Группа Ж15 ГОСУДАРСТВЕННЫЙ СТАНДАРТ СОЮЗ А ССР
МАСТИКА ПОЛИИЗОБУТИЛЕНОВАЯ
ГОСТ
14791—69
СТРОИТЕЛЬНАЯ УМС-50
Polyisobutelene building mastic—UMS-50
Постановлением Государственного комитета Совета Министров СССР по делам строительства от 23/VI 1969 г. № 72 срок введения установлен
с 1/VII 1970 г.
Несоблгодение стандарта преследуется по закону
Настоящий стандарт распространяется на полиизобутиленовую строительную мастику УМС-50, представляющую собой густовязкую однородную нетвердеющую массу, изготовляемую из высокомолекулярного полиизобутилена, нейтрального минерального масла и тонкоизмельченного наполнителя (мел, мрамор, известняк) и способную сохранять свои физико-механические свойства при температуре от минус 50°С до плюс 70°С.
Мастика предназначается для уплотнения стыков конструкций крупнопанельных зданий с целью их герметизации.
Издание официальное
Перепечатка воспрещена
1. ТЕХНИЧЕСКИЕ ТРЕБОВАНИЯ
1.1. Мастика должна соответствовать требованиям, указанным
в табл. 1. | Таблица 1 |
Наименование показателей | Нормы |
| От светло-серого до коричневого 0,07 10 0,8 4 70 |
ГОСТ 14791—69
1.2. Для изготовления мастики должен применяться высокомолекулярный полиизобутилен <марок П-118, П-118Н, П-155, П-155Н, П-200 и П-200Н, соответствующий требованиям ГОСТ 13303—67.
1.3. Минеральное нейтральное масло, применяемое для изготовления мастики, должно обладать:
кинематической вязкостью при температуре 50°С в пределах 30—50 сСт;
температурой вспышки не ниже 180°С;
температурой застывания не выше минус 18°С.
Содержание в масле водорастворимых кислот и щелочей, а также воды и механических примесей не допускается.
1.4. В качестве наполнителя для изготовления мастики должны применяться:
мел — по ГОСТ 842—52 и ГОСТ 12085—66;
мрамор и известняк с влажностью не более 0,2% и с тонкостью помола, характеризуемой величиной остатка после просева на ситах с сетками по ГОСТ 3584—53, не более 6% — для сетки № 006 и 2% — Для сетки № 018 п при отсутствии остатка на сите № 0315.
15. Готовая мастика должна быть принята техническим контро-лем предприятия-изготовителя.
Предприятие-изготовитель должно гарантировать соответствие выпускаемой продукции требованиям настоящего стандарта.
2. МЕТОДЫ ИСПЫТАНИЙ
2.1. Для контрольной проверки потребителем качества мастики, а также соответствия ее требованиям настоящего стандарта, должны применяться правила отбора проб и методы испытаний, указанные ниже.
2.2. При неудовлетворительных результатах испытаний хотя бы по одному из показателей по нему проводят повторное испытание удвоенного количества образцов, взятых от той же партии. При неудовлетворительных результатах повторных испытаний вся партия мастики бракуется.
2.3. Размеры партии мастики одного цвета устанавливаются в количестве сменной выработки.
2.4. Пробы отбирают не менее чем из трех тарных единиц одной партии мастики, а при количестве их в партии свыше 100 — нс менее чем от 5% тарных единиц. Вес отбираемой пробы должен быть не менее 0,5 кг. Перед отбором пробы срезают верхний слой мастики на глубину 5—7 см. Пробы помещают в стеклянные банки с притертыми пробками или завертывают в полиэтиленовую .пленку.
2-5. Для каждого испытания, предусмотренного настоящим стандартом, изготавливают по три образца из средней пробы мастики, получаемой путем тщательного перемешивания отдельных проб, взятых из тарных единиц.
Показатель каждого испытания устанавливают как среднее арифметическое значение результатов испытаний трех образцов.
2.6. Цвет мастики определяют визуально.
2.7. Предел прочности мастики при разрыве определяют величиной растягивающего усилия, воздействующего в течение установленного времени на мастичный шов между двумя бетонными плитками. Испытание проводят следующим образом (см. черт. 1).
Черт. 1
2.7.1. Подогретую до 70°С мастику наносят в виде валика посередине бетонной плитки 5 размером 50X50X25 мм, имеющей сухую ровную поверхность без трещин, вмятин и бугров.
Нанесенный валик мастики обжимают с двух сторон деревянными ограничительными планками высотой 20 мм и длиной 50 мм до размеров валика в плане 30X50 мм.
Во избежание прилипания мастики к деревянным планкам они должны быть со стороны, примыкающей к мастике, смазаны минеральным маслом и присыпаны наполнителем, применяемыми для изготовления мастики. Сверху мастичный валик прижимают второй бетонной плиткой 1 до придания ему формы прямоугольного сплошного шва 3 размером 50X50X20 мм. Выступившую с торцов образца излишнюю мастику удаляют шпателем или ножом.
Подготовленный таким способом образец выдерживают 4 ч при температуре 20±2°С, после чего удаляют ограничительные планки и образец закрепляют в металлические обоймы 2 и 4. Затем обра-
ГОСТ 14791—69
зец подвешивают при помощи крючка верхней металлической обоймы 2 к кронштейну лабораторного штатива или к другой опоре. К крючку нижней металлической обоймы 4 прикрепляют расчетный груз 6.
2.7.2. Напряжение в испытуемом мастичном шве 3 в 0,07 кгс/см2 создают растягивающим усилием в 1050 гс, которое слагается из весов расчетного груза 6, нижней бетонной плитки 5 и нижней металлической обоймы 4 с приспособлением для крепления груза, равнодействующая которых должна совпадать с вертикальной осью симметрии образца. Образец должен выдерживать приложенное усилие не мепее 60 с и иметь при последующей выдержке когезионное разрушение мастичного шва (разрыв по телу шва).
2.8. Относительное удлинение мастики определяют посредством растягивающего усилия, воздействующего в течение установленного времени на мастичный шов между двумя бетонными плитками по схеме, указанной на черт. 1.
Подготовку отобранных образцов к испытанию для определения относительного удлинения производят по методу, указанному в п. 2.7.1. настоящего стандарта. Растягивающее усилие, воздействующее на мастичный шов 3, должно составлять 315 гс и слагаться из весов: расчетного груза 6 нижней бетонной плитки 5 и нижней металлической обоймы с приспособлением для крепления грузам, равнодействующая которых должна совпадать с осью симметрии образца. Растягивающее усилие должно воздействовать на мастичный шов в течение 2ч.
В конце испытания в мастичном шве не должно быть разрушений.
Величину относительного удлинения (/) в процентах вычисляют по формуле:
/ = . 100,
где:
Lo — величина зазора между бетонными плитками до начала испытания в мм;
Ц\ — величина зазора между бетонными плитками в конце испытания в мм;
2.9. Для определения водопоглощения навеску мастики около 10 г наносят ровным слоем на стеклянную пластинку или полиэтиленовую пленку размером 50X50 мм. Подготовленный образец взвешивают с точностью до 0,01 г, а затем погружают в воду, где его выдерживают 24 ч при температуре 18±2°С.
По извлечении из воды образец промокают фильтровальной бумагой и снова взвешивают. Водопоглощение (ti^) в процентах вычисляют по формуле:
г = . юо,
где:
Go — вес образца до испытания в г;
Gi -- вес образца после испытания в г;
q — навеска мастики в г.
2.10. Для определения однородности структуры (потери в весе при воздействии раствора соляной кислоты) навеску мастики около 10 г наносят ровным слоем на стеклянную пластинку или полиэтиленовую пленку размером 50X50 мм. Подготовленный образец взвешивают с точностью до 0,01 г, а затем погружают в 10%-ный раствор соляной кислоты, в котором образец выдерживают в течение 24 ч при температуре 18±2°С- По извлечении образца из раствора его промывают проточной водой в течение 2—3 мин, а затем высушивают в течение 3 ч при температуре 70°С. После высушивания образец вновь взвешивают.
Потерю в весе (X) в процентах вычисляют по формуле:
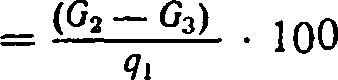
где:
G2 — вес образца до испытания в г;
G3 — вес образца после испытания в г;
qi — навеска мастики в г.
2.11. Испытание мастики на теплостойкость заключается в определении максимальной температуры, при которой мастика не проявляет свойств текучести.
Испытание проводят при помощи лотка, изображенного на черт. 2, изготовленного из листовой стали из алюминия толщиной 1,0—1,4 мм.
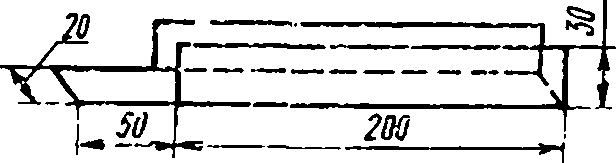
Черт. 2
Перед заполнением лотка мастику предварительно выдерживают в термостате не менее 1 ч при температуре 70°С. Лоток заполняют мастикой вровень с верхними и торцовыми обрезами боковых стенок.
Испытуемый образец устанавливают в термостат в вертикальном положении, выступающей частью лотка вниз, в котором его выдерживают в течение 24 ч при температуре не ниже 70°С.
После извлечения образца из термостата сплыв мастики по выступающей части лотка, ниже торцовых обрезов его боковых стенок, не должен превышать 2 мм.
ГОСТ 14791—69
2.12. Испытание исходного сырья для изготовления мастики УМС-50 по показателям, установленным настоящим стандартом, проводят:
а) высокомолекулярного полиизобутилена — по ГОСТ 13303—67;
б) минерального масла:
кинематическая вязкость — по ГОСТ 33—66; содержание водорастворимых кислот и щелочей — по ГОСТ 6307—60;
содержание воды — по ГОСТ 1547—42; содержание механических примесей — по ГОСТ 6370—59; температура вспышки — по ГОСТ 4333—48;
температура застывания — по ГОСТ 1533—42;
в) наполнителя — по ГОСТ 842—52-
3. УПАКОВКА, МАРКИРОВКА И ХРАНЕНИЕ
3.1. Готовую мастику упаковывают в инвентарные ящики, изготовленные из строганых досок и снабженные съемными крышками. Ящики должны иметь ручки для переноски. Вес брутто одного места не должен превышать 70 кг.
Примечания:
1. По согласованию между предприятием-изготовителем и потребителем допускается упаковка мастики в деревянные бочки и металлические барабаны со съемными крышками весом брутто до 100 кг, а также в специальные стеклопластиковые, полиэтиленовые и другие ампулы.
2. При повторном использовании тары ее внутренняя поверхность перед укладкой мастики должна быть очищена и обработана мелоклеевым составом.
3.2. Ящики, бочки и металлические барабаны должны быть снабжены наклейками или несмываемыми надписями с указанием:
а) наименования организации, в систему которой входит предприятие-изготовитель;
б) наименования предприятия-изготовителя;
в) наименования продукции;
г) веса брутто и нетто;
д) номера партии;
е) даты изготовления;
ж) номера настоящего стандарта;
з) штампа ОТК.
Примечание. Па ампулы наклеивают бумажные этикетки с указанием тех же обозначен'!!» или их помечают товарным знаком предприятия-изготовителя.
3.3. Каждая поставляемая партия мастики должна сопровождаться документом (паспортом) установленной формы и инструкцией по ее применению.
В документе (паспорте) должно быть указано:
а) наименование организации, в систему которой входит предприятие-изготовитель;
б) наименование предприятия-изготовителя и его адрес;
в) номер и дата составления документа;
г) наименование и марка продукции;
д) вес брутто;
е) дата изготовления;
ж) номер партии;
з) результаты проведенных испытаний;
и) номер настоящего стандарта.
3.4. Мастика должна храниться в закрытой таре в помещениях, предохраняющих ее от воздействия солнечных лучей и атмосферных осадков.
Замена
ГОСТ 12085—66 введен взамен ГОСТ 842—52 в части технических условий.
РАЗРАБОТАН всесоюзным научно-исследовательским институтом новых строительных материалов [ВНИИНСМ] Министерства промышленности строительных материалов СССР
Директор института Полуянов А. Ф.
Руководитель темы Панкратов В. Ф. Исполнители — Фомин А. И., Тюпиков Г. Г., Пфлаумер О. Э.
ВНЕСЕН Министерством промышленности строительных материалов СССР
Член коллегии Добужинский В. И.
ПОДГОТОВЛЕН К УТВЕРЖДЕНИЮ Отделом технического нормирования и стандартизации Госстроя СССР
Начальник отдела Шкинев А. Н.
Начальник подотдела стандартов и технических условий Мозольков В. С. Гл. специалист Балалаев Г. А.
УТВЕРЖДЕН Государственным комитетом Совета Министров СССР по делам строительства.
ВВЕДЕН В ДЕЙСТВИЕ Постановлением Госстроя СССР от 23 июня 1969 г. № 27
463