ФЕДЕРАЛЬНОЕ АГЕНТСТВО ПО ТЕХНИЧЕСКОМУ РЕГУЛИРОВАНИЮ И МЕТРОЛОГИИ
ГОСТР 50.05.03— 2022
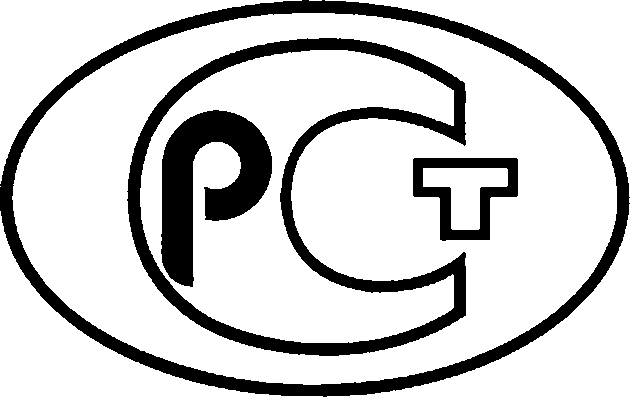
НАЦИОНАЛЬНЫЙ СТАНДАРТ РОССИЙСКОЙ ФЕДЕРАЦИИ
Система оценки соответствия в области использования атомной энергии
ОЦЕНКА СООТВЕТСТВИЯ
В ФОРМЕ КОНТРОЛЯ
Унифицированные методики.
Ультразвуковой контроль. Измерение толщины монометаллов, биметаллов и антикоррозионных наплавленных поверхностей
Издание официальное
Москва Российский институт стандартизации 2022
Предисловие
1 РАЗРАБОТАН Акционерным обществом «Российский концерн по производству электрической и тепловой энергии на атомных станциях» (АО «Концерн Росэнергоатом»)
2 ВНЕСЕН Техническим комитетом по стандартизации ТК 322 «Атомная техника»
3 УТВЕРЖДЕН И ВВЕДЕН В ДЕЙСТВИЕ Приказом Федерального агентства по техническому регулированию и метрологии от 19 декабря 2022 г. № 1525-ст
4 ВЗАМЕН ГОСТ Р 50.05.03—2018
Правила применения настоящего стандарта установлены в статье 26 Федерального закона от 29 июня 2015 г. № 162-ФЗ «О стандартизации в Российской Федерации». Информация об изменениях к настоящему стандарту публикуется в ежегодном (по состоянию на 1 января текущего года) информационном указателе «Национальные стандарты», а официальный текст изменений и поправок — в ежемесячном информационном указателе «Национальные стандарты». В случае пересмотра (замены) или отмены настоящего стандарта соответствующее уведомление будет опубликовано в ближайшем выпуске ежемесячного информационного указателя «Национальные стандарты». Соответствующая информация, уведомление и тексты размещаются также в информационной системе общего пользования — на официальном сайте Федерального агентства по техническому регулированию и метрологии в сети Интернет (www.rst.gov.ru)
© Оформление. ФГБУ «Институт стандартизации», 2022
Настоящий стандарт не может быть полностью или частично воспроизведен, тиражирован и распространен в качестве официального издания без разрешения Федерального агентства по техническому регулированию и метрологии
Содержание
1 Область применения
2 Нормативные ссылки
3 Термины и определения
4 Сокращения
5 Общие положения
6 Организация работ по ультразвуковому контролю
7 Способы измерения толщины
7.1 Измерение толщины монометалла
7.2 Измерение толщины биметалла
7.3 Измерение толщины антикоррозионной наплавленной поверхности
8 Требования к объекту контроля в зоне контроля
9 Требования к средствам ультразвукового контроля и образцам
10 Требования к персоналу, выполняющему ультразвуковой контроль
11 Погрешность измерений
12 Подготовка к проведению контроля
12.1 Общие требования при подготовке к проведению контроля
12.2 Разработка технологических карт контроля и технологических инструкций
12.3 Подготовка к проведению измерения толщины с применением пьезоэлектрических преобразователей
12.4 Подготовка к проведению измерения толщины с применением электромагнитно-акустических преобразователей
12.5 Настройка аппаратуры
12.6 Проверка настройки средства измерения
13 Проведение ультразвукового контроля
13.1 Подготовительные мероприятия
13.2 Технология измерения толщины металла
13.3 Измерение толщины монометалла в зоне контроля с применением пьезоэлектрических преобразователей дискретно (по отдельным точкам)
13.4 Измерение толщины биметалла в зоне контроля с использованием пьезоэлектрических преобразователей дискретно (по отдельным точкам)
13.5 Измерение толщины антикоррозионных наплавленных поверхностей в зоне контроля с использованием пьезоэлектрических преобразователей дискретно (по отдельным точкам)
13.6 Измерение толщины монометалла в зоне контроля с применением электромагнитноакустических преобразователей дискретно (по отдельным точкам) в статическом режиме
13.7 Измерение толщины металла в зоне контроля с применением электромагнитно-акустических преобразователей по полосам (линиям) в динамическом режиме
13.8 Измерение толщины металла в зоне контроля с применением электромагнитно-акустических преобразователей непрерывным сканированием
13.9 Измерение толщины металла в зоне контроля с применением электромагнитно-акустических преобразователей без фиксации толщины стенки
13.10 Измерение остаточной толщины металла в зонах контроля с коррозионными и эрозионными повреждениями
14 Учетная и отчетная документация
15 Требования к метрологическому обеспечению
16 Требования безопасности
Приложение А (обязательное) Процедура определения погрешности измерения
Приложение Б (обязательное) Требования к содержанию технологической карты контроля и технологической инструкции при измерении толщины металла
Приложение В (обязательное) Процедура определения шага сканирования при измерении толщины металла электромагнитно-акустическим преобразователем
Приложение Г (справочное) Форма и пример заполнения заключения по результатам измерения толщины металла
Библиография
ГОСТ Р 50.05.03—2022
НАЦИОНАЛЬНЫЙ СТАНДАРТ РОССИЙСКОЙ ФЕДЕРАЦИИ
Система оценки соответствия в области использования атомной энергии
ОЦЕНКА СООТВЕТСТВИЯ В ФОРМЕ КОНТРОЛЯ
Унифицированные методики. Ультразвуковой контроль. Измерение толщины монометаллов, биметаллов и антикоррозионных наплавленных поверхностей
Conformity assessment system for the use of nuclear energy. Conformity assessment in the form of examination. Unified procedures. Ultrasonic testing. Thickness measurement of monometals, bimetals and corrosion-resistant cladding surfaces
Дата введения — 2023—03—01
1 Область применения
1.1 Настоящий стандарт распространяется на оценку соответствия монометаллов, биметаллов и антикоррозионных наплавленных поверхностей (далее — металл)1) продукции2) в форме контроля (ультразвукового) при ее изготовлении, монтаже, эксплуатации.
1.2 Настоящий стандарт содержит унифицированные методики оценки соответствия в форме контроля (ультразвукового) толщины металла оборудования и трубопроводов, изготовленных в соответствии с [3], [6]—[11]. Нормы оценки качества металла указаны в [2], [4], [5], документах по стандартизации, а также конструкторской документации, технологической документации, устанавливающих требования к оценке соответствия металла оборудования и трубопроводов атомных энергетических установок и других элементов атомных станций.
2 Нормативные ссылки
В настоящем стандарте использованы нормативные ссылки на следующие стандарты:
ГОСТ 9.106 Единая система защиты от коррозии и старения. Коррозия металлов. Термины и определения
ГОСТ 2789 Шероховатость поверхности. Параметры и характеристики
ГОСТ 15467 Управление качеством продукции. Основные понятия. Термины и определения
ГОСТ 20911 Техническая диагностика. Термины и определения
ГОСТ Р 8.932 Государственная система обеспечения единства измерений. Требования к методикам (методам) измерений в области использования атомной энергии. Основные положения
ГОСТ Р 8.1015 Государственная система обеспечения единства измерений. Метрологическая экспертиза нормативной и технической документации в области использования атомной энергии. Организация и основные требования к содержанию
ГОСТ Р 50.05.11 Система оценки соответствия в области использования атомной энергии. Персонал, выполняющий неразрушающий и разрушающий контроль металла. Требования и порядок подтверждения компетентности
1) Качество и свойства материалов должны удовлетворять требованиям документов по стандартизации, включенных в Сводный перечень документов по стандартизации, предусмотренный [1].
2) В настоящем стандарте под продукцией понимаются оборудование, трубопроводы и другие элементы атомных станций (определены в [2]), на которые распространяются требования [2]—[11].
Издание официальное
ГОСТ Р 50.05.15 Система оценки соответствия в области использования атомной энергии. Оценка соответствия в форме контроля. Неразрушающий контроль. Термины и определения
ГОСТ Р 50.05.16 Система оценки соответствия в области использования атомной энергии. Оценка соответствия в форме контроля. Неразрушающий контроль. Метрологическое обеспечение
ГОСТ Р 53697 (ISO/TS 18173:2005) Контроль неразрушающий. Основные термины и определения
ГОСТ Р 55614 Контроль неразрушающий. Толщиномеры ультразвуковые. Общие технические требования
ГОСТ Р 55724—2013 Контроль неразрушающий. Соединения сварные. Методы ультразвуковые
Примечание — При пользовании настоящим стандартом целесообразно проверить действие ссылочных стандартов в информационной системе общего пользования — на официальном сайте Федерального агентства по техническому регулированию и метрологии в сети Интернет или по ежегодному информационному указателю «Национальные стандарты», который опубликован по состоянию на 1 января текущего года, и по выпускам ежемесячного информационного указателя «Национальные стандарты» за текущий год. Если заменен ссылочный стандарт, на который дана недатированная ссылка, то рекомендуется использовать действующую версию этого стандарта с учетом всех внесенных в данную версию изменений. Если заменен ссылочный стандарт, на который дана датированная ссылка, то рекомендуется использовать версию этого стандарта с указанным выше годом утверждения (принятия). Если после утверждения настоящего стандарта в ссылочный стандарт, на который дана датированная ссылка, внесено изменение, затрагивающее положение, на которое дана ссылка, то это положение рекомендуется применять без учета данного изменения. Если ссылочный стандарт отменен без замены, то положение, в котором дана ссылка на него, рекомендуется применять в части, не затрагивающей эту ссылку.
3 Термины и определения
В настоящем стандарте применены термины по ГОСТ 9.106, ГОСТ 15467, ГОСТ 20911, ГОСТ Р 50.05.15, ГОСТ Р 53697, а также следующие термины с соответствующими определениями:
3.1 антикоррозионная наплавленная поверхность: Наплавленная методом сварки поверхность основного металла детали (изделия), защищающая ее от воздействия коррозионной среды в процессе эксплуатации.
3.2
биметалл: Металлический материал, состоящий из двух слоев разнородных металлов или сплавов.
[ГОСТ Р 59129—2020, статья 147]
3.3 волнистость поверхности сканирования: Отношение максимальной стрелы прогиба (максимального отклонения от плоскостности) к периоду волнистости.
3.4
донная поверхность объекта контроля: Поверхность объекта контроля, противоположная поверхности ввода.
[ГОСТ 23829—85, статья 11]
3.5 затухания ультразвуковые в контролируемом металле: Уменьшение звукового давления при распространении волны в металле, вызванное процессами поглощения и рассеяния.
3.6
интервал допуска: Совокупность значений размера между пределами допуска, включая эти пределы.
[ГОСТ 25346—2013, статья 3.2.8.4]
3.7 контактный метод ввода ультразвуковых волн с применением пьезоэлектрического преобразователя: Сканирование ультразвуковым преобразователем (или преобразователями), находящимся в непосредственном контакте с объектом контроля (с использованием или без использования контактной среды).
3.8 линия задержки: Устройство, предназначенное для задержки электрических или электромагнитных сигналов на заданный промежуток времени.
3.9 монометалл: Однослойный металл.
3.10 поверхность ввода ультразвуковых колебаний: Поверхность объекта контроля, через которую вводятся упругие ультразвуковые колебания.
3.11
средство измерений: Техническое средство, предназначенное для измерений и имеющее нормированные (установленные) метрологические характеристики.
[ГОСТ Р 50.05.16—2018, пункт 3.1.8]
3.12
строб: Электронный способ выбора временного интервала на развертке для наблюдения, контроля или последующей обработки.
[ГОСТ Р ИСО 5577—2009, статья 2.6.9]
3.13 технологическая инструкция по неразрушающему контролю: Документ, регламентирующий объемы и технологию контроля качества металла (основного и наплавленных поверхностей) на каждом конкретном объекте контроля, в соответствии с унифицированной методикой контроля, а также содержащий нормы оценки качества.
3.14 технологическая карта контроля: Производственная контрольная документация или ее часть, регламентирующая средства, параметры, последовательность и содержание операций, в соответствии с которыми проводится неразрушающий контроль и оценка качества.
3.15 эксплуатационный контроль металла: Контроль, организованный для оценки изменения состояния металла объекта контроля и определения его пригодности к дальнейшей эксплуатации.
3.16 эквидистантная поверхность: Поверхность, расстояние до которой в любой точке постоянно от заданной поверхности.
3.17
электромагнитно-акустический преобразователь: Электроакустический преобразователь, принцип работы которого основан на взаимодействии возбуждаемого им электромагнитного поля с полем, наводимым в материале объекта контроля.
[ГОСТ 23829—85, статья 48]
4 Сокращения
В настоящем стандарте применены следующие сокращения: АНП — антикоррозионная наплавленная поверхность;
ЗИ — зондирующий импульс;
КД — конструкторская (проектная) документация;
КО — контрольный образец;
НО — настроечный образец;
НП — наклонный преобразователь;
ОК — объект контроля;
ПСП — прямой совмещенный преобразователь;
ПЭП — пьезоэлектрический преобразователь;
РСП — раздельно-совмещенный преобразователь;
СИ — средство измерений;
ТИ — технологическая инструкция;
ТКК — технологическая карта контроля;
У З — ультразвук (ультразвуковой);
У ЗК — ультразвуковой контроль;
У ЗТ — ультразвуковой контроль с измерением толщины;
ЭМА — электромагнитно-акустический;
ЭМАП — электромагнитно-акустический преобразователь.
5 Общие положения
5.1 Оценке соответствия в форме контроля (УЗ) толщины металла посредством ее измерения подлежат монометаллы, биметаллы и АНП с толщиной в диапазоне от 0,5 до 1000 мм и радиусом кривизны поверхности ввода от 8 мм и более.
5.2 Измерение толщины металла проводят с применением импульсных УЗ-толщиномеров или дефектоскопов, использующих для ввода и приема акустических волн ПЭП или ЭМАП.
5.3 УЗ-толщиномеры и УЗ-дефектоскопы вычисляют толщину металла путем умножения измеренного значения времени прохождения акустического импульса на известную скорость распространения УЗ в металле и деления на определяемое количество прохождений импульса.
5.4 УЗК посредством измерения толщины металла применяют в местах, недоступных для измерения его толщины прямым измерением (например, с помощью штангенциркуля или микрометра).
5.5 При проведении измерения толщины металла поверхность ввода и противоположная ей донная поверхность должны быть параллельны либо эквидистантны. Максимальное допустимое значение отклонения от параллельности (эквидистантности) контролируемых поверхностей — ±10°.
5.6 Необходимость проведения измерения толщины металла, объем измерений, участки сканирования (контроля), зоны контроля, схему разметки зоны контроля на точки, в которых необходимо проводить измерения, и критерии оценки результатов измерений указывают в КД.
Схема разметки должна иметь привязку к началу отсчета.
5.7 При измерении толщины следует учитывать требования федеральных норм и правил в области использования атомной энергии [2], [4], [5].
5.8 Проведение ручной УЗТ средствами контроля без автоматической записи процесса сканирования с 0 до 6 часов местного времени не допускается.
6 Организация работ по ультразвуковому контролю
6.1 Для проведения УЗТ, осуществления технологической подготовки к УЗТ, проведения подготовительных, проверочных работ, а также для хранения аппаратуры, ПЭП, образцов, вспомогательных приспособлений и другого инвентаря организуют подразделения (лаборатории, участки, группы) УЗК. Подразделения УЗК должны соответствовать требованиям [2] (раздел VI), располагать соответствующими площадями и помещениями.
6.2 Подразделение УЗК должно быть оснащено:
- СИ и средствами контроля (например, СИ с комплектом преобразователей и соединительными кабелями; металлическими измерительными линейками, штангенциркулями, металлическими рулетками и другими необходимыми СИ);
- комплектами КО, НО;
- вспомогательными устройствами (например, шаблонами, шкалами);
- розетками сети переменного тока напряжением 110 и/или 220 В, частотой 50 Гц, с заземлением; стабилизатором питающего напряжения (при необходимости).
Также подразделение УЗК оснащают:
- подводкой горячей и холодной воды;
- емкостями с контактной средой;
- лабораторными и канцелярскими столами;
- стеллажами, шкафами для хранения аппаратуры, образцов, запасных частей, документации;
- шкафами для одежды и обуви.
При необходимости подразделение УЗК может быть дооснащено:
- электроизмерительной и радиотехнической аппаратурой для проведения проверочных и ремонтных работ (при наличии подразделения по ремонту);
- электротельфером;
- слесарным инструментом;
- тележками для установки и транспортирования дефектоскопов;
- оборудованием и материалами, необходимыми для проведения УЗТ в конкретных условиях.
6.3 Участки УЗК в цехе, на монтажной площадке также оснащают роликоопорами, кантователями, розетками сети переменного тока напряжением 110 и/или 220 В, частотой 50 Гц, имеющими заземление.
6.4 При проведении УЗК должна обеспечиваться освещенность на поверхности ОК в зоне контроля не менее 500 лк.
Примечание — Измерение освещенности в обязанности специалиста по УЗК не входит.
6.5 При проведении УЗТ крупногабаритных ОК, а также в условиях монтажа и ремонта должны быть обеспечены следующие условия:
- леса и подмостки должны обеспечивать безопасное и удобное расположение специалиста по УЗК, аппаратуры относительно зоны контроля ОК;
- не допускается проведение работ, вызывающих вибрацию и загрязнение абразивной пылью ОК в зоне контроля, на расстоянии менее чем 10 м;
- яркие источники света (например, посты электросварки, резки), расположенные на расстоянии менее 15 м от места проведения УЗТ, должны быть экранированы;
- при ярком дневном свете или сильном искусственном освещении, затрудняющем наблюдение изображения на экране дефектоскопа, должны быть приняты меры по затемнению экрана дефектоскопа или рабочего места.
6.6 Колебания напряжения в электрической сети, к которой подключают СИ, не должны превышать значений, указанных в руководстве по эксплуатации СИ.
При больших колебаниях напряжения СИ следует подключать через стабилизаторы.
6.7 УЗТ проводят при температуре окружающего воздуха и металла ОК в зоне контроля от 5 °C до 40 °C.
Допускается проведение контроля в более широком температурном диапазоне при условии наличия средств контроля, технические характеристики которых позволяют проводить контроль при температурах, превышающих установленный диапазон. При этом персонал, проводящий контроль, должен быть обеспечен средствами индивидуальной защиты от воздействия высоких или низких температур соответственно.
6.8 Для ОК, допускающих кантование, проведение УЗТ в потолочном положении не допускается.
6.9 УЗТ проводят группой, состоящей из двух (или более) специалистов по УЗК. При этом как минимум один из них должен иметь уровень компетентности с правом выдачи заключения или уровень компетентности с правом проведения оценки компетентности персонала.
6.10 Контактная среда должна обладать достаточными смачиваемостью, вязкостью и однородностью для обеспечения стабильного акустического контакта. Также она должна быть прозрачной для УЗ в рабочем диапазоне частот и безвредной для специалиста по УЗК. Контактная среда должна удовлетворять требованиям пожарной безопасности организации, проводящей УЗТ, легко удаляться с поверхности и не вызывать коррозии ОК. При большой кривизне поверхности ОК в зоне контроля, а также при проведении УЗТ в вертикальном и/или потолочном положениях следует использовать контактную среду более густой консистенции.
6.11 Вещества, входящие в состав контактной среды, и сама контактная среда не являются дефектоскопическими материалами и входному контролю не подлежат.
7 Способы измерения толщины
7.1 Измерение толщины монометалла
Применяют следующие способы измерения толщины монометалла:
а) измерение времени прохождения от ЗИ до первого эхо-сигнала (рисунок 1а);
б) измерение времени прохождения между донными эхо-сигналами (рисунок 16);
в) измерение времени прохождения УЗ-импульса от излучателя до приемника, установленного на донной поверхности (рисунок 1в).
Измерение толщины монометалла реализуется контактным методом ввода УЗ волн с применением ПЭП способами, указанными в перечислениях а)—в), и контактным и бесконтактным методами с применением ЭМАП способами, указанными в перечислениях а) и б).
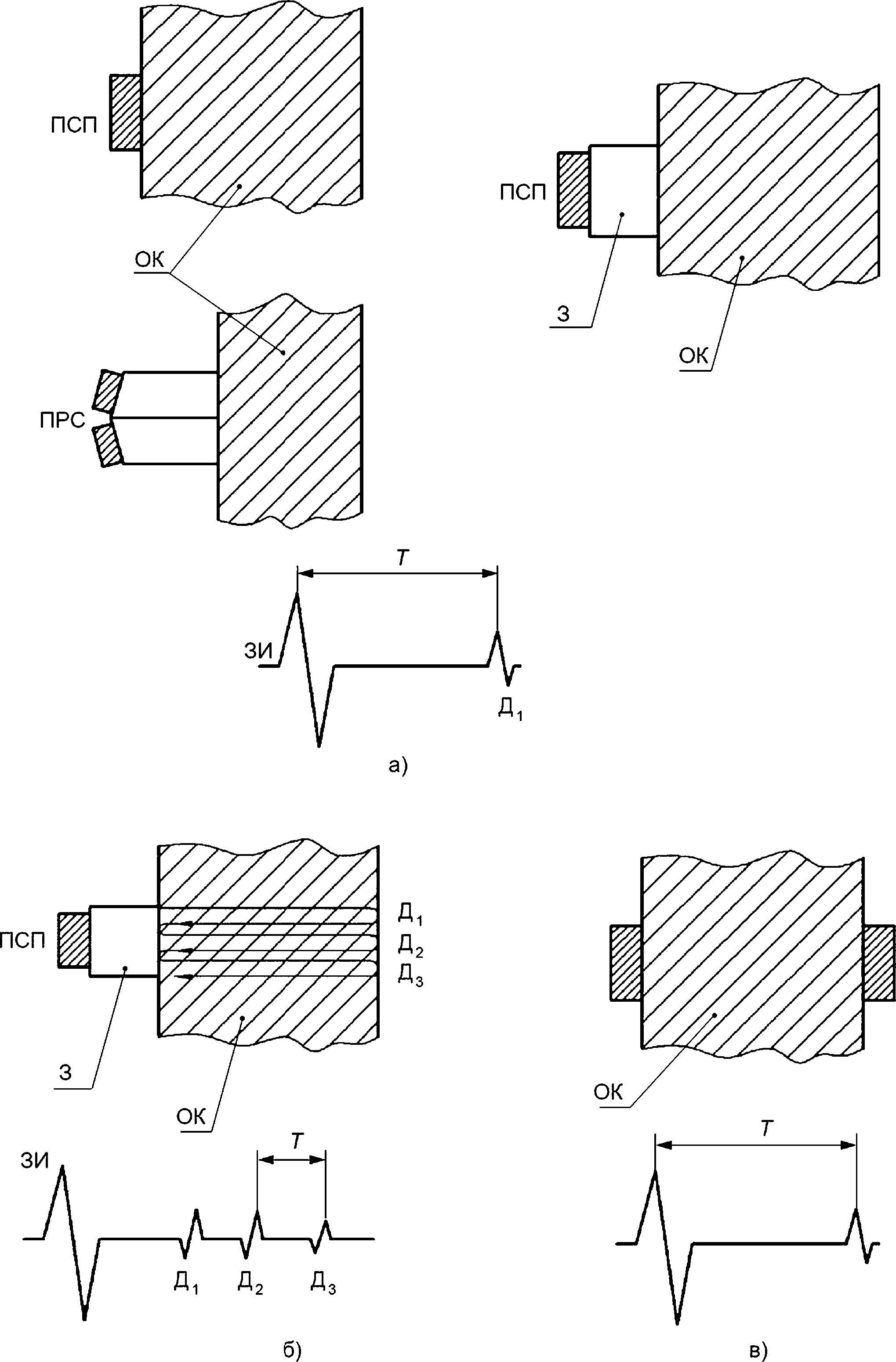
3 — линия задержки; Т — время прохождения акустического пути; Д1—Д3 — донные эхо-сигналы Рисунок 1 — Способы измерения толщины монометалла
7.2 Измерение толщины биметалла
Применяют следующие способы измерения толщины биметалла:
а) измерение времени прохождения от ЗИ до первого эхо-сигнала (рисунок 2а);
б) измерение времени прохождения от ЗИ до эхо-сигнала от границы сплавления для измерения толщины основного металла (рисунок 26);
в) измерение времени прохождения между донными эхо-сигналами (рисунок 2в).
Измерение толщины биметалла реализуется контактным способом ввода УЗ-волн с применением ПЭП.
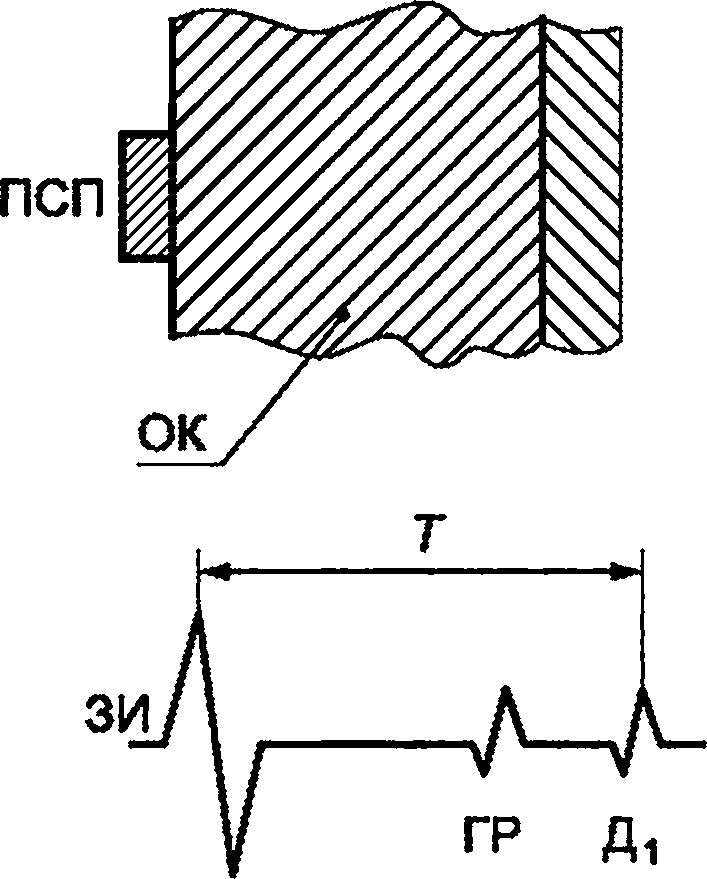
а)
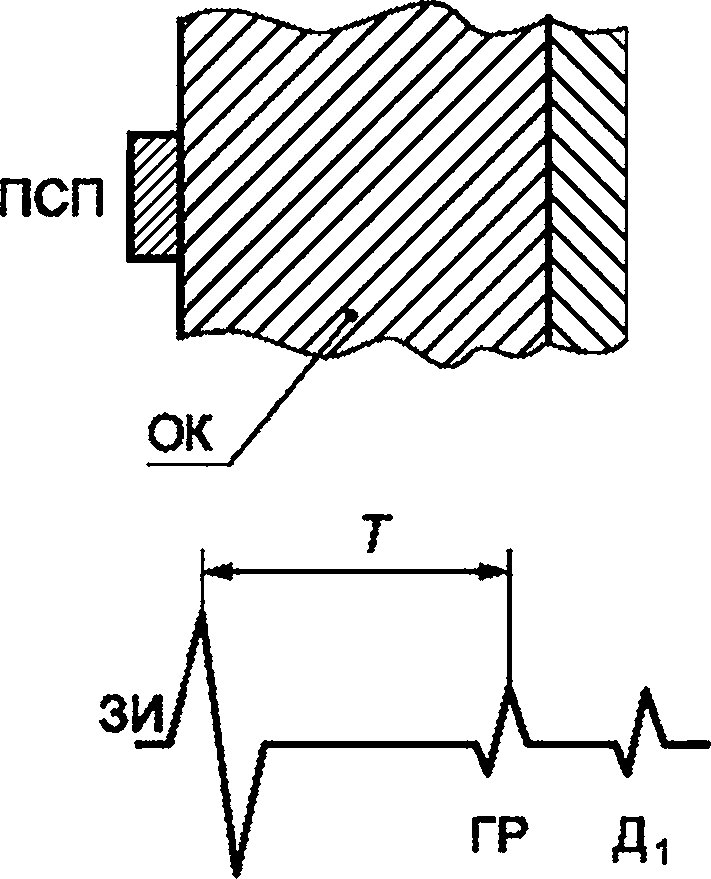
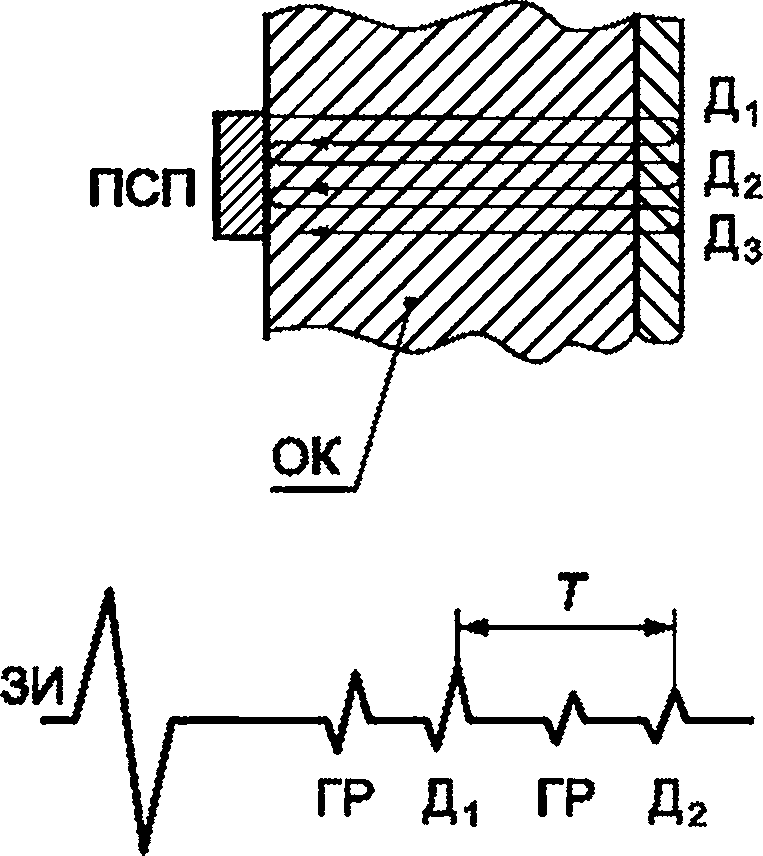
в)
Т — время прохождения акустического пути; Д1—Д2 — донные эхо-сигналы; ГР — эхо-сигналы от границы сплавления Рисунок 2 — Способы измерения толщины биметалла
7.3 Измерение толщины антикоррозионной наплавленной поверхности
Применяют следующие способы измерения толщины АНП:
а) измерение времени прохождения между эхо-сигналом от границы сплавления и донным эхо-сигналом (рисунок За);
б) измерение времени прохождения от ЗИ до эхо-сигнала от границы сплавления (рисунок 36);
в) измерение времени прохождения между эхо-сигналом от границы сплавления и донным эхо-сигналом (рисунок Зв).
Измерение толщины АНП реализуется контактным способом ввода УЗ-волн с применением ПЭП.
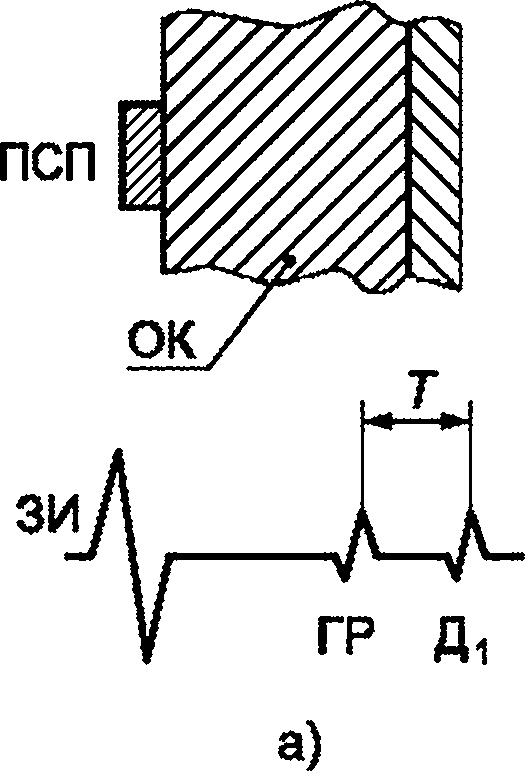
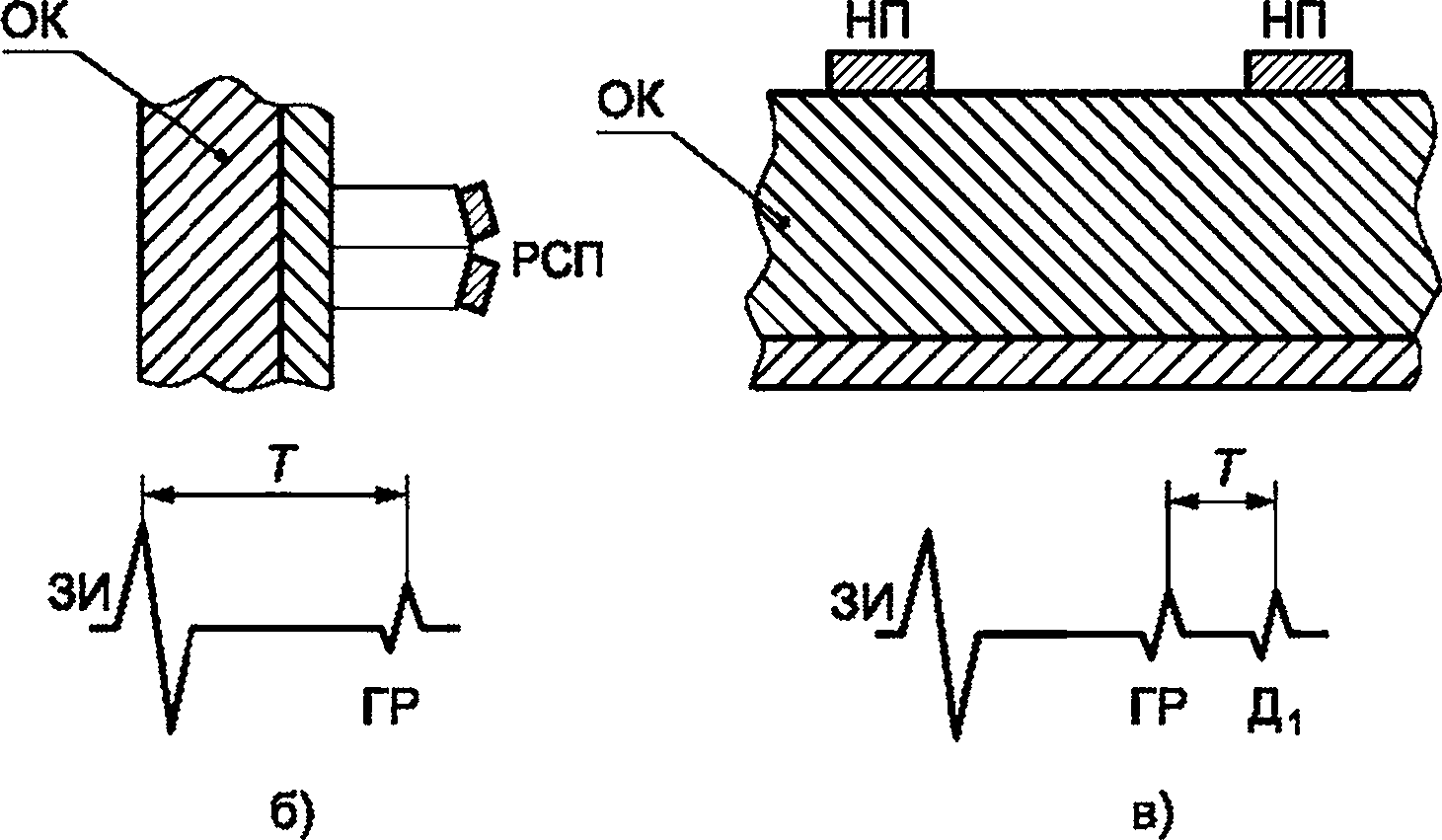
Т — время прохождения акустического пути; Д1 — донный эхо-сигнал; ГР — эхо-сигнал от границы сплавления Рисунок 3 — Способы измерения толщины АНП
8 Требования к объекту контроля в зоне контроля
8.1 При измерении толщины металла с применением ПЭП необходима предварительная подготовка поверхности ввода в зоне контроля в соответствии с требованиями:
- поверхность ввода должна быть свободна от загрязнений, препятствующих проведению контроля, отслаивающейся окалины или лакокрасочного покрытия, брызг металла;
- шероховатость поверхности ввода должна быть не более Ra 6,3 (Rz 40) мкм по ГОСТ 2789;
- зазор между поверхностью ОК в зоне контроля и ПЭП, образующийся из-за волнистости поверхности ОК в зоне контроля, не должен превышать 0,2 мм.
8.2 При проведении измерения толщины металла с применением ЭМАП предварительная обработка поверхности не требуется. Рекомендуемый зазор между ЭМАП и поверхностью ввода не должен превышать 1,0 мм.
8.3 Допускается проводить измерение толщины металла ОК, заполненных водой.
9 Требования к средствам ультразвукового контроля и образцам
9.1 Для измерения толщины металла используют следующие средства контроля:
а) УЗ- и ЭМА-толщиномеры с цифровым дисплеем, на котором отображается измеренное значение и/или развертка типа А, и удовлетворяющие общим требованиям ГОСТ Р 55614;
б) УЗ-дефектоскопы для проведения ручного УЗК с цифровым дисплеем, на котором отображаются измеренное значение и развертка типа А;
в) ПЭП: ПСП, прямой РСП и НП;
г) ЭМАП;
Д) НО.
Толщиномеры и дефектоскопы, указанные в перечислениях а) и б), являются СИ.
9.2 Используемые СИ должны обеспечивать получение донного эхо-сигнала на коррозионных поражениях поверхностей, противоположных поверхности ввода с шероховатостью до Ra 40 (Rz 160) мкм по ГОСТ 2789. При больших значениях шероховатости донной поверхности возможность проведения контроля должна определяться экспериментально.
9.3 Выбор преобразователя следует проводить в соответствии с руководством по эксплуатации СИ, с учетом измеряемой толщины, формы ОК в зоне контроля, затухания УЗ в контролируемом металле.
9.4 При проведении измерения толщины металла необходимо использовать ПЭП, обладающие высокой чувствительностью и низким уровнем реверберационных помех. Допускается использовать ПЭП в диапазоне частот от 1 до 15 МГц.
При проведении измерения толщины металла ЭМАП необходимо использовать частотный диапазон от 2 до 5 МГц.
9.5 Параметр «Диапазон измеряемой толщины» СИ должен соответствовать требуемым диапазонам измерения толщины металла ОК в зоне контроля.
9.6 Характеристики погрешности СИ указаны в описании типа СИ. Соответствие СИ (в том числе характеристик его погрешности) установленным в описании типа метрологическим требованиям подтверждается сведениями о результатах поверки СИ, включенными в Федеральный информационный фонд по обеспечению единства измерений. При необходимости может проводиться определение действительных значений характеристик погрешности СИ, для чего СИ должно быть подвергнуто процедуре калибровки. Предел допускаемой основной погрешности толщиномеров в каждой точке диапазона измерений не должен превышать значение ±(0,01 Н + 0,1) мм, а дефектоскопов — ±(0,02-Н + 0,1), где Н — измеренное значение толщины металла, указанное в миллиметрах.
9.7 Преобразователи, применяемые для измерения толщины металла, должны иметь заводской номер и маркировку.
9.8 Для настройки (регулировки) СИ на диапазон контролируемых толщин с учетом марки материала и кривизны поверхности следует применять НО.
9.9 Применение НО
9.9.1 НО необходимо изготавливать из того же материала и по той же технологии, что и ОК.
9.9.2 НО типа Т1 (рисунок 4) применяют для настройки на скорость УЗ в металле ОК при измерении толщины монометалла дефектоскопом и нуля толщиномера при измерении толщины монометалла и биметалла.
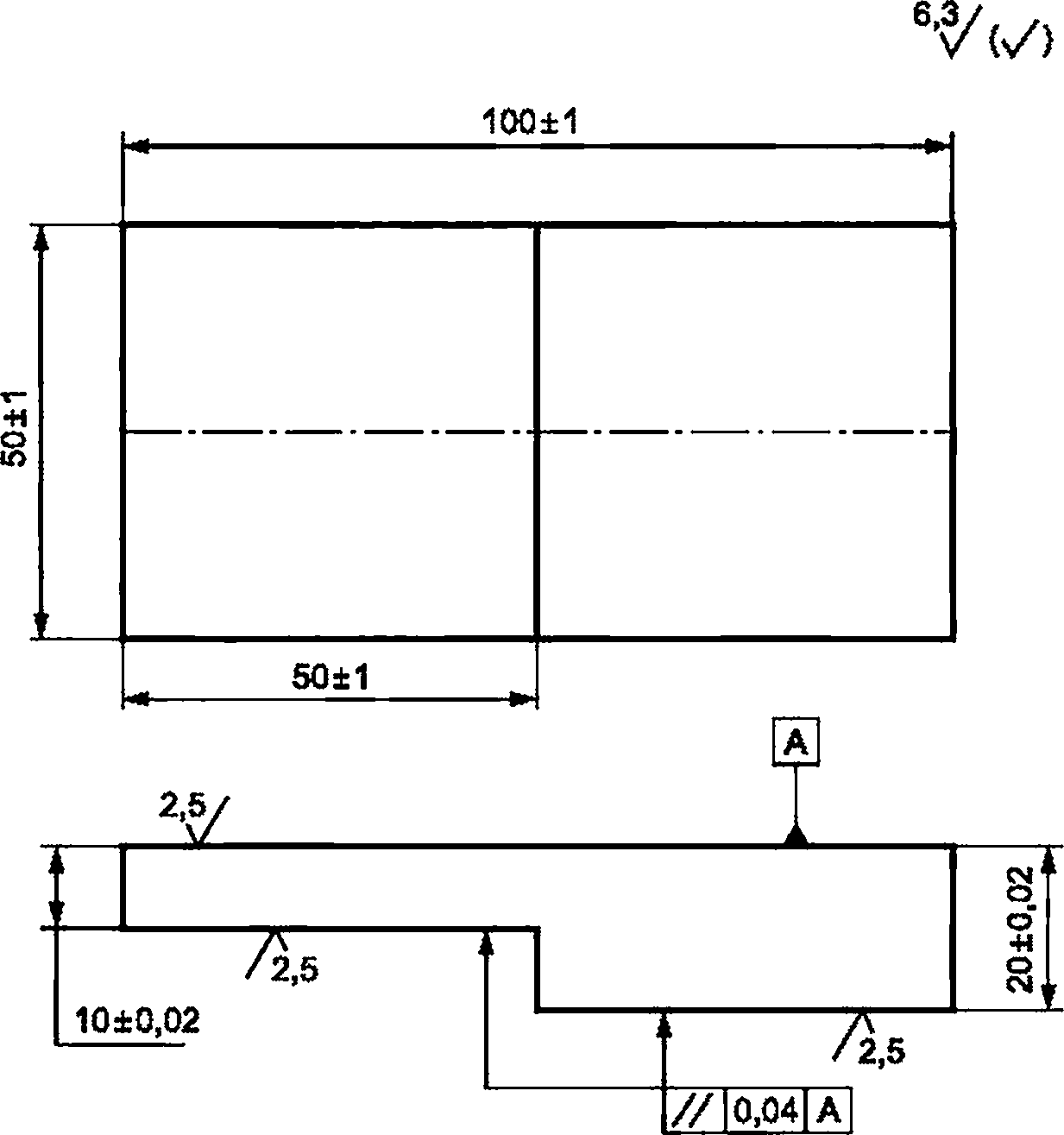
Рисунок 4 — НО типа Т1 для настройки скорости развертки дефектоскопа
9.9.3 НО типа Т2 (рисунок 5) применяют для настройки СИ при измерении толщины монометалла.
Н = (1 ± 0,1) • Но, где Но — номинальная толщина металла в зоне контроля
Примечание — Варианты 1 и 2 равнозначны.
Рисунок 5 — НО типа Т2 для настройки СИ при измерении толщины монометалла
9.9.4 НО ТБ 1 (рисунок 6) применяют для настройки СИ при измерении толщины биметалла.
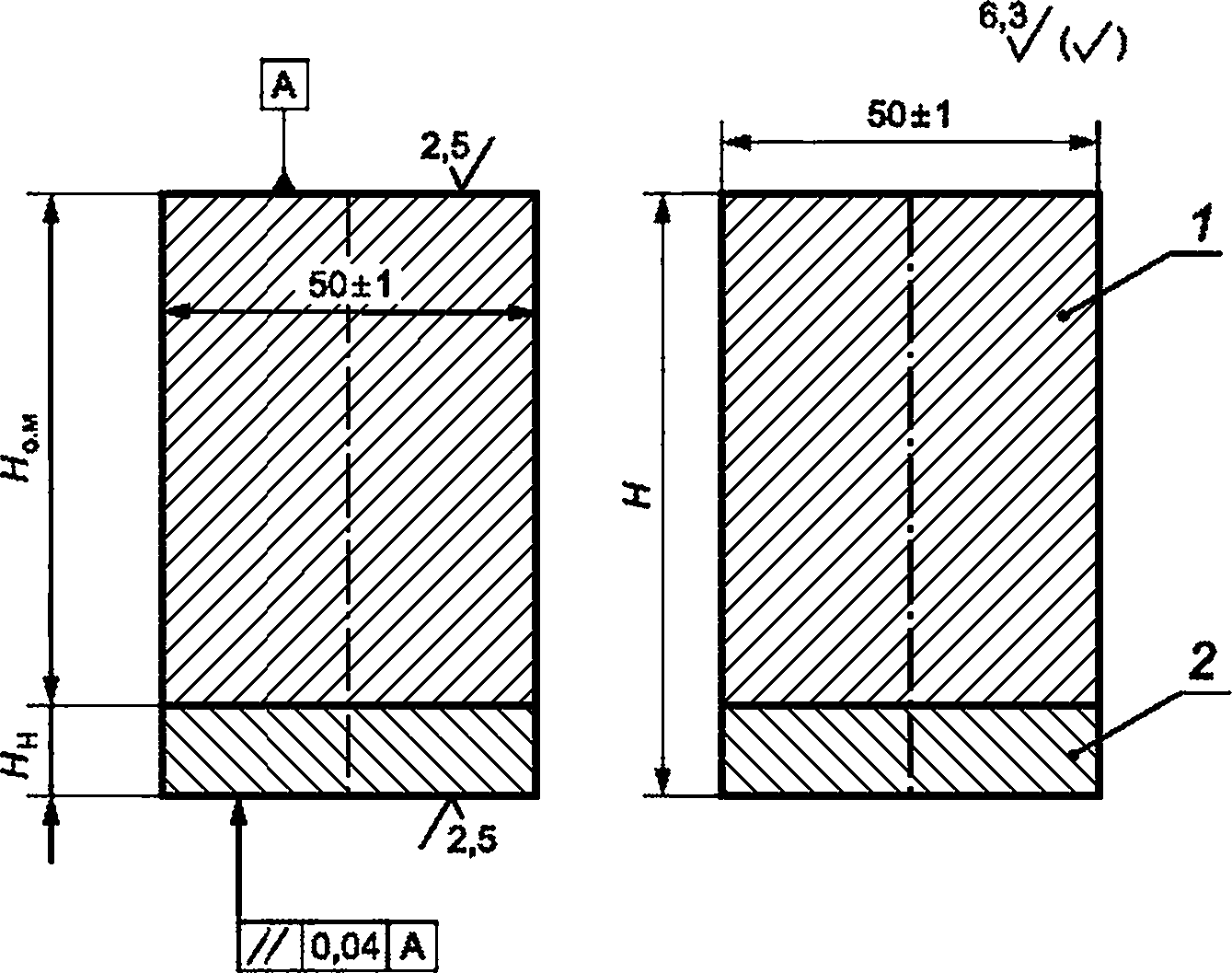
1 — основной металл; 2 — наплавленный слой
Н = (1 ± 0,1) • но, Но м = (1 ± 0,1) • Но м 0; Нн = Hmin + 2 мм,
где Н — значение толщины НО; /70— номинальное значение толщины биметалла ОК в зоне контроля; Но м — значение толщины основного металла НО; Но м 0 — номинальное значение толщины основного металла ОК в зоне контроля; Нн — значение толщины наплавленного слоя НО; Нтт — минимальная толщина наплавленного слоя металла в зоне контроля
Рисунок 6 — НО типа ТБ1 для настройки СИ при измерении толщины биметалла
9.9.5 НО типа ТН1 (рисунок 7) применяют для настройки скорости развертки дефектоскопа при измерении толщины АНП со стороны основного металла.
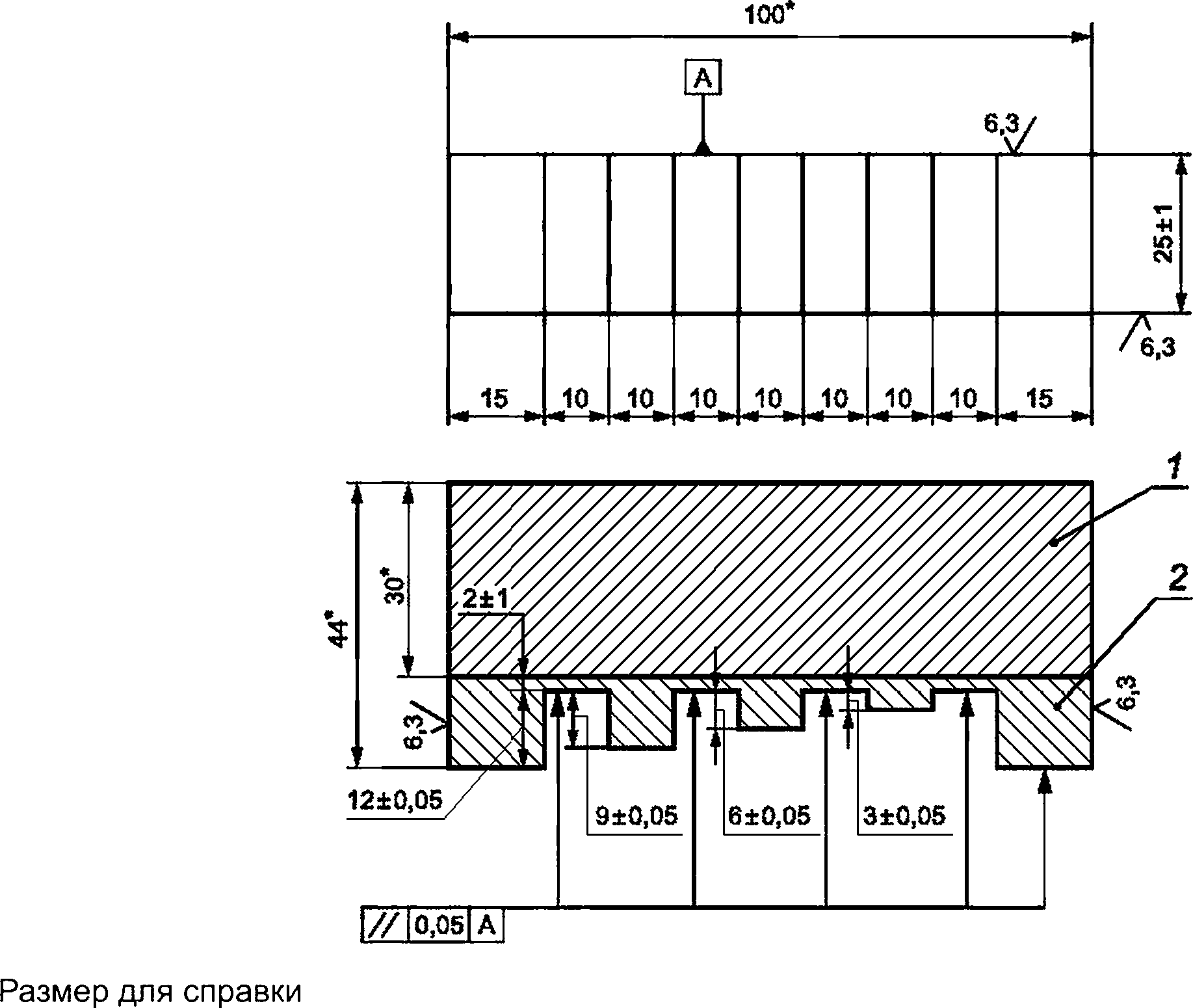
Примечание — Допуск на размеры 15 и 10 составляет ±2,0 мм.
1 — основной металл; 2 — АНП
Рисунок 7 — НО типа ТН1 для настройки скорости развертки при измерении толщины АНП со стороны основного металла
9.9.6 НО типа ТН2 (рисунок 8) применяют для настройки дефектоскопа при измерении толщины АНП со стороны наплавленной поверхности.
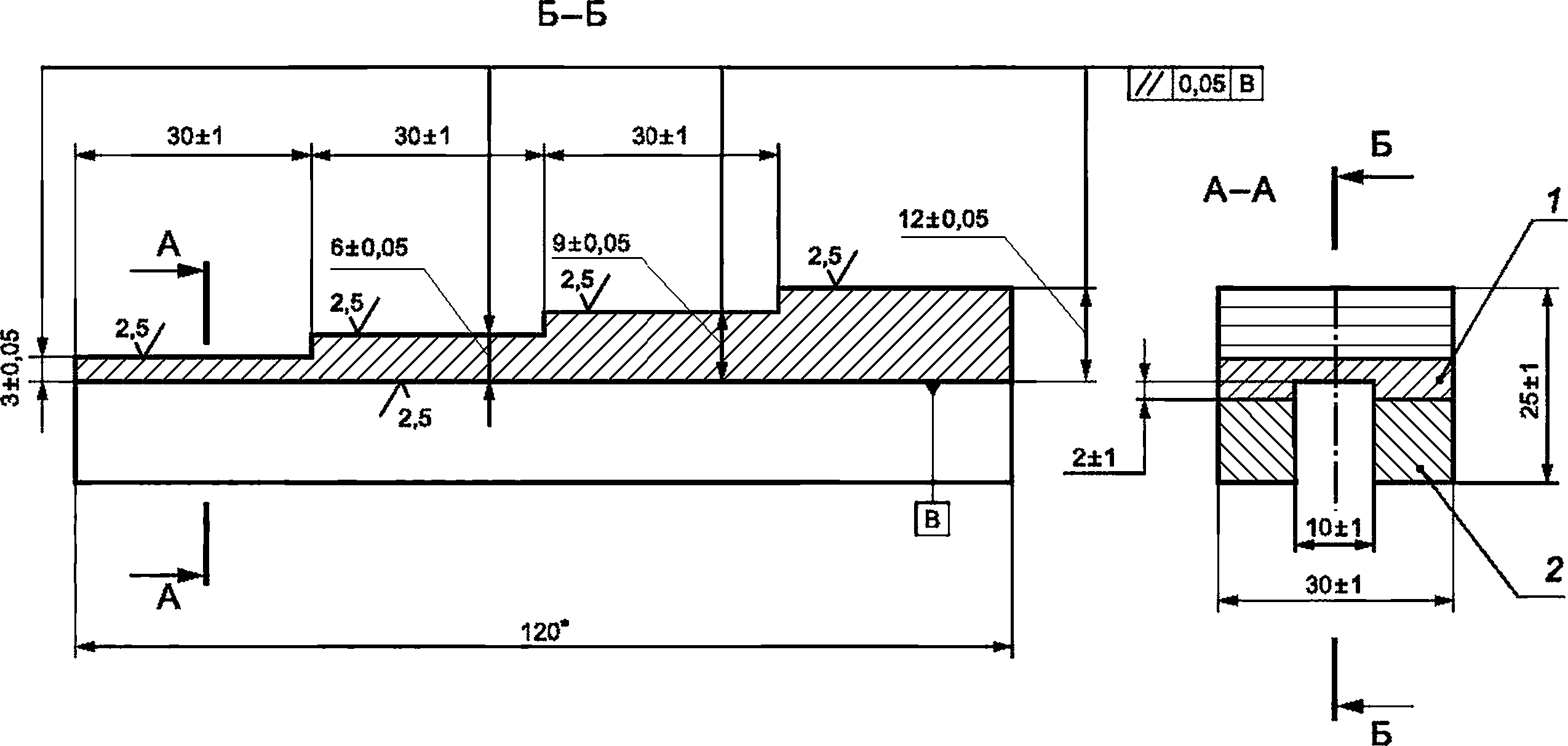
1 — АНП; 2 — основной металл
* Размер для справки
Рисунок 8 — НО типа ТН2 для настройки дефектоскопа при измерении толщины АНП со стороны наплавленной поверхности
9.9.7 НО типа ТНЗ (рисунок 9) применяют для настройки дефектоскопа при измерении толщины /-/АНП как со стороны основного металла, так и со стороны наплавленной поверхности.
* Размер для справки.
1 — АНП; 2 — основной металл;
Н = Ни ± 1, где Нн — номинальная толщина АНП
Рисунок 9 — НО типа ТНЗ для настройки дефектоскопа при измерении толщины Н АНП как со стороны основного металла, так и со стороны наплавленной поверхности
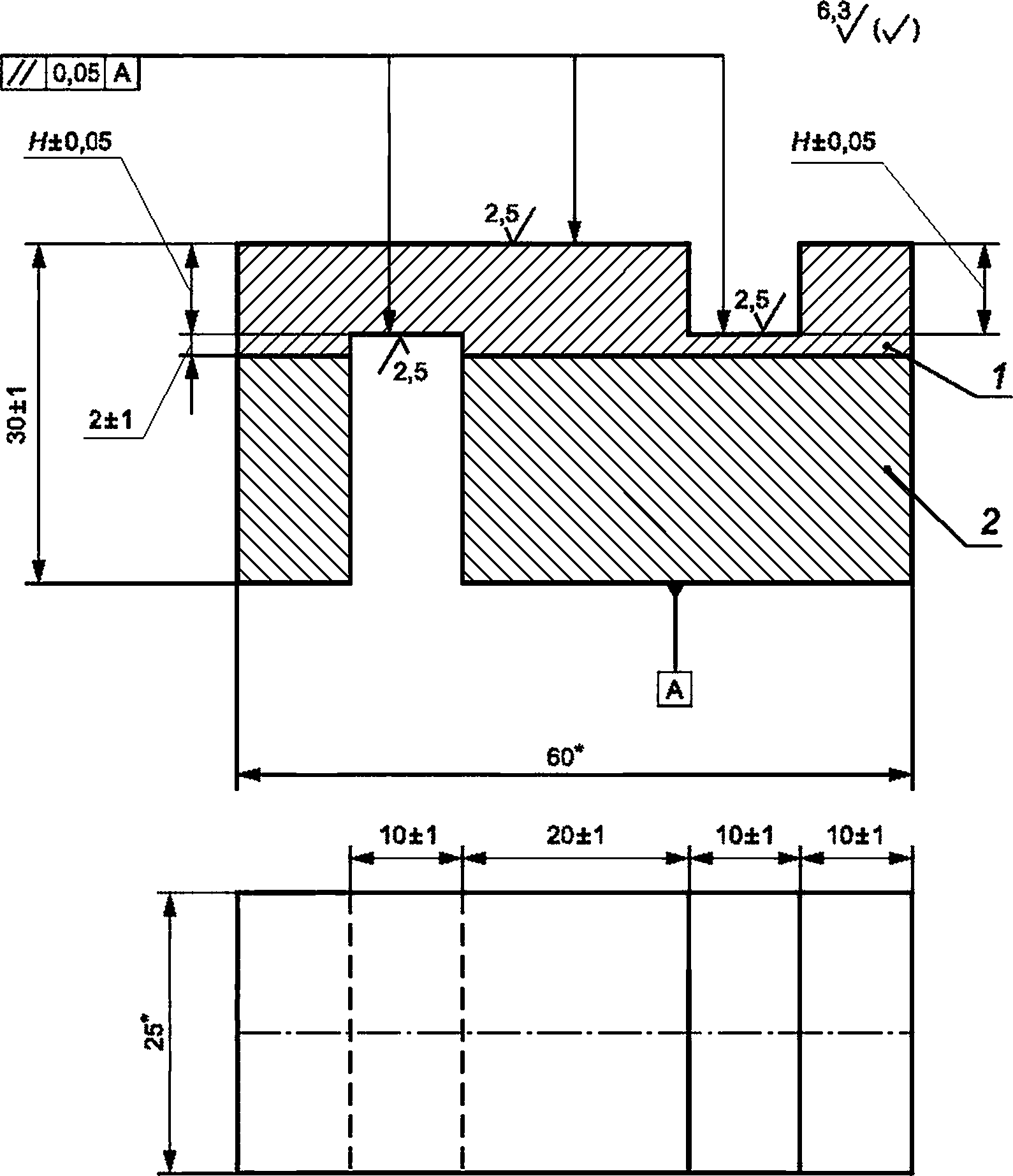
9.9.8 НО типа ТНН1 (рисунок 10) применяют для настройки дефектоскопа при измерении толщины АНП биметаллических труб НП.
При совмещении функции по 9.9.4 и 9.9.5 НО обозначается ТБ1Н1. При изготовлении НО типа TH положение границы сплавления определяют по значению расстояния до эхо-сигнала от границы сплавления.
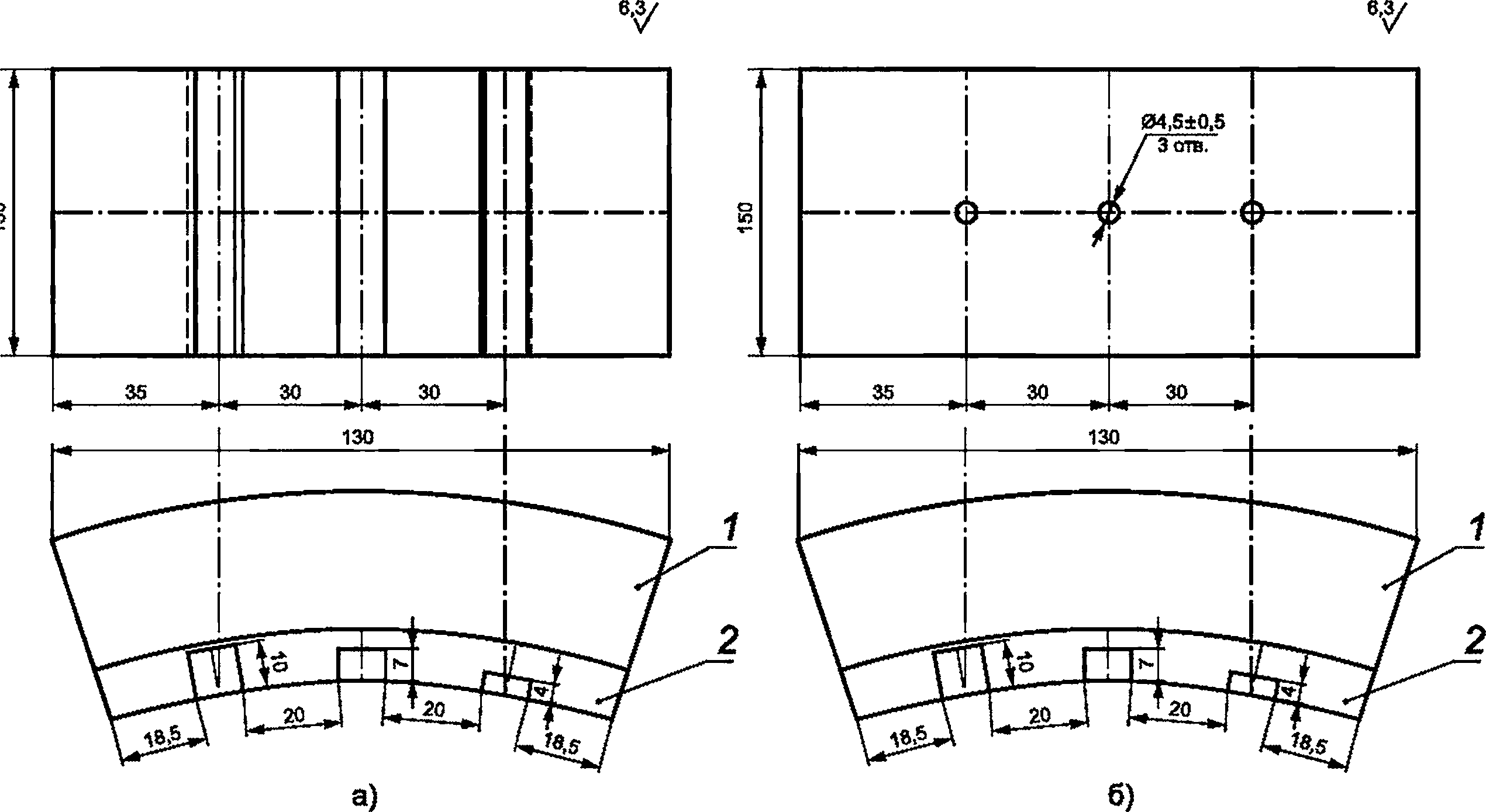
1 — основной металл; 2 — АНП
Примечание — В НО допускается изготавливать пазы (а) или плоскодонные отражатели (б). Глубина расположения дна отверстий должна быть такой же, как и глубина пазов.
Рисунок 10 — НО типа ТНН1 для измерения толщины АНП с применением НП
9.9.9 При измерении толщины металла труб и гибов с наружным диаметром менее 100 мм НО следует выполнять в виде фрагментов этих ОК (рисунки 11 и 12).
Рисунок 11 — НО в виде участка трубы
Рисунок 12 — НО в виде участка гиба (колена) трубопровода
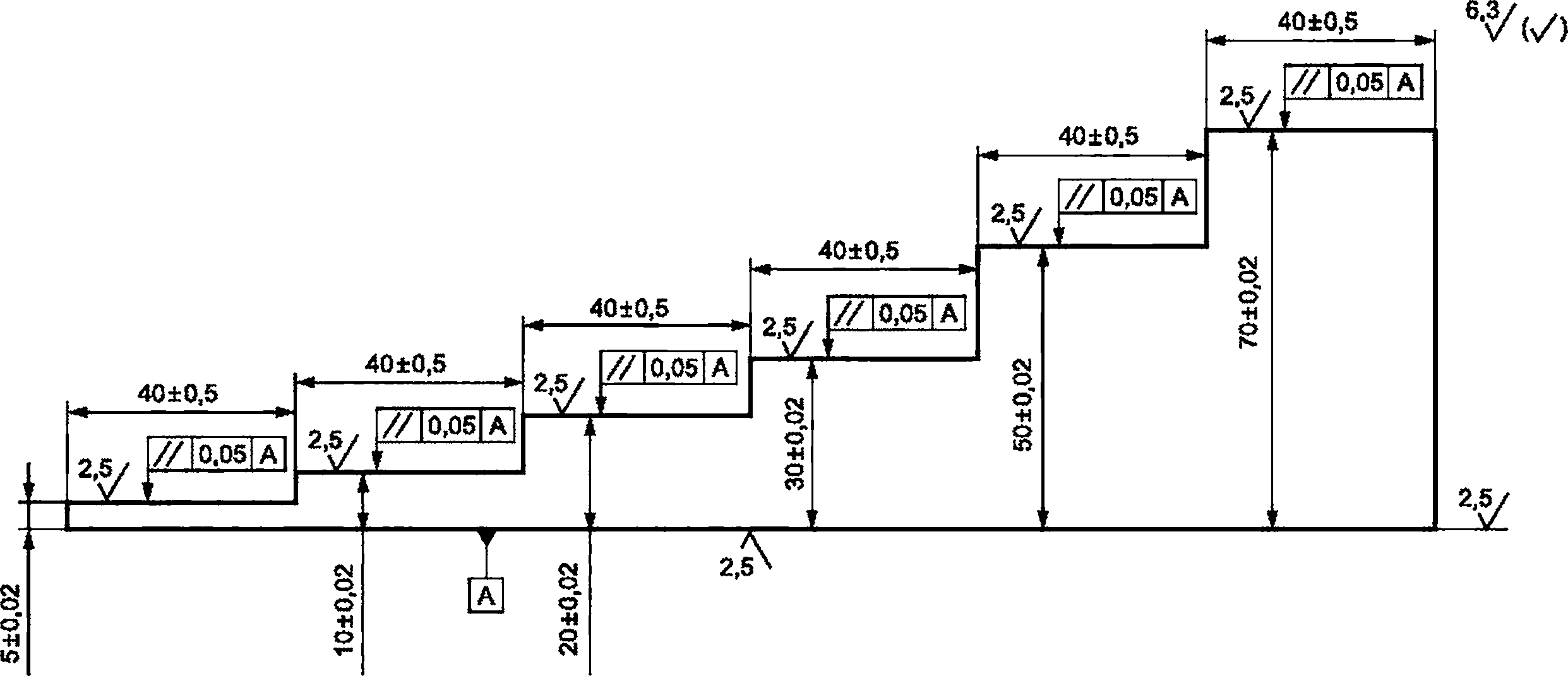
ю о* ■н
240±1 |
Рисунок 13 — НО типа НОТ-1
9.9.10 На НО, изготовленный в виде фрагмента ОК, следует отметить одну или две контрольные точки для проведения настройки (рисунок 11). Координаты контрольных точек указывают в паспорте НО.
9.9.11 Возможно применение НО из фрагментов ОК по 9.9.5 и 9.9.6. При этом глубину пазов или высоту ступеней выбирают исходя из толщины контролируемой поверхности. Обозначение типа НО (ТН1 или ТН2) сохраняется.
9.9.12 Толщину НО из монометалла, по которой проводится настройка, измеряют с погрешностью не более ±0,01 мм.
9.9.13 Каждый НО должен иметь маркировку, указывающую его тип, регистрационный номер и толщины, по которым проводится настройка.
9.9.14 Для настройки (регулировки) СИ допускается использовать НО типа НОТ-1, представленный на рисунке 13.
9.9.15 Допускается применять в качестве НО калибровочные образцы СО-2 и СО-3, образцы СО-2А и CO-ЗА, образцы V1, V2 по ГОСТ Р 55724 при условии выполнения требования 9.9.1.
9.9.16 Допускаемые отличия по свойствам металла НО и ОК:
- по скорости УЗ — ±1 %;
- по затуханию (характеризуется разностью амплитуд донных эхо-сигналов при одинаковой толщине) — ±4 дБ.
9.9.17 Допускается применение образцов, поставляемых комплектно со СИ, если их характеристики соответствуют требованиям 9.9.16.
10 Требования к персоналу, выполняющему ультразвуковой контроль
К проведению работ по измерению толщины металла по настоящему стандарту допускаются специалисты, обладающие теоретическими знаниями и практическими навыками контроля, прошедшие процедуру подтверждения компетентности в соответствии с требованиями ГОСТ Р 50.05.11.
11 Погрешность измерений
11.1 Погрешность измерений определяют при доверительной вероятности Р, равной 0,95 (приложение А). Необходимость оценки погрешности при более высоком значении доверительной вероятности указывают в КД, ТКК и ТИ.
11.2 При измерении толщины АНП погрешность принимается не более ±1,0 мм при доверительной вероятности Р, равной 0,95.
11.3 При измерении толщины плакировки листов и деталей (сборочных единиц), изготовленных из плакированных листов, погрешность принимается не более ±0,2 мм при доверительной вероятности Р, равной 0,95.
11.4 При измерении толщины монометаллических изделий из сталей перлитного класса и биметаллических изделий толщиной 20 мм или более погрешность должна быть не более ±1,5 % от номинальной толщины металла в зоне контроля, мм.
11.5 При измерении толщины монометаллических изделий толщиной менее 20 мм погрешность должна быть не более ±0,2 мм при Р, равной 0,95.
11.6 Для уменьшения погрешности измерений в ТКК и ТИ может быть предусмотрено изготовление НО непосредственно из ОК.
11.7 Погрешность измерения при Р, равной 0,95, может быть меньше значений, указанных в 11.4, 11.5, если это подтверждено выполнением процедуры, указанной в приложении А.
11.8 Оценку годности ОК по фактическим показаниям СИ проводят, если выполняется одно из следующих условий:
- погрешность измерений не превышает 35 % половины интервала допуска на контролируемый размер; при одностороннем допусковом контроле (отдельно по нижнему или верхнему отклонению) погрешность измерений не превышает 35 % соответствующего предельного отклонения;
- предельные значения толщины металла указаны в КД, которые согласованы с конструкторской организацией — разработчиком.
11.9 Если установленная погрешность измерения превышает значения, указанные в 11.9, и нет возможности применить более точное СИ, то назначаются сокращенные приемочные границы, смещение внутрь которых Д определяется по формуле
Д = |8| - 0,35(Дн + Дв)/2, (1)
где 8 — погрешность измерения, определенная по процедуре, изложенной в приложении А;
Дн, Дв — нижнее и верхнее отклонения от номинального размера.
12 Подготовка к проведению контроля
12.1 Общие требования при подготовке к проведению контроля
12.1.1 Подготовку поверхности ОК для проведения контроля и очистку поверхности ОК после его проведения (в т. ч. удаление контактной среды) осуществляют соответствующие подразделения организации — владельца или изготовителя ОК. Выполнение данных операций в обязанности специалиста по УЗК не входит.
12.1.2 Перед проведением контроля должна быть произведена разметка ОК в зоне контроля и нумерация точек измерения толщины металла в соответствии с КД. При контроле полуфабрикатов (например, листового проката, труб) для привязки разметки и нумерации точек измерения допускается использовать клеймо (маркировку) изготовителя. При проведении контроля на этапе монтажа или эксплуатации должна быть разработана и реализована процедура нанесения, поддержания или восстановления постоянной, не удаляемой в течение всего срока эксплуатации маркировки.
12.2 Разработка технологических карт контроля и технологических инструкций
12.2.1 Измерение толщины металла проводят согласно разработанным ТИ и/или ТКК.
12.2.2 При разработке ТИ и ТКК и определении координат точек измерения толщины металла необходимо руководствоваться КД, а также принятой в организации, проводящей контроль, системой отсчета координат. На атомной станции, например, руководствуются типовой (или рабочей) программой контроля.
12.2.3 ТИ и/или ТКК разрабатывает специалист, квалификация которого подтверждена в соответствии с требованиями ГОСТ Р 50.05.11, имеющий уровень компетентности специалиста с правом выдачи заключения или с правом проведения оценки компетентности персонала.
12.2.4 ТИ и ТКК должны иметь идентификационное обозначение (учетный номер), которое присваивает организация-разработчик, содержать дату разработки и быть подписанными (на каждом листе) разработчиком технологии УЗК с указанием номера его квалификационного удостоверения и даты его выдачи, а также проверяющим руководителем подразделения неразрушающего контроля.
12.2.5 На несколько ОК может быть разработана одна ТИ и/или ТКК, если выполняются следующие условия:
- ОК изготовлены из стали или сплава одинаковой марки и подвергались одинаковому типу пластического деформирования;
- поверхности ОК в зонах контроля имеют одинаковые значения шероховатости, волнистости, параллельности или эквидистантности поверхностей;
- толщина металла ОК в зонах контроля отличается не более чем на 10 %;
- для неплоских поверхностей с радиусом кривизны менее 250 мм выполняется неравенство
^L<0.1, г,<г2.
Г2 (2)
где г2 и Г1 — радиусы кривизны поверхностей измерения.
В такой ТИ и/или ТКК должна быть представлена информация в объеме, позволяющем воспроизвести технологию контроля и оценку качества для любого из указанных в ней ОК.
12.2.6 Требования к содержанию ТИ и ТКК, а также рекомендуемая форма ТКК приведены в приложении Б.
12.2.7 Допускается применять иные формы ТИ и ТКК, принятые в организации, проводящей УЗК.
12.3 Подготовка к проведению измерения толщины с применением пьезоэлектрических преобразователей
12.3.1 Для дискретного измерения толщины монометалла подготавливают площадку размером 30 х 30 мм с центром в точке измерения.
12.3.2 Для дискретного измерения толщины АНП прямым совмещенным преобразователем (ПСП) и раздельно-совмещенным преобразователем (РСП) подготавливают площадку размером 50 х 50 мм. При использовании НП размер площадки (ширина х длина) 40 х (2/-/ + 60) с центром в точке измерения, где Н — толщина металла ОК в зоне контроля, указанная в миллиметрах. Длина площадки на криволинейных поверхностях ориентирована вдоль образующей ОК в зоне контроля, в остальных случаях больший размер площадки ориентирован перпендикулярно к направлению наплавки.
12.3.3 Допускается проводить измерение толщины металла по поверхности, покрытой плотной оксидной пленкой или тонким, ровным слоем лакокрасочного покрытия, плотно прилегающими к металлу. При выполнении измерения толщины металла через оксидную пленку или слой лакокрасочного покрытия рекомендуется применять способ б) по 7.1 и использовать СИ с функцией измерения толщины металла через диэлектрическое наружное покрытие. Возможность проведения измерения толщины в этих условиях должна быть предварительно установлена экспериментальной проверкой специалистами по УЗК. Погрешность измерения определяют согласно приложению А.
12.3.4 При проведении измерения толщины металла на участках устранения поверхностных дефектов в местах максимальной глубины выборки для установки ПЭП должна быть подготовлена плоская площадка диаметром не менее 15 мм, параллельная поверхности ОК в зоне контроля. В некоторых случаях измерение может быть выполнено со стороны, противоположной выборке.
12.3.5 Если размер выборки не позволяет получить плоскую площадку необходимого размера для установки ПЭП, то измеряют толщину металла УЗ-методом в точках вокруг выборки. Измерение глубины выборки выполняют прямым измерением (например, штангенциркулем или индикатором). Толщина металла ОК в зоне контроля в месте выборки находится как разность между значением минимальной толщины в окрестности выборки поданным измерений УЗ-методом и максимальным значением глубины выборки, полученным прямым измерением. Погрешность этого измерения принимается равной погрешности измерения УЗ-методом.
12.4 Подготовка к проведению измерения толщины с применением электромагнитноакустических преобразователей
12.4.1 Для проведения измерения толщины металла ОК в зоне контроля должны быть освобождены от тепловой изоляции, отслаивающегося лакокрасочного покрытия. Данные работы осуществляют соответствующие подразделения организации — владельца или изготовителя ОК. Выполнение указанных операций в обязанности специалиста по УЗК не входит.
12.4.2 Подготовка поверхности металла в зоне контроля для измерения толщины с применением ЭМАП не требуется.
12.4.3 При выполнении измерения толщины металла через лакокрасочное покрытие или по поверхности с коррозионными повреждениями величина зазора между рабочей поверхностью ЭМАП и поверхностью ввода должна быть не более определенной по техническим характеристикам ЭМА толщиномера.
12.4.4 Рекомендуется использовать шаблон (маску) из диэлектрического материала (например, тонкий текстолит, стеклопластик) с разметкой зоны контроля (точки, полосы).
12.4.5 Измерение толщины металла через электропроводящие материалы (прослойки) не допускается.
12.5 Настройка аппаратуры
12.5.1 Настройка аппаратуры включает две операции:
- настройка на скорость УЗ в металле ОК (для всех СИ);
- установка нуля (для толщиномера) или настройка скорости развертки (для дефектоскопа).
12.5.2 Настройку проводят с применением той же контактной среды, что и при проведении измерений.
12.5.3 Настройку толщиномеров на скорость УЗ в металле проводят:
- для монометаллов — по образцу Т2;
- для биметаллов — по образцу ТБ1.
Настройка толщиномера на скорость УЗ в металле ОК заключается в такой регулировке прибора, чтобы показания толщиномера совпадали с толщиной образца, указанной в паспорте или сертификате калибровки;
12.5.4 Настройку дефектоскопа на скорость УЗ проводят:
- для монометаллов — по образцу Т1;
- для биметаллов — по образцу ТБ1;
- для АНП при измерении со стороны основного металла — по образцам ТН1 или ТНЗ;
- для АНП при измерении со стороны наплавленной поверхности — по образцам ТН2 или ТНЗ;
- для АНП биметаллических труб с применением НП — по образцу ТНН1.
Настройка на скорость УЗ в металле ОК заключается в такой регулировке прибора, чтобы:
- расстояние между эхо-сигналами от ступеней 10 и 20 мм образца Т1 соответствовало разности толщины металла в ступенях, указанных в паспорте и сертификате калибровки;
- расстояние между первым и вторым донными эхо-сигналами из образца ТБ1 (рисунок 14) составляло Н (при использовании дефектоскопа) или показание толщиномера составляло Н (при использовании толщиномера);
- расстояние между эхо-сигналами от впадины и выступа образцов ТН1, ТНЗ или ТНН1 (рисунки 15—17) соответствовало глубине паза или плоскодонного отражателя;
- расстояние между первым и вторым донными эхо-сигналами ступени образца ТН2 или покрытия под пазом образца ТНЗ (рисунок 16) соответствовало толщине покрытия на данном участке образца.
Рисунок 14 — Схема настройки на скорость УЗ в металле ОК по образцу ТБ1
Рисунок 15 — Настройка на скорость УЗ в АНП по образцу ТН1
Рисунок 16 — Схема настройки на скорость УЗ в металле ОК по образцу ТНЗ
6) Схема настройки дефектоскопа
а) Схема измерения
в) Осциллограммы экрана дефектоскопа
И — излучатель; П — приемник; Нп — толщина АНП; Н— глубина паза (плоскодонного отверстия)
Рисунок 17 — Настройка параметров дефектоскопа при измерении АНП с применением НП на образце ТНН1
12.5.5 Установку нуля толщиномеров проводят в соответствии с руководством по эксплуатации на НО.
12.5.6 Установку нуля толщиномеров для монометаллов и биметаллов выполняют по образцу Т1. Допускается установка нуля толщиномера по НО, входящему в комплект или встроенному в СИ.
12.5.7 Настройка скорости развертки дефектоскопов выполняется:
- для монометаллов — по образцу Т2;
- для биметаллов — по образцу ТБ1;
- для АНП со стороны основного металла — по донному эхо-сигналу в зоне контроля;
- для АНП при измерении со стороны наплавленной поверхности — по образцам ТН2 или ТНЗ;
- для АНП биметаллических труб с применением НП — по образцу ТНН1 (рисунок 17).
Примечание — Операции настройки для моно- и биметалла допускается проводить на участке ОК в зоне контроля, доступном прямому измерению, с погрешностью, не превышающей ±0,05 мм.
Расстояние R между передними торцами НП вычисляют по формуле
/? = 2 • (/7 • tga) - (^ +/2), (3)
где R— расстояние между передними торцами НП, мм;
Н—расстояние от поверхности ввода до донной поверхности ТНН1, мм;
a — угол ввода ПЭП, град;
/2 величины стрел излучающего преобразователя и принимающего преобразователя соответственно, мм.
12.5.8 Настройка скорости УЗ в металле ОК может быть выполнена путем установки на приборе известного значения этой скорости согласно руководству по эксплуатации.
12.5.9 Во всех случаях настройки и измерения высота измеряемого эхо-сигнала должна быть одинаковой и находиться в пределах 1/2—2/3 высоты экрана дефектоскопа.
12.5.10 Если форма измеряемого эхо-сигнала на экране прибора существенно отличается от формы эхо-сигнала, полученного при настройке, то путем вращения или небольшого перемещения ПЭП следует получить идентичный эхо-сигнал.
12.5.11 Форма эхо-сигнала может быть оптимизирована использованием специальных регулировок дефектоскопа, например отсечки. При этом положения оптимизирующих регулировок в режимах настройки и измерения не должны отличаться.
12.5.12 После окончания настройки ее следует проверить на НО или в контрольной точке на ОК в зоне контроля по толщине, отличающейся от настроечной не более чем на 10 %. Если при этом будет получено отклонение от фактической толщины металла ОК в зоне контроля более чем на величину дискретности измерения прибора, то настройку следует повторить.
12.5.13 После проверки настройки прибора необходимо зафиксировать и не изменять в процессе контроля.
12.5.14 При настройке и измерениях должно быть обеспечено плотное, равномерное прилегание ПЭП к поверхности ввода.
12.6 Проверка настройки средства измерения
12.6.1 Проверку настройки СИ на НО проводят в следующих случаях:
- перед началом работы;
- через каждые два часа работы;
- в случае возможного нарушения настройки;
- после окончания работы.
12.6.2 В случае обнаружения несоответствия в параметрах настройки их необходимо скорректировать и повторить измерение толщины металла всех ОК, проконтролированных после предыдущей проверки настройки.
13 Проведение ультразвукового контроля
13.1 Подготовительные мероприятия
Перед проведением контроля специалист должен:
а) получить задание (заявку) на контроль с указанием:
1) идентификационных данных ОК;
2) зоны контроля, схемы разметки точек измерения и их нумерации;
3) марки стали или сплава, а для АНП — номинальной толщины с указанием марки электродов;
4) номинальной толщины металла в зоне контроля с допускаемыми отклонениями;
5) состояния поверхности металла в зоне контроля;
6) сведений о характере коррозионных и эрозионных повреждений внутренней поверхности при эксплуатационном контроле;
б) ознакомиться с ТИ и/или ТКК;
в) проверить наличие и соответствие разметки в зоне контроля, указанной в ТКК;
г) выполнить настройку (регулировку) СИ в соответствии с 7.1—7.3:
1) установить ноль (при работе с толщиномером) или настроить задержку и скорость развертки дефектоскопа;
2) настроить СИ на скорость УЗ в металле ОК;
3) проверить показания СИ на НО.
13.2 Технология измерения толщины металла
Измерение толщины металла в зоне контроля проводят:
- дискретно (по отдельным точкам), рисунок 18;
- непрерывным сканированием по полосам (линиям), рисунок 19;
- непрерывным сканированием участка поверхности, рисунок 20.
L — расстояние между точками измерений (не менее 25 и не более 150 мм) в зависимости от размера (диаметра) OK; L1 — расстояние между двумя соседними проходами
Рисунок 18 — Дискретное измерение толщины металла в зоне контроля
1130
1200
Рисунок 19 — Измерение толщины металла в зоне контроля непрерывным сканированием по полосам (линиям)
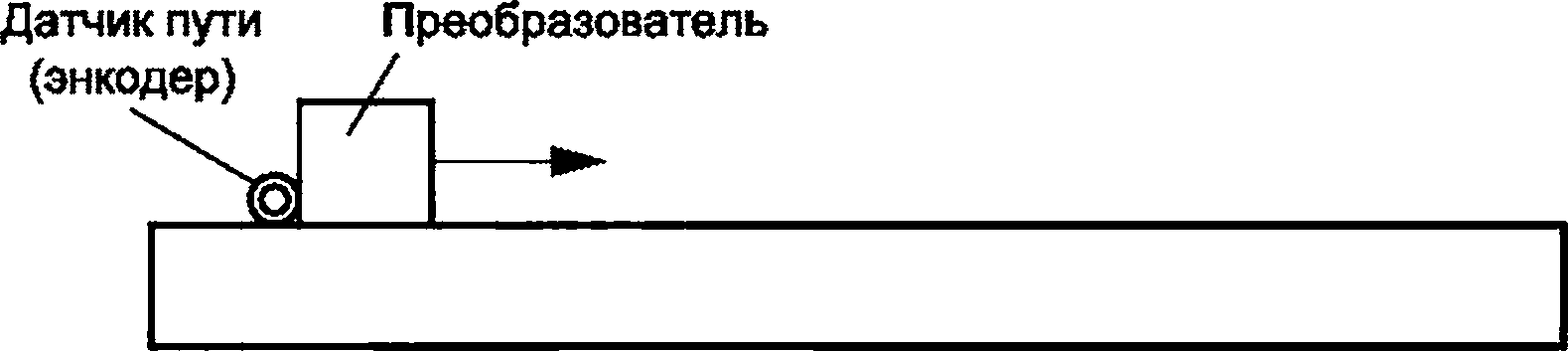
Рисунок 20 — Измерение толщины металла в зоне контроля непрерывным сканированием участка поверхности
13.3 Измерение толщины монометалла в зоне контроля с применением пьезоэлектрических преобразователей дискретно (по отдельным точкам)
13.3.1 На каждый участок, подготовленный для проведения измерений, наносят слой контактной среды.
13.3.2 Устанавливают на подготовленный участок ПЭП и выполняют однократное измерение толщины металла. Если при выполнении измерений произошла грубая ошибка, т. е. погрешность измерений существенно превысила ожидаемую в данных условиях, то результат не учитывают и выполняют три измерения взамен ошибочного. За результат измерения принимают среднее арифметическое значение.
13.3.3 При измерении толщины трубопроводов РСП-экран, разделяющий призмы ПЭП, должен быть ориентирован перпендикулярно к образующей трубы.
13.3.4 При измерении толщины УЗ-дефектоскопами необходимо обеспечить равенство амплитуд измеряемых эхо-сигналов с отклонением не более ±2 дБ и идентичность считывания результата измерения.
13.3.5 По окончании проведения контроля следует выполнить анализ полученных результатов измерения, фиксировать места с недопустимыми утонениями металла в зоне контроля.
13.4 Измерение толщины биметалла в зоне контроля с использованием пьезоэлектрических преобразователей дискретно (по отдельным точкам)
13.4.1 При измерении толщины биметалла следует руководствоваться требованиями 13.3.
13.4.2 При измерении толщины биметалла со стороны основного металла следует использовать ПСП с частотой от 2 до 6 МГц включительно с жестким протектором. Конструкция и размеры ПЭП должны обеспечивать получение качественного акустического контакта с поверхностью, металла. Это достигается путем выбора ПЭП с размером контактной поверхности, максимально прилегающей к поверхности металла в зоне контроля. При этом следует применять ПЭП с более высоким значением номинальной частоты и узкой диаграммой направленности.
13.5 Измерение толщины антикоррозионных наплавленных поверхностей в зоне контроля с использованием пьезоэлектрических преобразователей дискретно (по отдельным точкам)
13.5.1 При измерении толщины АНП следует руководствоваться требованиями 13.3.
13.5.2 При измерении со стороны основного металла толщина АНП определяется как разность положений эхо-сигналов от донной поверхности и зоны сплавления.
13.5.3 При отсутствии эхо-сигнала от зоны сплавления перед первым донным эхо-сигналом следует использовать для измерения второй или третий донный эхо-сигнал и соответствующий эхо-сигнал от зоны сплавления (рисунок 21) или применять НП.

Нп — толщина покрытия
Рисунок 21 — Экран дефектоскопа при измерении толщины АНП на биметаллической трубе и с увеличенным масштабом развертки
13.5.4 При невозможности измерения толщины АНП из-за отсутствия эхо-сигнала от зоны сплавления такие участки оконтуривают и составляют эскиз с указанием толщины АНП по краям участка и полной толщины в требуемой точке измерения.
13.5.5 При измерении толщины АНП с применением НП следует использовать два жестко скрепленных преобразователя с одинаковым углом ввода в диапазоне от 38° до 52°, частотой от 2 до 5 МГц, подключенных к дефектоскопу по раздельной схеме (рисунок 22). При измерении толщины плакирующего слоя труб ПЭП должны быть расположены на трубе вдоль ее образующей.
13.5.6 Для измерения толщины АНП со стороны наплавленной поверхности следует использовать прямой РСП с глубиной фокуса, превосходящей толщину наплавленной поверхности. При номинальной толщине наплавленной поверхности от 2 до 8 мм следует использовать ПЭП с частотой от 4 до 6 МГц, имеющие фокусное расстояние от 4 до 10 мм, а наплавленной поверхности с номинальной толщиной более 8 мм — прямые РСП с частотой от 4 до 5 МГц, имеющие фокусное расстояние от 20 до 30 мм. Диаметр контактной поверхности ПЭП должен составлять не более 16 мм.
13.5.7 На площадке, выделенной для измерения толщины НП, необходимо выбрать такое положение ПЭП, при котором эхо-сигнал от границы раздела двух металлических сред имеет наиболее гладкую форму и крутой передний фронт.
13.5.8 Заведомо недостоверные показания (эхо-сигналы от дефектов вблизи зоны сплавления, границ отдельных слоев (или проходов) (рисунок 23); структурные шумы из наплавки) не учитывают. При отнесении показаний эхо-сигналов к недостоверным руководствуются показаниями глубиномера дефектоскопа или положением эхо-сигналов на развертке экрана дефектоскопа.
Сигнал от зоны сплавления
Донный сигнал
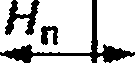
И — излучатель; П — приемник; Нп — толщина АНП Рисунок 22 — Измерение толщины АНП с применением НП
Основной
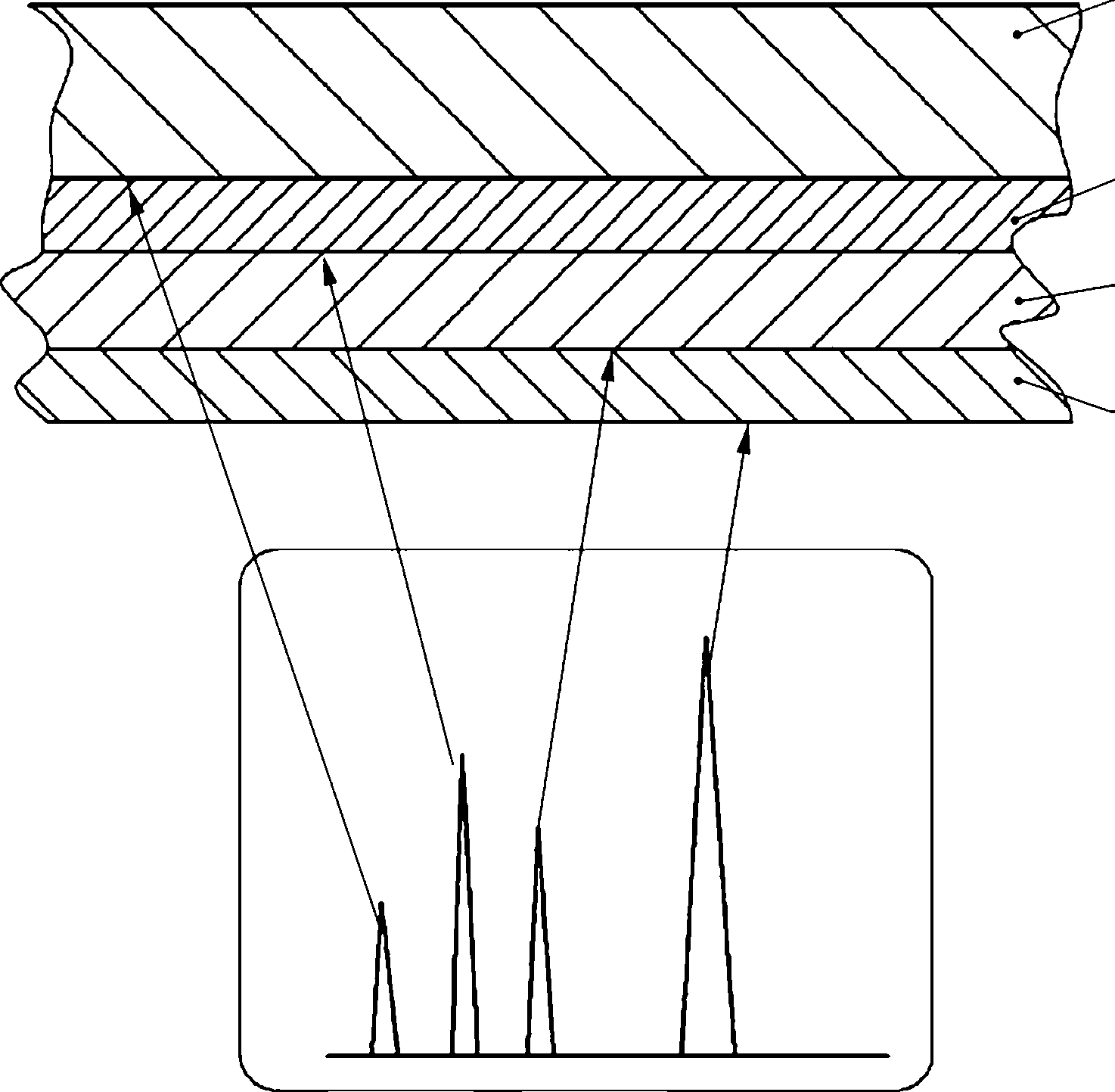
металл
Слой 1
Слой 2
Слой 3
Рисунок 23 — Отражения от зоны сплавления АНП с основным металлом
13.5.9 При измерении толщины АНП со стороны наплавленной поверхности толщина АНП определяется положением эхо-сигнала от зоны сплавления АНП с основным металлом.
13.5.10 Если при контроле со стороны наплавленной поверхности не удается получить отражение (эхо-сигнал) от зоны сплавления, то в заключении по результатам контроля отмечают отсутствие технической возможности измерения толщины АНП в данной точке.
13.6 Измерение толщины монометалла в зоне контроля с применением электромагнитноакустических преобразователей дискретно (по отдельным точкам) в статическом режиме
13.6.1 Для предохранения рабочей поверхности ЭМАП от повреждений рекомендуется на его рабочую поверхность поместить предохранительную прокладку (толщиной не более 0,5 мм) из диэлектрического материала (например, лейкопластырь, скотч, текстолит, стеклопластик).
13.6.2 При использовании предохранительной прокладки настройку СИ необходимо проводить через прокладку.
13.6.3 ЭМАП необходимо устанавливать на поверхность ввода в зоне контроля, поднося его под углом от 30° до 60° к поверхности. Перед снятием преобразователь необходимо наклонить под углом к поверхности ввода. Не рекомендуется передвигать ЭМАП по поверхности ввода без прокладки.
13.6.4 Устанавливают на отмеченный участок для проведения измерений ЭМАП и выполняют однократное измерение толщины металла. Если при выполнении измерений произошла грубая ошибка, т. е. погрешность измерений существенно превысила ожидаемую в данных условиях, то результат не учитывают и выполняют три измерения взамен ошибочного. За результат измерения принимают среднее арифметическое значение.
13.6.5 При измерении толщины металла трубопровода ЭМАП необходимо устанавливать так, чтобы линия, соединяющая полюса магнита, располагалась вдоль осевой линии трубы.
13.6.6 Если при установке ЭМАП на поверхность ввода в зоне контроля амплитуда донного эхо-сигнала не достигает уровня строба, то необходимо:
- развернуть ЭМАП вокруг своей оси и попытаться добиться увеличения амплитуды;
- повысить чувствительность СИ (увеличить амплитуду эхо-сигналов).
13.6.7 Выполнить анализ полученных результатов измерения, фиксировать места с недопустимыми утонениями металла в зоне контроля.
13.7 Измерение толщины металла в зоне контроля с применением электромагнитноакустических преобразователей по полосам (линиям) в динамическом режиме
13.7.1 Измерения следует проводить вручную или с помощью сканера.
13.7.2 Вручную контроль следует проводить плавно перемещая ЭМАП по прокладке (например, тонкий текстолит или стеклопластик), наложенной на поверхность ввода в зоне контроля.
13.7.3 При использовании сканера с ЭМАП и датчиком пути его следует установить на поверхность ввода в зоне контроля, выполнить сканирование по первой полосе (линии), получить профилограмму толщины металла в зоне контроля с указанием измеренных значений толщины металла и координат, сохранить данные в память ЭМА толщиномера.
13.7.4 Скорость сканирования определяется руководством по эксплуатации ЭМА толщиномера и должна быть указана в ТИ и/или ТКК. Скорость сканирования не должна превышать 100 мм/с.
13.7.5 Выполняют сканирование последующих полос, сохраняют результаты в память ЭМА толщиномера.
13.7.6 Выполняют анализ полученных результатов измерения, фиксируют места с недопустимыми утонениями металла в зоне контроля.
13.8 Измерение толщины металла в зоне контроля с применением электромагнитноакустических преобразователей непрерывным сканированием
13.8.1 Измерение толщины металла следует проводить вручную или с помощью сканера.
13.8.2 Вручную измерение толщины следует проводить, плавно перемещая преобразователь по поверхности ввода вдоль или поперек зоны контроля. Шаг сканирования — не более 5 мм. В случае обнаружения утонений необходимо зафиксировать их координаты и значения толщины. Рекомендуется проводить измерение, перемещая преобразователь по прокладке (например, тонкий текстолит или стеклопластик). Скорость сканирования не должна превышать 100 мм/с.
13.8.3 При использовании сканера с ЭМАП и датчиком пути его следует установить на поверхность ввода в зоне контроля, выполнить сканирование по первой полосе (линии), получить профило-24
грамму толщины металла в зоне контроля за один проход с указанием измеренных значений толщины металла и координат. Полученные данные необходимо сохранить в память ЭМА толщиномера.
13.8.4 Скорость сканирования определяется руководством по эксплуатации ЭМА толщиномера и должна быть указана в ТИ и/или ТКК. Скорость сканирования не должна превышать 100 мм/с.
13.8.5 Проводят многопроходное измерение толщины металла в зоне контроля, получают и записывают в память ЭМА толщиномера профилограммы каждого из проходов. Шаг сканирования должен быть указан в ТИ и/или ТКК. При отсутствии указаний шаг сканирования следует определять по приложению Б.
13.8.6 Выполняют анализ полученных результатов измерения, фиксируют места с недопустимыми утонениями металла в зоне контроля.
13.9 Измерение толщины металла в зоне контроля с применением электромагнитноакустических преобразователей без фиксации толщины стенки
13.9.1 Для удобства проведения контроля следует закрепить на поверхности ОК в зоне контроля диэлектрическую прокладку (например, тонкий текстолит или стеклопластик) с разметкой.
13.9.2 Устанавливают ЭМАП на участок контроля.
13.9.3 Проводят сканирование согласно ТИ и/или ТКК. Шаг сканирования — не более 5 мм.
13.9.4 Определяют места с минимальной толщиной стенки ОК в зоне контроля и фиксируют их.
13.10 Измерение остаточной толщины металла в зонах контроля с коррозионными и эрозионными повреждениями
13.10.1 Проведение измерения толщины металла ОК в зоне контроля на этапе эксплуатации следует выполнять согласно требованиям [5].
13.10.2 Перед измерениями следует получить сведения о характере коррозионных и эрозионных повреждений внутренней поверхности (например, визуальным осмотром, с помощью оптических СИ, в частности с использованием СИ на основе волоконной оптики, или радиографическим контролем), которые должны быть указаны в заявке на проведение контроля.
13.10.3 Выбор используемого СИ и преобразователя зависит от геометрии ОК, предполагаемой толщины металла в зоне контроля и состояния донной поверхности. Параметры преобразователей должны быть выбраны из расчета, что их контактная поверхность должна максимально прилегать к поверхности ввода.
13.10.4 Для измерения толщины металла в местах локальных утонений, связанных с наличием общей коррозии, язвенной (точечной) коррозии или эрозионных поражений, используют СИ с цифровым дисплеем или с разверткой типа А.
Для СИ с цифровым дисплеем используют преобразователи, указанные производителем для значения предполагаемой остаточной толщины металла в зоне контроля.
Для СИ с разверткой типа А выбор параметров преобразователя осуществляют следующим образом:
- частота преобразователя должна быть такой, чтобы не менее 1,5 длины волны охватывали стенку ОК;
- для толщин 10 мм и более рекомендуется использовать ПСП или ЭМАП;
- для толщин менее 10 мм необходимо использовать прямой РСП.
13.10.5 Для измерения толщины металла в зоне контроля с язвенной (точечной) коррозией используют СИ с разверткой типа А и прямой РСП с фокусным расстоянием, соответствующим предполагаемому расстоянию до точечной (язвенной) коррозии.
13.10.6 Если предполагается наличие язвенной (точечной) коррозии малого диаметра, то чувствительность обнаружения настраивают на НО с плоскодонными отверстиями малого диаметра в том же диапазоне толщин, что и для предполагаемой язвенной (точечной) коррозии.
13.10.7 При определении остаточной толщины металла в местах локальных утонений, связанных с наличием эрозионных поражений, общей коррозии и коррозии пятнами в заранее намеченных зонах контроля должны быть выполнены измерения с шагом не более 3 мм. При возможности получения нескольких донных эхо-сигналов предпочтительно использовать способ измерения согласно рисунку 16 (для ПСП). За результат измерения принимают минимальное показание СИ.
13.10.8 Если при измерении остаточной толщины металла на границе зоны контроля обнаружено утонение, то зона контроля должна быть расширена для определения границы утонения.
13.10.9 Для определения участков с наименьшей остаточной толщиной металла и уточнения границы утонения следует применять схему сплошного сканирования. Рекомендуется использовать СИ с разверткой типа А, а также с функцией записи результатов контроля. Шаг сканирования должен быть не более 5 мм. Скорость сканирования не должна превышать 100 мм/с.
13.10.10 Для измерения толщины металла в зонах контроля, где предполагаются участки с язвенной (точечной) коррозией, следует применять схему сплошного сканирования с функцией записи результатов контроля. Шаг сканирования должен быть не более 5 мм. Скорость сканирования не должна превышать 100 мм/с. При поиске точечной коррозии используют только первый донный эхо-сигнал. Вместе с донным эхо-сигналом могут возникать эхо-сигналы от точечной коррозии.
После обнаружения и фиксации способом сплошного сканирования зон контроля с язвенной (точечной) коррозией их необходимо исследовать измерением остаточной толщины металла с шагом не более 3 мм. За результат измерения принимают минимальное показание СИ.
Если невозможно идентифицировать тип отражателя как коррозию или включение, то проводят дополнительное исследование с помощью наклонных преобразователей. Чтобы различать включения и точечную коррозию, лучше всего подходят 45-градусные НП.
13.10.11 При измерении остаточной толщины металла до 20,0 мм, подвергнутого коррозионным или эрозионным повреждениям, следует принимать во внимание, что СИ не обеспечивают фиксацию изменения толщины, связанную с наличием одиночных язв сферической формы диаметром до 2,5 мм.
13.10.12 Изменения толщины металла, наблюдаемые на расстоянии, примерно равном длине УЗ-волны и меньше, при измерении толщины не фиксируются. Наименьший радиус кривизны углубления в месте наименьшей остаточной толщины должен быть более 1,5 мм.
13.10.13 При отсутствии сведений о характере коррозионных и эрозионных повреждений донной поверхности ОК в зоне контроля они могут быть получены при проведении исследования путем установки преобразователя в заранее намеченной зоне контроля. В случае, когда:
- СИ показывает значение толщины, равное с учетом погрешности измерения номинальной толщине металла, — ОК в зоне контроля коррозионным повреждениям не подвергнут;
- СИ показывает значение толщины металла меньше номинального значения (частным случаем является стабильное нулевое показание) — ОК в зоне контроля подвергнут равномерной коррозии;
- СИ при перестановке преобразователя показывает различные значения толщины металла, в том числе нулевое и номинальное значения толщины металла, а также значения толщины металла больше и меньше номинальной — ОК в зоне контроля подвергнут пятнистой коррозии;
- СИ показывает номинальное значение толщины металла, а при дальнейшей перестановке преобразователя на ограниченном участке — нулевое (или нестабильное) значение и значение меньше номинального — ОК в зоне контроля подвергнут язвенной коррозии или локальной коррозии (нулевое и нестабильное показания СИ соответствуют установке преобразователя над скосом язвы).
13.10.14 Если не удается получить стабильные показания толщины металла в зоне контроля при использовании СИ с цифровым дисплеем или результат измерения существенно отличается от ожидаемого и не связан с грубой ошибкой измерения, то необходимо эти участки проконтролировать СИ с разверткой типа А, так как причиной уменьшения измеренных значений толщины может быть нарушение сплошности металла. В этом случае настройку скорости развертки и глубиномера СИ проводят на номинальную толщину стенки ОК.
13.10.15 Выполняют анализ полученных результатов измерения, фиксируют места с недопустимыми утонениями металла в зоне контроля. При необходимости оценивают характер коррозионных и эрозионных повреждений донной поверхности ОК.
14 Учетная и отчетная документация
14.1 Требования к учетной документации
14.1.1 Требования к учетной документации (журналам) по неразрушающему контролю изложены в [2]—[5].
14.1.2 Журнал результатов УЗК должен иметь сквозную нумерацию страниц, быть сброшюрован и скреплен подписью руководителя подразделения неразрушающего контроля.
14.1.3 Все исправления и изменения в журнале должны быть заверены подписью руководителя подразделения неразрушающего контроля с указанием даты их внесения.
14.1.4 В журнал допускается вносить дополнительные данные.
14.1.5 Ведение журнала в электронном виде допускается при условии обеспечения восстановления результатов УЗК в случае утраты или порчи отчетной документации.
14.2 Требования к отчетной документации
14.2.1 На основании учетной документации должна быть оформлена отчетная документация в виде заключения (протокола).
14.2.2 Требования к отчетной документации, форме и содержанию заключения (протокола) по неразрушающему контролю изложены в [2]—[5].
14.2.3 В заключение (протокол) допускается вносить дополнительные данные.
14.2.4 Рекомендуемая форма заключения представлена в приложении В.
15 Требования к метрологическому обеспечению
15.1 Метрологическое обеспечение УЗТ, включая метрологическое обеспечение аттестованных объектов и методик измерений, должно соответствовать требованиям [12] и [13] с учетом ГОСТ Р 50.05.16.
15.2 СИ, входящие в сферу государственного регулирования, применяемые для измерения толщины металла ОК, должны быть утвержденного типа и пройти своевременную поверку.
15.3 Преобразователи, применяемые при измерении толщины металла ОК, должны иметь паспорт, заводской номер и маркировку.
15.4 НО и калибровочные образцы, применяемые для настройки (регулировки) СИ, должны соответствовать требованиям ГОСТ Р 50.05.16.
15.5 НО и калибровочные образцы, применяемые для настройки (регулировки) СИ, в случае отнесения к аттестованным объектам, в соответствии с [13], подлежат первичной и периодической аттестациям (подтверждение метрологических характеристик). Периодичность подтверждения метрологических характеристик устанавливают при первичной аттестации.
15.6 Проекты методик УЗК подлежат рассмотрению в соответствии с ГОСТ Р 50.04.07—2022 (пункт 6.15). Метрологическая экспертиза методик УЗК проводится в соответствии с ГОСТ Р 8.1015.
16 Требования безопасности
16.1 СИ для измерения толщины металла ОК являются переносными электроприемниками, поэтому при их эксплуатации должны выполняться требования по электробезопасности в соответствии с [14].
16.2 Перед допуском к проведению контроля все лица, участвующие в его выполнении, должны проходить соответствующий инструктаж по охране труда с регистрацией в журнале регистрации инструктажа на рабочем месте.
16.3 Инструктаж следует проводить периодически в сроки, установленные организационно-распорядительным документом организации.
16.4 При выполнении контроля на высоте, в стесненных условиях, а также внутри сосудов специалисты и обслуживающий персонал проходят дополнительный инструктаж по охране труда согласно положению, действующему в организации.
16.5 Специалисты по УЗК, участвующие в выполнении измерения толщины металла ОК, должны знать и выполнять общие требования по охране труда, установленные для работников цехов и участков, в которых проводят толщинометрию.
16.6 Требования относительно защиты от вредного воздействия постоянных магнитных полей должны соответствовать требованиям [15]. Специалисты должны быть обеспечены специальной защитной одеждой, не стесняющей движение (костюмами, комбинезонами, халатами), средствами защиты ног и рук, средствами защиты головы, обтирочными материалами (обрезками ткани с хорошей смачиваемостью), кремом для рук, мылом, полотенцами, блокнотами и пишущими инструментами. Номенклатура и нормы расхода средств индивидуальной защиты и материалов устанавливаются организацией в зависимости от объемов и условий работы.
16.7 При проведении УЗК вблизи мест выполнения сварочных работ рабочее место специалиста по УЗК должно быть ограждено светозащитными экранами.
16.8 При проведении работ в зоне ионизирующего излучения должны соблюдаться требования по обеспечению радиационной безопасности, установленные законодательством Российской Федерации в области использования атомной энергии [16].
16.9 Требования безопасности при проведении УЗК должны соответствовать ГОСТ Р 55724— 2013 (раздел 12).
Приложение А (обязательное)
Процедура определения погрешности измерения
А.1 Определение погрешности при измерении толщины моно- и биметаллов
А.1.1 Для выполнения измерений подготавливают не менее двух образцов, изготовленных из фрагментов зон контроля металла или по той же технологии, что и контролируемый металл. Аттестованное значение толщины первого образца должно быть близким (отклоняться не более чем на ±3 %) к номинальному значению толщины ОК. Аттестованное значение толщины второго образца должно быть близким (отклоняться не более чем на ±3 %) к минимально допустимому значению толщины ОК. Значение оценки А суммарной погрешности измерения толщины металла определяется для каждого образца.
А. 1.2 СИ настраивают в соответствии с 12.5.
А.1.3 На каждом образце подготавливают участки для выполнения измерений толщины металла в соответствии с разделом 8, 12.3.1, 12.3.2.
А.1.4 На подготовленных участках образцов проводят измерение толщины металла УЗ-методом не менее чем в 30 точках для каждого образца.
А.1.5 На тех же участках проводят определение действительной толщины хд металла прямыми измерениями (например, микрометром или штангенциркулем). Предельно допустимое значение модуля оценки суммарной погрешности измерения хд составляет 0,05 мм.
А.1.6 Оценку систематической составляющей погрешности измерений 5 проводят, вычисляя значение по формуле
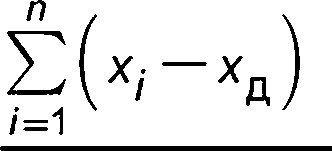
(А.1)
где п — число измерений;
Xj — результат /-го измерения толщины УЗ-прибором, мм;
хд — действительная толщина образцов, мм.
А.1.7 Оценку среднего квадратического отклонения случайной составляющей погрешности измерений о вычисляют по формуле
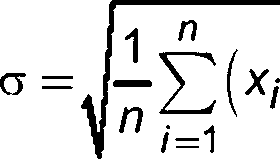

(А.2)
Верхнюю оценку среднего квадратического отклонения случайной составляющей погрешности измерений ов вычисляют по формуле
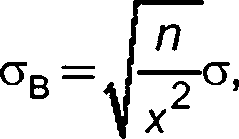
(А.З)
где х2 — 95 %-ный квантиль х2-распределения с п степенями свободы.
А.1.8 Верхнее и нижнее значения суммарной погрешности измерений приближенно определяются границами доверительного интервала для Р = 0,95
5-0<Д<5 + 0,
где 0 — полуширина доверительного интервала
0 — ^(1,96ов) + + Адт + Ащер + ^пар + ^ск >
(А.4)
(А.5)
где Дси — предел погрешности УЗ СИ,
Дэт — доверительные границы погрешности аттестованного значения настроечного образца,
Дшер — доверительные границы погрешности измерения, связанной с разностью значений шероховатости в различных точках образцов и ОК,
Дпар — доверительные границы погрешности измерения, связанной с непараллельностью поверхности ввода и донной поверхности образцов и ОК,
Дск — доверительные границы погрешности измерения, связанной с разностью значений скорости ультразвука в различных точках образцов и ОК.
А. 1.9 Если оценка систематической составляющей погрешности измерений 5 не превышает 1/3 О, то при вычислении суммарной погрешности измерений ею можно пренебречь.
А.1.10 Округление значений результата измерения толщины металла ОК вместе с оценкой суммарной погрешности измерения этой величины производится в соответствии с ГОСТ Р 8.932.
А.2 Определение погрешности при измерении толщины антикоррозионной наплавленной поверхности
А.2.1 Для выполнения измерений подготавливают образец с АНП, выполненный из фрагмента ОК или по той же технологии, что и ОК.
А.2.2 СИ настраивают в соответствии с требованиями 12.5.
А.2.3 Не менее чем в 60 точках, расположенных на одной линии, перпендикулярной к направлению валиков или лент наплавки, выполняют измерения толщины наплавленной поверхности.
А.2.4 Образец разрезают по линии измерений, поверхность реза шлифуют и протравливают.
А.2.5 В тех же 60 точках проводят определение действительной толщины наплавленной поверхности хд/, где /— номер точки, прямым измерением с погрешностью не более ±0,05 мм.
А.2.6 Дальнейшие действия выполняют в соответствии с А. 1.6—А.1.10, заменяя в формулах (А.1), (А.2) хд измеренными значениями хд/.
Приложение Б (обязательное)
Требования к содержанию технологической карты контроля и технологической инструкции при измерении толщины металла
Б.1 Содержание технологической карты контроля и технологической инструкции при измерении толщины металла
В общем случае ТКК и ТИ должны содержать следующую информацию:
- идентификационные данные ОК [например, наименование детали (сборочной единицы), номер чертежа, обозначение АНП];
- схему разметки ОК в зоне контроля для измерения толщины или наименование и номер КД или заявки на контроль, содержащие эту схему;
- обозначение марки стали или сплава основного металла, для АНП — номинальную толщину с указанием марки электродов или марки стали наплавленного слоя;
- указание о номинальной толщине металла в зоне контроля;
- информацию о применяемых средствах контроля; при этом параметры преобразователей и НО должны быть определены однозначно;
- указание о погрешности при измерении толщины металла;
- критерии оценки годности металла в зоне контроля;
- порядок подготовки поверхности и разметки зоны контроля;
- порядок проведения измерения толщины металла в соответствии с положениями настоящего стандарта.
В случае проведения контроля непрерывным сканированием или сканированием по полосам в ТКК и ТИ дополнительно должны быть указаны:
- шаг сканирования в зависимости от типа используемого преобразователя;
- максимальная скорость проведения сканирования;
- схемы проведения сканирования по поверхности зоны контроля;
- порядок наименования файлов, содержащих результаты измерения толщины;
- процедура обработки результатов сканирования;
- требования по обеспечению хранения файлов, содержащих результаты сканирования.
ТКК или ТИ могут включать дополнительные сведения. При необходимости, в ТКК или ТИ включают указания на условия и порядок проведения контроля (сведения о месте проведения работ, допускаемом диапазоне рабочих температур), составе звена специалистов, проводящих контроль, краткое описание последовательности операций по обработке зоны контроля после проведения контроля.
П ример заполнения ТКК приведен на рисунках Б.1 и Б.2.
Б.2 Пример заполнения технологической карты контроля при измерении толщины металла в зоне контроля с применением ультразвукового толщиномера
Наименование организации | № 0001-УЗТ | |
Подразделение, разработавшее карту | Технологическая карта контроля толщины металла гиба № XXX | Лист 1, листов 3 |
1 Объект контроля | |
1.1 Наименование контролируемого оборудования | Трубопровод острого пара |
1.2 Зона контроля | Крутозагнутый отвод |
1.3 Размеры объекта контроля, мм | 0325х 18 |
1.4 Материал | Сталь 20 |
1.5 Объем контроля | см. разметку |
2 Документация по контролю | |
2.1 Документ(ы), устанавливающий(е) нормы оценки | Правила контроля |
2.2 Документ, устанавливающий методику контроля | ГОСТ Р 50.05.03—2022 |
3 Средства контроля | |
3.1 Толщиномер (тип) | DMS 2 (DMS 2Е), DM-4 или аналог |
3.2 Преобразователь | DA-312 или аналог |
3.3 Настроечный образец: | 1—30 мм ст20 № Т4.У — для толщин 1—30 мм |
3.4 Материал настроечного образца | Сталь 20 |
3.5 Шероховатость поверхности настроечного образца | не более Ra = 6,3 мкм |
3.6 Образец шероховатости поверхности (сравнения) | Ra = 6,3 мкм |
4 Условия проведения контроля | |
Условия проведения контроля |
|
Карту разработал: | Карту проверил: |
_____________/Ф.И.О., должность, № удостоверения (подпись, дата) | _____________/Ф.И.О., должность, № удостоверения (подпись, дата) |
Рисунок Б.1, лист 1
Наименование организации | № 0001-УЗТ | |
Подразделение, разработавшее карту | Технологическая карта контроля толщины металла гиба № XXX | Лист 2, листов 3 |
5 Подготовка к контролю | |
5.1 При производственной необходимости непосредственно перед производством работ сведения о радиационной обстановке оформляются в установленном порядке нарядом-допуском | |
5.2 На объекте контроля в зоне контроля должна быть подготовлена разметка для измерения толщины, выполненная термостойким химическим маркером | |
5.3 На объекте контроля в зоне контроля должны быть подготовлены участки размером 30 * 30 мм в соответствии со схемой разметки объекта контроля в зоне контроля | |
5.4 Проверка качества подготовки поверхности |
|
5.5 Настройка толщиномера | - настройка толщиномера на настроечном образце в соответствии с руководством по эксплуатации |
5.6 Разметка объекта контроля в зоне контроля | - эскиз, см. схему а |
6 Порядок проведения контроля | |
Измерения толщины |
|
7 Оценка качества | |
Номинальная толщина металла объекта контроля в зоне контроля, мм | 18 |
Минимально допустимая толщина металла объекта контроля в зоне контроля, мм (согласно правилам контроля) | 14,5 |
Погрешность измерения, мм | ±0,2 при Р = 0,95 |
Качество объекта контроля считать удовлетворительным, если измеренная толщина металла за вычетом погрешности 0,2 мм более 14,5 мм | |
8 Операции после контроля | |
Результаты измерения записать в журнал замеров ультразвуковой толщинометрии и оформить заключение. В случае любого несоответствия схеме разметки приложить к заключению схему фактического состояния узла и проведенных измерений. | |
Карту разработал: | Карту проверил: |
/Ф.И.О. | /Ф.И.О. |
(подпись, дата) | (подпись, дата) |
Наименование организации | № 0001-УЗТ | |
Подразделение, разработавшее карту | Технологическая карта контроля толщины металла гиба № XXX | Лист 3, листов 3 |
Разметка объекта контроля в зоне контроля (схема а)
Сварное соединение (линия сопряжения)
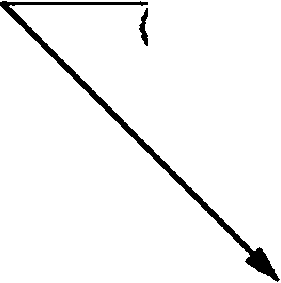
d*
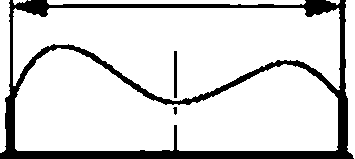
Х-Х"А XX X X А XX х х А х х X X А XX X х А X X
Сварное соединение (линия сопряжения)
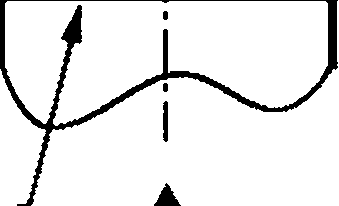
Направление движения среды
Плоскость измерения
Неуправляемая маркировка начала 1о+5 отсчета
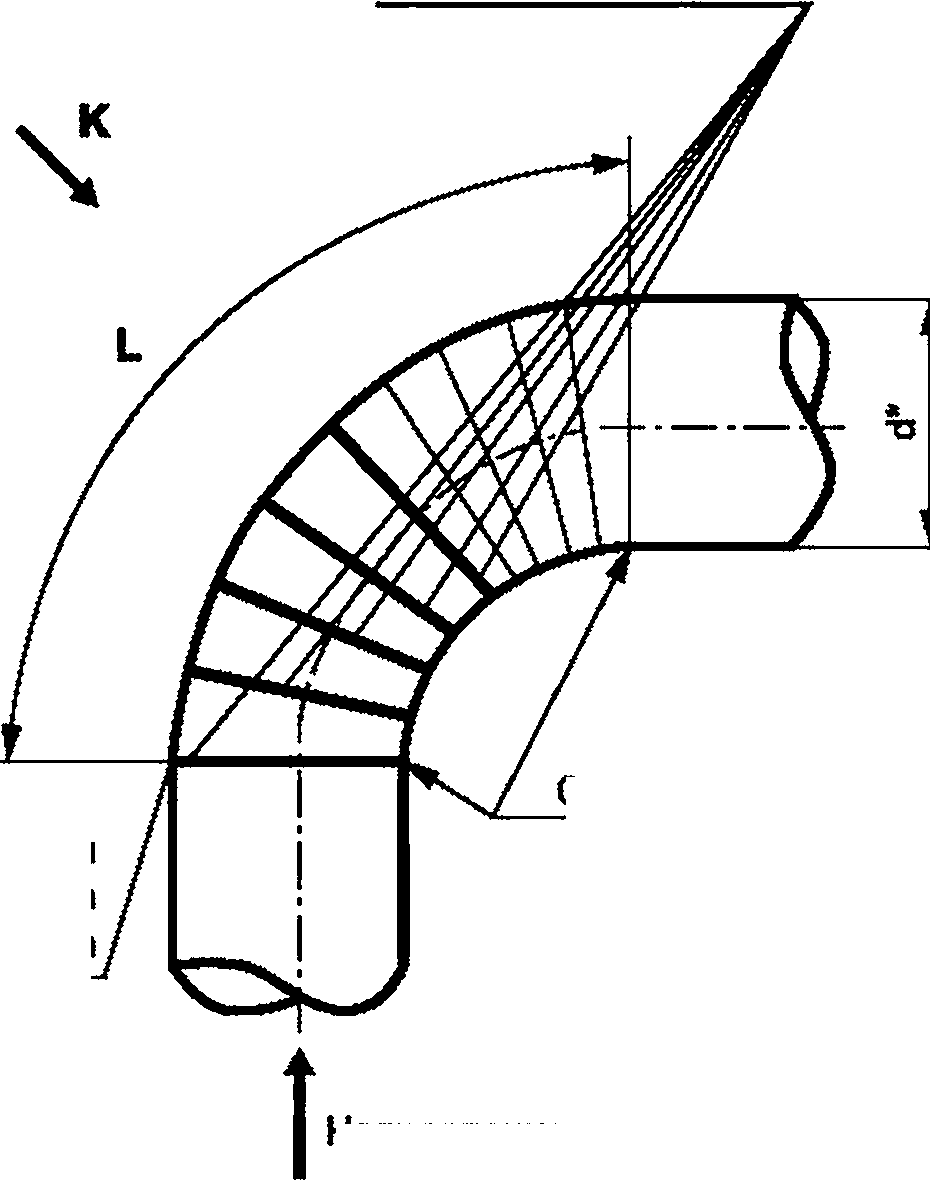
Направление движения среды
Сварное соединение (линия сопряжения)
Координаты точек измерения толщины для 0325 мм
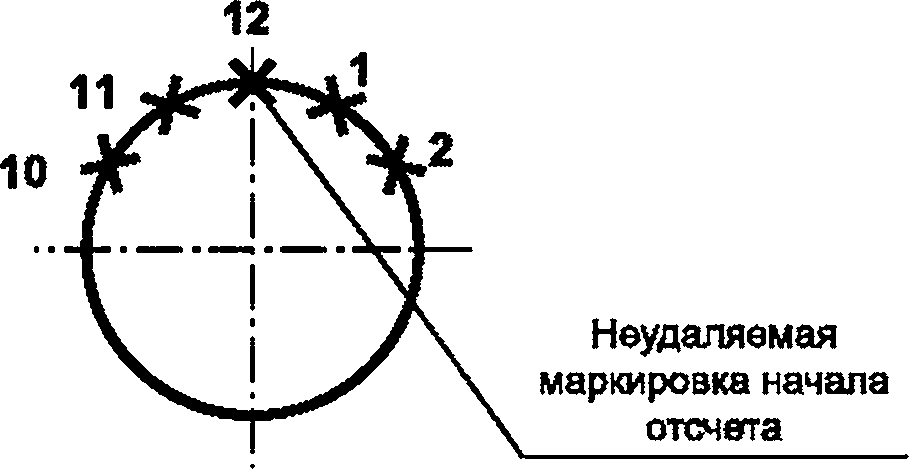
Таблица для заполнения результатов измерения
Координата точки | Плоскость измерения толщины/Н (мм) | ||||
А | Б | В | Г | Д | |
12 ч | |||||
1 ч | |||||
2 ч | |||||
10 ч | |||||
______11 ч______ |
1. ‘Размеры для справки.
2. X — точка измерения толщины.
3. 12 ч, 1 ч, 2 ч, 10 ч, 11 ч — координаты точек измерения.
4. А—Д — плоскости измерения.
5. L, = L*/9.
Карту разработал:
___________________/Ф.И.О.
(подпись, дата)
Карту проверил:
________________/Ф.И.О.
(подпись, дата)
Б.З Пример заполнения технологической карты контроля при измерении толщины металла в зоне контроля с применением электромагнитно-акустического толщиномера
Наименование организации | ||
Наименование подразделения, разработавшего карту | Технологическая карта контроля толщины металла листового проката № XXX | Лист 1, листов 3 |
1 Объект контроля | ||||||||
1.1 Наименование контролируемого оборудования | Заготовка обечайки | |||||||
1.2 Изготовитель | ВМК «Красный октябрь» | |||||||
1.3 Чертеж | 142.13.75 | |||||||
1.4 Объект контроля | Г/К Листовой прокат, основной металл | |||||||
1.5 Материал | Сталь 20 | |||||||
1.6 Контроль | Входной | |||||||
2 Документация по контролю | ||||||||
2.1 Документы, устанавливающие нормы оценки | Чертеж № 142.13.75 | 2.2 Документ, устанавливающий методику контроля | ГОСТ Р 50.05.03—2022 | |||||
3 Требования к технологии контроля и оценке качества | ||||||||
3.1 Объем контроля | По 6.2 | 3.2 Минимально допустимая толщина металла объекта контроля в зоне контроля, мм (согласно конструкторской документации) | 29,90 | |||||
3.3 Погрешность измерения, мм | ±0,3 при Р = 0,95 | |||||||
4 Тип и размеры объекта контроля | ||||||||
4.1 Размеры, мм: | Толщина металла, мм | 32 | Габарит(длина и ширина), мм | 6000 х1500 | ||||
5 Средства контроля | ||||||||
5.1 Толщиномер | УТ-04 ЭМА (Дельта) | |||||||
5.2 Преобразователь | ЭМА —2,5 | |||||||
5.3 Датчик пути (энкодер) | ДП 3500 | |||||||
5.4 Образцы: | ||||||||
Образец толщины — Т2 № 05, см [>Н | Н =32 мм, сталь 20 н см | • | < ю о о~ | У | ||||
5.5 Рулетка | Предел измерения 10 000 мм, погрешность измерений ±2,3 мм. | |||||||
Карту разработал: | Карту проверил: | |||||||
___________/Ф.И.О., должность, № удостоверения (подпись, дата) | ___________/Ф.И.О., должность, № удостоверения (подпись, дата) |
Наименование организации | ||
Наименование подразделения, разработавшего карту | Технологическая карта контроля толщины металла листового проката № XXX | Лист 2, листов 3 |
6 Подготовка к контролю | |||||
6.1 Проверка качества подготовки поверхности | Подготавливаемая поверхность должна быть свободна от плотного слоя ржавчины, отслоившейся окалины, лакокрасочного покрытия, толщина которого превышает технические характеристики электромагнитно-акустического толщиномера. | ||||
6.2 Проверка разметки объекта контроля | Разметка листа н согласно схеме. | а полосы для измерения толщины должна бь 6000 | !ть выполнена | ||
Л | |||||
S я— | |||||
3 | |||||
§ | |||||
2 | |||||
О о | | Марки-1 | ровка | | ||||
| 4 | 1 | |||
0 эазметить на полосы (1, 2, 3 ... л) согласно разметке, вдоль длинной ю отсчета — от края листа с маркировкой. олос 100 мм | |||||
7 Условия и порядок проведения контроля | |||||
7.1 Условия проведения контроля |
| ||||
7.2 Подготовка к контролю |
1 мм) на объекте контроля в зоне контроля | ||||
7.3 Измерения толщины |
| ||||
Карту разработал: | Карту проверил: | ||||
_______________/Ф.И.О. (подпись, дата) | _______________/Ф.И.О. (подпись, дата) |
Рисунок Б.2, лист 2
Наименование организации | ||
Наименование подразделения, разработавшего карту | Технологическая карта контроля толщины металла листового проката № XXX | Лист 3, листов 3 |
8 Оценка качества | ||
8.1 Качество листа считать удовлетворительным, если измеренная толщина металла объекта контроля за вычетом погрешности 0,3 мм более 29,9 мм | ||
8.2 Результаты контроля фиксировать в журнале. | ||
8.3 На основании записи в журнале оформить заключение. | ||
8.4 При обнаружении утонения составить картограмму. | ||
Карту разработал: | Карту проверил: | |
_______________/Ф.И.О. (подпись, дата) | _______________/Ф.И.О. (подпись, дата) |
Рисунок Б.2, лист 3
Приложение В (обязательное)
Процедура определения шага сканирования при измерении толщины металла электромагнитно-акустическим преобразователем
В.1 Для определения шага сканирования используется калибровочный образец СО-2.
В.2 Настраивают СИ в соответствии с 12.5.
В.З Устанавливают ЭМАП на калибровочный образец СО-2 над отверстием d, равным 6 мм на глубине 15 мм.
В.4 Совмещают центр преобразователя с центральной осью отверстия.
В.5 Получают показания блока цифровой обработки СИ и сохраняют результат.
В.6 Переставляют ЭМАП на 1 мм в одну из сторон от центральной оси отверстия и получают устойчивые показания блока цифровой обработки СИ.
В.7 Переставляют ЭМАП дальше в том же направлении с шагом 1 мм. При необходимости поднимают амплитуду, пока не пропадут показания блока цифровой обработки СИ.
В.8 Измеряют расстояние от центральной оси отверстия и осью ЭМАП, когда было получено последнее измерение.
В.9 Повторяют действия, указанные в В.4—В.8, в другую сторону.
В. 10 Максимальный шаг сканирования — удвоенное расстояние, при котором еще возможно определить глубину расположения отверстия d, равного 6 мм в СО-2 (в одну сторону от оси отверстия).
Приложение Г (справочное)
Форма и пример заполнения заключения по результатам измерения толщины металла атомная станция, Отдел дефектоскопии металлов и технического контроля Заключение №__от..г.
Метод неразрушающего контроля | Ультразвуковой | |
№ журнала: 30-40/207, том 2 | № записи в журнале:14 | |
Объект контроля | ||
Блок № 3 | ТЦ-2 | |
Наименование узла № чертежа | Трубопроводы питательной воды Б-805917СБ-3 | |
Изготовитель | ||
Оперативное обозначение | 3RL | |
Марка стали, типоразмер | Сталь 15ГС по ТУ 14-ЗР-55-2001; 0530x28; | |
Основной металл Сварной шов Наплавленная поверхность | Основной металл | |
Категория сварного соединения | — | |
Объем контроля Зона контроля (участок) Поверхность | Бл. 46 (№ 40—№41) | |
Сведения о термической обработке | Термическая обработка не проводилась | |
Цель контроля | Типовая программа, РП.к.вр.З.ТО.ОДМиТК/235, разд. 5 2.5.1 |
Специалист по УЗК:Ф.И.О. подпись, дата проведения контроля
(№ удостоверения, действ, до)
Руководитель:Ф.И.О.
подпись, дата
Начальник ОДМиТК:Ф.И.О.
подпись, дата
Рисунок Г.1, ЛИСТ 1
Технологические данные | Методика контроля | ГОСТ Р 50.05.03—2022 |
Карта контроля | И.О.ЗО.17, ОООЗ-УЗТ(а); 284/14/28У | |
Средства контроля | Толщиномер УТ-04 ЭМА (Дельта) |
Документ, устанавливающий нормы оценки качества | Правила контроля |
Результаты контроля: | |
Результаты см. на обороте | |
Оценка качества | Удовлетворяет требованиям правил контроля |
Специалист по УЗК:Ф.И.О. подпись, дата проведения контроля
(№ удостоверения, действ, до)
Руководитель:Ф.И.О.
подпись, дата
Начальник ОДМиТК:Ф.И.О.
подпись, дата
Рисунок Г.1, лист 2
Прямой участок бл. 46 (№ 40, № 41), L = 4900 мм, Н = 265 мм, 284/14/28У, ОООЗ-УЗТ(а)*
Координата точки | Плоскость измерения толщины / Н (мм) | |||
А | Б | В | Г | |
12ч | 24,7 | 30,9 | 32,3 | 32,5 |
1 ч | 24,8 | 30,8 | 32,2 | 32,1 |
2ч | 25,0 | 31,0 | 31,9 | 31,9 |
Зч | 25,2 | 31,4 | 31,6 | 31,6 |
4 ч | 25,1 | 31,1 | 32,0 | 31,8 |
5 ч | 24,7 | 31,3 | 31,9 | 31,3 |
6ч | 23,9 | 31,4 | 31,3 | 30,9 |
7ч | 24,2 | 31,0 | 31,6 | 30,8 |
8ч | 24,6 | 31,2 | 31,4 | 30,9 |
9 ч | 25,1 | 31,6 | 31,7 | 31,5 |
10ч | 25,2 | 31,5 | 32,1 | 31,1 |
11 ч | 24,9 | 31,5 | 32,0 | 31,3 |
$пгпп.факт 23,9 ММ > Smjn доп 16,01 ММ
* Приводится на оборотной стороне заключения.
Специалист по УЗК:Ф.И.О. подпись, дата проведения контроля
(№ удостоверения, действ, до)
Руководитель:Ф.И.О.
подпись, дата
Начальник ОДМиТК:Ф И О.
подпись, дата
Рисунок Г.1, лист 3
Библиография
[1] Положение о стандартизации в отношении продукции (работ, услуг), для которой устанавливаются требования, связанные с обеспечением безопасности в области использования атомной энергии, а также процессов и иных объектов стандартизации, связанных с такой продукцией (утверждено постановлением Правительства Российской Федерации от 12 июля 2016 г. № 669)
[2] Федеральные нормы и правила в области использования атомной энергии НП-084—15
[3] Федеральные нормы и правила в области использования атомной энергии НП-089—15
[4] Федеральные нормы и правила в области использования атомной энергии НП-105—18
[5] Федеральные нормы и правила в области использования атомной энергии НП-010—16
[6] Федеральные нормы и правила в области использования атомной энергии НП-068—05
[7] Федеральные нормы и правила в области использования атомной энергии НП-107—21
[8] Федеральные нормы и правила в области использования атомной энергии НП-044—18
[9] Федеральные нормы и правила в области использования атомной энергии НП-045—18
[10] Федеральные нормы и правила в области использования атомной энергии НП-046—18
[11] Федеральные нормы и правила в области использования атомной энергии НП-104—18
Правила контроля основного металла, сварных соединений и наплавленных поверхностей при эксплуатации оборудования, трубопроводов и других элементов атомных станций Правила устройства и безопасной эксплуатации оборудования и трубопроводов атомных энергетических установок Правила контроля металла оборудования и трубопроводов атомных энергетических установок при изготовлении и монтаже
Правила устройства и эксплуатации локализующих систем безопасности атомных станций
Трубопроводная арматура для атомных станций. Общие технические требования
Правила устройства и безопасной эксплуатации корпуса блока реакторного, оборудования, трубопроводов и внутрикорпусных устройств ядерной энергетической установки со свинцовым теплоносителем
Правила устройства и безопасной эксплуатации сосудов, работающих под избыточным давлением, для объектов использования атомной энергии
Правила устройства и безопасной эксплуатации трубопроводов пара и горячей воды для объектов использования атомной энергии
Правила устройства и безопасной эксплуатации паровых и водогрейных котлов для объектов использования атомной энергии
Сварка и наплавка оборудования и трубопроводов атомных энергетических установок
[12] Порядок проведения поверки средств измерений (утвержден приказом Минпромторга России от 31 июля 2020 г. № 2510)
[13] Метрологические требования к измерениям, эталонам единиц величин, стандартным образцам, средствам измерений, их составным частям, программному обеспечению, методикам (методам) измерений, применяемым в области использования атомной энергии (утверждены приказом Госкорпорации «Росатом» от 31 октября 2013 г. № 1/10-НПА)
[14] Правила технической эксплуатации электроустановок потребителей электрической энергии (утверждены приказом Министерства энергетики Российской Федерации от 12 августа 2022 г. № 811)
[15] Санитарно-эпидемиологические правила Санитарно-эпидемиологические требования к физическим и нормативы факторам на рабочих местах
СанПиН 2.2.4.3359—16
[16] Санитарные правила и нормативы Нормы радиационной безопасности НРБ-99/2009
СанПин 2.6.1.2523—09
УДК 620.179:1:006.354
ОКС 27.120
Ключевые слова: неразрушающий контроль, ультразвуковой контроль, измерение толщины металла
Редактор Л.В. Коретникова Технический редактор В.Н. Прусакова Корректор М.И. Першина Компьютерная верстка А.Н. Золотаревой
Сдано в набор 20.12.2022. Подписано в печать 27.12.2022. Формат 60x84%. Гарнитура Ариал. Усл. печ. л. 5,12. Уч.-изд. л. 4,62.
Подготовлено на основе электронной версии, предоставленной разработчиком стандарта
Создано в единичном исполнении в ФГБУ «Институт стандартизации» , 117418 Москва, Нахимовский пр-т, д. 31, к. 2.