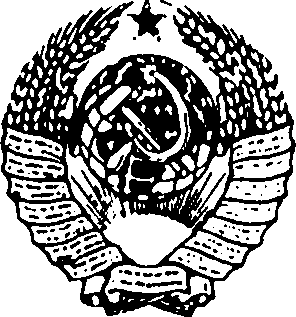
ГОСУДАРСТВЕННЫЙ СТАНДАРТ СОЮЗА ССР
ПРУТКИ и полосы ИЗ ИНСТРУМЕНТАЛЬНОЙ ЛЕГИРОВАННОЙ СТАЛИ
ТЕХНИЧЕСКИЕ УСЛОВИЯ
ГОСТ 5950-73
(СТ СЭВ 3895-82)
Издание официальное
КОМИТЕТ СТАНДАРТИЗАЦИИ И МЕТРОЛОГИИ СССР
Москва
Группа В32
ГОСУДАРСТВЕННЫЙ СТАНДАРТ СОЮЗА ССР
ГОСТ
5950—73
(СТ СЭВ 3895-82)
ПРУТКИ И ПОЛОСЫ ИЗ ИНСТРУМЕНТАЛЬНОЙ ЛЕГИРОВАННОЙ СТАЛИ
Технические условия
Bars and strips of tool alloyed steel. Specifications
ОКП 09 6105
Срок действия с 01.01.75 до 01.07.96
Настоящий стандарт распространяется на горячекатаные, кованые, калиброванные прутки и полосы, сталь со специальной отделкой поверхности (далее — металлопродукция) из инструментальной низколегированной^реднелегированной и высоколегированной стали.
В части норм химического состава настоящий стандарт распространяется на сталь марок ЗХ2МНФ, 4ХМНФС, 9ХФМ, а также слитки, блюмсы, слябы, заготовки, поковки, лист, ленту, трубы и другую металлопродукцию.
(Измененная редакция, Изм. № 5).
1. МАРКИ
1.1. Металлопродукцию по назначению подразделяют на группы:
I группа — для изготовления инструмента, используемого в основном для обработки металлов и других материалов в холодном состоянии;
II группа — для изготовления инструмента, используемого в основном для обработки металлов давлением при температуре выше 300° С.
Издание официальное
© Издательство стандартов, 1973 © Издательство стандартов, 1991
Переиздание с Изменениями
Настоящий стандарт нс может быть полностью или частично воспроизведен, тиражирован и распространен без разрешения Госстандарта СССР
С. 2 ГОСТ 5950-73
По способу дальнейшей обработки горячекатаную и кованую металлопродукцию I и II групп подразделяют на подгруппы: а — для горячей обработки давлением;
б — для холодной механической обработки (обточки, строжки, фрезерования и т. д.).
По состоянию поверхности металлопродукцию подгруппы б подразделяют на:
О “ обычного качества;
П — повышенного качества.
(Измененная редакция, Изм. № 2).
1.2. Марки стали по легированию подразделяют на: низколегированные инструментальные — 8ХФ, 9ХФ, 9ХФМ,
11ХФ, 13Х, В2Ф, 9X1, X, 12X1, 9ХС, ХГС, 9ХВГ, ХВГ.ХВСГФ, 9Г2Ф, 4ХС, 6ХС, 6ХВГ;
среднелегированные инструментальные — ХВ4Ф, 9Х5ВФ, 8Х6НФТ, Х6ВФ, 7ХГ2ВМФ, 6Х6ВЗМФС, 6Х4М2ФС, 11Х4В2МФЗС2, 8Х4В2МФС2, 7X3, 8X3, 5ХНМ, 5ХНВ, 5ХНВС, 4ХМФС, 4Х5В2ФС, 4Х5МФС, 4Х5МФ1С, 4ХЗВМФ, 4Х4ВМФС, ЗХЗМЗФ, 4Х2В5МФ, 5ХЗВЗМФС, 5Х2МНФ, ЗХ2МНФ, 4ХМНФС, 5ХВ2СФ, 6ХВ2С, 6ХЗМФС;
высоколегированные инструментальные — Х12, Х12ВМФ, Х12МФ, Х12Ф1, 05Х12Н6Д2МФСГТ.
Марки и химический состав стали по плавочному анализу должны соответствовать указанным в табл. 1.
(Измененная редакция, Изм. № 1, 2, 5).
1.3. Содержание серы и фосфора в стали не должно превышать 0,030 % (каждого элемента).
В стали, полученной методом электрошлакового переплава, содержание серы не должно превышать 0,015 %.
Содержание остаточного никеля в сталях всех марок, не легированных никелем, допускается до 0,35 %, в стали марки 4Х4ВМФС — до 0,60 %. Содержание остаточной меди в стали не должно превышать 0^30 %.
1.4. Допускается изготовление вольфрамосодержащих сталей с остаточным молибденом до 0,30 % (при содержании вольфрама в стали до 3,0 %) и до 0,50 % (при содержании вольфрама в стали свыше 3,0 %) с соблюдением всех остальных требований настоящего стандарта.
1.5. В стали, не легированной вольфрамом, ванадием, молибденом и титаном, допускается содержание вольфрама и молибдена до 0,20 % каждого (за исключением сталей марок 5ХНМ и 5Х2МНФ) ванадия — до 0,15 % и титана до 0,03 %.
(Измененная редакция, Изм. № 2, 5).
1.6. Для сталей марок 5ХНМ и 5Х2МНФ допускается частичная замена молибдена вольфрамом из расчета: одна массовая доля молибдена эквивалентна двум массовым долям вольфрама.
Таблица 1
Mapva | Массовая доля элемента, | % | ||||||
стали | Углерод | | Кремний | Марганец | | Хром | | Вольфрам | Ванадий | Молибден | Никель |
Группа I
8ХФ | 0.70-0,80 | 0.10-0.40 | 0,15-0,45 | 0,40-0,70 | — | 0,15-0,30 | * | |
9ХФ | 0,80-0,90 | 0.15-0.35 | 0.30-0,60 | 0,40-0.70 | 0,15-0,30 | — | — | |
9ХФМ | 0,80-0,90 | 0.15-0,35 | 0.30-0,60 | 0.40-0,70 | — | 0,15-0,30 | ОД 5-0,25 | — |
11ХФ(11Х) | 1,05-1,15 | 0,15-0,35 | 0.40-0.70 | 0,40-0,70 | 0,15-0,30 | — | — | |
13Х | 1.25-1.40 | 0.10-0,40 | 0,15-0,45 | 0,40-0,70 | — | — | — | — |
ХВ4Ф (XBS) | 1,25-1.45 | 0.15-0.35 | 0,15-0,40 | 0.40-0,70 | 3,50—4,30 | 0,15-0,30 | — | — |
В2Ф | 1,05-1,22 | 0.10-0.40 | 0,15-0,45 | 0.20-0,40 | 1,60-2,00 | 0,15-0,30 | — | — |
9X1 (9Х) | 0.80-0,95 | 0.25-0.4S | 0,15-0,40 | 1,40-1,70 | — | — | — | * |
X | 0.95-1.10 | 0.10-0,40 | 0,15—0,45 | 1,30-1,65 | — | — | — | |
12X1 (120Х. | ||||||||
ЭП430) | 1.15-1,25 | 0,15-0,35 | 0,30-0.60 | 1.30-1.65 | — | — | — | — |
9ХС | 0.85-0.95 | 1,20—1,60 | 0,30-0,60 | 0,95-1,25 | - | — | - | — |
ХГС | 0,95-1.05 | 0,40-0,70 | 0,85-1,25 | 1,30-1,65 | - | - | - | — |
9ХВГ | 0,85-0,95 | 0.15-0.35 | 0,90-1.20 | 0,50-0,80 | 0,50-0,80 | — | — | — |
ХВГ | 0.90-1,05 | 0,10-0,40 | 0,80-1,10 | 0.90-1,20 | 1,20-1,60 | — | - | — |
ХВСГФ | 0,95-1.05 | 0,65-1,00 | 0,60-0.90 | 0,60-1,10 | 0,50-0,80 | 0,05-0.15 | — | — |
9X5 ВФ 8Х6НФТ | 0,85-1,00 | 0,15-0,40 | 0,15-0,40 | 4,50-5,50 | 0,80-1,20 | 0,15-0,30 | — | — |
(85Х6НФТ) | 0,80-0,90 | 0.15-0.35 | 0,15-0,40 | 5,00-6,00 | 0,30-0,50 | 0,90-1,30 Титан 0,05-0,Ц | ||
9Г2Ф | 0,85-0.95 | 0,10-0.40 | 1,70-2.20 | — | - | 0,10-0.30 | - | — |
Х6ВФ | 1.05-1.15 | 0,15-0,35 | 0,15-0.40 | 5,50-6,50 | 1.10-1.50 | 0,50-0,80 | — | — |
Х12 | 2,00-2.20 | 0.10-0.40 | 0,15-0,45 | 11,50-13,00 | — | — | — | — |
Х12ВМФ | 2,00-2,20 | 0,10-0,40 | 0,15-0,45 | 11,00-12,50 | 0,50-0,80 | 0,15-0,30 | 0,60-0,90 | — |
Х12МФ | 1.45-1.65 | 0.10-0.40 | 0.15-0.45 | 11.00-12,50 | 0,15-0.30 | 0,40-0,60 |
ГОСТ 5950—73 С. 3
Продолжение пбл. 1
Марк* стали | Массовая доля элемента, % | |||||||
Углерод | Кремний | Марганец | Хром | Вольфрам | Ванадии | Молибден | Никель | |
Х12Ф1 | 1,25-1.45 | 0.15-0,35 | 0,15-0.40 | 11,00-1240 | 0,70-0,90 | |||
7ХГ2ВМФ 6Х6ВЗМФС (55Х6ВЗСМФ, | 0,68-0.76 | 0.20-0.40 | 1.80-2.30 | 140-1,80 | 0,55-0.90 | 0,10-0,25 | 0.50-0.80 | |
ЭП569) 6Х4М2ФС | 0,50-0,60 | 0,60-0,90 | 0,15-0,40 | 5,50-6,50 | 2,50-3,20 | 040-0.80 | 0.60-0.90 | — |
(ДИ55) 11Х4В2МФЗС2 | 0,57-0,65 | 0,70-1.00 | 0.15-0,40 | 3,80—4,40 | — | 0,40-0,60 | 2,00-2,40 | не более |
(ДИ37) 8Х4В2МФС2 | 1,05-1,15 | 1,40-1,80 | 0,20-0,50 | 340-4,20 | 2,00-2,70 | 230-2.80 | 0.30-040 | 0,40 |
(ЭП761) | 0,80-0,90 | 1.70-2.00 | 0.20-0.50 | 4,55—5,10 | 1,80-2,30 | 1,10-1,40 | 0,80-1,10 | — |
С. 4 ГОСТ 5960—73
Группа II
7X3 | 0,65-0,75 | 0,15-0,35 | 0,15-0,40 | 3,20-3,80 | Я» | * | ||
8X3 | 0.75-0.85 | 0,15-0.35 | 0.15-0.40 | 3,20-3,80 | — | — | — | — |
5ХНМ | 0.50-0,60 | 0,10-0.40 | 0.50-0.80 | 0.50-0.80 | — | — | 0.15-0,30 | 1,40-1,80 |
5ХНВ | 0.50-0,60 | 0,15-0,35 | 040-0.80 | 040-0,80 | 0.40-0.70 | — | — | 1,40-1,80 |
5ХНВС | 0.50-0,60 | 0,60-0,90 | 0,30-0,60 | 1,30-1,60 | 0,40-0,70 | * | — | 0,80-1.20 |
4ХМФС | ||||||||
(40ХСМФ) | 0,37-0.45 | 0,50-0,80 | 0.50-0.80 | 140-1,80 | — | 0,30-0,50 | 0,90-1.20 | — |
4Х5В2ФС | ||||||||
(ЭИ958) | 0,35-0,45 | 0.80-1,20 | 0,15-0,40 | 440-5.50 | 1,60-2.20 | 0,60-0,90 | - | — |
4Х5МФС | 0,32-0,40 | 0.90-1,20 | 0,20-040 | 440-540 | * | 0.30-0,50 | 1.20-140 | — |
4Х5МФ1С | ||||||||
(ЭП572) | 0,37-0,44 | 030-1,20 | 0,20-0,50 | 4,50-540 | — | 0.80-1,10 | 1.20-1.50 | — |
4ХЗВМФ | ||||||||
(ЭИ-2) | 0.40-0,48 | 0,60-0,90 | 0,30-0,60 | 2.80-340 | 0,60-1,00 | 0,60-0.90 | 0.40-0.60 | — |
4Х4ВМФС | ||||||||
(ДИ22) | 0,37-0.44 | 0,60-1,00 | 0,20-0,50 | 3,20-4,00 | 0,80-1,20 | 0,60-0,90 | 1.20-140 | — |
Продолжение табл 1
Марка стали | Массовая доля элемента, % | |||||||
Углерод | Кремний | Марганец | Хром | Вольфрам | Ванадий | Молибден | Никел: | |
ЗХЗМЗФ | 3,27-0,34 | 0,10-0,40 | 0.20-0,50 | 2,80-3,50 | 0.40-0,60 | 2.50-3.00 | ||
4Х2В5МФ (ЭИ959) | 0,30-0,40 | 0,15-0,35 | 0,15-0,40 | 2,20-3,00 | 4.50-530 | 0,60-0,90 | 0,60-0.90 | |
5ХЗВЗМФС (ДИ23) | 0.45-0.52 | 0,50-0,80 | 0,20-0,50 | 2,50-3,20 | 3,00-3,60 | 130-1.80 | 0.80-1,10 | Ниобий |
5Х2МНФ | 0,46-0,53 | 0,10-0,40 | 0,40-0.70 | 1.50-2.00 | 0,30-0,50 | 0,80-1.10 | 0,05-0,15 1,20-1,60 | |
ЗХ2МНФ | ),27-0,33 | 0,15-0.40 | 0,30-0.60 | 2.00-230 | 0.25-0,40 | 0,40-0.60 | 1,20-1,60 | |
4ХМНФС | ).35-0,42 | 0,70-1.00 | 0,15-0.40 | 1,25-135 | 0.35-030 | 0,65-0.85 | 1,20-1,60 | |
4ХС | 1,35-0,45 | 1,20-1,60 | 0,15-0,40 | 1,30-1,60 | * | |||
6ХС | 1.60-0,70 | 0,60-1,00 | 0,15-0,40 | 1,00-1.30 | ||||
5ХВ2СФ | 0.4S-0.55 | 0,80-1.10 | 0.15-0,45 | 0,90-1.20 | 1.80-2.30 | 0,15-0,30 | ||
6ХВ2С | 1.55-0.65 | 0,50-0,80 | 0,15-0,40 | 1,00-1,30 | 2.20-2,70 | |||
6ХВГ | 0,55-0,70 | 0.15-0,35 | 0,90-1,20 | 0,50-0,80 | 030-0,80 | |||
6ХЗМФС (ЭП788) | 0.55-0.62 | 0,35-0,65 | 0,20-0,60 | 2,60-3,30 | 0,30-0.60 | 0.20-030 | ||
05Х12Н6Ла{ФСГТ ЩИ80) | 0,01-0.08 | 0,60-1,20 | 0,20-1,20 | 11,50-1330 | — | 0.20-0.50 | 0.20-0.40 | 5,50-6,50 |
Примечания:
1. В обозначении марок первые цифры означают массовую долю углерода в десятых долях процента. Они могут не указы* ваться, если массовая доля углерода близка к единице или больше единицы. Буквы означают: Г - марганец, С - кремний, X -хром, В - вольфрам, Ф - ванадий, Н - никель, М - молибден. Цифры, стоящие после букв, означают среднюю массовую долю соответствующего легирующего элемента в целых единицах. Отсутствие цифры означает, что массовая доля этого легирующего элемента равна, примерно. 1 %. В отдельных случаях массовая доля легирующих элементов не указывается, если она не превы* шаег 1.8 %.
2. По согласованию изготовителя с потребителем сталь изготовляют с суженными пределами массовой доли отдельных эле* ментов.
3. Сталь марки Х12ВМФ по требованию потребителя может изготовляться без вольфрама, а сталь марки 6ХЗМФС - без молибдена.
4. В сталь марки 4ХМНФС вводят по расчету 0,05 % циркония и 0,003 % бора, в сталь марки 05Х12Н6Д2МФСГТ вводят по расчету магний и'кальиий по 0.03 % каждого элемента и цирконий 0,015 % и химическим анализом не определяют.
В стали марки 05Х12Н6Д2МФСГТ массовая доля меди составляет 1,40-2,20% и титана 0,40-0,80%.
По согласованию изготовителя с потребителем стали марок Х12,Х12ВМФ, Х12МФ, Х12Ф1 могут изготовляться с массовой долей марганца 0.15-0,60%.
5. Примерное назначение стали указано в справочном приложении 6.
(Измененная редакция, Из.м. N* 2, 3.4,5).
ГОСТ 5950-73 С. 5
С. 6 ГОСТ 5950-73
Минимальная массовая доля молибдена в стали марки 5ХНМ должна быть 0,10%. Сумма молибдена и вольфрама в пересчете на молибден не должна быть менее 0,15 % и более 0,30 %. Минимальная массовая доля молибдена в стали марки 5Х2МНФ должна быть 0,40 %. Сумма молибдена и вольфрама в пересчете на молибден не должна быть менее 0,80 % и более 1,20 %. При массовой доле вольфрама более 0,20 % сталь должна маркироваться 5Х2ВМНФ.
(Измененная редакция, Изм. № 3).
1.7. По требованию потребителя стали марок 8ХФ, 9ХФ, В2Ф должны изготовляться с содержанием серы и фосфора, не превышающими 0,020 % (каждого элемента), а никеля — 0,20%.
1.8. По требованию потребителя стали марок 8ХФ, 9ХФ и 11ХФ изготовляются без ванадия; в этом случае они должны обозначаться соответственно: 7Х, 8Х, 9Х и ИХ.
1.7.1.8. (Измененная редакция, Изм. № 3).
1.9. Для стали марки 9X1 по требованию потребителя содержание хрома может быть повышено до 1,9 %. Содержание углерода при этом должно быть 0,78—0,92 %.
1.10. В готовой продукции допускаются отклонения по
химическому составу, указанные в табл. 2. Таблица 2
Элемент | Массовая доля, % | Допускаемое отклонение, % |
Углерод | До 0,60 Св. 0,60 | ±0,01 ±0,02 |
Кремний | До 1,00 Св. 1,00 | ±0,02 ±0,05 |
Марганец | До 1,00 Св. 1,00 | ±0,02 ±0,05 |
Хром | До 1,00 Св. 1,00 до 4,00 Св. 4,00 | ±0,02 ±0,05 ±0,10 |
Вольфрам | До 2,50 Св. 2,50 | ±0,05 ±0,10 |
Молибден | До 1,00 Св. 1,00 | ±0,02 ±0,05 |
Никель Ниобий | По табл. 1 | ±0,05 ±0,01 |
Ванадий | До 0,60 Св. 0,60 | ±0,02 ±0,05 |
(Измененная редакция, Изм. № 2).
1.11. По требованию потребителя стали могут изготовляться методом электрошлакового переплава.
(Измененная редакция, Изм. № 3).
2. СОРТАМЕНТ
2.1. Сталь изготовляют в виде прутков, заготовок квадратного сечения и полос.
2.2. По форме, размерам и предельным отклонениям сталь должна соответствовать требованиям:
кованая круглого, и квадратного сечений — ГОСТ 1133—71; горячекатаная круглого сечения — ГОСТ 2590—88; горячекатаная квадратного сечения — ГОСТ 2591—88; полосовая — ГОСТ 4405—75;
калиброванная - ГОСТ 7417-75; ГОСТ 8559-75 и ГОСТ 8560-78;
сталь со специальной отделкой поверхности — ГОСТ 14955-77.
Примеры условных обозначений
Сталь горячекатаная круглая обычной точности прокатки — В, диаметром 80 мм по ГОСТ 2590—88 марки 9ХС подгруппы а:
В-80 ГОСТ 2590-88
Круг 9ХС-а ГОСТ 5950—73 *
Сталь калиброванная круглая диаметром 20 мм, квалитет Ы1 по ГОСТ 7417—75, марки ХВГ с качеством поверхности группы — Б по ГОСТ 1051-73;
20-hll ГОСТ 7417—75
Круг ХВГ-Б ГОСТ 5950-73
Полоса толщиной 40 мм, шириной 60 мм из стали марки 7ХГ2ВМФ подгруппы б обычного качества (О):
Полоса | 40X60 ГОСТ 4405-75 7ХГ2ВМФ-6-О ГОСТ 5950—73' |
(Измененная редакция, Изм. № 2, 3, 4, 5).
3. ТЕХНИЧЕСКИЕ ТРЕБОВАНИЯ
3.1а. Прутки и полосы изготовляют в соответствии с требованиями настоящего стандарта по технологическому регламенту, утвержденному в установленном порядке.
(Введен дополнительно, Изм. № 2).
3.1. Концы прутков и полос металлопродукции должны быть ровно обрезаны или обрублены без заусенцев и стружки. Длина смятых концов не должна превышать:
С. 8 ГОСТ 5950-73
1,5 диаметра или толщины — для металлопродукции диаметром или толщиной до 10 мм;
40 мм — для металлопродукции диаметром или толщиной свыше 10 до 60 мм;
60 мм — для металлопродукции диаметром или толщиной свыше 60 мм.
(Измененная редакция, Изм. № 2).
3.2. Сталь изготовляют термически обработанной (после отжига или высокого отпуска). Сталь марок 11ХФ, 13Х, ХВ4Ф, 9X1, X, 12X1, 9ХС, В2Ф, ХГС, 9ХВГ, ХВГ, ХВСГФ для режущего инструмента изготовляют отожженной.
(Измененная редакция, Изм. № 3).
3.3. Обезуглероженный слой горячекатаной и кованой стали (феррит + переходная зона) не должен превышать на сторону (считая от фактического размера) для стали размером:
от 4 до 8 мм — 0,35 мм;
св. 8 ” 15 мм — 0,4 мм;
св. 15 до 30 мм — 0,5 мм;
” 30 ” 50 мм -0.7 мм;
”50 ” 70 мм —1,0 мм;
” 70 ” 100 мм — 1,3 мм.
Обезуглероженный слой калиброванных прутков квали-тетов hll и Ы2 (ГОСТ 7417-75, ГОСТ 8559- 75 и ГОСТ 8560-78) не должен превышать на сторону:
1,5 % действительного диаметра или толщины — для прутков из стали, содержащей до 0,5 % кремния или до 1,0 % молибдена;
2,0 % действительного диаметра или толщины — для прутков из стали, содержащей свыше 0,5 % кремния или свыше 1,0 % молибдена.
На стали со специальной отделкой поверхности обезуглероженный слой не допускается.
3.4. На поверхности металлопродукции подгруппы а, а также металлопродукции, предназначенной для холодной протяжки, не должно быть трещин, закатов, плен, раскатанных или раскованных пузырей и загрязнений.
Дефекты должны быть удалены пологой вырубкой или зачисткой.
Глубина зачистки не должна превышать:
для прутков диаметром или толщиной менее 80 мм — половины допуска на размер (полусуммы отклонений), считая от действительного;
для прутков диаметром или толщиной от 80 до 140 мм — допуска (суммы отклонений) на данный размер, считая от действительного;
для прутков (заготовок) размером сечения более 140 мм — 5 % номинального размера (диаметра или толщины), считая от действительного размера;
для полос — допуска на размер.
В одном сечении допускается не более двух зачисток.
Допускаются без зачистки отдельные мелкие царапины, отпечатки, рябизна и другие дефекты механического происхождения на глубину, не превышающую половины допуска на размер.
3.3., 3.4. (Измененная редакция, Изм. №2,5).
3.5. На поверхности металлопродукции подгруппы б допускаются местные дефекты, глубина которых не должна превышать половины допуска на размер — для мёталлопродукции, диаметр или толщина которой менее 80 мм; допуска на размер — для металлопродукции, диаметр или толщина которой 80 мм и более.
Для металлопродукции обычного качества (О) глубину считают от действительного размера, а для повышенного (П) — от номинального.
(Измененная редакция, Изм. № 2).
3.6. В заказе должно быть указано, для какой обработки предназначается сталь.
3.7. Поверхность калиброванной стали должна соответствовать требованиям группы В ГОСТ 1051—73, калиброванной шлифованной — группы Б ГОСТ 1051—73, стали со специальной отделкой поверхности групп В, Г, Д ГОСТ 14955—77. Группа отделки поверхности должна указываться в заказе.
3.8. Величина зерна аустенита в закаленном состоянии в прутках диаметром или толщиной до 140 мм подгруппы б должна соответствовать нормам, указанным в табл. За.
Таблица За
Группа назначения | Марка стали | Диаметр или толщина метал-лопродукции, мм | Величина зерна аустенита не крупнее номера | |
по ГОСТ $639-82 | по шкале изломов | |||
I | Х6ВФ, Х12, Х12ВМФ | До 80 | 9 | 4 |
Х12МФ, Х12Ф1, 7ХГ2ВМФ, 6Х6ВЗМФС, 8Х4В2МФС2, 11Х4В2МФЗС2.6Х4М2ФС | Св. 80 до 140 | 8 | 3 | |
4ХС, 6ХС, | До 80 | 9 | 4 | |
И | 5ХВ2СФ, 6ХВ2С. 6ХВГ, 6ХЗМФС | Св. 80 до 140 | 8 | 3 |
Все остальные | До 80 Св. 80 до 140 | 8 6 | 3 2 |
Примечание. Величина зерна аустенита стали для полос должна соответствовать нормам для прутков квадратного профиля с равновеликой площадью поперечного сечения.
(Измененная редакция, Изм. № 1, 2, 3, 5).
к 10 ГОСТ 5050-73
3.;. Макроструктура стали при контроле на протравленных темплетах не должна иметь подусадочной рыхлости, пузырей, расслоений, грещин, включений, раковин и флокенов.
Допускаются:
подусадочная ликвация и ликвационный квадрат — не более балла 1;
центральная пористость и пятнистая ликвация — не более балла 2;
точечная неоднородность — не более балла 3.
Для металла непрерывной разливки стали допускается повышенная травимость осевой зоны не более балла 2.
(Измененная редакция, Изм. № 2, 3).
3.10. Твердость отожженной или высокоотпущенной стали по длине прутка, заготовки и полосы должна соответствовать нормам, указанным в табл. 3.
3.11. Твердость стали после закалки и закалки с отпуском должна соответствовать нормам, указанным в табл. 4.
Таблица 3
Марка стали | Твердость, НВ, не более | Диаметр отпечатка, мм, не менее | Марка стали | Твердость, НВ. нс более | Диаметр отпечатка, мм, не менее |
8ХФ | 241 | 3,9 | 5ХНВС | 255 | 3,8 |
9ХФ | 241 | 3,9 | В2Ф | 229 | 4,0 |
11ХФ | 229 | 4,0 | 9X1 | 229 | 4,0 |
13Х | 248 | 3,85 | X | 229 | 4,0 |
ХВ4Ф | 255 | 3,8 | 12X1 | 241 | 3.9 |
9Г2Ф | 229 | 4,0 | 9ХС | 241 | 3,9 |
9ХВГ | 241 | 3,9 | ХГС | 241 | 3,9 |
ХВГ | 255 | 3,8 | 4ХМФС | 241 | 3.9 |
ХВСГФ | 241 | 3,9 | 4Х5В2ФС | 241 | 3,9 |
9X5 ВФ | 241 | 3,9 | 4Х5МФС | 241 | 3,9 |
8Х611ФТ | 241 | 3,9 | 4Х5МФ1С | 241 | 3,9 |
Х6ВФ | 241 | 3.9 | 4ХЗВМФ | 241 | 3,9 |
Х12 | 255 | 3,8 | 4Х4ВМФС | 241 | 3,9 |
Х12ВМФ | 255 | 3,8 | ЗХЗМЗФ | 229 | 4.0 |
Х12МФ | 255 | 3.8 | 4Х2В5МФ | 241 | 3,9 |
Х12Ф1 | 255 | 3,8 | 5ХЗВЗМФС | 241 | 3,9 |
7ХГ2ВМФ | 255 | 3,8 | 4ХС | 217 | 4,1 |
6Х6ВЗМФС | 255 | 3,8 | 6ХС | 229 | 4,0 |
6Х4М2ФС | 255 | 3,8 | 5ХВ2СФ | 229 | 4.0 |
11Х4В2МФЗС2 | 255 | 3,8 | 6ХВ2С | 269 | 3,7 |
8Х4В2МФС2 | 255 | 3,8 | 6ХВГ | 217 | 4,1 |
7X3 | 229 | 4,0 | 5Х2МИФ | 255 | 3,8 |
8X3 | 241 | 3,9 | 6ХЗМФС | 241 | 3,9 |
5ХИМ | 241 | 3.9 | 05X12116Д2МФСГТ | 293 | 3,5 |
5ХНВ | 255 | 3,8 | 1 |
Примечания:
1. Сталь всех марок подгруппы а должна иметь твердость нс более ИВ 255 (диаметр отпечатка нс менее 3,8 мм).
2. По согласованию изготовителя с потребителем прутки из стали марок 8ХФ, 9ХФ. 6ХЗМФС могут изготовляться с твердостью, нс превышающей 217ПВ (диаметр отпечатка нсмснсс4,1 мм).
(Измененная редакция, Изм. № 2, 3, 5).
Таблица 4
Марка стали | Температура, °C, и среда закалки образцов | Температура от* пуска, С | Твердость НЯСЭ (HRC), нс менее |
11ХФ | 810-830, масло | 63(62) | |
9X1 | 820-850, масло | — | 63(62) |
12X1 | 850-870, масло | — | 63(62) |
9ХС | 840-860, масло | — | 63(62) |
ХГС | 820-860, масло | — | 63(62) |
9ХВГ | 820-840, масло | — | 63(62) |
ХВСГФ | 840-860, масло | — | 63(62) |
13Х | 800,вода | 180 | 61(60) |
V /к | 840, масло | 180 | 60(59) |
ХВГ | 830, масло | 180 | 61(60) |
9Г2Ф | 790, масло | 180 | 60(59) |
ЗХФ | 830, масло | 180 | 58(57) |
800,вода | 180 | 58(57) | |
В2Ф | 830,вода | 180 | 60(59) |
Х12 | 970, масло | 180 | 62(61) |
Х12МФ | 970, масло | 180 | 61(60) |
Х12ВМФ | 1020, масло | 180 | 61(60) |
4Х5МФС | 1020, масло | 550 | 48(47) |
4Х5МФ1С | 1030, масло | 550 | 48(47) |
ЗХЗМЗФ | 1040, масло | 550 | 46(45) |
4Х4ВМФС | 1060, масло | 550 | 50(49) |
5ХЗВЗМФС | 1130, масло | 550 | 50(49) |
5ХНМ | 850, масло | 550 | 36(35) |
5Х2МНФ | 970, масло | 550 | 45(44) |
5ХВ2СФ | 910, масло | 180 | 56(55) |
Примечания:
1. Отклонения от приведенных в таблице температур закалки и отпуска, кроме стали марок 11ХФ, 9X1, 9ХС, ХГС, 9ХВГ и ХВСГФ, нс должны превышать ±10 °C.
2. Значения твердости после закалки образцов стали остальных марок приведены в справочном приложении 5.
3. Значения твердости после закалки и отпуска в зависимости от температуры отпуска приведены в справочном приложении 7.
(Измененная редакция» Изм. № 2, 3, 4).
3.12. Микроструктура горячекатаной, кованой стали со специальной отделкой поверхности и калиброванной стали марок ИХФ, 13Х, ХВ4Ф, 9X1, X, 12X1, 9ХС, В2Ф, ХГС, 9ХВГ, ХВГ, ХВСГФ, 8ХФ и 9Г2Ф в прутках диаметром или толщиной до 60 мм включительно, подгруппы б должна соответствовать следующим нормам:
зернистый перлит — баллам 1—6,
остатки карбидной сетки стали марок 11ХФ, 9X1, X, 9ХС, Б2Ф, ХГС, 9ХВГ, ХВСГФ не должны превышать балла 3, а стали марки 12X1 — балла 4.
В сталях марок 13Х и ХВГ остатки карбидной сетки не должны превышать 3 или 4 балла. Балл карбидной сетки указывается в заказе.
Для прутков диаметром или толщиной свыше 60 мм нормы зернистого перлита и карбидной сетки устанавливают по согласованию изготовителя с потребителем.
Нормы микроструктуры (перлита и карбидной сетки) полосовой стали приравнивают к нормам микроструктуры квадратного профиля равновеликой площади поперечного сечения.
(Измененная редакция, Изм. № 2, 3, 5).
3.13. Карбидная неоднородность стали марок ХВ4Ф, 9Х5ВФ, 8Х6НФТ, 8Х4В2МФС2, Х6ВФ, Х12, Х12ВМФ, Х12МФ, Х12Ф1, 6Х6ВЗМФС, 11Х4В2МФЗС2, 6Х4М2ФС не должна превышать норм, указанных в табл. 5.
3.14. По требованию потребителей должен проводиться контроль карбидной неоднородности сталей марок 11ХФ, 13Х, 9X1, X, 12X1, 9ХС, В2Ф, ХГС, 9ХВГ, ХВГ, ХВСГФ по шкале 6А ГОСТ 8233—56. Нормы устанавливаются по согласованию изготовителя с потребителем.
(Измененная редакция, Изм. № 3).
Таблица 5
Диаметр или толщи-на прутка, мм | Наибольшая допустимая норма карбидной неоднородности, баллы, для стали марок | |
ХВ4Ф, 9Х5ВФ, 8Х6НФТ, 8Х4В2МФС2, Х6ВФ, 6Х6ВЗМФС, 11Х4В2МФЗС2, 6Х4М2ФС | Х12, Х12ВМФ, Х12МФ,Х12Ф1 | |
До 40 | 3 | 4 |
Св. 40 до 60 | 4 | 5 |
** 60 ” 80 | 5 | 6 |
” 80 ’* 100 | 6 | 7 |
Примечания:
1. Нормы карбидной неоднородности полосовой стали приравниваются к нормам карбидной неоднородности квадратного профиля с площадью, равновеликой площади поперечного сечения полосы.
2. По согласованию изготовителя с потребителем сталь изготовляют с карбидной неоднородностью на 1 балл ниже норм, указанных в табл. 5.
(Измененная редакция, Изм. № 3).
4. ПРАВИЛА ПРИЕМКИ
4.1. Сталь принимают партиями, состоящими из прутков и полос одной плавки, одной подгруппы, одного размера, одного качества поверхности и одного режима термической обработки.
Каждая партия стали должна сопровождаться документом о качестве, заполненным в соответствии с требованиями ГОСТ 7566-81.
4.2. Для проверки химического состава отбирается одна проба от плавки, от партии прутков или полос — один пруток или полоса.
4.1, 4.2. (Измененная редакция, Изм. № 2).
4.3. Для проверки размеров - 10% прутков, заготовок или полос от партии.
4.4. Для проверки глубины обезуглероженного слоя — два прутка или полосы от партии.
(Измененная редакция, Изм. № 2).
4.5. Качество поверхности проверяют на всех прутках, полосах партии.
4.6. Для проверки величины зерна аустенита в закаленном состоянии отбирают два прутка, две заготовки или полосы от партии.
(Измененная редакция, Изм. № 1).
4.7. Для проверки макроструктуры два прутка, две заготовки или полосы от партии.
4.8. Для проверки твердости стали в готовом виде отбирают: от прутков толщиной до 30 мм — два прутка от 1 т, но не
менее шести прутков от партии;
от прутков толщиной более 30 мм -- 5 % прутков от партии, но не менее пяти прутков;
от полос и заготовок две полосы или заготовки от 1 т, но не менее пяти от партии.
4.9. Для проверки твердости стали после закалки — один пруток, одну полосу или заготовку от партии, но не менее двух от плавки.
4.10. Для проверки микроструктуры (зернистого перлита, карбидной сетки и карбидной неоднородности) — два прутка или две полосы от партии.
4.11. При получении неудовлетворительных результатов испытаний хотя бы по одному из показателей (кроме размеров и флокенов), повторные испытания проводят по ГОСТ 7566-81.
В случае обнаружений флокенов партию не принимают, а при несоответствии размеров партию подвергают 100%-ной рассортировке.
(Измененная редакция, Изм. № 2).
4.12. Карбидная неоднородность, макроструктура, величина зерна, твердость прутков диаметром или толщиной до 40 мм включительно обеспечиваются технологией изготовления.
(Введен дополнительно, Изм. № 1).
5. МЕТОДЫ ИСПЫТАНИЙ
5.1. Отбор проб для определения химического состава стали проводят по ГОСТ 7565—81, химический анализ стали — по ГОСТ 12344-88, ГОСТ 12345-88, ГОСТ 12346-78, ГОСТ 12347-77, ГОСТ 12348-78, ГОСТ 12349-83, ГОСТ 12350-78, ГОСТ 12351-81, ГОСТ 12352-81, ГОСТ 12354-81, ГОСТ 12355-78, ГОСТ 12356-81, ГОСТ 12359-81, ГОСТ 12360-82, ГОСТ 12361-82, ГОСТ 12364-84, ГОСТ 12365-84, ГОСТ 28473—90 или другими методами, обеспечивающими необходимую точность.
(Измененная редакция, Изм. № 3).
5.2. Размеры горячекатаной, кованой стали проверяют универсальными измерительными инструментами или шаблонами, а калиброванной стали и стали со специальной отделкой поверхности микрометрами и скобами.
5.3. Глубину обезуглероженного слоя стали определяют по ГОСТ 1763 68. Сталь со специальной отделкой поверхности допускается контролировать- методом термоэлектродвижущей силы.
В случае разногласий между потребителем и изготовителем контроль глубины обезуглероженного слоя должен проводиться методом М.
П римечание. Глубину обезуглероженного слоя полосовой стали следует измерять по широкой стороне.
5.4. Качество поверхности стали проверяют без применения увеличительных приборов; в случае необходимости проводят зачистку поверхности (кольцами или змейкой).
5.5. Для проведения испытаний по пп. 4.4, 4.6—4.10 от каждой отобранной единицы продукции отрезают по одному образцу.
5.6. Температуры закалки образцов для контроля величины зерна аустенита приведены в справочном приложении 5, а для марок стали, не указанных в приложении, — в табл. 4.
Величину зерна аустенита допускается контролировать по микроструктуре или по излому.
Для получения излома образец надрезают с одной или двух сторон, после чего отламывают. Контроль величины зерна аустенита по излому проводят осмотром без применения увеличительных приборов путем сравнения образца с эталонами шкалы № 5 (см. обязательное приложение 36). По форме и размерам образцы должны соответствовать требованиям ГОСТ 10243—75.
Схема отбора образцов, их форма и размер для контроля величины зерна аустенита по микроструктуре приведены в обязательном приложении 4.
Зерно аустенита выявляется методом травления границ зерен. Контроль величины зерна аустенита проводится по ГОСТ 5639—82.
(Измененная редакция, Изм. № 1, 3, 5).
5.7. Макроструктуру прутков, заготовок, полос необходимо проверять на протравленных темплетах без применения увеличительных приборов по ГОСТ 10243—75.
Разрешается результаты контроля макроструктуры в крупных профилях проката распространять на более мелкие профили той же плавки. Повышенная травимость оценивается по шкале для оценки подусадочной ликвации.
Для прутков диаметром или толщиной свыше 140 мм допускается пробы перековывать на круг или квадрат диаметром или толщиной от 90 до 140 мм.
Допускается контролировать флокены в поставляемом профиле.
(Измененная редакция, Изм. № 1, 2, 5).
5.8. Твердость отожженной или высокоотпущенной стали проверяют по ГОСТ 9012—59 после снятия обезуглероженного слоя.
Испытание следует проводить на расстоянии примерно 100 мм от конца прутка, заготовки или полосы.
Количество отпечатков должно быть не менее трех, каждое значение твердости должно соответствовать указанным в табл. 3.
(Измененная редакция, Изм. № 2).
5.9. Твердость стали после закалки проверяют по ГОСТ 9013—59 на образцах, отобранных от готового профиля и закаленных от температуры, указанной в табл. 4.
Количество измерений должно быть не менее трех, причем первое измерение не учитывается.
Форма и размеры образцов такие же, как и для контроля величины зерна аустенита.
(Измененная редакция, Изм. № 2, 3).
5.10. Микроструктуру стали марок 8ХФ, 11ХФ, 13Х, ХВ4Ф, В2Ф, 9X1, X, 12X1, 9ХС, ХГС, 9ХВГ, ХВГ, ХВСГФ и 9Г2Ф оценивают:
перлит — по шкале № 1 в соответствии с приложениями № 1 и 4;
карбидную сетку (кроме сталей марок 8ХФ, ХВ4Ф, и 9Г2Ф) — по шкале № 4 в соответствии с приложениями За и 4.
5.11. Карбидную неоднородность стали марок Х12,Х12ВМФ, Х12МФ, Х12Ф1 оценивают по шкале № 2 в соответствии с приложениями 2 и 4; стали марок ХВ4Ф, 9Х5ВФ, 8Х6НФТ, Х6ВФ, 6Х6ВЗМФС, 6Х4М2ФС, 11Х4В2МФЗС2, 8Х4В2МФС2 - по шкале № 3 в соответствии с приложениями 3 и 4.
5.10, 5.11. (Измененная редакция, Изм. № 5).
5.12. Допускается применять статистические и неразрушающие методы контроля по нормативно-технической документации.
При возникновении разногласий применяются методы контроля, регламентированные настоящим стандартом.
(Введен дополнительно, Изм. № 3).
6. МАРКИРОВКА, УПАКОВКА, ТРАНСПОРТИРОВАНИЕ И ХРАНЕНИЕ
6.1. Общие правила маркировки — по ГОСТ 7566—81. Сталь, полученную методом электрошлакового переплава, дополнительно маркируют букой Ш, например, ЗХЗМЗФ-Ш.
Прутки диаметром или толщиной свыше 50 мм подвергают 100 % клеймению.
(Измененная редакция, Изм. № 5).
6.2. Упаковка горячекатаной и кованой стали должна проводиться в соответствии с требованиями ГОСТ 7566—81.
Упаковка стали со специальной отделкой поверхности — по ГОСТ 14955—77, калиброванной стали — по ГОСТ 1051—73.
6.3. Транспортирование и хранение должны соответствовать требованиям ГОСТ 7566—81.
6.4. Калиброванная сталь и сталь со специальной отделкой поверхности должны храниться в закрытых складских помещениях.
6.3, 6.4. (Введены дополнительно, Изм. № 3).
ПРИЛОЖЕНИЕ 1 Обязательное
ОПИСАНИЕ ШКАЛЫ № 1 ДЛЯ ОЦЕНКИ МИКРОСТРУКТУРЫ ИНСТРУМЕНТАЛЬНОЙ ЛЕГИРОВАННОЙ СТАЛИ (УВЕЛИЧЕНИЕ 500х )
Шкала включает 10 микрофотографий возможных микроструктур отожженной или высокоотпущенной стали.
Микроструктуры баллов 1—5 — структуры зернистого перлита с размерами зерен цементита менее 1 до 10 мкм.
Микроструктуры баллов 6—10 — структуры зернистого перлита с постоянно возрастающим количеством пластинчатого перлита (по площади) ;
балл 6 — до 10 % пластинчатого перлита;
балл 7 — до 30 % пластинчатого перлита;
балл 8 — до 50 % пластинчатого перлита;
балл 9 — до 80 % пластинчатого перлита;
балл 10 — до 100 % пластинчатого перлита.
Микроструктуры стали, лежащие между соседними баллами шкалы, относятся при оценке к большему баллу.
(Измененная редакция, Изм. № 5).
2-1824
ШКАЛА №1
Микроструктура инструментальной легированной стали в отожженном состоянии

Балл 1
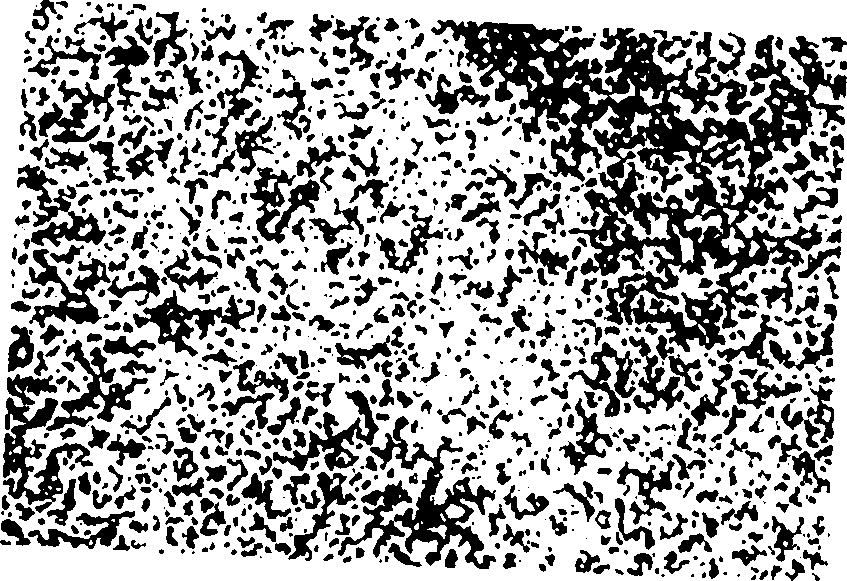
Балл 2
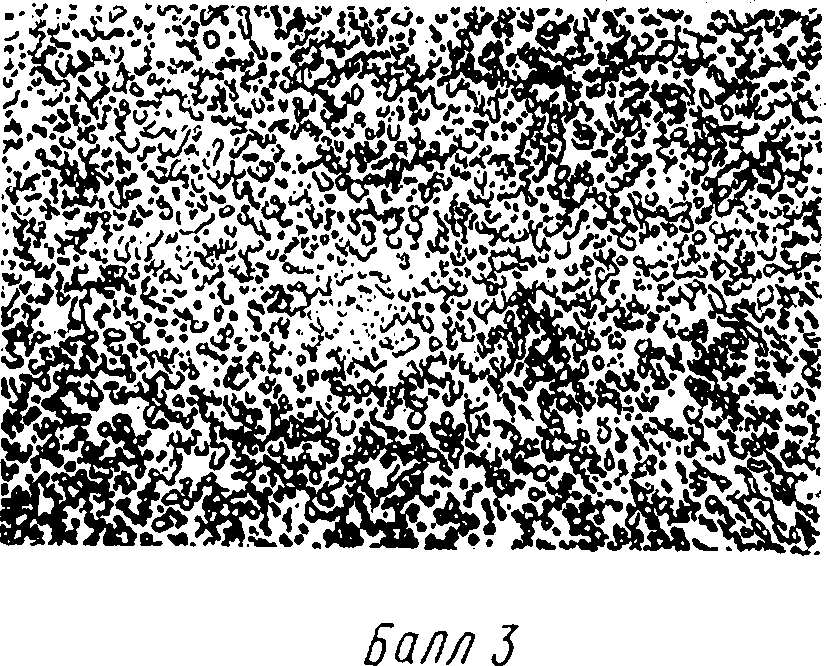

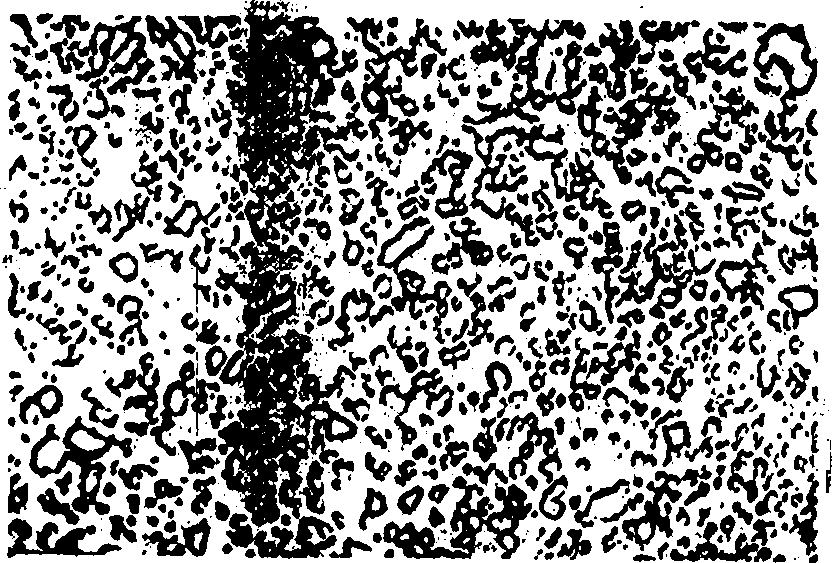
Валл 5
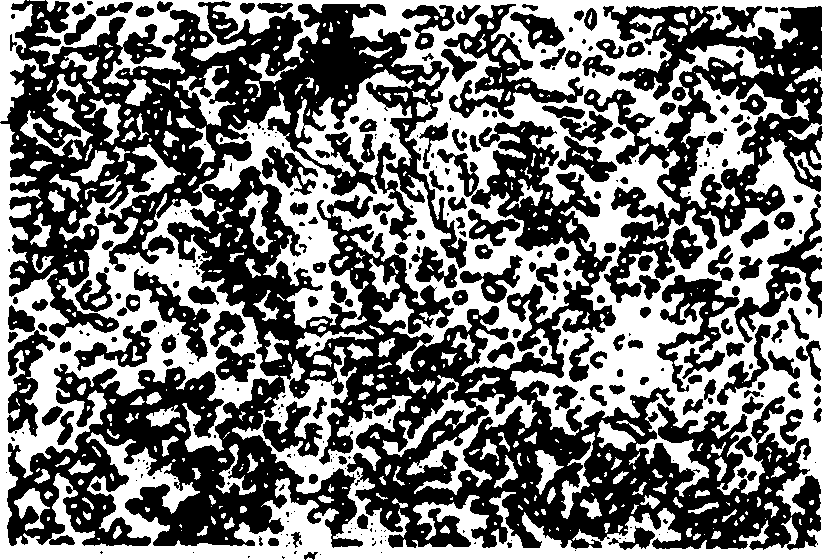
Балл 6
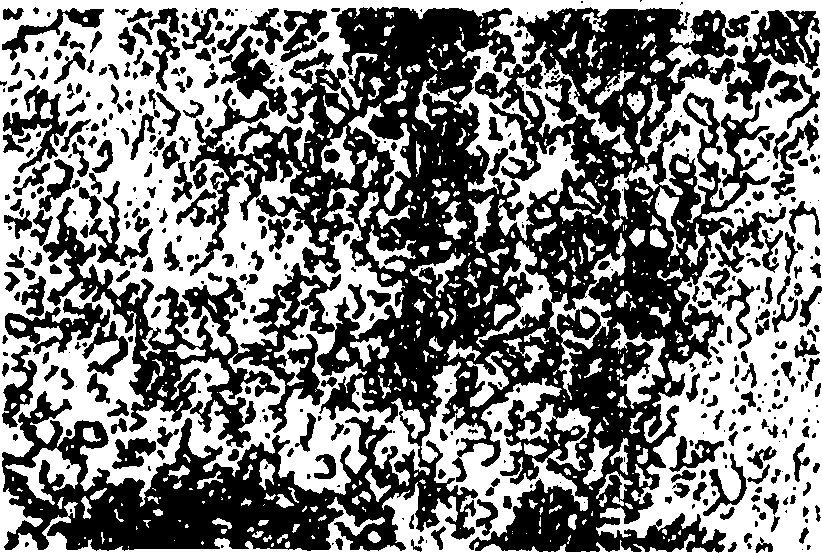
Балл 7

Балл 8
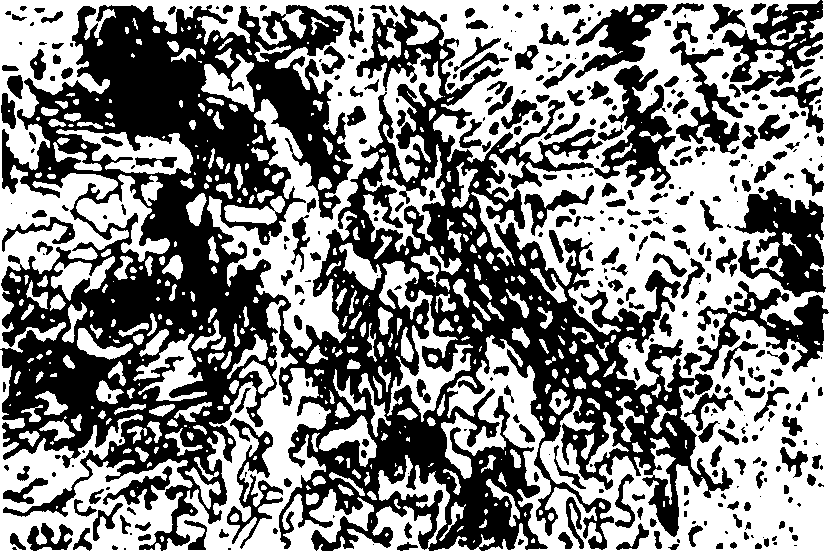
Балл 9
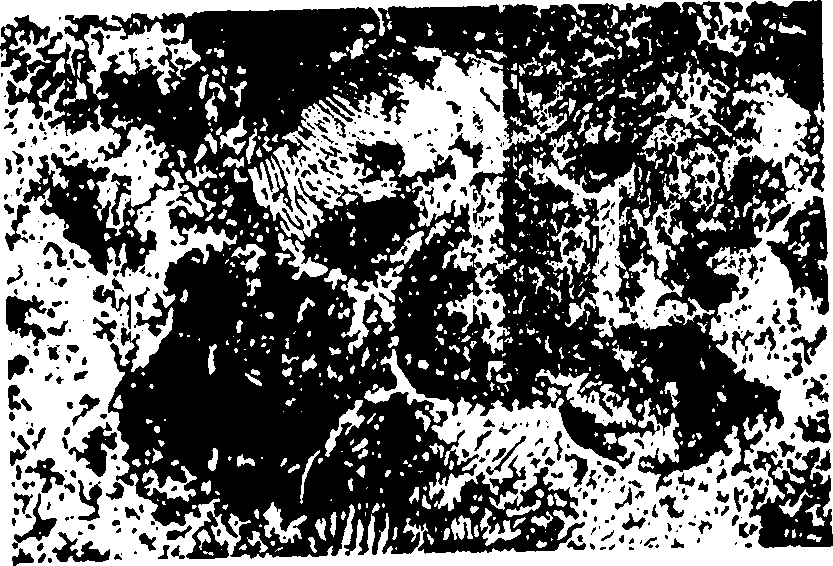
Балл 10
ПРИЛОЖЕНИЕ 2 Обязательное
ОПИСАНИЕ ШКАЛЫ № 2 ДЛЯ ОЦЕНКИ КАРБИДНОЙ НЕОДНОРОДНОСТИ СТАЛИ МАРОК Х12, Х12ВМФ, Х12МФ, Х12Ф1 (увеличение ЮОХ)
Шкала имеет два ряда эталонов микроструктур. Верхние микроструктуры предназначены для оценки карбидной неоднородности стали на образцах после термической обработки (закалка — отпуск) .
Нижние микроструктуры предназначены для оценки карбидной неоднородности отожженных образцов стали.
Описание структур, соответствующих отдельным баллам шкалы; балл 1 — равномерное распределение карбидов;
балл 2 — слабо выраженная полосчатость, тонкие строчки карбидов; балл 3 — строчечное расположение карбидов;
балл 4 — резко выраженная полосчатость, грубые строчки карбидов; балл 5 — значительно деформированная, местами разорванная сетка карбидов;
балл 6 — деформированная сетка эвтектических карбидов;
балл 7 — сплошная деформированная сетка карбидов с участками эвтектики;
балл 8 — слабо деформированная сетка карбидов с участками эвтектики;
балл 9 — слабо деформированная сетка с грубой карбидной эвтектикой;
балл 10 — структура, соответствующая литой стали. (Измененная редакция, Иэм. № 2, 3).
mvа пд № 2 ДЛЯ ОЦЕНКИ КАРБИДНОЙ НЕОДНОРОДНОСТИ СТАЛИ МАРОК Х12, Х12МФ, Х12ВМФ, Х12Ф1
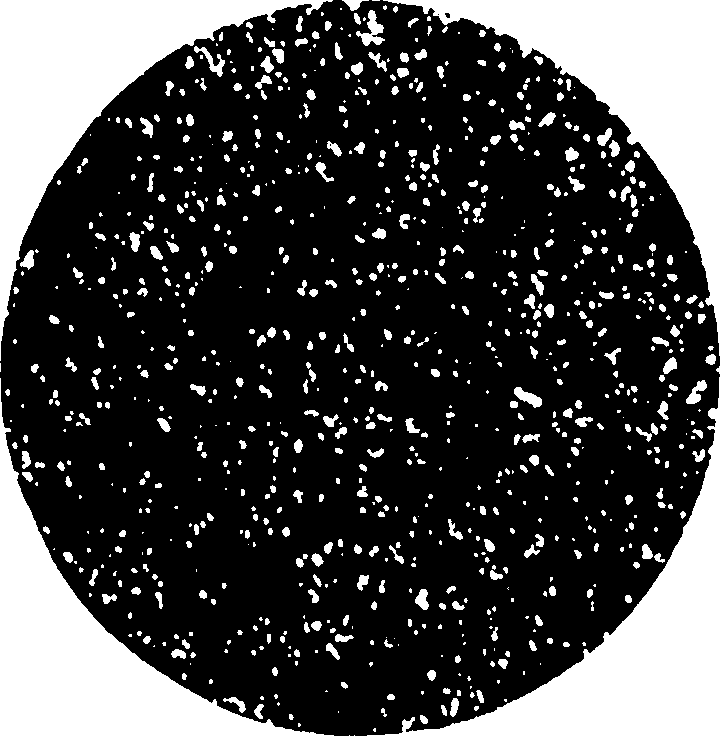
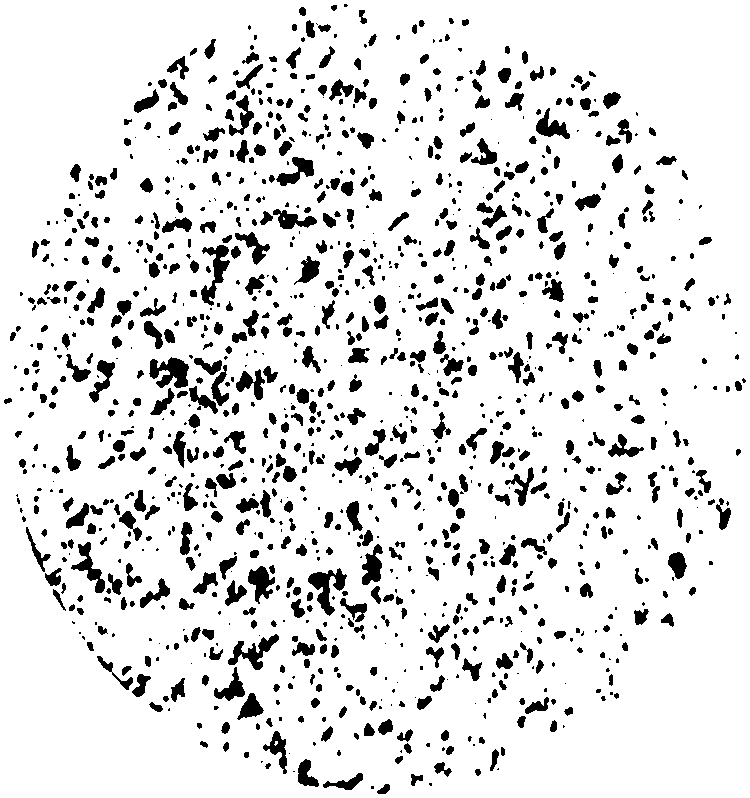
Балл 7
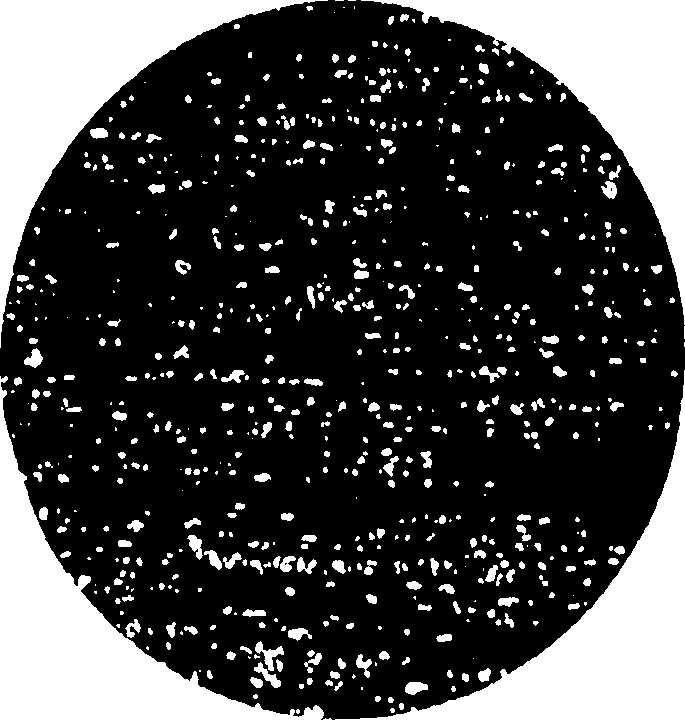
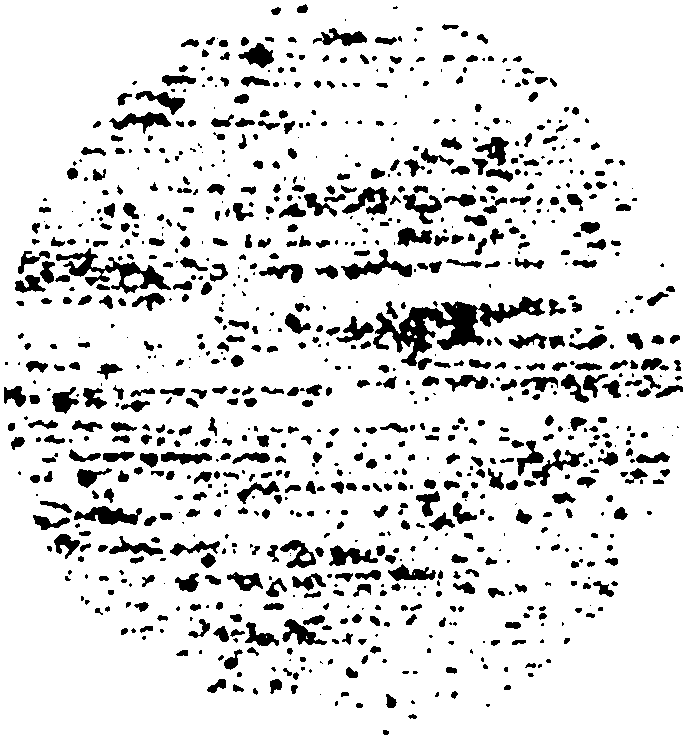
Балл 2
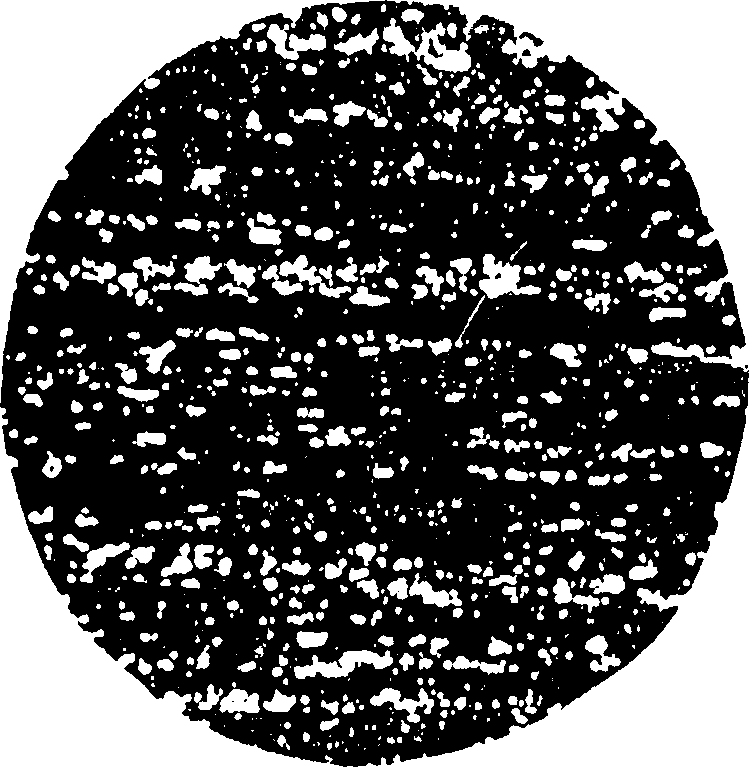
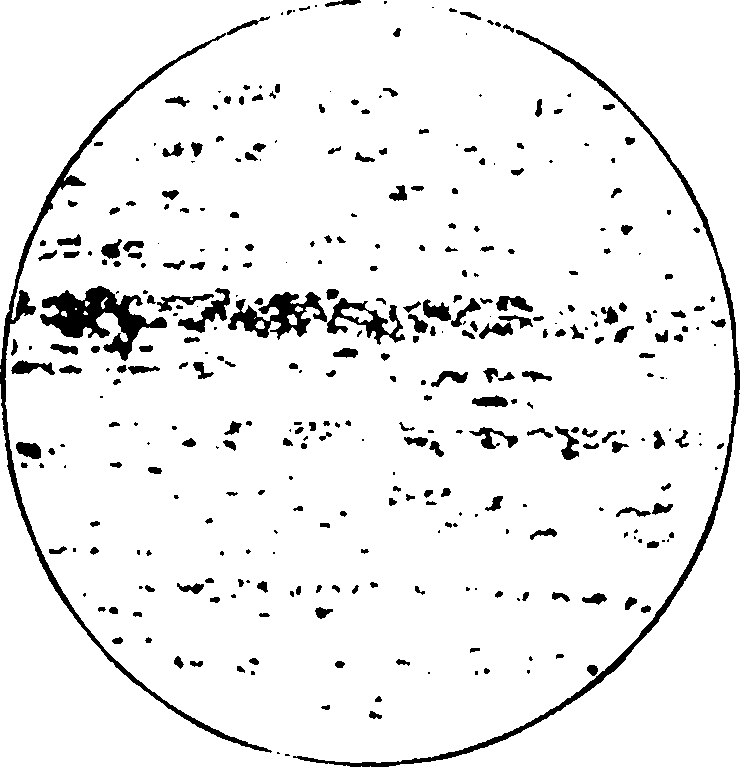
Балл 3
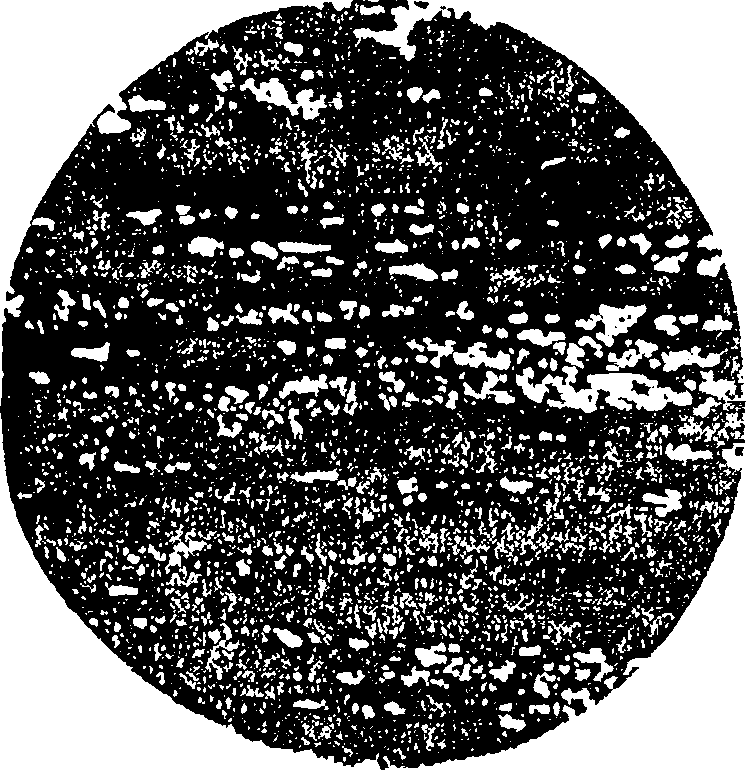
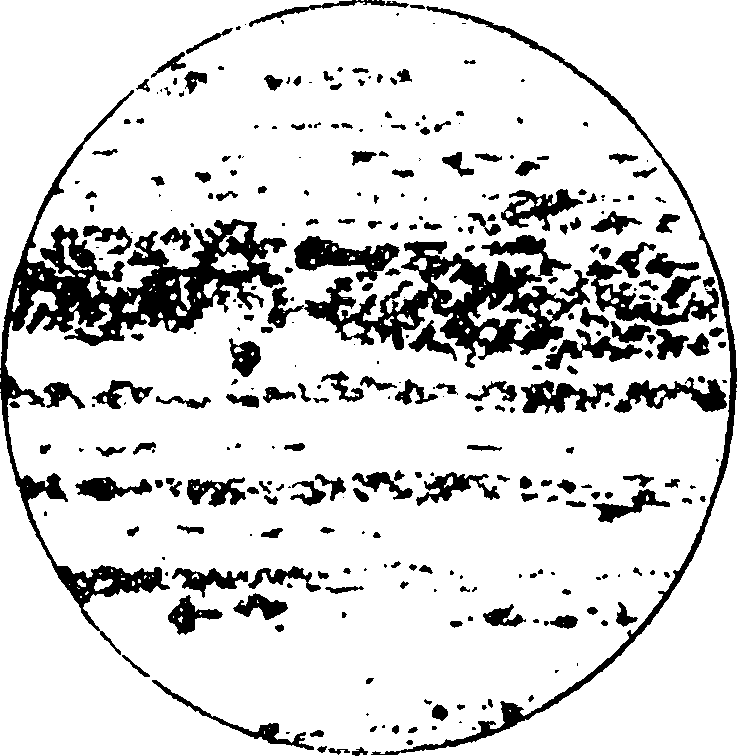
Болл 4
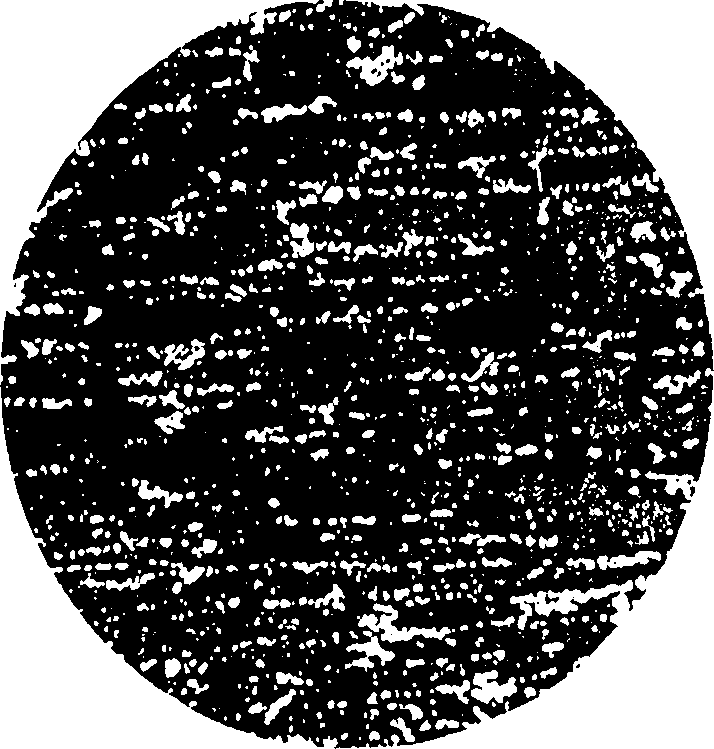
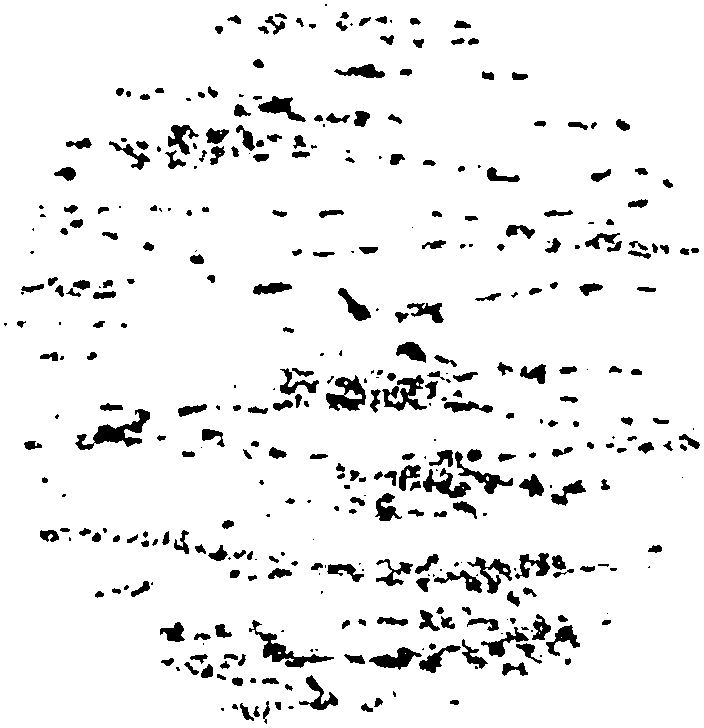
Балл 5
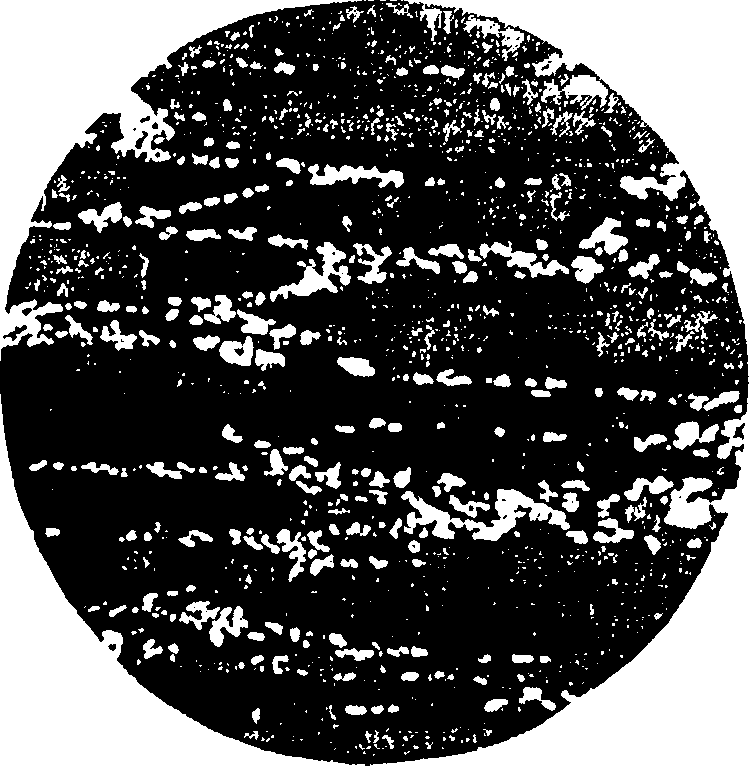
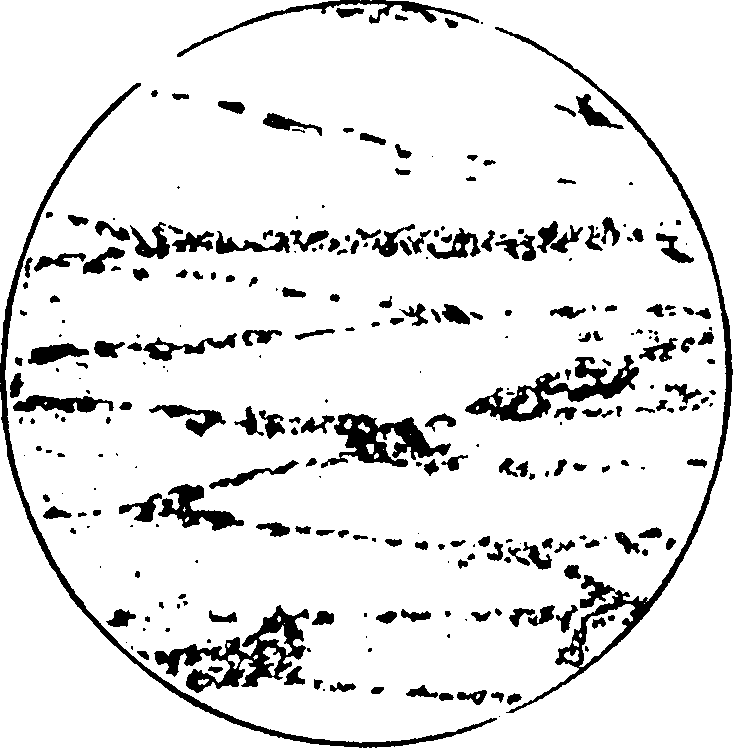
балл 6
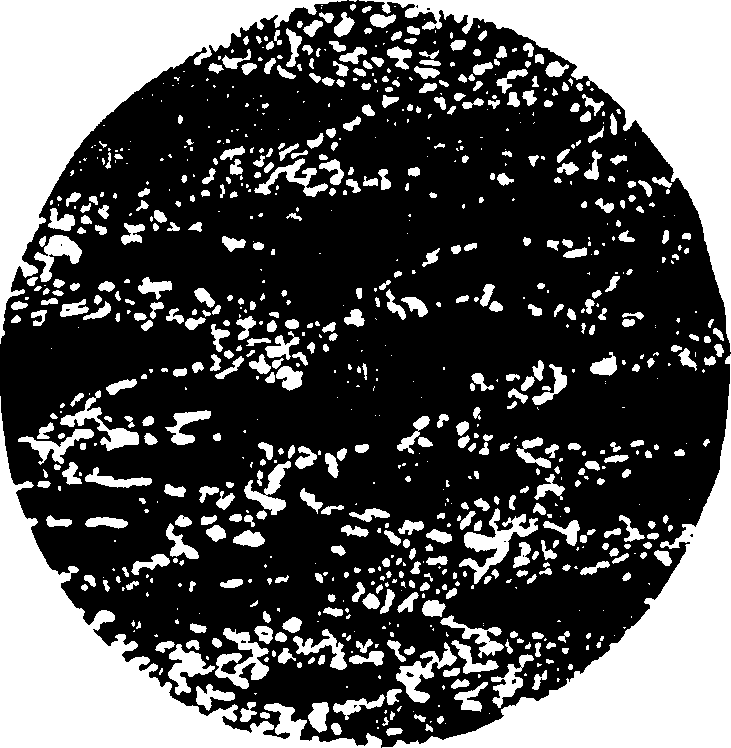
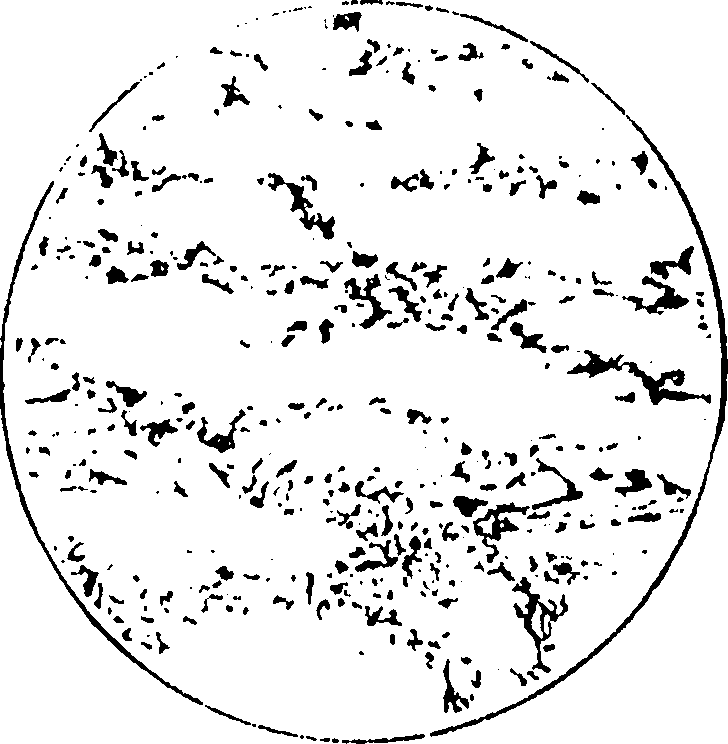
Балл 7
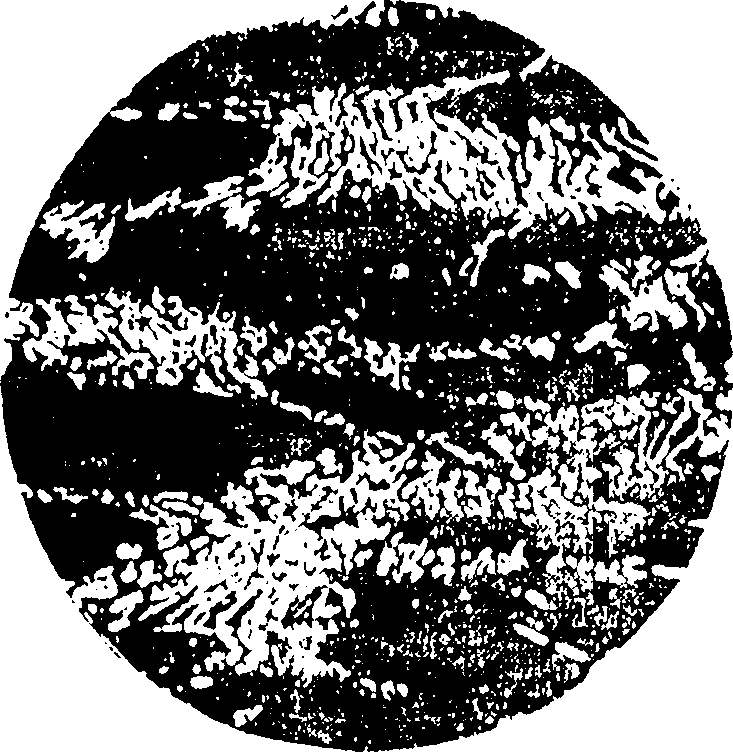

Балл 8
3. 32 ГОСТ 5950-73
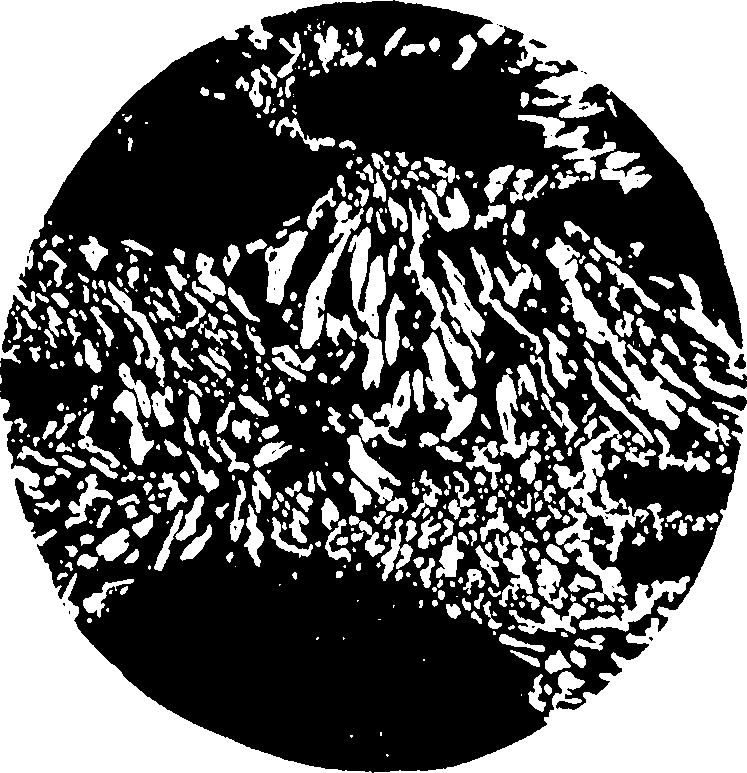
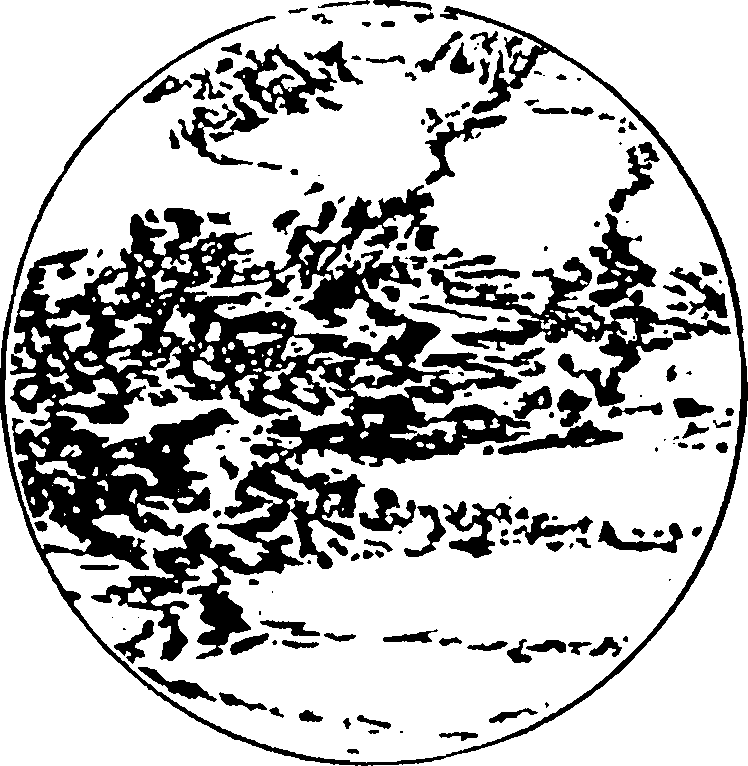
Балл 9
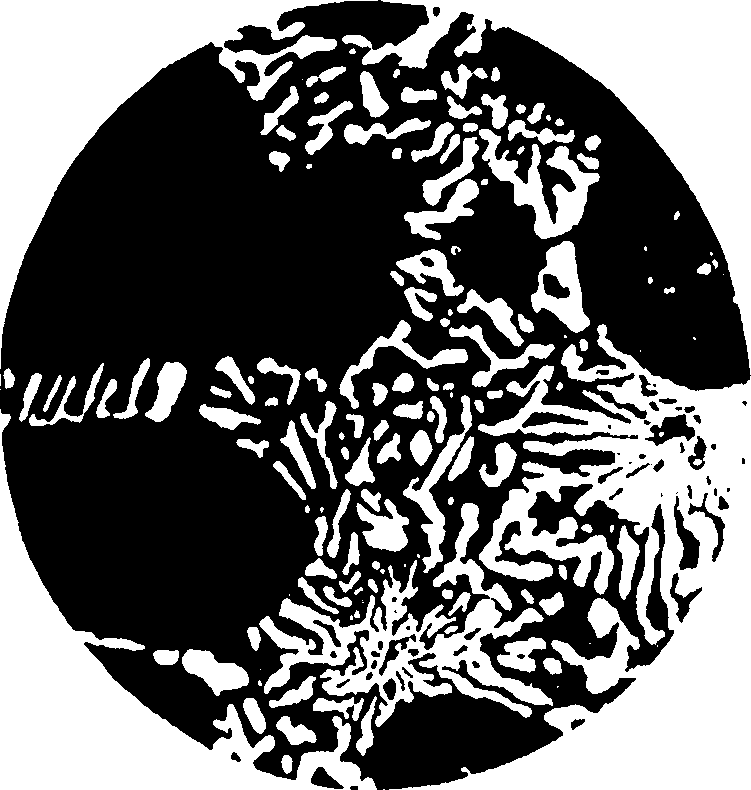

Балл 10
(Измененная редакция, Изм. N* 2).
С. 34 ГОСТ 5950-73
ПРИЛОЖЕНИЕ 3 Обязательное
ОПИСАНИЕ ШКАЛЫ № 3 ДЛЯ ОЦЕНКИ КАРБИДНОЙ НЕОДНОРОДНОСТИ СТАЛИ МАРОК ХВ4Ф, 9Х5ВФ, 8Х6НФТ, 8Х4В2МФС2, Х6ВФ» 6Х6ВЗМФС, 11Х4В2МФЗС2, 6Х4М2ФС (увеличение 100х)
Описание микроструктур, соответствующих отдельным баллам шкалы:
балл 1 — равномерное распределение карбидов;
балл 2 — слабо выраженная полосчатость;
балл 3 — полосчатость;
балл 4 — резко выраженная полосчатость;
балл 5 — резко выраженная полосчатость со скоплениями;
балл 6 — резко выраженная полосчатость со скоплениями, сильноде* формированная разорванная сетка эвтектических карбидов;
балл 7 — деформированная сетка эвтектических карбидов, разорванная в отдельных местах;
балл 8 — сплошная деформированная сетка эвтектических карбидов; балл 9 — сплошная деформированная сетка со скоплениями карбидов; балл 10 — структура, соответствующая литой стали.
ШКАЛА № 3 ДЛЯ ОЦЕНКИ КАРБИДНОЙ НЕОДНОРОДНОСТИ СТАЛИ МАРОК ХВ4Ф, 9Х5ВФ, 8Х6НФТ, 8Х4В2МФС2, Х6ВФ, 6Х6ВЗМФС, 11Х4В2МФЗС2, 6Х4М2ФС

Балл 1
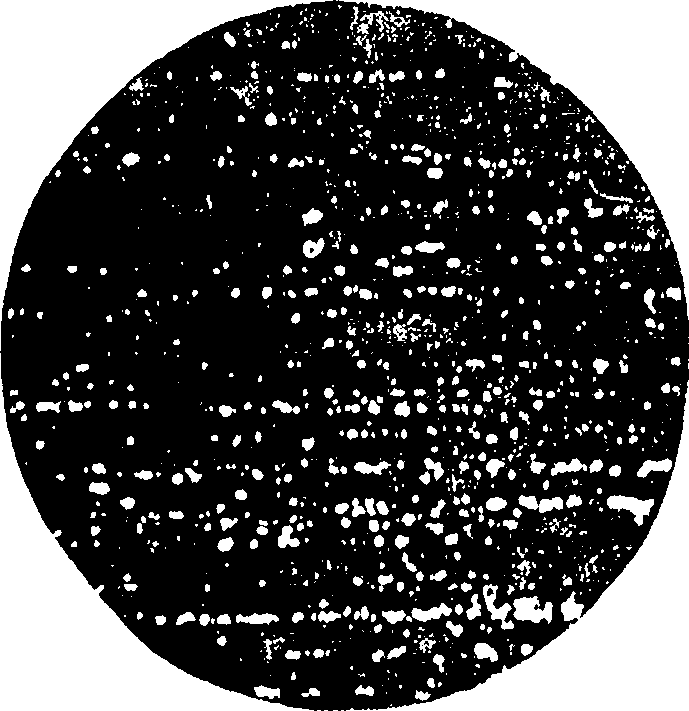
Балл 2
С. 36 ГОСТ 5950-73
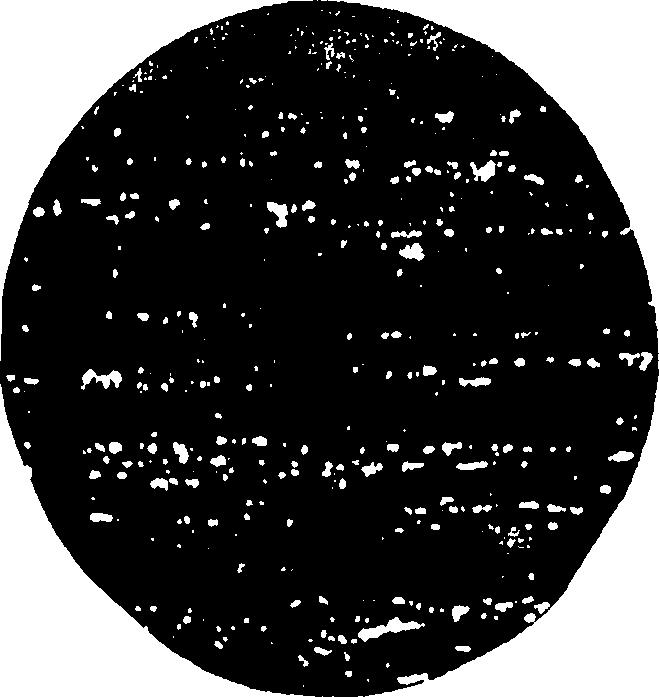
Балл J
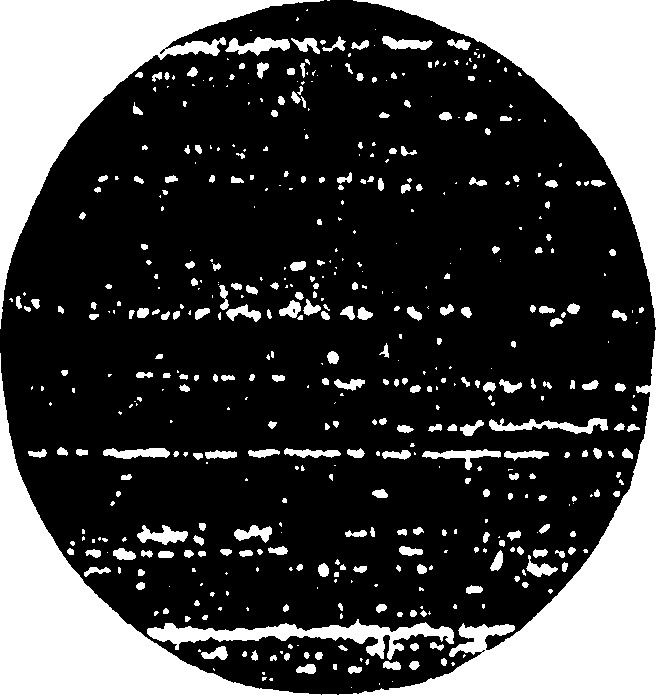
Балл 4

Балл 5

Балл 6
С. 3« гост 5950-73

балл 7
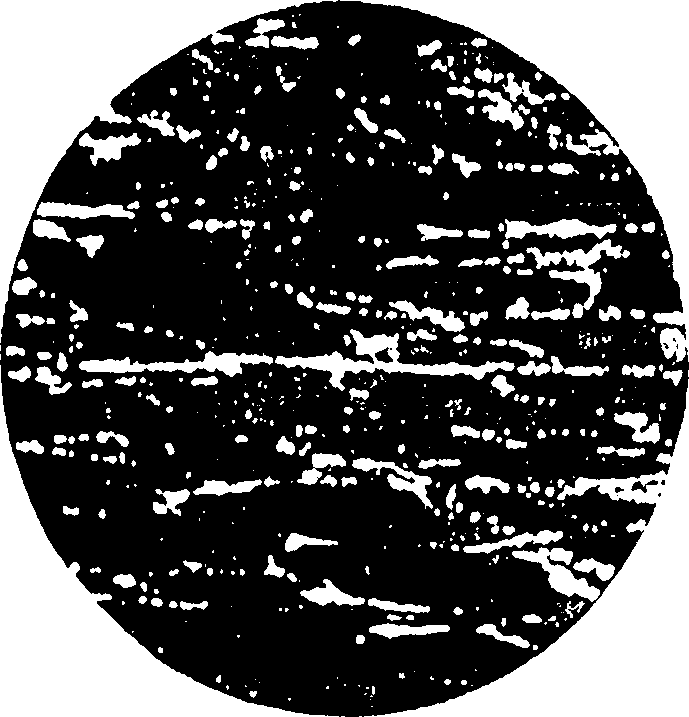
Балл 8
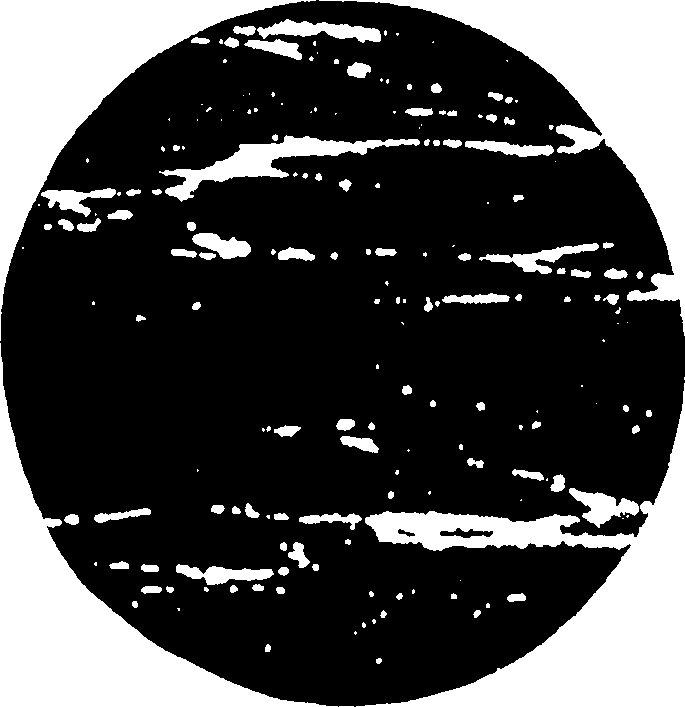
Балл 9
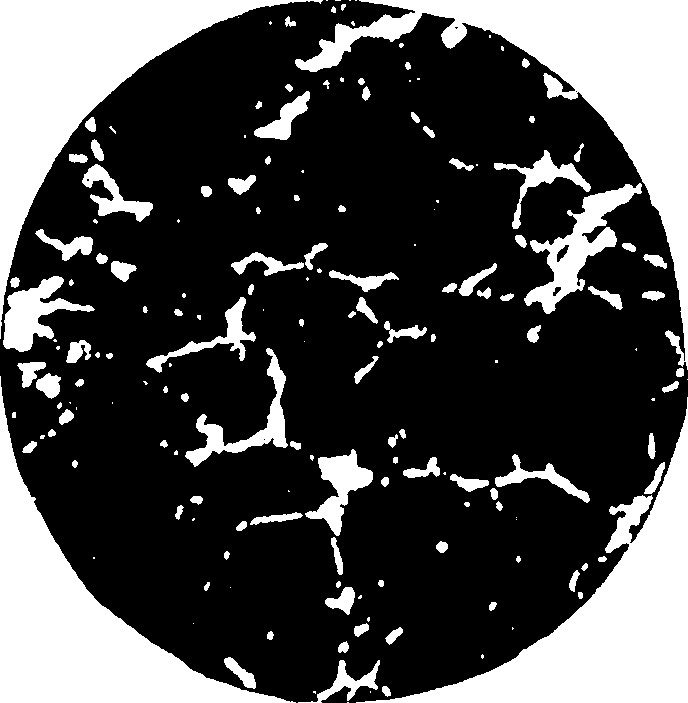
Балл 10
С. 40 ГОСТ 5950—73
ПРИЛОЖЕНИЕ За Обязательное
ОПИСАНИЕ ШКАЛЫ № 4 ДЛЯ ОЦЕНКИ КАРБИДНОЙ СЕТКИ В ИНСТРУМЕНТАЛЬНОЙ ЛЕГИРОВАННОЙ СТАЛИ (увеличение 500х )
Шкала включает 2 эталона возможных видов карбидной сетки — по 6 эталонов каждого вида.
Верхний — крупноячеистая сетка (средний относительный диаметр ячейки приблизительно 0,045 мм)
Нижний — мелкоячеистая сетка (средний относительный диаметр ячейки приблизительно 0,025 мм).
Эталоны отличаются по замкнутости сетки и соответствуют следующим баллам:
балл 1 — практически равномерное распределение карбидных частиц; балл 2— имеют место отдельные цепочки карбидных частиц;
балл 3 — цепочки карбидных частиц в виде обрывков слабо выраженной сетки;
балл 4 — цепочки карбидных частиц в виде заметно выраженной сетки; балл 5 — цепочки карбидных частиц образуют сетку с.отдельными полностью замкнутыми ячейками;
балл 6 — карбидные частицы образуют сетку с полностью замкнутыми ячейками. Причем стороны ячеек имеют вид не только цепочек карбидов, но и сплошных линий.
ШКАЛА № 4 ДЛЯ ОЦЕНКИ КАРБИДНОЙ СЕТКИ
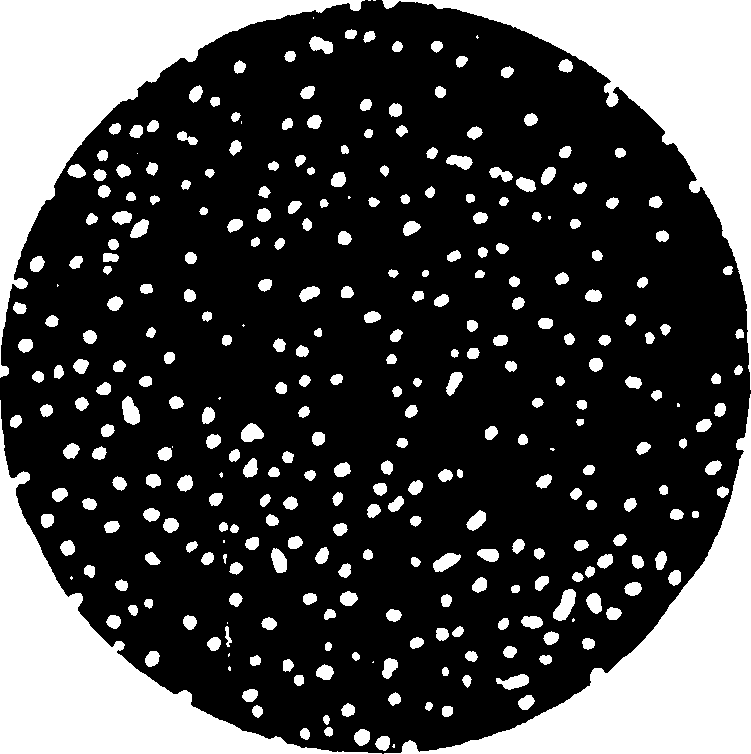
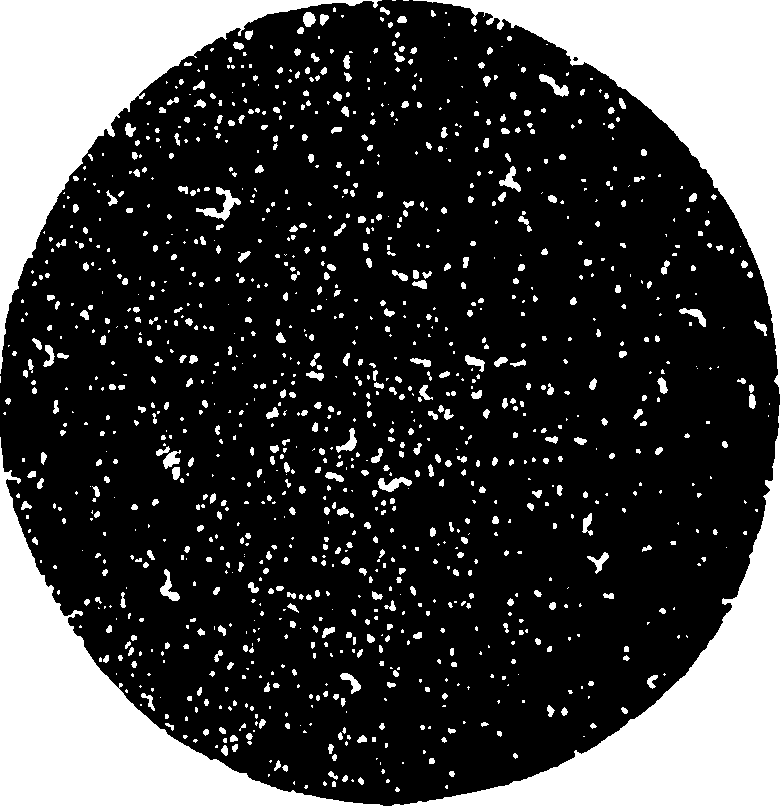
балл /
С. 4 2 ГОСТ 5950-73
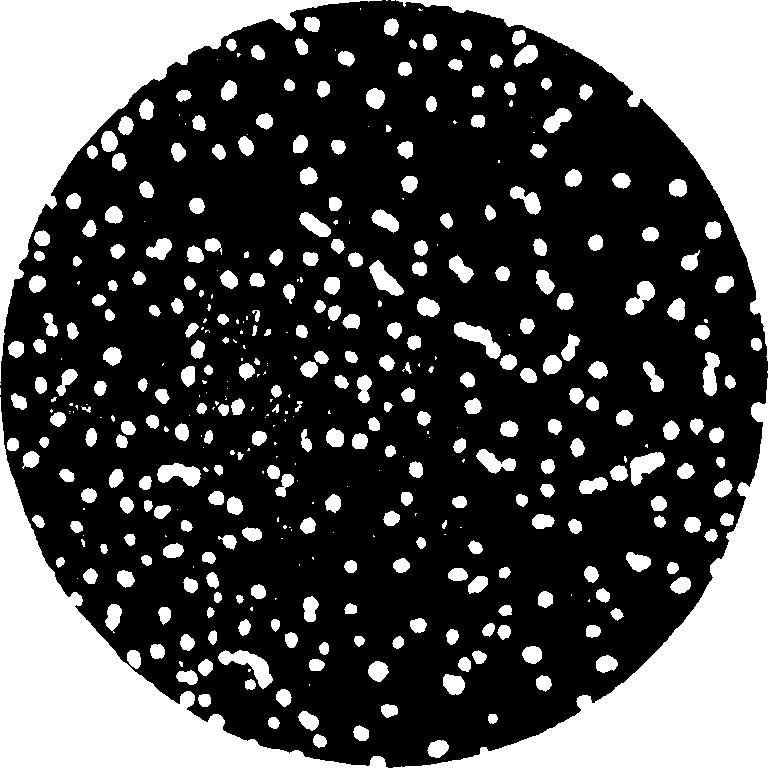
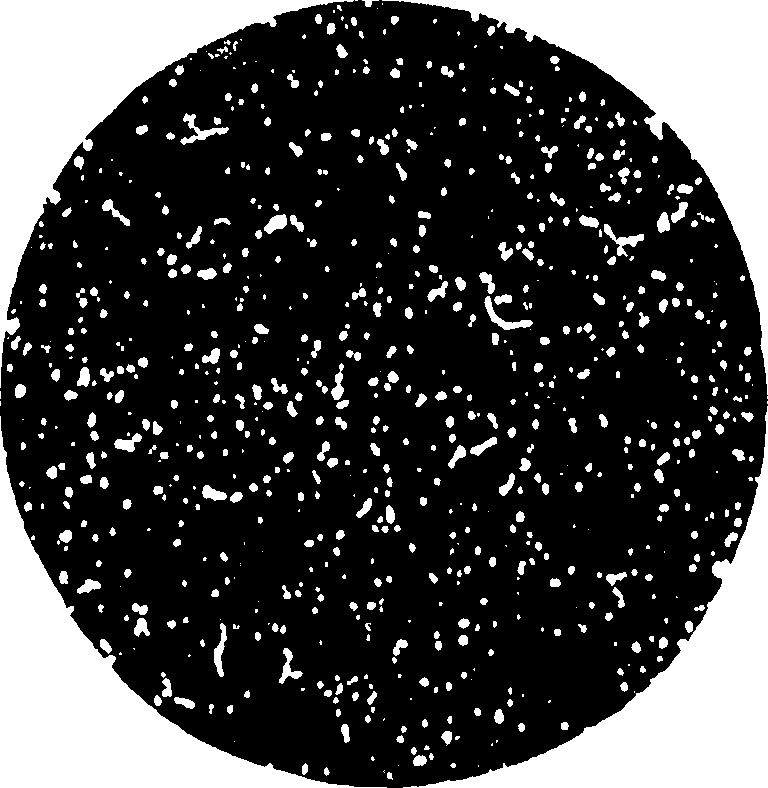
Балл £
1 OCT 5950-73 С. 4 3
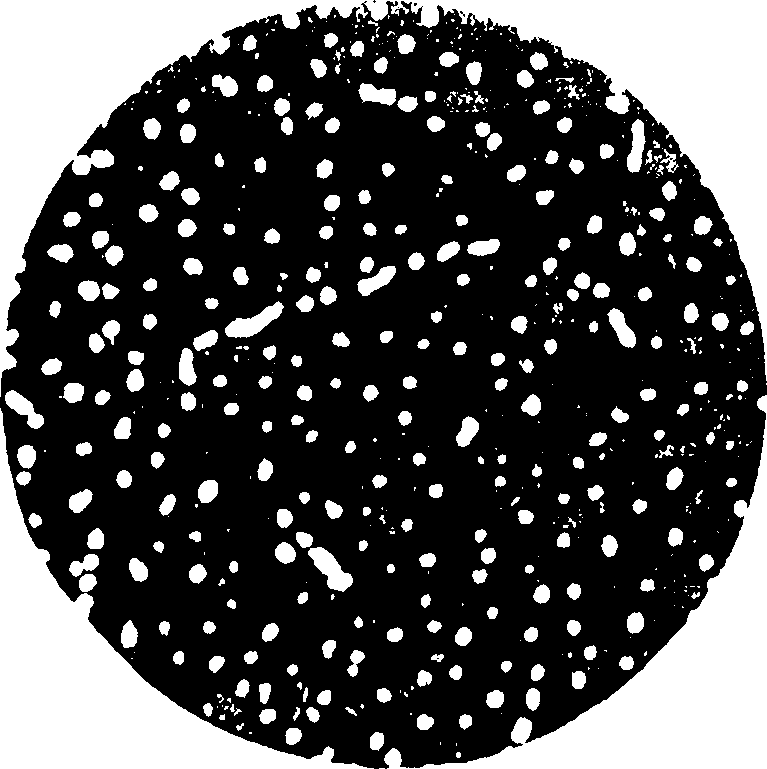
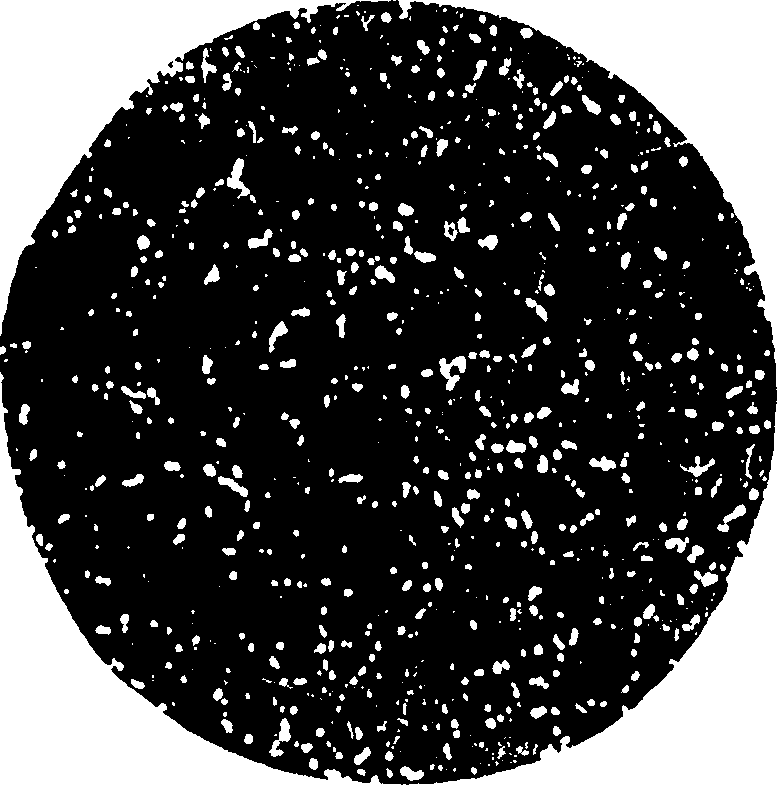
Балл 3
С. 44 ГОСТ 5950-73
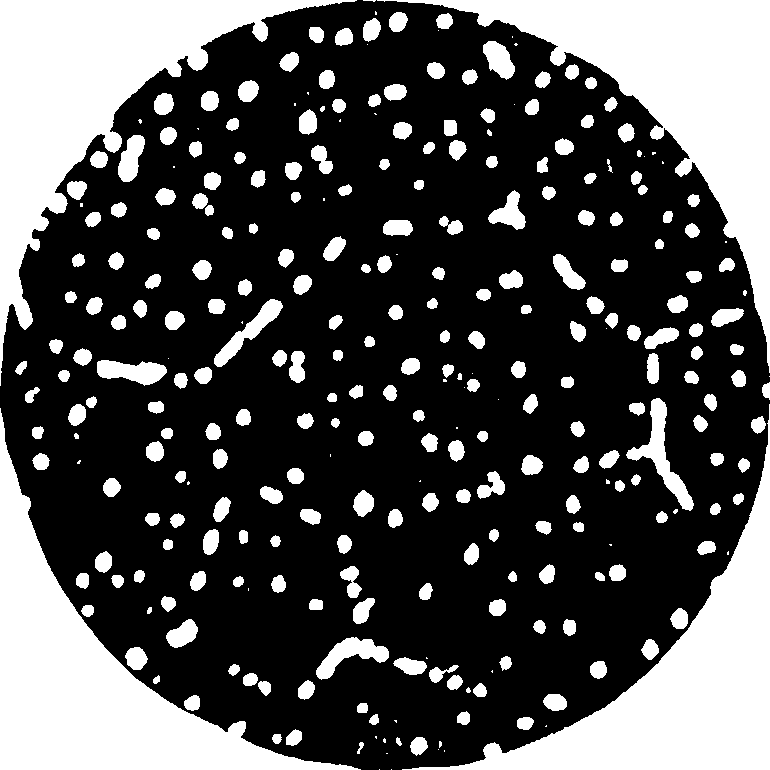
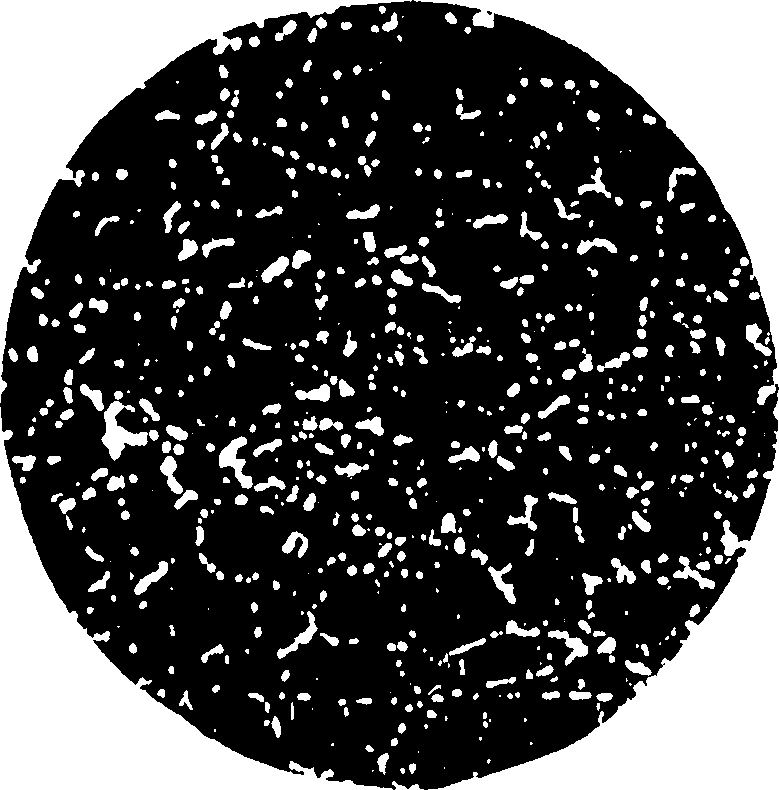
Балл Б
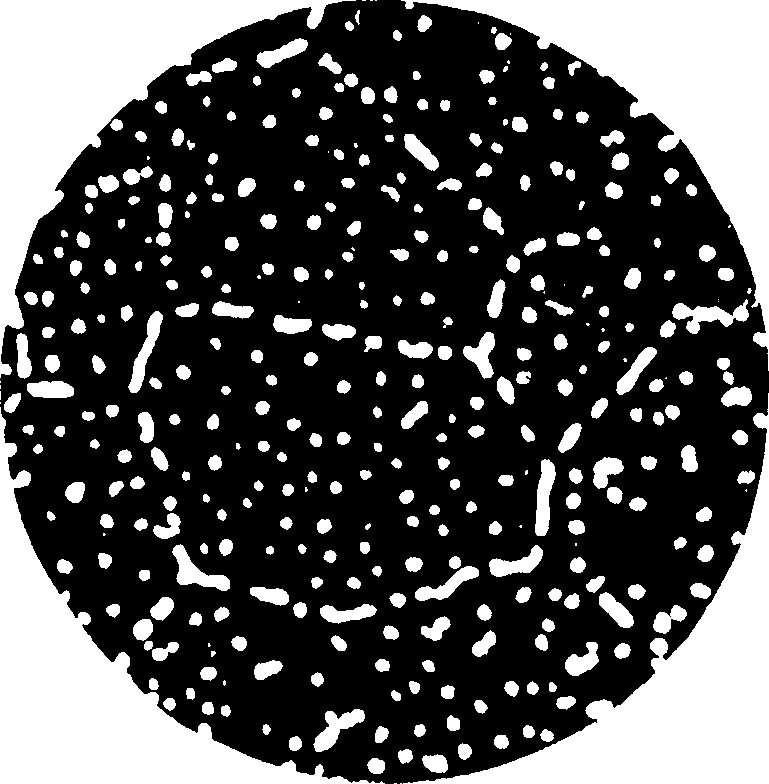

Балл 5
С. 4 6 ГОСТ 5950-73
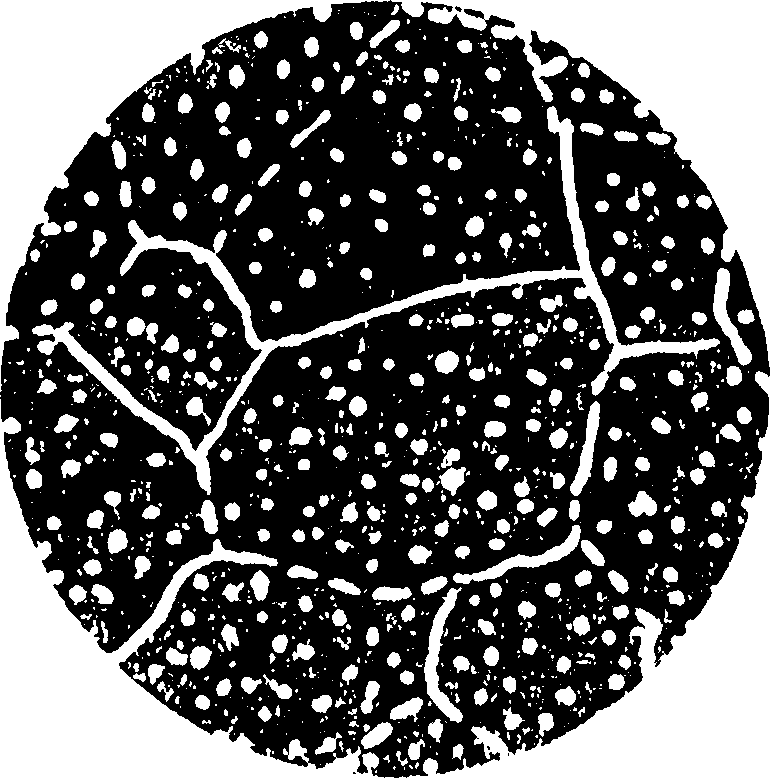
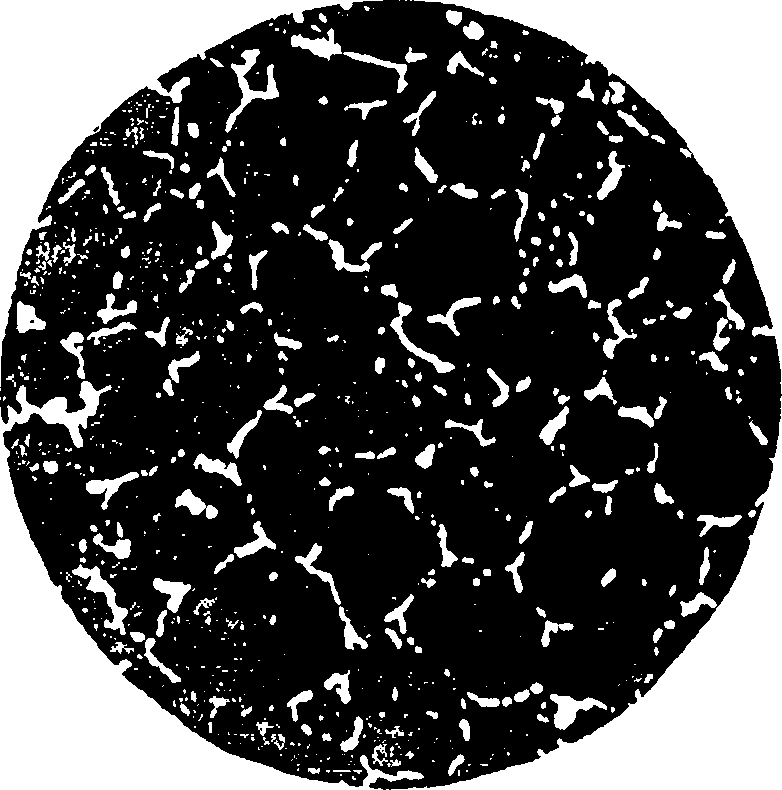
Балл 6
ПРИЛОЖЕНИЕ 36
Обязательное
ШКАЛА № 5 ДЛЯ ОЦЕНКИ ВЕЛИЧИНЫ ЗЕРНА АУСТЕНИТА ИНСТРУМЕНТАЛЬНОЙ ЛЕГИРОВАННОЙ СТАЛИ ПО ИЗЛОМУ

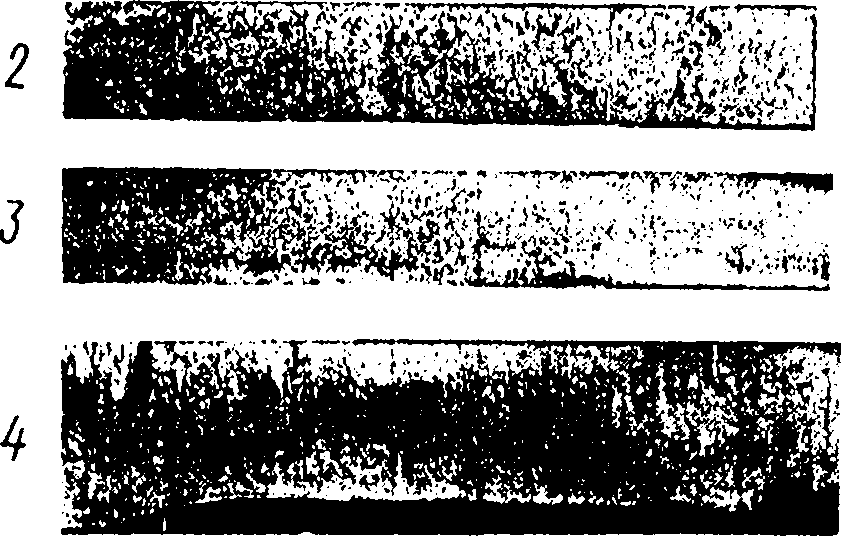

Описание шкалы № 5 для оценки по излому величины зерна аустенита инструментальной легированной стали
Номер зерна | Вид излома |
1 | Крупнозернистый с блестящими четко различимыми зернами |
2 | Среднезернистый с блестящими четко различимыми зернами |
3 | Среднезернистый с матовыми нечетко различимыми зернами |
4 | Мелкозернистый с матовыми почти неразличимыми зернами |
5 | Очень мелкозернистый матовый с неразличимыми зернами |
С. 48 ГОСТ 5950—73
ПРИЛОЖЕНИЕ 4 Обязательное
МЕТОДИКА КОНТРОЛЯ МИКРОСТРУКТУРЫ ИНСТРУМЕНТАЛЬНОЙ ЛЕГИРОВАННОЙ СТАЛИ
1. Схема отбора образцов, их форма и размер приведены в таблице
Схема вырезки образца из прутка
Расположение плоскости шлифа к направлению вытяжки при прокатке или ковке
Размер стали, мм
Контролируемая структура
Поперек
Вдоль
Поперек
До 25
До 40
От 26 до 40
Зернистый перлит, карбидная сетка, зерно аустенита
Карбидная неоднородность
Зернистый перлит, карбидная сетка, зерно аустенита
Продолжение
Номера чертежей | Схема вырезки образца из прутка | Расположение плоскости шлифа к направлению вытяжки при прокатке или ковке | Размер стали, мм | Контролируемая структура |
4 | Поперек | От 40 | Зернистый | |
до 50 | перлит, кар- | |||
бидная сетка, | ||||
зерно аустени- | ||||
R | та | |||
5 | Вдоль | От 40 | Карбид- | |
» '</ V4 | до 50 | пая неодно- | ||
■'Ж | родность | |||
R | ||||
6 | \V | Поперек | От 50 | Зернистый |
и выше | перлит, кар* | |||
1 Г1 I | бидная сетка. | |||
j vz 1 | зерно аустени- | |||
г j?X| | та | |||
7 | Вдоль | От 50 | Карбид- | |
T _£-Т ***~ | и выше | ная неодно- | ||
3 1 | | родность | |||
1 1 п 2oJ 1 | ||||
(«2Х-1 |
С. 50 ГОСТ 5950—73
Примечания:
1. Темплет для образца вырезают на расстоянии не менее 20 мм от торца прутка.
2. Плоскости шлифов на чертежах заштрихованы.
(Измененная редакция, Изм. №1).
2. Контроль микроструктуры отожженной стали (зернистого перлита, карбидной сетки) и закаленной стали (зерно аустенита) должен производиться на шлифах, плоскость которых перпендикулярна направлению вытяжки при прокатке и ковке.
Рекомендуемые размеры плоскости шлифа для контроля микроструктуры прутков круглого сечения должны быть следующими:
а) для стали диаметром до 25 мм — полная плоскость поперечного сечения прутка (черт. 1):
б) для стали диаметром от 26 до 40 мм — половина плоскости поперечного сечения прутка (черт. 3);
в) для стали диаметром от 40 до 50 мм — четверть плоскосги поперечного сечения прутка (черт. 4);
г) для стали диаметром от 50 мм и выше плоскость сечения шлифа должна соответствовать черт. 6.
(Измененная редакция, Изм. № 1).
3. Карбидную неоднородность в зависимости от формы поперечного сечения следует контролировать:
круг — по середине радиуса;
квадрат “ на расстоянии 0,25 стороны квадрата от середины стороны; полосу — на расстоянии 0,25 толщины от середины широкой стороны. (Измененная редакция, Изм. № 5).
4. Образцы для контроля кароидной сетки и карбидной неоднородности подвергают закалке от температур, указанных в п. 3.11 настоящего стандарта и приложения 5 для стали данной марки.
5. Допускаются:
а) контроль карбидной неоднородности стали марок Х12, Х12ВМФ, Х12МФ, Х12Ф1 на образцах после закалки и отпуска при температуре 400°C, а также на образцах после отжига;
б) контроль карбидной сетки на продольных шлифах.
В арбитражных случаях контроль должен производиться только на поперечных шлифах.
(Измененная редакция, Изм. № 3).
6. Образцы шлифуют и полируют обычными методами, принятыми на предприятиях при изготовлении микрошлифов.
Образцы для контроля величины зерна аустенита перед проведением закалки должны быть отполированы, а после закалки подвергнуты легкой переполировке.
(Измененная редакция, Изм. № 2).
7. Травление шлифов производят 4%-ным раствором азотной кислоты в этиловом спирте.
При контроле карбидной неоднородности стали марок Х12, Х12ВМФ, Х12МФ, Х12Ф1 на отожженных образцах рекомендуется применять электролитическое травление шлифов 'в 10%-ном водном растворе щавелевой кислоты (режим травления: плотность тока 40 А/дм2, время травления 30—40 с).
8. Оценку зернистого перлита производят при увеличении 500х по прилагаемой десятибалльной шкале № 1 эталонов микроструктур (см. обязательное приложение 1).
Оценку карбидной сетки производят при увеличении 500х по шестибалльной шкале N* 4.
Оценку карбидной неоднородности производят при увеличении 100х стали марок Х12, Х12ВМФ, Х12МФ, Х12Ф1 — по шкале № 2 (см. обязательное приложение 2);
стали марок ХВ4Ф, 9Х5ВФ, 8Х6НФТ, 8Х4В2МФС2, Х6ВФ, 6Х6ВЗМФС, 11Х4В2МФЗС2, 6Х4М2ФС — по шкале № 3 (обязательное приложение 3).
7.8. (Измененная редакция, Изм №3).
9. Увеличение, при котором оценивается микроструктура, является рекомендуемым. В зависимости от увеличений микроскопа допускается контролировать зернистый перлит и карбидную сетку при увеличении 450т-600х , карбидную неоднородность — при увсличении>90—125\
10. Оценка микроструктуры (зернистый перлит, карбидная сетка, карбидная неоднородность, зерно аустенита) производится по участку шлифа с наихудшей структурой, причем для стали размером до 25 мм просматривается вся плоскость шлифа, для стали больших размеров — поле шлифа на половине радиуса ± 5 мм
Примечали е.Наличие структуры пластинчатого перлита вследствие обеднения углеродом поверхностного слоя стали, отожженной на зернистый перлит, к оценке микроструктуры не относится, а принимается во внимание только при оценке обезуглероженного слоя.
(Измененная редакция, Изм № 1).
ПРИЛОЖЕНИЕ 5
Справочное
ТВЕРДОСТЬ ОБРАЗЦОВ РАЗЛИЧНЫХ МАРОК СТАЛИ
ПОСЛЕ ЗАКАЛКИ
Марка стали | Температура, °С1и среда закалки образцов | Твердость HRC3(HRC), нс менее |
ЗХФ | 800- 820, вода 830—860, масло | 59(58) 59 (58) |
9ХФ | 810—830, вода 850—880, масло | 59 (58) 61 (60) |
13Х | 820--840, вода 780—810, вода | 61 (60) 65 (64) |
ХВ4Ф | 800—820, вода | 66 (65) |
В2Ф | 800—350, вода | 63 (62) |
X | 840—860, масло | 63 (62) |
хвг | 830—850, масло | 63 (62) |
0Х5ВФ | 950—1000, масло | 59 (58) |
ЗХ6НФТ | 950—1000, масло | 59 (58) |
9Г2Ф | 730—800, масло | 61 (60) |
Х63Ф | 980—1000, масло | 62 (61) |
XI2 | 950—1000, масло | 61 (60) |
Х.12ВМФ | 1020—1040, масло | 61 (60) |
Х12МФ | 950—1000, масло | 61 (60) |
Х12Ф1 | 1050—1100, масло | 61 (60) |
отйгмф | 840-880, воздух | 59 (58) |
1055—1075, масло | 61 (60) | |
■6Х41У12ФС | | 1050—1070, масло | 60 (59) |
С. 52 ГОСТ 5950-73
Продолжение
Марка стали | Температура,0 С ,и среда закалки образцов | Твердость HRCj(HRC), не менее |
11Х4В2МФЗС2 | 1000—1030, масло | 63 (62) |
8Х4В2МФС2 | 1060—1090, масло | 61 (60) |
7X3 | 850—880, масло | 55 (54) |
8X3 | 850—880, масло | 56 (55) |
5ХНМ | 830—860, масло | 57 (56) |
5ХНВ | 840—860, масло | 57 (56) |
5ХНВС | 860—880, масло | 57 (56) |
4ХМФС | 920—930, масло | 56 (55) |
4Х5В2ФС | 1030—1050, масло или воздух | 51 (50) |
4Х5МФС | 1000—1020, масло | 51 (50) |
4Х.5МФ1С | 1020—1040, масло | 51 (50) |
4ХЗВМФ | 1040—1060, масло | 53 (52) |
4Х4ВМФС | 1050—1070, масло | 56 (55) |
ЗХЗМЗФ | 1030—1050, масло | 48 (47) |
4Х2В5МФ | 1060—1080, масло | 51 (50) |
5ХЗВЗМФС | 1120—1140, масло | 54 (53) |
4ХС | 880—900, масло | 48 (47) |
6ХС | 840—860, масло | 57 (56) |
5ХВ2СФ | 860—900, масло | 56 (55) |
6ХВ2С | 860—900, масло | 58 (57) |
6ХЗМФС | 980—1020, масло | 57 (56) |
6ХВГ | 850—900, масло | 58 (57) |
5Х2МНФ | 960—980, масло | 57 (56) |
(Измененная редакция* Изм № 2* 3» 5).
ПРИЛОЖЕНИЕ 6
Справочное
ПРИМЕРНОЕ НАЗНАЧЕНИЕ ИНСТРУМЕНТАЛЬНОЙ ЛЕГИРОВАННОЙ
СТАЛИ РАЗЛИЧНЫХ МАРОК
Марки стали
8ХФ
9ХФ
11ХФ
13Х
ХВ4Ф
В2Ф
9X1
X
12X1
9ХС
ХГС
хвг
9ХВГ
ХВСГФ
Область применения
Для штемпелей при холодной работе; ножей при холодной резке металла, обрезных матриц и пуансонов при холодной обрезке заусенцев, кернеров
Для рамных, ленточных круглых строгальных пил; штемпелей при холодной работе; ножей при холодной резке металла; обрезных матриц и пуансонов при холодной обрезке заусенцев; кернеров
Для метчиков и другого режущего инструмента диамет-рбм до 30 мм, закаливаемого с охлаждением в горячих средах
Для бритвенных ножей и лезвий, острого хирургического инструмента, шаберов, гравировального инструмента
Для резцов и фрез при обработке с небольшой скоростью резания твердых металлов (валки с закаленной поверхностью); гравировальных резцов при очень напряженной работе И т. д.
Для ленточных пил по металлу и ножовочных полотен
Для валков холодной прокатки, дрессировочных валков, клейм, пробойников, холодновысадочных матриц и пуансонов; деревообрабатывающего инструмента
Для зубил, применяемых при насечке напильников; очень твердых кулачков эксцентриков и пальцев; гладких цилиндрических калибров и калиберных колец; токарных, строгальных и долбежных резцов в лекальных и ремонтных мастерских
Для измерительного инструмента (плиток, калибров, шаблонов)
Для сверл, разверток, метчиков, плашек, гребенок, фрез, машинных штемпелей, клейм для холодных работ
Для валков холодной прокатки, холодновысадочных матриц и пуансонов, вырубных штампов небольших размеров (диаметром или толщиной до 70 мм). Сталь марки ХГС не может заменить сталь марок ХВГ, 9ХС, ХВСГФ при изготовлении режущих инструментов
Для измерительных и режущих инструментов, для которых повышенное коробление при закалке недопустимо; резьбовых калибров, протяжек, длинных метчиков, длинных разверток, плашек и другого вида специального инструмента, холодновысадочньпс матриц и пуансонов, технологической оснастки
Для резьбовых калибров, лекал сложной формы, сложных весьма точных штампов для холодных работ, которые при закалке не должны подвергаться значительным объемным изменениям и короблению.
Для круглых плашек, разверток и другого режущего инструмента
Продолжение
9Г2Ф
8Х6НФТ, 9Х5ВФ
Х6ВФ
Х12, Х12ВМФ
Х12МФ, Х12Ф1
Для режущего и штамповочного инструмента (плашек, метчиков, ножей, для ножниц, измерительного инструмента, штампов для прессования резины и пластмасс).
Для ножей, применяемых для фрезерования древесины, строгальных пил и других деревообрабатывающих инструментов подобного типа (например, цельных фрез и т. п.).
Для резьбонакатного инструмента (роликов и плашек), ручных ножовочных полотен, бритв, матриц, пуансонов, зубонакатников и других инструментов, предназначенных для холодной деформации, для дереворежущего фрезерного инструмента
Для холодных штампов высокой устойчивости против истирания (преимущественно с рабочей частью округлой формы), не подвергающихся» сильным ударам и толчкам; для волочильных досок и волок, глазков для калибрования пруткового металла под накатку резьбы, гибочных и формовочных штампов, сложных секций кузовных штампов, которые при закалке не должны подвергаться значительным объемным изменениям и короблению; матриц и пуансонов вырубных и просечных штампов; штамповки активной части электрических машин и электромагнитных систем электрических аппаратов
То же, что и для марки Х12, но когда требуется большая вязкость; для профилировочных роликов сложных форм; секций кузовных штампов сложных форм; сложных дыропрошивочных матриц при формовке листового металла, эталонных шестерен, накатных плашек, волок; матриц и пуансонов вырубных просечных штампов (в том числе совмещенных и последовательных) со сложной конфигурацией рабочих частей; штамповки активной части электрических машин
7ХГ2ВМФ
6Х6ВЗМФС (ЭП569)
Для штампов объемного холодного деформирования и вырубного инструмента сложной конфигурации, используемых при производстве изделий из цветных сплавов и малопрочных конструкционных сталей
Для резьбонакатных роликов, зубонакатников, шлице-накатников,обрезных матриц, пуансонов и других инструментов предназначенных для холодной пластической деформации металлов повышенной твердости; ножей труборазрубочных машин, ножей гильотинных ножниц, применительно к резке высокопрочных сталей и сплавов, рубильных ножей, применяемых в деревообрабатывающей промышленности; шарошек, разрушающих горные породы, и других аналогич-; ных инструментов
7X3, 8X3 ! Для инструмента (пуансонов, матриц) горячей высадки крепежа и заготовок из углеродистых и низколегированных | конструкционных сталей на горизонтальноковочных манш-i нах; деталей штампов (матриц, пуансонов, выталкивателей) ! для горячего прессования и выдавливания этих материалов на ' кривошипных прессах при мелкосерийном производстве; ги-I бочных, обрезных и просечных штампов
Продолжение
5ХНМ
5ХНВ, 5ХНВС 4ХМФС
4Х5МФС
4Х5В2ФС, 4Х5МФ1С
4ХЗВМФ
4Х4ВМФС
ЗХЗМЗФ
4Х2В5МФ
5ХЗВЗМФС
Для молотовых штампов паровоздушных и пневматических молотов с массой падающих частей свыше 3 т; прессовых штампов и штампов машинной скоростной штамповки при горячем деформировании легких цветных сплавов; блоков матриц для вставок горизонтальных машин
Для молотовых штампов паровоздушных и пневматических молотов с массой падающих частей до 3 т
Для молотовых штампов паровоздушных и пневматических молотов с массой падающих частей до 3 т при деформации легированных конструкционных и нержавеющих сталей (вместо менее теплостойких сталей марок 5ХНМ, 5ХНВ); прессового инструмента для обработки алюминиевых сплавов
Для мелких молотовых штампов; крупных (толщиной или диаметром более 200 мм) молотовых и прессовых вставок при горячем деформировании конструкционных сталей и цветных сплавов в условиях крупносерийного массового производства
Для пресс-форм литья под давлением цинковых, алюминиевых и магниевых сплавов; молотовых и прессовых вставок (толщиной или диаметром до 200—250 мм) при горячем деформировании конструкционных сталей; инструмента для высадки заготовок из легированных конструкционных и жаропрочных материалов на горизонтально-ковочных машинах
Для мелких молотовых штампов; молотовых и прессовых вставок, (толщиной или диаметром до 300—400 мм), инструмента горизонтально-ковочных машин при горячем деформировании конструкционных и жаропрочных сталей; инструмента для высокоскоростной машинной штамповки конструкционных сталей
Для инструмента высокоскоростной машинной штамповки, высадки на горизонтально-ковочных машинах; вставок штампов для горячего деформирования легированных конструкционных сталей и жаропрочных сплавов на молотах и кривошипных прессах (вместо менее теплостойких сталей марок 4Х5В2ФС, 4Х5МФ1С, 4ХЗВМФ); пресс-форм литья под давлением медных сплавов
Для инструмента горячего деформирования на кривошипных прессах и горизонтально-ковочных машинах, подвергающихся в процессе работы интенсивному охлаждению (как правило для мелкого инструмента); пресс-форм литья под давлением медных сплавов
Для тяжелонагруженного прессового инструмента (мелких вставок окончательного штампового ручья, мелких вста-ных знаков, матриц и пуансонов для выдавливания и т. п.) при горячем деформировании легированных конструкционных сталей и жаропрочных сплавов
Для тяжелонагруженного прессового инструмента (прошивных и формирующих пуансонов, матриц и т. п.); инстру-
Продолжение
мента для высадки на горизонтально-ковочных машинах и вставок штампов напряженных конструкций, для горячего объемного деформирования конструкционных сталей и жаропрочных металлов и сплавов (вместо менее теплостойких сталей марок ЗХ2В8Ф и 4Х2В5МФ). Наиболее высокие про-каливаемость и теплостойкость имеег сталь марки 5ХЗВЗМФС 4ХС Для зубил, обжимок, ножниц при горячей и холодной
резке металла; штампов горячей вытяжки
6ХС Для пневматических зубил и штампов небольших разме
ров для холодной штамповки; рубильных ножей
5ХВ2СФ, Для ножей при холодной резке металла, для резьбона-6ХВ2С катных плашек, пуансонов и обжимных матриц при холодной работе; деревообделочных инструментов при длительной работе
6ХВГ Для пуансонов сложной формы при холодной прошивке
преимущественно фигурных отверстий в листовом и полосовом материале; небольших штампов для горячей штамповки, главным образом, когда требуется минимальное изменение размеров при закалке
5Х2МНФ Крупногабаритные цельные штампы (со стороной квадрата или диаметром до 600 мм) для штамповки поковок из конструкционных сталей и жаропрочных сплавов на молотах и кривошипных прссрах (вместо менее теплостойких сталей 5ХНМ, 4ХМФС); инструменты (зажимные и формующие вставки, наборные и формовочные пуансоны) для высадки конструкционных сталей и жаропрочных сплавов на горизонтально-ковочных машинах (ГКМ); ножи горячей резки 8Х4В2МФС2 Матрицы и пуансоны штампов холодного объемного де* (ЭП761) формирования, испытывающие в процессе эксплуатации давление до 2300 МПа, резьбонакатные ролики
11Х4В2МФЗС2 Вырубные штампы, в том числе для обработки холодно-(ДИ37) катаных электротехнических сталей Э412 иЭ413 с покрытиями типа "карлит”; пуансоны и матрицы холодновысадочных автоматов; пуансоны и выталкиватели для холодного выдавливания, эксплуатируемые с удельными давлениями до 2000 МПа в условиях повышенного износа и нагрева рабочих поверхностей до 400 °C; шлице и резьбонакатной инструмент
6Х4М2ФС Вырубной и высадочный инструмент (штампы, пуансоны, (ДИ55) пневматические зубила и др.), накатной инструмент
9ХФМ Дисковые и рамные деревообрабатывающие пилы
6ХЗМФС Пуансоны, работающие с повышенными динамическими
нагрузками; холодновысадочные штампы, штемпели, клейма, чеканочные штампы и некоторые слесарно-монтажные инструменты (взамен сталей марок 7X3 и 6ХВ2С)
05Х12Н6Д Для изготовления инструмента, формообразующих дета-2МФСГТ лей пресс-форм формования резинотехнических и пластмас-(ДИ80) совых изделий
(Измененная редакция, Изм. № 2. 3, 5).
ПРИЛОЖЕНИЕ 7
Справочное
КРИВЫЕ ЗАВИСИМОСТИ ТВЕРДОСТИ ПО РОКВЕЛЛУ (IIRC) ОТ ТЕМПЕРАТУРЫ ОТПУСКА
Твердость, НРС Твердость, НРС
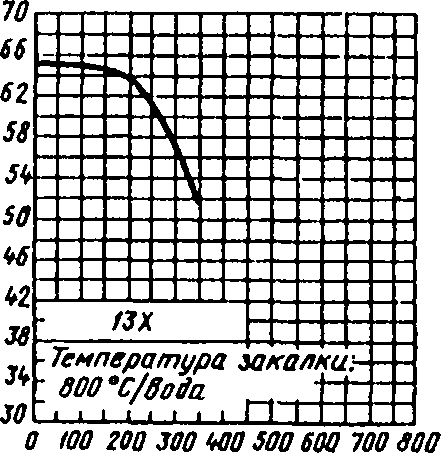
Температура отпуска,°C
Черт. 1
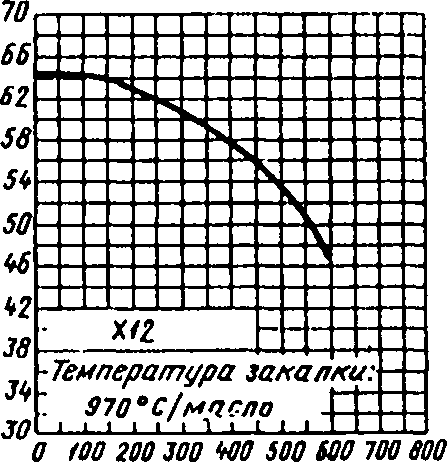
Температура отпуска, вС
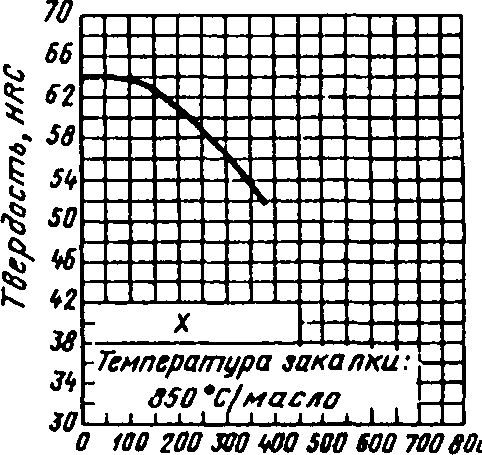
Температура отпуска, °C
Черт. 2
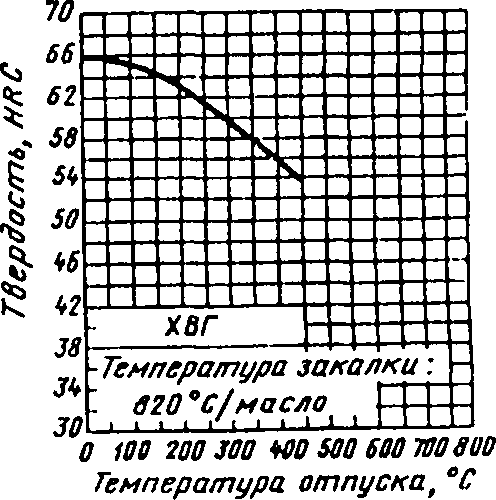
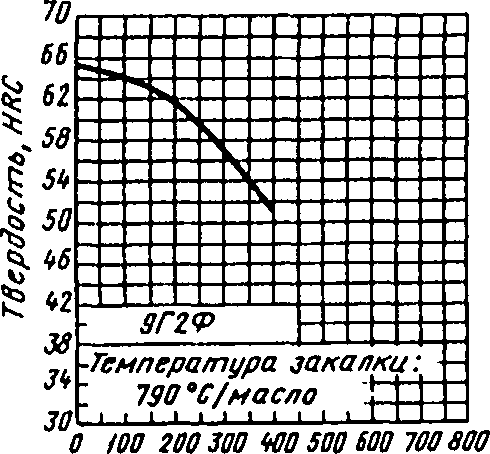
Температура отпуска, °C
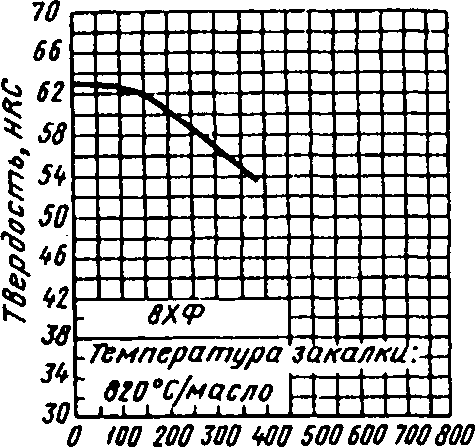
Температура отпуска, *С
Черт. 5
Черт. 6
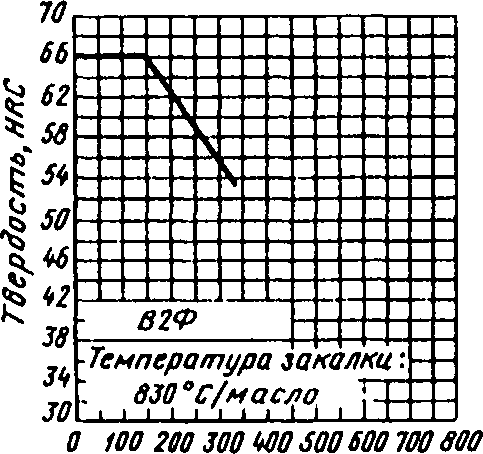
Температура отпуска, 9С
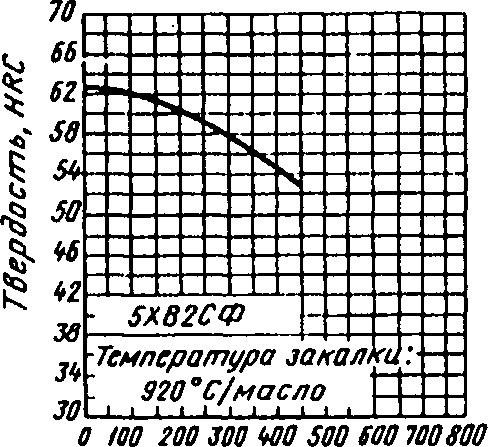
Температура отпуска, °C
Черт. 7
Черт. 8
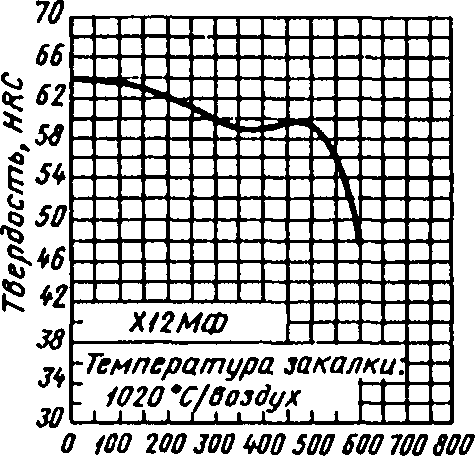
Температура отпуска, °C
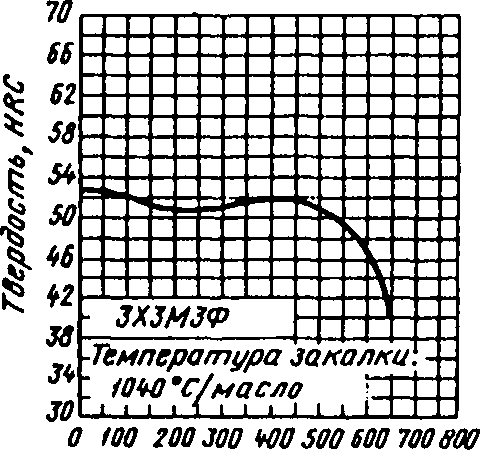
Температура отпуска, °C
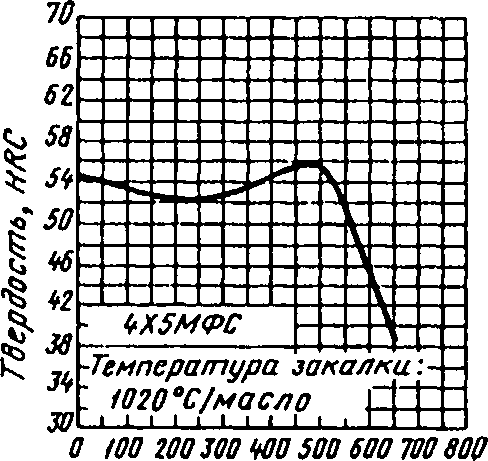
Температура отпуска, °C
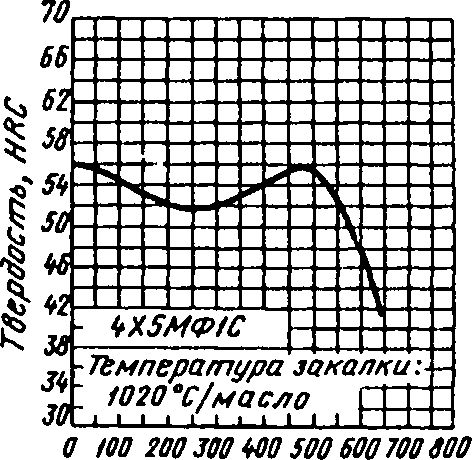
Температура отпуска, ЛС
Черт. 11
Черт. 12

0 100 200 300 4)0 S00 600700 800

Температура отпуска,°С
Температура отпуска, аС
Черт. 13
Черт.14
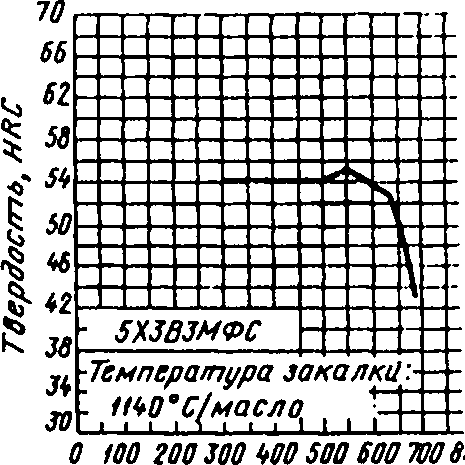
Температура отпуска, 0С
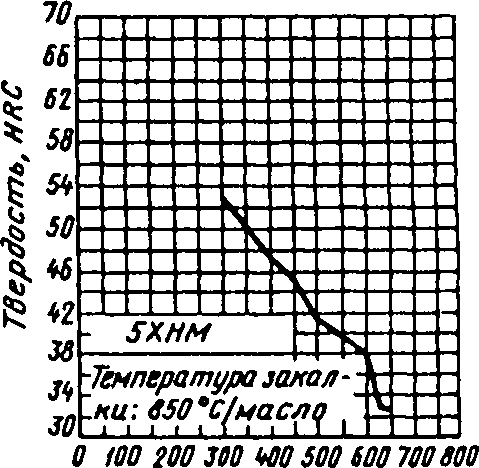
Температура отпуска, 9С
Черт. 16
Черт. 15
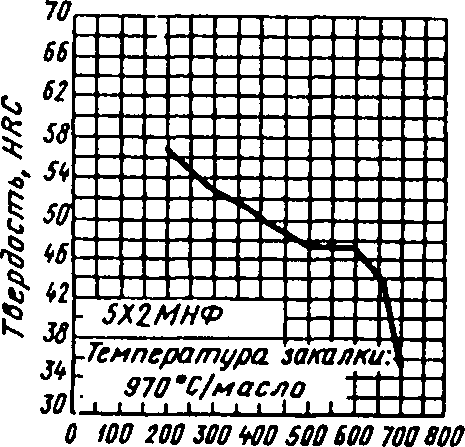
Температура отпуска, 9С

о ЮО 200 300 400 300 600 200 000 Температура отпуска t •С
Черт. 17
Черт. 18
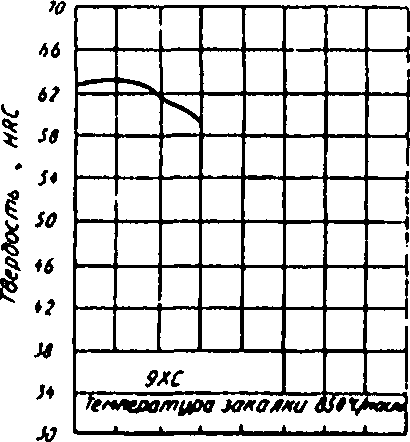
О 190 200300 400 500 600 ТОО W Температура отпуска , 9 С
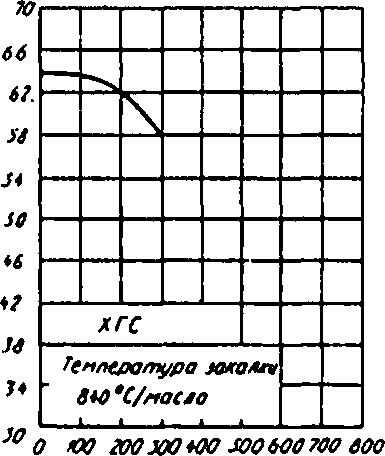
Температура отпуска. 9 С
Черт. 19
Черт. 20
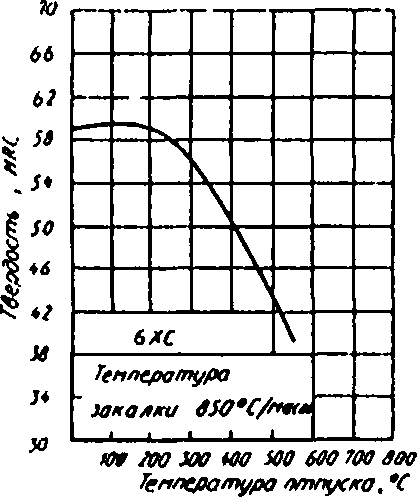
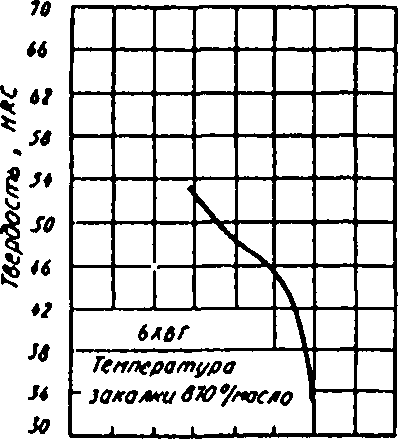
О Ю0 200 300 400 500600ХЮ ООО Температура отпуска. 9С
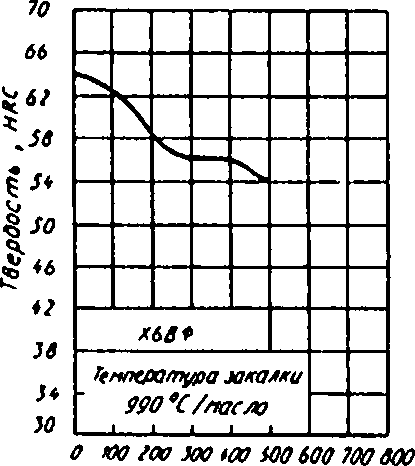
Температура отпуска. *С
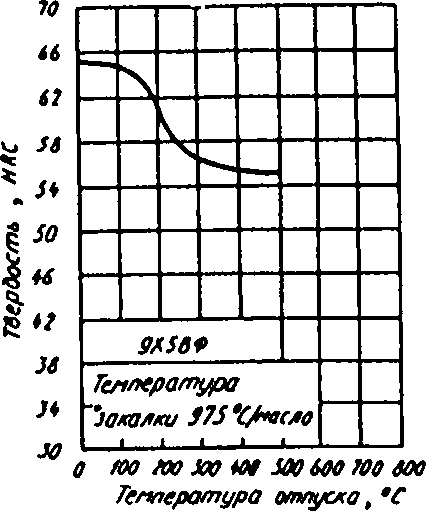
Jo
зз
Черт. 23
Черт. 24
70
66
53
36
62
- 34
'■Х | |||||||
8Х462МОС2 | |||||||
Температура закалки ГОЗО 9С/масло ± t 1.1. | |||||||
О МО 200300 400 500600 7ОО ООО
Температура отпуска, 9С
Черт. 25
66
62
34
30
• 36
I 5*
К 46
6X66JHOC | |||||||
Температура закалки Ю309С/мосло 1» ■ ■ ■ | |||||||
О Г00 200 300 600300000 700 600 Ьлпературо отпуска t 9(

Черт. 26
К | К | ||||||
т | |||||||
11A482H0JC2 | |||||||
Твмпературо за колки Ю139С/масло 1 1 111, |
О 700 300 300 400300600 ТООооО Температура отпуска»*
•о
SO
50
$
4}
34
30
ы
62
6А4М2ОС | |||||||
Температура лаколкц | |||||||
7060 *С/мосло 1 1 11 |
О ЮО МО 300*00500600700400 Температура отпуска, Ч
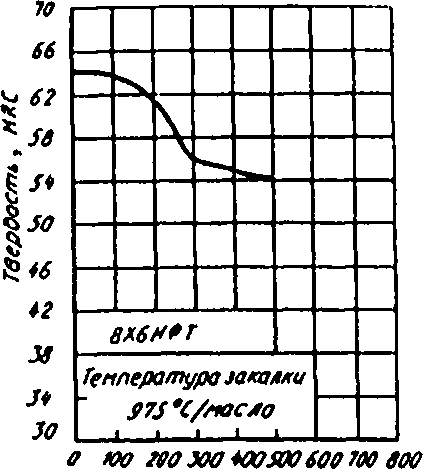
Температура отпуска, К
Черт. 29
Черт. 30
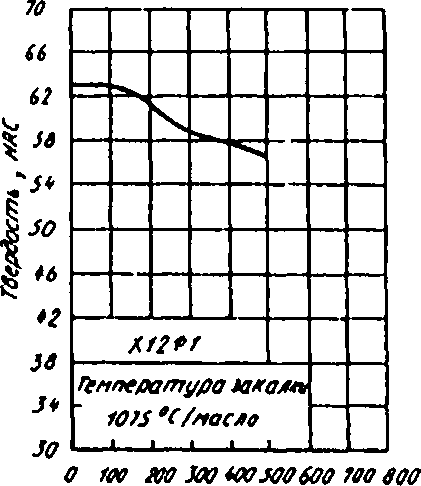
Температура отпуска, Ч
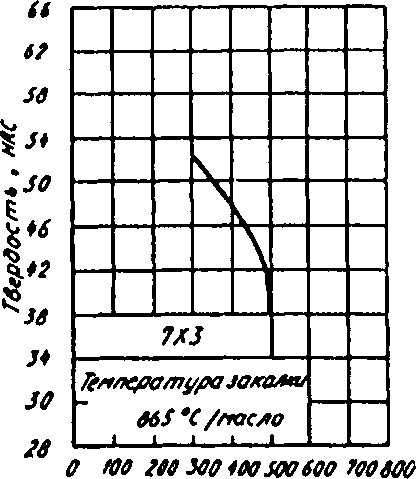
Черт. 31
Температура отпуска, *С
Черт. 32
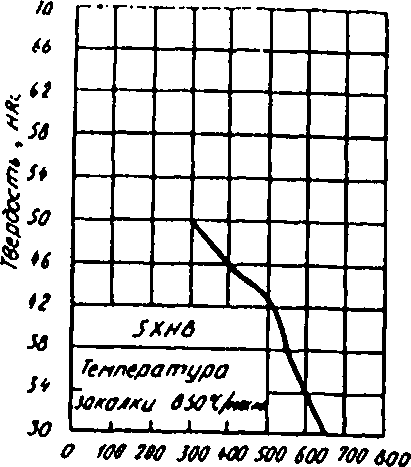
Температура отпуска, *с
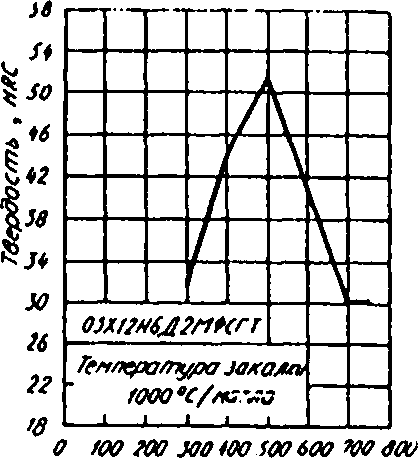
Температура отпуска, ч
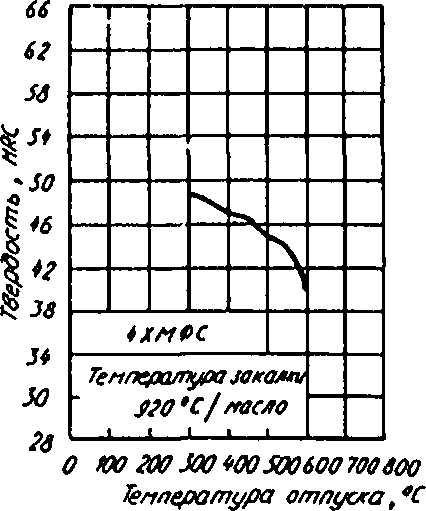
Черт. 35
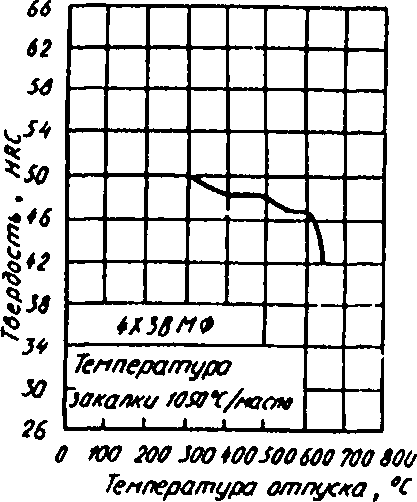
Черт. 36
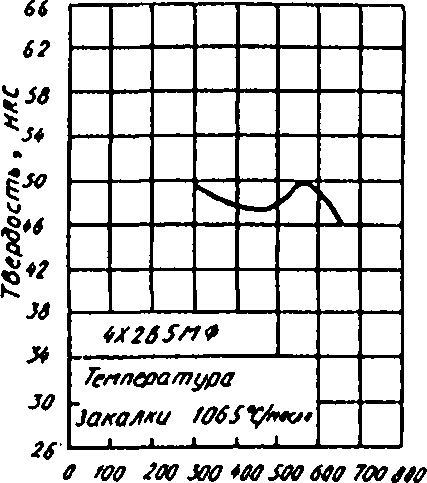
Температура отпуска, *С
Черт. 3*7
(Измененная редакция, Изм №5).
ИНФОРМАЦИОННЫЕ ДАННЫЕ
!♦ РАЗРАБОТАН И ВНЕСЕН Министерством черной металлургии СССР
РАЗРАБОТЧИКИ
jjL К. Петров, канд. техн, наук; Г. И. Капланов, канд. техн, наук; Л. А. Позняк, канд. техн, наук; Н. В. Стеценко, канд. техн, наук; С. И. Тишаев, канд. техн, наук; О. А. Распопина; А. И. СеребрянскаяГ|Р- А. Зыкова, канд. техн, наук; П. М. Геращенко, канд. техн. наук.
2. УТВЕРЖДЕН И ВВЕДЕН В ДЕЙСТВИЕ Постановлением Государственного комитета стандартов Совета Министров СССР от 10.12.73 № 2680
3. ВЗАМЕН ГОСТ 5950- 63
4. Стандарт полностью соответствует СТ СЭВ 3895-82
5. ССЫЛОЧНЫЕ НОРМАТИВНО-ТЕХНИЧЕСКИЕ ДОКУМЕНТЫ
Обозначение НТД, на который дана ссылка
Номер пункта
ГОСТ 1051-73
3.7, 6.2
ГОСТ 1133-71
2.2
ГОСТ 1763-68
5.3
ГОСТ 2590-88
2.2
ГОСТ 2591-88
2.2
ГОСТ 4405-75
2.2
ГОСТ 5639-82
5.6
ГОСТ 7417-75
2.2, 3.3
ГОСТ 7565-81
5.1
ГОСТ 7566-81
4.1,4.11,6.1,6.2,6.3
ГОСТ 8233-56
3.14
ГОСТ 8559-75
2.2, 3.3
ГОСТ 8560-78
2.2, 3.3
ГОСТ 9012-59
5.8
ГОСТ 9013-59
5.9
ГОСТ 10243-75
5.6, 5.7
ГОСТ 12344-88
5.1
ГОСТ 12345—88
5.1
ГОСТ 12346-78
5.1
ГОСТ 12347-77
5.1
ГОСТ 12348-78
5.1
Продолжение
Обозначение НТД, на который дана ссылка
Номер пункта
ГОСТ 12349-83
5.1
ГОСТ 12350-78
5.1
ГОСТ 12351-81
5.1
ГОСТ 12352-81
5.1
ГОСТ 12354-81
5.1
ГОСТ 12355-78
5.1
ГОСТ 12356-81
5.1
ГОСТ 12359-81
5.1
ГОСТ 12360-82
5.1
ГОСТ 12361-82
5.1
ГОСТ 12364-84
5.1
ГОСТ 12365-84
5.1
ГОСТ 14955-77
2.2, 3.7, 6.2
ГОСТ 28473-90
5.1
6. Срок действия продлен до 01.07.96 Постановлением Госстандарта СССР от 29.12.90 № 3691
7. Переиздание (март 1991 г.) с Изменениями № 1, 2, 3,4, 5, утвержденными в декабре 1977 г., октябре 1983 г., июне 1986 г., ноябре 1987 г., декабре 1990 г. (ИУС 2—78, 2—84, 9—86, 2-88,5-91).
Редактор И. В. Виноградская Технический редактор О.Ю. Захарова Корректор А.В. Прокофьева Оператор Е.Н. Мартемьянова
Сдано в набор 20.03.91. Подписано в печать 23.05.91. Формат 60X90V16* Бумага ТИП. № 1 4,0 усл. п. л., 4,12 усл. кр.-отт., 4,04 уч.-изд. л. Тираж 23000 экз.
Зак. 18^2 Цена 1р. 60 к.
Ордена ’’Знак Почета” Издательство стандартов, 123840, Москва, ГСП, Новопрссненский пер., 3
Набрано в Издательстве стандартов на НПУ Калужская типография стандартов, ул. Московская, 256