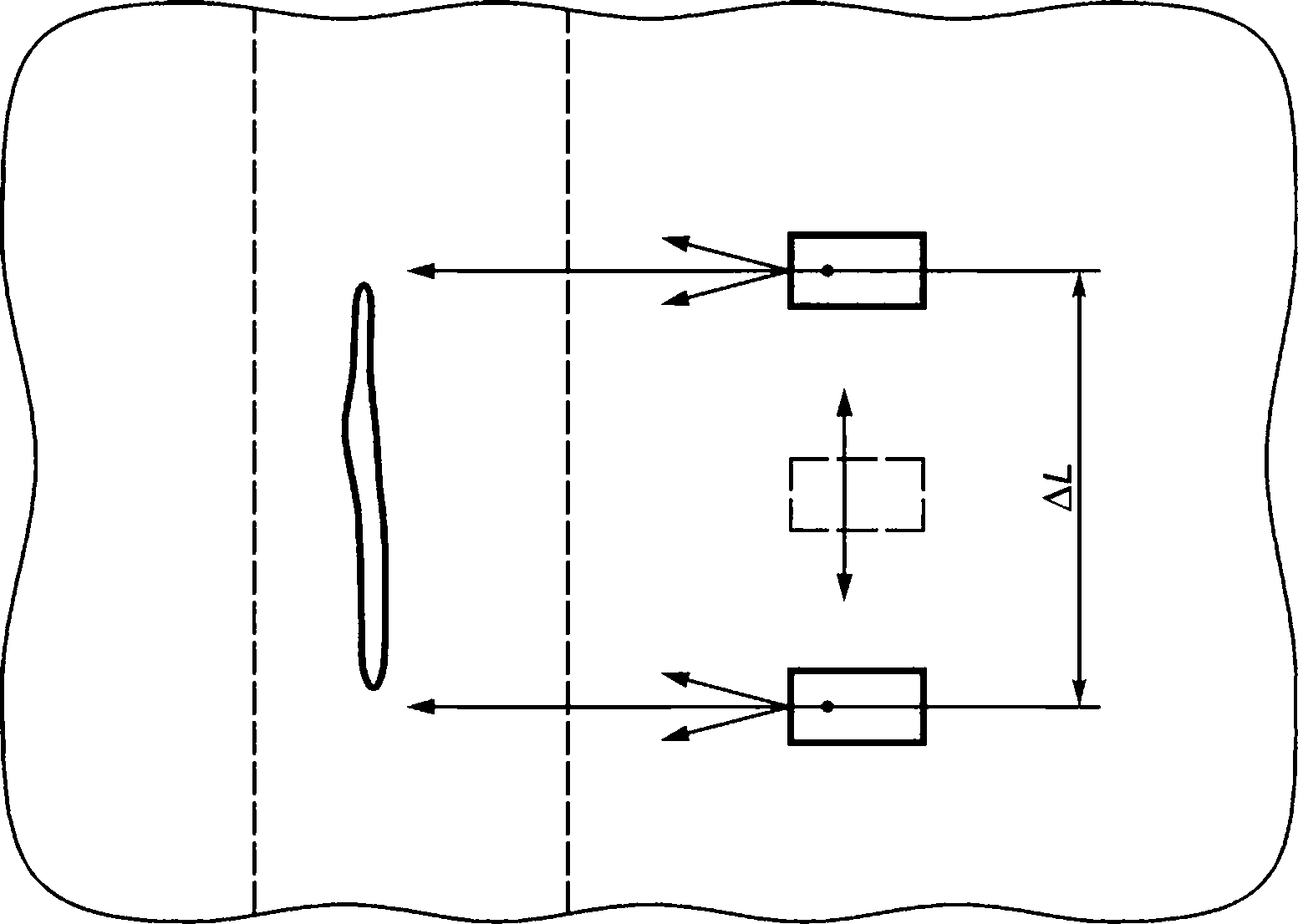
Поисковый
уровень
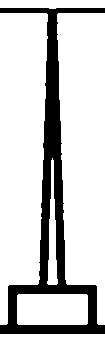
Рисунок И.7 — Схема определения крайних положений ПЭП с целью дальнейшего измерения условной протяженности несплошности
И.4.8 Оценка несплошностей
Оценку несплошностей, обнаруженных по схеме «корневой тандем», проводят следующим образом:
- несплошность, амплитуда сигнала от которой равна или превышает амплитуду сигнала от плоскодонного отражателя диаметром 6 мм в НО, является недопустимой (рисунок И.З);
- несплошность, амплитуда сигнала от которой равна или более поискового уровня, но менее браковочного уровня, и ее условная протяженность более условной протяженности плоскодонного отражателя диаметром 6 мм в НО, свидетельствует о наличии вертикальной несплошности (типа трещины);
- несплошность, обнаруженная по схеме «корневой тандем» с амплитудой ниже поискового уровня чувствительности на 6 дБ и менее, должна быть обследована дополнительно ПС и НП и оценена по совокупности полученных результатов УЗК.
Приложение К (справочное)
Реализуемая чувствительность
Реализуемая чувствительность S, мм2, при УЗК швов тавровых СС со стороны основной детали ПЭП с волновым размером К • а = (15 ± 1,5), где К— волновое число, а — радиус ПЭ, приведена на рисунке К.1.
При К ■ а # (15 ± 1,5) возможность УЗК следует определять экспериментально.
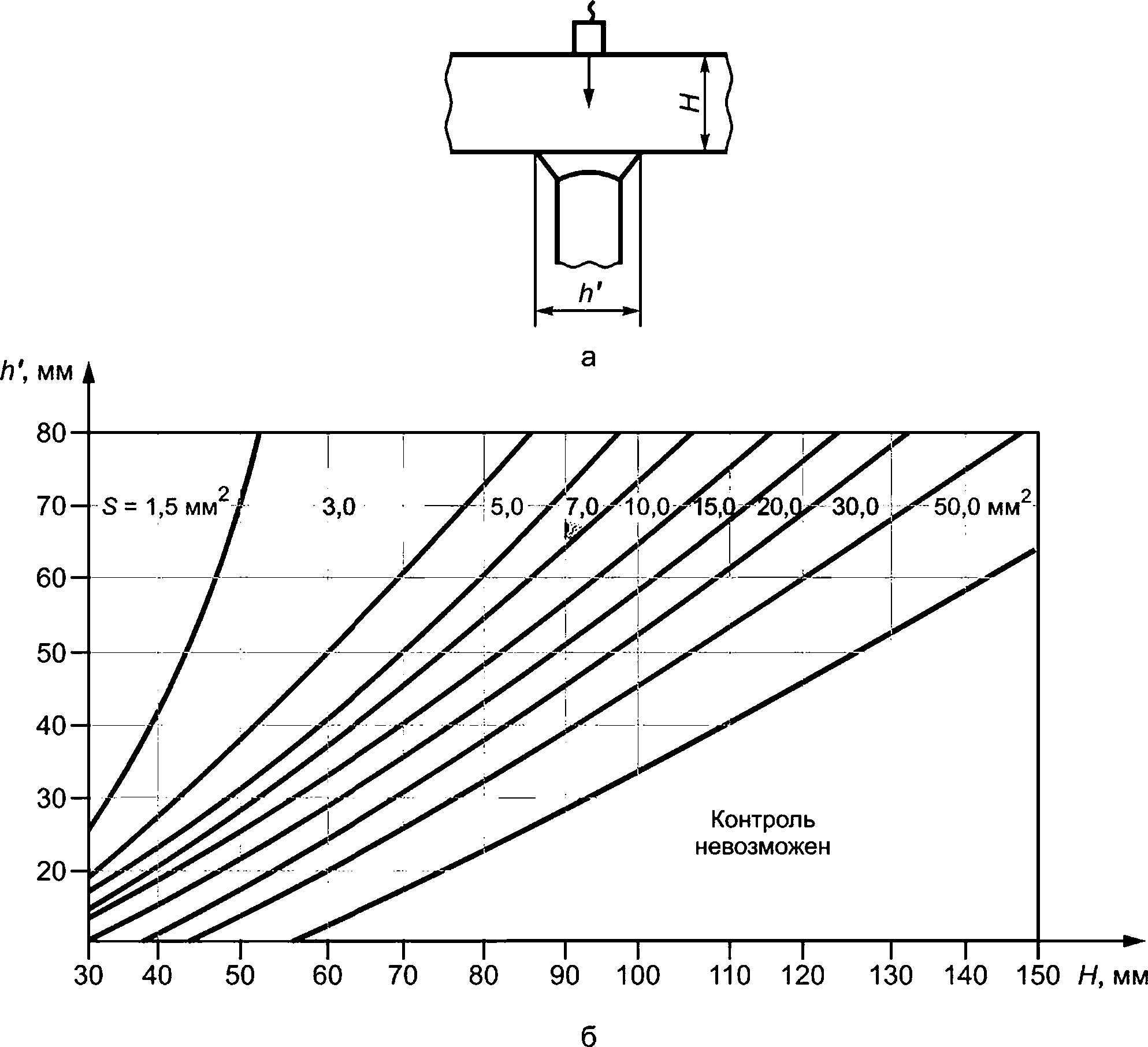
а — схема УЗК; б — график для расчета;
h' — толщина привариваемой детали; Н — толщина основной детали
Рисунок К.1 — Реализуемая чувствительность при УЗК тавровых СС со стороны основной детали
Приложение Л (обязательное)
Ультразвуковой контроль по схеме «стредл»
Л.1 УЗК по схеме «стредл» подвергаются стыковые СС плоских конструкций или кольцевые швы цилиндрических конструкций с наружным диаметром не менее 2000 мм с Х-образной разделкой свариваемых кромок с толщиной свариваемых деталей от 20 до 100 мм включительно. Схема контроля приведена на рисунке Л.1.
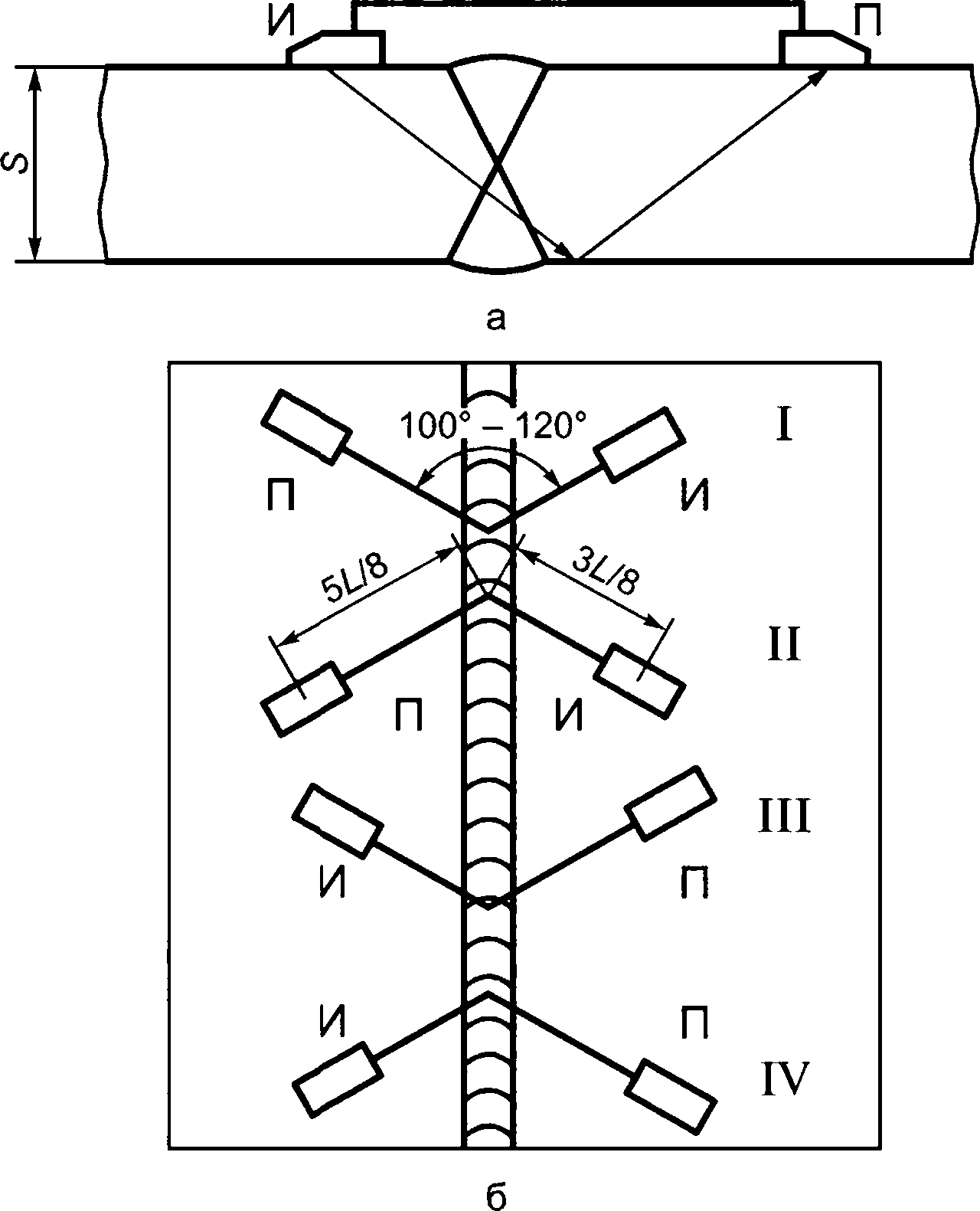
а — схема контроля (вид сбоку); И — излучающий ПЭП; П — ПЭП в режиме приема; б — схема контроля (вид сверху); I, II, III, IV — положения ПЭП при контроле по схеме «стредл»
Рисунок Л.1 — Схема контроля «стредл»
Л.2 УЗК по схеме «стредл» проводят с целью выявления плоскостных несплошностей, ориентированных перпендикулярно к поверхности СС и к продольной оси СС.
УЗК проводят при раздельном режиме работы дефектоскопа. Один из ПЭП (любой) работает в режиме излучения, другой — в режиме приема.
Л.З УЗК проводят на частоте 2,5 МГц с помощью НПЭП с углом ввода от 63° до 72° с размерами ПЭ диаметром 12 мм или 12x12 мм.
Л.4 При УЗК ПЭП жестко закрепляют между собой в требуемое положение с помощью специализированного устройства.
Л.5 Проверку возможности УЗК в зависимости от конструктивных размеров СС проводят с помощью графика, приведенного на рисунке Л.2.
Л.5.1 УЗК по схеме «стредл» возможен для СС, размеры которых попадают в область 1 (см. рисунок Л.2).
Л.5.2 УЗК по схеме «стредл» невозможен для СС, размеры которых попадают в область 3 (см. рисунок Л.2).
Л.5.3 Для СС, соответствующих области 2 (см. рисунок Л.2), необходима дополнительная проверка возможности проведения УЗК по схеме «стредл», которую следует проводить по Л.5.3.1—Л.5.3.3.
Примечание — Границу между двумя областями необходимо включать в область с меньшим порядковым номером.
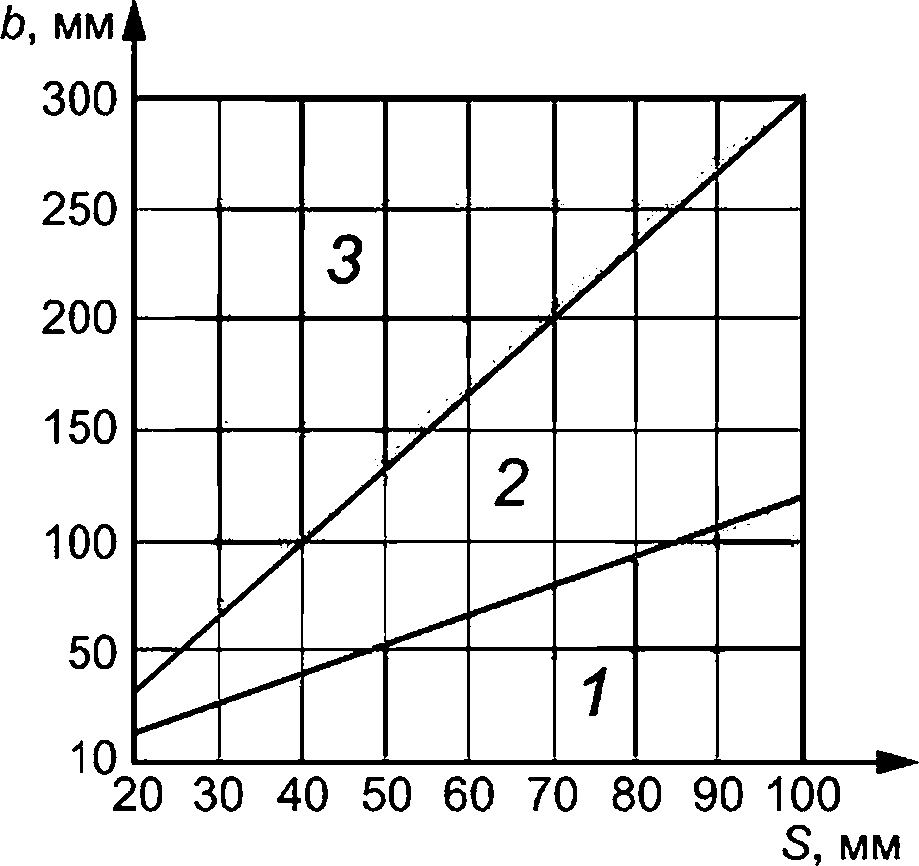
b — ширина усиления шва; S — толщина свариваемых деталей
Рисунок Л.2 — График определения возможности проведения УЗК в зависимости от конструктивных размеров СС
Л.5.3.1 По схеме, приведенной на рисунке Л.За, на поверхности металла вне зоны СС определяют максимум амплитуды опорного сигнала Аоп и соответствующее ему расстояние L между точками выхода ПЭП. Повторяют действия не менее пяти раз и вычисляют средние значения L и Аоп.
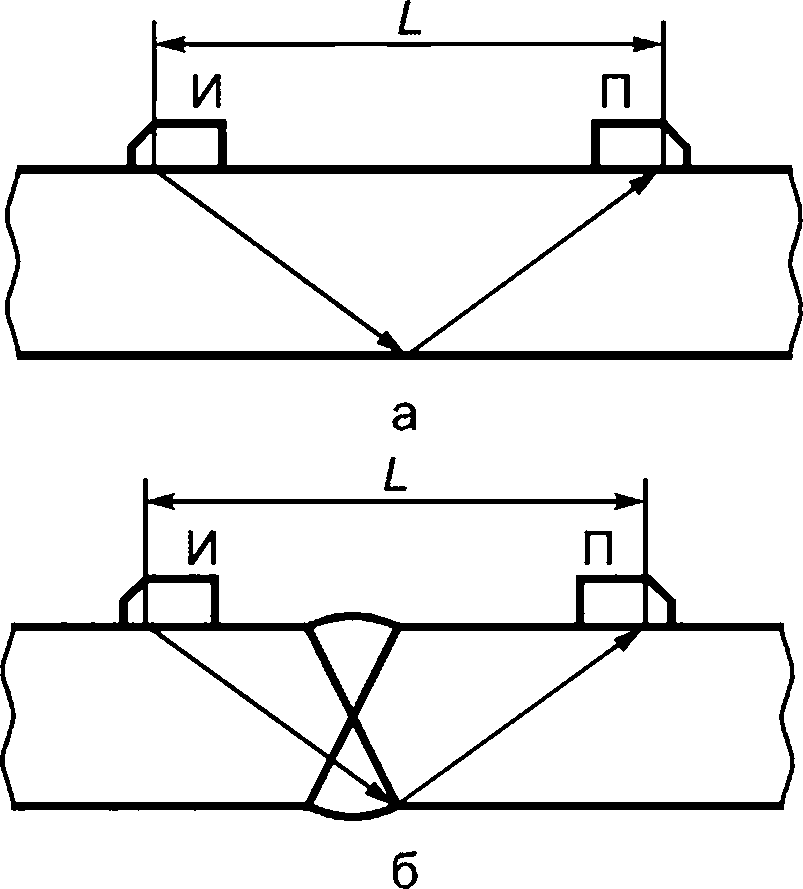
а — амплитуды отпорного сигнала Аоп и расстояния L между точками выхода ПЭП; б — амплитуды сигнала от поверхности усиления шва Авып
Л.З — Схемы оценки амплитуды
Л.5.3.2 Закрепляют ПЭП в устройстве таким образом, чтобы расстояние между их точками выхода было равно среднему значению L. Устанавливают ПЭП по обе стороны СС навстречу друг другу, как показано на рисунке Л.36, при произвольных расстояниях от точек выхода до СС. Определяют амплитуду эхо-сигнала от поверхности усиления шва Аусил Повторяют действия не менее чем в пяти точках шва и вычисляют среднее значение Аусил.
Л.5.3.3 УЗК СС данных типоразмеров возможен, если значения Аоп и Аусил отличаются друг от друга не более чем на 4 дБ.
Л.6 Чувствительность УЗК по схеме «стредл» может задаваться в значениях эквивалентной площади S3 или в значениях А = Аоп - Дд, где Ад — амплитуда эхо-сигнала от несплошности, Доп — амплитуда опорного сигнала по Л.5.3.1. Связь между значениями S3 и А показана на АРД-диаграммах (см. рисунки Л.4 и Л.5).
Форма задания и значение чувствительности определяются требованиями КД.
Примечание — При использовании АРД-диаграмм при УЗК по схеме «стредл» учет затухания УЗ не требуется.
Л.7 Перед началом контроля по схеме «стредл» необходимо выполнить действия по Л.7.1—Л.7.4.
Л.7.1 Выполняют оценку Аоп и L в соответствии с требованиями Л.5.3.1.
Л.7.2 На направляющих специализированного устройства закрепляют ПЭП таким образом, чтобы расстояние от оси шарнира устройства до точки выхода одного из ПЭП составляло 3/8/1, а от точки выхода другого ПЭП со-64
ставляло 5/8L (см. рисунок Л. 16). При таком закреплении точка пересечения акустических осей ПЭП расположена на глубине 0,75/т, а диапазон контролируемых глубин — от 0,5/т до h.
Л.7.3 Устанавливают угол между ПЭП равным от 100° до 120° и фиксируют его, закрепив шарнир на пересечении направляющих. При дальнейшей работе следует следить за тем, чтобы угол между направляющими оставался в указанных пределах.
Примечание — Особое внимание следует обращать на то, чтобы угол был не меньше 100°, так как в противном случае понизится чувствительность контроля.
Л.7.4 При настройке чувствительности следует повысить чувствительность дефектоскопа на необходимое значение △, дБ, по отношению к величине Доп. Поиск несплошностей производится на чувствительности на 6 дБ выше, чем заданная КД.
Пример — Толщина свариваемых деталей стыкового соединения составляет 48 мм. Заданная минимальная фиксируемая площадь несплошности S3 = 5 мм2. Используются ПЭП с частотой 2,5 МГц с углом ввода 70°. Среднее значение амплитуды опорного сигнала Аоп = 43 дБ. Необходимо настроить чувствительность поиска. Из АРД-диаграмм видно, что S3 = 5 мм2 соответствует значению Л = 25 дБ (см. рисунок Л.5, отрезки АВ и ВС). Показание аттенюатора дефектоскопа, соответствующее значению Ээ = 5 мм2, равно Аоп -Л- 43 -25 = 18 дБ. Для настройки поисковой чувствительности необходимо установить аттенюатор в положение 18-6 = 12 дБ.
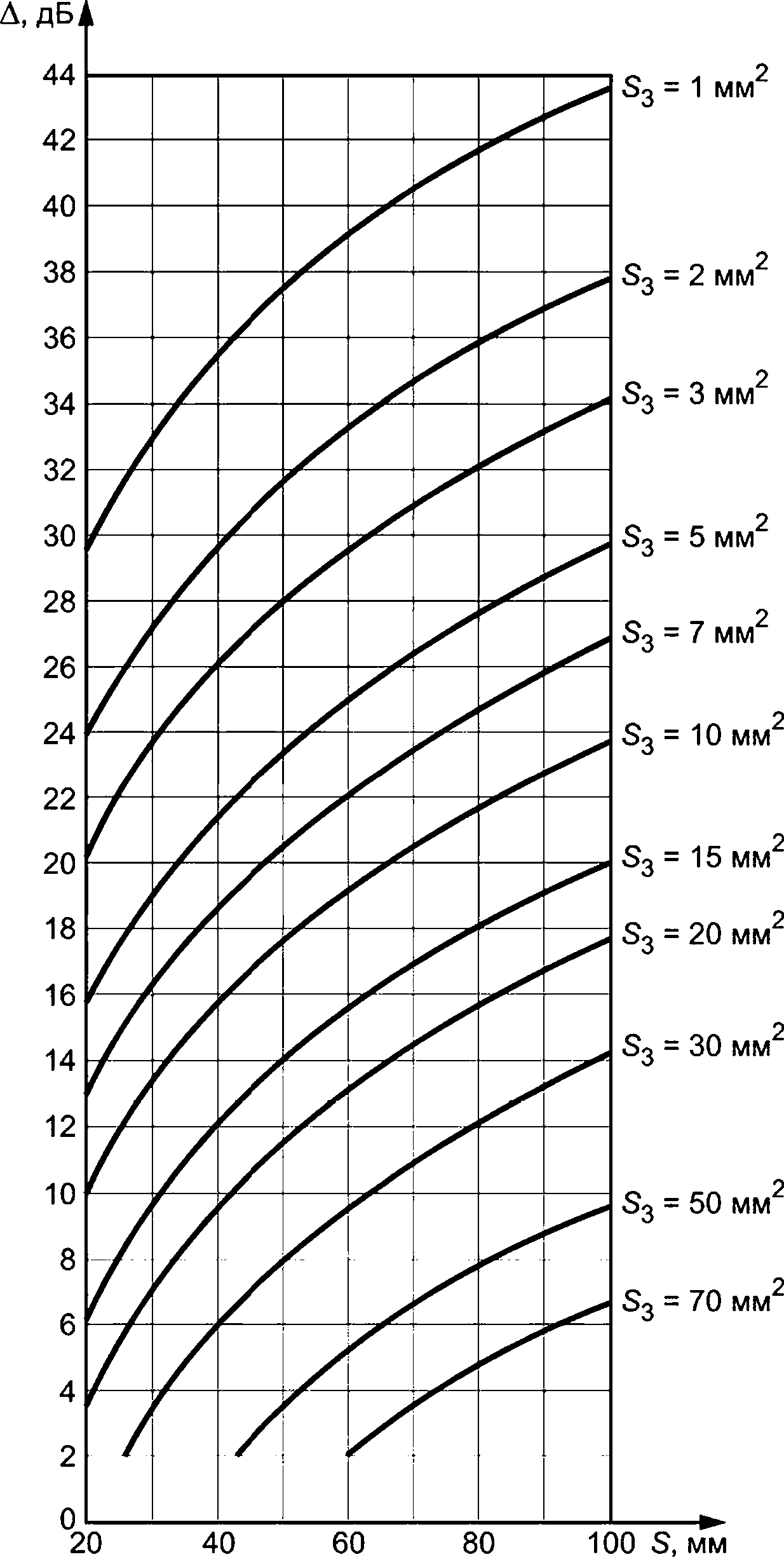
Рисунок Л.4 — АРД-диаграмма при УЗК по схеме «стредл» для f = 2,5 МГц и a = 63° — 67°
Л.8 Поиск несплошностей следует проводить путем поперечно-продольного или продольно-поперечного перемещения ПЭП, закрепленных в держателях специализированного устройства. Перемещения осуществляются между положениями, при которых шарнир находится над одним из краев поверхности СС (или, если размер СС не позволяет это сделать, между положениями, при которых ПЭП поочередно касаются поверхности СС).
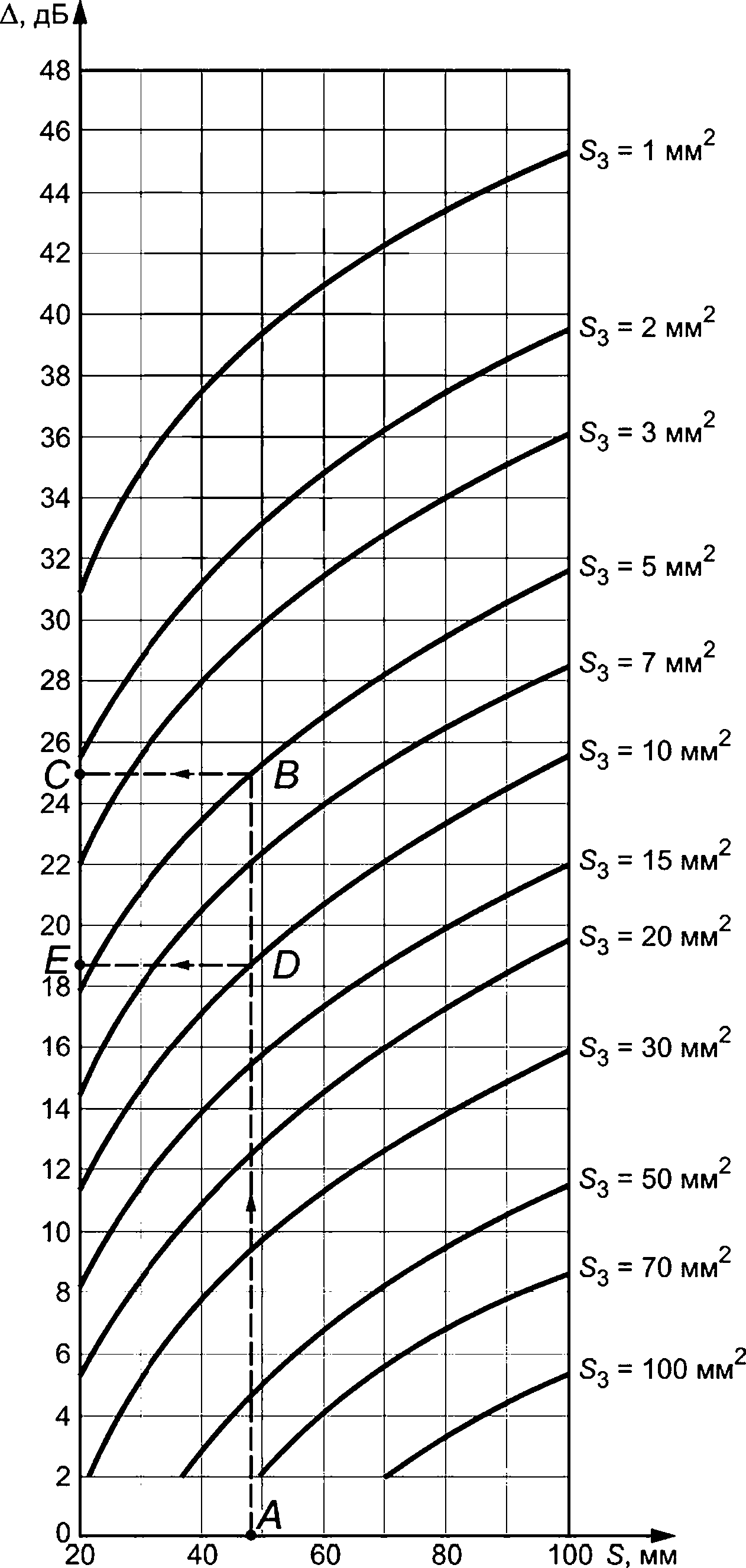
Рисунок Л.5 — АРД-диаграмма при УЗК по схеме «стредл» для f= 2,5 МГц и а = 68°—72°
Одновременно необходимо осуществлять развороты устройства от 10° до 15° в обе стороны от среднего положения.
Л.9 Эхо-сигналы от несплошностей возникают на экране дефектоскопа в том же месте развертки, что и при определении амплитуды опорного сигнала. При появлении эхо-сигнала необходимо выполнить действия по Л.9.1, Л.9.2.
Л.9.1 Следует убедиться, что эхо-сигнал не является ложным импульсом, вызванным отражением боковых лучей от противоположной поверхности СС. Этот импульс может возникнуть, если угол между направляющими устройствами ПЭП превышает 120°. Для этого необходимо ослабить шарнир и разворачивать направляющие под углом более 120°, одновременно наблюдая за экраном дефектоскопа. Если эхо-сигнал получен от несплошности, то он должен исчезнуть с экрана под определенным углом; при дальнейшем увеличении угла на том же месте развертки появляется эхо-сигнал от противоположной поверхности СС. Если же эхо-сигнал является ложным, то он будет монотонно возрастать при увеличении угла и достигнет максимума при таком положении направляющих, когда ПЭП расположены навстречу друг другу.
Л.9.2 Если эхо-сигнал не является ложным, то следует выполнить следующие действия:
- выполнить операции по Л.7.3;
- ослабить крепление ПЭП на направляющих;
- перемещая ПЭП вдоль направляющих по поверхности металла СС, найти максимум эхо-сигнала и определить его амплитуду;
- зафиксировать положение несплошности вдоль шва: она находится под шарниром в области радиусом около 15 мм относительно проекции точки крепления шарнира на поверхность ОК.
Л.10 Эквивалентную площадь несплошности определяют с помощью АРД-диаграмм.
Глубину залегания несплошности не определяют. В заключении по результатам УЗК указывают диапазон глубин, в котором расположена несплошность (см. Л.7.2).
Пример — При УЗК СС, указанного в примере пункта Л. 7.4, обнаружена несплошность, амплитуда эхо-сигнала от которого равна 24 дБ. Необходимо определить эквивалентную площадь несплошности. Разность А амплитуд опорного сигнала Аоп и эхо-сигнала от несплошности равна 43 - 24 = 19 дБ. Из АРД-диаграммы (см. рисунок Л.5, отрезки АД и ЕД) видно, что эквивалентная площадь S3 равна 10 мм2.
Приложение М (обязательное)
Методика ультразвукового контроля металла наплавленной поверхности головными волнами
М.1 Настоящая методика регламентирует порядок УЗК зоны сплавления металла наплавленной поверхности из сталей перлитного и аустенитного класса толщиной не более 13 мм с основным металлом в целях выявления поднаплавочных вертикально ориентированных плоскостных несплошностей (типа трещин), перпендикулярных к зоне сплавления.
М.2 Поверхность перед проведением УЗК должна быть подготовлена: зачищена от брызг металла, грязи и флюса, не должна иметь углублений и неровностей. Шероховатость поверхности Ra должна быть не более 6,3 мкм.
М.З УЗК проводят УЗ-дефектоскопом в комплекте с ПГВ типа «дуэт» (наклонный PC ПЭП, например, ИЦ-70 или ПГЦ-70) на частоте 1,8 МГц. Допускается применение других ПЭП, реализующих способ УЗК головными волнами и удовлетворяющих требованиям настоящего стандарта. Схема УЗК показана на рисунке М.1. Допускается проводить УЗК ПГВ типа «тандем» (наклонный PC ПЭП, например, ПГЦ-91), если они обеспечивают выявление настроечного отражателя на уровне, превышающем уровень шумов на 6 дБ.

1 — излучатель; 2 — наплавленная поверхность; 3, 4 — продольно-поверхностные волны; 5 — трещина; 6 — боковая волна; 7 — приемник; 8 — основной металл
Рисунок М.1 — Схема УЗК металла наплавленной поверхности головными волнами ПЭП ПГВ «дуэт»
М.4 Перед началом УЗК металла наплавленной поверхности ее рекомендуется разметить на участки размером приблизительно 200 х 200 мм. Поверхность перед проведением УЗК покрывают контактной средой.
М.5 Настройку диапазона развертки дефектоскопа осуществляют по отражению продольно-поверхностных волн от свободного прямого двугранного угла ОК или НО. Настройку чувствительности осуществляют по плоскодонному отражателю в НО.
М.6 Согласно [5] чувствительность при УЗК головными волнами должна устанавливаться в зависимости от толщины металла наплавленной поверхности по боковому плоскодонному отражателю диаметром 2 мм, 3 мм или 4 мм. На рисунке М.2 представлен один из вариантов исполнения НО.

Рисунок М.2 — НО (а) и схема настройки диапазона развертки и чувствительности (б)
НО изготавливают из тех же видов сталей (основной металл и металл наплавленной поверхности) и по той же технологии, что и ОК в зоне контроля. Толщина металла наплавленной поверхности НО не должна отличаться от толщины металла наплавленной поверхности ОК в зоне контроля более чем на 0,5 мм. Шероховатость контактной поверхности НО должна соответствовать шероховатости контактной поверхности Ra в зоне контроля, но не должна быть более 6,3 мкм.
М.7 Настройку диапазона развертки проводят в следующей последовательности:
- устанавливают ПГВ на НО таким образом, чтобы передняя грань ПГВ совпадала с плоскостью торца образца. Поднимают чувствительность дефектоскопа до появления на экране эхо-сигнала, соответствующего отражению от торца образца. При этом эхо-сигнал должен пальпироваться на глубине от 5 до 10 мм от контактной поверхности;
- стробируют эхо-сигнал, как показано на рисунке М.26.
М.8 Настройку чувствительности проводят в следующей последовательности:
- устанавливают ПГВ на образец таким образом, чтобы его передняя грань и дно отражателя находились в одной плоскости;
- увеличивают чувствительность дефектоскопа до появления эхо-сигнала, отраженного от дна плоскодонного отражателя в строб-импульсе, и перемещая ПГВ (ближе — дальше), находят его максимум;
- устанавливают браковочный уровень чувствительности. Для этого доводят высоту эхо-сигнала на экране до 50 % над линией развертки (рисунок М.26);
- устанавливают поисковый уровень чувствительности повышением чувствительности на 6 дБ выше браковочного уровня;
- УЗК проводят на поисковом уровне чувствительности путем плавного перемещения ПГВ по наплавленной поверхности;
- поиск несплошностей проводят путем плавного построчного сканирования с шагом не более половины диаметра ПЭ ПГВ (9 мм) со скоростью не более 50 мм/с.
М.9 Сканирование проводят по наплавленной поверхности в направлении, перпендикулярном и параллельном ходу наплавочной ленты или наплавочного электрода. При этом прозвучивание осуществляют в двух взаимно противоположных направлениях с поворотом ПГВ вокруг вертикальной оси на 30°, как показано на рисунке М.З.
М.10 При УЗК по размеченным участкам перекрытие границ участков должно быть не менее шага сканирования ПГВ.
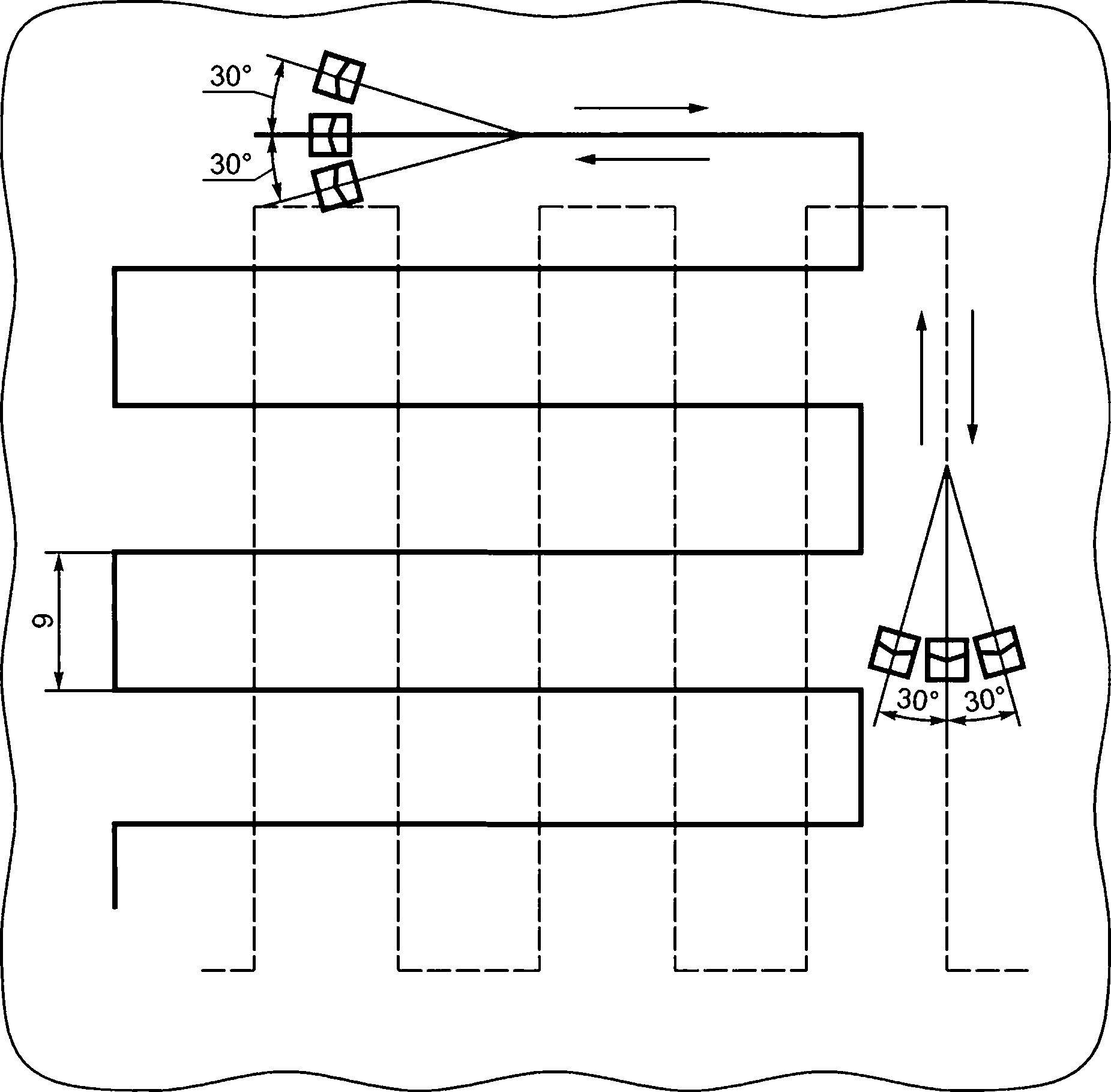
Рисунок М.З — Траектория сканирования ПЭП по наплавленной поверхности (стрелками показаны направления перемещения ПЭП)
М.11 В процессе сканирования необходимо обеспечивать постоянный акустический контакт ПГВ с наплавленной поверхностью.
Для наблюдения за акустическим контактом ПГВ рекомендуется следить за сигналами, проходящими от излучателя на приемник через металл наплавленной поверхности по кратчайшему расстоянию. Для обеспечения одновременного наблюдения за качеством акустического контакта и сравнения амплитуды эхо-сигналов от возможных несплошностей (при наличии) с уровнем браковочной чувствительности используют УЗ-дефектоскопы с большим динамическим диапазоном по экрану.
М.12 Для облегчения обнаружения несплошностей рекомендуется использовать систему АСД-дефектоскопа со звуковой и световой сигнализацией.
М.13 Оценку несплошностей проводят по нормам [2], [4], [10], документам по стандартизации, а также КД, ТД, устанавливающими требования к оценке соответствия объектов контроля оборудования и трубопроводов атомных энергетических установок и других элементов атомных станций.
Приложение Н (обязательное)
Методика настройки чувствительности дефектоскопа
Н.1 Настройка чувствительности дефектоскопа по угловым отражателям
Н.1.1 Браковочный уровень
Н.1.1.1 Устанавливают чувствительность: достаточную для обнаружения углового отражателя в НО.
Н.1.1.2 Находят максимальный эхо-сигнал от соответствующего углового отражателя, перемещая ПЭП по образцу.
Н.1.1.3 Уменьшают эхо-сигнал до принятого уровня на экране дефектоскопа. При этом запас чувствительности должен быть не менее 15 дБ.
Н.1.2 Контрольный уровень
Повышают чувствительность дефектоскопа относительно браковочного уровня по Н.1.1 на 6 дБ.
Н.1.3 Поисковый уровень
Повышают чувствительность относительно браковочного уровня по Н.1.1 на 12 дБ.
Н.2 Настройка чувствительности при УЗК СС с помощью АРД-диаграмм
Н.2.1 Для настройки чувствительности при УЗК СС с толщиной свариваемых деталей 12 мм и более вместо АРД-диаграмм могут быть использованы АРД-шкалы.
Н.2.2 Для настройки чувствительности и определения эквивалентной площади выявленных несплошностей по АРД-диаграммам (AVG-диаграммам, АРД-шкалам) необходимо пользоваться их бумажным вариантом с самостоятельным проведением расчетов или использовать встроенные в дефектоскоп АРД-диаграммы (AVG-диаграммы).
Н.2.3 В АРД-диаграммах (AVG-диаграммах) для ПС и ПРС ПЭП в качестве опорного сигнала используется донный сигнал. В АРД-диаграммах для НП в качестве опорного сигнала используется сигнал от двугранного угла или сигнал от отражателя диаметром 6 мм в мере СО-2. В AVG-диаграммах для НП в качестве опорного сигнала используется сигнал от цилиндрической поверхности (радиус 100 мм) в НО V1 (К1) или от цилиндрической поверхности (радиус 25,50 мм) в НО V2 (К2).
Н.2.4 В большинстве случаев АРД-диаграммы (AVG-диаграммы, АРД-шкалы) построены для металла с затуханием УЗ, равным нулю. Затухание в металле ОК следует учитывать путем введения соответствующих поправок.
Н.2.5 Работа с АРД-диаграммой при УЗК ПС ПЭП
Н.2.5.1 На рисунке Н.1 приведена АРД-диаграмма для ПЭП П111 -2.5-К12. По оси абсцисс внизу отложены значения глубины залегания несплошности h в мм. По оси ординат отложены значения амплитуд эхо-сигналов в отрицательных децибелах. В этих координатах построены графики зависимости амплитуд сигналов от плоскодонных отражателей. Площади плоскодонных отражателей указаны справа на концах этих графиков. Наклонные прямые характеризуют затухание УЗ в дБ/мм.
Н.2.5.2 В качестве опорного сигнала используется донный сигнал или отражение от бокового цилиндрического отражателя диаметром 6 мм в мере СО-2 на глубине 44 мм. Амплитуда от него привязана к данной АРД-диаграмме и соответствует значению минус 20 дБ.
Пример 1 — В угловом сварном шве с толщиной основной детали 60 мм и толщиной привариваемой детали 20 мм не допускаются несплошности эквивалентной площадью 5 мм2 и более. Необходимо настроить чувствительность для УЗК ПС ПЭП со стороны основной детали. Коэффициент затухания в данном шве составляет 0,00 дБ/мм.
На рисунке Н. 1 находим точку А, соответствующую донному сигналу на глубине 60 мм. От этой точки проводим горизонтальную линию (так как нет затухания) до оси ординат — точка В, соответствующая значению минус 8 дБ. Находим точку С, соответствующую площади недопустимой несплошности (5 мм2) на глубине, равной толщине основной детали 60 мм. От этой точки влево проводим горизонтальную прямую CD. Точка D находится на уровне минус 32 дБ. Этот уровень отличается от опорного сигнала на 32- 8 = 24 дБ.
Настройку следует выполнять следующим образом: на экране дефектоскопа получаем донный сигнал с глубины 60 мм и увеличиваем чувствительность на 24 дБ (так, чтобы донный сигнал пошел вверх). Далее следует увеличить чувствительность до уровня фиксации (зафиксировать значение) и до уровня поиска, на котором и следует выполнять контроль.
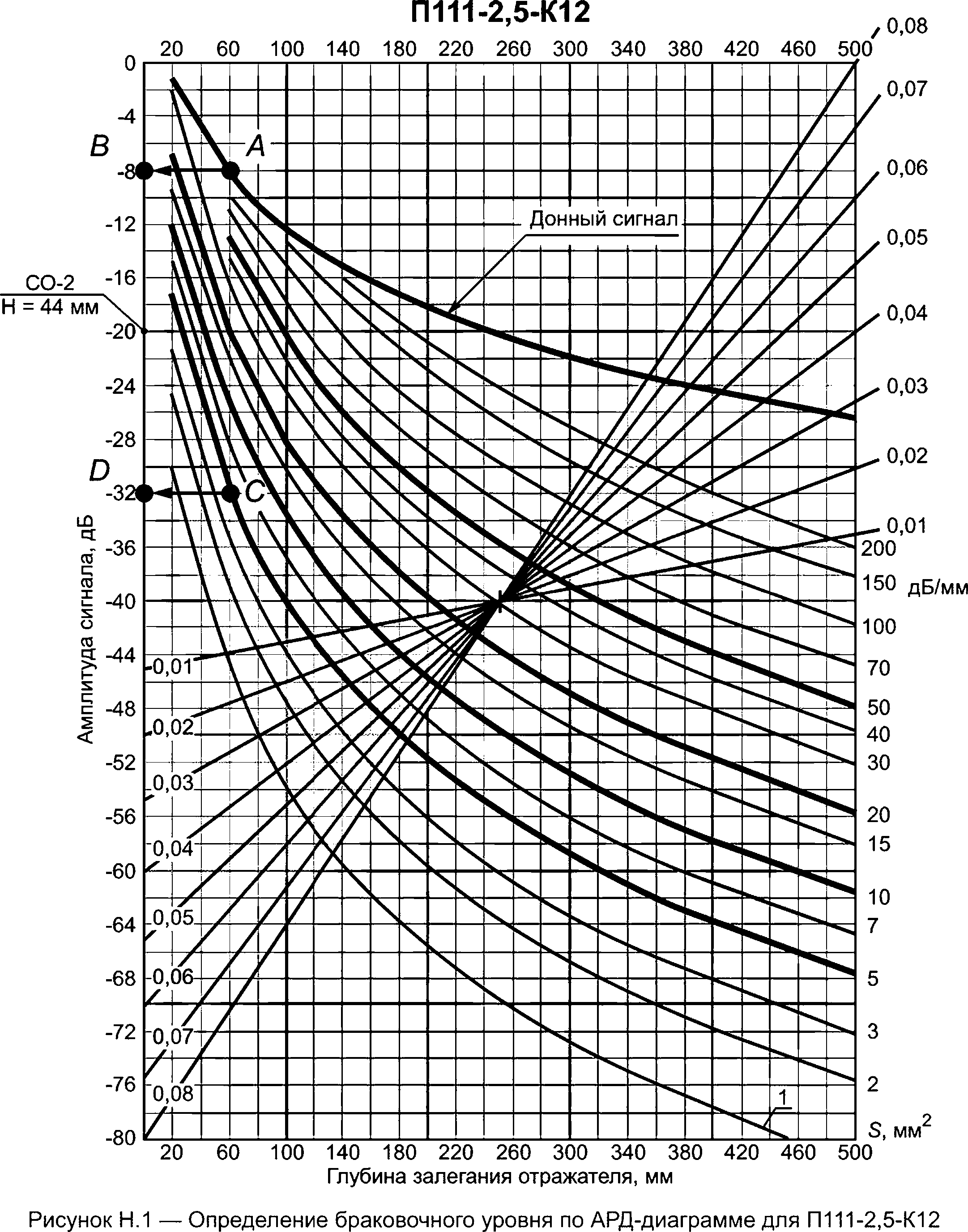
Н.2.6 Работа с AVG-диаграммой при УЗК ПС ПЭП
Н.2.6.1 На рисунке Н.2 приведена AVG-диаграмма для ПЭП B2S. По оси абсцисс внизу отложены значения расстояния до несплошности по лучу S, мм (лучевая дальность). По оси ординат отложены значения амплитуд эхо-сигналов в децибелах. В этих координатах построены графики зависимости амплитуд сигналов от плоскодонных отражателей. Диаметры плоскодонных отражателей указаны справа на этих графиках.
Н.2.6.2 В качестве опорного сигнала может использоваться сигнал от донной поверхности.
Пример 2 — Производят настройку чувствительности дефектоскопа для УЗК СС и зоны сплавления антикоррозионной наплавленной поверхности с металлом шва ГЦТ Ду850. Толщина ОК — 70 мм. Использован ПС ПЭП B2S (2 МГц, 0°, d=24 мм). Браковочный и контрольный уровни для СС определяют в соответствии с КД, например, $сс-бр ~ ? мм2> $сс-фикс ~ мм2- в соответствии с КД определяют браковочный и контрольный уровни для наплавленной поверхности, например, S н_6р = 20 мм2; S н-фикс~ -10 мм2. При настройке чувствительности по донному сигналу на биметаллической трубе поправкой на затухание в плакирующем слое пренебрегают. Необходимо определить чувствительность дефектоскопа на браковочном, контрольном и поисковом уровнях.
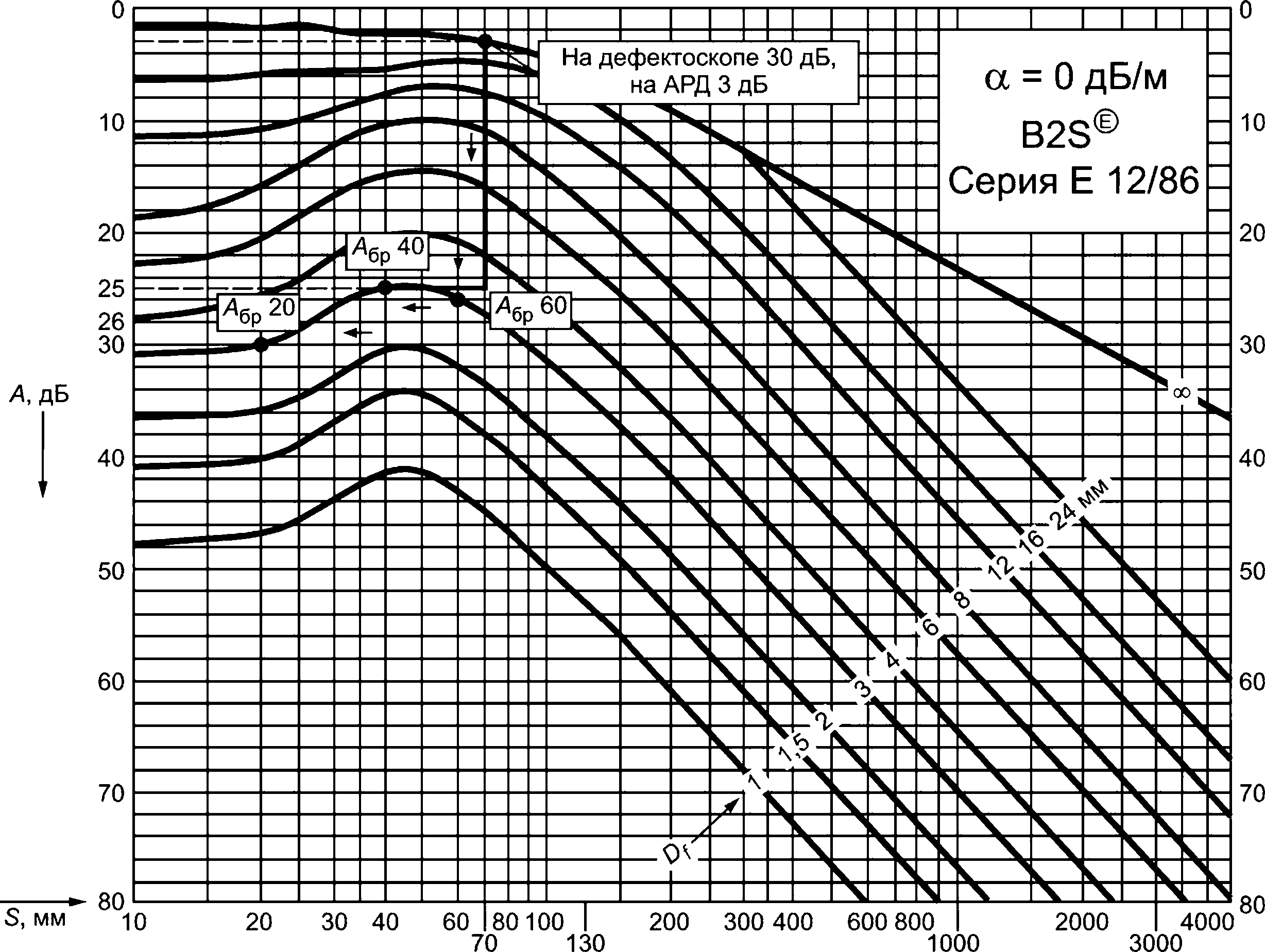
Рисунок Н.2 — Определение браковочного уровня при УЗК ГЦТ Ду850 по AVG-диаграмме для ПЭП B2S
1 Для СС:
- определяют значение донного сигнала на ОК, например Ад н0 = 30 дБ (определяют или непосредственно на ОК, или на НО, изготовленном из фрагмента ОК);
- находят значение Ад н0 на AVG-диаграмме (рисунок Н.2) на глубине 70 мм: Адн0 = 3 дБ. Амплитуда донного сигнала 3 дБ на АРД-диаграмме соответствует Ад н0 = 30 дБ на ОК;
- находят значение амплитуды для отражателя площадью 7 мм2 (d = 3 мм) на AVG-диаграмме (рисунок Н.2) на глубине 60 мм: Асс_бр = 26 дБ;
- находят разницу в значениях амплитуд отражателя площадью 7 мм2 (d = 3 мм) и донного сигнала на AVG-диаграмме 26- 3 = 23 дБ. Браковочный уровень чувствительности на глубине 60 мм определяют суммированием 30 + 23 = 53 дБ.
Для определения браковочного уровня на глубинах 40 и 20 мм необходимо найти пересечение кривой (для отражателя d = 3 мм) с глубиной 40 и 20 мм соответственно (рисунок Н.2). На глубине 40 мм находят разницу в значениях амплитуд отражателя (d = 3 мм) и донного сигнала на AVG-диаграмме 25-3 =22 дБ. Таким образом, браковочный уровень на глубине 40 мм равен 30 + 22 = 52 дБ.
На глубине 20 мм находят разницу в значениях амплитуд отражателя размером (d = 3 мм) и донного сигнала на АРД-диаграмме 30-3 = 27 дБ. Значение Абр на глубине 20 мм равно 30 + 27 = 57 дБ.
Контрольный уровень устанавливают на 6 дБ выше браковочного. Поисковый уровень устанавливают на 12 дБ выше браковочного. Сводят полученные данные в таблице Н. 1.
Таблица Н.1
Гпубина, мм | 20 | 40 | 60 |
Браковочный уровень, дБ | 57 | 52 | 53 |
Контрольный уровень, дБ | 63 | 58 | 59 |
Поисковый уровень, дБ | 69 | 64 | 65 |
При УЗК в случае обнаружения отражателя на глубине, отличной от 20, 40, 60 мм, необходимо определить значение амплитуды по AVG-диаграмме аналогично перечисленным глубинам.
2 Для зоны сплавления металла антикоррозионной наплавленной поверхности с основным металлом:
- находят значение донного сигнала Ад н0 = 30 дБ (определяют или непосредственно на ОК, или на НО, изготовленном из фрагмента ОК);
- находят значение Ад н0 на AVG-диаграмме (рисунок Н.З) на глубине 70 мм, Адн0 = 3 дБ. Амплитуда донного сигнала 3 дБ на AVG-диаграмме соответствует Ад н0 = 30 дБ на ОК;
- находят значение амплитуды для отражателя площадью 20 мм2 (d = 5 мм) на АРД-диаграмме (рисунок Н.З) на глубине 62 мм А = 18 дБ;
- находят разницу в значениях амплитуд отражателя размером (d = 5 мм) и донного сигнала 18-3-= 15 дБ.
Браковочный уровень чувствительности на глубине 62 мм определяют суммированием 30 + 15 = = 45 дБ. Контрольный уровень устанавливают на 6 дБ выше браковочного. Поисковый уровень устанавливают на 12 дБ выше браковочного.
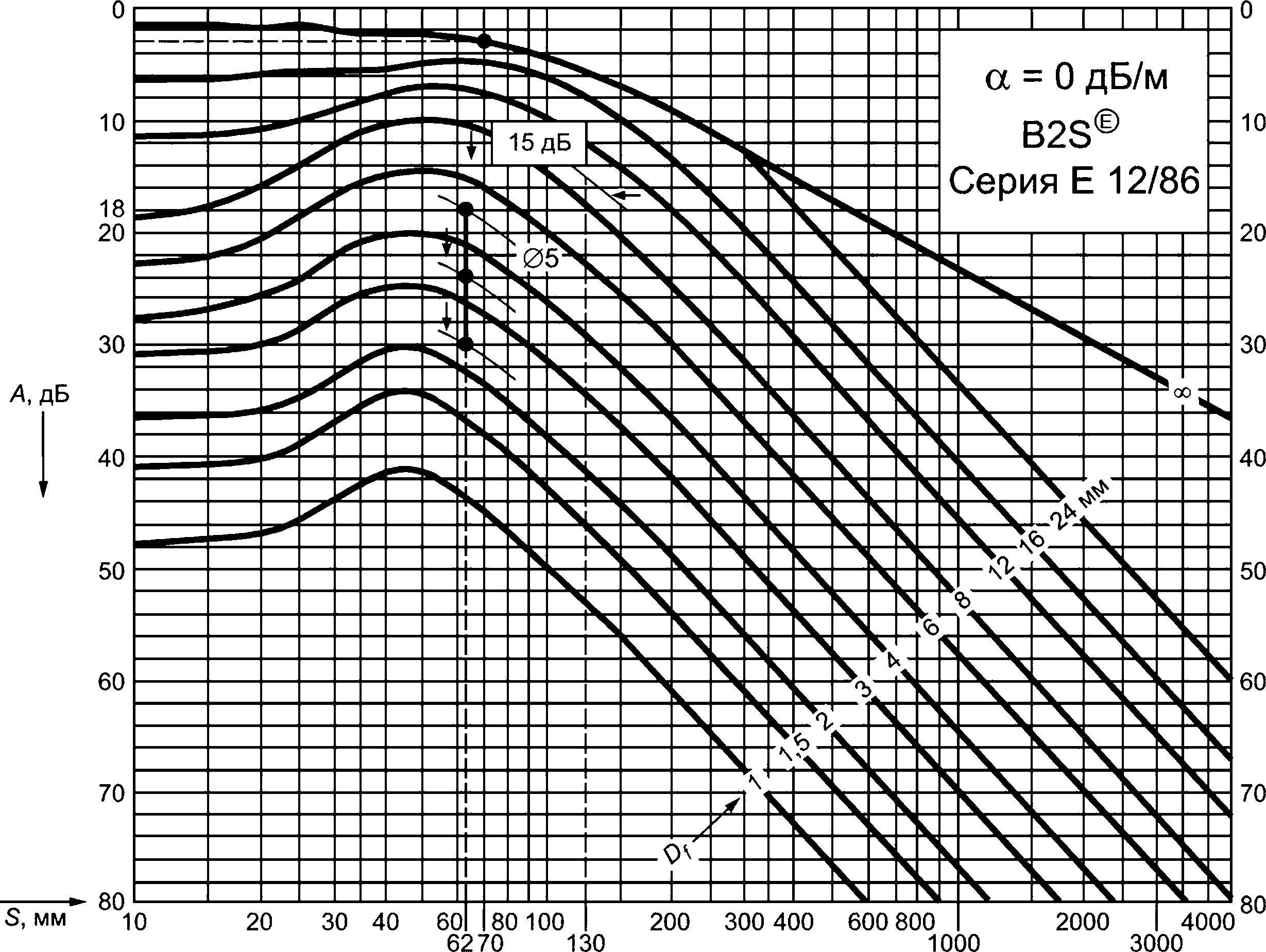
Рисунок Н.З — Определение браковочного, контрольного и поискового уровней при УЗК металла антикоррозионной наплавленной поверхности по AVG-диаграмме для ПЭП B2S
Н.2.7 Работа с АРД-диаграммой при УЗК НП (С)
Н.2.7.1 На рисунке Н.4 приведена АРД-диаграмма для ПЭП П121-2.5-65 (12 х 16). По оси абсцисс внизу отложены значения расстояния до несплошности по лучу (лучевая дальность) г, мм, вверху глубина залегания несплошности h, мм. По оси ординат отложены значения амплитуд эхо-сигналов в отрицательных децибелах. В этих координатах построены графики зависимости амплитуд сигналов от плоскодонных отражателей. Площади плоскодонных отражателей указаны справа на концах графиков. Наклонные прямые характеризуют затухание УЗ в дБ/мм.
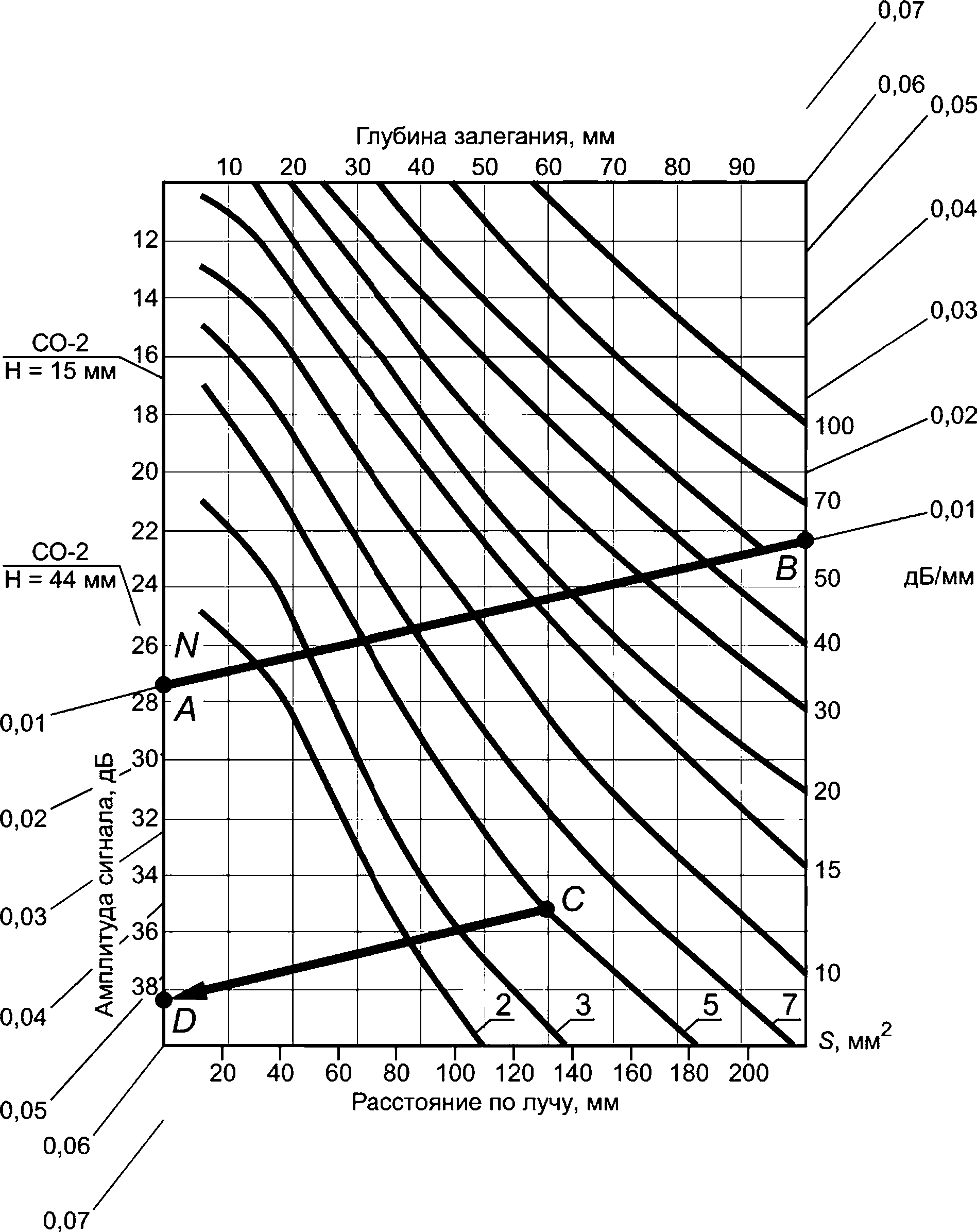
Рисунок Н.4 — Определение браковочного уровня по АРД-диаграмме для П121-2.5-65 (12 х 16)
Н.2.7.2 В качестве опорного сигнала используется отражение от бокового цилиндрического отражателя диаметром 6 мм в мере СО-2 на глубине 44 мм. Амплитуда от него привязана к АРД-диаграмме и соответствует уровню минус 27,5 дБ (точка N).
Пример 3 — При УЗК СС с толщиной свариваемых деталей 60 мм не допускаются несплошности эквивалентной площадью 5 мм2 и более. Коэффициент затухания в данном шве составляет 0,01 дБ/мм. На рисунке Н.4 через центр рисунка, обозначенный крестом, проводим прямую АВ, соответствующую затуханию 0,01 дБ/мм. Находим точку С, соответствующую площади несплошности 5 мм2 на глубине 60 мм. От этой точки влево проводим прямую CD, параллельную прямой АВ. Точка D находится на уровне минус 38,5 дБ. Этот уровень отличается от опорного сигнала на 38,5 - 27,5 = 11,0 дБ.
Настройку следует выполнять следующим образом: на экране дефектоскопа получаем сигнал от бокового цилиндрического отражателя в образце СО-2 и увеличиваем чувствительность на 11,0 дБ (так, чтобы сигнал пошел вверх). Далее следует увеличить чувствительность до уровня фиксации (зафиксировать значение) и до уровня поиска, на котором и следует выполнять контроль.
Н.2.8 Работа с AVG-диаграммами при УЗК НП (С)
Н.2.8.1 На рисунке Н.5 приведена AVG-диаграмма для ПЭП MWB 45-2 (2 МГц, 45°, размер ПЭ — 8x9 мм). По оси абсцисс внизу отложены значения расстояния до несплошности по лучу S, мм (лучевая дальность). По оси ординат отложены значения амплитуд эхо-сигналов в децибелах. В этих координатах построены графики зависи-
мости амплитуд сигналов от плоскодонных отражателей. Диаметры плоскодонных отражателей указаны справа на
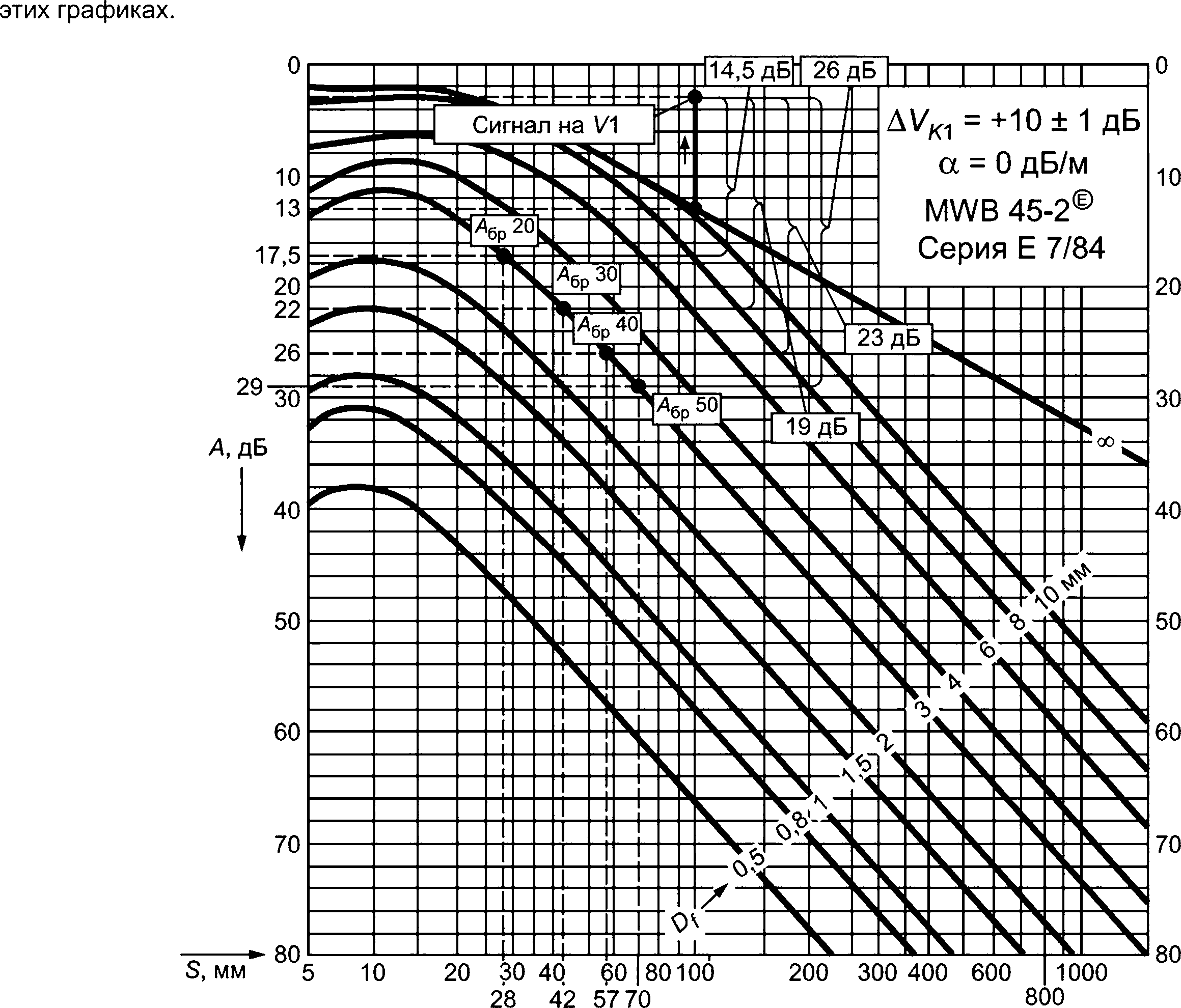
Рисунок Н.5 — Настройка чувствительности с использованием AVG-диаграммы и V1
Н.2.8.2 В качестве опорного сигнала может использоваться сигнал от плоскодонного отражателя или донной поверхности (отражение от поверхности, перпендикулярной к углу ввода) или от цилиндрической поверхности (радиус 100 мм) в НО V1 (/CI).
Пример 4 — При УЗК СС ГЦТ Ду850 в случае настройки с помощью V1 с толщиной свариваемых деталей 70 мм необходимо настроить браковочную чувствительность S6p = 7 мм2 и чувствительность фиксации (контрольный уровень) 8фикс = 3,5 мм2.
Определяют значение сигнала на V1 от цилиндрической поверхности (рисунок Н.6): AV1 = 23 дБ (расстояние по лучу = 100 мм). Вычисляют значение сигнала по кривой °° (Ад н0) на AVG-диаграмме (рисунок Н.5) на расстоянии 100 мм Адн0 = 13 дБ. Вычитают из Адн0 = 13 дБ поправку AVK1 (рисунок Н.5) AV1 = 13 - 10 = 3 дБ.
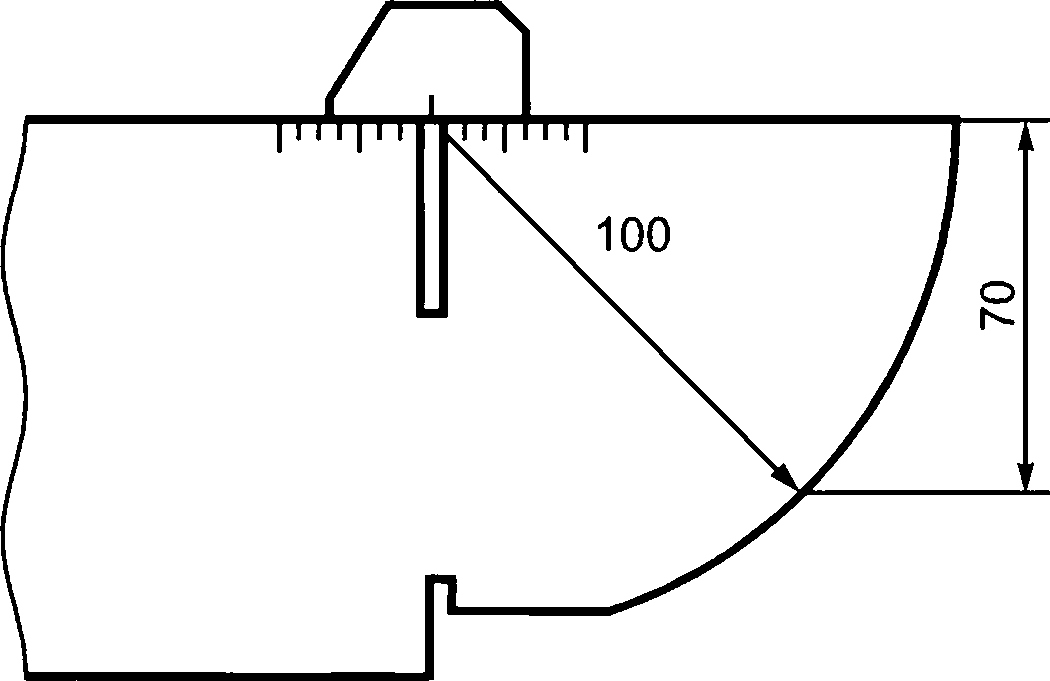
Рисунок Н.6 — Получение максимального сигнала на образце V1
Амплитуда 3 дБ на расстоянии по лучу 100 мм на AVG-диаграмме соответствует эхо-сигналу с амплитудой 23 дБ на образце V1. Вычисляют значения амплитуды для отражателя размером d = 3 мм (S6p = 7 мм2) на AVG-диаграмме (на глубине 50, 40, 30 и 20 мм (расстояния по лучу 70, 57, 42 и 28 мм соответственно)): А50 = 29 дБ; А40 = 26 дБ; А30 = 22 дБ; А20 = 17,5 дБ. Вычисляют разницу значений амплитуд отражателя размером d = 3 мм А50, А40, Азо, А20 и сигнала от V1 на AVG-диаграмме: ЛА50 = 29-3 = 26 дБ; ЛА40 = 26-3 = 23 дБ;ЛА30 = 22-3 = 19 дБ;ЛА20 = 17,5-3 = 14,5 дБ.
Чувствительность определяют следующим образом:
а) значение амплитуды сигнала от V1 на дефектоскопе суммируют со значением ДА50: 23 + 26 = = 49 дБ. Это значение соответствует браковочному уровню на глубине 50 мм;
б) браковочный уровень на глубинах 40, 30 и 20 мм определяют аналогично:
Абр40 = 23 + 23 = 46 дБ; Абр30 = 23+19=42 дБ; Абр20 = 23+ 14,5 = 37,5 дБ;
в) контрольный уровень устанавливают на 6 дБ выше браковочного;
г) поисковый уровень устанавливают на 12 дБ выше браковочного.
При УЗК в случае обнаружение отражателя на глубине, отличной от 20, 30, 40, 50 мм, необходимо определить значение амплитуды по AVG-диаграмме аналогично перечисленным глубинам.
Пример 5 — При УЗК СС из сталей перлитного класса ПЭП MWB 45-2 выявлен отражатель. Значение амплитуды эхо-сигнала от отражателя А =48 дБ. Гпубина залегания отражателя — 50 мм. Материал основного металла СС — Ст20 (сталь перлитного класса). Толщина свариваемых деталей — 100 мм. Использован НП MWB 45-2 (2 МГц, 45°, размер ПЭ — 8*9 мм). Необходимо определить эквивалентную площадь отражателя S3Kg в СС в случае получения донного сигнала на НО.
Так как AVG-диаграмма построена в зависимости от расстояния по лучу до отражателя, пересчитывают глубину 50 мм в расстояние по лучу (для этого глубину разделяют на косинус угла ввода): 50/cos 45 = 70 мм. Вычисляют значение донного сигнала на НО из того же материала, что и СС, на расстоянии 70 мм (рисунок Н.7): Адно = 32 дБ. Вычисляют значение Адн0 на AVG-диаграмме (рисунок Н.8) для расстояния 70 мм: Ад н0 = 10 дБ. Амплитуда 10 дБ на AVG-диаграмме соответствует Ад н0 = 32 дБ на НО. Вычисляют разницу в значениях амплитуд эхо-сигнала от отражателя и донного сигнала: Л А = = 48 — 32= 16 дБ. На AVG-диаграмме откладывают вниз 16 дБ от донного сигнала на расстоянии 70 мм (рисунок Н.8). Полученная точка соответствует S3Ke (d3Ke) для исследуемого отражателя. Определяют S^o с учетом близлежащих на AVG-диаграмме линий — d^o = 3,5 мм; S^a = 9,6 мм2.
ЭК& ~ ЗКо ЗКо
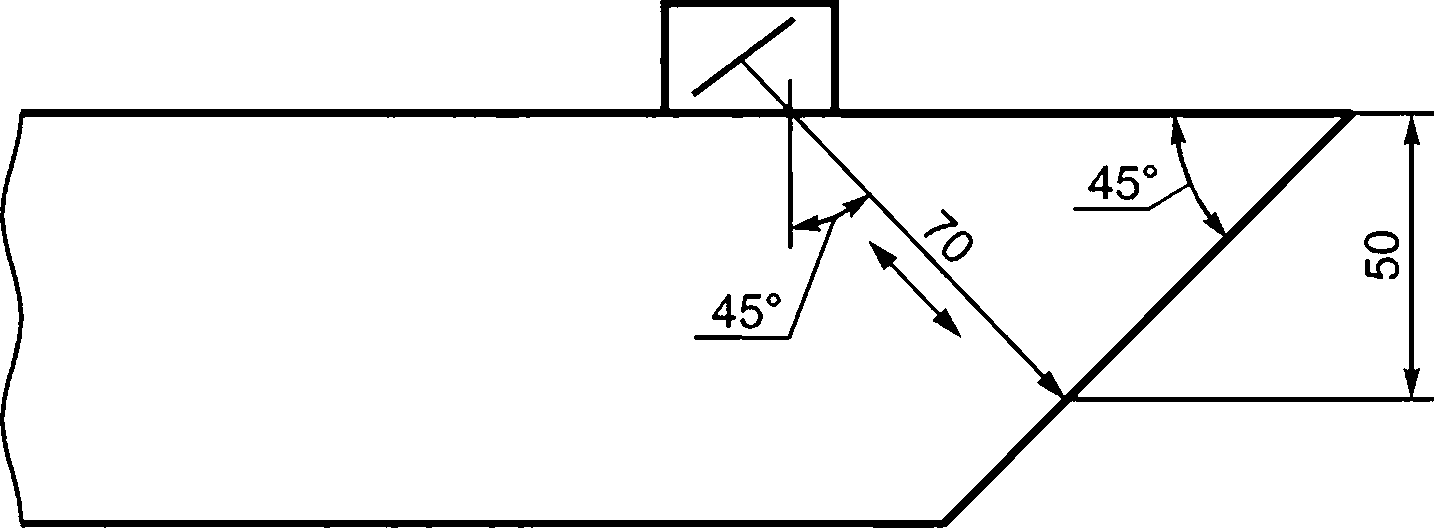
Рисунок Н.7 — Получение донного сигнала на НО
Пример 6 — При УЗК СС ГЦТ Ду850 с толщиной свариваемых деталей 70 мм НП MWB 45-2-Е (2 МГц, 45°, размер ПЭ — 8*9 мм) необходимо настроить браковочную чувствительность S6p = 7 мм2 и чувствительность фиксации Эфикс = 3,5 мм2. Необходимо определить чувствительность дефектоскопа на браковочном, контрольном и поисковом уровнях.
Определяют значение донного сигнала на НО на глубине 50 мм (расстояние по лучу равно 70 мм) (рисунок Н.7) на дефектоскопе: Ад н0 = 30 дБ. Вычисляют значение Ад н0 на AVG-диаграмме (рисунок Н.9) на расстоянии 70 мм: Ад н0 = 10 дБ. Амплитуда донного сигнала 10 дБ на AVG-диаграмме соответствует Ад н0 = 30 дБ на дефектоскопе. Вычисляют значение амплитуды для отражателя размером 7 мм2 (d = 3 мм) на AVG-диаграмме (рисунок Н.9) на расстоянии 70 мм: А = 29 дБ. Вычисляют разницу значений амплитуд отражателя размером 7 мм2 (d = 3 мм) на глубине 50 мм (расстояние по лучу равно 70 мм) и донного сигнала на AVG-диаграмме: ЛА = 29- 10 = 19 дБ.
Чувствительность дефектоскопа определяют следующим образом:
а) значение амплитуды донного сигнала на дефектоскопе суммируют со значением ЛА: 30 + 19 = = 49 дБ. Это значение соответствует браковочному уровню на глубине 50 мм;
б) для определения браковочного уровня на глубинах 60, 40, 30 и 20 мм необходимо установить пересечение AVG-кривой (для отражателя эквивалентной площадью 7 мм2) с глубиной 60, 40, 30 и 20 мм (на расстоянии по лучу 85, 57, 42 и 28 мм соответственно) (рисунок Н.9);
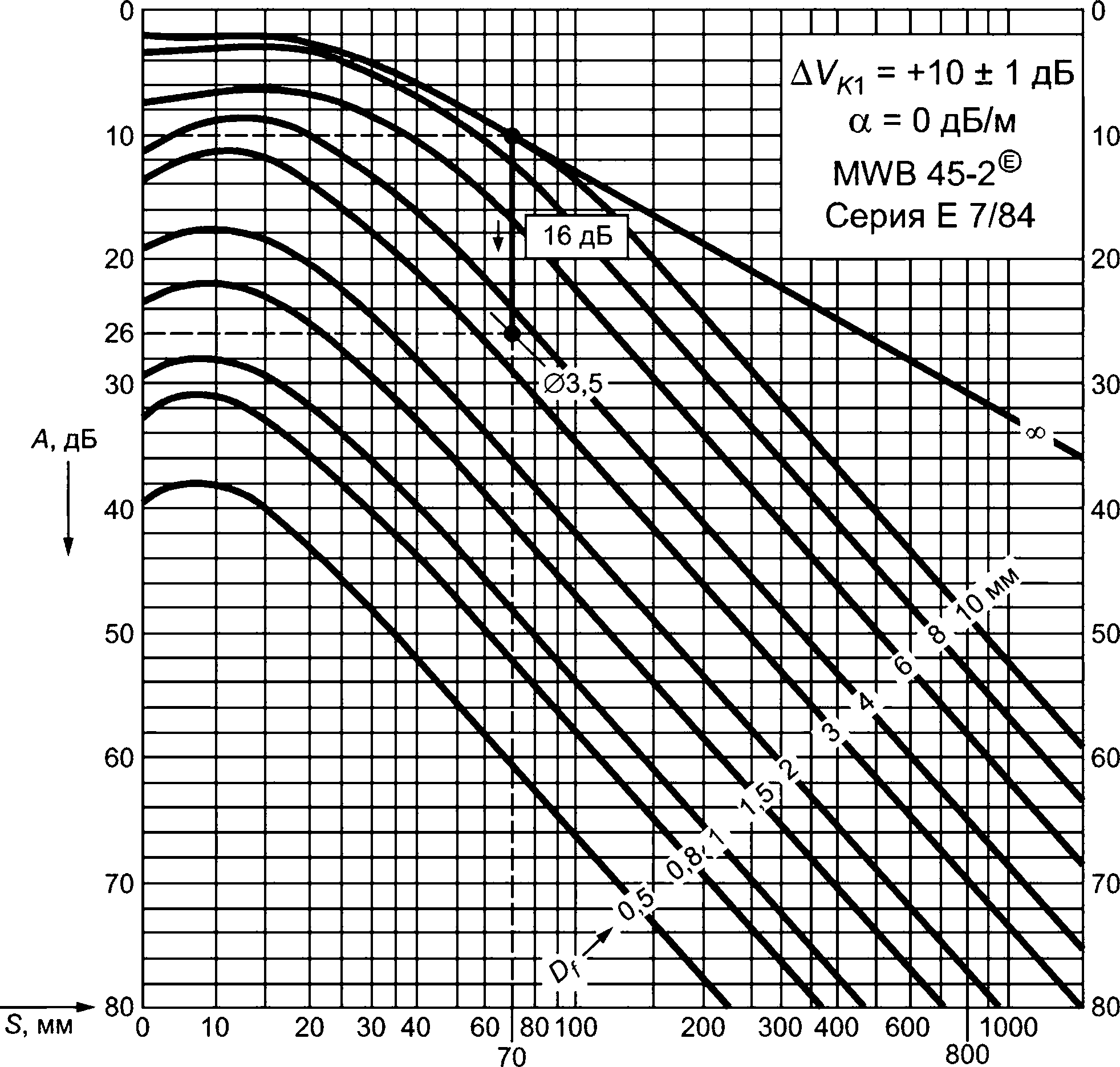
Рисунок Н.8 — Определение эквивалентной площади по AVG-диаграмме с использованием НО
в) на расстоянии 57 мм (глубина 40 мм) вычисляют разницу значений амплитуд отражателя эквивалентной площадью 7 мм2 (d = 3 мм) и донного сигнала на AVG-диаграмме: ЛА40 = 26- 10 = 16 дБ;
г) таким образом, браковочный уровень на глубине 40 мм равен сумме донного сигнала на дефектоскопе и значения ЛА40> Абр = 30 + 16 = 46 дБ;
д) на расстоянии 42 мм находят разницу значений амплитуд отражателя размером 7 мм2 (d = = 3 мм) и донного сигнала на AVG-диаграмме: 4А30 -22- 10- 12 дБ;
е) на глубине 30 мм Абр -30 + 12-42 дБ;
ж) на расстоянии 28 мм находят разницу значений амплитуд отражателя размером 7 мм2 (d = = 3 мм) и донного сигнала на AVG-диаграмме: 4А20 =17,5 -10= 7,5 дБ;
и) на глубине 20 мм Абр = 30 + 7,5 = 37,5 дБ;
к) на расстоянии 85 мм находят разницу значений амплитуд отражателя размером 7 мм2 (d = = 3 мм) и донного сигнала на AVG-диаграмме: 4А60 =32 -10 = 22 дБ;
л) на глубине 60 мм А6р = 30 + 22 = 52 дБ;
м) контрольный уровень устанавливают на 6 дБ выше браковочного. Поисковый уровень устанавливают на 12 дБ выше браковочного.
По лученные данные приведены в таблице Н.2. При УЗК в случае обнаружения отражателя на глубине, отличной от 20, 30, 40, 50, 60 мм, необходимо вычислить значение амплитуды по AVG-кривой аналогично перечисленным глубинам.
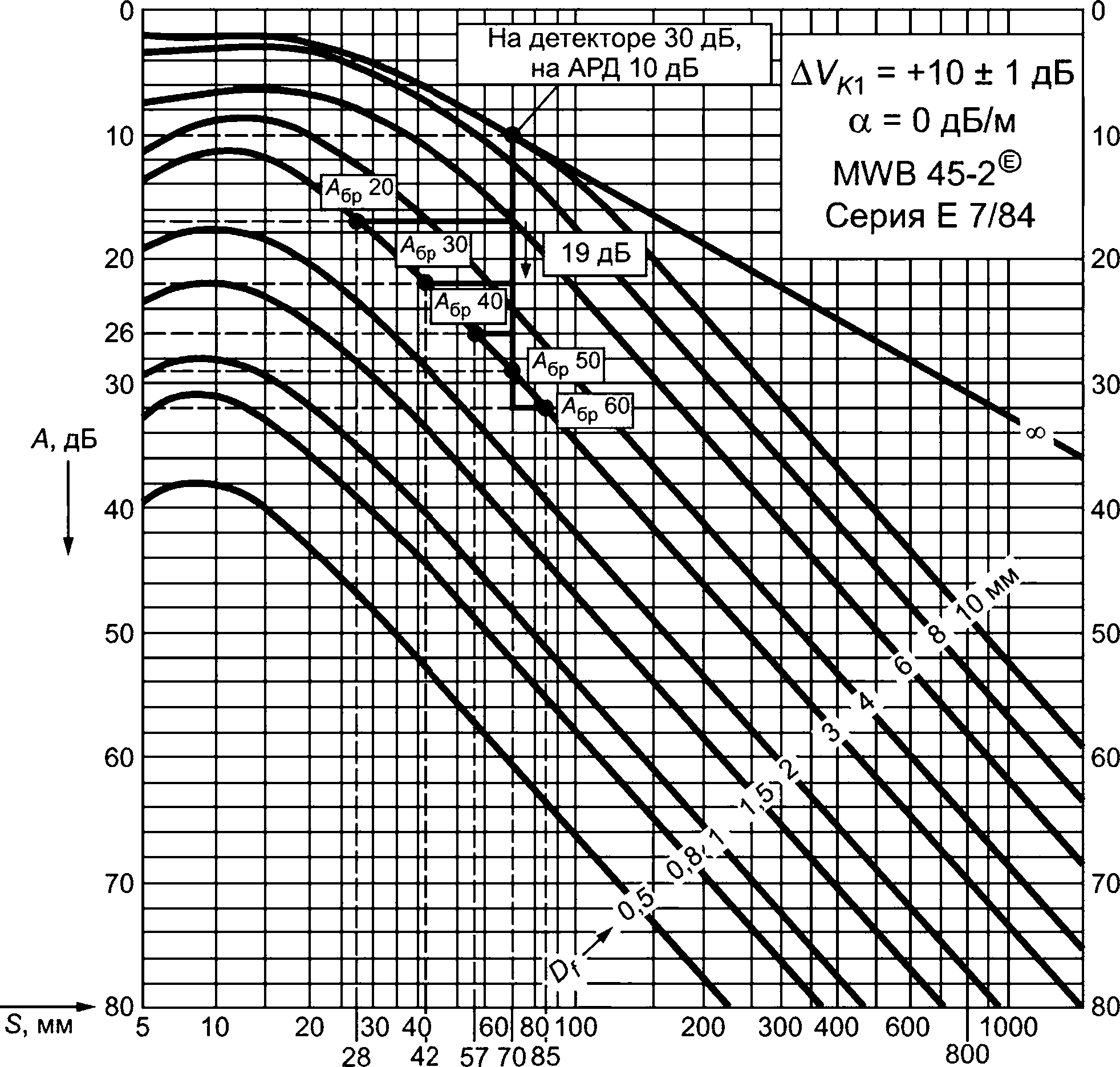
Рисунок Н.9 — Настройка чувствительности дефектоскопа с использованием AVG-диаграммы и НО
Таблица Н.2
Гпубина, мм | 20 | 30 | 40 | 50 | 60 |
Браковочный уровень, дБ | 37,5 | 42 | 46 | 49 | 52 |
Контрольный уровень, дБ | 43,5 | 48 | 52 | 55 | 58 |
Поисковый уровень, дБ | 49,5 | 54 | 58 | 61 | 64 |
Пример 7 — При УЗК СС сосуда с толщиной свариваемых деталей 200 мм использован НП WB 45-2-Е (2 МГц, 45°, размер ПЭ: 20 х 22 мм). Необходимо настроить браковочную чувствительность S6p = = 7 мм2 и чувствительность фиксации Зфикс = 3,5 мм2 при использовании в качестве опорного сигнала НО с плоскодонным отражателем площадью 7 мм2. Глубина залегания плоскодонного отражателя в НО составляет 150 мм. Необходимо определить чувствительность дефектоскопа на браковочном, контрольном и поисковом уровнях.
Определяют значение амплитуды сигнала от плоскодонного отражателя на НО на глубине 150 мм (расстояние получу равно 212 мм) (рисунок Н.10) на дефектоскопе: Апл дно~^ &Б- Вычисляют значение Апл д но на AVG-диаграмме (рисунок Н.11) на расстоянии 212 мм: Апл дно- 34 дБ. Амплитуда сигнала от плоскодонного отражателя 34 дБ на AVG-диаграмме соответствует Апл дНо~ $0 &Б на дефектоскопе.
Чувствительность дефектоскопа определяют следующим образом:
а) браковочный уровень на глубине 150 мм: Апл дНо~ $0 дБ;
б) для определения браковочного уровня на глубинах 200, 100 и 50 мм находят пересечение AVG-кривой (для отражателя эквивалентной площадью 7 мм2) с глубинами 200, 100 и 50 мм (расстояние по лучу 283, 141 и 71 мм соответственно) (рисунок Н.11);
в) для расстояния 283 мм вычисляют разницу между амплитудой от отражателя размером 7 мм2 (d = 3 мм) на глубине 150 мм (расстояние 212 мм) и амплитудой от отражателя размером 7 мм2 на глубине 200 мм (расстояние 283 мм) на AVG-диаграмме: ЛА200 = 38 - 34 = 4 дБ. Браковочный уровень на глубине 200 мм равен сумме значения амплитуды сигнала на дефектоскопе от плоскодонного отражателя на глубине 150 мм и значения ЛА200: Абр = 30 + 4- 34 дБ;
г) для расстояния 141 мм вычисляют разницу значений амплитуд отражателя размером 7 мм2 (d = 3 мм) на глубине 150 мм (расстояние 212 мм) и отражателя размером 7 мм2 на глубине 100 мм (расстояние 141 мм) на AVG-диаграмме: 4А100 = 34- 28 = 6 дБ;
д) поскольку отражатель на глубине 100 мм находится выше по AVG-кривой, чем отражатель на глубине 150 мм, браковочный уровень для глубины 100 мм равен разности значения амплитуды сигнала на дефектоскопе от плоскодонного отражателя на глубине 150 мм и значения ДА 100: Абр = 30-6 = 24 дБ;
е) для расстояния 71 мм вычисляют разницу значений амплитуд отражателя размером 7 мм2 (d = = 3 мм) на глубине 150 мм (расстояние 212 мм) и отражателя размером 7 мм2 на глубине 50 мм (расстояние 71 мм) на AVG-диаграмме: 4А50 = 34-25 = 9 дБ;
ж) на глубине 50 мм Абр = 30-9 = 21 дБ;
и) контрольный уровень устанавливают на 6 дБ выше браковочного. Поисковый уровень устанавливают на 12 дБ выше браковочного.
Полученные данные приведены в таблице Н.З.
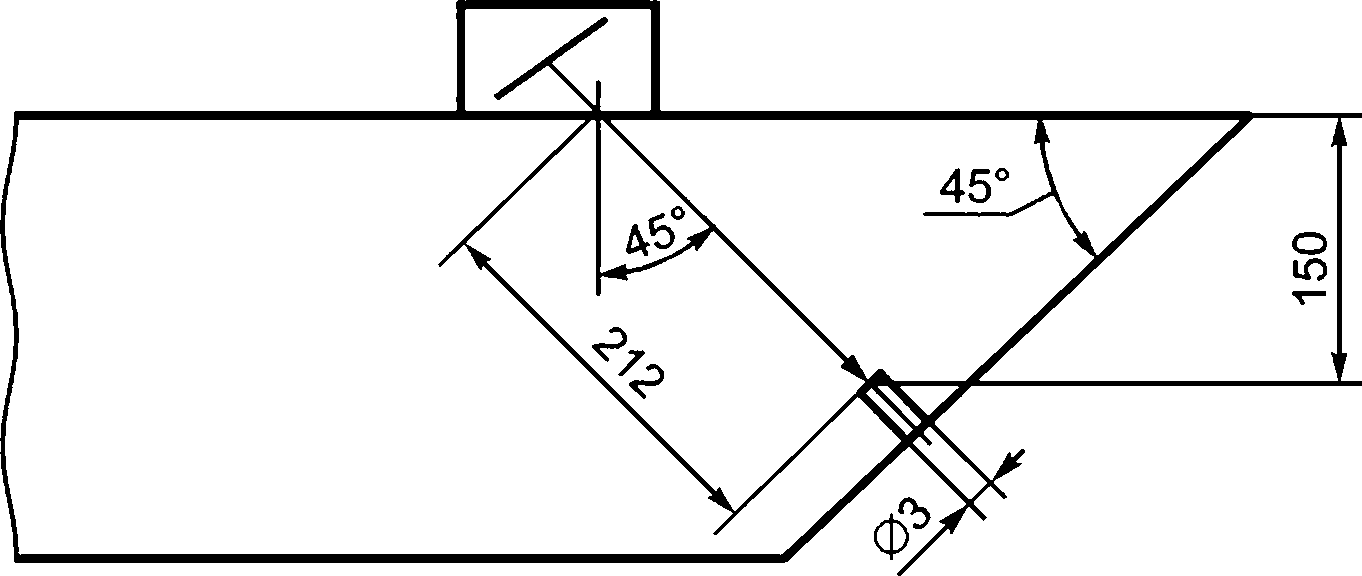
Рисунок Н.10 — Получение сигнала на НО с плоскодонными отражателями
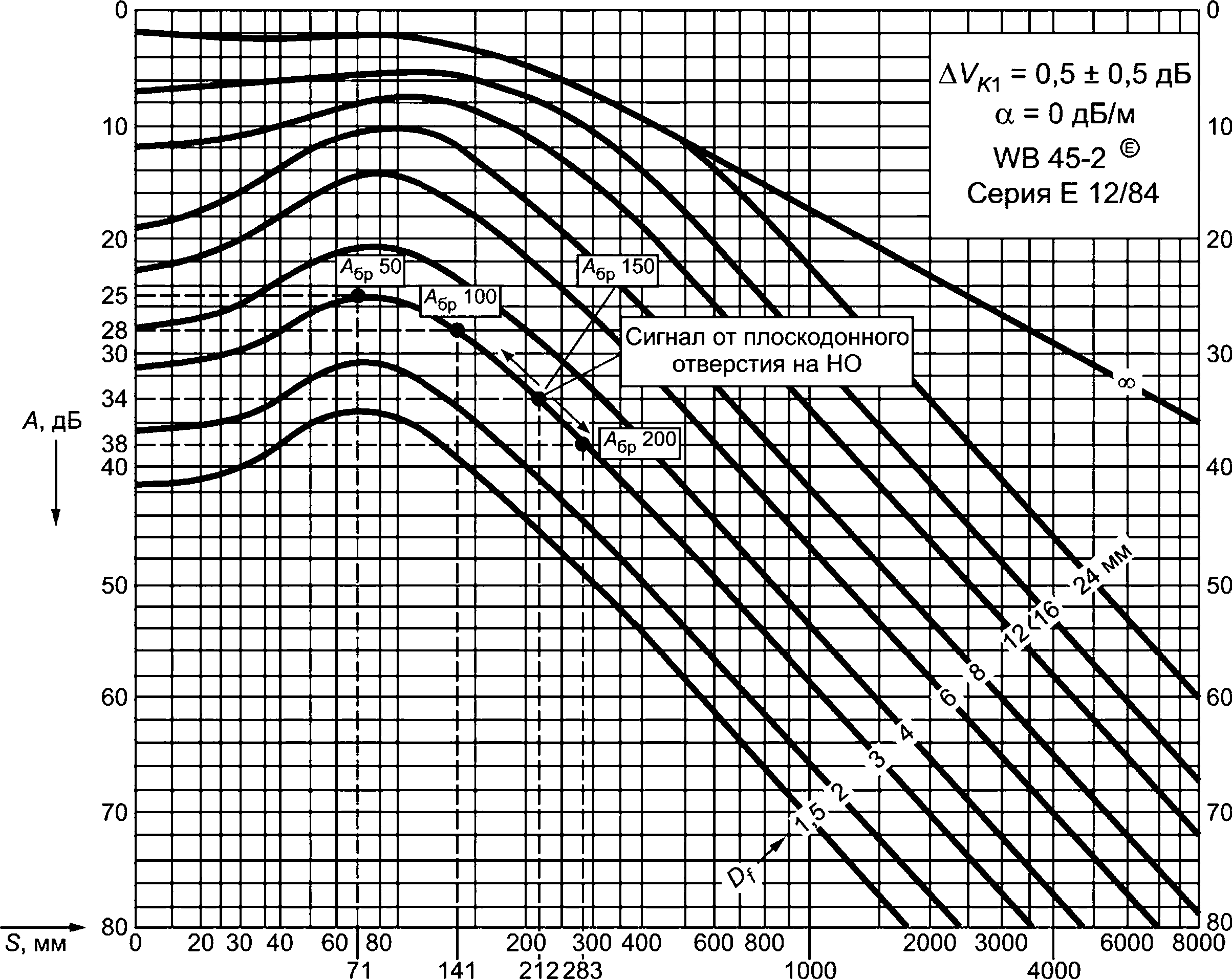
Рисунок Н.11 — Настройка чувствительности дефектоскопа с использованием AVG-диаграммы и НО с плоскодонными отражателями
Таблица Н.З
Гпубина, мм | 50 | 100 | 150 | 200 |
Браковочный уровень, дБ | 21 | 24 | 30 | 34 |
Контрольный уровень, дБ | 27 | 30 | 36 | 40 |
Поисковый уровень, дБ | 33 | 36 | 42 | 46 |
При УЗК в случае обнаружения отражателя на глубине, отличной от 200, 150, 100, 50 мм, необходимо определить значение амплитуды по AVG-кривой аналогично перечисленным глубинам.
Н.2.9 Работа с AVG-диаграммами при УЗК ПРС
Н.2.9.1 На рисунке Н.12 приведена AVG-диаграмма для ПЭП SEB 2Н (2 МГц, 0°, размер ПЭ — 7*18 мм). По оси абсцисс внизу отложены значения расстояния до несплошности по лучу S, мм (лучевая дальность). По оси ординат отложены значения амплитуд эхо-сигналов в децибелах. В этих координатах построены графики зависимости амплитуд сигналов от плоскодонных отражателей. Диаметры плоскодонных отражателей указаны справа на этих графиках.
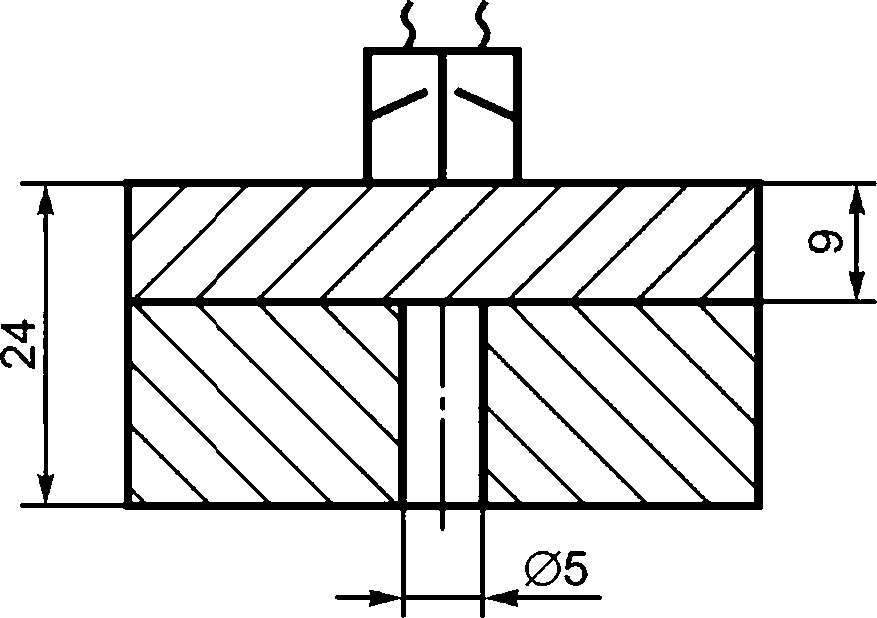
Рисунок Н.12 — НО для УЗК металла антикоррозионной наплавленной поверхности с плоскодонным отражателем
Н.2.9.2 В качестве опорного сигнала может использоваться сигнал от плоскодонного отражателя или донной поверхности [нормальное (90°) падение УЗ-волны на поверхность].
Пример 8 — При УЗК зоны сплавления металла антикоррозионной наплавленной поверхности с металлом СС сосуда со стороны наплавленной поверхности выявили несплошность на глубине 9 мм с амплитудой сигнала от несплошности на 2 дБ, превышающей браковочный уровень S6p = 20 мм2. Уровень фиксации $фикс - Ю мм2. В качестве опорного сигнала использовался сигнал от плоскодонного отражателя площадью 20 мм2 в НО, расположенного на глубине 9 мм (рисунок Н.12). Необходимо определить эквивалентную площадь несплошности.
Определяют значение сигнала от плоскодонного отражателя на НО: Апл дн0~ Вычисляют значение амплитуды на AVG-диаграмме для отражателя площадью 20 мм2 (d = 5 мм) (рисунок Н. 13) на глубине 9 мм Аплдн0 =13,5 дБ. Значение амплитуды сигнала от плоскодонного отражателя 13,5 дБ на AVG-диаграмме соответствует Апл ^но~^ &Б на дефектоскопе. Значение амплитуды 20 дБ на дефектоскопе является браковочным уровнем.
Поскольку амплитуда сигнала от несплошности превышает браковочный уровень на 2 дБ, необходимо на AVG-диаграмме отложить вверх 2 дБ от найденного значения амплитуды 13,5 дБ на глубине 9 мм (рисунок Н.13). Таким образом, результирующее значение амплитуды сигнала от несплошности на AVG-диаграмме: 13,5 -2 = 11,5 дБ. С учетом близлежащих на AVG-диаграмме линий вычисляют S3Ke = а 28,3 ММ2 (дэкв а 6 мм).
Н.2.10 Работа с АРД-диаграммой при контроле по схеме «тандем»
Н.2.10.1 В качестве опорного сигнала Ам (Аоп), дБ, используется амплитуда эхо-сигнала, полученного непосредственно на ОК при прохождении УЗ-луча от излучающего ПЭП к развернутому к нему приемному ПЭП через отражение от дна ОК (рисунок Н.14).
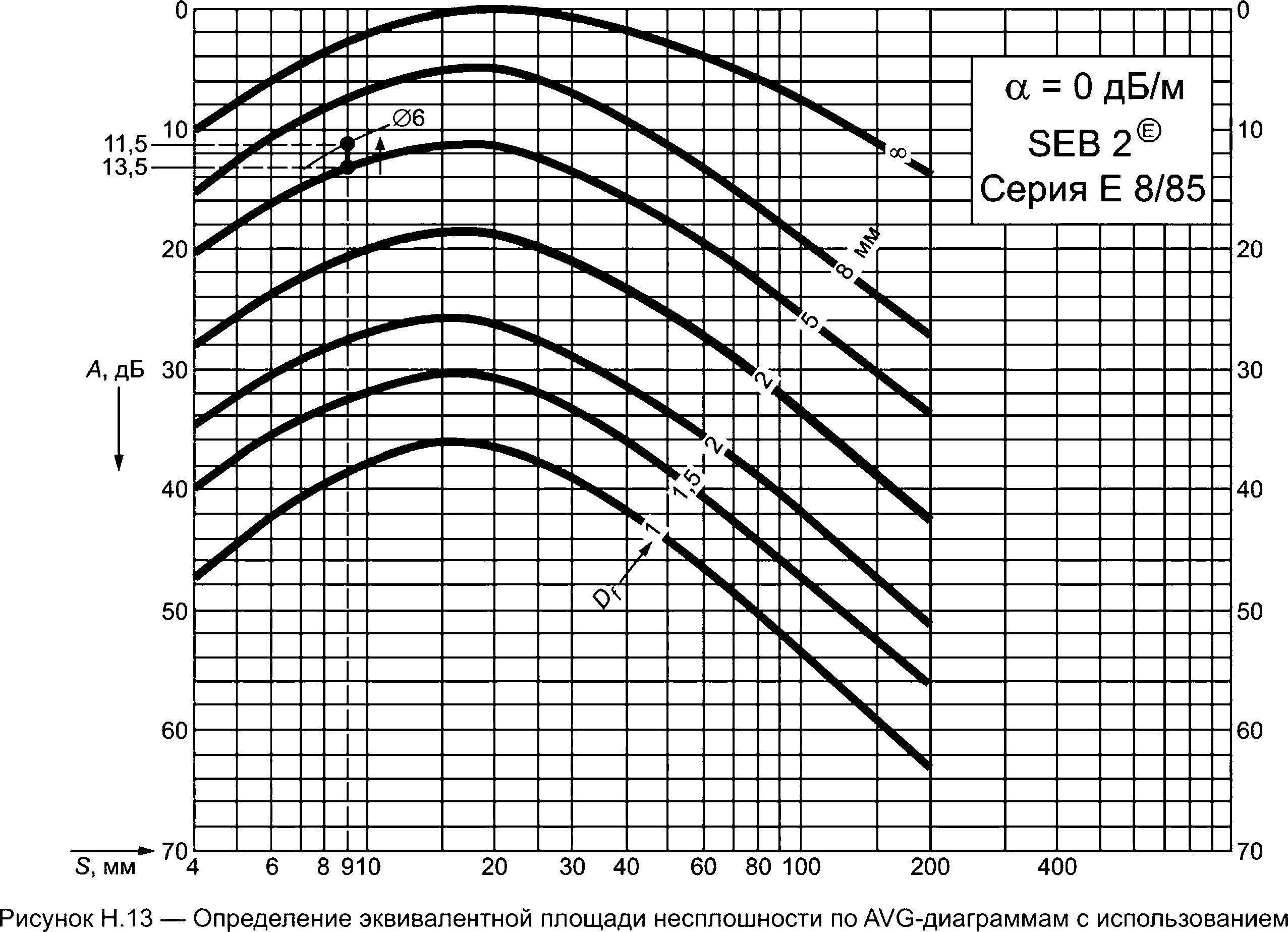
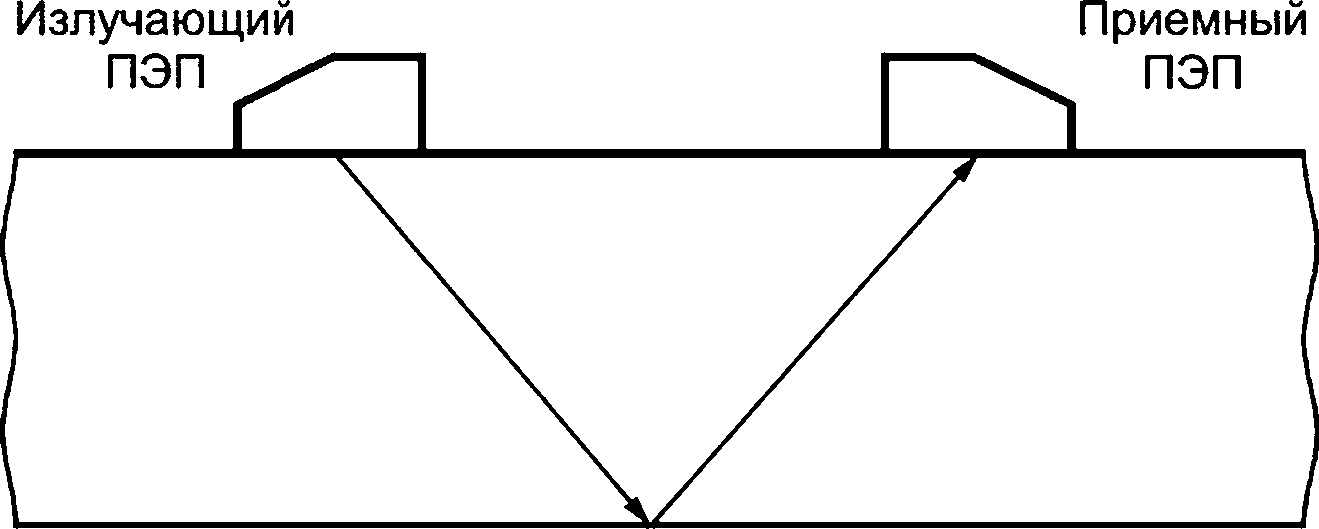
Рисунок Н.14 — Схема оценки опорного сигнала Дм (Доп), дБ
Допускается определение опорного сигнала по схеме, представленной на рисунке Н.15.
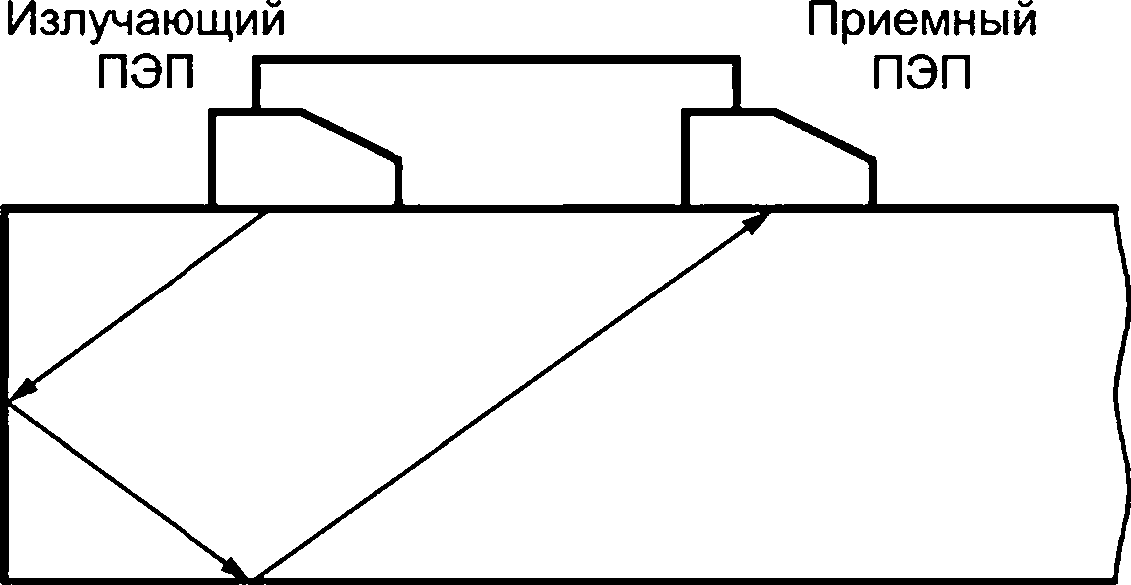
Рисунок Н.15 — Схема оценки опорного сигнала Ах (Аоп), дБ
Н.2.10.2 При использовании АРД-диаграмм при проведении УЗК по схеме «тандем» учет затухания УЗ не требуется.
Н.2.10.3 Настройка чувствительности с помощью АРД-диаграммы при контроле по схеме «тандем»
Н.2.10.3.1 В соответствии со схемой, приведенной на рисунке Н.14, определяют амплитуду опорного сигнала на ОК Аоп, дБ.
Н.2.10.3.2 На АРД-диаграмме при проведении УЗК по схеме «тандем» находят точку, соответствующую толщине свариваемых деталей. От этой точки через линию, соответствующую выбранному ПЭП, проводят прямую до пересечения с линией, соответствующей эквивалентному диаметру отражателя (браковочная чувствительность, определена КД). Далее проводят вертикальную прямую вверх и получают значение поправки чувствительности по АРД-диаграмме АД дБ. Значение браковочного уровня чувствительности, дБ, вычисляют по формуле
(Н.1)
^бр ^оп
Чувствительность фиксации на 6 дБ выше браковочного уровня, поисковая чувствительность — на 12 дБ выше браковочного уровня.
Пример 9 — При УЗК СС по схеме «тандем» ПЭП П121-2,5-50° (ПЭ 12 х 16 мм) с толщиной свариваемых деталей 60 мм необходимо настроить браковочную чувствительность S6p = 7,0 мм2, чувствительность фиксации и поисковую чувствительность с использованием АРД-диаграмме при проведении УЗК по схеме «тандем» (рисунок Н.16).
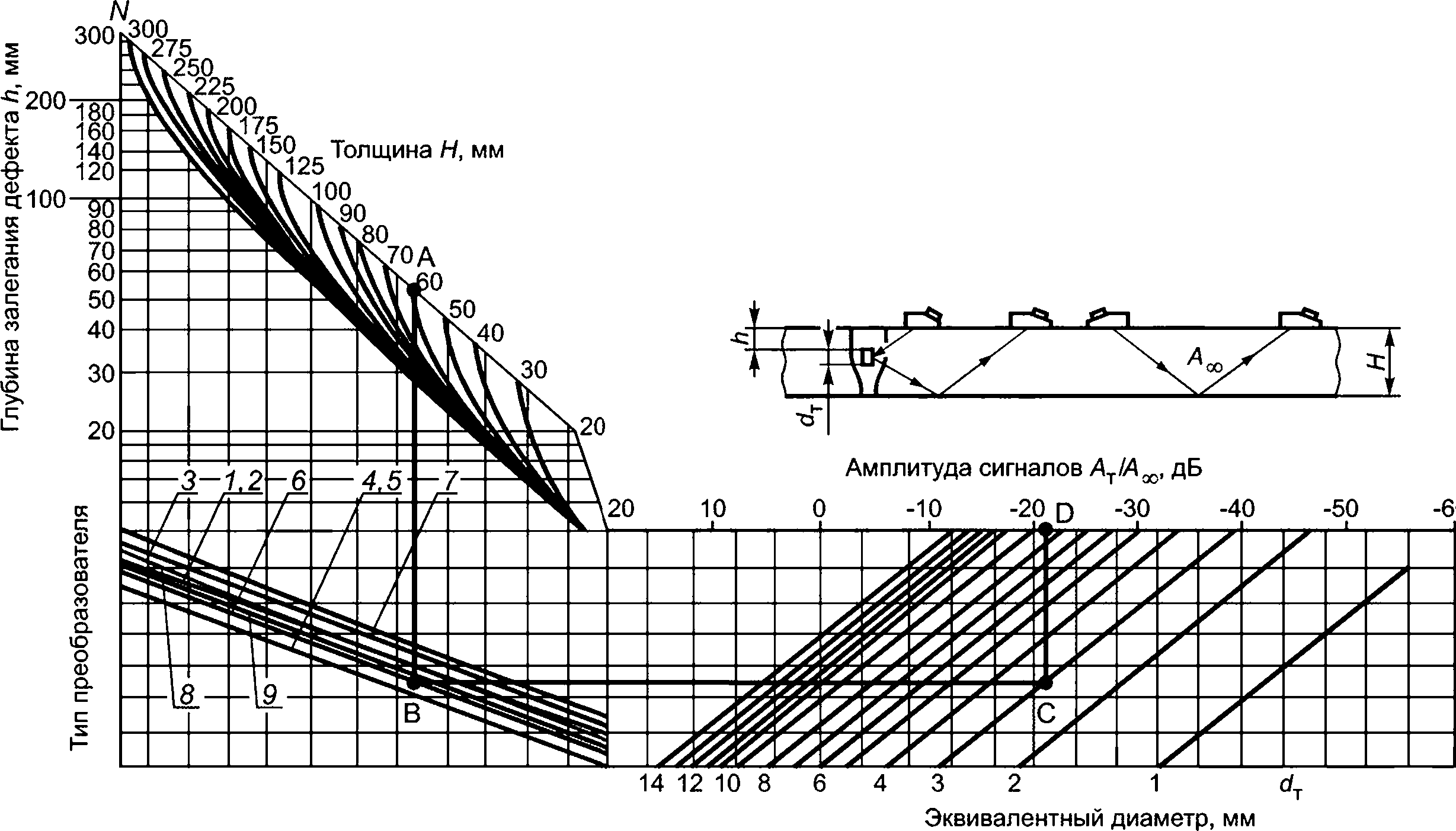
Рисунок Н.16 — Настройка чувствительности по АРД-диаграмме при проведении УЗК по схеме «тандем» для П121-2,5-50° (ПЭ 012 х 16 мм)
На ОК в соответствии со схемой (см. рисунок Н.14) получают опорный сигнал Аоп = 16 дБ.
Из точки А, соответствующей толщине 60 мм, следует провести вертикальную прямую АВ вниз до пересечения с линией 6 (для заданного ПЭП). Далее от точки В провести горизонтальную прямую ВС до пересечения с линией дэкв = 3 мм (Ээкв = 7,0 мм2). Из точки С провести вертикальную прямую СД. Полученное значение ЛА = -22 дБ является поправкой по АРД-диаграмме при проведении УЗК по схеме «тандем».
Браковочный уровень чувствительности для толщины 60 мм A6jJ -16 + 22-38 дБ.
Чувствительность фиксации на 6 дБ выше уровня браковочной чувствительности. Поисковая чувствительность на 12 дБ выше браковочной чувствительности.
Н.З АРД-шкалы и работа с ними
Н.3.1 АРД-шкала является одним из способов настройки чувствительности дефектоскопа. АРД-шкала построена для конкретных типов ПЭП с учетом ранее представленных формул акустического тракта и их экспериментальной проверки. Амплитудное значение эхо-сигнала определяют как разность между опорным сигналом и сигналом от отражателя.
Н.З.2 Общий вид АРД-шкалы представлен на рисунке Н.17.
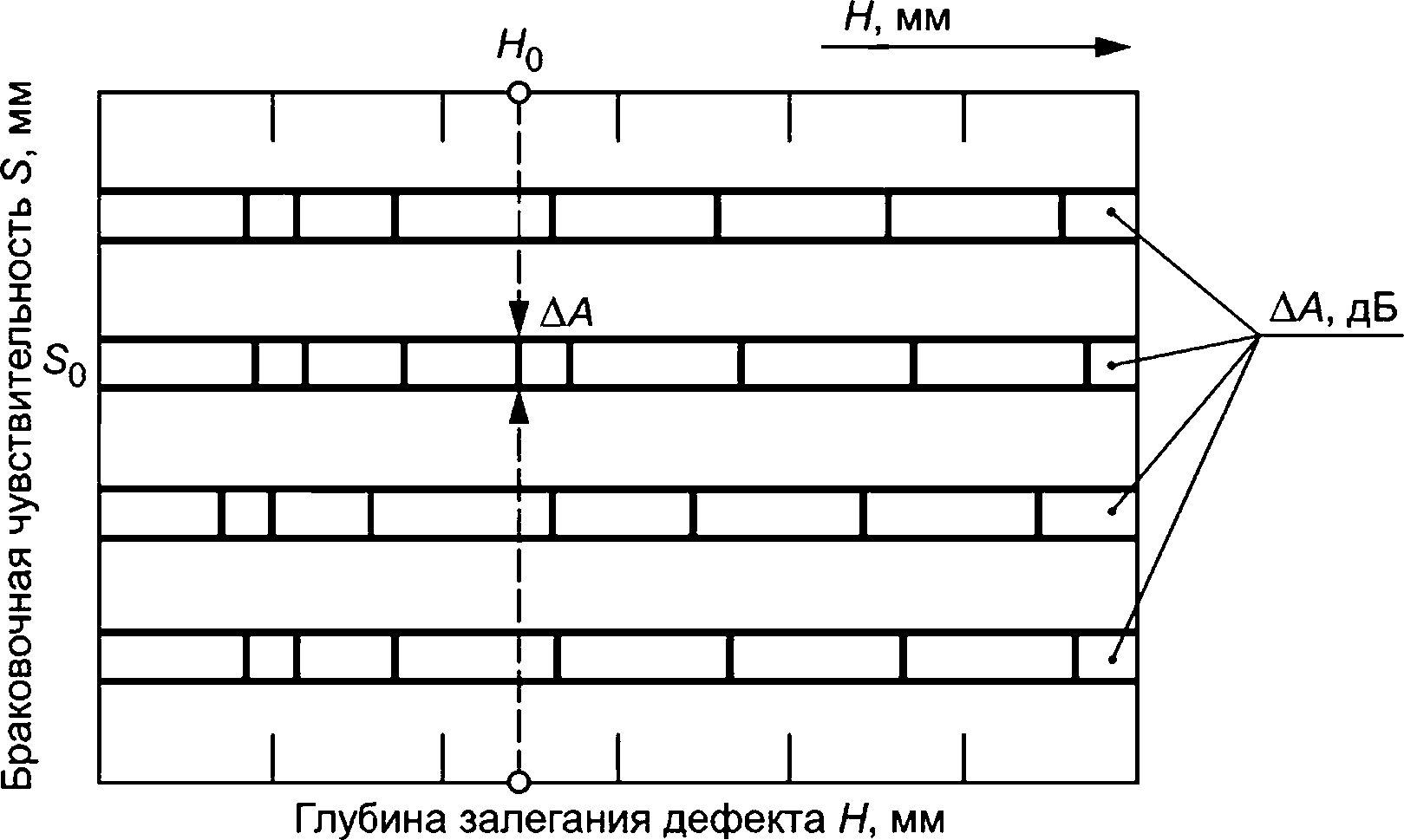
Абр, дБ — амплитуда эхо-сигнала, соответствующая браковочной чувствительности S6p;
Аоп, дБ — амплитуда опорного эхо-сигнала от бокового цилиндрического отражателя 0 6 мм в мере СО-2; ДА = Абр - Аоп, дБ — величина поправки чувствительности по АРД-шкале
Рисунок Н.17 — Общий вид АРД-шкалы и принцип работы с ней
Н.3.3 Настройка чувствительности с использованием АРД-шкал
Н.3.3.1 Исходя из параметров СС в соответствии с таблицами 1—3 выбирают ПЭП.
Н.3.3.2 Устанавливают ПЭП на меру СО-2 (рисунок Н.18). Находят максимум опорного эхо-сигнала от бокового цилиндрического отражателя диаметром 6 мм (глубина расположения отражателя 15 мм или 44 мм в зависимости от указаний на АРД-шкале) — опорный уровень чувствительности Аоп, дБ.
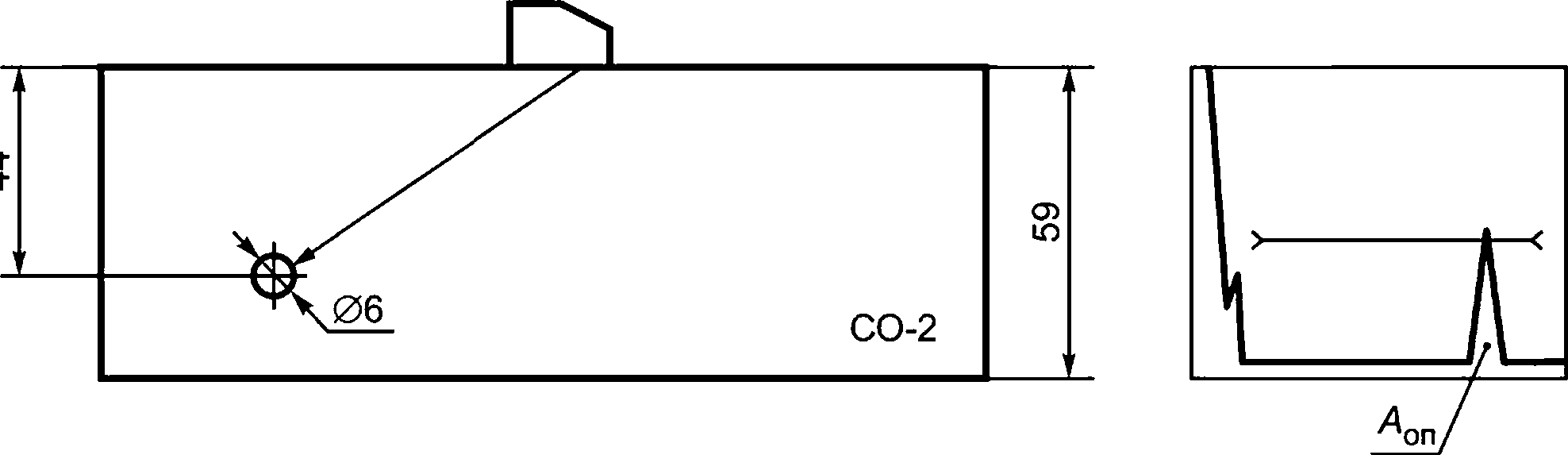
Рисунок Н.18 — Получение опорного сигнала на мере СО-2
Н.3.3.3 В зависимости от требуемой толщины определяют браковочный уровень и уровень фиксации (с учетом поправки чувствительности по АРД-шкале и, при необходимости, поправки на шероховатость поверхности). При этом S6p, мм2, определяют в соответствии с нормами для толщины контролируемого СС, глубину залегания определяют как максимально возможную в данном СС с учетом схемы прозвучивания (прямой и однократно отраженный луч). Значение браковочного уровня чувствительности вычисляют по формуле (Н.1).
Чувствительность фиксации на 6 дБ выше браковочного уровня, поисковая чувствительность — на 12 дБ выше браковочного уровня.
Пример 10 — При УЗК СС с толщиной свариваемых деталей 30 мм ПЭП П121-2,5-65 прямым и однократно отраженным лучами необходимо настроить браковочную чувствительность S6p = 5 мм2, чувствительность фиксации и поисковую чувствительность с использованием АРД-шкалы (рисунок Н.19).
Получаем опорный сигнал от бокового цилиндрического отражателя диаметром 6 мм в мере СО-2 - Аоп = 38 дБ. Проведя замер разницы шероховатости поверхности СС и меры СО-2, получили поправку на шероховатость 4 дБ. Для П121-2,5-65 получаем амплитуды, соответствующие браковочному уровню Абр с учетом поправок на шероховатость поверхности ААшер и поправки чувствительности по АРД-шкале ЛА для толщины 30 мм (контроль прямым лучом) и 60 мм (контроль однократно отраженным лучом).
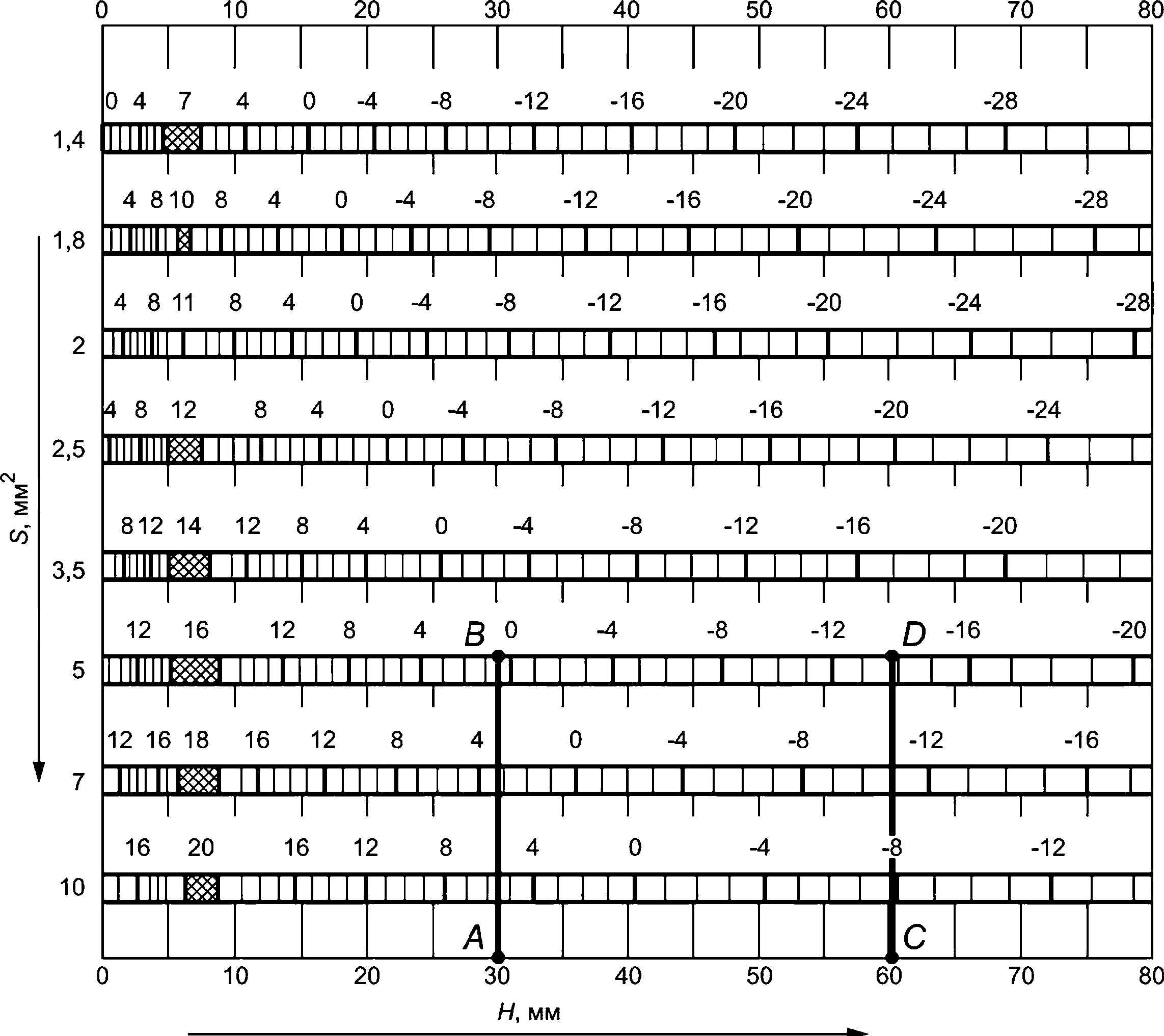
Рисунок Н.19 — АРД-шкала для ПЭП П121-2,5-65° (ПЭ 012 мм). Опорный сигнал от цилиндрического отражателя диаметром 6 мм на глубине 44 мм в мере СО-2 соответствует уровню 0 дБ
На шкале глубины залегания находим точку А, соответствующую 30 мм. От нее до пересечения с прямой, соответствующей эквивалентной площади 5 мм2 проводим прямую АВ, где точка В — значение поправки ЛА = 0,5 дБ по АРД-шкале для данной глубины. Получаем значение браковочной чувствительности Абр = 38 - 0,5 + 4 = 41,5 дБ. Чувствительность фиксации выше браковочной чувствительности на 6 дБ, поисковая чувствительность выше браковочной на 12 дБ.
На шкале глубины залегания находим точку С, соответствующую 60 мм. От нее до пересечения с прямой, соответствующей эквивалентной площади 5 мм2 проводим прямую CD, где точка D — значение поправки ЛА - -14 дБ по АРД-шкале для данной глубины. Получаем значение браковочной чувствительности Абр = 38 + 14 + 4 = 56 дБ. Чувствительность фиксации выше браковочной чувствительности на 6 дБ, поисковая чувствительность выше браковочной на 12 дБ.
Н.4 Связь АРД-диаграмм для бокового цилиндрического отражателя и плоскодонного отражателя
Н.4.1 Эхо-сигналы Р и Р' от плоскодонного отражателя и бокового цилиндрического отражателя вычисляют по формулам (Н.2) и (Н.З) акустического тракта:
- для плоскодонного отражателя
Р' _ $aSb- cosa e-2(r8+r282) Р X2 (г + r2)2 -cosp
(Н.2)
где Sa— площадь плоскодонного отражателя, мм2;
Sb— площадь ПЭ, мм2;
а — угол ввода, град;
X — длина волны, мм;
г — расстояние в металле от точки ввода УЗ до отражателя, мм;
С,пр cos а
— приведенное расстояние в призме, мм; вычисляется по формуле г2 - Хл ■——г-----,
2 C^cosp
где х1 — длина акустической оси в призме, мм; CznP — скорость продольных волн в призме, м/с; Ctok — скорость поперечных волн в металле, м/с; а — угол ввода, град; р — угол призмы, град;
Р — угол призмы, град;
5 — коэффициент затухания в металле, Нп/мм;
52 — коэффициент затухания в призме, Нп/мм;
- для бокового цилиндрического отражателя
Р' _ Sa ■ cosa j d 2(r5+r?8?) P X cosp ^8-(r + r2)3
(H.3)
где d — диаметр бокового цилиндрического отражателя, мм.
Выполняют расчет для несплошностей, расположенных на одинаковых расстояниях (глубинах).
Н.4.2 Пересчет плоскодонного отражателя в боковой цилиндрический отражатель, расположенных на одинаковом расстоянии, проводят путем приравнивания формул акустических трактов для плоскодонного и бокового цилиндрического отражателей, расположенных на одинаковом расстоянии — формулы (Н.4)—(Н.6):
Sn _ 1 I du X2(r + r3)2 х ^8(r + r3)3’
(Н.4)
где Sn — площадь плоскодонного отражателя, мм2;
X — длина волны, мм;
г — путь по лучу до несплошности, мм;
г3 — путь в призме, мм;
dy — диаметр бокового цилиндрического отражателя, мм;
Х2-(г + г3)4 8-(г + Гз)3 (Н-5) (Н.6)
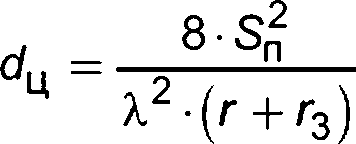
Н.4.3 Расчет для несплошностей, расположенных на разных расстояниях, производят путем приравнивания формул акустических трактов [формулы (Н.7)—(Н.9)]:
^•(Гп + 'з)2
1. I
V8-(г6 + г3)3
(Н.7)
где гп — расстояние от поверхности до плоскодонного отражателя, мм;
гб — расстояние от поверхности до бокового цилиндрического отражателя, мм;
Х2-(гп+г3)4 8-(г6 + г3)3
(Н.8)
С/ц =
8 Sn2-(r6+r3)3 ^2-(''п+'’з)4
(Н.9)
Н.4.4 Для определения размера бокового цилиндрического отражателя, эхо-сигнал от которого равен эхо-сигналу от плоскодонного отражателя с известным размером и расположенного на той же глубине, можно использовать соотношения, построенные для конкретного ПЭП.
Пример 11 — Необходимо определить размер бокового цилиндрического отражателя для настройки чувствительности при УЗК СС с толщиной свариваемых деталей 70 мм. УЗК выполняется ПЭП WB 45-2 (2 МГц, 45°, размер ПЭ — 20 к 22 мм). Браковочный уровень равен S6p = 15 мм2.
Вычисляют длину волны по формуле
(Н.10)
где Ct — скорость поперечной волны (3240 м/с); f— номинальная частота ПЭП, МГц.
Вычисляют расстояние по лучу г, мм, по формуле
Н cos 45
(Н.11)
Затем подставляют полученные значения в формулу для отражателей, расположенных на одинаковом расстоянии по формуле
dn =
8S2
%2-(г + г3)
Таким образом, боковой цилиндрический отражатель, расположенный на глубине 70 мм диаметром бц- 6 мм, имеет такую же отражательную способность, как и плоскодонный отражатель площадью Ээкв = 15 мм2 (d = 4,4 мм).
Н.5 Пересчет плоскодонного отражателя в зарубку
Н.5.1 При проведении УЗК СС с толщиной свариваемых деталей до 12 мм включительно настройку чувствительности следует выполнять по НО с угловыми отражателями (зарубками). При этом, браковочная чувствительность и чувствительность фиксации, как правило, заданы через эквивалентную площадь плоскодонного отражателя.
Н.5.2 Общий вид НО с угловым отражателем (зарубкой) приведен на рисунке Н.20. Необходимым условием является то, что ширина зарубки /, мм, и высота h, мм, должны быть больше длины УЗ-волны, а отношение высоты зарубки к ее ширине должно быть от 0,5 до 4,0.
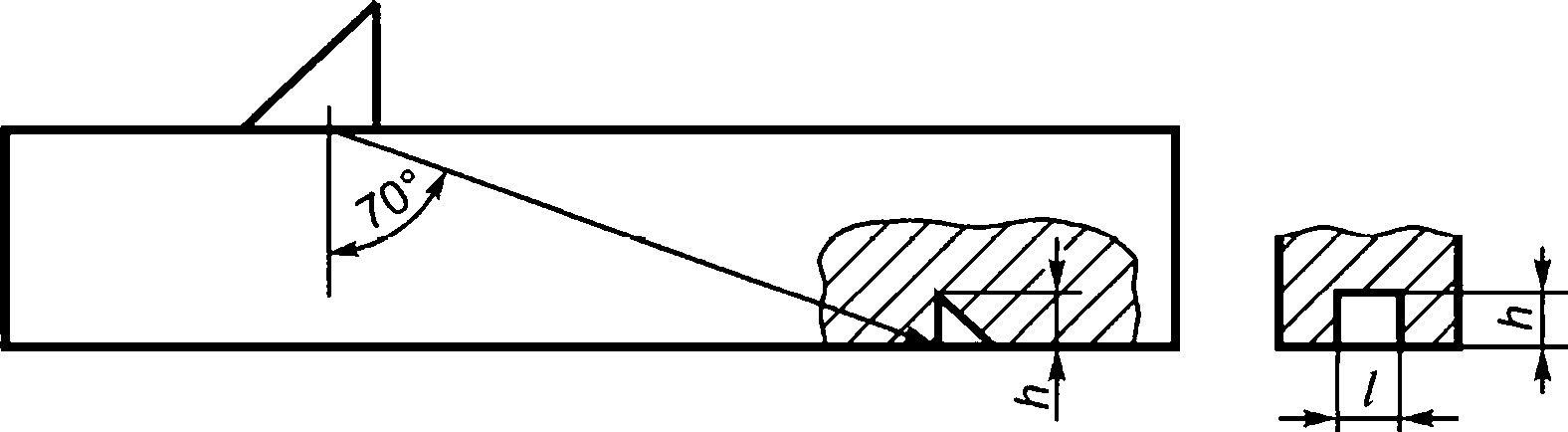
Рисунок Н.20 — Настройка на НО с зарубкой
Н.5.3 Площадь углового отражателя (зарубки) вычисляется по формуле
S3 = / • h,
(Н.13)
где I — ширина зарубки, мм; h — высота зарубки, мм.
Н.5.4 Площади углового отражателя (зарубки) и плоскодонного отражателя связаны между собой формулой (Н.14) через коэффициент Л/ (рисунок Н.21) — коэффициент для стали, алюминия и его сплавов, титана и его сплавов, зависящий от угла е, град, и угла ввода УЗ а, град.
(Н.14)
S3=—, 3 N
где S3 — площадь углового отражателя (зарубки), мм х мм; Sn — площадь плоскодонного отражателя, мм2.
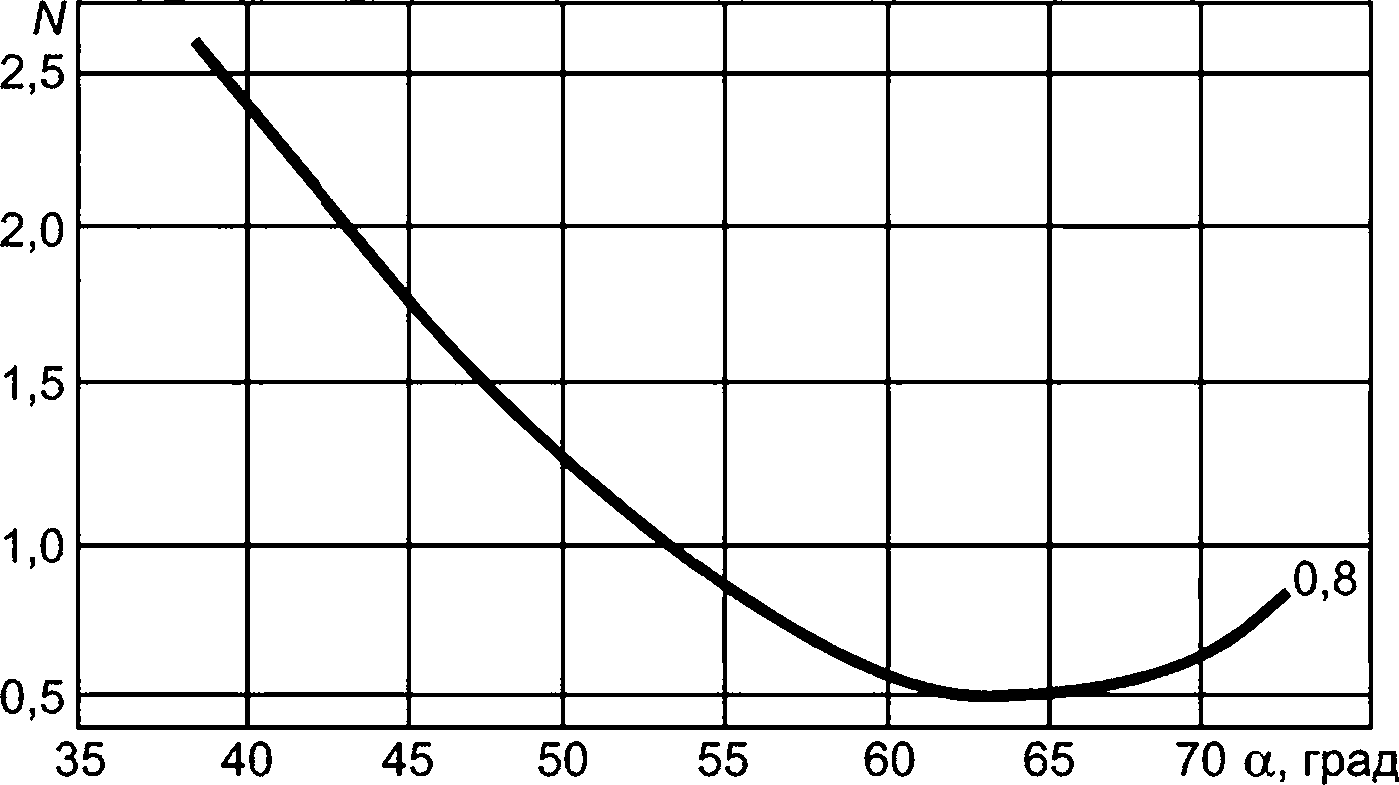
Рисунок Н.21 — Зависимость N = f (а) для стали, алюминия и его сплавов, титана и его сплавов
Пример 12 — При УЗК СС с толщиной свариваемых деталей 12 мм для настройки браковочной чувствительности S6p = 7 мм2 следует использовать НО с зарубкой. Необходимо определить размер зарубки, если УЗК выполняют ПЭП MWB70-4 (4 МГц, 70°, размер ПЭ — 8x9 мм).
По рисунку Н.21 с учетом угла ввода 70° вычисляют коэффициент N = 0,65.
S 7
По формуле (Н.14) вычисляют площадь зарубки S3 = —0- = —— = 10,8 мм2.
N 0,65
Так как отношение высоты зарубки к ее ширине должно быть в интервале от 0,5 до 4,0, принимают высоту зарубки h - 3,6 мм, тогда длина зарубки составляет 1 = 3 мм. Размеры зарубки — 3 х згб, мм х мм.
Приложение П (обязательное)
Методика ультразвукового контроля сварных соединений сферических корпусов задвижек трубопроводов
П.1 Настоящая методика определяет порядок и технологию УЗК диаметральных СС сферических корпусов задвижек из сталей марок 15ГС, 15X1 МФ, 12Х1М1Ф с диаметрами условного прохода DN100, 125, 150, 175, 200 и 250 мм.
П.2 При УЗК применяют НП с углом ввода от 40° до 50° с частотами от 1,8 до 2,5 МГц. ПЭП должны иметь кривизну контактной поверхности, соответствующую кривизне поверхности ОК в зоне контроля.
П.З Проводят операции в соответствии с 7.4.
П.4 Для осуществления технологических операций УЗК используют НО, изготовленные по рисунку П.1. Параметры НО вычисляют по формулам
Ф = arccos
(П.1)
где <р — угол между перпендикуляром к внешней поверхности ОК (радиус) и торцом НО, град (рисунок П.1); а — угол ввода, град;
Н — номинальная толщина свариваемых деталей, мм;
R — радиус ОК, мм;
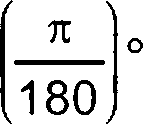
(П.2)
где Z — расстояние (по дуге) между точкой выхода и проекцией на внешнюю поверхность центра плоскодонного отражателя, мм (рисунок П.1).
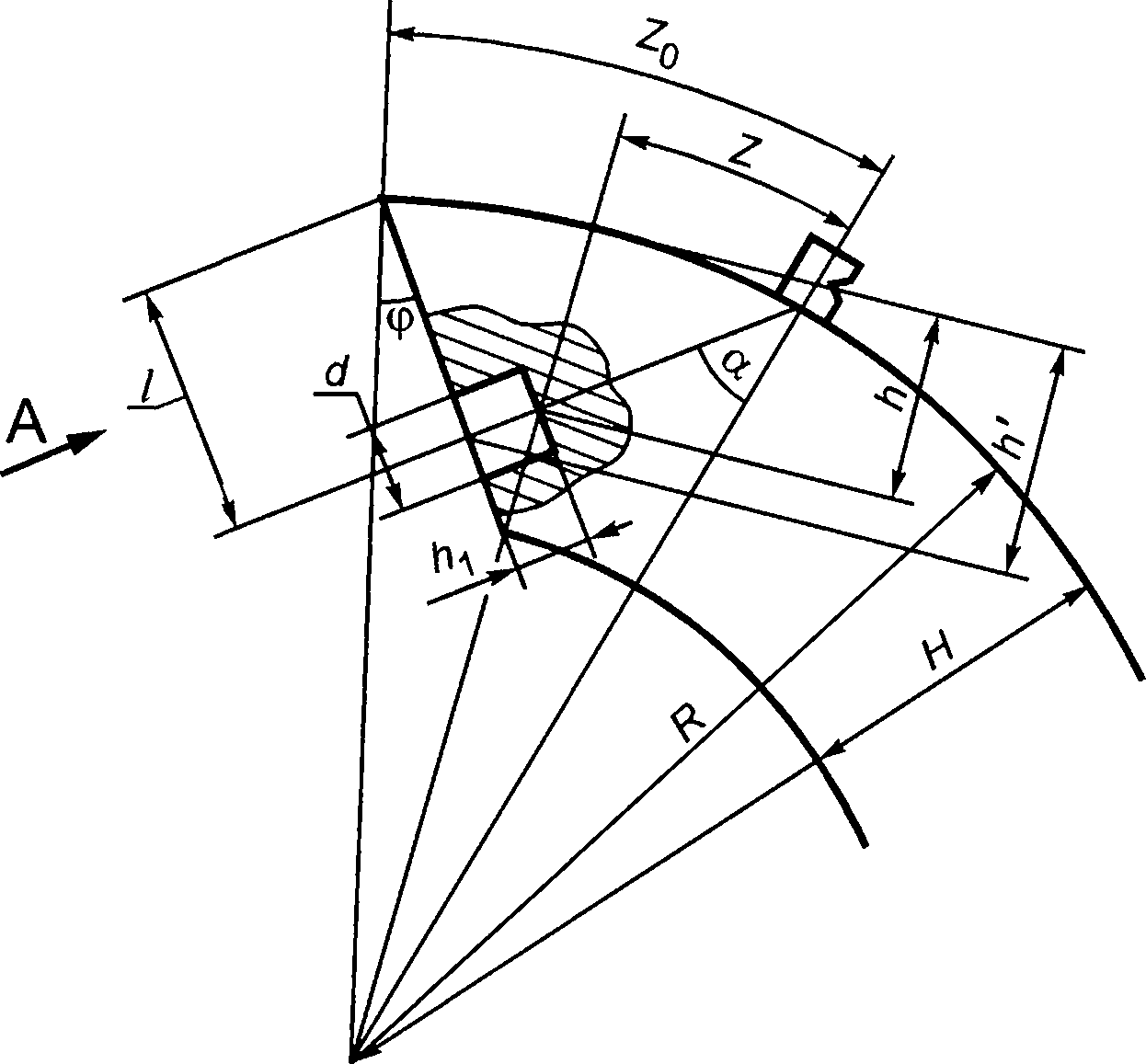
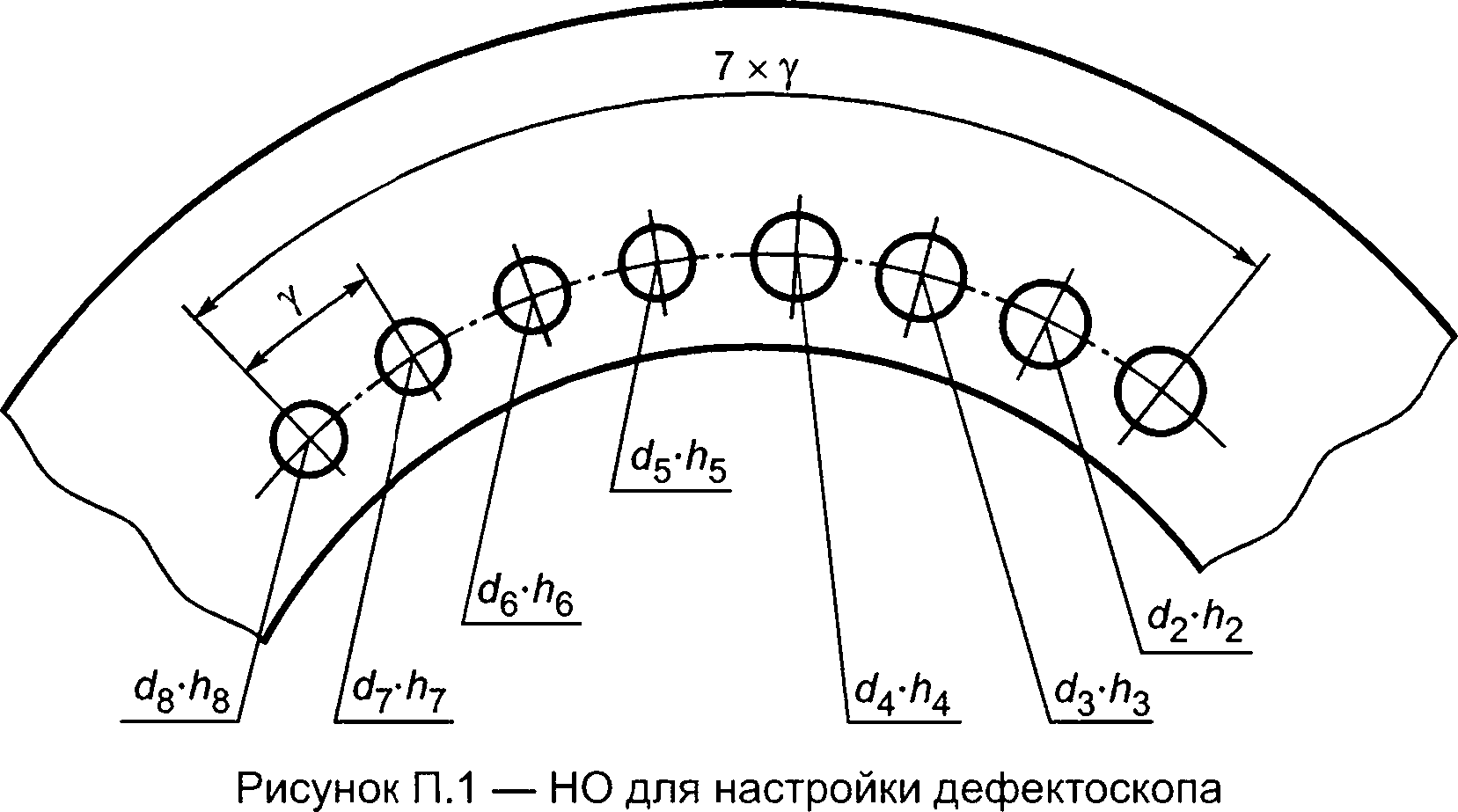
П.5 Для УЗК СС корпусов задвижек параметры НО представлены в таблице П.1.
Диаметр d плоскодонных отражателей выбирают в соответствии с требованиями федеральных норм и правил в области использования атомной энергии, документами по стандартизации, КД.
Таблица П.1 — Параметры НО для проведения УЗК СС корпусов задвижек
Параметр | Угол ввода а, град | |||||
40 | 50 | |||||
Диаметр условного прохода | ||||||
DN100-150 | DN175-200 | DN250 | DN100-150 | DN175-200 | DN250 | |
R, мм | 135 | 230 | 250 | 135 | 230 | 250 |
/7, мм | 30 | 45 | 72 | 30 | 45 | 72 |
Ф, град | 30 | 33 | 25 | 14 | 22 | 7 |
Г, град | 7 | 7 | 7 | 7 | 7 | 7 |
Zo, мм | 46 | 73 | 118 | 58 | 80 | 150 |
/, мм | 28 | 48 | 70 | 26 | 42 | 60 |
П.6 УЗК проводят путем сканирования ПЭП по сферической поверхности, чистота обработки поверхности должна быть не более Ra 6,3 мкм (Rz 40 мкм) по ГОСТ 2789. Ширина подготовленной под УЗК зоны с каждой стороны шва должна соотвествовать требованиям ТКК.
П.7 Дефектоскопы настраивают с учетом кривизны поверхности задвижек для определения глубины h несплошности и расстояния Z (по сфере) (рисунок П.1), значения h и Z вычисляют по формуле (П.2).
П.8 Настройку глубиномера и диапазона развертки дефектоскопов проводят по плоскодонным отражателям в НО (рисунок П.1).
П.9 Не допускается использование ПЭП, если полученные значения h и Z отличаются от истинных значений h и Z отражателей в НО более чем на 2 мм.
П.10 Настройку чувствительности дефектоскопа проводят по плоскодонным отражателям в НО. Браковочный уровень устанавливают по отражателям в НО (рисунок П.1), с наибольшей площадью.
П.11 При обнаружении несплошности ее полученные характеристики следует сравнивать с характеристиками от плоскодонного отражателя, расположенного на глубине, наиболее близкой к глубине обнаруженной несплошности.
П.12 УЗК проводят прямым лучом с двух сторон СС двумя ПЭП с выбранным углом ввода.
ПИЗ Проведение УЗК и определение характеристик несплошностей осуществляют в соответствии с положениями настоящего стандарта.
Приложение Р (справочное)
Особенности ультразвукового контроля сварных соединений различных конструкций
Р.1 Стыковые сварные соединения
Р.1.1 Особенностью стыковых СС с V-образной разделкой кромок без подкладных колец является наличие неровностей в корне шва — превышение проплава металла и смещений кромок. Отраженные от неровностей сигналы при УЗК прямым лучом совпадают по времени с сигналами, отраженными от надкорневых несплошностей, обнаруженных однократно отраженным лучом.
На рисунке Р.1 приведена схема обнаружения надкорневых несплошностей и неровностей корня шва. Участок развертки «а» — зона появления эхо-сигналов от несплошностей, расположенных в корне шва. Участок «х» — зона появления эхо-сигналов как от несплошностей, расположенных непосредственно над корнем шва, так и от превышения проплава (зона совпадения). Участок «б» — зона появления эхо-сигналов, отраженных от несплошностей в верхней части шва.
Примечание — Корневой частью соединения считают слой толщиной 1/ЗН, но не более 5 мм, считая от внутренней поверхности СС.
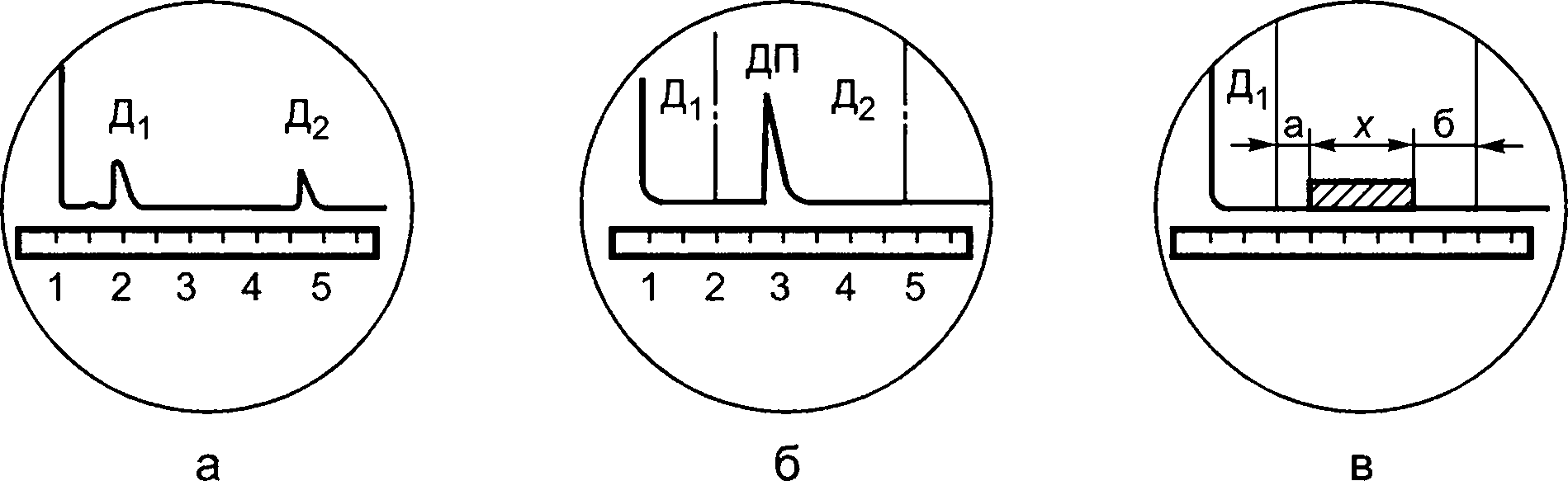

а — настройка диапазона развертки: Д1 — сигнал от нижней зарубки; Д2 — сигнал от верхней зарубки; б — обнаружение сигнала от надкорневых несплошностей и провисаний: Д — сигнал от несплошности; П — сигнал от провисания, совпадающий с сигналом Д по координате; в — разметка экрана после диапазона развертки
Рисунок Р.1 — Схема УЗК СС труб толщиной менее 15 мм
Р.1.2 Смещение кромок стыкуемых труб отличают от несплошности в корне шва по следующим признакам:
- эхо-сигнал от смещения расположен на экране там же, где и корневые несплошности;
- смещение кромок из-за разной толщины стыкуемых труб характеризуется наличием сигнала при прозвучи-вании только с одной стороны шва по всему периметру или на большей части периметра. В этом случае следует определить толщину стенок труб;
- смещение кромок из-за несоосности стыкуемых труб характеризуется появлением сигналов при прозвучи-вании с разных сторон шва в диаметрально противоположных точках (рисунок Р.2);
- амплитуда эхо-сигнала при прозвучивании с одной стороны обычно выше первого браковочного уровня, а с другой — ниже контрольного.
Р.1.3 Превышение проплава металла в корне шва отличают от несплошности по следующему признаку: эхо-сигналы от превышения проплава имеют как различные координаты на экране, так и амплитуды при прозвучивании с разных сторон шва.
Кроме того, для СС с толщиной свариваемых деталей менее 15 мм используют дополнительные признаки:
- эхо-сигнал от превышения проплава расположен на экране в зоне «х»;
- превышение проплава обычно выявляют при меньшем расстоянии между ПЭП и швом, чем при выявлении надкорневых несплошностей;
- образование превышения проплава наиболее вероятно на участках, выполненных сваркой в нижнем положении. В горизонтальных стыках провисания располагаются более равномерно и образуются реже, чем в вертикальных стыках. Величину превышения проплава определяют по методике, разработанной организацией-изготовителем и прошедшей оценку соответствия в форме испытаний.
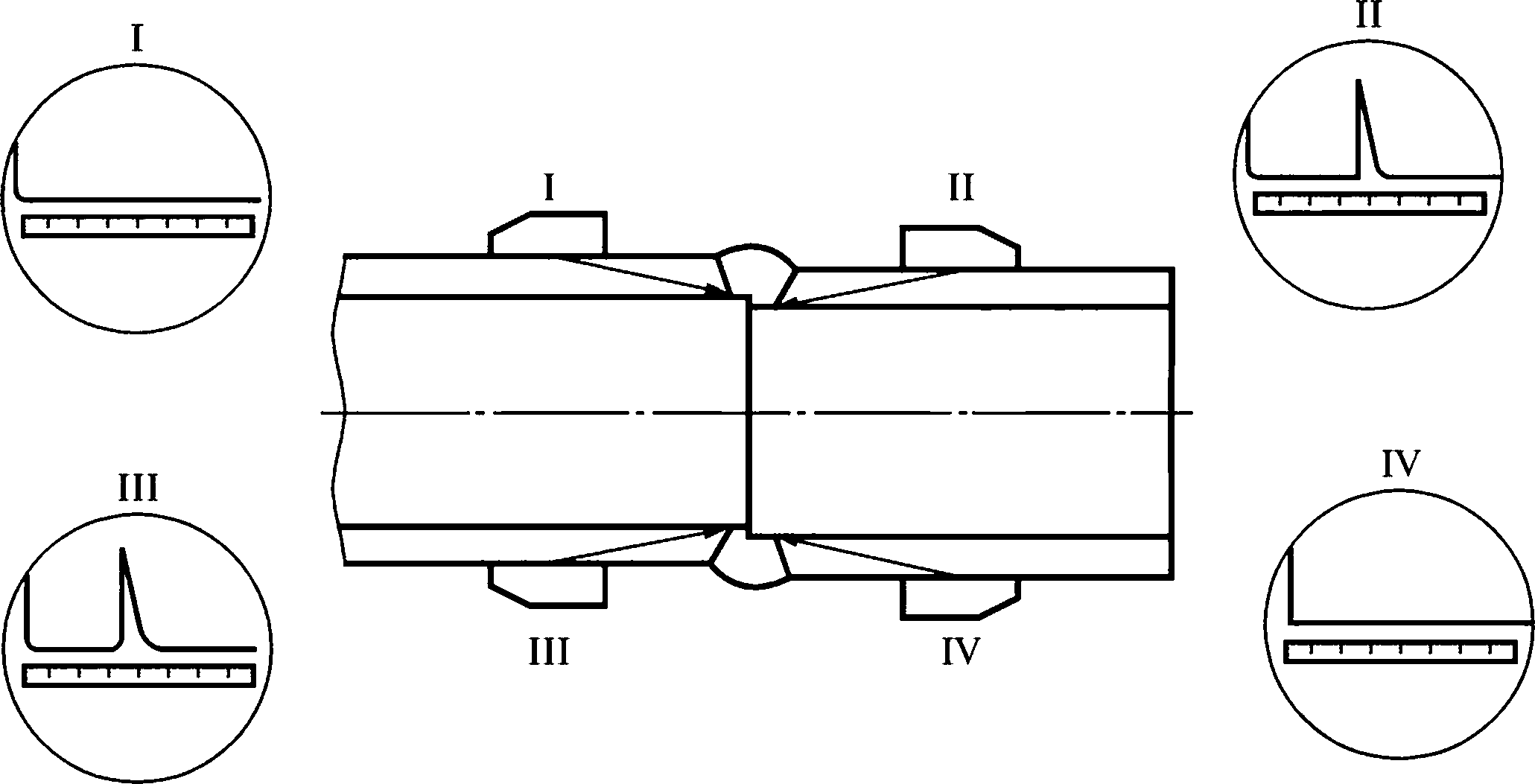
Рисунок Р.2 — Определение кромок стыкуемых труб из-за несоосности: I—IV — номера ПЭП
Примечание — Если при операционном радиографическом контроле корневой части шва на радиограмме имеется изображение превышения проплава, то оценку качества соответствующих участков корневой части шва допускается проводить только по результатам радиографического контроля.
Р.1.4 Размеры смещения кромок при УЗК не определяются.
Р.2 Стыковые соединения с подкладными кольцами
Р.2.1 Несплошности, располагающиеся над корневым слоем, могут быть выявлены или прямым лучом, или однократно отраженным лучом (рисунок Р.З). В последнем случае время прихода сигналов от подкладного кольца и несплошности может быть одинаковым.
Р.2.2 Для того, чтобы различить эти сигналы и избежать ошибки в оценке качества СС, необходимо определить линейкой расстояния хк, xv х2 от точки ввода луча (или от передней грани ПЭП) до середины усиления шва на НО. Сигнал от подкладного кольца появляется при меньшем расстоянии между швом и ПЭП, чем сигнал от несплошности, расположенной выше корня шва. В процессе УЗК следует периодически сравнивать эти расстояния с определенными по образцу.
Контролируя СС детали толщиной от 4,5 до 19,5 мм с углом разделки кромок 14° и менее, не следует приближать ПЭП к шву ближе чем на 5 мм от положения ПЭП, соответствующего максимуму сигнала от подкладного кольца, так как при этом возможно появление дополнительного сигнала от подкладного кольца, который может быть ошибочно принят за сигнал от корневой несплошности.
Р.2.3 Чтобы определить, к какой из кромок стыкуемых труб ближе расположена несплошность в корне шва, руководствуются следующим:
- если несплошность в корне шва расположена ближе к линии сплавления с трубой, со стороны которой ведется УЗК, то при медленном приближении ПЭП к шву на экране дефектоскопа первым появляется сигнал от несплошности, а затем, когда УЗ-лучи пройдут над несплошностью, частично экранирующей кольцо, на экране появляется сигнал от кольца;
- при УЗК этого участка шва со стороны второй трубы на экране первым появляется сигнал от подкладного кольца, а затем — сигнал от несплошности. Возможно также одновременное появление сигналов.
Р.2.4 При проведении УЗК следует учитывать качественные признаки, позволяющие судить о характере некоторых несплошностей.
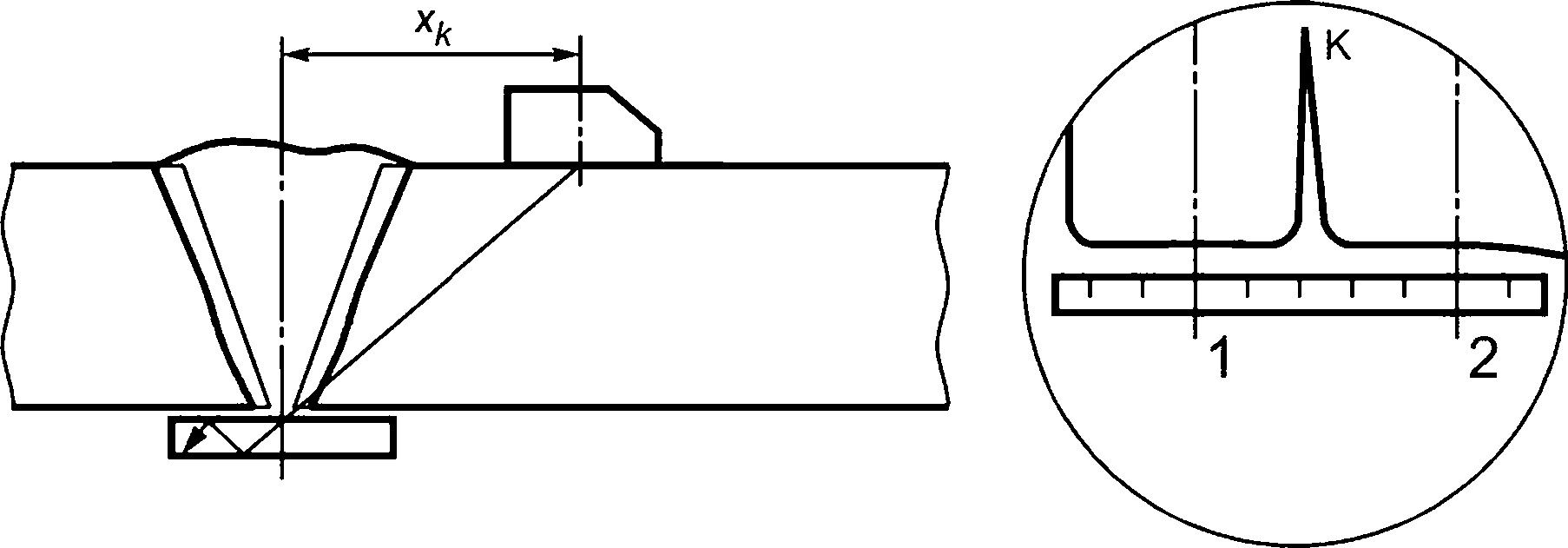
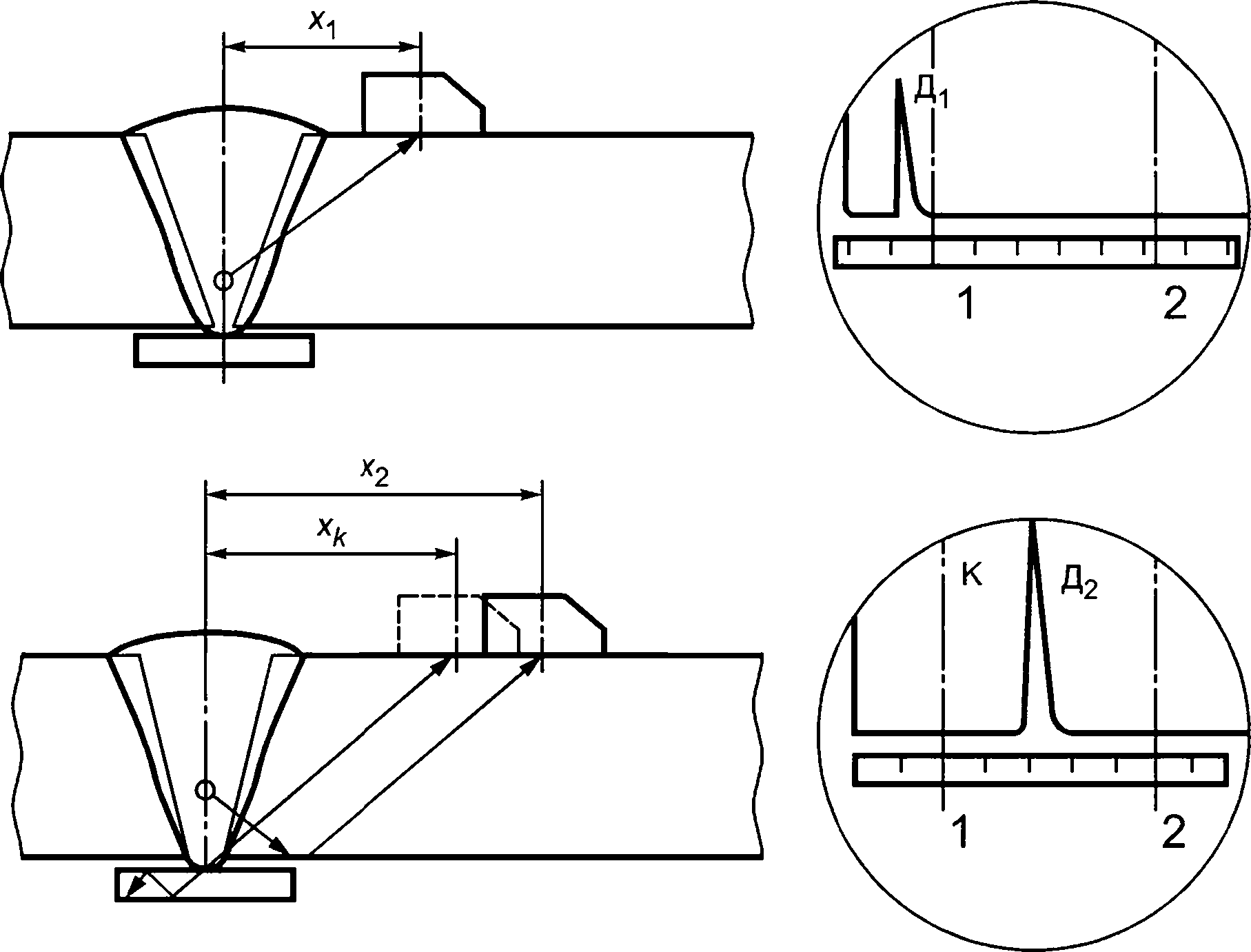
1 и 2 — положение сигналов от углового отражателя; К — сигнал от подкладного кольца; Д1 и Д2 — сигналы от надкорневой несплошности, обнаруженные прямым или однократно отраженным лучом; хк, и х2 — расстояния между серединой шва и точкой ввода ПЭП
Рисунок Р.З — Подкладное кольцо с проваром.
Схемы обнаружения подкладного кольца и надкорневой несплошности
Р2.5 Трещины в корне шва, как правило, начинаются от зазора, образованного кромкой стыкуемой трубы и подкладным кольцом. Распространяясь по наплавленному металлу, трещины выходят после первого или второго слоя на его середину. В связи с этим окончательным признаком трещин в корне шва является то, что они частично или полностью экранируют сигнал от подкладного кольца (рисунок Р.4) только при УЗК со стороны той из стыкуемых труб, у кромки которой они берут свое начало. При УЗК шва с противоположной стороны трещина не экранирует подкладное кольцо и УЗ-лучи свободно проходят в него. На экране дефектоскопа возникают два сигнала — от подкладного кольца и трещины. Сигнал от подкладного кольца имеет примерно ту же амплитуду и пробег на экране, как и на участках, где несплошность отсутствует. Трещины с этой стороны выявляются значительно хуже, а при небольшой высоте могут совсем не выявляться. На рисунке Р.4 показана схема выявления корневой трещины высотой 3 мм.
Р.2.6 Непровар, расположенный выше корневых слоев сварного шва, мало или совсем не экранирует отражение от подкладного кольца. На экране при УЗК с обеих сторон шва возникают сигналы от подкладного кольца и несплошности. Расстояние между этими сигналами более, чем в случае несплошностей, расположенных в корне шва. В некоторых случаях от несплошности и подкладного кольца на экране наблюдается несколько сигналов.
Р.2.7 Для шлаковых включений или пор характерно наличие на экране дефектоскопа импульсов, быстро исчезающих или появляющихся вновь при незначительных перемещениях ПЭП в продольном или поперечном направлении. Скопление мелких шлаковых включений или пор в наплавленном металле дает на экране один сигнал или группу близко расположенных.
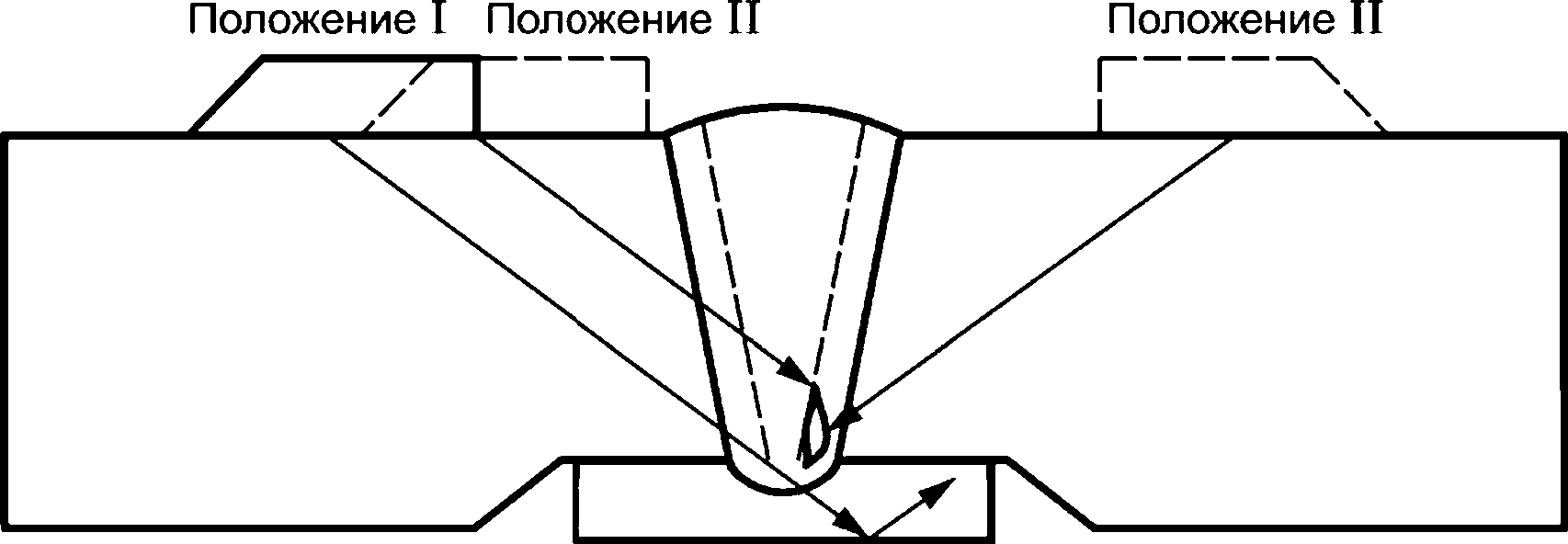
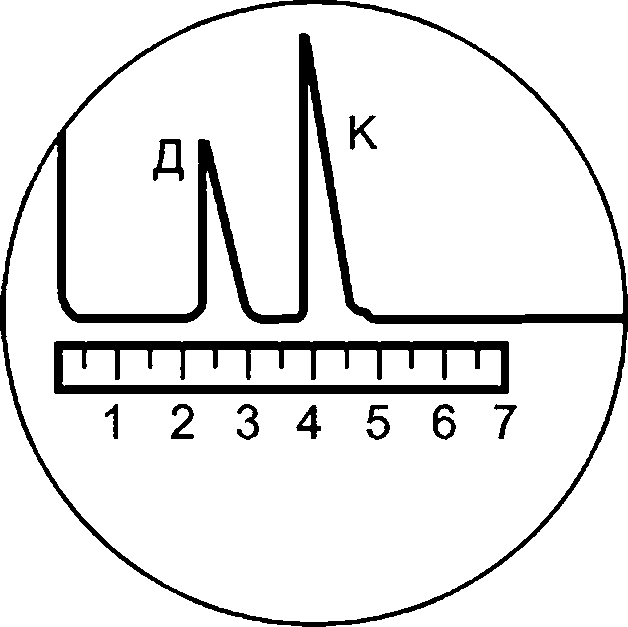
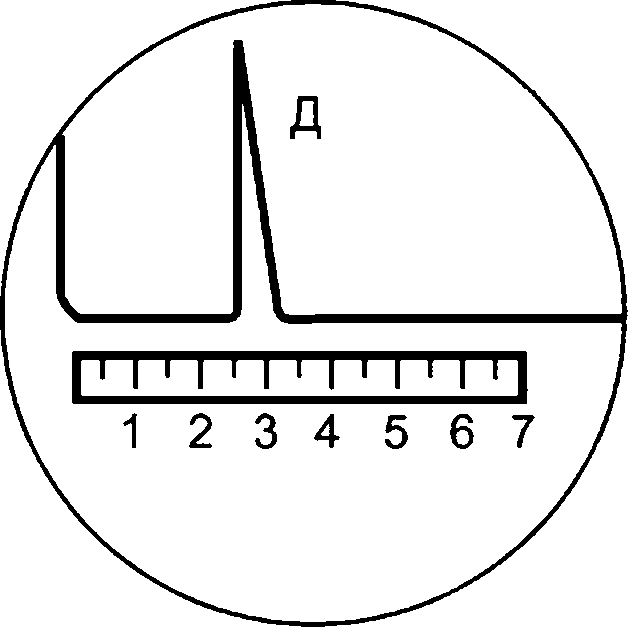
а — схема обнаружения трещины; б — осциллограмма при положении ПЭП I; в — осциллограмма при положении ПЭП II; Д — сигнал от несплошности; К — сигнал от подкладного кольца
Рисунок Р.4 — Подкладное кольцо с проваром. Схема обнаружения трещины в корне шва
Р.2.8 Прожог подкладного кольца характеризуется следующими признаками.
На экране дефектоскопа левее сигнала от подкладного кольца появляется сигнал от прожога. При этом амплитуда эхо-сигнала от кольца с прожогом менее, чем без прожога. При перемещении ПЭП вдоль образующей трубы на экране дефектоскопа в зоне расположения сигнала от подкладного кольца появляется один сигнал с двумя вершинами или два сигнала в непосредственной близости друг от друга. При УЗК с разных сторон шва форма и характер изменения сигналов от прожога аналогичны. Если прожог переходит в непровар наплавленного металла, то он обнаруживается как непровар.
Р.2.9 Зазор между подкладным кольцом и основным металлом трубы сопровождается появлением на экране дефектоскопа сигнала в том же месте, что и от несплошности в корне шва (непровар, трещина), и поэтому может оказаться причиной перебраковки сварного шва. Отличительными признаками зазора являются следующие: при плавном перемещении ПЭП вдоль образующей трубы к шву сначала появляется сигнал от подкладного кольца, а затем от зазора. При этом сигнал от подкладного кольца имеет такую же амплитуду, как и в месте шва, где зазор отсутствует. Следует также учитывать, что зазоры величиной не более 0,5 мм, как правило, не обнаруживаются, а не более 1 мм дают эхо-сигналы, меньше или примерно равные первому браковочному уровню.
Р.З Угловые соединения штуцеров (патрубков)
Р.3.1 Перед началом УЗК рекомендуется разметить СС согласно рисунку Р.5.
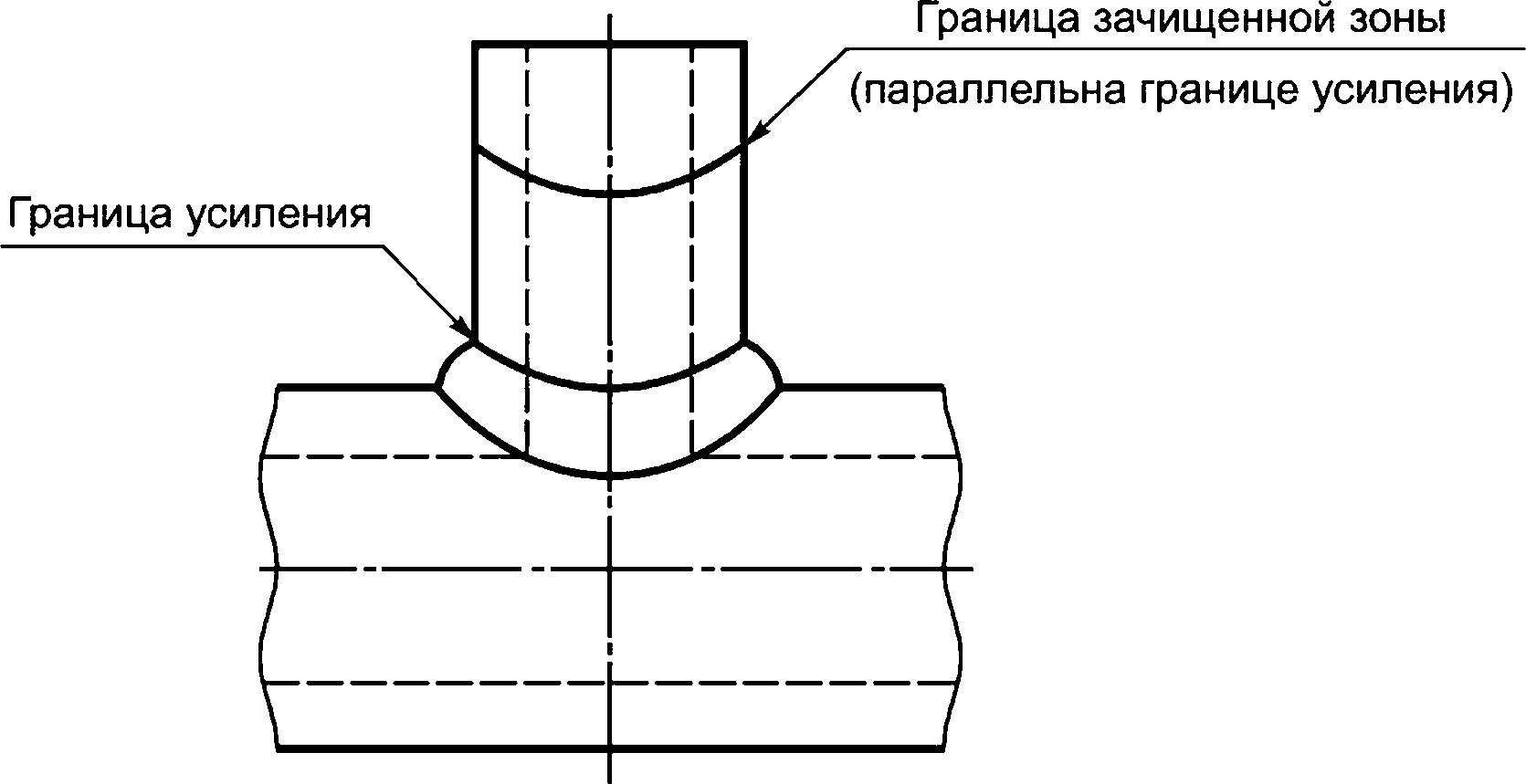
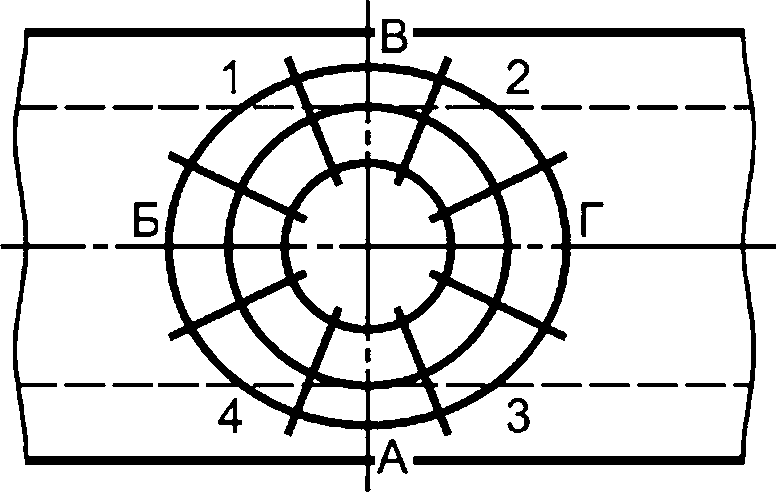
Рисунок Р.5 — Схема разметки углового кольцевого СС на секторы
Р.3.2 УЗК СС в разных секторах проводят в соответствии со схемами, приведенными на рисунке Р.6.
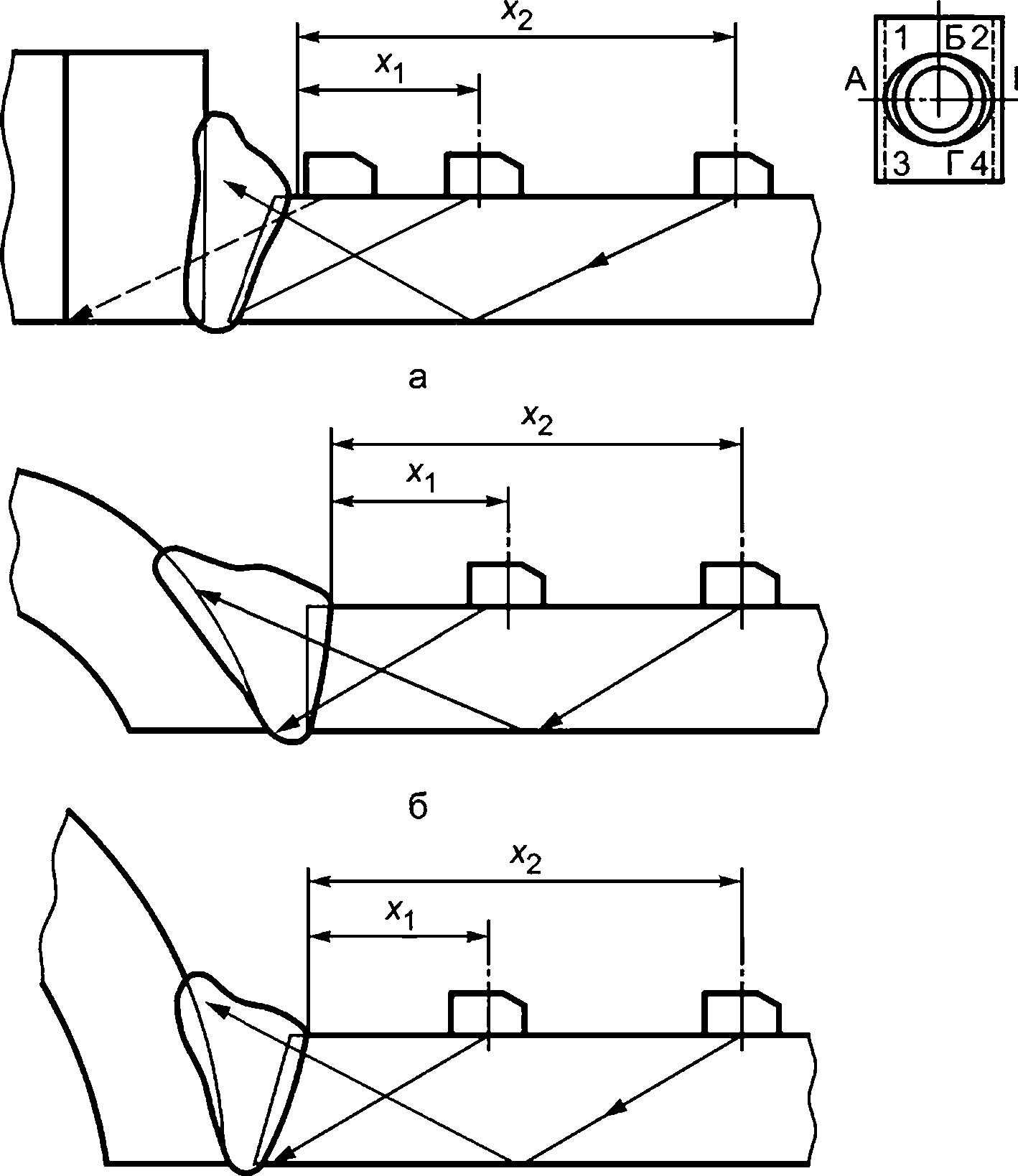
а — УЗК в секторах Б и Г; б — УЗК в секторах А и В; в — УЗК в промежуточных секторах 1—4 Рисунок Р.6 — Схемы УЗК углового кольцевого СС
УЗК проводят перемещением ПЭП между краем усиления шва и границей зачищенной зоны штуцера. При сканировании ПЭП следует поворачивать вокруг точки ввода таким образом, чтобы обеспечить его перпендикулярность относительно оси шва. Однако в процессе сканирования ПЭП не должен постоянно находиться в перпендикулярном к оси шва положении, так как при этом ухудшается контакт с поверхностью штуцера.
От двух до трех циклов перемещения ПЭП прозвучивается весь объем шва в данном сечении, после чего ПЭП смещается вдоль шва и цикл сканирования повторяется.
Р.3.3 При УЗК угловых СС о наличии несплошностей в сварном шве судят по результатам определения их координат. При УЗК СС с толщиной стенки штуцера менее 20 мм точно определить координаты не удается, поэтому о наличии несплошностей в шве судят по положению ПЭП относительно края усиления шва. Для этого при появлении эхо-сигнала в рабочей зоне развертки следует определить расстояние от точки ввода ПЭП до ближайшей границы усиления шва х^ (рисунок Р.6), если эхо-сигнал на экране расположен вблизи левой границы рабочей зоны развертки, или х2, если эхо-сигнал расположен вблизи правой границы. Полученные значения х1 или х2 сравнивают с соответствующими данными в таблице Р.1. Совпадение полученных и табличных значений с точностью ±5 мм свидетельствует о наличии несплошности. При УЗК СС с толщиной стенки штуцера 20 мм и более определяют координаты h и х.
Примечан и е — Сигналы от несплошностей, находящихся выше корня шва, могут быть получены прямым лучом при расстояниях, меньших х^ и однократно отраженным лучом при расстояниях, больших xv
Таблица Р.1 — Положения ПЭП при УЗК угловых СС
Толщина стенки | х1 в секторах, мм | х2 в секторах, мм | ||||
штуцера, мм | А, В | Б, Г | 1—4 | А, В | Б, Г | 1—4 |
4,5 | 7 | 5 | 5 | От 17 до 30 | От 17 до 30 | От 17 до 30 |
6 | 10 | 5 | 7 | От 20 до 32 | От 20 до 32 | От 20 до 32 |
9 | 20 | 15 | 17 | От 35 до 50 | От 35 до 50 | От 35 до 50 |
От 11 до 12 | 25 | 20 | 23 | От 45 до 60 | От 45 до 60 | От 45 до 60 |
16 | 23 | 15 | 20 | От 40 до 60 | От 40 до 60 | От 40 до 60 |
18 | 25 | 17 | 21 | От 45 до 65 | От 45 до 65 | От 45 до 65 |
На внутренней поверхности штуцера после механической обработки могут оставаться мелкие неровности (риски, впадины, бугры) и давать ложные сигналы. Признаком неровностей внутренней поверхности штуцера является несоответствие положения эхо-сигнала на развертке положению ПЭП на поверхности штуцера. Так, если на экране появляется эхо-сигнал у левой рабочей зоны развертки, а ПЭП при этом находится в положении, при котором луч не может попасть в корень шва, то причиной появления эхо-сигнала становятся неровности внутренней поверхности.
Р.3.4 При УЗК СС с толщиной стенки штуцера от 40 до 50 мм в центре секторов Б и Г (рисунок Р.6) может появляться эхо-сигнал от двугранного угла внутри трубы. Признаком принадлежности сигнала двугранному углу является то, что сигнал находится на экране у левой границы рабочей зоны развертки, ПЭП при этом вплотную придвинут к усилению шва.
Р.4 СС секторных отводов
Р.4.1 Особенностью УЗК секторных отводов является неперпендикулярность оси шва образующей трубы. При УЗК СС отводов диаметром 160 мм следует перемещать ПЭП перпендикулярно к оси шва. Контролируя соединения секторных отводов меньших диаметров, следует перемещать ПЭП параллельно образующей трубе.
Р.4.2 При оценке качества СС во избежание ложной браковки необходимо учитывать признаки смешения кромок и превышение проплава по Р.1.2 и Р.1.3.
Р.5 СС сосудов
Р.5.1 При проведении УЗК следует учитывать качественные признаки, позволяющие судить о характере некоторых несплошностей. Для сварных швов сосудов характерны непровары (несплавления) в корне Х-образного шва и по кромкам СС, трещины, шлаковые включения в виде цепочек и скоплений.
Р.5.2 Непровары по кромке характеризуются наличием эхо-сигнала при прозвучивании со стороны основного металла (рисунок Р.7а).
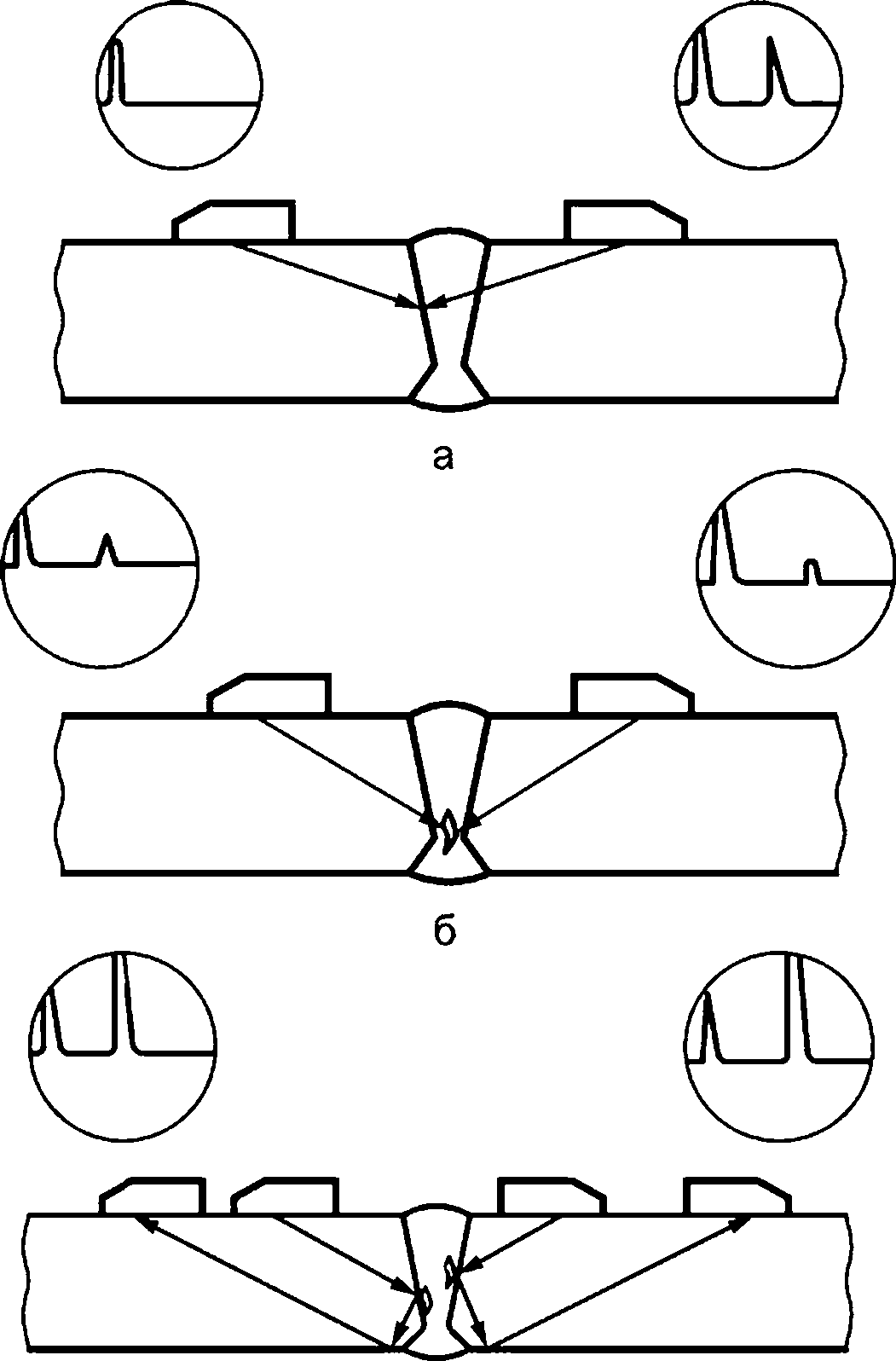
а — непровар (несплавление) по кромке; б — трещина; в — УЗК по схеме «тандем» Рисунок Р.7 — Выявление непроваров и трещин в СС
Р.5.3 При УЗК С ПЭП трещины дают небольшие эхо-сигналы или совсем не обнаруживаются (рисунок Р.76). В этом случае рекомендуется проведение УЗК по схеме «тандем».
Р.5.4 Отдельные шлаковые включения и поры характеризуются тем, что при прозвучивании с разных направлений эхо-сигналы слабо изменяют свое расположение и величину на экране дефектоскопа (рисунок Р.8). Рыхлость характеризуется появлением широкого эхо-сигнала неопределенной формы (рисунок Р.9).
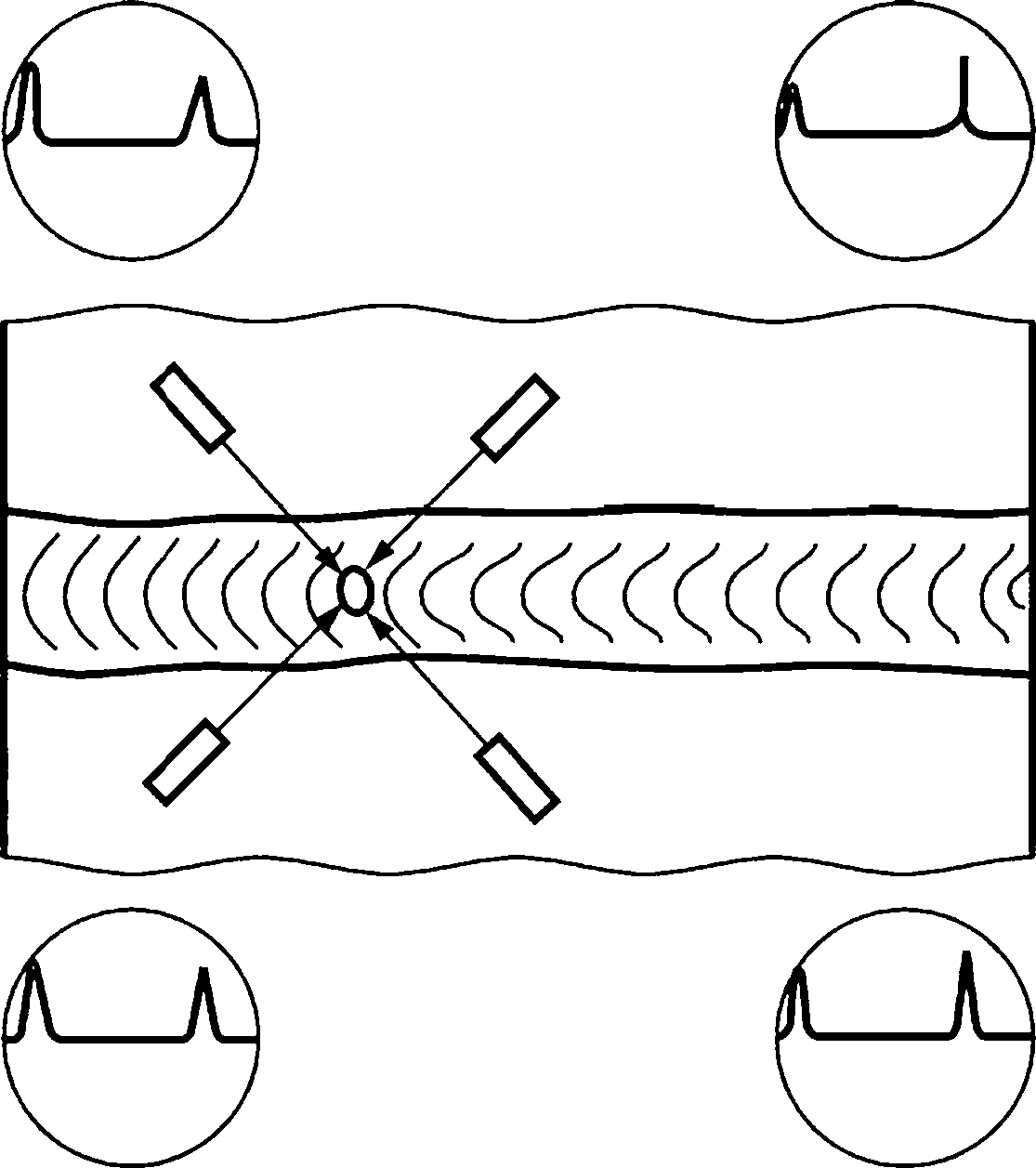
Рисунок Р.8 — Выявление отдельных шлаковых включений и пор в СС сосудов
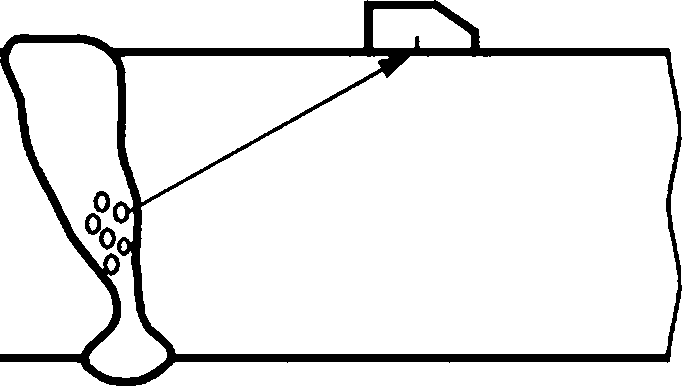
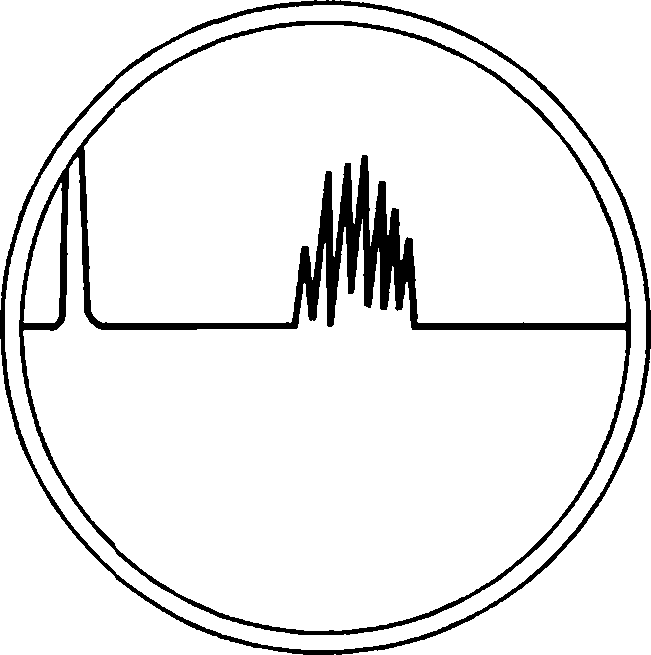
Рисунок Р.9 — Выявление рыхлости в СС сосудов
Р5.5 При проведении УЗК прямым и однократно отраженным лучами НП стыковых, а также угловых, тавровых и крестообразных СС со стороны привариваемой детали следует исключить из обзора сигналы, появляющиеся правее границы, соответствующей координате h, равной одной (прямой луч) или двойной (однократно отраженный луч) толщине детали, как показано на рисунке Р.10.
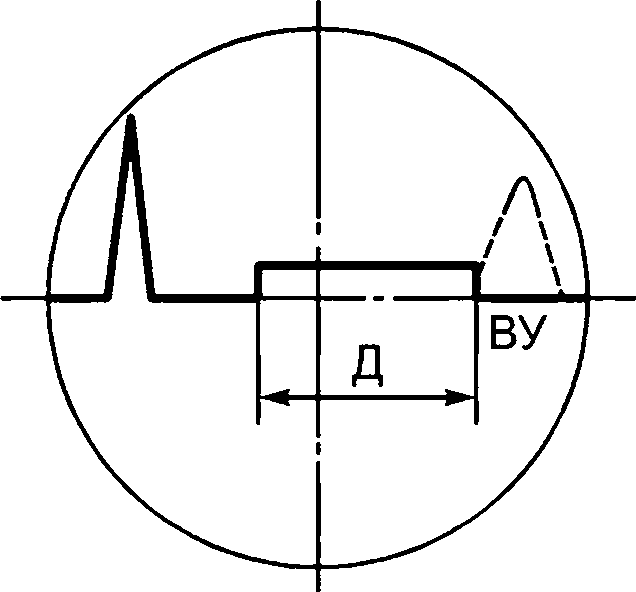
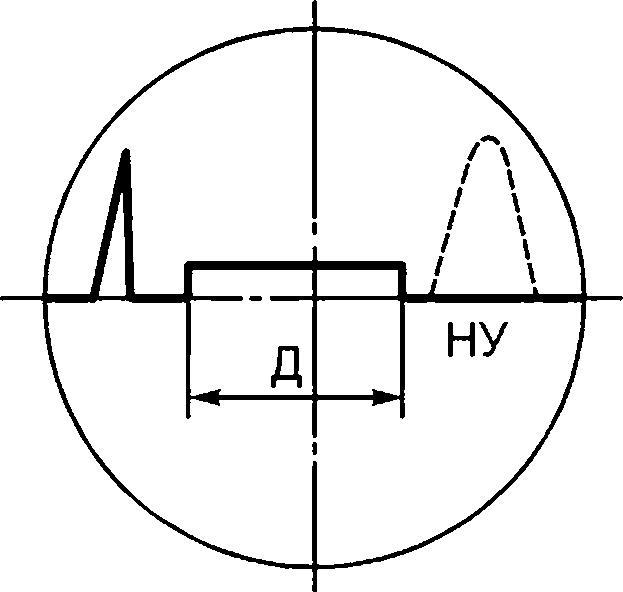
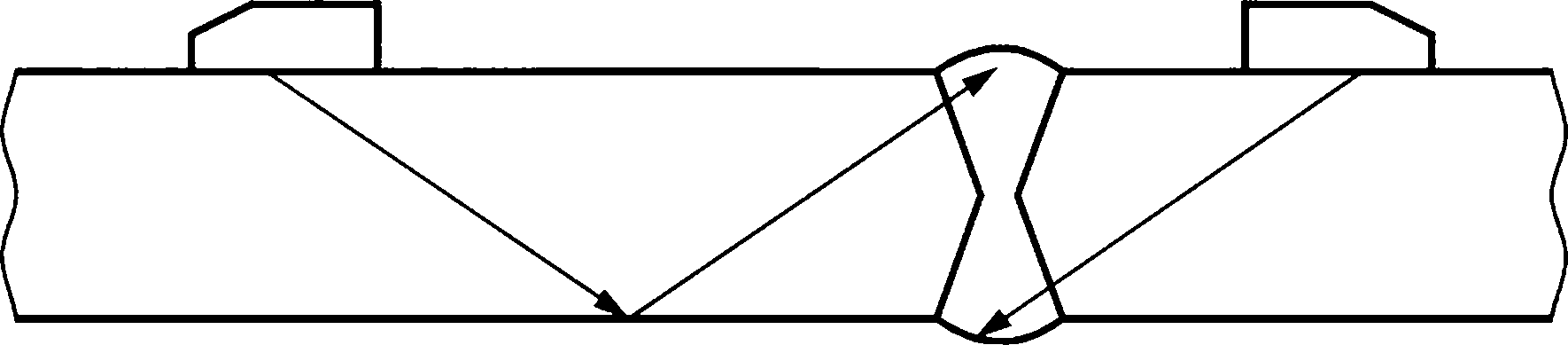
Д — зона появления эхо-сигналов от несплошностей шва; ВУ, НУ — зона появления эхо-сигналов от неровностей верхнего усиления и нижнего усиления шва соответственно
Рисунок Р.10 — Схема обнаружения эхо-сигналов от неровностей формирования усиления шва при УЗК стыковых (угловых, тавровых, крестообразных) СС со стороны привариваемой детали
Р.5.6 Особенностью УЗК СС плоских конструкций является наличие систематически появляющихся эхо-сигналов от неровностей формирования внутреннего и наружного усилений шва. Для исключения возможной ошибки при оценке результатов УЗК руководствуются следующими правилами:
- при УЗК прямым и однократно отраженным лучами НП стыковых, а также угловых, тавровых и крестообразных СС со стороны привариваемой детали следует исключить из обзора сигналы, появляющиеся на экране дефектоскопа правее границы, соответствующей координате h, равной одной (прямой луч) или двойной (однократно отраженный луч) толщине детали, как показано на рисунке Р.10;
- при УЗК однократно отраженным лучом НП стыковых, а также угловых, тавровых и крестообразных СС со стороны привариваемой детали зону перемещения ПЭП при его движении ко шву следует ограничить положением, соответствующим отражению прямого луча от зоны, прилегающей к границе усиления шва, на поверхности, противоположной той, по которой перемещают ПЭП (рисунок Р. 11 а);
- при УЗК НП угловых и тавровых СС прямым лучом со стороны основной детали зону перемещения ПЭП следует ограничивать положением, соответствующим координате X, равной расстоянию от точки ввода до дальней от ПЭП поверхности привариваемой детали, как показано на рисунке Р.116;
- при УЗК ПРС угловых и тавровых СС со стороны основной детали зону перемещения ПЭП ограничивают положением, соответствующим появлению эхо-сигнала от противоположной поверхности основной детали (рисунок Р11в).
Рисунок Р11 — Определение границ зон перемещения ПЭП при УЗК СС плоских конструкций
Приложение С (обязательное)
Методика классификации несплошностей по условной протяженности
С.1 Настоящая методика предназначена для классификации зафиксированных несплошностей на протяженные и непротяженные (точечные).
С.2 Классификацию проводят путем сравнения определенной по 7.6.1.5 условной протяженности &L. несплошности с условной протяженностью Д/_о плоскодонного отражателя площадью S6p, равной наибольшей допустимой площади одиночной несплошности по КД для данной толщины ОК, и расположенного на глубине залегания несплошности.
С.З Условную протяженность Д£о определяют как условную протяженность соответствующего плоскодонного отражателя или зарубки в образце.
С.4 Допускается вычислять Д/_о по формуле
Д£о = 0,Q7ry[N/af,
(С.1)
где г — расстояние от ПЭ до несплошности вдоль УЗ-луча, мм; г= гм + гпр, где гм и гпр — расстояние в металле и призме ПЭП, мм;
N — разность между браковочным и контрольным уровнями чувствительности по 7.4.2.3, дБ;
а — радиус (полуширина) ПЭ в плоскости, ортогональной плоскости прозвучивания, мм;
f — частота УЗ-колебаний, МГц.
Примечания
1 При г не более 135 мм Д/_о принимают равным 10 мм.
2 Коэффициент 0,67 учитывает скорость распространения УЗ-волн.
3 При работе ПЭП типа ИЦ и ПНЦ на частоте 1,8 и 2,5 МГц принимают Л/равным 3, af равным 15,5 и расчет проводят по формуле
(С.2)
Д/_о = 0,075г.
С.5 Несплошность считают протяженной, если Д/_ больше Д£о, и компактной, если AL меньше AL0.
Приложение Т (обязательное)
Сокращенная форма описания несплошностей
Т.1 При описании несплошностей, выявленных при проведении УЗК, применяют следующие обозначения:
- А — несплошность с амплитудой эхо-сигнала, не превышающей браковочный уровень (допустимый по амплитуде);
- Д — несплошность с амплитудой эхо-сигнала, превышающей браковочный уровень (недопустимый по амплитуде);
- Г — непротяженная несплошность;
- Е — протяженная несплошность;
- У — несплошность, недопустимая по условной высоте;
- О — несплошность, оцененная как объемная несплошность;
- П — несплошность, оцененная как плоскостная несплошность;
- Н — несплошность, с оцененной ориентацией (наклонная);
- Т — поперечная несплошность (тип «Т»).
Т .2 При описании несплошностей применяют следующую последовательность записи:
- значение глубины залегания, мм;
- индекс амплитуды эхо-сигнала (А или Д);
- индекс условной протяженности (Г или Е);
- индекс условной высоты (У); для допустимой по условной высоте несплошности индекс не записывают;
- индекс поперечной несплошности (Т);
- индекс объемной и плоскостной несплошностей (О или П);
- индекс ориентации (Н);
- значение координаты несплошности вдоль шва (выраженное в часах для трубопроводов и миллиметрах для плоских конструкций).
Т.З После каждой буквы (индекса) проставляют определенное значение (в цифрах) соответствующей характеристики несплошности.
Т .4 После индекса амплитуды сигнала записывают значение эквивалентной площади несплошности. Для непротяженной несплошности после индекса «Г» цифру не записывают.
Библиография
Положение о стандартизации в отношении продукции (работ, услуг), для которой устанавливаются требования, связанные с обеспечением безопасности в области использования атомной энергии, а также процессов и иных объектов стандартизации, связанных с такой продукцией (утверждено постановлением Правительства Российской Федерации от 12 июля 2016 г. № 669)
Федеральные нормы и правила в области использования атомной энергии НП-084-15
Федеральные нормы и правила в области использования атомной энергии НП-089-15
Федеральные нормы и правила в области использования атомной энергии НП-010-16
Федеральные нормы и правила в области использования атомной энергии НП-104-18
Федеральные нормы и правила в области использования атомной энергии НП-044-18
Федеральные нормы и правила в области использования атомной энергии НП-045-18
Федеральные нормы и правила в области использования атомной энергии НП-046-18
Федеральные нормы и правила в области использования атомной энергии НП-107-21
Федеральные нормы и правила в области использования атомной энергии НП-105-18
Правила контроля основного металла, сварных соединений и наплавленных поверхностей при эксплуатации оборудования, трубопроводов и других элементов атомных станций
Правила устройства и безопасной эксплуатации оборудования и трубопроводов атомных энергетических установок
Правила устройства и эксплуатации локализующих систем безопасности атомных станций
Сварка и наплавка оборудования и трубопроводов атомных энергетических установок
Правила устройства и безопасной эксплуатации сосудов, работающих под избыточным давлением, для объектов использования атомной энергии
Правила устройства и безопасной эксплуатации трубопроводов пара и горячей воды для объектов использования атомной энергии
Правила устройства и безопасной эксплуатации паровых и водогрейных котлов для объектов использования атомной энергии
Правила устройства и безопасной эксплуатации корпуса блока реакторного, оборудования, трубопроводов и внутрикорпусных устройств ядерной энергетической установки со свинцовым теплоносителем
Правила контроля металла оборудования и трубопроводов атомных энергетических установок при изготовлении и монтаже
Федеральный закон от 26 июня 2008 г. № 102-ФЗ «Об обеспечении единства измерений»
Метрологические требования к измерениям, эталонам единиц величин, стандартным образцам, средствам измерений, их составным частям, программному обеспечению, методикам (методам) измерений, применяемым в области использования атомной энергии (утверждены приказом Госкорпорации «Росатом» от 31 октября 2013 г. № 1/10-НПА)
Правила технической эксплуатации электроустановок потребителей электрической энергии (утверждены приказом Министерства энергетики Российской Федерации от 12 августа 2022 г. № 811)
Санитарно-эпидемиологические правила и Санитарно-эпидемиологические требования к физическим нормативы СанПиН 2.2.4.3359-16 факторам на рабочих местах
Федеральный закон от 9 января 1996 г. № З-ФЗ «О радиационной безопасности населения»
УДК 620.179:1:006.354
ОКС 27.120
Ключевые слова: ультразвуковой контроль, неразрушающий контроль, сварные соединения, наплавленные поверхности
Редактор Л.В. Каретникова Технический редактор И.Е. Черепкова Корректор И.А. Королева Компьютерная верстка А.Н. Золотаревой
Сдано в набор 20.12.2022. Подписано в печать 13.01.2023. Формат 60*841/в. Гарнитура Ариал. Усл. печ. л. 12,56. Уч.-изд. л. 11,30.
Подготовлено на основе электронной версии, предоставленной разработчиком стандарта
Создано в единичном исполнении в ФГБУ «Институт стандартизации» , 117418 Москва, Нахимовский пр-т, д. 31, к. 2.