ФЕДЕРАЛЬНОЕ АГЕНТСТВО
ПО ТЕХНИЧЕСКОМУ РЕГУЛИРОВАНИЮ И МЕТРОЛОГИИ
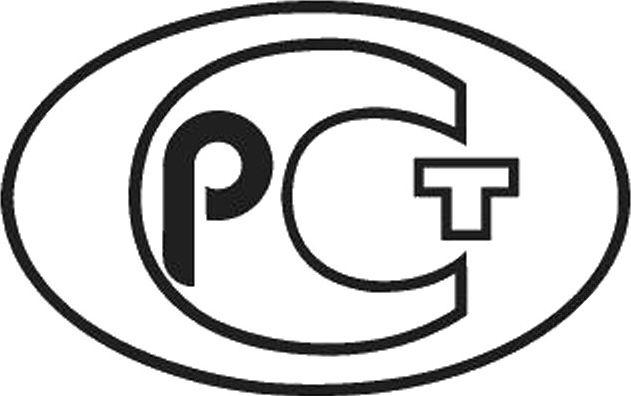
НАЦИОНАЛЬНЫЙ СТАНДАРТ РОССИЙСКОЙ ФЕДЕРАЦИИ
ГОСТ Р 71256-
2024
Арматура трубопроводная
ТЕРМИЧЕСКАЯ ОБРАБОТКА ДЕТАЛЕЙ, ЗАГОТОВОК И СВАРНЫХ СБОРОК ИЗ ВЫСОКОЛЕГИРОВАННЫХ СТАЛЕЙ, КОРРОЗИОННО-СТОЙКИХ И ЖАРОПРОЧНЫХ СПЛАВОВ
Издание официальное
Москва Российский институт стандартизации 2024
ГОСТ Р 71256—2024
Предисловие
1 РАЗРАБОТАН Акционерным обществом «Научно-производственная фирма «Центральное конструкторское бюро арматуростроения» (АО «НПФ «ЦКБА»)
2 ВНЕСЕН Техническим комитетом по стандартизации ТК 259 «Трубопроводная арматура и сильфоны»
3 УТВЕРЖДЕН И ВВЕДЕН В ДЕЙСТВИЕ Приказом Федерального агентства по техническому регулированию и метрологии от 15 апреля 2024 г. № 461-ст
4 ВВЕДЕН ВПЕРВЫЕ
Правила применения настоящего стандарта установлены в статье 26 Федерального закона от 29 июня 2015 г. № 162-ФЗ «О стандартизации в Российской Федерации». Информация об изменениях к настоящему стандарту публикуется в ежегодном (по состоянию на 1 января текущего года) информационном указателе «Национальные стандарты», а официальный текст изменений и поправок — в ежемесячном информационном указателе «Национальные стандарты». В случае пересмотра (замены) или отмены настоящего стандарта соответствующее уведомление будет опубликовано в ближайшем выпуске ежемесячного информационного указателя «Национальные стандарты». Соответствующая информация, уведомление и тексты размещаются также в информационной системе общего пользования — на официальном сайте Федерального агентства по техническому регулированию и метрологии в сети Интернет (www.rst.gov.ru)
© Оформление. ФГБУ «Институт стандартизации», 2024
Настоящий стандарт не может быть полностью или частично воспроизведен, тиражирован и распространен в качестве официального издания без разрешения Федерального агентства по техническому регулированию и метрологии
II
ГОСТ Р 71256—2024
Содержание
1 Область применения..................................................................1
2 Нормативные ссылки..................................................................1
3 Термины, определения, сокращения и обозначения........................................1
4 Технические требования...............................................................3
5 Режимы термической обработки деталей и сварных сборок из сталей мартенситного, аустенито-мартенситного, мартенсито-ферритного и ферритного классов......................3
6 Режимы термической обработки деталей и сварных сборок из сталей и сплавов аустенитного и аустенито-ферритного классов........................................................7
7 Режимы термической обработки деталей и сварных сборок из жаропрочных сталей и сплавов. ... 12
8 Общие технологические указания по термической обработке...............................15
9 Контроль термической обработки......................................................15
10 Оформление документации..........................................................16
Приложение А (обязательное) Механические свойства заготовок из высоколегированных сталей и сплавов................................................................17
Приложение Б (рекомендуемое) Режимы термической обработки для улучшения обрабатываемости.......................................................21
Библиография........................................................................22
III
ГОСТ Р 71256—2024
НАЦИОНАЛЬНЫЙ СТАНДАРТ РОССИЙСКОЙ ФЕДЕРАЦИИ
Арматура трубопроводная
ТЕРМИЧЕСКАЯ ОБРАБОТКА ДЕТАЛЕЙ, ЗАГОТОВОК И СВАРНЫХ СБОРОК ИЗ ВЫСОКОЛЕГИРОВАННЫХ СТАЛЕЙ, КОРРОЗИОННО-СТОЙКИХ И ЖАРОПРОЧНЫХ СПЛАВОВ
Pipeline valves. Heat treatment of parts, blanks and welded assemblies made of high-alloy steels, corrosion-resistant and heat-resistant alloys
Дата введения — 2024—08—01
1 Область применения
Настоящий стандарт устанавливает режимы и основные технологические требования по термической обработке заготовок, деталей и сварных сборок трубопроводной арматуры из высоколегированных сталей, коррозионно-стойких и жаропрочных сплавов и является типовым технологическим процессом проведения термической обработки.
2 Нормативные ссылки
В настоящем стандарте использованы нормативные ссылки на следующие стандарты:
ГОСТ 12.3.004 Система стандартов безопасности труда. Термическая обработка металлов. Общие требования безопасности
ГОСТ 6032 (ISO 3651-1:1998, ISO 3651-2:1998) Стали и сплавы коррозионно-стойкие. Методы испытаний на стойкость против межкристаллитной коррозии
ГОСТ 33439 Металлопродукция из черных металлов и сплавов на железоникелевой и никелевой основе. Термины и определения по термической обработке
ГОСТ Р 71255 Арматура трубопроводная. Поковки, штамповки и заготовки из проката. Технические требования
Примечание — При пользовании настоящим стандартом целесообразно проверить действие ссылочных стандартов в информационной системе общего пользования — на официальном сайте Федерального агентства по техническому регулированию и метрологии в сети Интернет или по ежегодному информационному указателю «Национальные стандарты», который опубликован по состоянию на 1 января текущего года, и по выпускам ежемесячного информационного указателя «Национальные стандарты» за текущий год. Если заменен ссылочный стандарт, на который дана недатированная ссылка, то рекомендуется использовать действующую версию этого стандарта с учетом всех внесенных в данную версию изменений. Если заменен ссылочный стандарт, на который дана датированная ссылка, то рекомендуется использовать версию этого стандарта с указанным выше годом утверждения (принятия). Если после утверждения настоящего стандарта в ссылочный стандарт, на который дана датированная ссылка, внесено изменение, затрагивающее положение, на которое дана ссылка, то это положение рекомендуется применять без учета данного изменения. Если ссылочный стандарт отменен без замены, то положение, в котором дана ссылка на него, рекомендуется применять в части, не затрагивающей эту ссылку.
3 Термины, определения, сокращения и обозначения
3.1 В настоящем стандарте применены термины по ГОСТ 33439, а также следующие термины с соответствующими определениями:
Издание официальное
1
ГОСТ Р 71256—2024
3.1.1 термическая обработка: Процесс обработки изделий из металлов и сплавов путем температурного воздействия и последующего охлаждения с определенной скоростью с целью изменения их структуры и свойств в заданном направлении.
3.1.2 аустенизация: Этап термической обработки, в ходе которого изделие нагревают до температуры выше интервала превращений и выдерживают при этой температуре для получения однородной структуры аустенита (полная аустенизация).
3.1.3 закалка: Термическая обработка, заключающаяся в нагреве изделия до температуры выше критической (Ас3 — для доэвтектоидной стали и Ас1 — для заэвтектоидной стали) или до температуры растворения избыточных фаз, в выдержке при этой температуре и последующем охлаждении со скоростью, превышающей критическую.
Примечание — Ас1 — температура (точка) фазового превращения, при которой начинается образование аустенита при нагреве; Ас3 — температура (точка) фазового превращения, при которой начинается образование феррита при охлаждении.
3.1.4 скорость нагрева: Изменение температуры в процессе нагрева, отнесенное ко времени.
3.1.5 отжиг: Термическая обработка, предусматривающая нагрев изделия до определенной температуры, выдержку и последующее медленное охлаждение с целью получения более равновесной структуры.
3.1.6 отпуск: Термическая обработка, проводимая после закалки или после другой термической обработки для обеспечения необходимых показателей определенных свойств изделия.
Примечание — При отпуске нагрев осуществляют до температур ниже точки Ас^
3.1.7 старение: Явление, при котором происходит изменение свойств изделия в процессе вылеживания при комнатной температуре или при нагреве и которое обусловлено термодинамической неравновесностью исходного структурного состояния и постепенного приближения структуры к равновесному состоянию.
3.1.8 сталь: Сплав железа с углеродом, содержащий не более 2,14 % углерода.
3.2 В настоящем стандарте применены следующие сокращения и обозначения:
АС — атомная станция;
ГМО — головная металловедческая организация;
КД — конструкторская документация;
КР — коррозионное растрескивание;
МКК — межкристаллитная коррозия;
МО РФ — Министерство обороны Российской Федерации;
НД — нормативные документы;
ПТД — производственно-технологическая документация;
РМРС — Российский морской регистр судоходства;
ТВЧ — ток высокой частоты;
ТО —термическая обработка;
HRC — твердость по шкале Роквелла;
НВ — твердость по шкале Бринелля;
°о 2 — предел текучести;
ов — временное сопротивление (предел прочности);
65 — относительное удлинение после разрыва;
у — относительное сужение после разрыва;
KCU — ударная вязкость, определенная на образце с концентратором вида U;
KCV — ударная вязкость, определенная на образце с концентратором вида V.
2
ГОСТ Р 71256—2024
4 Технические требования
4.1 Необходимость проведения ТО и ее режимы определены конкретными условиями изготовления и эксплуатации арматуры, которые должны быть установлены КД.
4.2 В соответствии с требованиями настоящего стандарта и КД изготовителям арматуры следует разрабатывать ПТД на ТО деталей и сварных сборок применительно к имеющемуся оборудованию. Для заготовок (деталей) и сварных сборок арматуры АС ПТД на ТО следует разрабатывать в соответствии с требованиями настоящего стандарта и [1]—[4].
5 Режимы термической обработки деталей и сварных сборок из сталей мартенситного, аустенито-мартенситного, мартенсито-ферритного и ферритного классов
5.1 Для получения показателей механических свойств и твердости, установленных ГОСТ Р 71255, и для достижения максимальной коррозионной стойкости детали (заготовки) арматуры из стали марок: 12X13, 20X13, 30X13, 14Х17Н2, 95X18, 25Х17Н2Б-Ш, 07Х16Н4Б, 07Х16Н4Б-Ш, 09Х16Н4Б-Ш, следует подвергать закалке и отпуску, а из стали марок 12X17, 15Х25Т и 16Х-ВИ — отжигу.
Для уменьшения остаточной магнитной индукции детали магнитопровода электромагнитов детали (заготовки) из стали марок 12X17, 14Х17Н2 следует подвергать длительному отжигу, а из стали марки 16Х-ВИ — высокотемпературному отжигу в вакууме.
5.2 ТО подвергают заготовки. При ТО готовых деталей нагрев до температуры закалки и отжига следует вести в вакууме не выше 104 мм рт. ст. или в контролируемой защитной атмосфере. Если защитной атмосферой служит аммиак, необходимо предусмотреть припуск под шлифовку не менее 0,3 мм на сторону.
5.3 Детали из стали марок 20X13, 30X13, 14X17Н2 и 25Х17Н2Б-Ш, входящие в узлы трения и уплотнения затвора, могут быть подвергнуты поверхностной закалке с нагревом ТВЧ с целью повышения твердости при одновременном сохранении высоких механических свойств в сердцевине детали. Подкалка деталей из стали марки 14Х17Н2 ТВЧ допускается при отсутствии в КД требования коррозионной стойкости стали против МКК.
5.4 Режимы ТО и твердость марок стали приведены в таблице 1. Механические свойства, определяемые на продольных образцах, термообработанных по режимам, представленным в таблице 1, — в соответствии с приложением А.
5.5 Нагрев деталей (заготовок) из стали марок: 20X13, 30X13, 95X18, 07X16Н4Б, 07Х16Н4Б-Ш, 09Х16Н4Б-Ш и 14Х17Н2, в интервале температур от 500 °C до 800 °C следует проводить со скоростью не более 200 °С/ч. В интервале температур от 750 °C до 800 °C необходимо дать выдержку до полного прогрева садки. Дальнейший нагрев до температуры закалки проводят по мощности печи.
Для деталей толщиной (диаметром) не более 120 мм скорость нагрева не лимитируется и выдержка при температуре от 750 °C до 800 °C не проводится.
5.6 Для стали марок: 30X13, 95X18, 09Х16Н4Б-Ш, 07X16Н4Б и 07Х16Н4Б-Ш, время между закалкой и началом отпуска — не более 3 ч.
5.7 Допускаются отклонения режимов отпуска (см. таблицу 1) в части длительности выдержек и температуры при условии обеспечения всех требований КД. Другие отклонения должны быть согласованы для изделий:
-АС и РМРС —с ГМО;
- МО РФ — с представителем заказчика.
5.8 Поверхностную закалку с нагревом ТВЧ стали марок: 20X13, 30X13, 14Х17Н2 и 25Х17Н2Б-Ш, применяют для деталей толщиной (диаметром) не менее 15 мм и проводят только после предварительной улучшающей ТО согласно данным, приведенным в таблице 1, на твердость до 36,5 HRC для сталей марок 20X13, 30X13, на твердость от 22 HRC до 31 HRC для стали марки 14Х17Н2 и на твердость более 31 HRC — для стали марки 25Х17Н2Б-Ш.
3
ГОСТ Р 71256—2024
Таблица 1 — Режимы ТО и твердость коррозионно-стойких сталей мартенситного, аустенито-мартенситного, мартенсито-ферритного и ферритного классов
Марка стали | ТО | Твердость | ||||||
Закалка | Обработка холодом | Отпуск | HRC | НВ | ||||
Температура, °C | Среда охлаждения | Температура, °C | Время выдержки, ч | Температура, °C | Среда охлаждения | |||
12X13 | 1000—1050 | Масло | — | — | 700—790 | Воздух | — | 170—195 |
20X13 | 280—370 | 39,6—44,5 | 350—400 | |||||
600—670 | 29—36 | 269—310 | ||||||
650—700 | 23,5—29,0 | 235—269 | ||||||
700—770 | — | 197—248 | ||||||
Поверхностная закалка с нагревом ТВЧ | — | — | 200—220 | Поверхностная твердость | ||||
1000—1050 | Масло, воздух | 39,5—48,5 | — | |||||
30X13 | 1000—1050 | Масло | — | — | 200—300 | Воздух | 49,5—55,5 | 460—530 |
650—670 | 29—37 | 269—330 | ||||||
670—720 | 23—30 | 235—277 | ||||||
Поверхностная закалка с нагревом ТВЧ | — | — | 200—220 | Поверхностная твердость | ||||
1000—1050 | Масло, воздух | 48,5—56,5 | — | |||||
14Х17Н2 | 975—1040 | Масло | — | — | 275—370 | 37,0—42,5 | 331—388 | |
560—600 | 30—37 | 277—331 | ||||||
680—700 | 22,5—31,0 | 229—285 | ||||||
Отжиг | — | — | — | — | 25—28 | 240—260 | ||
680—700, выдержка 20 ч | С печью | |||||||
Поверхностная закалка с нагревом ТВЧ | — | — | 200—220 | Воздух | Поверхностная твердость | |||
975—1040 | Масло, воздух | 39,5—47,5 | — | |||||
95X18 | 1000—1050 | Масло | — | — | 200—300 | >56,5 | — | |
25Х17Н2Б-Ш | 1100—1120 | Масло | Минус 70 | 2 | 250—320 | >44,5 | >415 | |
Поверхностная закалка с нагревом ТВЧ | 200—220 | Поверхностная твердость | ||||||
1100—1120 | Масло | >44,5 | — | |||||
950—970 | Масло | 630—650 | >31,0 | >285 | ||||
07Х16Н4Б, 07Х16Н4Б-Ш | 1040—1060 | Масло | — | — | 275—300 | Воздух | — | 302—331 |
640—660 | — | 269—302 |
4
Окончание таблицы 1
ГОСТ Р 71256—2024
Марка стали | то | Твердость | ||||||
Закалка | Обработка холодом | Отпуск | HRC | НВ | ||||
Температура, °C | Среда охлаждения | Температура, °C | Время выдержки, ч | Температура, °C | Среда охлаждения | |||
09Х16Н4Б, 09Х16Н4Б-Ш | 1030—1050 | Масло, воздух | — | — | 600—620 | Воздух | 30—36 | 277—330 |
Двухступенчатая ТО | 39,0—42,5 | 345—388 | ||||||
I ступень | — | — | I ступень | |||||
1030—1050 | Масло, воздух | 600—620 | ||||||
II ступень | II ступень | |||||||
970—990 | Масло, воздух | 300—350 | ||||||
12X17 | Отжиг | — | — | — | — | — | 126—197 | |
I режим 760—780 | Воздух | |||||||
II режим 780—810, выдержка 20 ч | С печью | |||||||
15Х25Т | Отжиг | — | — | — | — | — | 143—163 | |
730—780 | Воздух, вода | |||||||
16Х-ВИ | Отжиг | — | — | — | — | — | — | |
Нагрев в вакууме не выше 10~4 мм рт. ст. 1150—1200, выдержка 4-6 ч | В вакууме до температуры (700 ± 50)°C со скоростью не более 100 °С/ч; далее до температуры 200 °C со скоростью не менее 200 °С/ч; далее — воздух | |||||||
Примечания 1 Выдержка при температуре закалки — из расчета от 1 до 1,5 мин на 1 мм толщины (диаметра) заготовки, но не менее 20 мин. 2 Выдержка при температуре отжига для стали марок 12X17 и 15Х25Т — из расчета 1 мин на 1 мм толщины (диаметра) заготовки плюс 30 мин. 3 Выдержка при температуре отпуска — из расчета от 3 до 3,5 мин на 1 мм толщины (диаметра) заготовки, но не менее 2 ч. 4 Стали марок: 20X13, 30X13, 14Х17Н2, 07X16Н4Б, 07Х16Н4Б-Ш, допускается применять для работы в коррозионно-активных средах, вызывающих склонность к МКК или КР только после закалки и высокого отпуска (сталь марки 20X13 — от 197 до 248 НВ и от 235 до 269 НВ; сталь марки 30X13 — от 235 до 277 НВ и от 269 до 330 НВ; сталь марки 14Х17Н2 — от 229 до 285 НВ и от 240 до 260 НВ; сталь марок 07X16Н4Б, 07Х16Н4Б-Ш — с твердостью от 269 до 302 НВ). 5 Для длинных труб и замкнутых сосудов условную толщину берут равной трем толщинам стенки. 6 Допускается после отпуска деталей проводить охлаждение в масле или в воде. |
5.9 Длительный отжиг заготовок из стали марок 12X17 и 14X17Н2 применяют для уменьшения остаточной магнитной индукции в деталях магнитопровода электромагнитов. Длительный отжиг 5
ГОСТ Р 71256—2024
обеспечивает магнитные характеристики: для стали марки 12X17 коэрцитивная сила Нс равна 0,23 кА/м при остаточной магнитной индукции Вч 0,3 Тл; наибольшая индукция насыщения Bs 1,6 Тл при Нтах 20 кА/м; для стали марки 14X17Н2 наименьшая коэрцитивная сила Нс 0,1 кА/м при остаточной индукции Вч 0,5 Тл; индукция насыщения Bs 1,5 Тл при максимальной коэрцитивной силе Нтах 20 кА/м.
Магнитные характеристики, которые обеспечивает сплав марки 16Х-ВИ после высокотемпературного отжига, приведены в таблице 2.
Таблица 2 — Магнитные характеристики сплава 16Х-ВИ после высокотемпературного отжига
Магнитная индукция (10-4 Гс) при напряженности магнитного поля, А/см, не менее | Коэрцитивная сила Нс, не более | |||
1 | 25 | 100 | А/м | э |
0,6 | 1,2 | 1,4 | 64 | 0,8 |
Перед отжигом детали должны быть обезжирены.
Механическая обработка деталей после отжига не рекомендуется, так как резко снижаются магнитные свойства стали 16Х-ВИ.
5.10 При закалке заготовок (деталей) из стали марок 20X13, 30X13, 14Х17Н2 допускается охлаждение на воздухе при обязательном соблюдении всех требований КД.
5.11 Закалка стали марки 14Х17Н2 с последующим отпуском при температуре от 680 °C до 700 °C (на твердость от 229 до 285 НВ и от 240 до 260 НВ), а стали марки 07X16Н4Б после закалки и отпуска при температуре от 640 °C до 660 °C (на твердость от 269 до 302 НВ) обеспечивает стойкость при испытании на МКК по методу «А» или «АМ» ГОСТ 6032 (без провоцирующего нагрева, кипятить 15 ч).
5.12 Поковки и горячие объемные штамповки из стали 14Х17Н2, охлажденные в воде после горячей пластической деформации, для деталей общепромышленной арматуры применяют после проведения только высокого отпуска при обеспечении требований КД по твердости от 229 до 285 НВ, механическим свойствам и стойкости против МКК.
5.13 При поставке полуфабрикатов в термически обработанном состоянии по режимам, указанным в НД на поставку, допускается повторную ТО деталей (заготовок) не проводить при следующем условии:
- изготовление деталей не связано ни с какими видами горячей обработки стали (ковка, штамповка и т. д.);
- выполнение всех требований КД.
При указании в КД для стали марки 12X17 режима II, а для стали марки 14X17Н2 интервала твердости от 240 до 260 НВ проведение ТО (длительного отжига) обязательно.
5.14 Сварные сборки из стали марок: 12X13, 20X13, 12X17, 14Х17Н2, 07Х16Н4Б, 07Х16Н4Б-Ш, 09Х16Н4Б-Ш, с целью повышения коррозионной стойкости, пластических характеристик и снятия сварочных напряжений следует подвергать ТО по режимам, перечисленным в таблице 3.
Таблица 3 — Режимы ТО сварных сборок
Марка стали | Отпуск, отжиг | Примечание | ||
Температура, °C | Время выдержки, ч | Среда охлаждения | ||
12X13, 08X13, 20X13 | 690—730 | 1,5—2 | Воздух | — |
12X17 | 775—800 | 2—3 | При отсутствии требований стойкости против МКК | |
780—820 | 8 | При требовании стойкости против МКК | ||
14Х17Н2 | 680—700 | 2—3 | При отсутствии требований стойкости против МКК | |
3—5 | При требовании стойкости против МКК | |||
07Х16Н4Б, 07Х16Н4Б-Ш | 1 режим | — | ||
640—660 | 5* |
6
Окончание таблицы 3
ГОСТ Р 71256—2024
Марка стали | Отпуск, отжиг | Примечание | ||
Температура, °C | Время выдержки, ч | Среда охлаждения | ||
07Х16Н4Б, 07Х16Н4Б-Ш | 2 режим | Воздух | — | |
а) 670—680 б) 600—620 | 5* 2* | |||
09Х16Н4Б-Ш | 600—620 | 1,5—2 | При о02 = 80-85 кгс/мм2 | |
* Время выдержки — от 3 до 4 мин на 1 мм толщины, но не менее времени, указанного в графе «Время выдержки». Примечания 1 При наличии в сварной сборке из стали марки 14Х17Н2 твердых наплавок охлаждение сварной сборки после отпуска проводят с печью или с печью до температуры не выше 300 °C, далее — на воздухе. 2 Для стали марок 07X16Н4Б и 07Х16Н4Б-Ш режим 1 применяют для рабочей температуры не выше 100 °C, режим 2 — свыше 100 °C. |
6 Режимы термической обработки деталей и сварных сборок из сталей
и сплавов аустенитного и аустенито-ферритного классов
6.1 Для получения показателей механических свойств и твердости, установленных ГОСТ Р 71255 и для достижения максимальной коррозионной стойкости детали арматуры из сталей и сплавов аустенитного и аустенито-ферритного классов следует подвергать ТО по режимам, приведенным в таблице 4.
Таблица 4 — Режимы ТО и твердость коррозионно-стойких сталей аустенитного и аустенито-ферритного классов и сплава Н70МФ
Марка стали, сплава | ТО | Твердость | |||||
Закалка | Старение | HRC | НВ | ||||
Температура, °C | Среда охлаждения | Температура, °C | Время выдержки, ч | Среда охлаждения | |||
12Х18Н9 | 1020-1100 | Воздух | 121—179 | ||||
12Х18Н9Т, 12Х18Н10Т, 08Х18Н10Т, 08Х17Н15МЗТ, 10Х17Н13М2Т, 10X17H13M3T | Вода, воздух | ||||||
08Х18Н10Т-ВД, 08Х18Н10Т-Ш | 1040—1060 | ||||||
09Х14Н16Б | 1110—1130 | 131—156 | |||||
09Х14Н19В2БР | 1140—1160 | ||||||
10Х14Г14Н4Т | 1000—1080 | 121—179 | |||||
06ХН28МДТ | 1050—1080 | ^200 | |||||
15Х18Н12С4ТЮ, 15Х18Н12С4ТЮ-Ш | 950—1050 | Вода | 155—170 | ||||
08Х22Н6Т, 08Х21Н6М2Т | Вода, воздух | 140—200 |
7
ГОСТ Р 71256—2024
Окончание таблицы 4
Марка стали, сплава | ТО | Твердость | |||||
Закалка | Старение | HRC | НВ | ||||
Температура, °C | Среда охлаждения | Температура, °C | Время выдержки, ч | Среда охлаждения | |||
07Х21Г7АН5, 07X21Г7АН5-Ш | 1000—1050 | Вода, воздух | — | — | — | — | <207 |
03Х20Н16АГ6-Ш | 1030—1070 | Вода | — | ||||
10Х15Н9СЗБ1-Ш | 1030-1050 | Воздух | — | ||||
08Х15Н24В4ТР | — | — | 690—710 | 16 | Воздух | >229 | |
09Х15Н8Ю | 950—1000 | Воздух | 350—400 | 1—2 | 35,5—40,5 | — | |
После закалки обработка холодом при температуре минус 70 °C в течение 2 ч | |||||||
10Х32Н8, 10Х32Н8-ВД, 10Х32Н8-Ш | 1080—1120 | Вода | 270—300 | 2—4 | — | <26 | <248 |
450—500 | 26—35 | 262—293 | |||||
8-15 | 32—39 | 293—358 | |||||
Н70МФВ | 1100—1120 | — | — | — | — | 180—230 |
Примечания
1 Выдержка при температуре закалки — из расчета от 1 до 1,5 мин на 1 мм наибольшего сечения [диаметра(толщины)] заготовки, но не менее 30 мин.
2 Для заготовок толщиной (диаметром) 10 мм и менее охлаждение всех сталей и сплавов, за исключением марок 10Х32Н8, 10Х32Н8-ВД, 10Х32Н8-Ш и сплава марки Н70МФВ, допускается проводить на воздухе.
3 Для сталей, у которых в графе «Твердость» число твердости не указано, норму твердости не устанавливают.
Механические свойства перечисленных марок стали, определяемые на продольных образцах, ТО по указанным режимам — в соответствии с приложением А. ТО следует подвергать заготовки.
6.2 При поставке полуфабрикатов в термообработанном состоянии по режимам, указанным в НД на поставку, допускается повторную ТО заготовок (деталей) не проводить при следующем условии:
- при соблюдении требований 5.13;
- таком изготовлении детали, которое не связано с холодной обработкой давлением на величину максимальной деформации более 5 %, если детали работают в средах, не вызывающих КР (жидкие металлы, инертные газы, воздух и др.).
Поковки и штамповки из стали марок: 08Х18Н10Т, 12Х18Н10Т, 10X17H13M3T, предназначенных для изготовления деталей арматуры общего назначения, не подлежащих сварке, допускается использовать с применением закалки с ковочного нагрева при обеспечении всех требований КД.
6.3 Заготовки из стали марок: 12Х18Н9Т, 08Х18Н10Т, 08Х18Н10Т-Ш, 08Х18Н10Т-ВД, 10Х18Н10Т, 09Х14Н16Б, 09Х14Н19В2БР, допускается после аустенизации дополнительно подвергать стабилизирующему отжигу при температуре от 850 °C до 920 °C с выдержкой не менее 2 ч, с охлаждением на воздухе.
6.4 Стабилизирующий отжиг заготовок стали марок, перечисленных в 6.3, проводят, если детали предназначены:
а) для работы при температуре свыше 350 °C;
б) последующего азотирования.
6.5 Стабилизирующему отжигу при температуре от 850 °C до 920 °C с охлаждением в печи не ниже температуры 200 °C, далее на воздухе подвергают детали после выполнения наплавки твердыми сплавами.
6.6 Для предупреждения закалочных трещин в стали марок: 10Х32Н8, 10Х32Н8-ВД, 10Х32Н8-Ш, необходимо:
а) посадку заготовок при нагреве под закалку проводить в печь, нагретую до температуры выше 150 °C;
8
ГОСТ Р 71256—2024
б) переключить печь на температуру 200 °C и выдержать не менее 1 ч (в зависимости от размера садки и термического оборудования);
в) переключить печь на температуру от 300 °C до 360 °C, выдержать не менее 3 ч;
г) переключить печь на температуру от 1080 °C до 1120 °C, выдержать не менее 3 ч после достижения температуры;
д) охладить в проточной воде с температурой не выше 35 °C.
Примечания
1 Медленный нагрев проводить при наличии о-фазы в поставке. В этом случае нагрев под закалку рекомендуется проводить в электропечах.
2 При отсутствии о-фазы допускается посадка заготовок в печь на закалочную температуру.
Закалке рекомендуется подвергать заготовки толщиной (диаметром) не более 50 мм с минимальными припусками на механическую обработку с просверленными отверстиями.
Заготовки сечением или толщиной стенки более 50 мм, а также заготовки, имеющие резкие переходы в размерах поперечного сечения, подвергают охлаждению начиная с температуры закалки в горячих средах (температурой от 250 °C до 270 °C).
6.7 Для снятия наклепа на деталях из стали аустенитного класса после холодной обработки давлением в случае максимальной деформации более 5 % проводят ТО по режиму: температура нагрева — 950 °C, охлаждение — на воздухе.
6.8 Сварные сборки из сталей и сплавов следует подвергать ТО по режимам, указанным в таблице 5.
Таблица 5 — Режимы ТО сварных сборок
Режим | Марка стали, сплава | Закалка, стабилизирующий отжиг | Дополнительные указания | |
Температура, °C | Среда охлаждения | |||
1 | 12Х18Н9 | 970—1020 | Воздух | Для повышения стойкости к хрупким разрушениям в околошовной зоне сварных соединений, работающих при температуре выше 500 °C |
08Х17Н15МЗТ, 10Х17Н13М2Т, 10X17H13M3T | Для снятия остаточных напряжений в случае сварки электорами типа Э-07Х19Н11МЗГ2Ф (марка ЭА-400/10У, ЭА-400/10Т), проволока св. 04X19Н11 М3 и др.) | |||
12Х18Н9Т, 12Х18Н10Т, 08Х18Н10Т, 08Х18Н10Т-ВД, 08Х18Н10Т-Ш | Для предотвращения склонности к ножевой коррозии сварных сборок, работающих в азотной кислоте. При этом температуру нагрева держать на верхнем пределе. Время выдержки — не менее 1 ч | |||
2 | 09Х18Н9, 10Х18Н9, 12Х18Н9, 08Х18Н10, 10Х17Н13М2Т, 10X17H13M3T | 950-970 | С печью или не ниже 300 °C с печью, далее — на воздухе | При наличии твердых наплавок в сварных сборках |
3 | 12Х18Н9 | Отпуск 585—615 | Воздух | Для снятия остаточных напряжений сварных сборок сложной конфигурации, если рабочая температура изделия не выше 500 °C |
4 | 12Х18Н9Т, 12Х18Н10Т, 08Х18Н10Т, 08Х18Н10Т-Ш, 08Х18Н10Т-ВД, 08Х17Н15МЗТ, 10Х17Н13М2Т, 10X17H13M3T | 950—1050 | В случае сварки проволокой св. 04X19Н11 М3 или электродами типа Э-07Х19Н11МЗГ2Ф (марки ЭА-400/10У, ЭА-400/10Т, проволока св. 04Х19Н11МЗ и др.) |
9
ГОСТ Р 71256—2024
Окончание таблицы 5
Режим | Марка стали, сплава | Закалка, стабилизирующий отжиг | Дополнительные указания | |
Температура, °C | Среда охлаждения | |||
4 | 07X21Г7АН5, 07X21Г7АН5-Ш | 950—1050 | Воздух | Для повышения ударной вязкости сварных соединений при температуре эксплуатации, если изделие работает при криогенных температурах |
03Х20Н16АГ6-Ш | Для снятия остаточных напряжений сварных сборок, работающих при криогенных температурах | |||
08Х22Н6Т, 08X21Н6М2Т, 15Х18Н12С4ТЮ, 15Х18Н12С4ТЮ-Ш | Для повышения общей коррозионной стойкости и снятия остаточных напряжений | |||
5 | 12Х18Н9Т, 12Х18Н10Т, 08Х18Н10Т, 08Х18Н10Т-ВД, 08Х18Н10Т-Ш, 09Х14Н16Б, 10Х14Г14Н4Т, 09Х14Н19В2БР | 850—920 | В случае сварки электродами типа Э-08Х19Н10Г2МБ (марок ЭА 898/21Б и др.) для снятия остаточных напряжений в сварных сборках, работающих при температуре не выше 450 °C | |
6 | 10Х15Н9СЗБ1-Ш | 1000—1100 | Для повышения общей коррозионной стойкости и снятия остаточных напряжений | |
7 | 09Х14Н16Б | 1110—1130 | ||
8 | 09Х14Н19В2БР | 1140—1160 | ||
9 | 12Х18Н9Т*, 12Х18Н10Т, 08Х18Н10Т, 08Х18Н10Т-ВД | 950—970 | ТО проводят в случае приварки патрубков внутренним диаметром 100 мм и более к корпусу (без оттяжки) согласно КД | |
10 | 06ХН28МДТ** | 1050—1080 | Для повышения общей коррозионной стойкости, стойкости против МКК и снятия остаточных напряжений | |
11 | Н70МФВ | 1100—1120 | Вода, водяной душ | |
12 | 12Х18Н9Т, 12Х18Н10Т, 08Х18Н10Т, 08Х18Н10Т-ВД, 08Х18Н10Т-Ш | Отпуск 375—400 | Воздух | Для снятия остаточных напряжений сварных сборок, работающих при температуре не выше 350 °C, после окончательной механической обработки (до притирки), если проведение других видов ТО нецелесообразно |
* Для сплава марки 06ХН28МДТ допускается проводить ТО при температуре от 950 °C до 970 °C при условии обеспечения стойкости против МКК.
** Загрузка в печь при температуре от 950 °C до 970 °C, нагрев до температуры от 950 °C до 970 °C, выдержка от 2 до 2,5 ч, охлаждение на воздухе; набор температуры в печи после загрузки должен быть обеспечен в течение 1 ч.
Примечания
1 При наличии твердых наплавок охлаждение после ТО проводить с печью или не ниже 300 °C с печью, далее — на воздухе.
2 Выдержка при температуре отпуска по режиму 12 — от 6 до 10 ч.
3 При проведении стабилизирующего отжига по режимам 2, 5 выдержка после прогрева садки — не менее 2 ч.
4 Выдержка при температуре закалки по режимам 1,4, 6—8, 10 — не менее 2,5 мин, а по режиму 11 — не менее 2 ч.
10
ГОСТ Р 71256—2024
6.9 При полной ТО любых сварных соединений, а также при отпусках или аустенизации продольных, меридиональных, хордовых и круговых сварных соединений и всех наплавленных деталей сварные (наплавленные) изделия следует помещать в печь целиком.
При отпусках и аустенизации кольцевых сварных соединений труб и других цилиндрических деталей допускается местная ТО, что должно быть оговорено в КД или ПТД.
При местной ТО сварных соединений общая зона контролируемого нагрева металла состоит из основной и дополнительных зон и должна включать сварной шов и примыкающие к его краям участки основного металла на расстоянии L, минимальные значения которых в зависимости от диаметров и толщин свариваемых деталей приведены в таблице 6.
Основная зона контролируемого нагрева включает сварной шов и примыкающие к его краям участки основного металла на расстояниях, равных толщинам свариваемых деталей при толщине деталей не более 50 мм включительно, а при большей толщине деталей — на расстоянии 50 мм. В пределах основной зоны температура металла в процессе выдержки должна соответствовать заданной температуре отпуска (аустенизации) с учетом установленных допусков.
Таблица 6 — Ширина зоны контролируемого нагрева основного металла L, мм
Номинальные размеры свариваемых деталей на участках, примыкающих к сварному шву | Минимальное расстояние, мм | |
Наружный диаметр, мм | Толщина, мм | |
Не более 200 включ. | Не более 20 включ. | 40 |
Св. 20 | 50 | |
Св. 200 до 300 включ. | Не более 25 включ. | 60 |
Св. 25 | 70 | |
Св. 300 до 500 включ. | Не более 30 включ. | 90 |
Св. 30 | 120 | |
Св. 500 до 1000 включ. | Не более 50 включ. | 180 |
Св. 50 до 100 включ. | 250 | |
Св. 100 | 300 |
Примечание — При наружном диаметре свариваемых деталей свыше 1000 мм значение L устанавливают в ПТД.
Дополнительная зона контролируемого нагрева включает участки основного металла общей зоны, не входящие в основную зону. В пределах дополнительной зоны допускается снижение температуры металла в процессе выдержки по сравнению с заданной температурой отпуска (аустенизацией), но не более чем на 50 °C от минимально допустимой температуры (с учетом минусового допуска).
6.10 Аустенизации при температуре от 970 °C до 1020 °C подлежат сварные соединения деталей из стали аустенитного класса номинальной толщиной свыше 10 мм, предназначенные для работы при температуре:
- 450 °C и выше (сталь марок: 08Х18Н10Т, 12Х18Н9Т, 12Х18Н10Т);
- свыше 500 °C (сталь марки 12Х18Н9);
- свыше 560 °C (сталь марки 08Х16Н11МЗ).
Сварные сборки из стали марок 07X21Г7АН5, 07X21Г7АН5-Ш при толщине свариваемых деталей до 1,5 мм включительно допускается не подвергать ТО.
6.11 ТО сварных сборок из стали марок 10Х32Н8, 10Х32Н8-Ш, 10Х32Н8-ВД следует проводить по режимам, приведенным в таблице 7:
а) при необходимости повышения коррозионной стойкости и стабилизации размеров — по режиму 13 (в том числе и в случае сварки разнородных металлов стали марки 10Х32Н8 и стали типа Х18Н1 ОТ);
б) при необходимости получения твердости не менее 26 HRC отпуск следует проводить соответственно по режимам 14 или 15.
11
ГОСТ Р 71256—2024
Таблица 7 — Режимы ТО сварных сборок из сталей марок 10Х32Н8, 10Х32Н8-Ш, 10Х32Н8-ВД
Режим | Марка стали | ТО | Твердость, HRC | ||||
Закалка | Отпуск | ||||||
Температура, °C | Среда охлаждения | Температура, °C | Время выдержки, ч | Среда охлаждения | |||
13 | 10Х32Н8 10Х32Н8-Ш 10Х32Н8-ВД | 1080—1120 | Вода | 270—300 | 2—4 | Воздух | — |
14 | — | — | 450—500 | 26—32 | |||
15 | 8—15 | 32,0—37,5 | |||||
Примечания 1 Выдержка при температуре закалки — из расчета не менее 2,5 мин на 1 мм наибольшей толщины стенки, но не менее 1 ч. 2 При наличии о-фазы в стали марки 10Х32Н8, нагрев сварных сборок при ТО по режиму 13 следует проводить в соответствии с 6.5. |
6.12 Посадку сварных сборок на ТО проводят в печь, нагретую до температуры не выше 500 °C.
Для изделий АС температура печи при загрузке в нее сварной сборки для ТО должна отличаться от температуры основного металла деталей сварной сборки не более чем на 300 °C.
Сварные сборки с твердыми наплавками, подвергающиеся ТО непосредственно после наплавки, допускается загружать в печь, нагретую до температуры не выше 300 °C.
Посадку на ТО сварных сборок из стали марок 10Х32Н8, 10Х32Н8-Ш, 10Х32Н8-ВД (по режиму 13) и из сплава Н70МФВ проводят в печь, нагретую до температуры закалки.
6.13 Сварные сильфонные сборки после приварки сильфонов ТО не подвергают.
7 Режимы термической обработки деталей и сварных сборок
из жаропрочных сталей и сплавов
7.1 Для получения показателей механических свойств и твердости, установленных ГОСТ Р 71255, детали арматуры из сталей и сплавов подвергают ТО по режимам, приведенным в таблице 8.
Таблица 8 — Режимы ТО и твердость жаропрочных сталей и сплавов
Марка стали или сплава | ТО | Твердость, HRC | |||||
Закалка | Старение | ||||||
Температура, °C | Время выдержки, ч | Среда охлаждения | Температура, °C | Время выдержки, ч | Среда охлаждения | ||
45Х14Н14В2М | Режим 1 1170—1200 | 0,5—1 | Вода | 730—770 | 5 | Воздух | 170—270 |
Режим 2 1090—1110 | |||||||
12ХН35ВТ | 1080—1100 | 1—1,5* | Режим 1 Двойное старение | 207—269 | |||
а) 850—900 б) 690—710 | 10 10—50 | Воздух | |||||
Режим 2 | |||||||
690—700 | 50 | ||||||
12ХН35ВТ-ВД | 1080—1100 | 1—1,5* | Двойное старение | 207—269 | |||
а) 840—860 б) 690—710 | 10 35—50 | Воздух |
12
Продолжение таблицы 8
ГОСТ Р 71256—2024
Марка стали или сплава | ТО | Твердость, HRC | |||||
Закалка | Старение | ||||||
Температура, °C | Время выдержки, ч | Среда охлаждения | Температура, °C | Время выдержки, ч | Среда охлаждения | ||
ХН75ТБЮ | 1090—1110 | 6 | Вода | Режим 1 Для работы при температуре до 750 °C двойное ступенчатое старение | 255—285 | ||
а) 1000 | 2 | С печью не выше 900 °C | |||||
900 | 1 | С печью 800 °C | |||||
800 | 2 | Воздух | |||||
б) 750 | 20 | ||||||
Для работы при температуре не выше 700 °C | 269—302 | ||||||
700 | 48 | Воздух | |||||
Режим 2 Для работы при температуре 800 °C двойное ступенчатое старение | 255—285 | ||||||
а) 1000 | 2 | С печью не выше 900 °C | |||||
900 | 1 | С печью не выше 820 °C | |||||
820 | 2 | Воздух | |||||
б) 800 | 20 | ||||||
10ХН28ВМАБ | 1100—1120 | 1,5—2 мин на 1 мм наибольшего сечения | Воздух | — | — | — | — |
12Х25Н16Г7АР, 12Х25Н16Г7АР-Ш | 1050-1150 | 2 мин на 1 мм наибольшего диаметра (толщины) | Вода | — | — | — | 163—217 |
ХН60ВТ | 1190—1210 | 2 | Вода, воздух | 800 | 10 | Воздух | 190—250 |
10X11H23T3MP | Режим 1 1090—1110 | 1—2 | Масло | Двойное старение | |||
а) 780 б) 650 | 16 16 | Воздух | 285—341 | ||||
Режим 2** 1000— 1050 | 1 | Воздух | 700 | 3 | — |
13
ГОСТ Р 71256—2024
Окончание таблицы 8
Марка стали или сплава | то | Твердость, HRC | |||||
Закалка | Старение | ||||||
Температура, °C | Время выдержки, ч | Среда охлаждения | Температура, °C | Время выдержки, ч | Среда охлаждения | ||
ХН80ТБЮ | 1090—1110 | 6 | Вода | Тройное ступенчатое старение | 207—241 | ||
а) 1000 | 2 | С печью не выше 900 °C | |||||
900 | 1 | С печью не выше 800 °C | |||||
800 | 2 | Воздух | |||||
б) 750 | 20 | ||||||
Для рабочей температуры 700 °C | |||||||
700 | 48 | Воздух | |||||
Для рабочей температуры 650 °C | |||||||
650 | 48 | Воздух | |||||
ХН70ВМЮТ | 1140—1160 | 3 | Масло | 800 | 20 | Воздух | 270—320 |
ХН62МВКЮ | 1210— 1230 | 4—6 | Воздух | 950 | 8 | 260—360 | |
ХН63М9Б2Ю | 1050—1100 | 2 | 700 | 15 | 241—302 | ||
36НХТЮ | 920—950 | 1—3 мин на 1 мм наибольшего сечения | Вода | 650—670 | 2—4 | 32,0— 41,5 HRC |
* Время выдержки для заготовок диаметром (толщиной) от 90 до 150 мм включ. — 1,5—2,5 ч.
** Режим для работы материала при криогенных температурах.
Примечания
1 Заготовки из стали марки 12Х25Н16Г7АР диаметром (толщиной) менее 10 мм допускается охлаждать начиная от температуры закалки на воздухе.
2 Для сплавов 12ХН35ВТ, 12ХН35ВТ-ВД продолжительность старения при температуре от 690 °C до 710 °C определяют содержанием титана. При содержании титана от 1,1 % до 1,2 % продолжительность старения — 50 ч, при большем содержании титана — от 10 до 40 ч.
3 Если в таблице 8 не указаны температурные пределы, при старении заготовок допускается отклонение по температуре ±10 °C.
4 Значение твердости не устанавливливают для тех сталей, у которых в графе «Твердость» твердость не указана.
5 Для кованых штоков из сплава 12ХН35ВТ-ВД закалку следует проводить при температуре от 1020 °C до 1040 °C.
Механические свойства сталей, определяемые на продольных образцах, термообработанные по указанным режимам — в соответствии с приложением А.
Термической обработке подвергают заготовки.
7.2 Режим 2 ТО стали марки 45Х14Н14В2М применяют для деталей, работающих при температуре свыше 450 °C, а также для деталей, подвергаемых последующему азотированию.
7.3 Режим 2 ТО стали марки 10X11H23T3MP предназначен для деталей, работающих при криогенных температурах.
7.4 Для обеспечения максимальной пластичности стали марки 36НХТЮ применяют только аустенизацию согласно данным, приведенным в таблице 8.
14
ГОСТ Р 71256—2024
7.5 Старение деталей, предназначенных для наплавки стеллитом, следует проводить после наплавки с охлаждением после старения с печью или до температуры 300 °C в печи, далее на воздухе.
7.6 Если деталь подвергают азотированию, то в случае совпадения температуры старения и азотирования эти операции можно совместить.
7.7 При поставке полуфабрикатов в термообработанном состоянии по режимам, указанным в НД на поставку (см. сертификат на материал), допускается повторную ТО деталей (заготовок) не проводить при условии выполнения требований 5.13 по согласованию с проектирующей организацией.
7.8 Сварные сборки из сплавов марок: 12ХН35ВТ, 12ХН35ВТ-ВД, ХН60ВТ, ХН80ТБЮ, ХН63М9Б2Ю, подвергают старению в соответствии с таблицей 8.
Сварку перечисленных сплавов проводят в закаленном состоянии в соответствии с таблицей 8.
Сварные сильфонные сборки после приварки сильфона ТО не подвергают, в связи с этим детали подвергают закалке и старению до сварки.
7.9 Сварные сборки из стали марок 12Х25Н16Г7АР, 12Х25Н16Г7АР-Ш следует подвергать ТО по режиму: закалка при температуре от 950 °C до 1050 °C с последующим охлаждением на воздухе.
Сварные сборки из стали марки 10ХН28ВМАБ подвергают ТО для снятия сварочных напряжений при температурах от 950 °C до 1000 °C. После сварки узлы толщиной сварных соединений не более 5 мм включительно можно ТО не подвергать.
Выдержку при температуре закалки определяют исходя из расчета не менее 2,5 мин на 1 мм наибольшей толщины стенки.
Посадку сварных сборок на ТО проводят в печь, нагретую до температуры не выше 500 °C. Сварные сборки с наплавкой стеллита, подвергающиеся ТО непосредственно после наплавки, допускается загружать в печь, нагретую до температуры не выше 600 °C.
7.10 ТО сварных сборок, изготовленных из стали марок 10ХН28ВМАБ, 12Х25Н16Г7АР, 12Х25Н16Г7АР-Ш, где допускается пониженная по сравнению с основным металлом прочность сварных швов и снятие напряжений не является обязательным, можно не проводить, кроме сборок, работающих при криогенных температурах.
8 Общие технологические указания по термической обработке
8.1 При нагреве в пламенных печах не допускается прямое попадание пламени непосредственно от форсунки на заготовки и сварные сборки.
8.2 Основными охлаждающими средами являются спокойный воздух при температуре цеха, вода температурой от 20 °C до 60 °C и минеральные масла температурой от 20 °C до 70 °C.
8.3 В качестве горячей среды для охлаждения заготовок из стали марок 10ХН32Н8, 10Х32Н8-ВД и 10Х32Н8-Ш в сечении более 50 мм рекомендуется применять селитру. Ванну необходимо охлаждать проточной водой. При разогреве ванны температура селитры должна быть не выше 450 °C.
8.4 При расчете времени выдержки длинных труб и замкнутых сосудов условную толщину принимают равной трем стенкам.
8.5 Время выдержки заготовок (деталей), сварных сборок исчисляют с момента прогрева садки и выхода печи на заданную температуру.
8.6 При необходимости допускается проводить повторную ТО. Количество повторных ТО должно быть не более двух. Дополнительный отпуск не считают повторной ТО, а их количество не ограничено.
8.7 Детали или сварные сборки, на которых по условиям работы недопустима окисленная поверхность, а механическая зачистка окалины или осветление травлением невозможны, подвергают ТО в защитных средах или предохраняют от окисления другим надежным способом.
9 Контроль термической обработки
9.1 При ТО заготовок (деталей), сварных соединений и наплавленных деталей в соответствии с требованиями ПТД и КД, а также изделий АС согласно [1], [2] следует контролировать соблюдение:
- методов и видов ТО;
- применяемого термического оборудования;
- последовательности и порядка выполнения ТО и отдельных ее этапов (в том числе предварительных, промежуточных и окончательных отпусков);
- режимов ТО (температуры печи при загрузке, скорости нагрева, температуры и продолжительности выдержек, условий, среды или скорости охлаждения);
15
ГОСТ Р 71256—2024
- методов и порядка контроля температурных режимов (расположения термопар или других устройств для измерения температуры, их количество и т. п.);
- температуры в точках, предусмотренных в [2], при контроле требуемой зоны нагрева сварного соединения и прилегающих к нему участков;
- условий, исключающих пластическую деформацию под действием собственной массы;
- других параметров, контроль которых предусмотрен в ПТД.
9.2 Печные агрегаты, в которых изделия нагреваются под ТО, должны обеспечивать распределение температуры в рабочей части печи в пределах допуска, указанного в режиме ТО.
Все печные агрегаты должны проходить проверку на распределение температуры по поду и высоте печи по установленному(ым) графику (инструкциям).
9.3 После ремонта печного агрегата, а также при замене нагревателей следует проводить регулирование печи с контрольной проверкой. При проверке устанавливают рабочую зону печи, в пределах которой можно располагать детали (заготовки), сварные сборки при ТО.
Перед началом каждой смены необходимо проверять состояние пирометрической аппаратуры, регулирующей и контролирующей температуру печи.
9.4 Для контроля режимов ТО деталей изделий МО РФ и АС следует использовать термоэлектрические преобразователи (термопары) с устройствами для автоматической записи параметров режима.
Термопары должны быть установлены в печи непосредственно на подвергаемых ТО сварных (наплавленных) изделиях. Количество и расположение термопар должны обеспечивать возможность контроля по всему объему печи при общей ТО и контроля зон нагрева при местной ТО.
При внепечной ТО допускается использование других средств контроля режимов ТО, обеспечивающих требуемую точность измерения температуры (радиационные пирометры и др.).
При ТО изделий АС со сварными соединениями категории III по согласованию с ГМО допускается контроль режимов ТО проводить по термопаре, установленной в печи. При этом проводят контрольные нагревы с периодичностью не реже одного раза в 3 мес, подтверждающие, что разность показаний термопар, установленных в печи и непосредственно на термообрабатываемом изделии (в конкретной точке), не превышает 15 °C, фиксируя результаты контроля в специальном журнале.
После выполнения ТО должны быть зафиксированы номер садки и номер печи (для печной ТО) для проведения ТО, данные партии металла и производственный шифр (номер) сварного (наплавленного) изделия или сварного соединения.
9.5 Объем контроля качества изделий, прошедших ТО, и сдаточные характеристики устанавливают в КД в соответствии с ГОСТ Р 71255 и с учетом требований [1], [2].
9.6 При отсутствии в КД требования по контролю твердости или механических свойств, термически обработанные детали или заготовки проходят контроль твердости по группе II ГОСТ Р 71255. Твердость должна соответствовать нормам, указанным в таблицах 1,4, 7, 8.
9.7 При проведении ТО следует соблюдать правила техники безопасности в соответствии с ГОСТ 12.3.004.
10 Оформление документации
10.1 Необходимость проведения ТО деталей (заготовок) и сварных сборок указывают в КД с ссылкой на настоящий стандарт.
10.2 В зависимости от назначения отжига для стали марки 12X17 указывают номер режима ТО.
10.3 В зависимости от требуемого уровня механических свойств или температуры рабочей среды для стали марок 45Х14Н14В2М, 10X11H23T3MP и сплава ХН75ТЮБ в КД дополнительно указывают номер режима ТО. Для сплава 12ХН35ВТ режим ТО определяет изготовитель.
10.4 Для сварных сборок из сталей и сплавов аустенитного и аустенитно-ферритного классов в КД дополнительно указан номер режима по таблицам 5 и 7.
10.5 При наличии сварки или наплавки деталей, упрочняемых старением, в КД свариваемой или наплавляемой детали указывают: «Термообработка по ГОСТ Р 71256—2024; старение заготовки (детали) следует проводить после сварки (или наплавки)».
10.6 Фактический режим ТО и результаты замеров твердости деталей (заготовок) и сварных сборок фиксируют в журнале термического цеха с указанием обозначений КД деталей и изделия.
10.7 После выполнения ТО фиксируют номер садки и номер печи (для печной ТО), дату проведения ТО и производственный шифр (номер) сварной (наплавленной) сборки.
16
Приложение А (обязательное)
Механические свойства заготовок из высоколегированных сталей и сплавов
Таблица А.1 — Механические свойства заготовок из высоколегированных сталей и сплавов
Марка стали или сплава | Диаметр (толщина) заготовки, мм | Механические свойства, не менее | Твердость | |||||
Временное сопротивление ов, МПа | Предел текучести о0 2, МПа ’ | Относительное удлинение 65, % | Относительное сужение у, % | Ударная вязкость, KCU, Дж/см2 | HRC | НВ | ||
12X13 | Не более 60 включ. | 588 | 410 | 20 | 60 | 9 | — | 170—195 |
20X13 | 1274—1470 | 1078—1274 | 3—8 | — | 10—40 | 39,6—44,5 | 350—400 | |
882 | 686 | 10 | 40 | 40 | 29—36 | 269—310 | ||
784 | 539 | 12 | 45 | 60 | 23,5—29,0 | 235—269 | ||
647 | 441 | 16 | 55 | 80 | — | 197—248 | ||
Не более 100 включ. | 15 | 50 | 75 | |||||
Не более 300 включ. | 13 | 45 | 50 | |||||
30X13 | Не более 60 включ. | 1470—1666 | 1176—1372 | 1—6 | 2—7 | — | 49,5—55,5 | — |
882 | 686 | 10 | 40 | 30 | 29—37 | 269—330 | ||
784 | 588 | 12 | 42 | 40 | 23—30 | 235—277 | ||
Не более 200 включ. | 735 | 40 | ||||||
95X18 | Не более 60 включ. | 1470—1666 | — | — | — | 3—5 | >56,5 | — |
12X17 | 392 | 245 | 20 | 50 | 30 | — | 126—197 | |
157 | 25 | 55 | 5 | |||||
15Х25Т | 441 | 294 | 20 | 45 | — | 143—163 | ||
16Х-ВИ | — | 250 | 196 | 25 | 65 | 109* | ||
07X16Н4Б, 07Х16Н4Б-Ш | Не более 200 включ. | 1029 | 931 | 10 | 45 | 78 | 302—351 | |
882 | 735 | 13 | 50 | 84 KCV, 60 | 269—302 | |||
Не более 400 включ. | 686 | |||||||
Не более 500 включ. | 12 | 40 |
ГОСТ Р 71256—2024
00
Продолжение таблицы А. 1
Марка стали или сплава | Диаметр (толщина) заготовки, мм | Механические свойства, не менее | Твердость | |||||
Временное сопротивление ав, МПа | Предел текучести о0 2, МПа ' | Относительное удлинение 35, % | Относительное сужение у, % | Ударная вязкость, KCU, Дж/см2 | HRC | НВ | ||
14Х17Н2 | Не более 60 включ. | 1080 | 834 | 10 | 25 | 50 | 37,0—42,5 | 331—389 |
931 | 735 | 30 | 30—37 | 277—331 | ||||
735 | 490 | 14 | 50 | 60 | 25—28 | 240—260 | ||
784 | 568 | 22,5—31,0 | 229—285 | |||||
Не более 100 включ. | 687 | 540 | 12 | 43 | 50 | |||
Не более 300 включ. | 40 | 40 | ||||||
25Х17Н2Б-Ш | Не более 60 включ. | 1470 | 1176 | 8 | 45 | 40 | >44,5 | >415 |
980 | 784 | 12 | 50 | 50 | >31 | >285 | ||
09X16Н4Б | 1180 | 830 | 8 | 40 | 60 | 39—42,5 | 345—388 | |
980 | 835 | 45 | 30—36 | 269—302 | ||||
Не более 200 включ. | 931 | 784 | 42 | |||||
12Х18Н9 | Не более 60 включ. | 490 | 196 | 45 | 55 | 121—179 | ||
Не более 200 включ. | 40 | 48 | ||||||
Не более 300 включ. | 38 | 45 | ||||||
12Х18Н9Т | Не более 60 включ. | 510 | 40 | 55 | ||||
Не более 100 включ. | 39 | 50 | ||||||
Не более 160 включ. | 37 | 45 | ||||||
Не более 500 включ. | 44 | |||||||
08Х18Н10Т, 12Х18Н10Т | Не более 60 включ. | 490 | 40 | 55 | ||||
Не более 100 включ. | 39 | 50 | ||||||
Не более 200 включ. | 38 | 40 | ||||||
Более 200 | 35 | |||||||
08Х18Н10Т-ВД | Не более 250 включ. | 206 | 40 | 55 |
ГОСТ Р 71256—2024
Продолжение таблицы А. 1
Марка стали или сплава | Диаметр (толщина) заготовки, мм | Механические свойства, не менее | Твердость | |||||
Временное сопротивление ав, МПа | Предел текучести о0 2, МПа ' | Относительное удлинение 35, % | Относительное сужение у, % | Ударная вязкость, KCU, Дж/см2 | HRC | НВ | ||
10Х17Н13М2Т, 10X17H13M3T | Не более 60 включ. | 510 | 196 | 40 | 55 | — | — | 121—179 |
Не более 200 включ. | 38 | 50 | ||||||
Не более 500 включ. | 36 | 45 | ||||||
10Х15Н9СЗБ1-Ш | Не более 60 включ. | 589 | 245 | 25 | — | 100 | — | |
08Х17Н15МЗТ | Не более 500 включ. | 490 | 196 | 35 | 45 | — | <200 | |
09Х14Н16Б | Не более 60 включ. | 50 | 131—156 | |||||
09Х14Н19В2БР | 510 | 216 | ||||||
10Х14Г14Н4Т | 637 | 245 | 121—179 | |||||
06ХН28МДТ | Не более 200 включ. | 510 | 216 | 36 | 40 | <200 | ||
Не более 500 включ. | 33 | 35 | ||||||
15Х18Н12С4ТЮ, 15Х18Н12С4ТЮ-Ш | Не более 60 включ. | 715 | 372 | 25 | 40 | 80 | 155—170 | |
08Х22Н6Т | Не более 60 включ. | 589 | 343 | 20 | 45 | — | 140—200 | |
Не более 100 включ. | 19 | 40 | 80 | |||||
Не более 300 включ. | 17 | 35 | 60 | |||||
08X21Н6М2Т | Не более 60 включ. | 590 | 345 | 25 | 45 | 80 | ||
Не более 200 включ. | 539 | 343 | 22 | 40 | ||||
От 200 до 500 включ. | 18 | 37 | 60 | |||||
07X21Г7АН5 | Не более 60 включ. | 686 | 363 | 40 | 50 | 130 | <207 | |
07X21Г7АН5-Ш | 657 | 333 | ||||||
03X20 Н16АГ6-Ш | 637 | 343 | 30 | — | При температуре минус 196 °C 120 | — | ||
Н70МФВ | Не более 60 включ. | 784 | — | 180—230 |
ГОСТ Р 71256—2024
bJ о
Окончание таблицы А. 1
Марка стали или сплава | Диаметр (толщина) заготовки, мм | Механические свойства, не менее | Твердость | |||||
Временное сопротивление ав, МПа | Предел текучести о0 2, МПа ' | Относительное удлинение 35, % | Относительное сужение у, % | Ударная вязкость, KCU, Дж/см2 | HRC | НВ | ||
45Х14Н14В2М | — | 686 | 294 | 20 | 35 | 50 | — | 170—270 |
08Х15Н24В4ТР | Не более 200 включ. | 735 | 490 | 18 | 80 | >229 | ||
09X15Н8Ю | — | 1130 | 882 | 11 | — | 40 | 35,5—40,5 | — |
10Х32Н8, 10Х32Н8-Ш, 10Х32Н8-ВД | Не более 60 включ. | 637 | 490 | 20 | 45 | 80 | <26 | |
931—1225 | 784—1078 | 10 | — | 10 | 32—39 | |||
833—931 | 686—784 | 15 | 40 | 26—32 | ||||
12ХН35ВТ | Не более 650 включ. | 735 | 392 | 25 | 70 | — | 207—269 | |
12ХН35ВТ-ВД | Не более 200 включ. | 830 | 490 | 18 | 40 | 60 | ||
ХН70ВМЮТ | Не более 100 включ. | 980 | 588 | 20 | 25 | 270—320 | ||
12Х25Н16Г7АР, 12Х25Н16Г7АР-Ш | Не более 180 включ. | 735 | 343 | 45 | 45 | 250 | — | 163—217 |
ХН60ВТ | Не более 100 включ. | 686 | 20 | 30 | 70 | 190—250 | ||
10X11H23T3MP | 980 | 784 | 25 | 50 | 285—341 | |||
ХН62ВМКЮ | Не более 60 включ. | 1178 | 735 | 12 | 15 | 30 | 260—360 | |
36НХТЮ | 1029 | 637 | 14 | 25 | 50 | 32—42 | — | |
ХН75ТБЮ | Не более 200 включ. | 931 | 539 | 24 | 28 | 100 | — | 255—302 |
10ХН28ВМАБ | — | 735 | 343 | 30 | 40 | 80 | — | |
ХН80ТБЮ | Не более 55 включ. | 833 | 441 | 18 | 18 | 60 | 207—241 | |
ХН63М9Б2Ю | — | 931 | 539 | 30 | — | — | 241—302 |
ГОСТ Р 71256—2024
Справочные данные.
Примечание — Механические свойства приведены для продольных образцов; температура испытаний — 20 °C.
ГОСТ Р 71256—2024
Приложение Б (рекомендуемое)
Режимы термической обработки для улучшения обрабатываемости
Таблица Б.1 — Режимы термической обработки для улучшения обрабатываемости
Марка материала | Отжиг, отпуск | Твердость, НВ, не более | ||
Температура, °C | Время выдержки, ч | Среда охлаждения | ||
12X13 | 740—780 | 1—3 | Воздух | 170 |
20X13 | 197 | |||
30X13 | 2—6 | 205 | ||
95X18 | 240 | |||
14Х17Н2 | 620—670 | 4—8 | 229 | |
07X16Н4Б | 630—650 | 4—8 | 269 | |
09Х16Н4Б-Ш | Режим 1 | С печью до температуры 300 °C, далее на воздухе | 285 | |
600—630 | 4—8 | |||
Режим 2 (двухступенчатый) | ||||
I ступень 690—710 II ступень 570—590 | 8 | |||
25Х17Н2Б-Ш | Режим отжига двухступенчатый | |||
I ступень 870—890 | 4 | С печью с скоростью от 30 °С/ч до 40 °С/ч до 400 °C, далее на воздухе | 293 | |
II ступень 650—670 | С печью с скоростью от 30 °С/ч до 40 °С/ч до 500 °C, далее на воздухе |
21
ГОСТ Р 71256—2024
Библиография
[1] Федеральные нормы и правила в области использования атомной энергии НП-089-15
[2] Федеральные нормы и правила в области использования атомной энергии НП-104-18
[3] Правила и нормы в атомной энергетике НП-105-18
[4] Федеральные нормы и правила в области использования атомной энергии НП-071-18
Правила устройства и безопасной эксплуатации оборудования и трубопроводов атомных энергетических установок
Сварка и наплавка оборудования и трубопроводов атомных энергетических установок
Правила контроля металла оборудования и трубопроводов атомных энергетических установок при изготовлении и монтаже
Правила оценки соответствия продукции, для которой устанавливаются требования, связанные с обеспечением безопасности в области использования атомной энергии, а также процессов ее проектирования (включая изыскания), производства, строительства, монтажа, наладки, эксплуатации, хранения, перевозки, реализации, утилизации и захоронения
22
ГОСТ Р 71256—2024
УДК 001.4:621.643.4:006.354 ОКС 23.060
Ключевые слова: термическая обработка, заготовка, деталь, режим термической обработки, закалка, среда охлаждения, время выдержки
23
Редактор fl.С. Зимилова Технический редактор И.Е. Черепкова Корректор С.И. Фирсова Компьютерная верстка Л.А. Круговой
Сдано в набор 17.04.2024. Подписано в печать 03.05.2024. Формат 60x847s. Гарнитура Ариал.
Усл. печ. л. 3,26. Уч.-изд. л. 2,77.
Подготовлено на основе электронной версии, предоставленной разработчиком стандарта
Создано в единичном исполнении в ФГБУ «Институт стандартизации» , 117418 Москва, Нахимовский пр-т, д. 31, к. 2.