ФЕДЕРАЛЬНОЕ АГЕНТСТВО
ПО ТЕХНИЧЕСКОМУ РЕГУЛИРОВАНИЮ И МЕТРОЛОГИИ
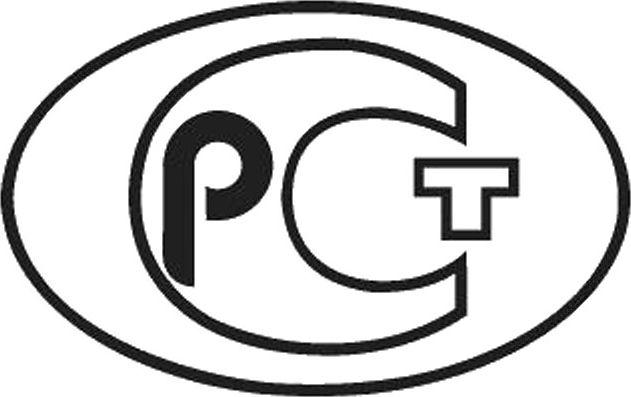
НАЦИОНАЛЬНЫЙ СТАНДАРТ РОССИЙСКОЙ ФЕДЕРАЦИИ
ГОСТ Р
71257— 2024
Арматура трубопроводная
ТЕРМИЧЕСКАЯ ОБРАБОТКА ЗАГОТОВОК ИЗ УГЛЕРОДИСТЫХ И ЛЕГИРОВАННЫХ КОНСТРУКЦИОННЫХ СТАЛЕЙ
Издание официальное
Москва Российский институт стандартизации 2024
ГОСТ Р 71257—2024
Предисловие
1 РАЗРАБОТАН Акционерным обществом «Научно-производственная фирма «Центральное конструкторское бюро арматуростроения» (АО «НПФ «ЦКБА»)
2 ВНЕСЕН Техническим комитетом по стандартизации ТК 259 «Трубопроводная арматура и сильфоны»
3 УТВЕРЖДЕН И ВВЕДЕН В ДЕЙСТВИЕ Приказом Федерального агентства по техническому регулированию и метрологии от 26 апреля 2024 г. № 561-ст
4 ВВЕДЕН ВПЕРВЫЕ
Правила применения настоящего стандарта установлены в статье 26 Федерального закона от 29 июня 2015 г. № 162-ФЗ «О стандартизации в Российской Федерации». Информация об изменениях к настоящему стандарту публикуется в ежегодном (по состоянию на 1 января текущего года) информационном указателе «Национальные стандарты», а официальный текст изменений и поправок — в ежемесячном информационном указателе «Национальные стандарты». В случае пересмотра (замены) или отмены настоящего стандарта соответствующее уведомление будет опубликовано в ближайшем выпуске ежемесячного информационного указателя «Национальные стандарты». Соответствующая информация, уведомление и тексты размещаются также в информационной системе общего пользования — на официальном сайте Федерального агентства по техническому регулированию и метрологии в сети Интернет (www.rst.gov.ru)
©Оформление. ФГБУ «Институт стандартизации», 2024
Настоящий стандарт не может быть полностью или частично воспроизведен, тиражирован и распространен в качестве официального издания без разрешения Федерального агентства по техническому регулированию и метрологии
II
ГОСТ Р 71257—2024
Содержание
1 Область применения..................................................................1
2 Нормативные ссылки..................................................................1
3 Термины, определения, сокращения и обозначения........................................1
4 Технические требования...............................................................2
5 Режимы термической обработки........................................................3
6 Общие технологические указания по термической обработке................................7
7 Контроль термической обработки.......................................................7
8 Оформление документации............................................................8
Приложение А (обязательное) Механические свойства углеродистых и легированных конструкционных сталей в зависимости от толщины (диаметра) заготовки..........9
Приложение Б (рекомендуемое) Методика расчета времени нагрева садки.....................12
Приложение В (рекомендуемое) Продолжительность охлаждения изделий больших сечений в охлаждающих средах при закалке.........................................14
Библиография........................................................................15
III
ГОСТ Р 71257—2024
НАЦИОНАЛЬНЫЙ СТАНДАРТ РОССИЙСКОЙ ФЕДЕРАЦИИ
Арматура трубопроводная
ТЕРМИЧЕСКАЯ ОБРАБОТКА ЗАГОТОВОК ИЗ УГЛЕРОДИСТЫХ И ЛЕГИРОВАННЫХ КОНСТРУКЦИОННЫХ СТАЛЕЙ
Pipeline valves.
Heat treatment of blanks made of carbon and alloy structural steels
Дата введения — 2024—08—01
1 Область применения
Настоящий стандарт устанавливает режимы и основные технологические требования по термической обработке заготовок из углеродистых и легированных конструкционных сталей и является типовым технологическим процессом проведения термической обработки.
2 Нормативные ссылки
В настоящем стандарте использованы нормативные ссылки на следующие стандарты:
ГОСТ 12.3.004 Система стандартов безопасности труда. Термическая обработка металлов. Общие требования безопасности
ГОСТ 33439 Металлопродукция из черных металлов и сплавов на железоникелевой и никелевой основе. Термины и определения по термической обработке
ГОСТ Р 71255 Арматура трубопроводная. Поковки, штамповки и заготовки из проката. Технические требования
Примечание — При пользовании настоящим стандартом целесообразно проверить действие ссылочных стандартов в информационной системе общего пользования — на официальном сайте Федерального агентства по техническому регулированию и метрологии в сети Интернет или по ежегодному информационному указателю «Национальные стандарты», который опубликован по состоянию на 1 января текущего года, и по выпускам ежемесячного информационного указателя «Национальные стандарты» за текущий год. Если заменен ссылочный стандарт, на который дана недатированная ссылка, то рекомендуется использовать действующую версию этого стандарта с учетом всех внесенных в данную версию изменений. Если заменен ссылочный стандарт, на который дана датированная ссылка, то рекомендуется использовать версию этого стандарта с указанным выше годом утверждения (принятия). Если после утверждения настоящего стандарта в ссылочный стандарт, на который дана датированная ссылка, внесено изменение, затрагивающее положение, на которое дана ссылка, то это положение рекомендуется применять без учета данного изменения. Если ссылочный стандарт отменен без замены, то положение, в котором дана ссылка на него, рекомендуется применять в части, не затрагивающей эту ссылку.
3 Термины, определения, сокращения и обозначения
3.1 В настоящем стандарте применены термины по ГОСТ 33439, а также следующие термины с соответствующими определениями:
3.1.1 термическая обработка: Процесс обработки изделий из металлов и сплавов путем температурного воздействия и последующего охлаждения с определенной скоростью с целью изменения их структуры и свойств в заданном направлении.
3.1.2 закалка: Термическая обработка, заключающаяся в нагреве изделия до температуры выше критической (Ас3 — для доэвтектоидной стали и Ас1 — для заэвтектоидной стали) или до температуры
Издание официальное
1
ГОСТ Р 71257—2024
растворения избыточных фаз, в выдержке при этой температуре и в последующем охлаждении со скоростью, превышающей критическую.
Примечание — Ас1 — температура (точка) фазового превращения, при которой начинается образование аустенита при нагреве; Ас3 — температура (точка) фазового превращения, при которой начинается образование феррита при охлаждении.
3.1.3 нормализация: Термическая обработка — разновидность отжига, при которой изделие нагревают до температуры выше Ас3 для доэвтектоидной стали или Аст для заэфтектоидной стали с последующим охлаждением на спокойном воздухе с целью получения мелкого зерна и равномерного распределения структурных составляющих.
Примечание — Аст — температура, при которой у заэфтектоидных сталей заканчивается растворение цементита в аустените.
3.1.4 выдержка: Часть температурного режима, в течение которой температура остается постоянной.
3.1.5 скорость нагрева: Изменение температуры в процессе нагрева, отнесенное ко времени.
3.1.6 отжиг: Термическая обработка, предусматривающая нагрев изделия до определенной температуры, выдержку и последующее медленное охлаждение с целью получения более равновесной структуры.
3.1.7 отпуск: Термическая обработка, проводимая после закалки или после другой термической обработки, чтобы обеспечить необходимые показатели определенных свойств изделия.
Примечание — При отпуске нагрев осуществляют до температур ниже точки Ас1.
3.1.8 старение: Явление, при котором происходит изменение свойств изделия в процессе вылеживания при комнатной температуре или при нагреве, обусловленное термодинамической неравно-весностью исходного структурного состояния и постепенного приближения структуры к равновесному состоянию.
3.1.9 сталь: Сплав железа с углеродом, содержащий не более 2,14 % углерода.
3.2 В настоящем стандарте применены следующие сокращения и обозначения:
АС — атомная станция;
ГМО — головная металловедческая организация;
КД — конструкторская документация;
МО РФ — Министерство обороны Российской Федерации;
ПТД — производственно-технологическая документация;
РМРС — Российский морской регистр судоходства;
ТО — термическая обработка;
НВ — твердость по шкале Бринелля;
HRC — твердость по шкале Роквелла;
°о 2 — предел текучести;
ов — временное сопротивление (предел прочности);
85 — относительное удлинение после разрыва;
V — относительное сужение после разрыва;
KCU - ударная вязкость, определенная на образце с концентратором вида U.
4 Технические требования
4.1 Необходимость проведения ТО и ее режимы определяют исходя из конкретных условий изготовления и эксплуатации арматуры, которые должны быть установлены КД.
4.2 В соответствии с требованиями настоящего стандарта и КД изготовителям арматуры следует разрабатывать ПТД на ТО применительно к имеющемуся оборудованию. Для заготовок (деталей) арматуры АС ПТД на ТО следует разрабатывать в соответствии с требованиями настоящего стандарта и[1], [2], [3].
2
ГОСТ Р 71257—2024
5 Режимы термической обработки
5.1 Для обеспечения необходимых показателей механических свойств и твердости заготовки деталей должны быть подвергнуты ТО: нормализации или закалке (нормализации) с отпуском.
5.2 Механические свойства сталей, определяемые на продольных образцах, вырезанных из заготовок, в зависимости от толщины (диаметра) после ТО, указанной в таблице 1 (см. также приложение А).
Рекомендуемые режимы ТО заготовок для получения соответствующего предела текучести в зависимости от толщины (диаметра) заготовок приведены в таблице 1.
Режимы ТО стали, для которой необходимо получить предел текучести, не указанный в таблице 1, а также для сталей, не приведенных в настоящем стандарте, устанавливает изготовитель.
Таблица 1 — Режимы ТО и твердость углеродистых и легированных конструкционных сталей
Марка стали | Предел текучести о0 2, МПа | Наиболь-шая(ий) толщина (диаметр) заготовки, мм | то | Твердость, НВ (HRC) | |||
Закалка, нормализация | Отпуск | ||||||
Температура, °C | Среда охлаждения | Температура, °C | Среда охлаждения | ||||
СтЗсп | 195 | 300 | 900—950 | Воздух | — | — | 111—156 |
СтЗпс | 175 | 101—143 | |||||
Ст5 | 245 | 100 | 850—880 | — | — | 143—179 | |
195 | 500 | 111—156 | |||||
20 | Режим I | ||||||
215 | 300 | 900—920 | Воздух | — | — | 123—167 | |
195 | 111—156 | ||||||
175 | 800 | 101—143 | |||||
Режим II | |||||||
215 | 300 | 900—920 | Вода или воздух | 600—680 | Воздух | 123—167 | |
195 | 111—156 | ||||||
175 | 800 | 101—143 | |||||
25 | 245 | 100 | 890—910 | Воздух | — | — | 143—179 |
215 | 300 | 123—167 | |||||
35* | 275 | 100 | 880—900 | — | — | 156—197 | |
245 | 800 | 143—179 | |||||
315 | 100 | 860—880 | Вода или масло | 600—650 | Воздух | 167—207 | |
275 | 300 | 156—197 | |||||
40* | 275 | 870—890 | Воздух | — | — | ||
345 | 100 | 830—850 | Вода от 20 °C до 40 °C | 580—640 | Воздух | 174—217 | |
45 | 785 | 40 | 830—860 | Вода от 20 °C до 40 °C | 350—400 | Воздух | 293—331 |
540 | 50 | 540—560 | 223—262 | ||||
440 | 120 | 560—600 | 197—235 |
3
ГОСТ Р 71257—2024
Продолжение таблицы 1
Марка стали | Предел текучести о0 2, МПа | Наиболь-шая(ий) толщина (диаметр) заготовки, мм | ТО | Твердость, НВ (HRC) | |||
Закалка, нормализация | Отпуск | ||||||
Температура, °C | Среда охлаждения | Температура, °C | Среда охлаждения | ||||
09Г2С | 345 | 10 | 930—940 | Вода | 630—640 | Воздух | 174—217 |
323 | 20 | ||||||
304 | 32 | 167—207 | |||||
284 | 60 | ||||||
275 | 80 | 143—197 | |||||
265 | 160 | ||||||
10ХСНД | 390 | 125 | 930—950 | 650—680 | 197—235 | ||
10Г2 | 215 | 100 | 910—930 | Воздух | — | — | 123—167 |
200 | |||||||
400 | |||||||
800 | |||||||
ЗОХМА | 635 | 80 | 860—880 | Вода или масло | 540—600 | Воздух | 229—286 |
540 | 120 | 620—640 | 223—262 | ||||
395 | 300 | 640—660 | 187—229 | ||||
35ХМ | 1176 | 30 | 840—860 | Масло | 200—220 | (48,4—52,2) | |
785 | 50 | 560—580 | 293—331 | ||||
640 | 80 | 560—600 | 229—286 | ||||
590 | 120 | 600—630 | 235—277 | ||||
490 | 200 | 640—660 | 212—248 | ||||
20ХНЗА | 685 | 50 | 820—840 | 500—580 | Вода или масло | 248—293 | |
640 | 80 | 262—311 | |||||
40ХН2МА | 1470 | 20 | 840—860 | 200—250 | Масло или воздух | (49,3—54,2) | |
785 | 80 | 550—560 | Вода или масло | 293—331 | |||
735 | 100 | 550—620 | 277—321 | ||||
590 | 240 | 570—600 | Масло или воздух | 235—277 | |||
490 | 500 | 580—620 | 212—248 | ||||
40ХФА | 640 | 60 | 880—900 | 660—680 | Воздух | 248—293 | |
540 | 100 | 670—700 | 223—262 | ||||
440 | 300 | 680—700 | 197—235 | ||||
38ХНЗМФА | 1176 | 30 | 840—860 | Масло или через воду в масло | 550—570 | Масло или воздух | (42,5—46,4) |
980 | 100 | 570—580 | (39,6—43,5) | ||||
880 | 150 | 580—590 | (34,8—42,5) | ||||
785 | 240 | 590—600 | (30,9—38,6) | ||||
685 | 350 | 600—620 | (28—33,8) |
4
Окончание таблицы 1
ГОСТ Р 71257—2024
Марка стали | Предел текучести gq 2} МПа | Наиболь-шая(ий) толщина (диаметр) заготовки, мм | ТО | Твердость, НВ (HRC) | |||
Закалка, нормализация | Отпуск | ||||||
Температура, °C | Среда охлаждения | Температура, °C | Среда охлаждения | ||||
18Х2Н4МА | 635 | 200 | 845—875 | Масло | 620—650 | 248—293 | |
38Х2МЮА | 835 | 40 | 935—965 | 620—650 | Вода или масло | (32,8—38,7) | |
590 | 160 | ||||||
15ХМ | 490 | 100 | 910—930 | Вода | 560—580 | Воздух | 197—217 |
255 | 300 | 930—950 | Воздух | 620—640 | 143—163 | ||
12X1 МФ | 255 | 250 | 960—980 | Воздух или масло | 740—760 | 131—170 | |
18ХЗМВ | 440 | 100 | 965—995 | Масло | 680—730 | Воздух | 197—235 |
25X1 МФ | 590 | 200 | 940—960 | 660—680 | 235—272 | ||
685 | 150 | 640—660 | 269—311 | ||||
20ХЗМВФ | 735 | 25 | 1030— 1080 | 660—700 | 277—321 | ||
635 | 400 | 248—293 | |||||
15Х5М | 294 | 200 | 950—970 | Воздух | 750—770 | В печи не выше 400 °C, далее на воздухе | 149—197 |
08ГДНФ | 440 | 900—940 | Вода | 590—630 | Воздух | 159—208 | |
395 | Воздух | 159—192 | |||||
20Х | 345 | 80 | 880—900 | Вода | 500—560 | 174—217 | |
зох | 440 | 60 | 850—870 | Масло | 470—530 | Вода или масло | 197—235 |
395 | 150 | 187—229 | |||||
35Х | 640 | 60 | 840—870 | 500—550 | 248—293 | ||
590 | 80 | 235—277 | |||||
440 | 120 | 197—235 | |||||
40Х | 1274 | 25 | Масло или через воду в масло | 130—200 | Воздух или масло | (46,4—53,1) | |
880 | 30 | 400—420 | (36,7—43,5) | ||||
785 | 500—560 | 293—331 | |||||
685 | 50 | 560—580 | 262—311 | ||||
540 | 80 | 580—600 | 223—262 | ||||
490 | 120 | 600—620 | 212—248 | ||||
440 | 200 | 620—660 | 197—235 | ||||
18ХГ | 735 | 15 | 865—895 | Масло | 200—220 | 277—321 | |
440 | 80 | 650—700 | 197—235 | ||||
20ЮЧ | 235 | 180 | 900—920 | Воздух | — | — | <190 |
* Согласно технологической документации при нормализации заготовок сечением более 200 мм из сталей марок 35 и 40 для снятия напряжений проводят отпуск при температуре от 620 °C до 650 °C.
5
ГОСТ Р 71257—2024
5.3 Если в сопроводительной документации на данную партию проката или поковок из стали марок СтЗ, Ст5, 20, 25, 30, 40 имеется указание о проведенной нормализации, то повторную нормализацию заготовок из этой партии можно не проводить при условии соответствия механических свойств или твердости требованиям КД.
5.4 ТО рекомендуется подвергать заготовки после предварительной механической обработки в наименьших сечениях, без надрезов, резких переходов и острых углов, являющихся местами концентрации напряжений.
5.5 Перепад температуры в рабочем пространстве печи не должен превышать 25 °C.
5.6 При установке термопар в печи, их концы (горячий спай) должны находиться на расстоянии не более 100 мм от поверхности заготовок.
Правильность показаний рабочих термопар периодически проверяют по контрольной платиновой термопаре.
5.7 Рекомендуемая температура печи во время посадки заготовок для ТО в зависимости от толщины (диаметра) заготовки приведена в таблице 2.
Таблица 2 — Рекомендуемая температура печи при посадке заготовок
Марка стали | Наибольшая(ий) толщина (диаметр) заготовки, мм | Наибольшая температура печи при посадке заготовок на закалку,нормализацию, °C | Наибольшая температура печи при посадке заготовок на отпуск, °C |
СтЗсп, Ст5, СтЗпс, 20, 25, 35, 40, 45, 09Г2С, 18ХГ, 10Г2, 20Х, ЗОХ, 35Х, 40Х, ЗОХМА, 35ХМ, 40ХФА, 15ХМ | <100 | 850 | Температура отпуска |
>100 | 650 | 450 | |
38Х2МЮА, 10ХСНД, 08ГДНФ, 12X1 МФ, 18ХЗМВ, 25X1 МФ, 20ХЗМВФ, 15Х5М | <100 | 700 | Температура отпуска |
>100 | 450 | 450 | |
40ХН2МА, 20ХНЗА, 38ХНЗМФА, 18Х2Н4МА | <100 | 700 | 200 |
>100 | 450 |
5.8 Время прогрева садки устанавливают с учетом наибольшей(го) толщины (диаметра) заготовок, веса садки и расположения заготовок на поду печи.
Рекомендуемые нормы выдержки при нагреве: в пламенных печах — 1 мин; в электропечах — от 1,5 мин до 2 мин; в соляных ваннах — 0,5 мин; в свинцовых ваннах — от 0,1 мин до 0,15 мин на 1 мм толщины (диаметра).
Для более точного расчета времени прогрева садки (время нагрева и выравнивания температуры по сечению) в пламенных и электрических печах рекомендуется методика, приведенная в приложении Б. Методика пригодна для расчета при условии, что скорость нагрева не ограничена, а температура посадки заготовок в печь примерно равна температуре проведения операции.
5.9 Нагрев заготовок для закалки (нормализации) проводят с производственной скоростью, если скорость нагрева в ПТД не указана.
5.10 Время выдержки после полного прогрева садки (при нагреве под закалку, нормализацию) устанавливают в ПТД на ТО с учетом массы (садки) из расчета нормы выдержки на 1 мм наибольшей(го) толщины (диаметра) заготовок: для углеродистых сталей 1 мин; для легированных — от 1,5 до 2 мин. Рекомендуемое время выдержки заготовок в печи при температурах отпуска в зависимости от толщины (диаметра) заготовки и массы (садки) заготовок приведено в таблице 3.
6
ГОСТ Р 71257—2024
Таблица 3 — Рекомендуемое время выдержки заготовок в печи при температуре отпуска
Наибольшая(ий) толщина (диаметр) заготовок, мм | Наибольшая масса (садка) заготовок, кг | Выдержка (после прогрева металла садки) при температуре отпуска, ч, для сталей марок | |
СтЗсп, Ст5, СтЗпс, 20, 25, 35, 40, 45, 09Г2С, 18ХГ, 10Г2, 20X, ЗОХ, 35Х, 40Х, 18ХГ, ЗОХМА, 38Х2МЮА, 35ХМ, 40ХФА, 15ХМ | 10ХСНД, 08ГДНФ, 20ХНЗА, 40ХН2МА, 38ХНЗМФА, 15Х5М, 18Х2Н4МА, 12X1 МФ, 20ХЗМВФ, 18ХЗМВ, 25X1 МФ | ||
<100 | 500 | 2,0—2,5 | 2,0—3,0 |
1000 | 2,5—3,0 | 3,0—3,5 | |
1500 | 3,0—3,5 | 3,5—4,0 | |
>100 | 500 | 2,5—3,0 | 3,0—3,5 |
1000 | 3,0—3,5 | 3,5-40 | |
1500 | 3,5—4,0 | 4,0—4,5 |
5.11 При охлаждении заготовок (в процессе закалки) через воду в масло температура воды должна быть в пределах от 30 °C до 40 °C. При охлаждении массивных заготовок в масле начальная температура его, во избежание загорания, не должна превышать 50 °C.
Продолжительность охлаждения изделий больших сечений в охлаждающих средах при закалке приведена в приложении В.
5.12 Время между охлаждением после закалки и началом отпуска для заготовок из стали мартенситного класса марок 15Х5М, 18Х2Н4МА не должно превышать 3 ч.
5.13 Нагрев заготовок для отпуска проводят с производственной скоростью. Для сталей перлитно-мартенситного и мартенситного классов марок 18Х2Н4МА, 38ХНЗМФА и 20ХНЗА скорость нагрева не должна превышать 240 °С/ч; для этого рекомендуется назначать ступенчатый режим нагрева с полным прогревом при температуре от 300 °C до 400 °C.
Указанное ограничение скорости нагрева рекомендуется, чтобы избежать появления в структуре отпущенной стали ориентации сорбита по мартенситу, ведущей к понижению ударной вязкости стали.
5.14 Учитывая индивидуальные особенности термического оборудования изготовителя, допускаются отклонения от рекомендуемых режимов ТО в части длительности выдержек, температуры отпуска и температуры печи во время посадки заготовок для ТО при условии обеспечения механических свойств или твердости металла согласно требованиям КД.
Другие отклонения должны быть согласованы для изделий:
- АС и РМРС —с ГМО;
- МО РФ — с представителем заказчика.
6 Общие технологические указания по термической обработке
6.1 При нагреве в пламенных печах не допускается прямое попадание пламени непосредственно от форсунки на заготовки.
6.2 Основными охлаждающими средами являются спокойный воздух при температуре цеха, вода с температурой от 20 °C до 60 °C и минеральные масла с температурой от 20 °C до 70 °C.
6.3 Время выдержки заготовок (деталей) исчисляют с момента прогрева садки и выхода печи на заданную температуру.
6.4 При необходимости, проводят повторную ТО. Количество повторных ТО должно быть не более двух. Дополнительный отпуск не считается повторной ТО, а их количество не ограничивается.
7 Контроль термической обработки
7.1 При ТО заготовок (деталей) следует контролировать соблюдение ПТД и КД деталей, а изделий АС также в соответствии с [1]:
- методов и видов ТО;
- применяемого термического оборудования;
7
ГОСТ Р 71257—2024
- последовательности и порядка выполнения ТО и ее отдельных этапов (в том числе предварительных, промежуточных и окончательных отпусков);
- режимов ТО (температуры печи при загрузке, скорости нагрева, температуры и продолжительности выдержек, условий, среды или скорости охлаждения);
- методов и порядка контроля температурных режимов (расположения термопар или других устройств для измерения температуры, их количество и т. п.);
- условий, исключающих пластическую деформацию под действием собственной массы;
- других параметров, контроль которых предусмотрен ПТД.
7.2 Печные агрегаты, в которых заготовки (детали) нагревают под ТО, должны обеспечивать распределение температуры в рабочей части печи в пределах допуска, указанного в режиме ТО.
Все печные агрегаты должны проходить проверку на распределение температуры по поду и высоте печи согласно установленному(ым) графику (инструкциям).
7.3 После ремонта печного агрегата, а также при замене нагревателей следует проводить регулирование печи с контрольной проверкой. При проверке устанавливают рабочую зону печи, в пределах которой можно располагать заготовки (детали), при проведении ТО.
Перед началом каждой смены необходимо проверять состояние пирометрической аппаратуры, регулирующей температуру печи.
7.4 Для контроля ТО деталей МО РФ и АС следует использовать термоэлектрические преобразователи (термопары) с устройствами для автоматической записи параметров режима.
7.5 Объем контроля качества изделий, прошедших ТО, и сдаточные характеристики устанавливают в КД в соответствии с ГОСТ Р 71255 и с учетом требований [1].
7.6 При отсутствии в КД требований по контролю твердости или механических свойств термообработанные детали или заготовки проходят контроль твердости по Гр. II ГОСТ Р 71255. Твердость должна соответствовать нормам, указанным в таблице 1.
7.7 При проведении ТО следует соблюдать правила техники безопасности в соответствии с ГОСТ 12.3.004.
8 Оформление документации
8.1 Необходимость проведения ТО деталей (заготовок) должна быть указана в КД со ссылкой на настоящий стандарт.
8.2 Фактический режим ТО деталей (заготовок) фиксируют в журнале термического цеха с указанием обозначений деталей и изделия.
8.3 После выполнения ТО должны быть зафиксированы номер садки и номер печи (для печной ТО), а также дата проведения ТО.
8
ГОСТ Р 71257—2024
Приложение А (обязательное)
Механические свойства углеродистых и легированных конструкционных сталей в зависимости от толщины (диаметра) заготовки
Таблица А.1 — Механические свойства углеродистых и легированных конструкционных сталей в зависимости от толщины (диаметра) заготовки
Марка стали или сплава | Наиболь-шая(ий) толщина (диаметр) заготовки, мм | Механические свойства, не менее | Твердость | ||||
Временное сопротивление ов, МПа | Предел текучести а0 2, МПа ’ | Относительное удлинение з5. % | Относительное сужение V. % | Ударная вязкость, KCU, кДж/м2 | НВ (HRC) | ||
СтЗсп | 300 | 390 | 195 | 23 | 50 | 540 | 111—156 |
СтЗпс | 355 | 175 | 24 | 590 | 101—143 | ||
Ст5 | 100 | 470 | 245 | 22 | 48 | 490 | 143—179 |
500 | 390 | 195 | 20 | 45 | 111—156 | ||
20 | 300 | 430 | 215 | 48 | 123—167 | ||
390 | 195 | 23 | 50 | 540 | 111—143 | ||
800 | 355 | 175 | 20 | 40 | 490 | 143—179 | |
25 | 100 | 470 | 245 | 22 | 48 | ||
300 | 390 | 215 | 20 | 123—167 | |||
35 | 100 | 530 | 275 | 40 | 441 | 156—197 | |
800 | 470 | 245 | 15 | 30 | 343 | 143—179 | |
100 | 570 | 315 | 17 | 38 | 392 | 167—207 | |
300 | 530 | 275 | 343 | 156—197 | |||
40 | 275 | ||||||
100 | 590 | 345 | 18 | 45 | 588 | 174—217 | |
45 | 40 | 930 | 785 | 12 | 40 | 490 | 293—331 |
50 | 785 | 540 | 10 | 223—262 | |||
120 | 676 | 440 | 17 | 197—235 | |||
10ХСНД | 125 | 615 | 395 | 15 | 539 | ||
09Г2С | 10 | 490 | 345 | 21 | — | 588 | 174—217 |
20 | 470 | 323 | |||||
32 | 461 | 304 | 167—207 | ||||
60 | 451 | 284 | |||||
80 | 441 | 275 | 143—197 | ||||
09Г2С | 160 | 430 | 265 | 21 | — | 588 | 143—197 |
10Г2 | 100 | 215 | 22 | 53 | 539 | 123—167 | |
200 | 20 | 48 | 441 | ||||
400 | 18 | 40 | 392 | ||||
800 | 16 | 35 | 343 |
9
ГОСТ Р 71257—2024
Продолжение таблицы А. 1
Марка стали или сплава | Наиболь-шая(ий) толщина (диаметр) заготовки, мм | Механические свойства, не менее | Твердость | ||||
Временное сопротивление ов, МПа | Предел текучести о0 2, МПа | Относительное удлинение 55. % | Относительное сужение V. % | Ударная вязкость, KCU, кДж/м2 | НВ (HRC) | ||
08ГДНФ | 200 | 539 | 440 | 20 | 45 | 392 | 159—208 159—192 |
490 | 395 | ||||||
20Х | 80 | 590 | 345 | 16 | 588 | 174—217 197—235 | |
ЗОХ | 60 | 635 | 440 | ||||
150 | 615 | 395 | 15 | 40 | 539 | 187—229 | |
35Х | 60 | 785 | 640 | 13 | 45 | 588 | 248—293 |
80 | 685 | 590 | 14 | 235—277 | |||
120 | 635 | 440 | 40 | 539 | 197—235 | ||
40Х | 25 | 1470 | 1275 | 7 | 25 | -294 | (46,4—51,3) |
30 | 1078 | 880 | ~7 | ~35 | -392 | (36,7—43,5) | |
930 | 785 | 12 | 40 | 588 | 293—331 | ||
50 | 835 | 675 | 13 | 42 | 262—311 | ||
80 | 685 | 540 | 15 | 45 | 223—262 | ||
120 | 655 | 490 | 13 | 40 | 490 | 212—248 | |
200 | 635 | 440 | 14 | 539 | 197—235 | ||
18ХГ | 15 | 880 | 735 | 10 | — | 277—321 | |
80 | 635 | 440 | 16 | 45 | 588 | 197—235 | |
ЗОХМА | 880 | 640—785 | 13 | 42 | 229—286 | ||
120 | 813 | 540 | 16 | 40 | 392 | 223—262 187—229 | |
300 | 590 | 395 | 15 | ||||
35ХМ | 30 | 1372 | 1176—1274 | 10 | 45 | 490 | (48,4—52,2) |
50 | 980 | 785—880 | 11 | 686 | 293—331 | ||
80 | 785 | 640—785 | 13 | 42 | 588 | 229—286 | |
120 | 590 | 15 | 50 | 686 | 235—277 | ||
200 | 685 | 490 | 45 | 588 | 212—248 | ||
20ХНЗА | 50 | 835 | 675—785 | 12 | 55 | 784 | 248—294 |
80 | 785 | 640 | 10 | 42 | 262—311 | ||
40ХФА | 60 | 785 | 640 | 15 | 588 | 248—293 | |
100 | 685 | 540 | 45 | 223—262 | |||
300 | 635 | 440 | 14 | 40 | 539 | 197—235 |
10
Окончание таблицы А. 1
ГОСТ Р 71257—2024
Марка стали или сплава | Наиболь-шая(ий) толщина (диаметр) заготовки, мм | Механические свойства, не менее | Твердость | ||||
Временное сопротивление ов, МПа | Предел текучести о0 2, МПа ’ | Относительное удлинение з5. % | Относительное сужение V, % | Ударная вязкость, KCU, кДж/м2 | НВ (HRC) | ||
40ХН2МА | 20 | 1617 | 1470 | 9 | 45 | 490 | (44,0—54,2) |
80 | 930 | 785—930 | 12 | 40 | 588 | 293—331 | |
100 | 880 | 735—835 | 13 | 277—321 | |||
240 | 735 | 590 | 490 | 235—277 | |||
500 | 655 | 490 | 12 | 35 | 212—248 | ||
38ХНЗМФА | 30 | 1372 | 1176—1274 | 7 | 392 | (42,5—46,4) | |
100 | 1176 | 980—1078 | 490 | (39,6—43,5) | |||
150 | 1078 | 880—980 | 10 | (34,8—42,5) | |||
240 | 980 | 785—880 | 38 | (30,9—38,7) | |||
350 | 882 | 675—785 | 40 | 588 | (28,0—33,8) | ||
18Х2Н4МА | 200 | 835 | 640—735 | 13 | 50 | 882 | 248—293 |
38Х2МЮА | 40 | 1078 | 835—880 | 10 | 35 | 686 | (32,8—38,7) |
160 | 735 | 590 | 13 | 40 | 490 | 235—277 | |
15ХМ | 100 | 615 | 490 | 18 | 50 | 686 | 197—217 |
300 | 441 | 255 | 22 | 40 | 588 | 143—163 | |
12Х1МФ | 250 | 470 | 20 | 50 | 131—170 | ||
18ХЗМВ | 100 | 590 | 440 | 15 | 45 | 197—235 | |
25X1 МФ | 200 | 735 | 590—675 | 16 | 50 | 235—272 | |
150 | 813 | 675—785 | 269—311 | ||||
20ХЗМВФ | 25 | 880 | 735—835 | 12 | 40 | 277—321 | |
400 | 735 | 640—735 | 13 | 490 | 248—293 | ||
15Х5М | 200 | 490 | 294 | 18 | 588 | 149—197 | |
20ЮЧ | 180 | 412 | 235 | 23 | — | При температуре минус 40 °C — 490°С | <190 |
11
ГОСТ Р 71257—2024
Приложение Б (рекомендуемое)
Методика расчета времени нагрева садки
Б.1 Для заготовок с отношением
^3. (Б.1)
где / — длина заготовки;
d — диаметр заготовки,
расчет продолжительности периода нагрева и выравнивания температуры по сечению следует вести на максимальное поперечное сечение изделия по следующей методике:
а) при сплошных круглых сечениях — на максимальный диаметр;
б) при сплошных прямоугольных сечениях — на меньшую сторону прямоугольного максимального сечения;
в) при полых, круглых и прямоугольных сечениях:
1) для изделий с осевым отверстием не более 50 мм (если наружный диаметр или минимальная сторона прямоугольника более 500 мм) на сплошное сечение, без учета значения диаметра осевого отверстия, 2) для заготовок с осевым отверстием не более 50 мм (при наружных размерах сечения менее 500 мм), а также для изделий с осевым отверстием диаметром свыше 50 мм, но не более 500 мм (при любом значении наружного диаметра или минимальной стороны прямоугольника) сечение приводят к «сплошному», для этого сумму толщин стенок считают за «сплошное» круглое или прямоугольное сечение,
3) для заготовок с осевым отверстием свыше 500 мм (при любом значении наружного диаметра или стороны прямоугольника) максимальную толщину стенки следует умножать на коэффициент 1,7; полученную величину считают приведенным диаметром «сплошного» сечения.
Нормы продолжительности нагрева, выраженной в минутах, на 1 мм поперечного сечения (с подразделением по области температур) приведены в таблице Б.1.
Таблица Б.1 — Нормы продолжительности нагрева садки
Наименование операции | Температура, °C | Время выдержки, мин |
Нормализация (закалка) | 850—920 | 1,5 |
950—980 | 1,3 | |
1000—1100 | 1,0 | |
Отпуск | 150—400 | От 3 до 4 (включая выдержку, т. е. для общей продолжительности операции) |
400—600 | 2,5—3,0 | |
600—740 | 2—3 |
Примечание — При нагреве изделий в электрических печах следует умножать каждую норму на коэффициент 1,2.
Если садка печи состоит из нескольких заготовок с различным положением на поду (или в рабочем пространстве вертикальной печи), то полученный при расчете результат нужно умножить на коэффициент равномерности нагрева в соответствии с приведенными в таблице Б.2.
Таблица Б.2 — Коэффициенты равномерности нагрева
Схема расположения заготовок в печи | А. | А | л | А | ж | |||||||
Коэффициент равномерности нагрева | 1 | 1 | 1 | 1,8 | 1,4 | 1,7 | 2,2 | 4—8 | ||||
Примечание — Коэффициент равномерности нагрева выбирают исходя из фактического расположения заготовок в печи. |
12
ГОСТ Р 71257—2024
Б.2 Для заготовок с отношением
4 s3' (Б.2)
где / — длина заготовки;
d — диаметр заготовки,
расчет продолжительности периода нагрева и выравнивания температуры по сечению тн проводят по формуле
t„ = kW, (Б.З)
где к — коэффициент, характеризующий суммарный физический фактор нагрева, мин/см, выбираемый в пределах от 45 до 50;
И/ — геометрический показатель тела, рассчитываемый по формуле
»4' (Б.4)
где V — объем заготовки, см3;
F — поверхность заготовки, см2.
Значение И/определяют по формулам, приведенным в таблице Б.З.
Таблица Б.З — Формулы вычисления геометрического показателя тела И/
Форма изделия | Геометрический показатель тела И/ | Обозначение |
Сплошной цилиндр | DI 4I + 2D | D — наружный диаметр, см; d— внутренний диаметр, см; В — ребро куба или толщина плиты, см; а — ширина пластины, см; / — длина, см |
Полый цилиндр | 4-/ + 2-(D-d) | |
Куб | В 6 | |
Прямоугольная плита | Bal 2-(B-/ + Ba + a-f) |
Полученные результаты актуальны при нагреве заготовки со всех сторон, в противном случае применяют коэффициенты равномерности, приведенные в таблице Б.2.
13
ГОСТ Р 71257—2024
Приложение В (рекомендуемое)
Продолжительность охлаждения изделий больших сечений в охлаждающих средах при закалке
Таблица В.1 — Продолжительность охлаждения изделий больших сечений в охлаждающих средах при закалке
Охлаждающая среда | Продолжительность охлаждения, мин | ||||
Максимальное сечение заготовки, мм | |||||
<200 | 200—400 | 400—600 | 600—800 | 800—1000 | |
Масло | 30—70 | 70—120 | 120—180 | 180—240 | 240—300 |
Через воду в масло: в воде в масле | 1—3 20—50 | 3—4 50—90 | 4—6 90—140 | 6—8 140—200 | 8—10 200—260 |
14
ГОСТ Р 71257—2024
Библиография
[1] Федеральные нормы и правила в области использования атомной энергии НП-089-15
[2] Правила и нормы в атомной энергетике НП-105-18
[3] Федеральные нормы и правила в области использования атомной энергии НП-071-18
Правила устройства и безопасной эксплуатации оборудования и трубопроводов атомных энергетических установок
Правила контроля металла оборудования и трубопроводов атомных энергетических установок при изготовлении и монтаже
Правила оценки соответствия продукции, для которой устанавливаются требования, связанные с обеспечением безопасности в области использования атомной энергии, а также процессов ее проектирования (включая изыскания), производства, строительства, монтажа, наладки, эксплуатации, хранения, перевозки, реализации, утилизации и захоронения
15
ГОСТ Р 71257—2024
УДК 001.4:621.643.4:006.354
ОКС 23.060
Ключевые слова: термическая обработка, заготовка, деталь, режим термической обработки, закалка, среда охлаждения, время выдержки
Редактор Л.С. Зимилова Технический редактор И.Е. Черепкова Корректор И.А. Королева Компьютерная верстка И.А. Налейкиной
Сдано в набор 02.05.2024. Подписано в печать 14.05.2024. Формат 60x847s. Гарнитура Ариал. Усл. печ. л. 2,32. Уч.-изд. л. 1,90.
Подготовлено на основе электронной версии, предоставленной разработчиком стандарта
Создано в единичном исполнении в ФГБУ «Институт стандартизации» , 117418 Москва, Нахимовский пр-т, д. 31, к. 2.