ФЕДЕРАЛЬНОЕ АГЕНТСТВО ПО ТЕХНИЧЕСКОМУ РЕГУЛИРОВАНИЮ И МЕТРОЛОГИИ
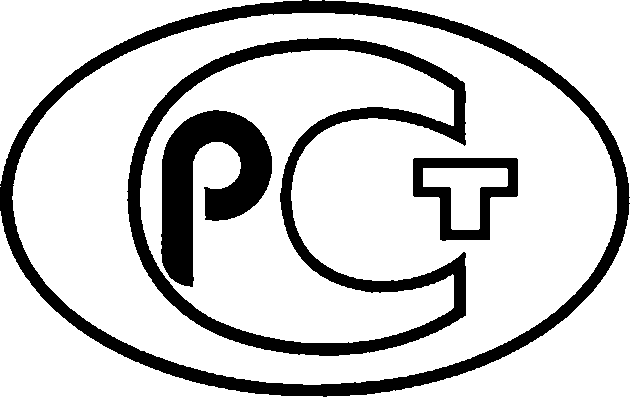
пнет 692— 2022
ПРЕДВАРИТЕЛЬНЫЙ НАЦИОНАЛЬНЫЙ СТАНДАРТ РОССИЙСКОЙ ФЕДЕРАЦИИ
Нефтяная и газовая промышленность
СИСТЕМЫ ПОДВОДНОЙ ДОБЫЧИ
Устьевое оборудование. Штуцерный модуль
Издание официальное
Москва Российский институт стандартизации 2023
Предисловие
1 РАЗРАБОТАН Обществом с ограниченной ответственностью «Газпром 335» (ООО «Газпром 335»)
2 ВНЕСЕН Техническим комитетом по стандартизации ТК 023 «Нефтяная и газовая промышленность»
3 УТВЕРЖДЕН И ВВЕДЕН В ДЕЙСТВИЕ Приказом Федерального агентства по техническому регулированию и метрологии от 27 декабря 2022 г. № 160-пнст
Правила применения настоящего стандарта и проведения его мониторинга установлены в ГОСТР 1.16—2011 (разделы 5 и 6).
Федеральное агентство по техническому регулированию и метрологии собирает сведения о практическом применении настоящего стандарта. Данные сведения, а также замечания и предложения по содержанию стандарта можно направить не позднее чем за 4 мес до истечения срока его действия разработчику настоящего стандарта по адресу: [email protected] и/или в Федеральное агентство по техническому регулированию и метрологии по адресу: 123112 Москва, Пресненская набережная, д. 10, стр. 2.
В случае отмены настоящего стандарта соответствующая информация будет опубликована в ежемесячном информационном указателе «Национальные стандарты» и также будет размещена на официальном сайте Федерального агентства по техническому регулированию и метрологии в сети Интернет (www.rst.gov.ru)
© Оформление. ФГБУ «Институт стандартизации», 2023
Настоящий стандарт не может быть полностью или частично воспроизведен, тиражирован и распространен в качестве официального издания без разрешения Федерального агентства по техническому регулированию и метрологии
Содержание
1 Область применения
2 Нормативные ссылки
3 Термины, определения, обозначения и сокращения
4 Общие положения
5 Классификация
6 Технические требования
7 Требования безопасности и охраны окружающей среды
8 Правила приемки
9 Методы контроля и испытаний
10 Транспортирование и хранение
11 Указания по эксплуатации и монтажу
12 Гарантии изготовителя
Приложение А (справочное) Примеры общего вида штуцерного модуля и соединительной муфты. . .31
Библиография
Введение
Создание и развитие отечественных технологий и техники для освоения морских нефтегазовых месторождений должно быть обеспечено современными стандартами, устанавливающими требования к проектированию, строительству и эксплуатации систем подводной добычи. Для решения данной задачи Министерством промышленности и торговли Российской Федерации и Федеральным агентством по техническому регулированию и метрологии реализуется «Программа по обеспечению нормативной документацией создания отечественной системы подводной добычи для освоения морских нефтегазовых месторождений». В объеме работ программы предусмотрена разработка национальных стандартов и предварительных национальных стандартов, областью применения которых являются системы подводной добычи углеводородов.
Целью разработки настоящего стандарта является установление единых правил проектирования и общих требований к штуцерным модулям, применяемым при строительстве и эксплуатации систем подводной добычи углеводородов.
НАЦИОНАЛЬНЫЙ СТАНДАРТ РОССИЙСКОЙ ФЕДЕРАЦИИ
Нефтяная и газовая промышленность
СИСТЕМЫ ПОДВОДНОЙ ДОБЫЧИ
Устьевое оборудование.
Штуцерный модуль
Petroleum and natural gas industry. Subsea production systems. Wellhead equipment. Choke module
Срок действия — с 2023—05—30 до 2026—05—30
1 Область применения
1.1 Настоящий стандарт распространяется на штуцерные модули, предназначенные для обустройства подводных нефтегазовых скважин систем подводной добычи углеводородов.
1.2 Настоящий стандарт устанавливает положения в области правил приемки, методов испытаний, транспортирования и хранения, безопасной эксплуатации и монтажа, а также условий гарантии изготовителя штуцерного модуля.
1.3 Настоящий стандарт не распространяется на оборудование системы управления подводной добычи, установленное на штуцерном модуле.
2 Нормативные ссылки
В настоящем стандарте использованы нормативные ссылки на следующие стандарты:
ГОСТ 9.014 Единая система защиты от коррозии и старения. Временная противокоррозионная защита изделий. Общие требования
ГОСТ 9.306 Единая система защиты от коррозии и старения. Покрытия металлические и неметаллические неорганические. Обозначения
ГОСТ 9.407 Единая система защиты от коррозии и старения. Покрытия лакокрасочные. Метод оценки внешнего вида
ГОСТ 12.2.063 Арматура трубопроводная. Общие требования безопасности
ГОСТ 15.309 Система разработки и постановки продукции на производство. Испытания и приемка выпускаемой продукции. Основные положения
ГОСТ 17.1.1.04 Охрана природы. Гидросфера. Классификация подземных вод по целям водопользования
ГОСТ 17.1.3.02 Охрана природы. Гидросфера. Правила охраны вод от загрязнения при бурении и освоении морских скважин на нефть и газ
ГОСТ 1497 (ИСО 6892—84) Металлы. Методы испытаний на растяжение
ГОСТ 5632 Нержавеющие стали и сплавы коррозионно-стойкие, жаростойкие и жаропрочные. Марки
ГОСТ 7565 (ИСО 377-2—89) Чугун, сталь и сплавы. Метод отбора проб для определения химического состава
ГОСТ 9012 (ИСО 410—82, ИСО 6506—81) Металлы. Метод измерения твердости по Бринеллю
Издание официальное
ГОСТ 9013 (ИСО 6508—86) Металлы. Метод измерения твердости по Роквеллу
ГОСТ 9293 (ИСО 2435—73) Азот газообразный и жидкий. Технические условия
ГОСТ 10198 Ящики деревянные для грузов массой св. 200 до 20000 кг. Общие технические условия
ГОСТ 14192 Маркировка грузов
ГОСТ 14771—76 Дуговая сварка в защитном газе. Соединения сварные. Основные типы, конструктивные элементы и размеры
ГОСТ 15150 Машины, приборы и другие технические изделия. Исполнения для различных климатических районов. Категории, условия эксплуатации, хранения и транспортирования в части воздействия климатических факторов внешней среды
ГОСТ 17216 Чистота промышленная. Классы чистоты жидкостей
ГОСТ 18442 Контроль неразрушающий. Капиллярные методы. Общие требования
ГОСТ 23170 Упаковка для изделий машиностроения. Общие требования
ГОСТ 24054 Изделия машиностроения и приборостроения. Методы испытаний на герметичность. Общие требования
ГОСТ 24297 Верификация закупленной продукции. Организация проведения и методы контроля
ГОСТ 24950 Отводы гнутые и вставки кривые на поворотах линейной части стальных трубопроводов. Технические условия
ГОСТ 26828 Изделия машиностроения и приборостроения. Маркировка
ГОСТ 31993 (ISO 2808:2007) Материалы лакокрасочные. Определение толщины покрытия
ГОСТ 32299 (ISO 4624:2002) Материалы лакокрасочные. Определение адгезии методом отрыва
ГОСТ 33855 Обоснование безопасности оборудования. Рекомендации по подготовке
ГОСТ 34437 Арматура трубопроводная. Методика экспериментального определения гидравлических и кавитационных характеристик
ГОСТ ISO 17636-1 Неразрушающий контроль сварных соединений. Радиографический контроль. Часть 1. Способы рентгено- и гаммаграфического контроля с применением пленки
ГОСТ ISO/IEC 15459-1 Информационные технологии. Технологии автоматической идентификации и сбора данных. Идентификация уникальная. Часть 1. Индивидуальные транспортируемые единицы
ГОСТ ISO/IEC 15459-2 Информационные технологии. Технологии автоматической идентификации и сбора данных. Идентификация уникальная. Часть 2. Порядок регистрации
ГОСТ Р 2.601 Единая система конструкторской документации. Эксплуатационные документы
ГОСТ Р 2.610 Единая система конструкторской документации. Правила выполнения эксплуатационных документов
ГОСТ Р 8.568 Государственная система обеспечения единства измерений. Аттестация испытательного оборудования. Основные положения
ГОСТ Р 15.301 Система разработки и постановки продукции на производство. Продукция производственно-технического назначения. Порядок разработки и постановки продукции на производство
ГОСТ Р 50.05.03 Система оценки соответствия в области использования атомной энергии. Оценка соответствия в форме контроля. Унифицированные методики. Ультразвуковой контроль. Измерение толщины монометаллов, биметаллов и антикоррозионных наплавленных поверхностей
ГОСТ Р 50556—93 (ИСО 4021—77) Гидропривод объемный. Анализ загрязненности частицами. Отбор проб жидкости из трубопроводов работающих систем
ГОСТ Р 51365 Нефтяная и газовая промышленность. Оборудование для бурения и добычи. Оборудование устья скважины и фонтанное устьевое оборудование. Общие технические требования
ГОСТ Р 51876 (ИСО 1496-1:1990) Контейнеры грузовые серии 1. Технические требования и методы испытаний. Часть 1. Контейнеры общего назначения
ГОСТ Р 53678—2009 (ИСО 15156-2:2003) Нефтяная и газовая промышленность. Материалы для применения в средах, содержащих сероводород, при добыче нефти и газа. Часть 2. Углеродистые и низколегированные стали, стойкие к растрескиванию, и применение чугунов
ГОСТ Р 54123 Безопасность машин и оборудования. Термины, определения и основные показатели безопасности
ГОСТ Р 56237 (ИСО 5667-5:2006) Вода питьевая. Отбор проб на станциях водоподготовки и в трубопроводных распределительных системах
ГОСТ Р 56512 Контроль неразрушающий. Магнитопорошковый метод. Типовые технологические процессы
ГОСТ Р 57546—2017 Землетрясения. Шкала сейсмической интенсивности
ГОСТ Р 58218 Нефтяная и газовая промышленность. Арктические операции. Обслуживание объектов
ГОСТ Р 59304 Нефтяная и газовая промышленность. Системы подводной добычи. Термины и определения
ГОСТ Р 59305—2021 (ИСО 13628-1:2005) Нефтяная и газовая промышленность. Проектирование и эксплуатация систем подводной добычи. Часть 1. Общие требования и рекомендации
ГОСТ Р ЕН 13018 Контроль визуальный. Общие положения
ГОСТ Р ИСО 148-1 Материалы металлические. Испытание на ударный изгиб на маятниковом копре по Шарли. Часть 1. Метод испытания
ГОСТ Р ИСО 5817 Сварка. Сварные соединения из стали, никеля, титана и их сплавов, полученные сваркой плавления (исключая лучевые способы сварки). Уровни качества
ГОСТ Р ИСО 6507-1 Металлы и сплавы. Измерение твердости по Виккерсу. Часть 1. Метод измерения
ГОСТ Р ИСО 8501-1 Подготовка стальной поверхности перед нанесением лакокрасочных материалов и относящихся к ним продуктов. Визуальная оценка чистоты поверхности. Часть 1. Степень окисления и степени подготовки непокрытой стальной поверхности и стальной поверхности после полного удаления прежних покрытий
ГОСТ Р ИСО 9001—2015 Системы менеджмента качества. Требования
ГОСТ Р ИСО 9606-1 Аттестационные испытания сварщиков. Сварка плавлением. Часть 1. Стали
ГОСТ Р ИСО 9712 Контроль неразрушающий. Квалификация и сертификация персонала
ГОСТ Р ИСО 13628-4—2016 Нефтяная и газовая промышленность. Проектирование и эксплуатация подводных эксплуатационных систем. Часть 4. Подводное устьевое оборудование и фонтанная арматура
ГОСТ Р ИСО 14732 Персонал, выполняющий сварку. Аттестационные испытания сварщиков-операторов и наладчиков для полностью механизированной и автоматической сварки металлических материалов
ГОСТ Р ИСО 15614-1 Технические требования и аттестация процедур сварки металлических материалов. Проверка процедуры сварки. Часть 1. Дуговая и газовая сварка сталей и дуговая сварка никеля и никелевых сплавов
ГОСТ Р ИСО 17637 Контроль неразрушающий. Визуальный контроль соединений, выполненных сваркой плавлением
ГОСТ Р ИСО 17640 Неразрушающий контроль сварных соединений. Ультразвуковой контроль. Технология, уровни контроля и оценки
Примечание — При пользовании настоящим стандартом целесообразно проверить действие ссылочных стандартов в информационной системе общего пользования — на официальном сайте Федерального агентства по техническому регулированию и метрологии в сети Интернет или по ежегодному информационному указателю «Национальные стандарты», который опубликован по состоянию на 1 января текущего года, и по выпускам ежемесячного информационного указателя «Национальные стандарты» за текущий год. Если заменен ссылочный стандарт, на который дана недатированная ссылка, то рекомендуется использовать действующую версию этого стандарта с учетом всех внесенных в данную версию изменений. Если заменен ссылочный стандарт, на который дана датированная ссылка, то рекомендуется использовать версию этого стандарта с указанным выше годом утверждения (принятия). Если после утверждения настоящего стандарта в ссылочный стандарт, на который дана датированная ссылка, внесено изменение, затрагивающее положение, на которое дана ссылка, то это положение рекомендуется применять без учета данного изменения. Если ссылочный стандарт отменен без замены, то положение, в котором дана ссылка на него, рекомендуется применять в части, не затрагивающей эту ссылку.
3 Термины, определения, обозначения и сокращения
3.1 В настоящем стандарте применены термины по ГОСТ Р 51365, ГОСТ Р 59304, а также следующие термины с соответствующими определениями:
3.1.1
дроссель (choke): Оборудование, используемое для ограничения и регулирования потока жидкости и газа.
[ГОСТ Р ИСО 13628-4—2016, пункт 3.1.9]
3.1.2
запирающий элемент; ЗЭл (Нрк. захлопка; запирающий орган; запорный орган; замыкающий элемент; затвор)'. Подвижная часть затвора, связанная с приводом, позволяющая при взаимодействии с седлом осуществлять управление потоком рабочих сред путем изменения проходного сечения и обеспечивать определенную герметичность.
[ГОСТ 24856—2014, статья 7.46]
3.1.3 изготовитель: Организация независимо от ее организационно-правовой формы, а также индивидуальный предприниматель, которые осуществляют производство или производство и реализацию оборудования и отвечают за соответствие продукции установленным техническим требованиям.
3.1.4
коррозионно-стойкий сплав (corrosion-resistant alloy); CRA: Сплав цветных металлов, в котором один или сумма определенного количества следующих легирующих элементов превышает 50 %: титан, никель, кобальт, хром и молибден.
Примечание — Данный термин относится к коррозионно-стойким сплавам, а не к трещинно-стойким сплавам, как определено в ИСО 15156 (все части).
[ГОСТ Р ИСО 13628-4—2016, пункт 3.1.13]
3.1.5
метод испытаний: Правила применения определенных принципов и средств испытаний.
[ГОСТ 16504—81, статья 11]
3.1.6
нормально закрытая задвижка (fail-closed valve): Приводная задвижка, спроектированная на переход в закрытое положение при отказе управляющего сигнала.
[ГОСТ Р ИСО 13628-4—2016, пункт 3.1.19]
3.1.7
обратная арматура (check valve): Устройство, предназначенное для предотвращения обратного потока.
[ГОСТ Р ИСО 13628-4—2016, пункт 3.1.8]
3.1.8
прослеживаемость (traceability): Возможность проследить историю, применение или местонахождение объекта (3.6.1).
Примечания
1 Прослеживаемость применительно к продукции (3.7.6) или услуге (3.7.7) может относиться:
- к происхождению материалов и комплектующих;
- истории создания;
- распределению и местонахождению продукции или услуги после поставки.
2 В области метрологии принято определение, приведенное в Руководстве ИСО/МЭК 99:2007.
[ГОСТ Р ИСО 9000—2015, пункт 3.6.13]
3.1.9
система соединителя выкидного трубопровода/выкидной линии (flowline connector system): Оборудование, используемое для соединения подводных трубопроводов и/или управляющих шлан-гокабелей с подводной устьевой елкой.
Пример — Смонтированные на устьевой елке соединительные системы, используемые для соединения подводных выкидных трубопроводов с подводной устьевой елкой, соединяют концевой терминал выкидного трубопровода с подводной устьевой елкой с помощью гибкого трубного соединителя, соединяют подводную устьевую елку с манифольдом с помощью гибкого трубного соединителя и т. д.
[ГОСТ Р ИСО 13628-4—2016, пункт 3.1.23]
3.1.10 специальные процессы: Процессы производства и обслуживания, результаты которых не могут быть верифицированы последующим мониторингом или измерениями.
Примечание — К специальным процессам относятся все процессы, недостатки которых становятся очевидными только после начала использования продукции или после оказания услуги.
3.1.11
спуско-подъемный инструмент (running tool): Инструмент, предназначенный для дистанционного выполнения с поверхности операций по спуску, извлечению, позиционированию или подсоединению подводного оборудования.
Пример — Инструмент для спуска-подъема устьевой елки, заглушки устьевой елки, соединителей выкидных линий и т. п.
[ГОСТ Р ИСО 13628-4—2016, пункт 3.1.45]
3.1.12
телеуправляемый НПА (ТИПА): Необитаемый подводный аппарат, связанный с носителем (судном, подводной лодкой, подводным аппаратом) посредством кабель-троса, по которому передаются электропитание и/или сигналы управления, а также происходит обмен информацией.
[ГОСТ Р 56960—2016, пункт 3.3]
3.1.13
техническое обслуживание; ТО (maintenance): Комплекс технологических операций и организационных действий по поддержанию работоспособности или исправности объекта при использовании по назначению, ожидании, хранении и транспортировании.
[ГОСТ 18322—2016, статья 2.1.1]
3.1.14
электрохимическая защита: Защита металла от коррозии, осуществляемая поляризацией от внешнего источника тока или путем соединения с металлом (протектором), имеющим более отрицательный или более положительный потенциал, чем у защищаемого металла.
Примечание — В зависимости от направления поляризации различают катодную и анодную защиты.
[ГОСТ 9.106—2021, статья 98]
3.2 В настоящем стандарте применены следующие обозначения и сокращения:
Fpren — коэффициент стойкости к питтинговой коррозии, %;
PN — номинальное давление, МПа (кгс/см2);
Тмакс — максимальная рабочая температура, °C;
ТМИн — минимальная рабочая температура, °C;
Kv — пропускная способность (гидравлическая), м3/ч;
ов — временное сопротивление, МПа;
°0 2 — предел текучести, МПа;
85 — относительное удлинение, %;
\|/ — относительное сужение, %;
БРС — быстроразъемное соединение;
ЗА — запорная арматура;
ЗИП — запасные части, инструменты и принадлежности;
ИМ — инструкция по монтажу; пуску, регулированию и обкатке изделия;
КД — конструкторская документация;
КИП — контрольно-измерительные приборы и оборудование;
ЛКП — лакокрасочное покрытие;
МФР — многофазный расходомер;
МЭГ — моноэтиленгликоль;
НД — нормативные документы;
ОТК — отдел технического контроля;
ПИ — приемочные испытания;
ПМ — программа и методика испытаний;
ПМУ — подводный модуль управления;
ПСИ — приемо-сдаточные испытания;
ПТФЭ — политетрафторэтилен;
ПФА — подводная фонтанная арматура;
РА — регулирующая арматура;
РЭ — руководство по эксплуатации;
СПД — системы подводной добычи;
СУ СПД — система управления системы подводной добычи;
ТЗ — техническое задание;
ТР ТС — Технический регламент Таможенного союза;
ТУ — технические условия;
УТТ — уровень технических требований;
ФО — формуляр;
ШМ — штуцерный модуль;
ЭД — эксплуатационная документация;
ЭХЗ — электрохимическая защита.
4 Общие положения
4.1 ШМ в составе ПФА обеспечивает регулирование режима работы скважины с подводным расположением устья и предназначен для размещения в нем регулирующего оборудования и КИП.
4.2 Основные компоненты ШМ включают, но не ограничиваются ими:
- выкидную линию ШМ;
- эксплуатационный дроссель;
- соединительную муфту;
- комплект КИП;
- комплект электрических соединителей и кабелей;
- систему подачи химических реагентов;
- несущую раму.
4.3 Общий вид ШМ представлен на рисунке А.1 (приложение А).
4.3.1 Выкидная линия ШМ представляет собой систему сваренных деталей трубопроводов из коррозионно-стойких сплавов, соединительных элементов фланцевого типа с уплотнениями типа металл по металлу или сварными, оборудованную местами для установки и подключения КИП, линий впрыска химических реагентов и т. д.
4.3.2 Эксплуатационный дроссель предназначен для регулирования потока флюида путем изменения проходного сечения.
4.3.3 В состав эксплуатационного дросселя (далее — дроссель) входят:
- проточная часть;
- привод;
- регулирующий элемент.
Примечание —Дроссель допускается изготавливать в неизвлекаемом исполнении, полностью извлекаемом исполнении и исполнении с извлекаемым приводом.
4.3.4 Привод дросселя предназначен для перемещения и фиксации положения регулирующего элемента.
4.3.5 Привод дросселя комплектуют вспомогательными механизмами (системой аварийного управления, механизмом индикации и т. д.) и датчиками положения, для передачи информации в СУ СПД.
4.3.6 Соединительная муфта предназначена для дистанционного герметичного присоединения и отсоединения ШМ (выкидной линии ШМ и прочих линий) к ПФА. Общий вид соединительной муфты хомутового типа приведен на рисунке А.2 (приложение А). Соединительную муфту допускается выполнять в хомутовом и цанговом исполнении.
4.3.7 Как правило, в состав соединительной муфты входят гидравлические БРС и уплотнительные кольца типа металл по металлу.
4.3.8 Комплект КИП должен включать датчики давления, температуры, выноса песка, эрозии трубопроводов и т. д., предназначенные для передачи и измерения соответствующей информации в СУ СПД. В КИП может также входить МФР, если его наличие предусмотрено требованиями к ШМ.
4.3.9 Комплект электрических соединителей и кабелей предназначен для передачи электрического питания от СУ СПД, а также обмена данными с СУ СПД посредством электрических или сигнальных линий. Электрические соединители и кабели присоединяют к СУ СПД посредством разъемов, предназначенных для стыковки в подводном положении с использованием ТИПА.
4.3.10 Система подачи химических реагентов состоит из следующих основных компонентов:
- шиберной ЗА линии подачи химических реагентов;
- дросселя подачи химических реагентов;
- трубной обвязки.
4.3.11 Система подачи химических реагентов предназначена для контролируемой подачи различных химических реагентов в выкидную линию ШМ (ингибиторы коррозии, МЭГ и т. д.).
4.3.12 Несущая рама представляет собой сварную металлоконструкцию для размещения элементов ШМ и обеспечивает его транспортировку отдельно от ПФА, спуск и подъем.
4.3.13 Несущая рама ШМ состоит из следующих основных компонентов:
- системы мягкой посадки ШМ;
- системы ЭХЗ;
- грузозахватных элементов.
5 Классификация
5.1 ШМ подразделяют по основным классификационным признакам, приведенным в таблице 1.
Таблица 1—Классификация ШМ
Классификационный признак | Разновидность |
Извлекаемость | Извлекаемый |
Интегрированный | |
Монтаж | По направляющим канатам, направляющим элементам конструкции |
Без направляющих элементов конструкции | |
Номинальный диаметр выкидной линии | 130 мм (5 1/8 дюйма) |
179 мм (7 1/16 дюйма) | |
Подача химических реагентов | С регулированием |
Без регулирования | |
Не предусмотрена | |
Количество гидравлических линий управления/подачи | Количество линий (от 0 до 16) |
Номинальное давление выкидной линии в соответ-ствии с ГОСТ Р ИСО 13628-4 | 34,5 МПа |
69,0 МПа | |
103,5 МПа | |
Интерфейсы ТИПА (см. [1]) | Вращательный высокомоментный, класс 4 |
Вращательный низкомоментный, типы А, В и С | |
Толкательный тип А | |
Управление соединительной муфтой | ОтПМУ |
От штепсельного разъема ТИПА | |
Механическое | |
Номинальное давление линий управления в соответствии с ГОСТ Р ИСО 13628-4 | 10,3 МПа |
20,7 МПа | |
34,5 МПа | |
Климатическое исполнение по ГОСТ 15150 | ОМ (MU) |
УТТ по ГОСТ Р 51365 | УТТЗ |
УТТ4 | |
Количество линий подачи химических реагентов | 1 |
2 | |
3 | |
4 | |
Тип соединителя соединительной муфты | 1 — хомутовый |
2 — цанговый | |
0 — отсутствие (неразъемное соединение) | |
Класс коррозионной стойкости по ГОСТ Р 51365 | FF |
НН |
5.2 Схема условного обозначения ШМ приведена на рисунке 1.
ШМ -XX-XX- X -х-х-хх
| Класс коррозионной стойкости
Тип соединителя выкидной линии
Номинальный диаметр выкидной линии, мм
Температурный класс
Уровень технических требований
Номинальное давление PN, МПа
Штуцерный модуль
Рисунок 1 — Схема условного обозначения штуцерного модуля
Пример условного обозначения ШМ номинальным диаметром выкидной линии 130 мм, номинальным давлением 69,0 МПа с УТТ 4, температурного класса U с соединителем хомутового типа и коррозионно-стойкого исполнения НН
ШМ—69,0—4—U—130-1-НН
6 Технические требования
6.1 Общие требования
6.1.1 ШМ должен соответствовать требованиям настоящего стандарта, а также требованиям, приведенным в ГОСТ Р ИСО 13628-4, ГОСТ Р 51365 (см. также [1]).
6.1.2 ШМ должен соответствовать основополагающим барьерным принципам согласно ГОСТ Р 59305—2021 (приложение J).
6.2 Основные показатели и характеристики
6.2.1 Элементы ШМ, контактирующие с пластовым флюидом, должны быть выполнены в соответствии со стандартным рядом номинальных давлений в соответствии с ГОСТ Р ИСО 13628-4—2016 (подпункт 5.1.2.1.2.1):
- 34,5 МПа;
- 69,0 МПа;
- 103,5 МПа.
6.2.2 Элементы оборудования ШМ должны соответствовать принятому климатическому исполнению по ГОСТ 15150.
6.2.3 Элементы ШМ, подверженные влиянию переходных низкотемпературных эффектов охлаждения (в корпусе дросселя и сопряженных компонентах, расположенных после него), вызванных воздействием эффекта охлаждения Джоуля—Томпсона вследствие экстремальных перепадов давления газа, должны быть выполнены с учетом расширения нижней границы рабочего диапазона температур в соответствии с ГОСТ Р ИСО 13628-4—2016 (подпункт 5.1.2.2.1).
6.2.4 Элементы ШМ, контактирующие с пластовым флюидом, должны соответствовать требованиям УТТ 3 или УТТ 4 согласно ГОСТ Р 51365 в зависимости от установленных требований к ШМ.
6.2.5 Номинальное давление линий управления ШМ следует выбирать из следующего стандартного ряда в соответствии с ГОСТ Р ИСО 13628-4—2016 (подпункт 7.21.3.2.3):
- 10,3 МПа;
- 20,7 МПа;
- 34,5 МПа.
6.2.6 Исключение составляют элементы обратной линии, давление которых может отличаться от указанных выше значений, но не должно быть менее 5 МПа.
6.2.7 Гидравлические приводы ЗА и РА должны сохранять работоспособность при отклонении давления управления в пределах от 0,9 до 1,1 от номинального давления в соответствии с ГОСТ Р ИСО 13628-4—2016 (подпункт 5.1.2.1.6).
6.2.8 Запас прочности корпусных и рамных элементов ШМ должен быть не менее 1,5 в соответствии с ГОСТ Р ИСО 13628-4—2016 (подпункты 5.1.3.6—5.1.3.8).
6.2.9 Система защиты от коррозии элементов ШМ должна учитывать требования ГОСТ Р ИСО 13628-4—2016 (пункт 5.2.4).
6.2.10 ЭХЗ должна быть спроектирована в соответствии с учетом требований ГОСТ Р ИСО 13628-4—2016 (пункт 5.4.8).
6.3 Требования к конструкции
6.3.1 Конструкция ШМ должна обеспечивать:
- взаимозаменяемость в целом и ее элементов;
- сохраняемость в период транспортировки и хранения;
- возможность дистанционного подводного монтажа/демонтажа и эксплуатации;
- взаимное позиционирование с сопрягаемыми элементами ПФА во время монтажа;
- герметичность сопрягаемых элементов оборудования;
- возможность регулируемой подачи химических реагентов в выкидную линию ШМ.
6.3.2 КИП ШМ должны иметь электрические соединители для подключения к ответным блокам разъемов ПМУ при помощи инструментов ТИПА.
6.3.3 Конструкция ШМ должна обеспечивать взаимное позиционирование с сопрягаемыми элементами ПФА.
6.3.4 Конструкция выкидной линии ШМ должна обеспечивать размещение МФР, датчиков давления и температуры, датчика эрозии и датчика выноса песка и прочих КИП в случае необходимости, а также мест подключения линий подачи химических реагентов.
6.3.5 Соединительная муфта ШМ должна:
- иметь направляющие элементы, обеспечивающие точное позиционирование сопрягаемого оборудования;
- содержать гидравлические разъемы линий управления ЗА и РА и линии подачи химических реагентов;
- обеспечивать фиксацию на ПФА при помощи механических фиксирующих элементов, приводимых в действие приводом (гидравлическим или механическим);
- должна обеспечивать герметичность соединения выкидной линии, а также линий подачи химических реагентов за счет сменных металлических кольцевых уплотнений;
- в случае необходимости обеспечивать возможность подачи давления на металлические кольцевые уплотнения для проверки их герметичности;
- обеспечивать герметичность соединения управляющих гидравлических линий ШМ с соответствующими линиями ПФА, как правило, при помощи БРС.
- снабжаться индикатором положения «открыто—закрыто» для обеспечения визуального контроля положения при помощи ТИПА. Индикатор положения должен быть расположен в непосредственной близости от привода соединительной муфты.
6.3.6 Проточную часть дросселя присоединяют к выкидной линии ШМ посредством фланцевых соединений с уплотнениями типа металл по металлу и выполняют из коррозионно-стойких сплавов.
6.3.7 В конструкции регулирующего элемента, являющегося наиболее подверженным воздействию регулируемой среды, учитывают требования ГОСТ Р 51365.
6.3.8 Выкидная линия ШМ должна иметь не менее двух датчиков для контроля давления и температуры флюида, расположенных за дросселем.
6.3.9 Эксплуатационный дроссель должен располагаться после МФР в выкидной линии ШМ по направлению потока добываемого флюида.
6.3.10 Шиберные задвижки ШМ должны быть снабжены гидравлическим приводом, иметь индикатор положения и иметь вариант исполнения «нормально закрытые».
6.3.11 Линии подачи химических реагентов должны содержать интегрированные обратные клапаны и шиберную задвижку с гидравлическим приводом и дублером управления для ТИПА.
6.3.12 МФР предназначен для измерения параметров добываемого флюида и передачи их в СУ СПД. МФР монтируют в разрыв выкидной линии ШМ посредством фланцевых соединений и уплотнений металл по металлу.
6.3.13 Шиберные задвижки, перекрывающие технологические линии, должны обеспечивать двустороннюю герметичность согласно УТТ 4 по ГОСТ Р 51365.
6.3.14 ЗА, перекрывающая линии трубной обвязки СУ СПД, должна обеспечивать двустороннюю герметичность согласно УТТ 3 по ГОСТ Р 51365.
6.3.15 Регулирование подачи химических реагентов следует выполнять для каждой линии отдельно посредством РА, изготовленной в исполнении, позволяющем осуществлять ее дистанционную установку и извлечение посредством ТИПА.
6.3.16 Выкидная линия должна иметь минимальное количество разборных соединений.
Примечание — Как правило, предпочтение отдается сварным соединениям.
6.3.17 Конструкция несущей рамы ШМ должна обеспечивать монтаж внутри рамы выкидной линии ШМ, соединительной муфты ШМ, КИП, системы мягкой посадки, а также прочих узлов, входящих в конструкцию ШМ.
6.3.18 В конструкции несущей рамы ШМ в случае необходимости предусматривают наличие системы мягкой посадки ШМ на ПФА.
6.3.19 Узлы и отдельные элементы ШМ не должны выходить за габаритные размеры рамы ШМ в плане.
6.3.20 Конструкция несущей рамы ШМ должна предусматривать места крепления для транспортирования.
6.3.21 Конструкция несущей рамы ШМ должна предусматривать возможность присоединения (монтажа) элементов ЭХЗ.
6.3.22 Конструкция рамы ШМ должна обеспечивать защиту от повреждений при спуске со скоростью до 0,5 м/с.
6.3.23 ШМ должен выдерживать нагрузки, возникающие при монтаже ШМ, съемных дросселей, а также прочих съемных элементов ШМ (например, электроразъемов).
6.3.24 Конструкция несущей рамы ШМ должна предусматривать наличие элементов присоединения инструмента для спуска ШМ.
6.3.25 Конструкция несущей рамы ШМ должна предусматривать возможность извлечения элементов ШМ посредством ТИПА, а также наличие поручней для стабилизации положения ТИПА (см. пункт 6.3 [1]).
6.3.26 Интерфейсы ЗА и РА трубной обвязки для линий СУ СПД и подачи химических реагентов с номинальным диаметром до 26 мм включительно должны соответствовать типам А или В (см. пункт 6.5 [1]).
6.3.27 Элементы трубопроводной обвязки линий СУ СПД и подачи химических реагентов должны быть закреплены на несущей раме и между собой. Расстояние между точками крепления трубопроводов не должно превышать 1,5 м.
6.3.28 Ответные части БРС должны быть снабжены обратными клапанами, исключающими свободное истечение рабочей жидкости из трубопроводов и попадание в них морской воды. Обратные клапаны должны открываться при соединении частей БРС.
6.3.29 Конструкция гидравлических приводов элементов ШМ должна обеспечивать работоспособность при классе чистоты гидравлической жидкости не выше класса 13 в соответствии с ГОСТ 17216.
6.3.30 Конструкция гидравлических приводов и трубной обвязки элементов СУ СПД, размещенных на ШМ, должна обеспечивать возможность промывки СУ СПД до требуемого класса чистоты без осуществления разборки.
6.3.31 Конструкция трубной обвязки гидравлической СУ СПД и линий подачи химических реагентов ШМ должна обеспечивать возможность выпуска воздуха при помощи специальных устройств без осуществления разборки системы.
6.3.32 Фланцевые соединения ШМ должны обеспечивать герметичность соединения металлическими кольцевыми уплотнениями типа металл по металлу в соответствии с ГОСТ Р ИСО 13628-4—2016 (подразделы 7.1 и 7.6).
6.3.33 Система мягкой посадки ШМ должна включать в себя демпферные устройства (гидроцилиндры), обеспечивающие торможение ШМ при посадке на ПФА с вертикальной скоростью до 0,5 м/с. Рабочей средой демпферных устройств является морская вода.
6.3.34 Демпферные устройства системы мягкой посадки должны иметь фиксаторы для закрепления штоков во втянутом положении (транспортном), исключающие возможность их самопроизвольного открытия.
6.3.35 ШМ должен иметь направляющие устройства (помимо направляющих в соединительной муфте ШМ), обеспечивающие его предварительную ориентацию на расположенных на ПФА специализированных ловителях.
6.3.36 Датчик выноса песка должен располагаться на выкидной линии ШМ между МФР и эксплуатационным дросселем.
6.3.37 Характеристики МФР должны соответствовать условиям работы в типе, составе и характеристиках добываемого углеводорода.
6.3.38 Датчик эрозии трубопровода должен располагаться на выкидной линии ШМ после эксплуатационного дросселя.
6.3.39 Эксплуатационный дроссель выкидной линии ШМ должен быть оснащен диафрагмой с конфигурацией типа с, d или f по ГОСТ Р ИСО 13628-4—2016 (подпункт 7.21.2.1.3).
6.3.40 Эксплуатационный дроссель должен иметь подтвержденную испытаниями характеристику пропускной способности Kv в соответствии с ГОСТ 34437.
6.3.41 Привод эксплуатационного дросселя должен иметь гидравлическое управление с механическим дублированием, приводимым в движение посредством ТИПА.
6.3.42 Дроссели подачи химических реагентов должны быть изготовлены в извлекаемом исполнении для возможности их замены при помощи ТИПА и иметь устройства их дистанционной стыковки с электрогидравлической системой управления и линией подачи химических реагентов посредством БРС и специальных разъемов подводной стыковки.
6.3.43 Вся РА, используемая в ШМ, должна сохранять текущее положение регулирующего органа в случае отказа системы управления или привода РА.
6.4 Требования к надежности
6.4.1 ШМ должен быть обслуживаемым, восстанавливаемым, ремонтопригодным объектом.
6.4.2 Показатели надежности должны соответствовать следующим требованиям (в случае соблюдения требований, изложенных в ЭД):
- наработка до отказа должна составлять не менее 5 лет;
- срок службы должен составлять не менее 30 лет;
- срок сохраняемости должен составлять не менее 3 лет.
6.4.3 Ремонтопригодность ШМ должна быть обеспечена конструкционными особенностями, позволяющими выполнять ТО и ремонт или замену его элементов.
6.4.4 Элементы ШМ, требующие технического обслуживания или ремонта в течение срока, устанавливаемого требованиями безотказной работы, должны обладать резервированием и/или конструктивной возможностью замены без демонтажа основной конструкции и, по возможности, остановки добычи.
6.4.5 Для обеспечения надежности требуется проведение мониторинга технического состояния и проведения технического обслуживания оборудования ШМ. Состав и периодичность необходимых процедур должны указываться в ЭД и содержать, но не ограничиваться, следующие процедуры:
- визуальный осмотр;
- очистка от биологических обрастаний;
- измерение потенциалов протекторной защиты;
- ультразвуковая толщинометрия;
- определение планово-высотного положения.
6.4.6 Следующее оборудование должно быть подвержено испытаниям в соответствии с ГОСТ Р ИСО 13628-4—2016 (пункт 5.1.7):
- металлические кольцевые уплотнения, подверженные воздействию флюида при эксплуатации;
- ЗА и РА;
- приводы ЗА и РА;
- обратные клапаны;
- соединительные элементы разъемов гидравлических и электрических соединителей.
6.4.7 Показатели надежности и безопасности оборудования (при наличии) должны быть указаны в ЭД и ТУ.
6.4.8 ШМ должен выдерживать проектные сейсмические воздействия.
6.5 Требования к покрытиям
6.5.1 Материалы ЛКП должны соответствовать требованиям, представленным в таблице 2.
Таблица 2 — Технические требования к ЛКП
Наименование показателя | Значение показателя |
Внешний вид покрытия | Равномерная сплошная пленка без пропусков и видимых дефектов |
Диэлектрическая сплошность покрытия (отсутствие пробоя), кВ/мм | Не менее 5,0 |
Адгезионная прочность методом нормального отрыва, МПа | Не менее 5,0 |
Минимальное количество слоев | 2 |
Толщина покрытия, мкм | В соответствии с технической документацией, но не менее 350 |
Величина распространения коррозии от надреза (шириной 2 мм) при погружении в морскую воду в течение 4200 ч, мм | Не более 3 |
Снижение адгезионной прочности методом нормального отрыва при погружении в морскую воду в течение 4200 ч, % | Не более 50 |
Площадь отслаивания покрытия при катодной поляризации в течение 4200 ч, мм2 | Не более 3 |
6.5.2 Антифрикционные покрытия, такие как покрытия на основе ПТФЭ, должны соответствовать технической документации и выбираться с учетом срока службы и условий эксплуатации.
6.5.3 Крепежные изделия из углеродистой и легированной стали, используемые в оборудовании ШМ, кроме рамных и защитных конструкций, должны быть покрыты электролитическим цинком, либо покрытиями на основе ПТФЭ при обеспечении электропроводности соединения, или химическими покрытиями, такими как фосфаты в соответствии с ГОСТ 9.306.
Примечание — При электролитическом цинковании изделия подвергают дополнительной термообработке для снижения склонности стали к водородному охрупчиванию согласно ГОСТ Р 59305.
6.5.4 На крепежные изделия не допускается наносить покрытия, содержащие кадмий.
6.5.5 Износостойкие неметаллические покрытия, такие как покрытия на основе карбида вольфрама или нитрида титана, должны соответствовать технической документации, согласованной с заказчиком.
6.5.6 Металлические покрытия для улучшения герметичности уплотнительных элементов ШМ, такие как покрытия на основе серебра, должны соответствовать технической документации.
6.6 Требования к сырью, материалам, покупным изделиям
6.6.1 Материалы для изготовления ШМ следует выбирать согласно положениям ГОСТ Р ИСО 13628-4 (см. также [2]), с учетом заданных условий эксплуатации, включая:
a) PN, МПа;
б) температуру окружающей среды;
в) максимальную и минимальную температуры рабочей среды;
г) свойства рабочей среды:
1) коррозионная активность;
2) взрывоопасность;
3) наличие примесей, приводящих к эрозионному износу;
4) параметры потока рабочей среды;
д) химический состав рабочей среды:
1) парциальное давление сероводорода;
2) концентрация метанола;
3) концентрация двуокиси углерода (СО2);
4) кислотность среды (pH);
5) наличие хлоридов и т. п.;
е) параметры окружающей среды и внешних воздействий;
ж) другие факторы, влияющие на коррозию:
1) электрохимическое воздействие при контакте различных материалов;
2) обрастание микроорганизмами.
6.6.2 Материалы ШМ с подтвержденным положительным опытом использования в оборудовании СПД являются приоритетными при выборе.
6.6.3 Все поверхности элементов ШМ, контактирующих с пластовым флюидом, а также зоны уплотнительных поверхностей, изготовленных из углеродистых и легированных сталей, должны быть покрыты антикоррозионной наплавкой.
6.6.4 Материалы элементов ШМ, контактирующих с пластовым флюидом, должны соответствовать положениям ГОСТ Р 53678—2009 (приложение А) — для углеродистых и легированных сталей (для коррозионно-стойких сталей и сплавов см. [3]).
6.6.5 Материал наплавки для уплотнительных поверхностей должен иметь коэффициент стойкости к питтинговой коррозии FPREN б°лее 40 (см. [3]). Коэффициент FPREN, 0/°’ вычисляют по формуле
FPREN = wCr+ 3,3 (vvMo+ 0’6n/w) +16 W/N , (1)
где wCr — массовая доля хрома в сплаве, %;
wMo — массовая доля молибдена в сплаве, %;
W\N — массовая доля вольфрама в сплаве, %;
wN — массовая доля азота в сплаве, %.
6.6.6 Рекомендованным материалом проволоки для наплавки является ERNiCrMo-З (см. [4]).
6.6.7 Элементы ШМ, изготовленные из углеродистых и легированных сталей и контактирующие с пластовым флюидом, должны иметь твердость не более 22 HRC в соответствии с требованиями ГОСТ Р 53678—2009 (приложение А).
6.6.8 Элементы ШМ, находящиеся под воздействием ЭХЗ, должны иметь твердость не более 35 HRC (328 НВ, 350 HV10) (см. [2]).
6.6.9 Стальные рамные конструкции ШМ должны быть изготовлены из конструкционной стали с минимальным пределом текучести не более 560 МПа (см. [2]).
6.6.10 Корпусные изделия ШМ должны быть коваными. Коэффициент уковки должен быть не менее 4,0.
6.6.11 Поковки элементов ШМ должны быть выполнены согласно УТТ 3 или УТТ 4 по ГОСТ Р 51365.
6.6.12 Химический состав поковок элементов ШМ, изготовленных из углеродистых и легированных сталей, должен соответствовать требованиям, приведенным в таблице 3.
Таблица 3 — Требования к химическому составу поковок из углеродистых и низколегированных сталей
Химический элемент | Массовая доля, не более |
Углерод | 0,45 % |
Марганец | 1,80 % |
Кремний | 1,00 % |
Хром | 2,75 % |
Молибден | 1,50 % |
Ванадий | 0,30 % |
Никель | 1,00 %* |
Сера | 0,010 % |
Фосфор | 0,015% |
Водород | 0, 0002 %** |
Кислород | 0, 0025 %** |
|
6.6.13 Механические свойства корпусных элементов ШМ должны соответствовать значениям, указанным в таблице 4, с учетом требований ГОСТ Р 51365—2009 (таблица 11).
Таблица 4 — Механические свойства материалов корпусных элементов ШМ
Характеристика | Значения параметра для различных классов прочности материалов | ||||
К248(36К) | К310 (45К) | К414 (60 К) | К517 (75К) | К586 (85К) | |
Временное сопротивление ов, МПа, не менее | 483 | 483 | 586 | 655 | 655 |
Предел текучести о02, МПа, не менее | 248 | 310 | 414 | 517 | 586 |
Относительное удлинение 55, %, не менее | 21 | 19 | 18 | 17 | 17 |
Поперечное сужение \|/, %, не менее | — | 32 | 35 | 35 | 35 |
Твердость НВ, не более или в пределах | 140 | 140 | 174 | 197—237 | 212—237 |
6.6.14 Для поковок из углеродистых и легированных сталей соотношение фактических значений предела текучести к пределу прочности не должно быть выше 0,9.
6.6.15 Среднее значение величины энергии удара при температуре минус 46 °C при испытаниях поковок из углеродистых и легированных сталей должно быть не ниже 60 Дж, при этом каждое отдельное значение не должно быть ниже 45 Дж.
6.6.16 Минимальное нормативное значение предела текучести для элементов ШМ, предназначенных для сварки, которые могут подвергаться катодной защите, изготовленных из углеродистых и низколегированных сталей, не должно превышать 560 МПа. Изделия с более высоким минимальным нормативным значением предела текучести допускается применять при условии документального подтверждения свариваемости с указанием свойств основного металла, зоны термического влияния и сварного шва.
6.6.17 Фактическое значение предела текучести для всех деталей ШМ, находящихся под воздействием ЭХЗ, не должно превышать 950 МПа (см. [2]).
6.6.18 Твердость материала металлических кольцевых уплотнений должна быть ниже твердости материалов поверхностей, соприкасающихся с уплотнением согласно ГОСТ Р 59305.
6.6.19 Металлические кольцевые уплотнения для элементов ШМ, контактирующих с пластовым флюидом и морской водой, должны быть изготовлены из коррозионно-стойких сплавов. Для совместимости с материалом наплавки по 6.6.5 на уплотнительных поверхностях металлические уплотнения следует изготавливать из сплава на основе никеля с FpREN более 40.
6.6.20 Материалы труб ШМ должны быть выбраны в соответствии с таблицей 5 и ГОСТ Р 59305 (см. также [2]).
Таблица 5 — Материалы труб ШМ
Область применения материала | Марка материала |
Трубопроводы, контактирующие с пластовым флюидом | Углеродистые и легированные стали с наплавкой на внутренней поверхности коррозионно-стойкими сплавами |
Двухфазные феррито-аустенитные стали с содержанием Сг 22 % | |
Двухфазные феррито-аустенитные стали с содержанием Сг 25 % | |
Трубопроводы, не контактирующие с пластовым флюидом | Аустенитная коррозионно-стойкая сталь [316L (см. [5]) и 03X17H14M3 в соответствии с ГОСТ 5632] |
Сплавы с более высоким FPREN, чем 316L (см. [5]) |
6.6.21 Изделия, изготовленные из двухфазных феррито-аустенитных сталей, должны быть выполнены с учетом [6].
6.6.22 Значения величины энергии удара при испытании на ударный изгиб образцов eV-образным надрезом по Шарли при температуре минус 46 °C для материалов элементов трубопроводной обвязки (трубы, фитинги, фланцы) должны соответствовать таблице 6.
Таблица 6 — Значения величины энергии удара
Тип стали | Среднее значение, Дж, не менее | Отдельные значения, Дж, не менее |
Углеродистые и легированные стали с минимальным пределом текучести менее 415 МПа | 50 | 38 |
Углеродистые, легированные и мартенситные нержавеющие стали с минимальным пределом текучести не менее 415 МПа | 60 | 45 |
Двухфазные феррито-аустенитные стали | 60 | 45 |
6.6.23 Запирающие элементы ЗА и РА должны быть изготовлены из нержавеющей стали типа 13Сг либо из сплава, обладающего более высокой коррозионной стойкостью, чем материал корпуса арматуры (см. [2]).
6.6.24 Применение титановых сплавов в конструкциях, находящихся под ЭХЗ, не допускается (см. [2]).
6.6.25 Применение титановых сплавов для элементов, контактирующих с метанолом с содержанием воды менее 5 %, не допускается (см. [2]).
6.6.26 Материалы крепежных изделий, применяемые в ШМ, выбирают с учетом [2].
6.6.27 Материал протекторов ЭХЗ следует выбирать в зависимости от условий эксплуатации.
6.6.28 Выбор химического состава и электрохимических характеристик материала протекторов ЭХЗ —см. [7].
6.6.29 Неметаллические материалы ШМ должны быть стойкими к воздействию рабочих сред в диапазоне рабочих температур в течение всего срока эксплуатации.
6.6.30 Неметаллические материалы уплотнений, контактирующих с пластовым флюидом, должны быть стойкими к быстрой декомпрессии и старению в углеводородной среде.
6.7 Требования к изготовлению
6.7.1 Изготовителем должны быть определены, идентифицированы и установлены требования к специальным процессам.
6.7.2 Перечень специальных процессов должен включать, как минимум, сварку, наплавку, термическую обработку.
6.7.3 Специальные процессы подлежат аттестации с целью проверки и оценки соответствия продукции установленным требованиям нормативных документов в соответствии с ГОСТ Р ИСО 9001 — 2015 [пункт 8.5.1, перечисление f)].
6.7.4 Контроль качества изготовления и приемку материалов, деталей и сборочных единиц осуществляют на специально подготовленных площадках, обеспечивающих доступ для проведения визуально-измерительного контроля 100 % поверхности элементов ШМ.
6.7.5 При приемке обязательно наличие документированной информации, подтверждающей качество технологических процессов.
Примечание — Аттестация технологического процесса может быть: первичной (на этапе освоения продукции), периодической (по истечении срока действия предыдущей аттестации, указанной в заключении комиссии) и внеочередной (ухудшение качества изготовляемой продукции, реконструкция технологического оборудования, неприменение технологического процесса в течение одного года и более и т. п.).
6.7.6 Все работы по сварке, наплавке и ремонту следует выполнять в соответствии с процедурами, аттестованными в соответствии с ГОСТ Р ИСО 15614-1 (см. также [8]).
6.7.7 До начала сварочных работ выполняют квалификационные испытания технологий сварки с целью подтверждения того, что технологии сварки, сварочные материалы, сварочное оборудование обеспечивают качественные и количественные характеристики (свойства) сварных соединений, соответствующие установленным требованиям. Квалификационные испытания проводят с участием разработчика настоящего стандарта.
6.7.8 Все работы по сварке, наплавке и ремонту должен выполнять персонал, аттестованный для проведения таких работ в соответствии с ГОСТ Р ИСО 9606-1 и ГОСТ Р ИСО 14732.
6.7.9 Персонал, выполняющий неразрушающий контроль (кроме визуально-измерительного контроля), должен быть аттестован в соответствии с ГОСТ Р ИСО 9712.
6.7.10 Допускается проведение местной термообработки для сварного шва и прилегающего металла. Требования к режимам термообработки после сварки должны быть указаны в соответствующих процедурах термообработки. Процедуры термообработки должны быть аттестованы с учетом [9].
6.7.11 Перед началом производства должна быть разработана схема сварки конструкции, содержащая эскизы, последовательность сварки, номера сварочных процедур и процедур неразрушающего контроля для каждого сварного соединения и наплавки.
6.7.12 Минимальный рекомендуемый катет угловых сварных швов для элементов рамных конструкций составляет:
- 6 мм — для толщины основного металла менее или равного 12 мм;
- 8 мм — для толщины основного металла более 12 мм и менее 20 мм;
- 10 мм — для толщины основного металла более 20 мм.
6.7.13 При выборе катета угловых сварных швов учитывают требования ГОСТ 14771—76 (приложения 1—4).
6.7.14 Максимально допустимое несовпадение кромок на стыковых сварных швах — не более 10 % толщины основного металла или 3,0 мм, в зависимости от того, что меньше.
6.7.15 Рекомендуемое минимально допустимое расстояние между швами на трубах гидравлической системы и выкидной линии ШМ должно соответствовать трем внешним диаметрам трубы, но составлять не менее 50 мм.
6.7.16 Не допускается наличие сварных швов в зонах, подвергнутых деформации в холодном состоянии, например изгибах гнутой трубы, выполненных в холодном состоянии.
6.7.17 Грузоподъемные проушины должны быть приварены с использованием сварных швов с полным проплавлением в соответствии с ГОСТ Р ИСО 13628-4—2016 (подпункт К.3.3.3.2).
6.7.18 Число наплавленных слоев коррозионно-стойкого сплава должно быть не менее двух.
6.7.19 Толщина наплавленного слоя коррозионно-стойкого сплава после механической обработки должна быть не менее 3 мм (см. [2]). Наружные дефекты не допускаются.
6.7.20 Содержание железа на поверхности наплавленного коррозионно-стойкого материала после механической обработки должно быть не более 10 % (по массе).
6.7.21 Твердость поверхности наплавленного коррозионно-стойкого материала не должна превышать 35 HRC (см. [3]).
6.7.22 При нанесении ЛКП должны соблюдаться требования, приведенные в таблице 7.
Таблица 7 — Требования к нанесению ЛКП
Материал подложки | Подготовка поверхности |
Углеродистые и низколегированные стали | Степень абразивной струйной очистки поверхности в соответствии с ГОСТ Р ИСО 8501-1 не менее Sa 21/2 |
Шероховатость поверхности: 50—85 мкм | |
Коррозионно-стойкие стали и сплавы | Степень абразивной струйной очистки поверхности в соответствии с ГОСТ Р ИСО 8501-1 не менее Sa 21/г |
Абразив при абразивной струйной очистке должен быть неметаллическим и не должен содержать хлоридов | |
Шероховатость поверхности: 25—45 мкм |
6.7.23 Изготовление гнутых отводов и кривых вставок должно удовлетворять требованиям ГОСТ 24950.
6.8 Комплектность
6.8.1 Стандартный комплект поставки ШМ приведен в таблице 8. Документация должна быть передана на бумажном носителе в двух экземплярах за исключением формуляра (подлинник формуляра поставляется на бумажном носителе в одном экземпляре) и на электронном носителе. Состав эксплуатационной документации — в соответствии с ГОСТ Р 2.601.
Таблица 8 — Комплект поставки ШМ
Наименование | Количество, шт. |
Документация | |
Ведомость эксплуатационных документов | 1 |
ФО | 1 |
Пояснительная записка | 1 |
РЭ | 1 |
ИМ | 1 |
ТУ | 1 |
Копии документов (сертификаты соответствия) о подтверждении соответствия требованиям ТР ТС | 1 |
Программа обеспечения надежности | 1 |
Упаковочные листы | 1 |
Таблица материалов | 1 |
Документы прослеживаемости | 1 |
Протоколы аттестации процедуры сварки | 1 |
Спецификация процедуры сварки | 1 |
Протоколы контроля сварки и наплавки | 1 |
Сертификаты соответствия на материалы | 1 |
Сертификаты соответствия на покрытия | 1 |
Сопроводительная документация покупных комплектующих изделий | 1 |
Методика проведения неразрушающего контроля | 1 |
Протоколы неразрушающего контроля | 1 |
Комплект отгрузочной документации | 1 |
Ведомость комплекта ЗИП | 1 |
Протокол взвешивания | 1 |
Руководство по транспортированию, консервации и хранению | 1 |
Комплект расчетов на прочность | 1 |
Комплект расчетов обеспечения стабильности потока | 1 |
Протоколы приемо-сдаточных испытаний | 1 |
Детализированный перечень документации поставки | 1 |
Чертежи габаритные с присоединительными размерами | 1 |
Чертежи общего вида | 1 |
Монтажный чертеж | 1 |
Чертеж комплекта поставки | 1 |
Схема электрогидравлическая принципиальная | 1 |
Отчет об оценке доступа ТИПА к узлам устьевой елки, имеющим интерфейсы управления от ТИПА | 1 |
Окончание таблицы 8
Наименование | Количество, шт. |
Протоколы контроля электрохимических характеристик протекторного сплава | 1 |
Сборочные единицы | |
ШМ | 1 |
Защитная крышка для соединительной муфты ШМ | По ТУ |
Детали | |
Основной комплект металлических уплотнений соединительной муфты ШМ | По ТУ |
Комплект ЗИП* | |
Комплект принадлежностей и инструментов** | |
Инструмент для спуска и подъема ШМ | По ТУ |
Комплект инструмента ТИПА для управления ЗА и РА | По ТУ |
Инструмент ТИПА для управления соединительной муфтой | По ТУ |
Комплект металлических уплотнений соединительной муфты | По ТУ |
Комплект БРС соединительной муфты | По ТУ |
Комплект такелажный для перемещений ШМ в надводном положении | По ТУ |
Комплект ЗИП электрических соединителей | По ТУ |
Комплект ЗИП эксплуатационного дросселя | По ТУ |
Комплект ЗИП МФР | По ТУ |
Защитный чехол для хранения | По ТУ |
|
6.8.2 Комплект поставки может быть скорректирован в соответствии с условиями заключенного договора.
6.8.3 Эксплуатационная документация (ФО и РЭ) должна быть разработана в соответствии с ГОСТ Р 2.610 и условиями заключенного договора. В ФО указывают:
- товарный знак и/или наименование изготовителя;
- местонахождение и контактные данные изготовителя;
- наименование и обозначение изделия;
- условное обозначение;
- назначение;
- дату изготовления;
- заводской (серийный) номер;
- сведения о подтверждении соответствия;
- PN, МПа;
- Т °с-'мин’ _ т ' макс
- максимальную глубину установки;
- рабочую среду;
- сведения о материалах основных деталей:
- данные по химическому составу,
- механическим свойствам,
- неразрушающему контролю основного материала,
- сварных соединений и наплавки;
- сведения о консервации;
- стойкость к внешним воздействиям;
- сейсмостойкость по шкале MSK-64 в соответствии с ГОСТ Р 57546—2017 (приложение А);
- номинальный диаметр выкидной линии ШМ, мм (дюйм);
- тип соединительной муфты;
- технические и функциональные характеристики интерфейсов для сопрягаемого оборудования;
- массу в воздухе и морской воде, кг;
- тип ЗА, РА и их основные технические характеристики;
- габаритные размеры изделия, мм;
- срок службы, лет;
- коррозионное исполнение ШМ;
- показатели надежности;
- гарантии изготовителя (поставщика).
6.8.4 Руководство по эксплуатации должно содержать информацию, детально описывающую следующие процессы:
- описание и работу;
- использование по назначению;
- ТО;
- текущий ремонт;
- хранение;
- транспортирование;
- утилизацию.
6.8.5 В ЭД могут быть приведены иные сведения, обеспечивающие эксплуатацию ШМ.
6.9 Упаковка
6.9.1 Упаковка должна обеспечивать сохраняемость ШМ при транспортировании и хранении. Упаковка также должна обеспечивать сохранность при транспортировании и хранении в условиях морского климата.
6.9.2 ШМ перед упаковкой должен пройти процедуру консервации в соответствии с ЭД. Вариант противокоррозионной защиты и упаковки выбирают в соответствии с ГОСТ 9.014 и указывают в ЭД.
6.9.3 Защитный чехол должен обеспечивать возможность просмотра маркировки или ее дублирования и присоединения грузоподъемного оборудования к крепежным элементам, расположенным на раме без демонтажа чехла.
6.9.4 Присоединительные элементы ШМ, наружные уплотнительные и посадочные поверхности должны быть закрыты защитными крышками, предохраняющими внутренние полости от загрязнения, попадания влаги и механических повреждений.
6.9.5 Компоненты, входящие в комплектацию поставки согласно 6.8.1, упаковывают в отдельную транспортную тару — ящики по ГОСТ 10198, контейнеры по ГОСТ Р 51876 или специальные корзины. Способ крепления в транспортной таре выбирают по усмотрению изготовителя с учетом требований к условиям транспортирования. Крепление должно исключать повреждение компонентов при транспортировании.
6.9.6 ЭД и другую сопроводительную документацию вкладывают в герметичный пакет из полиэтиленовой пленки толщиной не менее 150 мкм. Упакованную документацию помещают в специальную тару, на упаковочном листе которой делают соответствующую пометку.
6.10 Маркировка
6.10.1 Сведения о маркировке приводят в ЭД. Маркировка должна быть выполнена в соответствии с ГОСТ 26828. При маркировке должны быть соблюдены нормы законодательства, действующего в каждом из государств — участников Евразийского экономического сообщества и устанавливающего порядок маркирования продукции информацией на государственном языке.
6.10.2 Потребительскую маркировку наносят на информационную табличку, размещаемую в легкодоступном месте на раме ШМ.
6.10.3 Потребительская маркировка должна в общем случае содержать:
- условное обозначение ШМ;
- наименование изделия;
- обозначение изделия по основному конструкторскому документу;
- заводской (серийный) номер;
- наименование страны-изготовителя;
- наименование и/или товарный знак изготовителя;
- юридический адрес изготовителя;
- PN, МПа;
_ т °C'-
1 макс ’
- Т °C-
' МИН’
- срок службы, лет;
- класс материалов, контактирующих с пластовым флюидом;
- массу нетто, т;
- дату изготовления;
- обозначение стандарта организации и/или ТУ;
- штриховой код продукции (в случае наличия).
6.10.4 Транспортную маркировку наносят на ламинированный упаковочный лист, прикрепленный к защитному чехлу (брезент и т. п.) любым способом, обеспечивающим сохранность надписи в течение транспортирования.
6.10.5 Транспортная маркировка в соответствии с ГОСТ 14192 должна содержать:
- полное или условное зарегистрированное в установленном порядке наименование грузополучателя;
- наименование пункта назначения с указанием при необходимости места перегрузки;
- наименование пункта отправления;
- массы брутто и нетто грузового места, кг;
- габаритные размеры грузового места, см (например, длина, ширина и высота);
- состав оборудования(комплектность);
- дату упаковки;
- уникальный идентификатор транспортируемой единицы по ГОСТ ISO/IEC 15459-1. Порядок присвоения идентификатора должен соответствовать положениям ГОСТ ISO/IEC 15459-2;
- отметку о приемке.
6.10.6 На транспортную тару должны быть нанесены следующие манипуляционные знаки, а также при необходимости другие манипуляционные знаки:
- местоположение центра тяжести;
- обозначения мест строповки.
6.10.7 Манипуляционные знаки допускается наносить на внешнюю поверхность защитного чехла.
6.10.8 Маркировку оборудования, сборочных единиц, такелажных точек, индикаторов, интерфейсов ТИПА наносят согласно ГОСТ Р 51365 и ГОСТ Р 59305—2021 (приложение В).
6.10.9 Маркировку, наносимую ЛКП, следует осуществлять по трафарету. Рекомендуемые размеры шрифтов — согласно ГОСТ Р 59305—2021 (приложение В).
6.10.10 Маркировка должна сохраняться в течение всего срока эксплуатации при выполнении требований ЭД изготовителя.
7 Требования безопасности и охраны окружающей среды
7.1 При проектировании, изготовлении и испытаниях ШМ необходимо соблюдать требования ГОСТ 12.2.063 и [10].
7.2 Оценка безопасности ШМ на всех стадиях жизненного цикла должна быть приведена в обосновании безопасности в соответствии с требованиями ГОСТ 33855.
7.3 Контроль и порядок обеспечения показателей безопасности должны соответствовать ГОСТ Р 54123.
7.4 ШМ должен соответствовать требованиям [11].
7.5 ШМ должен соответствовать требованиям охраны окружающей среды в соответствии с ГОСТ 17.1.3.02.
8 Правила приемки
8.1 Для контроля качества изготовления ШМ в соответствии с требованиями ГОСТ Р 15.301 и ГОСТ 15.309 устанавливают следующие основные виды испытаний:
- на опытные образцы — ПИ;
- серийную продукцию — ПСИ.
8.2 Виды и методы контроля и испытаний указаны в таблице 9.
Таблица 9 — Виды и методы контроля и испытаний
Контролируемый параметр | Элементы настоящего стандарта или НД | ПИ | ПСИ | |
Технические требования | Метод контроля и испытаний | |||
Твердость материала | 6.6.7, 6.6.8, 6.7.21,6.6.18 | 9.2 | + | + |
Химический состав материала | 6.6.5, 6.6.12, 6.6.19 | 9.3 | + | + |
Механические свойства материала при растяжении | 6.6.9, 6.6.13, 6.6.14, 6.6.15, 6.6.16, 6.6.17, 6.3.26 | 9.4 | + | + |
Ударная вязкость материала | 6.6.22 | 9.5 | + | + |
Стойкость к старению в углеводородной среде и быстрой декомпрессии | 6.6.30 | 9.6 | + | + |
Стойкость к углеводородной среде и химическим реагентам | 6.6.29 | 9.8 | + | + |
Контроль сварочных и наплавочных процедур | 6.7.6, 6.7.8, 6.7.10, 6.7.11,6.7.17, 6.7.18 | 9.10 | + | + |
Неразрушающий контроль сварных соединений и наплавки | 6.7.9, 6.7.12, 6.7.14, 6.7.19, 6.7.20, 6.7.21 | 9.11 | + | + |
Качество покрытия | 6.5, 6.7.22 | 9.12 | + | + |
Контроль протекторов | 6.6.27 | 9.13 | + | + |
Контроль гибки труб | 6.7.15, 6.7.23 | 9.14 | + | + |
Требования КД | По 6.2.2—6.2.4,6.2.6,6.2.11, 6.2.12, 6.3.4, 6.3.6, 6.3.12, 6.3.13, 6.3.19—6.3.23, 6.3.25, 6.3.27— 6.3.30, 6.3.34, 6.3.36—6.3.46, 6.6.1—6.6.4, 6.6.10, 6.6.11, 6.6.20, 6.6.21,6.6.23—6.6.28 | 9.16 | + | + |
Прочность корпусов | 6.2.1,6.2.5, 6.2.9 | 9.18.1—9.18.8 | + | + |
Герметичность уплотнений ЗА жидкой испытательной средой | 6.2.1, 6.2.5, 6.3.16, 6.3.17 | 9.18.9— 9.18.11 | + | + |
Класс чистоты гидравлической жидкости | 6.3.32, 6.3.33 | 9.18.12 | + | + |
Герметичность трубной обвязки системы управления | 6.2.5, 6.2.7, 6.3.31 | 9.18.13 | + | + |
Прочность трубной обвязки подачи химических реагентов | 6.2.5 | 9.18.16 | + | + |
Герметичность уплотнений ЗА газовой испытательной средой | 6.2.1,6.2.5, 6.3.17 | 9.19 | + | + |
Электрическая проводимость | 6.2.11, 6.2.12, 6.3.24 | 9.20 | + | + |
Прочность грузоподъемных проушин | 6.7.11 | 9.21 | + | + |
Окончание таблицы 9
Контролируемый параметр | Элементы настоящего стандарта или НД | ПИ | пси | |
Технические требования | Метод контроля и испытаний | |||
Конструкционная целостность соединений | 6.3.1,6.3.3, 6.3.5, 6.3.7, 6.3.8, 6.3.10, 6.3.30, 6.3.38 | 9.22.2 | + | + |
Герметичность соединения | 6.2.1, 6.2.5, 6.3.1,6.3.3, 6.3.8—6.3.10, 6.3.35 | 9.22.3—9.22.4 | + | + |
Ресурс | 6.2.2, 6.2.6, 6.4.3 | 9.23 | + | - |
Работоспособность при критических температурных режимах | 6.2.2—6.2.4, 6.3.18 | 9.24 | + | - |
Функционирование | 6.1, 6.3.1, 6.3.2, 6.2.8, 6.3.11, 6.3.14, 6.3.15, 6.3.18 | 9.26 | + | + |
Примечание — Знак «+» означает, что данный вид контроля или испытания обязателен к исполнению, знак «-» — контроль и испытания не проводят.
8.3 ПИ проводят с целью оценки всех характеристик ШМ: подтверждения соответствия требованиям ТЗ и/или ТУ, принятия решения о возможности постановки на производство и использовании их по назначению. Испытаниям подвергают опытные образцы ШМ.
8.4 Порядок проведения ПСИ — в соответствии с ТУ, ПМ (если программа ПСИ не включена в ТУ) и ГОСТ 15.309.
8.4.1 Каждый ШМ подвергают ПСИ в полном объеме.
8.4.2 При положительных результатах испытаний ОТК изготовителя оформляет ФО на ШМ.
8.4.3 Испытательные заглушки высокого давления должны быть предусмотрены для всех требуемых соединительных элементов, работающих под избыточным давлением.
8.4.4 Требования к организации и методам контроля закупаемой продукции определяют в соответствии с ГОСТ 24297.
8.4.5 Совместно с оборудованием, поставляемым на испытания, следует предоставлять полный пакет документации по 6.8.1, а также сертификаты качества приобретенных у других компаний-производителей комплектующих и примененных материалов (металл, ЗА, трубы, протекторы, ЛКП, масло и др.), а также результаты контроля качества сварных и болтовых соединений, выполненных службой контроля качества изготовителя до начала проведения ПИ и ПСИ. Качество применяемых материалов должно быть подтверждено соответствующими сертификатами качества и ПС на партию, серию изделия.
8.5 Согласование ТУ и ПМ с заказчиком необходимо выполнить до начала изготовления и испытаний.
8.6 ШМ должен пройти подтверждение соответствия требованиям:
- [10] и/или нормативных правовых актов Российской Федерации в области промышленной безопасности и технического регулирования;
- настоящего стандарта;
- системы добровольной сертификации ИНТЕРГАЗСЕРТ.
8.7 Подтверждение соответствия ШМ требованиям настоящего стандарта допустимо только в случае проведения контроля в объеме ПИ.
9 Методы контроля и испытаний
9.1 Требования, предъявляемые к условиям, обеспечению и проведению испытаний, требования к испытательным стендам и средам, средствам измерений, а также критерии положительной оценки результатов испытаний — в соответствии с ГОСТ Р ИСО 13628-4 и ГОСТ Р 51365.
9.1.1 Испытательное оборудование, используемое для проверки, испытания и исследования материала или объектов испытаний, должно быть идентифицировано, откалибровано, отрегулировано в соответствии с инструкциями изготовителя, аттестовано в соответствии с ГОСТ Р 8.568.
9.1.2 Все испытания следует проводить при климатических условиях в соответствии с ГОСТ 15150 для принятого климатического исполнения, если не оговорено иное.
9.1.3 Конкретные методы контроля и испытаний и способы их реализации, перечень испытательного оборудования и средств измерения указывают в ТУ, ПМ и РЭ.
9.2 Контроль твердости выполняют в соответствии с ГОСТ 9012, ГОСТ 9013 и ГОСТ Р ИСО 6507-1.
9.2.1 Контроль твердости сварных швов и наплавки осуществляют в процессе аттестации по 9.8. Методики испытания и критерии прохождения контроля в сварных швах и наплавке определяют в соответствии с ГОСТ Р 53678.
9.3 Контроль химического состава элементов ШМ проводят любым из известных методов определения химического состава:
- эмиссионной спектроскопии;
- рентгеновской спектроскопии;
- атомно-адсорбционным;
- сжигания.
9 .3.1 Отбор проб проводят в соответствии с ГОСТ 7565.
9 .3.2 Контроль химического состава наплавки осуществляют методом стилоскопирования по [12].
9.4 Контроль механических свойств при растяжении металлов проводят с помощью испытания на растяжение в соответствии с ГОСТ 1497.
9.5 Испытания на ударную вязкость необходимо проводить в соответствии с ГОСТ Р ИСО 148-1 не менее чем на трех образцах типа II с острым надрезом по Шарпи.
9.6 Стойкость к старению в углеводородной среде и быстрой декомпрессии должна быть подтверждена испытаниями (см. [13] — для термопластов или [14] — для эластомеров). Для испытаний на стойкость к быстрой декомпрессии должны быть выбраны кольца с диаметром поперечного сечения не менее размера кольцевых уплотнений устьевой елки.
9.7 При наличии протоколов ранее проведенных испытаний материала и заключения о его стойкости к старению и декомпрессии допускается не проводить повторные испытания при условии, что испытывался идентичный материал, изготовленный по той же технологии, что и материал уплотнений.
9.8 Стойкость к химическим реагентам определяют контролем совместимости неметаллических уплотнений со всеми реагентами, нагнетаемыми в систему, и она должна быть подтверждена гидравлическими испытаниями по ГОСТ Р 51365. Критерии приемки — см. [13] для термопластов или [14] для эластомеров.
9.9 При наличии протоколов ранее проведенных испытаний материала и заключения о его совместимости со средами допускается не проводить повторные испытания при условии, что испытывался идентичный материал, изготовленный по той же технологии, что и материал уплотнений.
9.10 Контроль сварочных и наплавочных процедур выполняют проверкой документации, подтверждающей:
- аттестацию сварки в соответствии с ГОСТ Р ИСО 15614-1;
- аттестацию наплавки (см. [8]);
- аттестацию процедур по ремонту сварных соединений и наплавки;
- наличие технологии послесварочной термообработки;
- квалификацию персонала, осуществляющего сварочные и наплавочные работы.
9.11 Перед выполнением неразрушающего контроля сварных соединений и наплавки выполняют проверку документации, подтверждающей квалификацию персонала на проведение неразрушающего контроля в соответствии с ГОСТ Р ИСО 9712.
9.11.1 Сварные швы и прилегающую поверхность основного металла, шириной не менее 20 мм по обе стороны шва, очищают от шлака, брызг металла, окалины и других загрязнений.
9.11.2 Сварные соединения и наплавку контролируют в объеме, указанном в ГОСТ Р 51365, следующими неразрушающими методами контроля:
- визуально-измерительный контроль, который проводят в объеме 100 % в соответствии с ГОСТ Р ИСО 17637 для всех сварных соединений;
- магнитопорошковый контроль, который проводят в объеме 100 % в соответствии с ГОСТ Р 56512.
Примечание — Магнитопорошковый контроль допускается заменять на капиллярный контроль, проводимый по ГОСТ 18442;
- ультразвуковой контроль в соответствии с методикой по ГОСТ Р ИСО 17640;
- радиографический контроль в соответствии с методикой по ГОСТ ISO 17636-1;
- контроль толщины наплавки, который проводят методом ультразвукового контроля по ГОСТ Р 50.05.03.
9.11.3 Качество сварных швов должно соответствовать уровню В по ГОСТ Р ИСО 5817.
9.11.4 По результатам проведения каждого вида неразрушающего контроля выпускается отдельный протокол, содержащий:
- вид неразрушающего контроля;
- результат неразрушающего контроля;
- ФИО сварщика/оператора, проводившего сварку;
- ФИО инспектора, проводившего контроль;
- список оборудования, использованного при неразрушающем контроле;
- дату и подпись лица, проводившего контроль.
9.12 Осуществляют контроль качества покрытий проведением предварительных аттестационных испытаний и контроль качества нанесенного покрытия.
9.12.1 Проведение аттестационных испытаний включает в себя испытание на стойкость покрытия при погружении в морскую воду и испытание на стойкость покрытия к воздействию катодной поляризации.
9.12.2 Испытание на стойкость покрытия при погружении в морскую воду выполняют с учетом положений [15]. Контрольными параметрами являются:
- величина распространения коррозии от надреза (см. [16]);
- адгезионная прочность по ГОСТ 32299.
9.12.3 Определяют стойкость покрытия к воздействию катодной поляризации (см. [17], метод А).
9.12.4 Покрытия, наносимые на элементы штуцерного модуля с рабочей температурой более 50 °C, дополнительно испытывают на стойкость к отслаиванию при катодной поляризации.
9.12.5 Контроль качества нанесенного покрытия включает контроль подготовленной поверхности и контроль показателей нанесенного покрытия.
9.12.6 Контроль показателей нанесенного покрытия выполняют в соответствии с методиками, указанными в таблице 10.
Таблица 10 — Контроль показателей покрытий
Наименование показателей | Методика |
Внешний вид покрытия | В соответствии с ГОСТ 9.407 |
Диэлектрическая сплошность покрытия (отсутствие пробоя) | См. [18] |
Адгезионная прочность методом нормального отрыва | В соответствии с ГОСТ 32299 |
Толщина покрытия | В соответствии с ГОСТ 31993 |
9.12.7 Контроль параметров допускается проводить на тестовой пластине, выполненной из того же класса материала, что и покрываемый элемент ШМ.
9.12.8 Проверку колеровки покрытия проводят методом визуального сравнения цвета Л КП с эталоном (контрольным или специально подготовленным).
9.13 Контроль качества изготовления протекторов и проведение аттестационных испытаний протекторов допускается выполнять с учетом [7].
Примечание — При наличии протоколов ранее проведенных аттестационных испытаний протекторов (в рамках испытаний опытного образца или при проведении периодических испытаний — каждые 15 т продукции) повторные испытания допускается не проводить.
9.14 Контроль гибки труб выполняют проверкой документации, подтверждающей аттестацию технологии гибки труб, и документации, подтверждающей квалификацию персонала на проведение неразрушающего контроля, и проведением неразрушающего контроля.
9.15 Визуальный контроль проводят в соответствии с ГОСТ Р ЕН 13018. Положительным критерием прохождения контроля является отсутствие вмятин, задиров, механических повреждений, коррозии на внешних поверхностях объектов испытаний.
9.16 Контроль соответствия ШМ КД осуществляют по сборочным чертежам и чертежам общего вида с возможным дополнительным измерением, с помощью универсальных или специальных измерительных средств и приборов.
9.16.1 Критерием положительного прохождения контроля является полное соответствие размеров КД.
9.17 Проходные диаметры ЗА должны быть проверены путем прохода шаблона через контролируемые отверстия (каналы блоков задвижек и ЗА в открытом положении). Шаблон выполняют согласно ГОСТ Р 51365.
9.17.1 Размеры шаблона должны соответствовать значениям согласно ГОСТ Р 51365.
9.17.2 Объект испытаний считают прошедшим контроль при отсутствии заклинивания шаблона во время контроля и отсутствия на поверхности шаблона механических повреждений.
9.17.3 Проходы, которые не позволяют произвести контроль шаблоном из-за конструктивных особенностей, могут быть подвержены контролю с использованием бороскопа или визуальному контролю.
9.18 Гидростатические испытания проводят как для отдельных единиц оборудования ШМ, так и для оборудования ШМ в сборе.
9.18.1 При проведении испытаний ШМ необходимо обеспечить наличие испытательного оборудования и технической документации по подключению к устройству нагнетания давления. Испытательное оборудование (крышки, заглушки, установочные тумбы и т. д.), необходимое для гидростатических испытаний ШМ, должно точно воспроизводить интерфейсы ПФА и прочего сопрягаемого оборудования СПД.
9.18.2 Перед проведением испытаний линии ШМ должны быть промыты водой по ГОСТ Р 56237. Поверхности сопрягаемых и уплотнительных элементов ШМ, а также крышек, заглушек и испытательных тумб осматривают перед сборкой на наличие повреждений и загрязнений. Испытания проводят в соответствии с ГОСТ Р ИСО 13628-4—2016 (подраздел 5.4).
9.18.3 Испытательной средой является раствор с соотношением 40 % об. воды и 60 % об. моноэтиленгликоля, за исключением трубопроводной обвязки линий управления.
9.18.4 Испытания на прочность и плотность отдельных компонентов ШМ следует проводить при полуторакратном пробном давлении от номинальных значений. Гидростатические испытания корпусов проводят до пневматических испытаний газообразной средой и нанесения покрытий. После проведения испытаний на прочность и плотность выполняют испытания на герметичность относительно внешней среды по уплотнению подвижных и неподвижных соединений, минимум при однократном пробном давлении от номинального давления.
9.18.5 Начальное давление испытаний не должно превышать указанное пробное давление испытаний более чем на 5 %.
9.18.6 Процедура гидростатических испытаний должна состоять из следующих периодов:
- период первичного удержания давления;
- снижение давления до нуля;
- период вторичного удержания давления.
9.18.7 Продолжительность периодов удержания давления — не менее 3 мин для первичного периода удержания и не менее 15 мин для вторичного. Отсчет времени выдержки начинают после стабилизации давления испытаний на уровне не менее пробного давления.
9.18.8 Приемочными критериями гидростатических испытаний является выполнение следующих условий:
- отсутствие видимых утечек в течение периода выдержки под давлением;
- давление, зафиксированное в конце периода выдержки, не ниже уровня пробного давления испытаний;
- изменение давления во время периода выдержки не превышает 1,5 % пробного давления испытаний.
9.18.9 Гидростатические испытания уплотнений ЗА проводят в соответствии с требованиями 9.16.1, с дополнительным периодом выдержки 15 мин. Пробное давление испытания должно быть не менее чем номинальное давление. При проведении испытания ЗА должна находиться в закрытом положении.
9.18.10 Для двунаправленной ЗА необходимо последовательно прикладывать давление на каждую сторону запирающего элемента. Обратная сторона ЗА должна быть открытой в атмосферу во время периода выдержки под давлением.
9.18.11 Однонаправленная ЗА должна быть испытана в направлении движения потока флюида, указанном на корпусе, за исключением обратной арматуры, которая подвергается испытаниям с противоположной стороны.
9.18.12 Промывку трубопроводной обвязки линий управления выполняют для обеспечения требуемого класса чистоты, указанного в РЭ. Промывку осуществляют циклами по 15 мин турбулентным потоком гидравлической жидкости до достижения требуемого класса чистоты. Контроль чистоты выполняют после отбора проб, проведенного в соответствии с требованиями ГОСТ Р 50556—93 (раздел 7), при помощи автоматического счетчика частиц или микроскопа.
9.18.13 Испытания трубопроводной обвязки линий управления гидравлических приводов запорной и регулирующей арматуры проводят в соответствии с требованиями 9.18.1—9.18.9.
9.18.14 Испытательной и промывочной средой для проведения гидростатических испытаний элементов гидравлической линии управления должна быть гидравлическая жидкость требуемого класса чистоты согласно 9.18.12. Пробное давление испытаний должно соответствовать номинальному давлению соответствующей линии.
9.18.15 Процедура проведения испытания должна соответствовать 9.18.9—9.18.11.
9.18.16 Гидростатические испытания трубной обвязки линий подачи химических реагентов выполняют в соответствии с требованиями 9.18.1—9.18.8.
9.19 Контроль герметичности газом (пневматические испытания) проводят как для отдельных единиц оборудования ШМ, так и для оборудования ШМ в сборе.
9.19.1 Механический вытеснитель допустимо применять для уменьшения объема требуемой испытательной среды.
9.19.2 Испытательной средой должен быть азот в соответствии с ГОСТ 9293.
9.19.3 Испытание проводят пузырьковым методом компрессионным способом в соответствии с ГОСТ 24054. Для обеспечения визуального контроля утечек контролируемое оборудование полностью погружают в резервуар с технической водой по ГОСТ 17.1.1.04.
9.19.4 Испытание состоит из одного периода выдержки пробным давлением, равным номинальному давлению, в течение не менее 15 мин.
9.19.5 Начальное давление испытаний не должно превышать указанное давление испытаний более чем на 5 % в соответствии с требованиями ГОСТ Р ИСО 13628-4—2016 (подраздел 5.4). Отсчет периода выдержки начинается после стабилизации давления испытания и изолирования источника давления. Окончательное установленное давление не должно падать ниже испытательного давления до окончания периода выдержки под давлением.
9.19.6 Испытание проводят с непрерывной записью показаний устройств регистрации давления и температуры.
9.19.7 Приемочными критериями гидростатических испытаний являются:
- отсутствие видимых пузырьков в течение периода выдержки под давлением;
- давление, зафиксированное в конце периода выдержки не ниже уровня пробного давления испытаний.
9.19.8 Пневматические испытания газом уплотнений ЗА проводят в соответствии с требованиями 9.17.1 с дополнительной выдержкой под давлением, равным 2 МПа. Вторичный контролируемый период выдержки под давлением должен составлять не менее 15 мин, затем давление со стороны скважины сбрасывают до нуля, но не за счет открытия запирающего элемента. Запирающие элементы должны сохранять свое положение между периодами выдержки.
9.19.9 Для двунаправленной ЗА и РА необходимо прикладывать давление на каждую сторону запирающего элемента. Обратная сторона ЗА и РА должна быть открытой в атмосферу во время периода выдержки под давлением.
9.20 Подтверждением работоспособности ЭХЗ является контроль непрерывности электрической цепи между элементами устьевой елки и протекторами с помощью омметра. Электрическая непрерывность ЭХЗ должна быть подтверждена замерами для всех элементов и частей, не имеющих сварного соединения с анодами.
9.20.1 Значение сопротивления не должно превышать 0,1 Ом.
9.20.2 Допускается использование электрической шины в виде сварной металлической планки с нанесением защитного покрытия на участках, не соответствующих критериям приемки, и повторное проведение контроля.
9.21 Контроль грузоподъемных проушин выполняется проведением испытаний в соответствии с ГОСТ Р ИСО 13628-4—2016 (раздел К.4 приложения К).
9.22 Контроль сопряжения выполняют для подтверждения конструкционной целостности и герметичности систем соединений.
9.22.1 Контроль сопряжения выполняют для следующих систем соединений:
- ШМ и устьевой елки в целом;
- системы мягкой посадки ШМ с направляющими элементами устьевой елки;
- соединительной муфты ШМ с ответной частью устьевой елки;
- электрических разъемов ШМ с соответствующим оборудованием;
- инструментов ТИПА и элементов управления оборудования ШМ (ЗА, дросселей и пр.);
- спускоподъемных инструментов ШМ и инструментов для его технического обслуживания.
9.22.2 Подтверждение целостности конструкции выполняют проведением испытаний в соответствии с ПМ производителя, в которых должны быть учтены следующие эксплуатационные факторы:
- нагрузки от спускоподъемного инструмента;
- нагрузки от натяжения, провисания или бокового изгиба сопрягаемого оборудования, возникающие в процессе монтажа эксплуатации;
- возможность замены уплотнений системы соединений;
- функциональные испытания требуемого спускоподъемного инструмента и инструмента для проведения технического обслуживания;
- максимально допустимая несоосность.
9.22.3 Подтверждение герметичности ШМ, при необходимости, выполняют проведением испытаний в соответствии с 9.16 или 9.17 в зависимости от УТТ системы соединений.
9.22.4 Испытания проводят с применением сопрягаемого оборудования. Возможно проведение испытаний с использованием макетов сопрягаемого оборудования.
9.23 Контроль ресурса элементов ШМ проводят проведением испытаний в соответствии с ГОСТ Р ИСО 13628-4—2016 (пункт 5.1.7):
- испытания с циклическим изменением давления/испытания под нагрузкой;
- испытания с циклическим изменением температуры;
- ресурсные испытания.
9.23. 1 Объектами контроля ресурса являются элементы ШМ, перечисленные в ГОСТ Р ИСО 13628-4—2016 (таблица 3).
9.24 Соответствие применяемого оборудования условиям работы при переходных низкотемпературных эффектах, связанных с эффектом охлаждения Джоуля-Томпсона и условиями пуска в эксплуатацию, устанавливают одним или несколькими методами:
- испытаниями с циклическим изменением температуры компонентов с учетом требуемой минимальной температуры, в соответствии с ГОСТ Р ИСО 13628-4—2016 (пункт 5.1.7);
- контролем компонентов в стандартном рабочем температурном диапазоне с проверкой материала с V-образным надрезом по Шарпи при минимальной переходной рабочей или более низкой температуре в соответствии с требованиями ГОСТ Р ИСО 13628-4—2016 (пункт 4.1.3);
- контролем компонентов в стандартном рабочем температурном диапазоне при наличии документации, подтверждающей применимость материала для работы в диапазоне переходных температур.
9.25 Контроль доступа ТИПА для управления элементами ШМ осуществляют проверкой отчета о результатах проведения моделирования морских операций, с учетом:
- наличия поручней стабилизации;
- защитных конструкций;
- высоты расположения панели управления;
- расположения элементов управления;
- извлечения съемного оборудования.
9.26 Контроль функционирования ШМ выполняется проведением функционального испытания каждого управляемого элемента ШМ в соответствии с ПМ изготовителя, и в общем случае контроль функционирования ШМ должен содержать:
- проверку возможности управления гидравлически управляемыми компонентами ШМ;
- проверку возможности управления компонентами, управляемыми при помощи ТИПА;
- проверку возможности монтажа и демонтажа съемных элементов с последующей проверкой функционирования в соответствии с заявленными характеристиками;
- проверку обеспечения обмена сигнала между КИП и передающим/принимающим устройством;
- проверку герметичности, где это предусмотрено функциональными требованиями;
- проверку стойкости к кратковременным отклонениям технологического режима эксплуатации оборудования, обусловленного функциональными особенностями (такими как превышение/критиче-
ское снижение давления в приводах гидравлически управляемых компонентах и т. п.), с учетом условий эксплуатации и информации из технологического регламента объекта, на котором предполагается эксплуатация ШМ.
9.26.1 Проверка функционирования подразумевает проверку оборудования и компонентов в эксплуатационных или приближенных к эксплуатационным режимах.
10 Транспортирование и хранение
10.1 Транспортирование и хранение ШМ осуществляют в упакованном и законсервированном виде.
10.2 ШМ подлежит перевозке автомобильным, воздушным, железнодорожным и морским транспортом в соответствии с правилами перевозки грузов, действующими на соответствующем транспорте, с учетом массогабаритных характеристик. Оборудование должно быть подготовлено к морской перевозке и хранению на морских платформах.
10.3 Условия транспортирования и хранения:
- по климатическим факторам внешней среды в части хранения — в соответствии с типом ОЖЗ по ГОСТ 15150;
- по механическим факторам — в соответствии с типом Ж по ГОСТ 23170.
10.4 Допускаются другие условия транспортирования и хранения в соответствии с требованиями, указанными в ЭД.
10.5 ШМ упаковывают в защитный чехол для снижения воздействия климатических факторов и защиты от загрязнений и повреждений при транспортировании и хранении.
10.6 ШМ должен быть надежно закреплен во время транспортирования.
10.7 Перед постановкой ШМ на хранение необходимо провести консервацию в соответствии с ЭД и ГОСТ 9.014, вариант временной противокоррозионной защиты ВЗ-8 по ГОСТ 9.014.
10.8 Консервацию оборудования и комплектующих следует осуществлять методами и средствами, не требующими последующей разборки оборудования при монтаже и расконсервации.
10.9 Срок действия консервации должен быть не менее 36 мес со дня отгрузки, без дополнительной переконсервации. Окончание срока действия консервации должно определяться по формулярам, ПС или по промаркированной предупредительной надписи: «Законсервировано до ...» на упаковке.
10.10 Все интерфейсы должны быть закрыты крышками или заглушками во время хранения. Все не защищенные от внешней среды металлические наружные и внутренние поверхности (без антикоррозионного покрытия) должны быть покрыты антикоррозионной обработкой.
10.11 ШМ в состоянии поставки следует хранить при температуре окружающей среды от минус 40 °C до плюс 50 °C и относительной влажности до 98 % при температуре 25 °C.
10.12 Регулярное ТО оборудования при консервации следует выполнять по процедурам, установленным в РЭ (ТУ), но не менее одного раза в год. ТО должно выполняться квалифицированными специалистами, прошедшими соответствующее обучение и имеющими подтверждающие документы о прохождении обучения.
11 Указания по эксплуатации и монтажу
11.1 Следует выделять следующие режимы эксплуатации ШМ:
- подготовка к работе (стендовые испытания);
- транспортирование и хранение;
- монтаж/демонтаж (включая соответствующие испытания);
- пуско-наладочные работы;
- нормальная эксплуатация;
- аварийная эксплуатация;
- ТО и ремонт.
11.2 Монтаж ШМ следует осуществлять только при наличии подписанного акта выполнения стендовых испытаний.
11.3 Транспортирование и хранение следует выполнять в соответствии с разделом 10.
11.4 Эксплуатацию ШМ в каждом режиме следует осуществлять согласно требованиям ЭД.
11.5 Эксплуатацию ШМ в режимах пуско-наладочных работ и нормальной эксплуатации следует осуществлять в пределах температурного класса при давлениях, не превышающих номинальное давление.
11.6 Периодичность и состав работ по организации и проведению ТО ШМ — с учетом требований ГОСТ Р 58218.
11.7 ТО ШМ осуществляют согласно ЭД с соответствующей фиксацией в ФО.
11.8 К ТО, эксплуатации, монтажу (демонтажу) и ремонту ШМ допускаются лица, изучившие ЭД и прошедшие аттестацию в соответствии с [19], в том числе в области эксплуатации опасных производственных объектов нефтегазоперерабатывающих производств, а также в области контроля и управления скважиной при газонефтеводопроявлениях.
11.9 Монтаж ШМ должен предусматривать возможность установки с помощью специализированного инструмента как в надводном положении на ПФА, так и в подводном положении дистанционно.
11.10 Монтаж ШМ на ПФА в подводном положении следует осуществлять при помощи ТИПА.
11.11 При монтаже ШМ на ПФА в подводном положении следует осуществлять контроль за положением ШМ по азимуту.
11.12 При монтаже ШМ средства ориентации должны обеспечивать точность позиционирования по азимуту не более ± 1°.
11.13 Пусконаладочные работы следует выполнять в соответствии с РЭ.
11.14 Управление ШМ в режиме нормальной эксплуатации проводят дистанционно с береговой станции управления посредством ПМУ.
11.15 Режим аварийной эксплуатации ШМ должен предусматривать применение ТИПА для контроля и управления элементами ШМ.
11.16 Демонтаж ШМ по возможности рекомендуется производить с привлечением таких типов судов, технических средств и оборудования, которые использовались при его монтаже. Допускается применение иных типов, если это ускоряет выполнение работ без ущерба для их безопасности и качества.
11.17 Требуется периодическая проверка функционирования ЗА и РА в процессе эксплуатации ШМ. Периодичность проверки указывается в ЭД.
12 Гарантии изготовителя
12.1 Изготовитель должен гарантировать соответствие качества ШМ требованиям ТУ при соблюдении условий и правил эксплуатации, хранения и транспортирования, установленных ЭД.
12.2 Условия применения гарантий изготовителя определяют в соответствии с [20] (часть 2) и заключенным договором на поставку продукции.
Приложение А (справочное)
Примеры общего вида штуцерного модуля и соединительной муфты
А.1 Пример общего вида штуцерного модуля приведен на рисунке А.1.
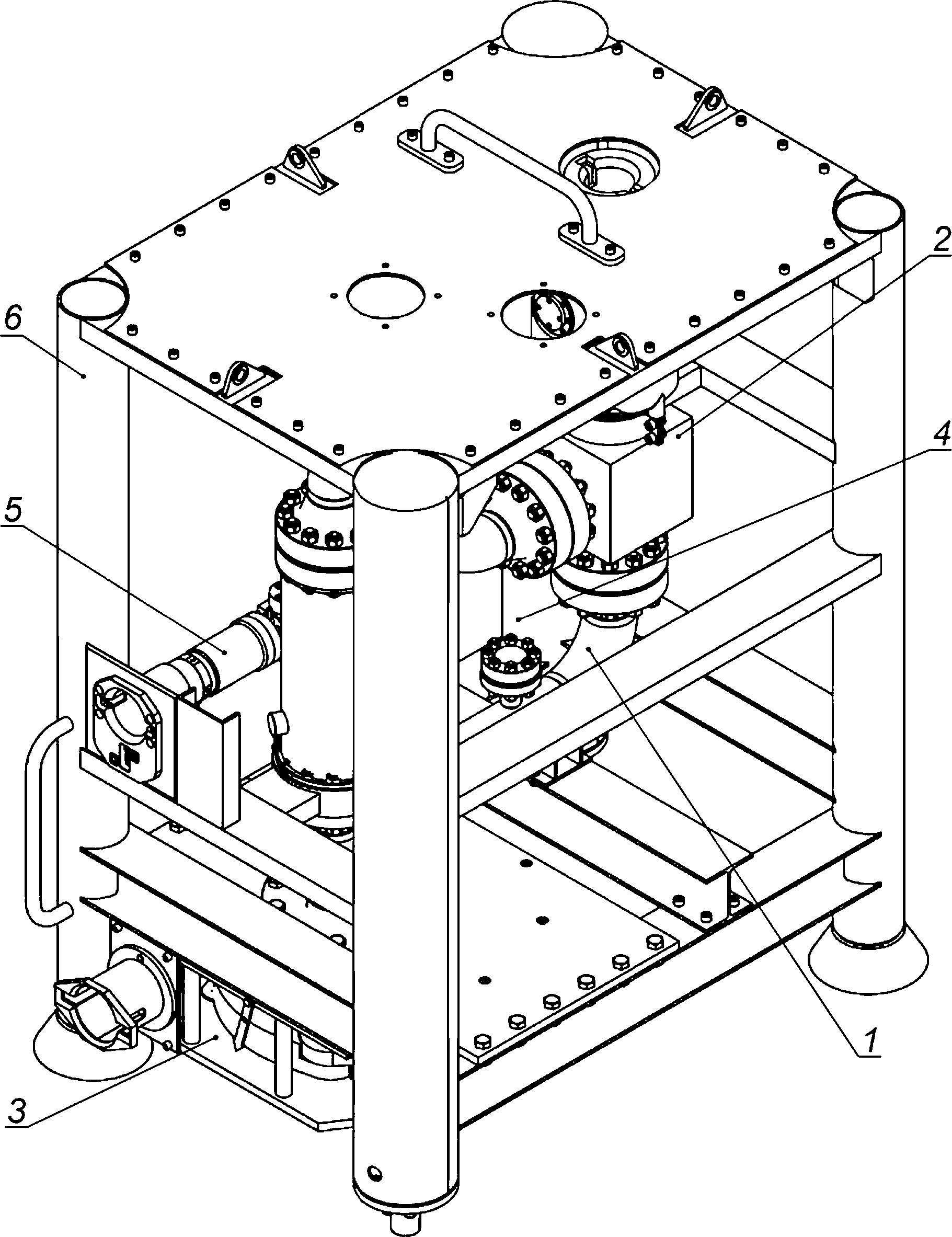
7 — выкидная линия ШМ; 2 — эксплуатационный дроссель; 3 — соединительная муфта; 4 — комплект КИП (электрические соединители и кабели условно не показаны); 5 — система подачи химических реагентов; 6 — несущая рама ШМ
Рисунок А.1 — Штуцерный модуль. Общий вид
А.2 Пример общего вида соединительной муфты хомутового типа приведен на рисунке А.2.
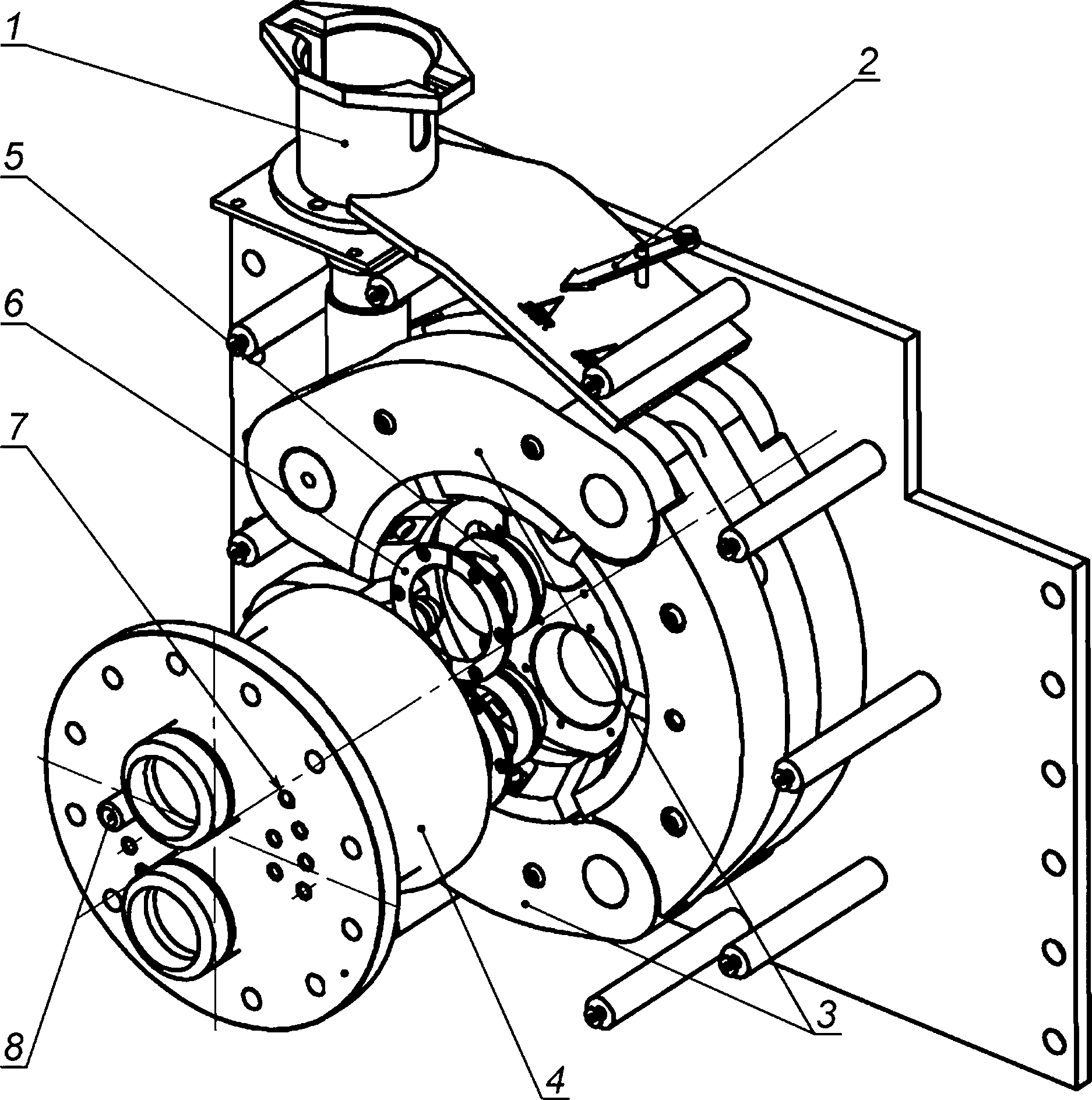
1 — интерфейс ТИПА; 2 — индикатор положения; 3 — рычаги соединителя; 4 — втулка; 5 — металлические уплотнения; б — фиксаторы; 7 — линии управления ЗА и РА; 8 — линия подачи химических реагентов
Рисунок А.2 — Соединительная муфта хомутового типа. Общий вид
Библиография | |
ИСО 13628-8:2002 | Нефтяная и газовая промышленность. Проектирование и эксплуатация систем подводной добычи. Часть 8. Интерфейсы дистанционно управляемых аппаратов (ROV) на системах подводной добычи [Petroleum and natural gas industries — Design and operation of subsea production systems — Part 8: Remotely Operated Vehicle (ROV) interfaces on subsea production systems] |
ИСО 21457:2010 | Нефтяная, нефтехимическая и газовая промышленности. Выбор материалов и коррозионный контроль систем добычи нефти и газа (Petroleum, petrochemical and natural gas industries — Materials selection and corrosion control for oil and gas production systems) |
ИСО 15156-3:2020 | Промышленность нефтяная и газовая. Материалы для применения в средах, содержащих сероводород, при нефте- и газодобыче. Часть 3. Трещиностойкие (коррозионно-стойкие) и другие сплавы [Petroleum and natural gas industries — Materials for use in H2S-containing environments in oil and gas production — Part 3: Cracking-resistant CRAs (corrosion-resistant alloys) and other alloys] |
ANSI/AWS А5.14/А5.14М:2008 | Сварочные электроды и стержни из никеля и никелевых сплавов. Технические условия (Specification for Nikel and Nikel-Alloy Bare Welding Electrodes and Rods) |
АСТМ А269/А269М-15а (2019) | Стандартная спецификация на бесшовные и сварные трубы из аустенитной нержавеющей стали общего назначения (Standard Specification for Seamless and Welded Austenitic Stainless Steel Tubing for General Servic) |
DNV RP-F112:2021 | Дуплексная нержавеющая сталь — предотвращение водородного растрескивания под напряжением при проектировании (Duplex stainless steel — design against hydrogen induced stress cracking) |
ИСО 15589-2:2012 | Промышленность нефтяная и газовая. Катодная защита систем транспортирования по трубопроводам. Часть 2. Морские трубопроводы (Petroleum, petrochemical and natural gas industries — Cathodic protection of pipeline transportation systems — Part 2: Offshore pipelines) |
ИСО 15614-7:2016 | Технические требования и аттестация процедур сварки металлических материалов. Проверка процедуры сварки. Часть 7. Наплавка (Specification and qualification of welding procedures for metallic materials — Welding procedure test — Part 7: Overlay welding) |
ИСО 17663:2009 | Сварка. Требования к качеству термической обработки в процессе сварки и смежных процессов (Welding — Quality requirements for heat treatment in connection with welding and allied processes) |
Технический регламент Таможенного союза ТР ТС 010/2011 | О безопасности машин и оборудования |
Федеральные нормы и правила в области промышленной безопасности «Правила безопасности в нефтяной и газовой промышленности» (утверждены приказом Федеральной службы по экологическому, технологическому и атомному надзору от 15 декабря 2020 г. № 534)
РД 26.260.15-2001 | Стилоскопирование основных и сварочных материалов и готовой продукции |
ИСО 23936-1:2022 | Нефтяная, нефтехимическая и газовая промышленность. Неметаллические материалы, контактирующие со средами при добыче нефти и газа. Часть 1. Термопласты (Petroleum, petrochemical and natural gas industries — Non-metallic materials in contact with media related to oil and gas production — Part 1: Thermoplastics) |
[14] | ИСО 23936-2:2011 Нефтяная, нефтехимическая и газовая промышленность. Неметалличе ские материалы, контактирующие со средами при добыче нефти и газа. Часть 2. Эластомеры (Petroleum, petrochemical and natural gas in-dustries — Non-metallic materials in contact with media related to oil and gas production — Part 2: Elastomers) |
[15] | ИСО 2812-2:2018 Материалы лакокрасочные. Определение устойчивости к воздействию жидко стей. Часть 2. Метод погружения в воду (Paints and varnishes — Determination of resistance to liquids — Part 2: Water immersion method) |
[16] | ИСО 12944-9:2018 Материалы лакокрасочные. Защита стальных конструкций от коррозии при помощи лакокрасочных систем. Часть 9. Защитные лакокрасочные системы и лабораторные методы проверки рабочих характеристик морских и аналогичных сооружений (Paints and varnishes — Corrosion protection of steel structures by protective paint systems — Part 9: Protective paint systems and laboratory performance test methods for offshore and related structures) |
[17] | ИСО 15711:2003 Материалы лакокрасочные. Определение сопротивления катодному разру шению покрытий под воздействием морской воды (Paints and varnishes — Determination of resistance to cathodic disbonding of coatings exposed to sea water) |
[18] | ACTMD5162-15 Стандартная методика контроля несплошности (пропусков) непроводя щих защитных покрытий на металлических подложках [Standard Practice for Discontinuity (Holiday) Testing of Nonconductive Protective Coating on Metallic Substrates] |
[19] | Перечень областей аттестации в области промышленной безопасности, по вопросам безопасности гидротехнических сооружений, безопасности в сфере электроэнергетики (утвержден приказом Федеральной службы по экологическому, технологическому и атомному надзору от 4 сентября 2020 г. № 334) |
[20] | Гражданский кодекс Российской Федерации (часть 2) |
УДК 622.276.04:006:354
ОКС 75.020
Ключевые слова: системы подводной добычи, устьевое оборудование, штуцерный модуль
Редактор Н.В. Таланова
Технический редактор В.Н. Прусакова
Корректор Е.Д. Дульнева
Компьютерная верстка Е.А. Кондрашовой
Сдано в набор 13.01.2023. Подписано в печать 20.01.2023. Формат 60х841/8. Гарнитура Ариал.
Усл. печ. л. 4,65. Уч.-изд. л. 4,12.
Подготовлено на основе электронной версии, предоставленной разработчиком стандарта
Создано в единичном исполнении в ФГБУ «Институт стандартизации» , 117418 Москва, Нахимовский пр-т, д. 31, к. 2.